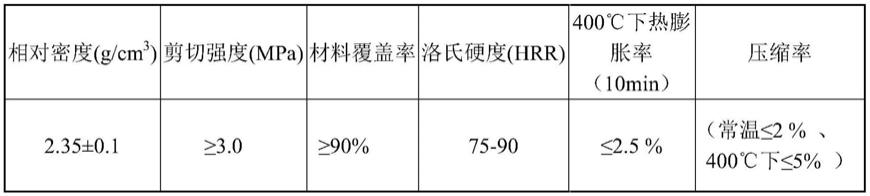
1.本发明涉及摩擦材料技术领域,具体涉及一种碳陶制动盘对偶刹车片用摩擦材料、制备方法及其用途。
背景技术:
2.近20年来,随着运输事业的蓬勃发展,摩擦材料发展尤为迅猛,出现了许多新型摩擦材料及制动盘,并广泛应用于各类工程机械和交通运输设备。21世纪科技发展的趋势是高速、环保和节能,为适应这一新形势发展的需要,对摩擦副材料的综合性能提出更高的要求。
3.减轻1kg的簧下质量的效能可以等同于减轻约10-15kg的簧上质量。在簧上质量一定的情况下,尽可能地减小簧下质量,可以提升车辆的加速,稳定性以及操控性。因此,轻量化制动盘得到广泛应用。
4.轻量化碳陶制动盘是应用广泛的一种轻量化制动盘。碳陶制动盘是选用长纤维进行三维编织针刺碳纤维预制体,使用高温化学气相沉积(cvi)生产工艺制成。碳陶制动盘重量仅为铸铁制动盘的30%左右,可以提高驾驶舒适度,提高启动加速,以及制动反应速度。碳陶制动盘具有耐磨损,抗氧化,不生锈,无热衰退,无污染,制动刹车距离缩短30%,提高安全系数等优越特性,正常行驶里程可达30万公里。
5.然而传统的刹车片匹配的多是灰铸铁制动盘或铸钢制动盘,与轻量化碳陶制动盘匹配性不好,而且与灰铸铁制动盘或铸钢制动盘组成的摩擦副在制动过程中,还具有因制动盘易锈蚀、高温制动过程中制动盘基体金属转移粘结等原因导致制动盘耐热性低和使用寿命短等缺陷。
技术实现要素:
6.因此,本发明要解决的技术问题在于克服现有技术中刹车片与碳陶制动盘匹配性不好缺陷,从而提供一种碳陶制动盘对偶刹车片用摩擦材料、制备方法及其用途。
7.为了解决上述技术问题,本发明采用了如下技术方案:
8.一种碳陶制动盘对偶刹车片用摩擦材料,按照重量份数计,包括:
9.(a)碳纤维2~4重量份,
10.(b)微孔金属陶瓷8-13重量份,
11.(c)硅酸铝纤维5~10重量份,
12.(d)双马来酰亚胺树脂8~12重量份,
13.(e)碳化硅2~4重量份,和
14.(f)钛酸铝6~11重量份。
15.所述碳纤维的含量为2~4重量份,例如2.2重量份、2.4重量份、2.6重量份、2.8重量份、3重量份、3.2重量份、3.4重量份、3.6重量份或4重量份。碳纤维的耐热性高,其可以增强基体、提高耐热性、降低摩擦系数并提高刹车片剪切强度。可选的,碳纤维可为短切碳纤
维,可选的,短切碳纤维的长度可为2.5-4mm。
16.本发明所述微孔金属陶瓷为本领域常规现有微孔金属陶瓷,本发明不对微孔金属陶瓷的具体成分做具体限定,可选的,所述微孔金属陶瓷,以质量分数计,包括如下组分:3-4%sio2,7-8%al2o3,87-88%fe2o3,0.05-0.1%cao,0.05-0.1%mgo,0.1-0.8%c,其它为不可避免的杂质。进一步优选的,所述微孔金属陶瓷,以质量分数计,包括如下组分:3.61%sio2,7.28%al2o3,87.62%fe2o3,0.092%cao,0.069%mgo,0.54%c,其它为不可避免的杂质。上述提供的微孔金属陶瓷其比重为1.5-2.0g/cm3,莫氏硬度为2-3,进一步优选的,其粒径可为30-150目,烧失量可达3.3%,残余量可达96.7%。进一步,本发明所述的微孔金属陶瓷的制备方法为本领域的常规制备方法,在此不再赘述。
17.微孔金属陶瓷材料作为耐磨材料,具有耐热性好的优点,并可以提高刹车片摩擦系数。适量的微孔金属陶瓷材料与碳陶盘匹配效果较好,摩擦性能稳定。如果微孔金属陶瓷材料的含量过低,则增磨作用不明显,如果含量过高,则会降低刹车片剪切强度。
18.所述硅酸铝纤维的含量为5~10重量份,例如为5重量份、5.5重量份、6重量份、6.5重量份、7重量份、7.5重量份、8重量份、8.5重量份、9重量份、9.5重量份或10重量份。硅酸铝纤维的耐热性高,其可以增强基体、提高耐热性、降低摩擦系数并提高刹车片剪切强度。如果硅酸铝纤维的含量过低或者过高,均无法有效地提供足够的剪切强度。
19.所述双马来酰亚胺树脂的含量为8~12重量份,例如为8重量份、8.5重量份、9重量份、9.5重量份、10重量份、10.5重量份、11重量份、11.5重量份或12重量份。所述双马来酰亚胺作为粘结剂,主要起粘结的作用,并提供刹车片适宜的硬度。如果双马来酰亚胺的含量过低,则无法起到粘结作用,含量过高,则刹车片整体耐热性降低,且刹车片硬度会过高。可选的,所述双马来酰亚胺树脂的熔点为152~158℃,酸值为<1.0kohmg/g。
20.所述碳化硅的含量为2~4重量份,例如2.2重量份、2.4重量份、2.6重量份、2.8重量份、3重量份、3.2重量份、3.4重量份、3.6重量份或4重量份。碳化硅作为耐磨材料,可以提高刹车片摩擦系数。如果碳化硅的含量过低,则无法有效增加刹车片摩擦系数,如果碳化硅的含量过高,则会提高制动盘磨损。
21.所述钛酸铝的含量为6~11重量份,例如为6重量份、6.5重量份、7重量份、7.5重量份、8重量份、8.5重量份、9重量份、9.5重量份、10重量份、10.5重量份或11重量份。钛酸铝作为耐磨材料,可以提高刹车片摩擦系数。如果钛酸铝的含量过低,则无法有效增加刹车片摩擦系数,如果钛酸铝的含量过高,则会提高制动盘磨损。
22.所述“包括”意指,所述摩擦材料除上述组分外,还可以包括其他任选地组分,所述组分赋予所述摩擦材料附加的效果。
23.在本发明一种优选地实施方式中,所述摩擦材料包括(g)弹性颗粒,含量为5~10重量份,例如为5重量份、5.5重量份、6重量份、6.5重量份、7重量份、7.5重量份、8重量份、8.5重量份、9重量份、9.5重量份或10重量份。弹性颗粒具有调节刹车片硬度、压缩性能及提高孔隙率的作用,且耐热性优于直接添加橡胶组分。如果弹性颗粒的含量小于5重量份,则不能起到调节刹车片硬度,且稳定摩擦性能的作用,如果弹性颗粒的重量大于10重量份,则刹车片耐热性降低。
24.弹性颗粒,意指(橡胶)弹性体颗粒,典型但非限制性的弹性颗粒,以各组分占质量百分比计,包括:耐热硅橡胶10~25%、四氧化三铁2~10%、纤维素纤维5~15%、导热氧化
铝1~5%、鳞片石墨40~50%以及碳酸钙晶须10~20%。上述弹性颗粒可通过将原料混合然后密炼成型的方式得到。示例性的耐热硅橡胶如高温硫化硅胶htv。
25.典型但非限制性的弹性颗粒,以各组分占质量百分比计,包括:耐热硅橡胶18%、四氧化三铁5%、纤维素纤维12%、导热氧化铝3%、鳞片石墨46%以及碳酸钙晶须16%。所述弹性颗粒制备方法包括:采用密炼机经80℃,0.5mpa压强下捏合10min,形成块状混合物,然后经破碎机破碎加工成3-5mm直径颗粒。
26.在本发明一种优选地实施方式中,所述摩擦材料包括(h)腰果壳油摩擦粉,含量为6~10重量份,例如为6重量份、6.5重量份、7重量份、7.5重量份、8重量份、8.5重量份、9重量份、9.5重量份或10重量份。腰果壳油摩擦粉的作用主要是稳定摩擦系统、降低刹车片密度以及提高孔隙率。如果腰果壳油摩擦粉的含量过低,则刹车片孔隙率较低,对衬片噪音产生不良影响,含量过高,则孔隙率过高,降低刹车片剪切强度。
27.在本发明一种优选地实施方式中,所述摩擦材料包括(i)氢氧化钙,含量为10~20重量份,例如11重量份、12重量份、13重量份、14重量份、15重量份、16重量份、17重量份、18重量份、19重量份或20重量份。所述氢氧化钙的作用主要是中和总体刹车片酸度、调节刹车片酸碱度以及稳定刹车片摩擦系数。如果氢氧化钙的含量过低,则无法有限中和刹车片酸度,如果氢氧化钙的含量过高,则刹车片在高温制动时在摩擦界面产生水蒸气较多,会降低瞬时摩擦系数。在本发明一种优选地实施方式中,所述摩擦材料包括(j)芳纶浆粕,所述芳纶浆粕的含量为1~3重量份,例如为1.2重量份、1.4重量份、1.6重量份、1.8重量份、2重量份、2.2重量份、2.4重量份、2.6重量份、2.8重量份或3重量份。所述芳纶浆粕的主要作用是增强基体以及提高刹车片的剪切强度。如果芳纶浆粕的含量过高,则混合料易结团,且降低刹车片密度,影响整体性能,如果含量过低,则不能起到增强产品剪切强度的作用。
28.在本发明一种优选地实施方式中,所述摩擦材料包括(k)萤石,含量为9~12重量份,例如为9.5重量份、10重量份、10.5重量份、11重量份、11.5重量份或12重量份。所述萤石作为耐磨填料,可以提高刹车片摩擦系数。如果萤石含量过低,无法起到增加摩擦系数的作用,如果萤石含量过高,则会提高制动盘磨损。
29.在本发明一种优选地实施方式中,所述摩擦材料包括(m)紫铜纤维,含量为10~15重量份,例如10.5重量份、11重量份、11.5重量份、12重量份、12.5重量份、13重量份、13.5重量份、14重量份、14.5重量份或15重量份。紫铜纤维的耐热性高,其可以增强基体、提高耐热性、降低摩擦系数并提高刹车片剪切强度。如果紫铜纤维的含量过低或者过高,均无法有效地提供足够的导热性并稳定摩擦系数。紫铜纤维含量过低,刹车片导热率降低,不能及时将摩擦界面较高的瞬时温度传导散热,会导致刹车片表面烧蚀。紫铜纤维含量过高,会降低摩擦系数,并将过多热量传导至刹车片钢背,进而传导至制动卡钳,若温度过高,则卡钳内制动液气化将不产生制动力,影响制动效果。在本发明一种优选地实施方式中,碳陶制动盘对偶刹车片用摩擦材料,按重量份数包括:
30.(a)碳纤维2~4重量份,
31.(b)微孔金属陶瓷8-13重量份,
32.(c)硅酸铝纤维5~10重量份,
33.(d)双马来酰亚胺树脂8~12重量份,
34.(e)碳化硅2~4重量份,
35.(f)钛酸铝6~11重量份,
36.(g)弹性颗粒5~10重量份,
37.(h)腰果壳油摩擦粉6~10重量份,
38.(i)氢氧化钙10~20重量份,
39.(j)芳纶浆粕1~3重量份,
40.(k)萤石9~11重量份,和
41.(m)紫铜纤维10~15重量份。
42.采用该优选方案的刹车片摩擦系数稳定,刹车片及制动盘磨损低,摩擦副整体耐热性更高。
43.本发明还提供了一种由如上所述的摩擦材料制备而成的碳陶制动盘对偶刹车片。
44.本发明还提供了一种如上所述的碳陶制动盘对偶刹车片的制备方法,包括如下步骤:
45.将混合后的各组分进行压制以及固化,得到碳陶制动盘对偶刹车片。
46.在本发明一种优选地实施方式中,将各组分混合,混合时间为30~60min,可以完成各组分的充分混合,得到混合后的各组分。
47.在本发明一种优选地实施方式中,将混合后的各组分进行压制,压制压力为15~20mpa,压制时间为350-420s。所述压制例如可以在模具中进行。
48.压制的目的是要使摩擦材料按模具的形状压塑成形,同时保证材料压制后密度在要求范围2.85
±
0.1g/cm3之内。在本发明一种优选地实施方式中,固化温度为190~230℃,固化时间为8~12h。
49.本发明还提供了一种摩擦副,包括如上所述的碳陶制动盘对偶刹车片和碳陶制动盘。
50.本发明还提供了一种汽车,包括如上所述的摩擦副。
51.与现有技术相比,本发明具有如下有益效果:
52.本发明通过采用双马来酰亚胺树脂、微孔金属陶瓷、碳纤维、钛酸铝、硅酸铝纤维和碳化硅相互配合,使得到的刹车片的摩擦和磨损性能达到最优,刹车片系数在高温情况下可以在0.30以上,而且,与碳陶制动盘匹配性优异。
53.此外,所述刹车片抗热裂性和耐磨性好,磨损率低,进而延长了使用寿命。而且,所述刹车片能够提供卓越的制动性能,具有噪声小、振动低等特性,经久耐用,并且只生成极少的粉尘,不会影响车辆轮毂美观。而且,所述刹车片还可以为碳陶制动盘提供更高静摩擦性能,这对于斜坡驻车尤为有益。所述刹车片产品与行车制动器、驻车制动器均配合良好。
54.所述刹车片不仅适用于新能源车辆,与赛车制动系统配合也具有良好表现。
55.而且,本发明实现了制动摩擦副轻量化,解决了灰铸铁或铸钢制动盘摩擦副制动过程中制动盘锈蚀问题,完全避免刹车片在与普通铸铁或铸钢制动盘高温制动过程中基体金属的转移、粘接问题,实现有机碳陶刹车片与轻量化碳陶制动盘的匹配,并延长制动盘的使用寿命,实现绿色环保以及轻量化目标。
56.所述刹车片具体性能如下所示:
57.物理性能:所述碳陶制动盘对偶刹车片物理性能如表1所示:
58.表1
[0059][0060]
摩擦性能及nvh性能如下所示:
[0061]
摩擦性能符合sae j2522等有关标准,摩擦系数:名义摩擦系数0.35-0.45,最小摩擦系数0.30;nvh性能按照sae j2521标准进行,达到a级;
[0062]
使用寿命:正常工作状态下产品使用寿命达到≥6万公里。
[0063]
试验温度:所述碳陶制动盘对偶刹车片能耐受800℃,具有优异的耐热性能。
具体实施方式
[0064]
实施例1
[0065]
一种碳陶制动盘对偶刹车片用摩擦材料,包括如下原料:
[0066]
(a)长度3mm的短切碳纤维(型号t300)4kg,
[0067]
(b)微孔金属陶瓷10kg,
[0068]
(c)硅酸铝纤维8kg,
[0069]
(d)双马来酰亚胺树脂10kg,熔点为153℃,酸值为0.8kohmg/g,
[0070]
(e)碳化硅3kg,
[0071]
(f)钛酸铝9kg,
[0072]
(g)弹性颗粒7kg,
[0073]
(h)腰果壳油摩擦粉8kg,
[0074]
(i)氢氧化钙15kg,
[0075]
(j)芳纶浆粕2kg,型号hp300;厂家常州赛邦新材料科技有限公司,
[0076]
(k)萤石11kg,和
[0077]
(m)紫铜纤维13kg。
[0078]
所述微孔金属陶瓷,以质量分数计,由如下组分组成:3.61%sio2,7.28%al2o3,87.62%fe2o3,0.092%cao,0.069%mgo,0.54%c,其它为不可避免的杂质。
[0079]
弹性颗粒,以各组分占质量百分比计,包括:耐热硅橡胶htv18%、四氧化三铁5%、纤维素纤维12%、导热氧化铝3%、鳞片石墨46%以及碳酸钙晶须16%。所述弹性颗粒制备方法包括:采用密炼机经80℃,0.5mpa压强下捏合10min,形成块状混合物,然后经破碎机破碎加工成3-5mm直径颗粒。
[0080]
采用如上所述的摩擦材料得到的刹车片的制备方法包括:
[0081]
将各原料混合,混合时间为30min,可以完成各原料的充分混合,得到混合后原料;
[0082]
将混合后原料置于模具中压制,压制压力为15mpa,压制时间为400s,将压制后的毛坯加热至230℃固化9h,得到碳陶制动盘对偶刹车片。
[0083]
对得到的刹车片进行性能测试,具体如下:
[0084]
(1)物理性能,如表2所示
[0085]
表2
[0086][0087]
(2)摩擦性能及nvh性能:
[0088]
摩擦性能按照sae j2522标准要求,进行台架试验,试验结果如表3所示:名义摩擦系数0.431,最小摩擦系数0.332;nvh性能按照sae j2521标准进行,达到a级;
[0089]
表3
[0090][0091]
(3)试验温度:刹车片能耐受800℃。按照sae j2522标准进行台架试验,其中衰退试验最高温度超过800℃,衬片摩擦系数≥0.30,衬片外观良好,无裂纹,无金属镶嵌。
[0092]
(4)磨损性能:如表4所示:
[0093]
表4
[0094]
[0095]
实施例2
[0096]
一种碳陶制动盘对偶刹车片用摩擦材料,包括如下原料:
[0097]
(a)长度3mm的短切碳纤维(型号t300)3kg,
[0098]
(b)微孔金属陶瓷10kg,
[0099]
(c)硅酸铝纤维5kg,
[0100]
(d)双马来酰亚胺树脂12kg,熔点为153℃,酸值为0.8kohmg/g,
[0101]
(e)碳化硅4kg,
[0102]
(f)钛酸铝6kg,
[0103]
(g)弹性颗粒5kg,
[0104]
(h)腰果壳油摩擦粉10kg,
[0105]
(i)氢氧化钙20kg,
[0106]
(j)芳纶浆粕3kg,型号hp300;厂家常州赛邦新材料科技有限公司,
[0107]
(k)萤石11kg,和
[0108]
(m)紫铜纤维10kg。
[0109]
所述微孔金属陶瓷,以质量分数计,由如下组分组成:3.61%sio2,7.28%al2o3,87.62%fe2o3,0.092%cao,0.069%mgo,0.54%c,其它为不可避免的杂质。
[0110]
弹性颗粒,以各组分占质量百分比计,包括:耐热硅橡胶htv18%、四氧化三铁5%、纤维素纤维12%、导热氧化铝3%、鳞片石墨46%以及碳酸钙晶须16%。所述弹性颗粒制备方法包括:采用密炼机经80℃,0.5mpa压强下捏合10min,形成块状混合物,然后经破碎机破碎加工成3-5mm直径颗粒。
[0111]
采用如上所述的摩擦材料得到的刹车片的制备方法包括:
[0112]
将各原料混合,混合时间为40min,可以完成各原料的充分混合,得到混合后原料;
[0113]
将混合后原料置于模具中压制,压制压力为20mpa,压制时间为350s,将压制后的毛坯加热至190℃固化12h,得到碳陶制动盘对偶刹车片。
[0114]
对得到的刹车片进行性能测试,具体如下:
[0115]
(1)物理性能,如表5所示
[0116]
表5
[0117][0118]
(2)摩擦性能及nvh性能:
[0119]
摩擦性能按照sae j2522标准要求,进行台架试验,试验结果如表6所示:名义摩擦系数0.434,最小摩擦系数0.339;nvh性能按照sae j2521标准进行,达到a级;
[0120]
表6
[0121][0122]
(3)试验温度:刹车片能耐受800℃。按照sae j2522标准进行台架试验,其中衰退试验最高温度超过800℃,衬片摩擦系数≥0.30,衬片外观良好,无裂纹,无金属镶嵌。
[0123]
(4)磨损性能:如表7所示:
[0124]
表7
[0125][0126]
实施例3
[0127]
一种碳陶制动盘对偶刹车片用摩擦材料,包括如下原料:
[0128]
(a)长度3mm的短切碳纤维(型号t300)2kg,
[0129]
(b)微孔金属陶瓷10kg,
[0130]
(c)硅酸铝纤维10kg,
[0131]
(d)双马来酰亚胺树脂8kg,熔点为153℃,酸值为0.8kohmg/g,
[0132]
(e)碳化硅2kg,
[0133]
(f)钛酸铝11kg,
[0134]
(g)弹性颗粒10kg,
[0135]
(h)腰果壳油摩擦粉6kg,
[0136]
(i)氢氧化钙16kg,
[0137]
(j)芳纶浆粕1kg,型号hp300;厂家常州赛邦新材料科技有限公司,
[0138]
(k)萤石9kg,和
[0139]
(m)紫铜纤维15kg。
[0140]
所述微孔金属陶瓷,以质量分数计,由如下组分组成:3.61%sio2,7.28%al2o3,87.62%fe2o3,0.092%cao,0.069%mgo,0.54%c,其它为不可避免的杂质。
[0141]
弹性颗粒,以各组分占质量百分比计,包括:耐热硅橡胶htv18%、四氧化三铁5%、纤维素纤维12%、导热氧化铝3%、鳞片石墨46%以及碳酸钙晶须16%。所述弹性颗粒制备方法包括:采用密炼机经80℃,0.5mpa压强下捏合10min,形成块状混合物,然后经破碎机破碎加工成3-5mm直径颗粒。
[0142]
采用如上所述的摩擦材料得到的刹车片的制备方法包括:
[0143]
将各原料混合,混合时间为60min,可以完成各原料的充分混合,得到混合后原料;
[0144]
将混合后原料置于模具中压制,压制压力为18mpa,压制时间为420s,将压制后的毛坯加热至220℃固化8h,得到碳陶制动盘对偶刹车片。
[0145]
对得到的刹车片进行性能测试,具体如下:
[0146]
(1)物理性能,如表8所示
[0147]
表8
[0148][0149]
(2)摩擦性能及nvh性能:
[0150]
摩擦性能按照sae j2522标准要求,进行台架试验,试验结果如表9所示:名义摩擦系数0.429,最小摩擦系数0.341;nvh性能按照sae j2521标准进行,达到a级;
[0151]
表9
[0152][0153][0154]
(3)试验温度:刹车片能耐受800℃。按照sae j2522标准进行台架试验,其中衰退试验最高温度超过800℃,衬片摩擦系数≥0.30,衬片外观良好,无裂纹,无金属镶嵌。
[0155]
(4)磨损性能:如表10所示:
[0156]
表10
[0157][0158]
对比例1
[0159]
其余与实施例1相同,除将双马来酰亚胺树脂替换为酚醛树脂pf6130,购自山东圣泉新能源科技有限公司,聚速65-95s/150℃,流动度为18-25mm/125℃,游离酚为≤1.0%。
[0160]
对比例2
[0161]
其余与实施例1相同,除将弹性颗粒替换为粉末丁腈橡胶型号pnbr-60,购自盛东科技有限公司。
[0162]
对比例3
[0163]
其余与实施例1相同,除将硅酸铝纤维含量调整为3kg,将钛酸铝含量调整为14kg。
[0164]
对比例4
[0165]
其余与实施例1相同,除将双马来酰亚胺的含量调整为6kg,腰果壳油摩擦粉含量
调整为12kg。
[0166]
对对比例1-4的刹车片进行性能测试,具体如下:
[0167]
(1)物理性能,如表11所示
[0168]
表11
[0169][0170]
(2)摩擦性能及nvh性能:
[0171]
摩擦性能按照sae j2522标准要求,进行台架试验,如表12所示,nvh性能按照sae j2521标准进行,达到bb级;
[0172]
表12
[0173]
对比例名义摩擦系数最小摩擦系数对比例10.3600.251对比例20.3810.270对比例30.4270.292对比例40.4050.306
[0174]
(3)试验温度:刹车片能耐受650℃,高于650℃时,摩擦系数降低至0.30以下。
[0175]
(4)磨损性能,如表13所示
[0176]
表13
[0177][0178]
注:
[0179]
所述相对密度的测试方法依据gb/t 1033.1进行;
[0180]
所述剪切强度的测试方法依据gb/t 22309进行;
[0181]
所述材料覆盖率的测试方法为:剪切强度试验后,摩擦材料粘在钢背上的面积百分比,覆盖率越高越好;
[0182]
所述洛氏硬度的测试方法依据gb/t 5766进行;
[0183]
所述热膨胀率的测试方法依据gb/t 22310进行;
[0184]
所述压缩应变的测试方法依据gb/t 22311进行。
[0185]
显然,上述实施例仅仅是为清楚地说明所作的举例,而并非对实施方式的限定。对于所属领域的普通技术人员来说,在上述说明的基础上还可以做出其它不同形式的变化或变动。这里无需也无法对所有的实施方式予以穷举。而由此所引伸出的显而易见的变化或变动仍处于本发明创造的保护范围之中。
再多了解一些
本文用于企业家、创业者技术爱好者查询,结果仅供参考。