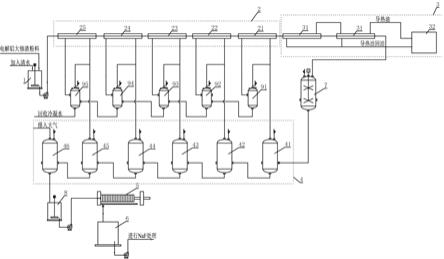
1.本发明属于电解铝废弃物处理技术领域,具体涉及一种对铝电解槽大修渣进行脱毒的处理系统及处理方法。
背景技术:
2.铝电解槽大修渣是电解槽破损后拆除的内衬,其中因含有氟化物/氰化物而被列入危险废物名录。现有的大修渣处理工艺分为火法和湿法,其中火法由于能耗高未能推广应用,湿法处理是目前大修渣处理的主流技术。湿法处理线是在大修渣中加入氧化剂将氰离子分解脱毒,加入ca
2
/mg
2
/al
3
形成相应的氟化盐沉淀脱毒。这种方法效率高、脱毒效果稳定。但是这种方法在将氰化物分解和将f离子沉淀除去的同时生成了可溶性钠盐,通常是氯化钠。随着反应的反复进行,氯化钠的浓度会在循环水中越来越高,固液分离后存在于尾渣中的废液也给尾渣中带入了较多的可溶性盐。可溶性盐的含量高给尾渣的再利用带来了很大的困难。
3.申请公布号为cn101444660a的发明专利申请,公开了在常温下电解槽大修渣或固体含氰化物和氟化物无害化处理及回收工艺的方法,其是采用将含有氰化物和氟化物的电解槽大修渣与可在水中分解为次氯酸的钙,镁,钠化合物以及可溶于水的钙,镁,铝盐加1∶1重量比的水球磨共混制浆,使氰化物在球磨制浆的液相中被分解还原,同时可溶于水的钙,镁,铝盐释放出的钙,镁,铝离子在液相中与氟离子生成不溶于水的氟化钙,氟化镁,氟化铝无害的沉淀物,固液分离后使中性水与泥浆分离,达到无害化无排放的目的。该发明专利申请即在氰化物分解和将f离子沉淀除去的同时生成了可溶性氯盐。
技术实现要素:
4.本发明为了优化资源利用、低能耗除氰脱氟的同时使尾渣滤饼中不含氯盐,采用高温高压的浸出系统,在高温高压的条件下将铝电解槽大修渣中的氟化物浸出,同时将氰化物分解,高温料浆经多级自蒸发将浸出浆液降到常压,自蒸发产生的二次蒸汽用于预热料浆。本发明可充分利用系统热量,将能耗降到最低。
5.铝电解槽大修渣中含有剧毒物氰化钠,氰化钠易溶于水。本发明采用加压除氰的方法将大修渣中的剧毒氰化物除去,同时将大修渣中的可溶性氟化钠溶解回收。
6.本发明加压水解除氰的基本原理是,将氰化物水溶液置于密闭的容器内,在一定的压力和温度条件下,经过一定的反应时间,使氰化物分解成为甲酸盐、氨等无毒或微毒的化合物。当废水中的氰化物以游离状态存在,其反应方程式为:cn- 2h2o=hcoo- nh3。
7.本发明所采用的对铝电解槽大修渣进行脱毒的处理系统,包括:混合槽、预热装置、高温加热装置、自蒸发装置和固液分离装置;混合槽用于对铝电解槽大修渣磨粉料和清水进行混合搅拌制浆;所述预热装置包括多级预热段,每级预热段均为套管结构,混合槽出料口连接预热装置的管程入口,预热装置的壳程中通入蒸汽对管程内的料浆进行预热;
所述高温加热装置包括多级高温加热段,每级高温加热段均为套管结构,所述预热装置的末端连接高温加热装置的管程入口,高温加热装置的壳程连接有热源,热源采用导热油或其它热源如高温蒸汽、熔盐等。经过高温加热装置处理后,在停留罐中,料浆中的可溶性氟化物浸出和除氰反应完成。
8.高温加热装置的管程末端连接有自蒸发装置,自蒸发装置主要是为了将浸出料浆由高压降到常压,以利于常压下的液固分离,自蒸发的同时释放二次蒸汽,二次蒸汽可用于预热料浆,最大限度的利用热能,降低大修渣脱毒处理过程中的能耗,更加优化了资源利用。自蒸发装置包括多级自蒸发器,自蒸发装置的级数比预热装置的级数多一级,除末级自蒸发器外,其他自蒸发器的蒸汽出口与预热装置的壳程连接。自蒸发器产生的二次蒸汽用来对预热装置管程中的料浆进行多级预热。
9.自蒸发装置的末端连接有固液分离装置,用来将自蒸发后的渣液分离。
10.另外,预热装置的每级预热段的壳程连接有冷凝水罐,自蒸发器的蒸汽出口通过管道与每级预热段的壳程连接,自蒸发器和每级预热段的壳程之间的管道上还设置有与冷凝水罐连接的冷凝水管。冷凝水罐用来接收预热装置的壳程和自蒸发器产生的冷凝水。
11.作为优选方案,高温加热装置和自蒸发装置之间还设置有停留罐,用以保证料浆反应的浸出时间。
12.作为优选方案,末端自蒸发器和固液分离装置之间设置有缓冲罐,用以对物料进行缓冲,这是因为自蒸发器的来料是连续的,而固液分离装置有可能是间断工作,如压滤机。
13.作为优选方案,固液分离装置为压滤机,也可采用其他固液分离装置,压滤机下设置有浸出液槽。
14.作为优选方案,所述预热装置包括二~八级预热段,高温加热装置包括二级高温加热段,自蒸发装置包括三~九级自蒸发器。
15.本发明具体操作流程如下:(1)粉磨:将铝电解槽大修渣磨细制粉,得到粒度《100目的大修渣细粉,然后将粉料送入混合槽。
16.(2)制浆:在混合槽内按照3:1~10:1的液固比加入清水进行混合搅拌制浆。
17.(3)浸出:将料浆用泵送往预热装置的管程,依次进行多级预热,将料浆温度升至140℃~180℃;然后经高温加热装置加热至200℃~300℃,高温加热装置热源采用导热油或其它热源如高温蒸汽、熔盐等;经过预热装置和高温加热装置处理后,可溶性氟化物浸出和除氰反应完成。
18.在进入自蒸发装置前,料浆进入停留罐;料浆在停留罐中的时间设置为40~100min。然后料浆再依次经多级自蒸发装置,将温度降到105℃,自蒸发的二次蒸汽用来预热料浆,产生的冷凝水可返回混合槽用于制浆。
19.在对料浆进行高温加热前先进行预热,是为了利用自蒸发器产生的二次蒸汽。将料浆加热至一定温度后再加热至200℃~300℃,可以减少高温加热装置的热源的消耗。
20.料浆在高温加热装置的管程中进行加热时,因温度为200℃~300℃,此时其中压力为1.5~8.5mpa。
21.(4)降温后的料浆进行液固分离,绝大部分naf进入到液相中,与常温浸出naf相比,浸出率可提高50%以上。在进行固液分离之前,料浆先进入缓冲罐进行缓冲。
22.本发明的有益效果为:本发明方法在高温高压的条件下一步就实现了除氰和脱氟的目标,且不需要其它药剂,仅需要消耗热能,且除氰脱氟后的滤饼不含氯盐,便于进一步综合利用。
23.本发明的处理系统经过多级预热后再加热至浸出温度,浸出料浆自蒸发产生的二次蒸汽用来对料浆进行多级预热,将热能的利用做到了最大化,生产运行消耗和成本也降到了最低。
附图说明
24.图1为本发明对铝电解槽大修渣进行脱毒的处理系统的结构示意图。
25.附图中,1为混合槽,2为预热装置,21为一级预热段,22为二级预热段,23为三级预热段,24为四级预热段,25为五级预热段,3为高温加热装置,31为导热油加热段,32为导热油炉,4为自蒸发装置,41为一级自蒸发器,42为二级自蒸发器,43为三级自蒸发器,44为四级自蒸发器,45为五级自蒸发器,46为六级自蒸发器,5为压滤机,6为浸出液槽,7为停留罐,8为缓冲槽,91为一号冷凝水罐,92为二号冷凝水罐,93为三号冷凝水罐,94为四号冷凝水罐,95为五号冷凝水罐。
具体实施方式
26.下面通过具体实施方式对本发明进行更加详细的说明,以便于对本发明技术方案的理解,但并不用于对本发明保护范围的限制。
27.实施例1如图1所示,本实施例的对铝电解槽大修渣进行脱毒的处理系统,包括:混合槽1、预热装置2、高温加热装置3、自蒸发装置4和固液分离装置;混合槽1用于对铝电解槽大修渣磨粉料和清水进行混合搅拌制浆;所述预热装置2包括五级预热段,每级预热段均为套管结构,混合槽1出料口连接预热装置2的管程入口,具体的,所述五级套管结构包括一级预热段21、二级预热段22、三级预热段23、四级预热段24、五级预热段25,混合槽1出料口依次连接五级预热段25、四级预热段24、三级预热段23、二级预热段22,一级预热段21;所述高温加热装置(3)包括二级高温加热段,每级高温加热段均为套管结构,一级预热段21的管程末端连接高温加热装置3的管程入口,高温加热装置3的壳程上连接有热源,经过高温加热装置处理后,料浆中的可溶性氟化物浸出和除氰反应完成。本实施例的热源采用导热油,具体的,本实施例可采用导热油加热炉32向二级导热油加热段31的壳程提供导热油。
28.高温加热装置3的末端连接有停留罐7,停留罐7的出料口连接自蒸发装置4,自蒸发装置4包括六级自蒸发器:一级自蒸发器41、二级自蒸发器42、三级自蒸发器43、四级自蒸发器44、五级自蒸发器45、六级自蒸发器46,一级自蒸发器41、二级自蒸发器42、三级自蒸发器43、四级自蒸发器44、五级自蒸发器45的蒸汽出口通过管道分别与一级预热段21、二级预热段22、三级预热段23、四级预热段24、五级预热段25的壳程连接。六级自蒸发器26的蒸汽
排入大气。
29.自蒸发装置4的末端连接有缓冲槽8,缓冲槽8的出料口连接固液分离装置,用来将自蒸发后的渣液分离。本实施例的固液分离装置为压滤机5,压滤机5下设置有浸出液槽6。
30.另外,预热装置2的每级预热段的壳程连接有冷凝水罐,具体的,一级预热段21、二级预热段22、三级预热段23、四级预热段24、五级预热段25分别连接一号冷凝水罐91、二号冷凝水罐92、三号冷凝水罐93、四号冷凝水罐94、五号冷凝水罐95,冷凝水罐之间相互连通,只对末端的五号冷凝水罐95的冷凝水进行回收即可,或者将五号冷凝水罐95的冷凝水返回混合槽1进行制浆。自蒸发器和预热段壳程之间的管道上还设置有与冷凝水罐连接的冷凝水管。
31.实施例2采用实施例1的处理系统进行铝电解槽大修渣脱毒处理的方法,包括:(1)粉磨:将铝电解槽大修渣磨细制粉(粒度《100目),常温下检测f-浸出浓度为2410mg/l,cn-浓度为7mg/l;将粉料送入混合槽。
32.(2)制浆:在混合槽内按照10:1的液固比加入清水进行混合搅拌制浆。
33.(3)浸出:将料浆用泵送往预热装置,依次经过五级预热将料浆温度升至160℃,然后经过二级高温加热段加热至220℃;在进入自蒸发装置前,料浆进入停留罐,料浆在停留罐中停留40min;接着料浆再依次经六级自蒸发,将温度降到105℃,自蒸发的二次蒸汽用来对预热装置中的料浆进行预热。
34.(4)降温后的料浆经缓冲槽缓冲后进行液固分离,绝大部分naf进入到液相中,检测f-浸出浓度为4761mg/l,cn-浓度为1mg/l,氟化钠的浸出率提高97%。
35.实施例3采用实施例1的处理系统进行铝电解槽大修渣脱毒处理的方法,包括:(1)粉磨:将大修渣磨细制粉(粒度《100目),常温下检测f-浸出浓度为5855mg/l,cn-浓度为12mg/l;将粉料送入混合槽。
36.(2)制浆:按照5:1的液固比加入清水进行混合搅拌制浆。
37.(3)浸出:在混合槽内将料浆用泵送往预热装置,依次经过五级预热将料浆温度升至150℃,然后经过二级高温加热段加热至200℃,在进入自蒸发装置前,料浆进入停留罐,料浆在停留罐中停留60min,料浆再依次经六级自蒸发,将温度降到105℃,自蒸发的二次蒸汽用来预热料浆。
38.(4)降温后的料浆经缓冲槽缓冲后进行液固分离,绝大部分naf进入到液相中,检测f-浸出浓度为9744mg/l,cn-浓度为2mg/l,氟化钠的浸出率提高66%。
39.实施例4采用实施例1的处理系统进行铝电解槽大修渣脱毒处理的方法,包括:(1)粉磨:将大修渣磨细制粉(粒度《100目),常温下检测f-浸出浓度为4335mg/l,cn-浓度为20mg/l;将粉料送入混合槽。
40.(2)制浆:在混合槽内按照8:1的液固比加入清水进行混合搅拌制浆。
41.(3)浸出:将料浆用泵送往预热装置,依次经过五级预热将料浆温度升至180℃,然后经过高温加热段加热至260℃,在进入自蒸发装置前,料浆进入停留罐,料浆在停留罐中
停留90min,料浆再依次经六级自蒸发,将温度降到105℃,自蒸发的二次蒸汽用来预热料浆。
42.(4)降温后的料浆经缓冲槽缓冲后进行液固分离,对液相进行检测,检测f-浸出浓度为7266mg/l,cn-浓度为0.5mg/l,氟化钠的浸出率提高67%。
43.以上所述之实施例,只是本发明的较佳实施例而已,并非限制本发明的实施范围,故凡依本发明专利范围所述的构造、特征及原理所做的等效变化或修饰,均应包括于本发明申请专利范围内。
再多了解一些
本文用于企业家、创业者技术爱好者查询,结果仅供参考。