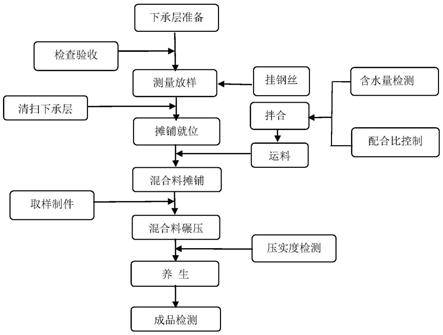
1.本发明属于市政工程领域,涉及导行路水泥稳定碎石施工,尤其涉及导行路双层联铺试验段施工方法。
背景技术:
2.市政道路工程是城市建设工作的一个重要组成部分,是为城市居民和企业,事业单位的生活和生产提供服务的基础工程,因此,道路工程施工质量,直接影响城市的各项经济建设。
3.在实际工作生活中,经常会遇到高速公路某某路段因为天气、事故或者道路施工需要封闭道路中断交通的情况,此时候需要修筑导行路,执行标准按照高速公路标准进行,保证通行的顺畅性。
4.为了确定压路机型号以及小型夯机等机械的使用最佳配合经济必选;确定松铺厚度和压实厚度以及其他参数,需要设置试验段,以保证后续整个工程的施工质量,所以试验段的施工至关重要。
技术实现要素:
5.本发明要解决的问题是在于提供导行路双层联铺试验段施工方法,解决了以上背景技术中存在的问题,施工质量稳定可靠,效率高。
6.为解决上述技术问题,本发明采用的技术方案是:导行路双层联铺试验段施工方法,包括以下步骤,
7.s1、下承层准备,底基层施工前下承层检查验收合格,在下承层内侧支设钢模板,然后对下承层进行彻底清扫;
8.s2、测量放样,放样出中桩、边桩,确定摊铺的宽度,便于路肩培土,在两侧打设基准点,控制高程;
9.s3、混合料的拌和与运输;混合料拌合均匀,使混合料运至现场摊铺时的含水率不小于最佳含水率,运输上料时,出料口距车厢槽帮最高点距离不得大于50cm,卸料时,让混合料自然卸到摊铺机料斗中,卸料速度与摊铺速度相协调,避免运输车撞击摊铺机以及将混合料卸在摊铺机外面;
10.s4、混合料的摊铺,采用两台摊铺机梯形作业,在摊铺起点,将摊铺机熨平板升起,按照虚铺厚度将已加工好的枕木放在下面,放置平衡,满足虚铺厚度要求,然后落下熨平板,正常摊铺时,连续、均匀地摊铺;
11.s5、混合料的碾压,驱动轮朝向摊铺机方向,由路边向路中、先轻后重、先慢后快、低速行驶碾压,避免出现推移、起皮和漏压的现象,严禁压路机在碾压成型或正在碾压路段调头或急刹车;碾压过程为初压-复压-终压,初压使摊铺好的混合料经初压成稳定状态,复压进行路面密实,终压进行收面;
12.s6、接缝处理,避免纵向接缝,横向施工缝用人工把含水量合适的混合料补齐,垂
直于路中心线放置方木,方木高度同压实层厚度相等,碾压密实;
13.s7、养生和质量检验,水泥稳定碎石混合料碾压完成,检测合格后及时覆盖透水式土工布洒水进行养生,两幅间应相互搭接20cm以上,保证表面湿润,养生期不少于7天,质量符合设计和施工规范要求。
14.进一步的,在步骤s2中,用φ20mm的钢钎在两侧打设基准点,基准点高程为设计高程加20cm,基准点设立时,直线段每10米一个钢钎,曲线段每5米一个钢钎,挂钢丝绳拉紧,保证基准线水平,基准线采用φ5mm的钢丝固定在钢钎上,每段长度应小于200m,用紧线器拉紧,其拉力不小于1000n。
15.进一步的,在步骤s4中,采用两台摊铺机梯形作业,外侧摊铺机在前,内侧摊铺机在后,前面摊铺机外侧采用标高基准线控制,路中采用6m长导梁控制;后面摊铺机外侧采用标高基准线控制;前后摊铺机相距不超过10m,横向搭接宽度30cm,异型路段人工铺筑时,采用挂线控制标高,摊铺速度要均匀,控制在1.5m-2.0m/min,中途不得变速,摊铺不停顿、间断。
16.进一步的,在步骤s5中,用灌砂法检测压实度是否合格,若不合格应增加碾压遍数,压实度检测频率每200m每车道2处,压路机停车要错开,相隔间距不小于3m,停在已碾压好的路段上,复压完成后对碾压隆起部位人工处理,设专人用6m直尺进行平整度检测,每车道检测。
17.进一步的,在步骤s1之前先进行混合料原料的准备,包括水泥、粗集料、细集料,混合料采用振动成型法进行配合比设计,调配矿质混合料级配,配制不同水泥剂量,水泥剂量在4%-6%。
18.进一步的,水泥采用32.5普通硅酸盐水泥,细集料选用级配良好的石屑,细集料中小于0.075mm的颗粒含量应不大于15%,塑性指数不大于8%,并且集料的亚甲蓝值不大于10g/kg,砂当量不小于50%。
19.进一步的,当拌合设备调试完毕,材料组成设计完成后,进行施工配合比调试,包括第一阶段试生产:按设定的施工参数,不掺加水泥和水,在皮带上取料筛分,验证级配是否符合设计要求,必要时调整生产参数并做好相关的记录;
20.第二阶段试生产:先按设计配合比掺加水泥和水,然后按标准剂量的
±
1%调整剂量掺加水泥和水,分别取样进行含水量测定、水泥剂量测定、标准密度及无侧限抗压强度试验确定施工配合比指导施工。
21.进一步的,正式拌合前,做集料筛分试验,检验碎石混合料级配是否满足要求,如有问题及时调整,严格控制19mm,9.5mm,4.75mm关键筛孔的通过率,当集料的颗粒级配发生变化时,应重新调整配合比,保证混合料级配符合设计要求,拌合时,水泥剂量比设计增加0.5%,每半天进行一次混合料筛分,保证矿料级配准确,级配发生变化时,计算进行调整,混合料拌合均匀,严禁出现花白料及离析现象,含水率1.0%-2.0%。
22.进一步的,搅拌过程中,减少混合料的离析,水稳混合料在搅拌站输出时,降低出料高度,成品仓应间歇放料,成品仓放料口距运料车厢的垂直距离不宜大于0.5m;摊铺过程中,摊铺机的螺旋布料器有三分之二埋入混合料中,使螺旋布料器均匀地运转。
23.与现有技术相比,本发明具有的优点和积极效果如下。
24.1、本发明严格控制混合料拌合质量,拌合过程当中时时检测,并调整设备性能,保
证水泥剂量,拌合时,水泥剂量宜比设计增加0.5%,每半天进行一次混合料筛分,保证矿料级配准确,级配发生变化时,计算进行调整,从原料上进行预防和准备,保证厚度的施工质量;
25.2、本发明在运输和摊铺的过程中,设置上料和下料的注意事项,尽可能减少混合料的离析,保证均匀装料,连续摊铺和卸料,速度平稳,摊铺机后面应设专人消除细集料离析现象,同时摊铺设备布料螺栓加反向叶片,并调整好角度,防止离析,稳定可靠,效率高;
26.3、本发明可保证水稳层平整度,碾压在水泥初凝前及试验确定的延迟时间内完成,并达到要求压实度,摊铺机铺装过程中,保证连续均匀地摊铺,保证压实度。
附图说明
27.构成本发明的一部分的附图用来提供对本发明的进一步理解,本发明的示意性实施例及其说明用于解释本发明,并不构成对本发明的不当限定。在附图中:
28.图1是本发明导行路双层联铺试验段施工方法实施例的导向路横断面图;
29.图2是本发明导行路双层联铺试验段施工方法的流程图;
30.图3是本发明水泥稳定类基层检测标准表。
具体实施方式
31.需要说明的是,在不冲突的情况下,本发明中的实施例及实施例中的特征可以相互组合。
32.在本发明的描述中,需要理解的是,术语“中心”、“纵向”、“横向”、“上”、“下”、“前”、“后”、“左”、“右”、“竖直”、“水平”、“顶”、“底”、“内”、“外”等指示的方位或位置关系为基于附图所示的方位或位置关系,仅是为了便于描述本发明和简化描述,而不是指示或暗示所指的装置或元件必须具有特定的方位、以特定的方位构造和操作,因此不能理解为对本发明的限制。此外,术语“第一”、“第二”等仅用于描述目的,而不能理解为指示或暗示相对重要性或者隐含指明所指示的技术特征的数量。由此,限定有“第一”、“第二”等的特征可以明示或者隐含地包括一个或者更多个该特征。在本发明的描述中,除非另有说明,“多个”的含义是两个或两个以上。
33.在本发明的描述中,需要说明的是,除非另有明确的规定和限定,术语“安装”、“相连”、“连接”应做广义理解,例如,可以是固定连接,也可以是可拆卸连接,或一体地连接;可以是机械连接,也可以是电连接;可以是直接相连,也可以通过中间媒介间接相连,可以是两个元件内部的连通。对于本领域的普通技术人员而言,可以通过具体情况理解上述术语在本发明中的具体含义。
34.下面结合附图对本发明的具体实施例做详细说明。
35.如图1-图3所示,导行路桩号范围为dxk0 222.425-dxk1 200.120,全长977.695m,全线采用双向四车道高速公路标准,设计速度采用80km/h,路基标准宽度21.5m,行车道宽度采用为4*3.75m,中央分隔带为1m,路缘带为2*1.5m,硬路肩为2*1.5m,土路肩为2*0.75m,如图1所示,为导行路横断面图。
36.导行路水泥稳定碎石试验段选在dxk0 427.591-dxk0 994.954,总长567.363m,压实厚度为0.18m,试验段水泥稳定碎石分为两层,分别为底基层3.0mpa/7d以及基层4.0mpa/
7d,摊铺方式采用双层联铺,强度按照基层4.0mpa/7d执行,此段落作为水泥稳定碎石双层联铺试验段。
37.本工程所处区域属暖温带季风型大陆性半湿润干旱气候,春旱少雨,夏湿多雨,秋凉干燥,冬寒少雪。多年平均气温12.4℃,极端最高气温41.2℃,极端最低气温-22.2℃。多年平均降水量495.1毫米,极端最大年降水量931.8毫米,极端最小降水量207.3毫米。全年以偏北风最多,年平均风速2.1米/秒。历史极端最大风速为20米/秒。
38.本项目所在场地地基基本稳定,地下水水位对工程建设影响较小,基本不存在软弱土、可液化土等问题,地面沉降问题发育程度弱。该场地15米深度范围内分布有第四系冲洪积堆积物,在垂向上具有明显的沉积韵律,水平方向上分布厚度较稳定。场地土主要划分为粉质黏土、粉土、粉砂、中砂等。场地地下水位埋深12.74-13.41米,场地非液化土层厚度和地下水位深度符合dw》d0 db-3,场地可不考虑液化影响,且本区标准冻深为0.6米。
39.导行路双层联铺试验段施工方法,包括以下步骤。
40.一、在进行施工前,先按照以下步骤进行施工准备。
41.1、场站准备
42.(1)水泥稳定碎石采用商品拌合站成品料运至现场,商品拌合站位置在河北省廊坊市霸州市开发区大何庄村,运距为23.5公里,需要45分钟运至施工现场,商品站采用wcb-800型(800t/h)稳定土拌合设备,设备采用双拌缸,拌缸长度不小于5m,冷料仓5个,配备水流量计和水泥重量计,并能在操作室显示加水量和水泥用量,拌合设备计量准确,并经质量技术监督所检定合格,拌合楼电脑能随时记录分时段的生产配合比及产量以及总量累计,并可以储存或导出,并且拌合站安装监控。
43.(2)料斗上方加设10cm
×
10cm的直径不小于φ16的钢筋方格网,筛除超出粒径规格的集料和杂物,料斗间设置挡板,高度不小于80cm。
44.(3)废料集中堆放,特别是运料车上未清空的废料。
45.(4)拌合场地应干净、整洁,集料堆下不积水,设备停放有序。
46.(5)试验段方案经监理单位审批后,对作业班组进行技术和安全交底后,才可进行试验段施工。
47.2、原材准备
48.由于水泥稳定碎石采用外购成品料运至施工现场,故施工单位进行过程材料与配合比的把控工作。
49.(1)水泥
50.根据室内配合比设计验证,采用32.5普通硅酸盐水泥,进场水泥经试验室取样检测,各项技术指标要符合国家技术标准的要求。
51.表1泥技术指标
[0052][0053]
(2)粗集料:粗集料级配符合下表要求。
[0054]
表2粗集料技术指标
[0055]
检测项目技术要求试验方法有机物含量浅于标准颜色t03160.075mm以下粉尘含量(%)≦2t0316针片状含量(%)≦20t0316硫酸盐含量(%)≦0.25t0316软石含量(%)≦5t0316压碎值(%)≦26t0316
[0056]
(3)细集料:细集料选用级配良好的石屑,细集料中小于0.075mm的颗粒含量应不大于15%,塑性指数不大于8%,并且集料的亚甲蓝值不大于10g/kg,砂当量不小于50%。
[0057]
表3细集料技术指标
[0058]
检测项目技术要求亚甲蓝值≦100.075mm以下粉尘含量(%)≦15塑性指数≦8
[0059]
3、混合料组成设计
[0060]
混合料采用振动成型法进行配合比设计,调配矿质混合料级配,配制不同水泥剂量,水泥剂量配置2种,分别为4%、5%,4%水泥剂量现场实际检测结果为4.1,5%水泥剂量现场实际检测结果为5.4,5%水泥剂量符合设计图纸7d/4.0mpa的要求,经过试验的理论配比以及其他指标如下:
[0061]
表4混合料设计
[0062][0063]
水泥稳定碎石7d浸水抗压强度应符合《公路路面基层施工技术规范》相关要求。
[0064]
为减少底基层裂缝,在满足设计强度的基础上控制水泥用量,水泥剂量控制在
4%,最大不超过6%。在减少水泥量的同时,限制细集料、粉料用量;根据施工气候条件调整用水量。
[0065]
4、矿料级配
[0066]
水泥稳定碎石的组成设计包括原材料质量检验,矿质混合料级配组成设计,确定必需的水泥剂量和混合料的最佳含水量等。拌合厂开始生产前,应根据现场集料进行设计配合比复验,复验合格的配合比作为标准配合比控制生产。
[0067]
表5水泥稳定碎石级配范围
[0068][0069][0070]
5、底基层的生产配合比调试
[0071]
当拌合设备调试完毕,材料组成设计完成后,应进行施工配合比调试。
[0072]
第一阶段试生产:按设定的施工参数,不掺加水泥和水,在皮带上取料筛分,验证级配是否符合设计要求,必要时调整生产参数并做好相关的记录。
[0073]
第二阶段试生产:先按设计配合比掺加水泥和水,然后按标准剂量的
±
1%调整剂量掺加水泥和水。分别取样进行含水量测定、水泥剂量测定、标准密度及无侧限抗压强度试验确定施工配合比指导施工。
[0074]
6、施工现场准备
[0075]
(1)路基交验:路基交验由总监办、施工单位方共同参与实现。
[0076]
(2)路基质量检查:应检查路基施工质量(高程、中线偏位、宽度、横坡度、平整度、压实度、反射裂缝、弯沉等)。
[0077]
(3)在水泥稳定碎石(4.0mpa/7d)施工前应无过干、过湿现象,表面平整、无积水、无松散现象。
[0078]
二、导行路双层联铺试验段施工工艺流程如下
[0079]
工艺流程:如图2所示,下承层准备
→
测量放样
→
混合料拌合
→
混合料运输
→
混合料摊铺
→
混合料碾压
→
压实度检测
→
养生
→
成品验收
→
下一道工序。
[0080]
1、下承层准备
[0081]
(1)底基层施工前下承层检查验收合格。包括高程、中线偏位、宽度、横坡度、平整度、反射裂缝、弯沉等。下承层表面应平整、坚实,具有合适的路拱和横坡,没有任何松散、软弱部位,边沿顺直,路肩平顺、整齐。
[0082]
(2)在下承层内侧支设高180mm钢模板,钢模板支立牢固线条要顺直;在外侧先培
土路肩,用小型压实机压实,达到规定的压实度后切边与底面垂直,再铺设塑料薄膜以防止水稳碎石边缘水份损失,摊铺宽度保证上层设计宽度要求。
[0083]
(3)对下承层进行彻底清扫,并适量洒水,在施工过程当中,保持下承层表面湿润,以保证上下层之间的结合。
[0084]
2、测量放样
[0085]
(1)下承层经监理工程师检查验收合格后,采用gps准确放样出中桩、边桩,确定摊铺的宽度,便于路肩培土。
[0086]
(2)用φ20mm的钢钎在两侧打设基准点,以此来严格控制高程,基准点高程为设计高程加20cm,基准点设立时,直线段每10米一个钢钎,曲线段每5米一个钢钎,挂钢丝绳要拉紧,保证基准线水平。
[0087]
(3)基准线采用φ5mm的钢丝固定在钢钎上,每段长度应小于200m,用紧线器拉紧,其拉力不小于1000n。
[0088]
3、混合料的拌和
[0089]
(1)水泥稳定碎石混合料采用wcb800t/h的稳定土拌合设备进行拌合,拌合前对拌合设备进行反复检验调整,使拌合设备计量准确,并经质量技术监督所检定合格。
[0090]
(2)采用3台zl-50装载机给料斗上料,开工前对机手进行培训,铲料符合要求,减少上料时的离析现象的发生,供料均匀,不宜过满,料斗间用隔板分隔,避免串料现象发生。上料前试验人员应测定集料的含水率,避免集料含水率变化频繁,影响混合料的含水率。
[0091]
(3)开始正式拌合前,做集料筛分试验,检验碎石混合料级配是否满足要求,如有问题及时调整,严格控制19mm,9.5mm,4.75mm关键筛孔的通过率。当集料的颗粒级配发生变化时,应重新调整配合比,保证混合料级配符合设计要求。
[0092]
(4)混合料拌合要均匀,严禁出现花白料及离析现象,根据天气温度的变化及时调整含水率,一般控制在大于最佳含水率1.0%-2.0%左右,使混合料运至现场摊铺时的含水率不小于最佳含水率。
[0093]
(5)拌合站现场试验员,检测拌合时混合料的水泥剂量、含水率和各种集料的配合比,并做好记录,发现异常时及时调整或停止生产。
[0094]
(6)各料斗配备1-2名工作人员及时清理料仓口超粒径石块及杂物,时刻监视下料情况,保证不出现卡堵现象,确保机械设备正常运转。
[0095]
4、混合料的运输
[0096]
(1)根据拌合能力(800t/h)、运输距离(约23.5km)及摊铺速度(1.5m-2.0m/min),拟采用20辆载重50t以上大吨位自卸车运输,自卸车车厢应清理干净,不得有剩余料或水积聚在车厢底部。
[0097]
(2)从拌和楼向运料车上放料时,出料口距车厢槽帮最高点距离不得大于50cm,采取三次卸料法,以减少粗细集料的离析现象。
[0098]
(3)自卸车装料后,采用不透水篷布覆盖,篷布下缘到达槽帮的2/3(由上至下计算)并绑扎牢固,避免水份损失,以免影响压实及成型效果。
[0099]
(4)运输车辆出场时,过磅、开具出场单,标明吨位、出场时间、车数编号一式四份,存根磅房留存,混合料到现场后,施工人员查看出场单及目测混合料的质量,对于时间过长的混合料予以废除,摊铺后签收出场单,并写明摊铺时间。
[0100]
(5)运输车由专人进行负责指挥,装有联络通讯工具,及简单的维修工具,车辆出现问题能够及时沟通处理,保证车辆出现故障后,能够及时抢修,能在最短的时间内恢复运转。
[0101]
(6)运输车卸料时,设专人指挥,使运输车在摊铺机前方30cm左右停车,挂空挡,摊铺机前进碰到运输车,由工人敲开运输车后挡门栓,运输车料斗分三次起升,让混合料自然卸到摊铺机料斗中,避免自卸车起升过快,粗集料滚落集中造成局部离析,运输车司机与摊铺机操作手密切配合,边前进边卸料,卸料速度与摊铺速度相协调,避免运输车撞击摊铺机以及将混合料卸在摊铺机外面。
[0102]
5、混合料的摊铺
[0103]
摊铺前下承层清扫干净,无杂物,并洒水湿润,洒水量不宜过大或过小,以不流淌为准;摊铺时保持下承层处于湿润状态,随洒随铺,洒水不宜过量。
[0104]
(1)摊铺机型号:两台徐工摊铺机,型号分别为:903、953t
[0105]
水泥稳定碎石4.0mpa/7d分上下基层,一般路段下基层设计摊铺宽度为10.81,基层设计摊铺宽度为10.48;两台摊铺机组装宽度分别为6.5m和4.50m。
[0106]
松铺系数分两段验证分别为:
[0107]
①
dxk0 427.591-dxk0 677.591段松铺系数拟采用1.25,松铺厚度=18cm
×
1.25=22.5cm,施工时按22.5cm松铺厚度控制。
[0108]
②
dxk0 677.591-dxk0 994.954段松铺系数拟采用1.30,松铺厚度=18cm
×
1.30=23.4cm,施工时按23.5cm松铺厚度控制,根据压实后的厚度检测及时调整。
[0109]
(2)采用两台摊铺机梯形作业(外侧摊铺机在前,内侧摊铺机在后)。前面摊铺机外侧采用标高基准线控制,路中采用6m长导梁控制;后面摊铺机外侧采用标高基准线控制;前后摊铺机相距不超过10m,横向搭接宽度30cm。异型路段人工铺筑时,采用挂线控制标高。摊铺机就位具体做法如下:在摊铺起点,将摊铺机熨平板升起,按照虚铺厚度将已加工好的枕木放在下面,放置平衡,满足虚铺厚度要求,然后落下熨平板,检查螺旋送料器的运转情况和传感器的灵敏度,保证机械能够正常运转。
[0110]
(3)正常摊铺时,每台摊铺机前有2~3辆运输车在等待卸料,以保证连续、均匀地摊铺。卸料时运输车起斗角度应尽量大些,使混合料整体塌落,以避免卸料时产生离析。摊铺时,螺旋送料器要匀速送料,杜绝高速运转,避免粗骨料集中滚落造成底部混合料离析;摊铺速度要均匀,控制在1.5m-2.0m/min,中途不得变速,摊铺不停顿、间断,运料车倒车、卸料尽量连续,不能造成摊铺停机待料;要保持储料室内料位稳定,并使摊铺机的螺旋布料器均衡向两侧供料,螺旋布料器料位略高于螺旋布料器,满埋螺旋低速输料,使熨平板挡板前混合料在全宽范围内保持一致,避免摊铺层出现离析现象。
[0111]
(4)摊铺时,摊铺机两侧设专人看管传感器,保证基准线不被扰动。同时采用拉线,随时检测下返高度,以便发现问题及时与摊铺机操作手沟通,进行调整,确保摊铺厚度,避免出现波浪式表面。摊铺过程中及时检测松铺厚度。
[0112]
(5)每台摊铺机前要有2人清理履带前的粒料。每台摊铺机后设1名工人对摊铺后的表面进行检查,对异常混合料及时换填,并通知前场负责人,便于及时分析异常混合料产生原因,与试验负责人、拌和负责人沟通解决;对粗细集料离析现象,特别是局部粗集料窝要铲除,并用筛子筛细混合料人工找补。
[0113]
(6)摊铺机操作手应时时观察混合料的状态,如发现含水量过小、混合料颜色差异性大(水泥含量小)、拌合不均匀等情况,应立即停止摊铺并通知现场技术人员处理。
[0114]
(7)运输车离开时撒在地上的混合料,立即铲除,避免摊铺机履带压在上面而影响摊铺面平整度。设专人用6m直尺纵、横向量测,对平整度差的部位用人工铲除找平。
[0115]
6、混合料的碾压
[0116]
(1)水泥稳定碎石混合料在摊铺30~50m长度后,压路机即可在全宽范围内进行碾压。碾压时,驱动轮朝向摊铺机方向,由路边向路中、先轻后重、先慢后快、低速行驶碾压的原则,避免出现推移、起皮和漏压的现象。严禁压路机在碾压成型或正在碾压路段调头或急刹车。
[0117]
(2)碾压工艺:
[0118]
碾压机械:2台22t轮胎式振动压路机、1台30t胶轮压路机和1台13t双钢轮压路机。为确定水稳碎石底基层试验段压实效果,拟采用两种碾压方式(选择一种最佳碾压组合):
[0119]
dxk0 427.591-dxk0 677.591段采用碾压方式一:
[0120][0121]
初压:(稳压)采用胶轮轮压路机,外侧留30cm不碾压(防止溜肩),压路机以2.5km/h行走速度碾压一遍,停机接头形成45度梯形碾压一遍,使摊铺好的混合料经初压成稳定状态。
[0122]
复压:(密实)采用22吨振动压路机错1/2轮,轻振一遍、重振三遍,碾压速度控制在2.0km/h。
[0123]
终压:采用30t胶轮压路机碾压两遍收面。
[0124]
dxk0 677.591-dxk0 994.954段采用碾压方式二:
[0125][0126]
初压:(稳压)采用钢轮压路机,压路机以2.5km/h行走速度碾压一遍,停机接头形成45度梯形碾压一遍,使摊铺好的混合料经初压成稳定状态。
[0127]
复压:(密实)采用22吨振动压路机错1/2轮,轻振一遍、重振两遍、轻振一遍,碾压
速度控制在2.0km/h。
[0128]
终压:采用胶轮压路机碾压两遍,再用钢轮压路机碾压一遍收面。
[0129]
单钢轮振动压路机重振两遍后,用灌砂法检测压实度是否合格,若不合格应增加碾压遍数,压实度检测频率每200m每车道2处(试验段检测频率加倍)。
[0130]
(3)压路机倒车应自然停车,无特殊情况,不许刹车;换挡要轻且平顺,不要拉动基层。在第一遍初步稳压时,倒车后应原路返回,换挡位置应在已压好的段落上,在未碾压的一头换挡倒车位置错开,要成齿状,出现个别翻浆、起皮时,应进行铲平处理。
[0131]
(4)压路机停车要错开,相隔间距不小于3m,应停在已碾压好的路段上。严禁压路机在刚完成的或正在碾压的路段上调头和急刹车。碾压宜在水泥初凝前及试验确定的延迟时间内完成,达到要求的压实度,同时没有明显的轮迹。
[0132]
(5)混合料加水拌合至碾压成型时间,不得超过水泥初凝时间。
[0133]
(6)平整度检测及处理:复压完成后对碾压隆起部位人工处理,设专人用6m直尺进行平整度检测,每车道检测。
[0134]
7、接缝处理
[0135]
(1)横向接缝
[0136]
混合料摊铺时不宜中断,如因故中断超过2小时或每天施工结束后应设横向施工缝。将摊铺机驶离混合料末端,用人工把含水量合适的混合料补齐。垂直于路中心线放置方木,方木高度同压实层厚度相等,碾压密实。用6m直尺检测平整度,确定切割范围并划线,沿线将平整度不合格的混合料铲除。重新铺筑混合料之前将下承层清理干净,接缝处涂刷水泥浆。
[0137]
(2)纵向接缝
[0138]
避免纵向接缝,在必须分两幅施工时,纵缝必须垂直相等,不允许斜接。
[0139]
8、养生
[0140]
(1)水泥稳定碎石混合料碾压完成,检测合格后及时覆盖透水式土工布洒水进行养生,两幅间应相互搭接20cm以上,保证表面湿润。
[0141]
(2)养生期内,除洒水车外任何车辆禁止通行,采用高度1.5m的标识栏杆进行横向全幅布设并设置“禁止通行”标识牌,设专人进行看管。
[0142]
(3)养生期不少于7天,每天完成段设置养生天数标识牌,前三天洒水次数每天至少6次以上,之后以保持表面湿润为度,每个作业面设专人负责养生工作。
[0143]
9、质量检验
[0144]
(1)粒料应符合设计和施工规范要求,并应根据当地料源选择质坚干净粒料。
[0145]
(2)水泥用量和矿料级配应按设计控制准确。
[0146]
(3)摊铺时应注意消除离析现象,尤其是带状离析和窝状离析。
[0147]
(4)混合料应处于最佳含水量状况下,用压路机碾压至要求的压实度。从加水拌合到碾压终了的时间不应超过水泥初凝时间。
[0148]
(5)碾压检查合格后应立即覆盖或洒水养生,养生期应符合规范要求。
[0149]
(6)表面平整密实、边线整齐、无松散、坑洼、软弹现象,施工接茬平顺。
[0150]
实测项目如图3所示。
[0151]
10、外观要求
[0152]
(1)表面平整密实、无坑洼、无明显离析。
[0153]
(2)施工接茬平整、稳定。
[0154]
三、保障措施
[0155]
1、混合料拌合质量(含水量、水泥剂量、矿料级配)
[0156]
含水量是水稳碎石碾压的关键,当实际含水量w接近最佳含水量(w0)时,压实度才能保证,当w》w0时,水分过大碾压时容易“弹簧”,且在振动碾压时,容易将水泥浆集聚在表面。这样在取芯检查时,试件下部易出现松散或强度不够,当w《w0,水稳层容易松散,碾压不密实,造成强度不足。为保证含水量合适,应设专人检测含水量,并根据气候情况及时调整拌合含水量。
[0157]
水泥剂量是水泥稳定碎石强度是否合格的关键,拌合过程当中必须时时检测,并调整设备性能,保证水泥剂量。为保证水泥剂量,拌合时,水泥剂量宜比设计增加0.5%。每半天进行一次混合料筛分,保证矿料级配准确,级配发生变化时,计算进行调整。
[0158]
2、混合料的离析
[0159]
为尽可能减少混合料的离析,要求做到以下几点要求:
[0160]
(1)水稳混合料在搅拌站输出时,应尽量降低出料高度,成品仓应间歇放料。
[0161]
(2)成品仓放料口距运料车厢的垂直距离不宜大于0.5m,运料车应及时移动前后位置,保证均匀装料,以降低每次装料的堆体高度。
[0162]
(3)运料车辆在运输过程中,应匀速行驶,起步刹车要平稳,路况差时应慢行,避免强烈的颠簸振动。
[0163]
(4)运料车辆在向摊铺机受料斗卸料时,应缓慢均匀地提升车厢,切忌速度太快。
[0164]
(5)摊铺过程中,摊铺机的螺旋布料器应有三分之二埋入混合料中,应使螺旋布料器均匀地运转,切忌或快或慢。在摊铺机后面应设专人消除细集料离析现象,特别应该铲除局部粗集料“窝”,并用新拌混合料填补。
[0165]
(6)人工找平时,应扣锹布料,切忌扬锹远抛,同时,刮爬拖动次数不大于2次。
[0166]
(7)摊铺设备布料螺栓加反向叶片,并调整好角度,防止离析。
[0167]
(8)适当减少摊铺机收斗次数,尽量不收斗。
[0168]
(9)适当降低熨平板高度。
[0169]
(10)摊铺机螺旋布料器后加橡胶垫,防止大料向后滚落造成上下离析。
[0170]
3、平整度
[0171]
水稳基层的平整度事关面层施工质量,如果控制不好,一方面会影响面层的平整度,另一方面会造成面层的厚度难以控制。为保证水稳层平整度,做到以下几点:
[0172]
(1)水稳基层的下承层必须达到规定的平整度要求后,才能进行水稳基层的摊铺,若下承层表面是平整度很差的波浪状,则势必会反射至基层表面,而造成基层表面的平整度难以控制。
[0173]
(2)碾压宜在水泥初凝前及试验确定的延迟时间内完成,并达到要求压实度,同时没有明显的轮迹。严格按照施工方案碾压工艺进行碾压,防止出现波浪,影响平整度。
[0174]
(3)人工找平时,应选用经验丰富、责任心强的人员负责找平,同时要配备6m左右的直尺辅助检查不平整处。
[0175]
(4)摊铺机铺装过程中,应保证连续均匀地摊铺,摊铺机前方应有运料车辆在等候
卸料,否则摊铺机经常停顿会影响平整度。
[0176]
(5)碾压完毕立即做压实度试验,若试验结果达不到标准重新进行碾压。
[0177]
(6)严格控制混合料的用水量,避免含水率过大或过小。
[0178]
4、碾压质量
[0179]
为保证水泥稳定碎石基层的压实度,压实机械是关键,对压实设备能力要求较高。施工过程中必须严格按照试验段确定的碾压组合,配备压路机,保证压实度。质量保证措施
[0180]
5、建立“横向到边、纵向到底、控制有效”的质量检验体系。项目经理部组织严密完善的职能管理机构,按照质量保证体系正常运转的要求,依据分工负责,相互协调的管理原则,层层落实职能、责任、风险和利益,保证在整个工程施工过程中,质量保证体系的正常动作及发挥保障作用。
[0181]
6、施工过程质量控制
[0182]
6.1、原材料
[0183]
(1)水泥、碎石等材料必须经监理工程师批准,未经批准的不允许使用。
[0184]
(2)水泥:选用终凝时间较长(宜在6小时以上)的水泥,宜用32.5水泥。快硬水泥、早强水泥以及受潮变质的水泥严禁使用。
[0185]
(3)碎石:要求其压碎值不超过26%,最大粒径不大于31.5mm;碎石的颗粒组成应符合规范级配要求。小于0.075mm的颗粒含量应小于20%的要求。
[0186]
(4)水:采用饮用水。
[0187]
6.2、混合料的组成设计
[0188]
(1)组成设计原则:粉料含量不宜过多;在达到强度的前提下,采用最佳水泥剂量;改善集料级配,减少水泥用量。
[0189]
(2)不断优化施工配合比,使其强度、压实度达到最优。
[0190]
6.3、水泥稳定基层混合料的拌合
[0191]
拌和站配制混合料,灰剂量、含水量、级配都要符合设计值。由于机器运行误差、气候等因素的影响,混合料各种指标偏离设计值。试验检测人员应及时监测、调整,使之保持在设计值内。
[0192]
6.4、控制混合料含水量
[0193]
拌和站从出料含水量应高于最佳含水率1%左右,到摊铺碾压前,混合料含水量平均损失1%左右。
[0194]
6.5、水泥稳定基层混合料的运输
[0195]
运料车必须有篷布覆盖,装料后立即覆盖,直至卸料时方可取下覆盖篷布,防止水分蒸发影响摊铺、碾压质量。
[0196]
6.6、水泥稳定基层混合料的摊铺
[0197]
混合料从出拌和站到摊铺地点,应尽量缩短时间,在水泥的初凝时间内完成拌和、运输、摊铺、碾压等。
[0198]
6.7、水泥稳定基层混合料的碾压
[0199]
碾压时应遵循碾压原则,设专人检测平整度。
[0200]
严格按照以上步骤进行,从原料的准备,混料到运输进行严格控制,按照以下工艺进行,下承层准备
→
测量放样
→
混合料拌合
→
混合料运输
→
混合料摊铺
→
混合料碾压
→
压
实度检测
→
养生
→
成品验收
→
下一道工序,减少了返工过程,提升了试验段施工的质量和效率。
[0201]
以上对本发明的一个实施例进行了详细说明,但所述内容仅为本发明的较佳实施例,不能被认为用于限定本发明的实施范围。凡依本发明申请范围所作的均等变化与改进等,均应仍归属于本发明的专利涵盖范围之内。
再多了解一些
本文用于企业家、创业者技术爱好者查询,结果仅供参考。