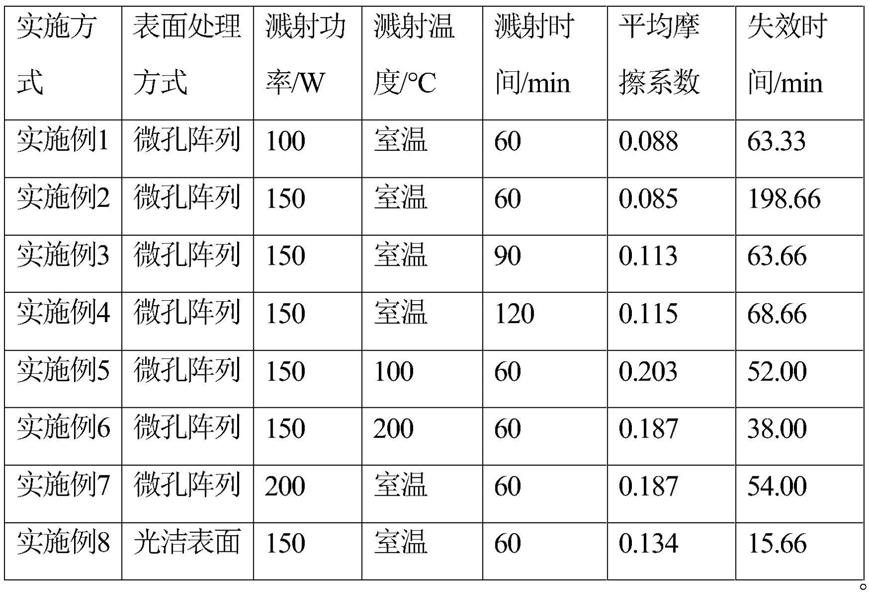
1.一种轴承钢表面固载二硫化钼薄膜的技术,属于金属材料表面改性技术领域。
背景技术:
2.高碳铬(gcr15)轴承钢自诞生之日起就因其抗疲劳性能及耐磨性好,热处理方法简单等优点成为世界上第一代专用的轴承钢,多年来受到国内外专家学者的广泛关注。但是其中存在的问题仍然不能忽视,国内轴承生产主要集中在中低端轴承产品,而在航空航天等领域要求轴承具有良好的耐磨性及更长的使用寿命。随着科学技术的发展,轴承所工作的环境越来越苛刻,对其工作性能要求越来越高。机械系统的摩擦性能对其提高承载,可靠运行及延长服役寿命起到了重要作用,特别是在航空航天领域,对于在真空环境下摩擦及润滑尤其重要。因此,为了减小各种零部件滑动接触表面的摩擦磨损,通过材料改性、润滑剂添加及表面工程技术等方法提高材料的摩擦学性能就显得非常重要。二硫化钼(mos2)具有六方层状(各向异性)的晶体结构,层间以弱的范德瓦尔斯力结合,剪切强度低。它作为良好的固体润滑剂,能大大降低工件表面的摩擦和磨损,延长工件的使用寿命,广泛应用于宇航工程、机械工业制造、电子等方面。将固体润滑剂mos2引入到轴承钢表面可以降低其表面的摩擦系数,磁控溅射是一种非常有效的物理气相沉积方法,其制备mos2薄膜具有沉积速率快、沉积温度低、成膜质量高、可控性好、不影响基材性能等优点,所以很适于金属表面改性。由于轴承钢表面通过抛磨工艺之后,表面光滑,粗糙度较低,因此仅通过磁控溅射在其表面沉积一层mos2时结合力较低,在摩擦过程中薄膜容易过早失效,导致轴承等零件寿命大大缩短,为了解决这个问题,本研究首先在轴承钢表面通过脉冲激光器加工出一系列的微孔结构以增加材料表面的粗糙度,进而增强轴承钢表面mos2的稳定性。同时在摩擦过程中,通过微孔可以存储磨屑,挤出固载的二硫化钼来补充润滑,起到进一步延长使用寿命的作用。同时通过调控磁控溅射的参数,在室温至200℃温度范围内进行mos2的沉积,为了增加轴承钢表面固体润滑材料的量,将沉积时间延长至60min-120min。创新性的在轴承钢表面获得了性能优异的减磨薄膜。由于轴承钢应用前景较为广泛,故深入研究采用脉冲激光器制造微孔阵列固载mos2,获得更优异的摩擦学性能,既具有重要的科学意义,也具有广泛的应用前景。
技术实现要素:
3.本发明解决的是一种轴承钢表面固载mos2薄膜的新技术,属于金属材料表面改性技术领域。首先使用脉冲激光器在轴承钢表面制备微孔阵列,然后利用射频磁控溅射技术将mos2固体润滑剂引入到轴承钢表面。经固载后的轴承钢表面的摩擦系数最低可降至0.10,远低于光滑表面轴承钢的摩擦系数1.10。固体润滑剂沉积在轴承钢表面,摩擦失效时间为198.66分钟,光滑轴承钢表面摩擦时间失效时间为15.66分钟。本发明提供的轴承钢表面微孔固载mos2的技术,可以大幅降低轴承钢表面的摩擦系数,提高固体润滑材料的稳定性。本研究将为航空航天用轴承提供一种固体润滑涂层固载及涂层制备结合的新型方式,
为解决轴承因过早薄膜损坏提供一条新的有效措施。
4.本发明所提供的制备方法,其特征在于,包括以下步骤:
5.1)将淬火轴承钢打磨后镜面抛光,用丙酮超声清洗除掉表面油污,再放入酒精中清洗,干燥后待用;
6.2)预净化处理后的淬火轴承钢经过脉冲激光器进行微孔阵列制备,抛光除掉表面氧化层,后通过酒精超声清洗除掉表面残渣,干燥待用;3)以具有微孔阵列的淬火轴承钢表面作为基体,mos2为靶材,采用射频电源进行溅射,经过抽真空、加热、保温、预溅射、溅射,在多孔阵列结构轴承钢上溅射得到mos2薄膜,冷却至室温取出。
7.其中步骤3)进行溅射时,背底真空度为5x10-4
,预溅射时间180s,氩气压力为1pa,加热温度为室温-200℃,溅射功率为100w-200w,溅射时间为60min-120min。
8.本发明的有益效果是:
9.采用脉冲激光器在轴承钢基体上制备结构可控、排列高度有序的轴承钢微孔阵列结构,采用射频磁控溅射的方法将mos2颗粒固载到轴承钢微孔阵列上,本发明采用微孔结构和溅射mos2颗粒相结合使得mos2薄膜在轴承钢表面上固载量更多及更牢固。所制备的样品进行力学性能测试,其中摩擦系数最低可达到0.05,远低于光滑表面轴承钢的摩擦系数1.10。将固体润滑剂直接沉积在轴承钢表面,在5n载荷下,未含微孔阵列表面摩擦失效时间为15.66分钟,固体润滑剂沉积在微孔阵列表面上摩擦失效时间为198.66分钟,有效降低了摩擦系数。本发明的技术方案重复性好,效果优异明显。本发明得到的mos2颗粒会沉积在微孔里面,固载更多的mos2。采用本发明方法可以在轴承等部件进行表面处理,用于减小摩擦,同时增加强度。
附图说明
10.图1:实施例2通过脉冲激光器进行微孔阵列制备后的淬火轴承钢表面宏观形貌图。
11.图2:实施例2通过脉冲激光器进行微孔阵列制备后的淬火轴承钢表面微观形貌图。
12.图3:实施例2磁控溅射二硫化钼后表面扫描电子显微镜图(sem)。
13.图4:实施例2磁控溅射二硫化钼后表面x射线衍射图(xrd)。
14.图5:实施例2与实施例8摩擦系数对比图。
具体实施方式
15.先做表面处理即将淬火态轴承钢做镜面抛光处理,用丙酮超声清洗除掉表面油污,再放入酒精中超声清洗,然后干燥处理。通过脉冲激光器进行微孔制备再抛光除掉表面氧化层,微孔孔径微80微米,间距200微米,深度8微米左右。具体激光参数为:波长1064ns,频率20khz,扫描速度100mm/s,功率20%。最后通过循环摩擦实验:通过球载往复式测试仪(cft-1材料表面综合性能测试仪)在空气中测试摩擦学性质。在测试仪中使用设备所配的轴承钢球,其硬度为60-65hrc,测试设定载荷5n、转速500r/m、摩擦半径6mm。所有数据至少是三个实验结果的平均值。当润滑失效时,摩擦试验暂停。以下实施例除实施例8不进行微孔制备外均相同。
16.实施例1:
17.将φ25mm*5mm的淬火轴承钢进行镜面抛光处理,去除表面杂质和氧化皮。通过脉冲激光器进行微孔制备再抛光除掉表面氧化层。将预处理完成后的淬火轴承钢片放入磁控溅射覆膜系统中,溅射功率定为100w,溅射温度设置为室温,溅射时间为60min,背底真空度为5
×
10-4
pa,预溅射时间为180s,氩气压力为1pa,经过抽真空、预溅射、调压、溅射,冷却至室温取出。
18.实施例2:
19.将φ25mm*5mm的淬火轴承钢进行镜面抛光处理,去除表面杂质和氧化皮。通过脉冲激光器进行微孔制备再抛光除掉表面氧化层。将预处理完成后的淬火轴承钢片放入磁控溅射覆膜系统中,溅射功率定为150w,溅射温度设置为室温,溅射时间为60min,背底真空度为5
×
10-4
pa,预溅射时间为180s,氩气压力为1pa,经过抽真空、预溅射、调压、溅射,冷却至室温取出。
20.实施例3:
21.将φ25mm*5mm的淬火轴承钢进行镜面抛光处理,去除表面杂质和氧化皮。通过脉冲激光器进行微孔制备再抛光除掉表面氧化层。将预处理完成后的淬火轴承钢片放入磁控溅射覆膜系统中,溅射功率定为150w,溅射温度设置为室温,溅射时间为90min,背底真空度为5
×
10-4
pa,预溅射时间为180s,氩气压力为1pa,经过抽真空、预溅射、调压、溅射,冷却至室温取出。
22.实施例4:
23.将φ25mm*5mm的淬火轴承钢进行镜面抛光处理,去除表面杂质和氧化皮。通过脉冲激光器进行微孔制备再抛光除掉表面氧化层。将预处理完成后的淬火轴承钢片放入磁控溅射覆膜系统中,溅射功率定为150w,溅射温度设置为室温,溅射时间为120min,背底真空度为5
×
10-4
pa,预溅射时间为180s,氩气压力为1pa,经过抽真空、预溅射、调压、溅射,冷却至室温取出。
24.实施例5:
25.将φ25mm*5mm的淬火轴承钢进行镜面抛光处理,去除表面杂质和氧化皮。通过脉冲激光器进行微孔制备再抛光除掉表面氧化层。将预处理完成后的淬火轴承钢片放入磁控溅射覆膜系统中,溅射功率定为150w,溅射温度设置为100℃,溅射时间为60min,背底真空度为5
×
10-4
pa,预溅射时间为180s,氩气压力为1pa,经过抽真空、加热、预溅射、调压、溅射,冷却至室温取出。
26.实施例6:
27.将φ25mm*5mm的淬火轴承钢进行镜面抛光处理,去除表面杂质和氧化皮。通过脉冲激光器进行微孔制备再抛光除掉表面氧化层。将预处理完成后的淬火轴承钢片放入磁控溅射覆膜系统中,溅射功率定为150w,溅射温度设置为200℃,溅射时间为60min,背底真空度为5
×
10-4
pa,预溅射时间为180s,氩气压力为1pa,经过抽真空、加热、预溅射、调压、溅射,冷却至室温取出。
28.实施例7:
29.将φ25mm*5mm的淬火轴承钢进行镜面抛光处理,去除表面杂质和氧化皮。通过脉冲激光器进行微孔制备再抛光除掉表面氧化层。将预处理完成后的淬火轴承钢片放入磁控
溅射覆膜系统中,溅射功率定为200w,溅射温度设置为室温,溅射时间为60min,背底真空度为5
×
10-4
pa,预溅射时间为180s,氩气压力为1pa,经过抽真空、预溅射、调压、溅射,冷却至室温取出。
30.实施例8:
31.将φ25mm*5mm的淬火轴承钢进行镜面抛光处理,去除表面杂质和氧化皮。将预处理完成后的淬火轴承钢片放入磁控溅射覆膜系统中,溅射功率定为150w,溅射温度设置为室温,溅射时间为60min,背底真空度为5
×
10-4
pa,预溅射时间为180s,氩气压力为1pa,经过抽真空、预溅射、调压、溅射,冷却至室温取出。
32.表1实施例参数汇总表
33.
再多了解一些
本文用于企业家、创业者技术爱好者查询,结果仅供参考。