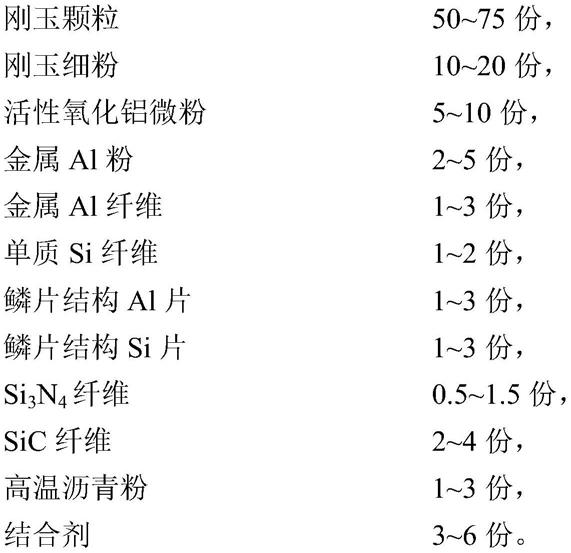
1.本发明涉及炼钢用耐火材料技术领域,具体涉及一种高导热不烧氧化铝(al2o3)-碳(c)滑板砖及其制备方法。
背景技术:
2.滑动水口耐材是钢包控流系统的关键元件,起着控制和调节钢水流量的作用,其使用过程中工况条件非常苛刻,主要表现在:1)长时间和高温钢水接触,受到不同化学成分钢水氧化、冲刷和侵蚀作用;2)浇钢过程中温度梯度达到1000℃左右的急剧变化,造成材料内部产生巨大热应力作用;3)通过开闭滑板来控制钢水流量,滑板来回拉动过程中板面间存在很大磨损。以上工况条件要求滑板具有非常优异的中高温强度、抗氧化性能、耐磨性、抗热震稳定性能、抗钢水侵蚀性能等。
3.根据国内外钢厂的使用经验,大中型钢包一般使用高温烧成铝锆碳滑板,滑板使用寿命一般在3-4次,但这种滑板生产过程中一般需要经过1300℃以上高温烧成处理,其制作工序和生产周期长,合格率相对较低,且高温烧成过程中能耗很大,不符合国家施行“碳达峰、碳中和”政策的发展方向。
4.近年来不烧滑板作为一种新材质体系逐步受到了重视,目前在小型钢包(《150吨)上得到了推广使用,但使用寿命较低,一般为1~2次,使用过程中存在的主要问题如下:
5.1)中温强度低:滑板使用过程中结合剂发生裂解,降低了材质内部结合强度;
6.2)板面拉毛掉块问题:滑板浇钢过程中铸孔周边接触钢水,其温度较高,可以烧结产生较大强度,但铸孔以外滑程区和非滑程区温度较低,抗氧化剂尚不能熔化或反应形成陶瓷相结合,导致这些区域强度较低,使得滑板开闭来回拉动过程中出现板面拉毛掉块的问题;
7.3)热震性能较差:不烧滑板使用过程中内部难以形成连续碳结合、金属结合或陶瓷结合的方式,因此热震稳定性能较差;
8.4)氧化拉毛问题突出:产生原因与第2)点类似,铸孔以外滑程区和非滑程区温度较低,抗氧化剂难以发挥良好作用,碳源会出现明显氧化,导致出现氧化拉毛问题,严重时会存在漏钢风险。
9.近年来科技工作者在不烧滑板方面做了很多研究工作,如发明专利申请文献cn 106986619 a、cn 103011867 a、cn109400121 a、cn109160807 a、cn 106001532 a等分别报道在不烧滑板中引入纳米氧化铝粉体、镁砂、尖晶石、钛酸铝等来改善不烧滑板材质的致密度、强度、抗氧化性能、热震稳定性能等,但这些报道都没有从根本上解决滑板热导率低、中温强度低等问题,使用过程中仍会存在氧化拉毛、滑程板面掉块等问题。
技术实现要素:
10.针对上述技术问题以及本领域存在的不足之处,本发明提供了一种高导热不烧al2o
3-c滑板砖,其热导率高,连铸浇钢过程中滑板铸孔处温度很快传递到周边滑程区及非
滑程区域,使得材料自烧结形成较高强度和耐磨性,避免使用过程中滑程和非滑程区域出现掉块、氧化拉毛等问题。同时,该滑板砖还具有非常优异的抗氧化性能、热震稳定性能及韧性,用于大中小型各类钢包上均可以大幅度提高使用寿命。
11.一种高导热不烧al2o
3-c滑板砖,以质量份计,原料组成包括:
[0012][0013]
在一优选例中,所述的高导热不烧al2o
3-c滑板砖,以质量份计,所述刚玉颗粒的粒度级配为:
[0014]
2~1mm
ꢀꢀꢀꢀꢀꢀꢀꢀꢀꢀꢀꢀꢀꢀꢀꢀꢀꢀꢀꢀꢀ
20~30份,
[0015]
1~0.5mm,不包括1mm
ꢀꢀꢀꢀꢀꢀꢀꢀꢀ
10~20份,
[0016]
0.5~0.089mm,不包括0.5mm
ꢀꢀꢀ
20~25份。
[0017]
在一优选例中,所述的高导热不烧al2o
3-c滑板砖,以质量份计,所述刚玉细粉的粒度级配为:
[0018]
0.088~0.045mm
ꢀꢀꢀꢀꢀꢀꢀꢀꢀꢀꢀꢀꢀ
5~10份,
[0019]
《0.045mm
ꢀꢀꢀꢀꢀꢀꢀꢀꢀꢀꢀꢀꢀꢀꢀꢀꢀꢀꢀ
5~10份。
[0020]
在一优选例中,所述的高导热不烧al2o
3-c滑板砖,所述金属al纤维中al》97.0wt%,纤维直径为20~200μm,长度为0.2~3mm。
[0021]
在一优选例中,所述的高导热不烧al2o
3-c滑板砖,所述单质si纤维中si》97.0wt%,纤维直径为20~200μm,长度为0.2~3mm。
[0022]
在一优选例中,所述的高导热不烧al2o
3-c滑板砖,所述鳞片结构al片中al》97.0wt%,鳞片大小为(0.2~2.0)mm
×
(0.25~1)mm,片厚为0.02~0.08mm。
[0023]
在一优选例中,所述的高导热不烧al2o
3-c滑板砖,所述鳞片结构si片中si》97.0wt%,鳞片大小为(0.2~2.0)mm
×
(0.25~1)mm,片厚为0.02~0.08mm。
[0024]
在一优选例中,所述的高导热不烧al2o
3-c滑板砖,所述si3n4纤维中si3n4》97.0wt%,纤维直径为5~15μm,长度为2~10mm。
[0025]
在一优选例中,所述的高导热不烧al2o
3-c滑板砖,所述sic纤维中sic》97.0wt%,
纤维直径为5~15μm,长度为2~10mm。
[0026]
在一优选例中,所述的高导热不烧al2o
3-c滑板砖,所述高温沥青粉的指标如下:软化点为120~250℃,550℃下结焦值为60%~85%,800℃埋炭气氛下残碳率为70wt%~85wt%,粒度为《0.045mm。
[0027]
在一优选例中,所述的高导热不烧al2o
3-c滑板砖,所述刚玉颗粒采用电熔白刚玉或烧结板状刚玉中的至少一种,所述刚玉颗粒中al2o3≥99.0wt%。
[0028]
在一优选例中,所述的高导热不烧al2o
3-c滑板砖,所述刚玉细粉采用电熔白刚玉或烧结板状刚玉中的至少一种,所述刚玉细粉中al2o3≥99.0wt%。
[0029]
在一优选例中,所述的高导热不烧al2o
3-c滑板砖,所述活性氧化铝微粉中al2o3》99.0wt%,粒度为d50≤2μm;
[0030]
在一优选例中,所述的高导热不烧al2o
3-c滑板砖,所述金属al粉中al》97.0wt%,粒度为《0.045mm;
[0031]
在一优选例中,所述的高导热不烧al2o
3-c滑板砖,所述结合剂为热固性酚醛树脂、有机硅树脂中的至少一种。
[0032]
本发明还提供了所述的高导热不烧al2o
3-c滑板砖的制备方法,包括步骤:
[0033]
(1)将除刚玉颗粒和结合剂以外的其他原料先预混合均匀制备成预混合粉;
[0034]
(2)将刚玉骨料放入高速混碾机中混碾3~5min,再加入结合剂混碾5~8min,最后加入所述预混合粉混碾30~50min,混完的泥料在恒温室中困料24h以上,然后在1000t摩擦压力机上压制成型,成型后的滑板砖进入干燥窑在180~260℃下烘烤24h以上,烘烤后的滑板砖直接进行套钢带和钢壳、钻孔、抛光和涂抹石墨涂层工序,得到所述高导热不烧al2o
3-c滑板砖。
[0035]
传统不烧al2o
3-c滑板中一般碳源加入量较低,主要是防止使用过程中出现氧化拉毛等问题,同时引入较高含量金属al粉作为抗氧化增强剂。滑板组分中一般骨料占比在60wt%~70wt%左右,基质部分(细粉、外加剂、碳源等)占比在30wt%~40wt%左右,金属al粉一般以细粉形式引入到材料中,主要以小粒子(《0.088mm)形式分布在基质中。因材料中骨料占比较高,故基质中金属al粉分布过程中容易受到颗粒阻隔,导致在材料中不能形成网络结构,故传统不烧滑板热导率很低。滑板使用过程中铸孔以外滑程和非滑程区域温度低,因金属al粉熔化温度在660℃左右,反应形成陶瓷相温度在800℃以上,滑程和非滑程处温度不足以使金属al粉熔化或氧化达到产生结合强度和防止碳源氧化的作用,从而导致使用过程中该区域出现氧化拉毛、掉块和裂纹等问题。
[0036]
本发明与现有技术相比,主要优点包括:
[0037]
1、本发明通过在滑板中引入金属al纤维、单质si纤维、鳞片结构al片、鳞片结构si片、si3n4纤维和sic纤维,这些组分协同作用,具有如下方面优势:
[0038]
a)上述原料导热性能好且都具有二维结构,通过混合均匀后分布于材料中,与金属al粉一起能够在骨料和基质中形成点-线-面接触方式,从而形成良好的网络状结合方式,可以大幅度提高材料的导热性能,避免了传统不烧滑板中金属al细粉在材料中不连续分布导致热导率偏低的问题。热导率提高有利于降低材料使用过程中内部热应力作用,从而提高抗热冲击性能。
[0039]
b)在不烧滑板中引入鳞片结构al片和si片,除了大幅度提高热导率外,片状结构
在材料使用过程中还具有“弯曲、桥连和断裂”等增韧作用,赋予材料非常优异的韧性,提高材料使用过程中断裂应力,从而提高热震稳定性能。
[0040]
c)引入si3n4和sic纤维,除了具有高热导率外,也能够大幅度提高材料的断裂应力,更为重要的是,与传统碳素原料(碳纤维、炭黑等)相比,si3n4和sic纤维在中高温下稳定性能较好,使用过程中基本不会发生结构蚀变的问题,同时还能够提高滑板的耐磨和耐冲刷性能。
[0041]
2、通过在滑板中引入高残碳率沥青粉,在滑板烘烤过程中沥青发生熔化并均匀分布于材料基质内部和骨料周边,形成网络结构,在滑板使用过程中沥青裂解形成网络状石墨化结构,提高了材料的热导率和热震性能。
[0042]
3、通过上述原料组合,所制备的不烧al2o
3-c滑板砖具有非常高的导热性能,在浇注钢水过程中,滑板铸孔处的热量很快传递到周边滑程和非滑程区域,从而使得金属al粉、al纤维及鳞片结构al片发生熔化产生自烧结作用,提高不烧al2o
3-c滑板中温强度。同时,滑板铸孔周边滑程和非滑程因温度较高,al和si抗氧化剂可优先与环境或钢水中氧反应,避免滑板中的碳发生氧化作用,且随着浇钢时间延长,材料内部温度进一步升高,金属al和si进一步原位反应形成al4c3、aln和sic陶瓷结合相,从而进一步提高材料的中高温强度。
[0043]
综上来看,本发明的不烧al2o
3-c滑板砖具有高热导率,使用过程中能够自烧结,从而大幅度提高了材料的中高温强度,同时使得材料还具有非常优异的抗氧化性能、热震稳定性能、耐磨性能、韧性等,从而解决了滑板使用过程中容易出现裂纹、热剥落、氧化拉毛和铸孔周边掉块等问题。
具体实施方式
[0044]
下面结合具体实施例,进一步阐述本发明。应理解,这些实施例仅用于说明本发明而不用于限制本发明的范围。下列实施例中未注明具体条件的操作方法,通常按照常规条件,或按照制造厂商所建议的条件。
[0045]
各实施例、对比例所用部分原料说明如下:
[0046]
刚玉采用电熔白刚玉或烧结板状刚玉,al2o3≥99.0wt%;
[0047]
活性氧化铝微粉中al2o3》99.0wt%;
[0048]
金属al粉中al》97.0wt%;
[0049]
金属al纤维中al》97.0wt%;
[0050]
单质si纤维中si》97.0wt%;
[0051]
鳞片结构al片中al》97.0wt%;
[0052]
鳞片结构si片中si》97.0wt%;
[0053]
si3n4纤维中si3n4》97.0wt%;
[0054]
sic纤维中sic》97.0wt%;
[0055]
高温沥青粉的指标如下:软化点为120~250℃,550℃下结焦值为60%~85%,800℃埋炭气氛下残碳率为70wt%~85wt%;
[0056]
鳞片石墨的化学组成为c≥94.0%,粒度为《0.045mm。
[0057]
纳米炭黑的化学组成为c≥96.0%,粒度为d50≤10μm。
[0058]
各实施例、对比例的不烧al2o
3-c滑板砖的制备方法包括步骤:
[0059]
(1)将除刚玉颗粒和结合剂以外的其他原料先预混合均匀制备成预混合粉;
[0060]
(2)将刚玉颗粒放入高速混碾机中混碾4min,再加入结合剂混碾6min,最后加入所述预混合粉混碾40min,混完的泥料在恒温室中困料24h以上,然后在1000t摩擦压力机上压制成型,成型后的滑板砖进入干燥窑在220℃下烘烤24h以上,烘烤后的滑板砖直接进行套钢带和钢壳、钻孔、抛光和涂抹石墨涂层工序,得到不烧al2o
3-c滑板砖。
[0061]
表1
[0062][0063]
表2展示了各实施例、对比例的不烧al2o
3-c滑板砖的性能测试结果。
[0064]
表2
[0065][0066]
由表2可以看出,本发明的高导热不烧al2o
3-c滑板,在常温和经中高温处理后耐压和抗折强度、高温抗折强度、热震稳定性能、中高温抗氧化性能都有明显提升,同时热导率相对于常规产品提高一倍以上。本发明的高导热不烧al2o
3-c滑板使用过程中能够自烧结,会大幅度提高材料的中高温强度,使得材料具有非常优异的抗氧化性能、热震稳定性能、耐磨性能、韧性等,从而解决了滑板使用过程中容易出现裂纹、热剥落、氧化拉毛和铸孔周边
掉块等问题,能大幅度提高使用寿命。
[0067]
此外应理解,在阅读了本发明的上述描述内容之后,本领域技术人员可以对本发明作各种改动或修改,这些等价形式同样落于本技术所附权利要求书所限定的范围。
再多了解一些
本文用于企业家、创业者技术爱好者查询,结果仅供参考。