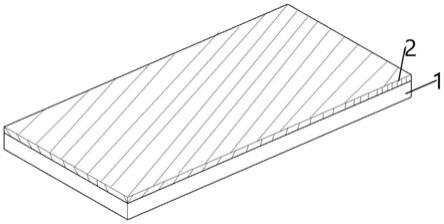
1.本发明是一种结合激光选区熔化和热等静压技术制备钨基复合片的工艺方法,属于异种金属复合技术领域。
背景技术:
2.聚变能的开发应用是彻底解决人类能源危机的希望,目前磁约束核聚变能开发已经进入工程验证阶段,聚变堆内部部件的设计和研制是摆在国内外科研工作者面前最后的屏障。
3.聚变堆内部部件直接面对高温等离子体,工作环境极为恶劣,要求材料必须具有高热导和高机械强度,特别是面对等离子体材料还要与等离子体具有好的兼容性,通常聚变堆内部部件采用多种材料的复合焊接设计,比如偏滤器部件采用钨铜复合设计,而包层部件采用钨钢复合设计,其中钨材料为防护铠甲材料,铜和钢为热沉结构材料,为了提高铜和钢的使用温度和耐辐照性能,一般选择铜合金和低活化钢(rafm)。为了缓解钨铠甲与铜合金热沉或者与rafm钢之间热机械性能失配问题,通常在钨与铜合金或者rafm钢之间添加中间过渡层,比如无氧铜中间层,制备工艺主要为:首先采用热等静压或者浇筑技术制备钨/无氧铜复合片(钨层厚2mm,铜层厚1mm),之后通过热等静压扩散焊技术将钨铜片与铜合金或者rafm钢焊接起来,最后加工制造所需尺寸的内部部件。无氧铜作为高纯铜,具有高热导率和高塑性,但在聚变堆高温和高中子通量环境中长期服役,易发生高温蠕变和辐照脆化,在发生塑性变形过程中易发生接头断裂行为,导致部件失效,影响装置安全。
4.为了增强纯铜中间层的高温力学性能和抗中子辐照性能,目前研究提出了添加钨、sic等复合增强铜层的解决方案。添加钨和sic物质的形式主要有纤维和颗粒两种,也就是先将钨、sic的颗粒或者短纤维与铜粉混合,之后采用高温液相熔合法将二者复合在一起。因为钨和sic颗粒或者纤维与铜的密度不同,在铜熔化过程中极易产生添加掺杂物偏析问题,降低增强效果,导致复合层的整体高温性能失控。为此,也有方法采用将钨和sic纤维预编制好,之后浇筑铜熔液的方法,该工艺虽然可以实现掺杂物的有序添加,但是工序复杂,制作成本高,不利于批量生产。另外也有采用pvd等方法开展复合层的沉积,但是效率太低。
技术实现要素:
5.本发明将针对上述问题,提出结合激光选区熔化和热等静压技术来制备钨基复合片。激光选区熔化技术经过十余年的发展,已经相对成熟,特别适合于阵列式制备薄片。这就为本发明的施行奠定了坚实的技术基础。另一方面,热等静压技术也十分适宜于复合材料的致密化和内部的扩散焊接,进而提高复合材料的性能。因此,拟结合激光选区熔化和热等静压焊接方法,制备钨基复合片,进而大规模应用于聚变堆内部部件的焊接制造。
6.本发明是为钨基复合片提供了一种新的制备方法。
7.为实现上述目的,本发明具体方案如下:
8.一种结合激光选区熔化和热等静压技术制备钨基复合片的工艺方法,包括以下步骤:
9.a)结构设计:所述钨基复合片包括钨片和钨基复合层,其中钨片厚为1-6mm,钨基复合层厚为0.01-2mm。
10.b)连接工艺:将钨片作为基体,采用激光选区熔化技术在钨片上开展复合粉的选区熔化,经过多层熔覆在钨基复合层达到一定厚度,将钨基复合片放入热等静压炉子内,并选择合适热等静压参数开展钨片与钨基复合层以及复合层内钨与其他金属的扩散焊接。
11.进一步的,所述钨片为纯钨或者钨基合金材料。
12.进一步的,所述钨基复合层的材料是钨铜、钨镍、钨铁、钨铬、钨钒、钨钛、钨锆、钨钒铬、钨钒铜或钨铜铁。
13.进一步的,所述钨基复合层的元素在厚度方向上按比例分布。
14.进一步的,所述钨基复合层采用激光选区熔化方法涂覆在钨片上,所述钨基复合层所用的基础材料为钨粉,另外一种材料为铜粉、镍粉、铁粉、铬粉、钒粉、钛粉或锆粉,或者直接用钨钒合金粉、铜包钨粉、镍包钨粉、铁包钨粉、钨铬合金粉、钨钒合金粉、钨钛合金粉、钨锆合金粉、钨钒铬合金粉、钨钒铜合金粉或钨铜铁合金粉。
15.进一步的,所述激光选区熔化指在熔化室摆放一个或者多个钨片并固定,之后铺粉并在每个钨片上开展选区熔化,根据厚度需要经过多次选区熔化进而制备成钨基复合片。
16.进一步的,所述的热等静压过程中,钨基复合层内的复合元素会发生元素扩散,同时钨基复合层内的一些密闭空隙会闭合,进而实现钨基复合层的致密化。
17.进一步的,所述钨基复合片的外形尺寸由设计决定,其外形尺寸在热等静压后加工而成;所述钨片为钨钾、钨铼合金,或者碳化锆掺杂钨合金。
18.进一步的,所述钨基复合层内钨的原子分数在厚度方向上从100%到0%连续变化。
19.进一步的,所述钨基复合层分四层,钨的原子分数在厚度方向上梯度变化。
20.本发明的有益效果如下:
21.本发明通过结合激光选区熔化和热等静压两种技术来制备钨基复合片,其中激光选区熔化是一个实现一种或者两种金属材料的瞬时液态熔化复合焊接过程,而热等静压是一个缓慢实现两种材料固态热压扩散焊接的过程,将二两个过程结合起来,既可以克服瞬时熔化凝固过程残余应力大的问题,还可以实现复合材料的致密扩散,从而达到复合层的强韧化和抗辐照等性能提升;另外,本发明介绍的技术可以实现钨基复合片的批量化生产,特别有利于其在聚变领域的工业化应用。
附图说明
22.图1钨基复合片结构图;
23.图2钨基复合片在激光选区熔化打印室内的排列和熔覆示意图;
24.图中,1为钨片,2为钨基复合层,3为打印室基板,4为激光束。
具体实施方式
25.下面结合附图及具体实施例详细介绍本发明。但以下的实施例仅限于解释本发明,本发明的保护范围应包括权利要求的全部内容,而且通过以下实施例的叙述,本领域的技术人员是可以完全实现本发明权利要求的全部内容。
26.本发明的一种结合激光选区熔化和热等静压技术制备钨基复合片的工艺方法,包括如下步骤:
27.(1)制备的钨基复合片结构如图1所示,其包括钨片1和打印的钨基复合层2。
28.(2)首先在轧制钨板上切加工钨片1,之后将钨片1磨加工成所需尺寸,加工后的表面粗糙度ra控制在小于1.6μm,之后清洗去油污和氧化皮,烘干后摆放在激光选区熔化设备打印室,钨片1排放平整,确保上表面在一个平面,如图2所示。
29.(3)在气氛保护下开展打印室铺粉作业,要求复合粉的高度刚好覆盖钨片1。
30.(4)选用合适的参数开展钨片1区域复合粉的选区熔化,将钨片1上的一层复合粉熔化并沉积在钨片1上形成钨基复合层2。
31.(5)重复(3)和(4)步骤,开展多层选区熔化,在钨基复合层2厚度达到所需尺寸后停止选区熔化。
32.(6)将钨基复合片放入热等静压炉并选择合适热等静压参数开展扩散焊接。
33.(7)按照设计将钨基复合片加工到要求尺寸,一般钨基复合片的尺寸为45x12x2.5mm。
34.优选的,所述钨片1为纯钨或者钨基合金材料。
35.优选的,所述钨基复合层2的材料是钨铜、钨镍、钨铁、钨铬、钨钒、钨钛、钨锆、钨钒铬、钨钒铜或钨铜铁。
36.优选的,所述钨基复合层2的元素在厚度方向上按比例分布,如所述钨基复合层2内钨的原子分数在厚度方向上从100%到0%连续变化或所述钨基复合层2分四层,钨的原子分数在厚度方向上梯度变化。
37.优选的,所述钨基复合层2采用激光选区熔化方法涂覆在钨片1上,所述钨基复合层2所用的基础材料为钨粉,另外一种材料为铜粉、镍粉、铁粉、铬粉、钒粉、钛粉或锆粉,或者直接用钨钒合金粉、铜包钨粉、镍包钨粉、铁包钨粉、钨铬合金粉、钨钒合金粉、钨钛合金粉、钨锆合金粉、钨钒铬合金粉、钨钒铜合金粉或钨铜铁合金粉。
38.优选的,所述激光选区熔化指在熔化室摆放一个或者多个钨片1并固定,之后铺粉并在每个钨片1上开展选区熔化,根据厚度需要经过多次选区熔化进而制备成钨基复合片。
39.优选的,所述的热等静压过程中,钨基复合层2内的复合元素会发生元素扩散,同时钨基复合层2内的一些密闭空隙会闭合,进而实现钨基复合层2的致密化。
40.优选的,所述钨基复合片的外形尺寸由设计决定,其外形尺寸在热等静压后加工而成。
41.优选的,所述钨片1为钨钾、钨铼合金,或者碳化锆掺杂钨合金。现以中国聚变工程试验反应堆(cfetr)水冷陶瓷包层第一壁所用钨铜复合片的制备为例进行更进一步说明。包括以下关键点和步骤:
42.(1)从轧制钨板上线切钨片1,之后上磨床将钨片1的各个面磨到ra小于1.6μm,清洗干净并烘干备用。
43.(2)将清洗干净的钨片1放入选区熔化设备打印室,钨片1按照2x10阵列排放在固定工装内,确保钨片1上表面在一个平面。
44.(3)在打印室按比例铺撒钨粉和铜粉,比如开始时钨粉的原子比例为80%,当复合粉的高度覆盖钨片后用刮刀将复合粉抹平,复合粉的厚度大约为25μm。
45.(4)选用合适的参数开展钨片1区域复合粉的选区熔化,将钨片1上的一层复合粉熔化并沉积在钨片1上形成钨基复合层2。
46.(5)按照程序,打印板自动降低一个打印层厚度,再次铺粉并用刮刀抹平,进而开展第二次选区熔化。
47.(6)开展多层选区熔化,在钨基复合层2厚度达到0.2mm后停止选区熔化。
48.(7)钨基复合层2分为四层,每层厚度为50μm,四层中钨的占比依次为80%、60%、40%和20%。
49.(8)将钨基复合片放入热等静压炉并选择合适热等静压参数开展扩散焊接,针对钨铜复合片,热等静压温度选择为1050℃。
50.(9)按照设计将钨基复合片加工到要求尺寸,一般为45x12x2.2mm。
51.本发明未详细阐述部分属于本领域技术人员的公知技术。以上所述仅为本发明的较佳实施例,并不用以限制本发明,凡在本发明的精神和原则之内,所作的任何修改、等同替换、改进等,均应包含在本发明的保护范围之内。
再多了解一些
本文用于企业家、创业者技术爱好者查询,结果仅供参考。