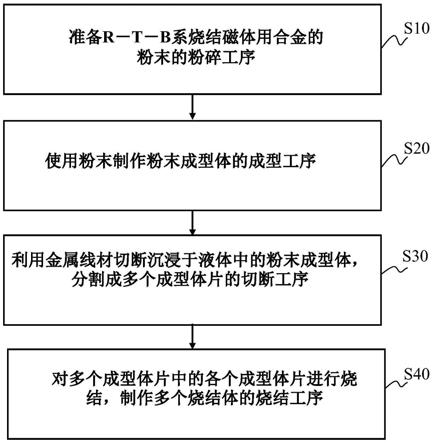
r-t-b系烧结磁体的制造方法
技术领域
1.本发明涉及r-t-b系烧结磁体的制造方法。
背景技术:
2.r-t-b系烧结磁体(r为稀土元素,必须包含选自nd、pr和ce中的至少一种,t为过渡金属的至少一种,必须包含fe,b为硼)由具有r2fe
14
b型结晶结构的化合物的主相和位于该主相的晶界部分的晶界相以及由于微量添加元素或杂质的影响而生成的化合物相构成。r-t-b系烧结磁体表现高的残留磁通密度br(以下,有时仅记载为“b
r”)和高的矫顽力h
cj
(以下,有时仅记载为“h
cj”),并且具有优异的磁特性,因此,作为在永久磁体中性能最高的磁体被已知。因此,r-t-b系烧结磁体被用于硬盘驱动器的音圈电动机(vcm)、电动汽车(ev、hv、phv)用电动机、工业设备用电动机等各种电动机以及家电制品等各种各样的用途。
3.这种r-t-b系烧结磁体例如经由准备合金粉末的工序、对合金粉末进行压制成型而制作粉末成型体的工序、烧结粉末成型体的工序而制造。合金粉末通过例如以下的方法制作。
4.首先,通过铸锭法或薄带连铸法等方法,由各种原料金属的熔液制造合金。将得到的合金供于粉碎工序,得到具有规定的粒径分布的合金粉末。在该粉碎工序中,通常包括粗粉碎工序和微粉碎工序,前者利用例如氢脆化现象进行,后者使用例如气流式粉碎机(喷射磨)进行。
5.关于通过烧结粉末成型体的工序而得到的烧结体,之后会实施研削、切断等机械加工,单片化成具有期望的形状和尺寸。更详细而言,首先,通过使用压制装置对r-fe-b系稀土磁体粉末进行压缩成型,制作比最终的磁体产品大的尺寸的成型体。然后,通过烧结工序将成型体制成烧结体后,利用例如超硬合金制刀锯或旋转磨石等对烧结体进行研削加工,赋予期望的形状。例如,首先制作具有块形状的烧结体之后,利用刀锯等对该烧结体进行切片,由此切出多个板状烧结体部分。
6.但是,r-fe-b系烧结磁体等稀土合金磁体的烧结体极其硬而脆,而且加工负荷大,因此高精度的研削加工是困难的作业,加工时间长。另外,不可避免地产生因加工而损失的材料部分。因此,加工工序成为制造成本增加的主要原因。
7.为了解决例如前者的问题,专利文献1记载一种技术,在烧结前使用线锯对磁体成型体进行加工。线锯是如下的加工技术,将在一个方向或两个方向上行进的锯线按压在所要加工的成型体上,通过位于锯线和成型体之间的磨粒对成型体进行研削或切断。根据该技术,切断处于比烧结体格外柔软且容易加工的状态的粉末成型体,因此,大幅度缩短切断加工所需要的时间。
8.现有技术文献
9.专利文献
10.专利文献1:日本特开2003-303728号公报
技术实现要素:
11.发明所要解决的技术问题
12.专利文献1公开了使用具有0.1mm以上1.0mm以下的外径的锯线和固定于该锯线的磨粒的线锯,在将氧浓度调节成以摩尔比计为整体的5%以上18%以下的不活泼气体气氛中加工粉末成型体。在这样控制氧浓度的不活泼气氛中进行线锯加工,其设备和管理变得复杂,量产性差。
13.本发明的实施方式提供能够进行不需要准备不活泼气氛的线锯工序的新型r-t-b系烧结磁体的制造方法。
14.用于解决技术问题的技术方案
15.本发明提供一种r-t-b系烧结磁体的制造方法,在示例的实施方式中,包括:准备r-t-b系烧结磁体用合金(r为稀土元素,必须包含选自nd、pr和ce中的至少一种,t为过渡金属的至少一种,必须包含fe,b为硼)的粉末的粉碎工序;使用上述粉末制作粉末成型体的成型工序;切断上述粉末成型体,分割成多个成型体片的切断工序;和对上述多个成型体片中的各个成型体片进行烧结,制作多个烧结体的烧结工序,上述切断工序包括通过行进的金属线材切断沉浸于液体中的上述粉末成型体的步骤。
16.在一个实施方式中,在上述切断工序中,上述金属线材的行进速度为300m/分钟以上。
17.在一个实施方式中,在上述切断工序中,上述金属线材的张力为3kgf以上。
18.在一个实施方式中,在上述切断工序中,相对于上述金属线材的行进方向正交的方向的切入速度为100mm/分钟以上。
19.在一个实施方式中,准备上述粉末成型体的工序包括通过湿式压制将上述粉末成型的步骤。
20.在一个实施方式中,上述湿式压制通过将与上述切断工序中的上述液体相同种类的液体添加到上述粉末中而进行。
21.在一个实施方式中,还包括从上述液体中回收通过上述切断工序从上述粉末成型体削掉的上述粉末的颗粒的工序。
22.发明效果
23.根据本发明的实施方式,不准备不活泼气氛,可利用线锯进行切断,量产性优异。另外,也能够防止从线锯脱落的磨粒混入切削粉中。因此,容易在利用线锯进行的切断工序中再利用从粉末成型体产生的切削粉并用于磁体的制造,也能够维持高性能磁体的特性,并且能够实现制造成本的降低。
附图说明
24.图1是表示本发明的实施方式的制造方法的主要工序的流程图。
25.图2是示意性地表示本发明的实施方式中使用的线锯装置的构成的立体图。
26.图3a是用于说明通过线锯切断沉浸于液体中的粉末成型体的工序的主视图。
27.图3b是用于说明通过金属线材的线锯切断沉浸于液体中的粉末成型体的工序的主视图。
28.图4a是用于说明通过线锯切断沉浸于液体中的粉末成型体的工序的侧视图。
29.图4b是用于说明通过线锯切断沉浸于液体中的粉末成型体的工序的侧视图。
30.图5a是用于说明通过线锯切断沉浸于液体中的粉末成型体的工序的侧视图。
31.图5b是用于说明通过线锯切断沉浸于液体中的粉末成型体的工序的侧视图。
32.图6a是示意性地表示通过线锯而形成于粉末成型体10的切断面的图。
33.图6b是示意性地表示通过线锯而形成于粉末成型体10的切断面的图。
34.图6c是示意性地表示通过线锯而形成于粉末成型体10的切断面的图。
35.图7是表示锯线行进速度和切入速度对成型体片的形状产生如何的影响的图表。
36.图8是表示锯线行进速度和切入速度对成型体片的形状产生如何的影响的图表。
37.符号说明
38.10
…
粉末成型体;20
…
固定用基座;30a、30b、30c
…
辊;40
…
锯线;50
…
支承装置;60
…
液体;70
…
槽;100
…
线锯装置。
具体实施方式
39.以下,说明本发明的r-t-b系烧结磁体的制造方法的实施方式。如图1的流程图所示,本实施方式的r-t-b系烧结磁体的制造方法包括:
40.·
准备r-t-b系烧结磁体用合金(r为稀土元素,必须包含选自nd、pr和ce中的至少一种,t为过渡金属的至少一种,必须包含fe,b为硼)的粉末的粉碎工序(s10);
41.·
使用粉末制作粉末成型体的成型工序(s20);
42.·
切断粉末成型体,分割成多个成型体片的切断工序(s30);
43.·
对多个成型体片中的各个成型体片进行烧结,制作多个烧结体的烧结工序(s40),
44.切断工序(s30)包括通过行进的金属线材切断沉浸于液体中的上述粉末成型体的步骤。
45.根据本发明的r-t-b系烧结磁体的制造方法,在将粉末成型体沉浸于液体中的状态下利用线锯进行切断,因此,不需要准备不活泼气氛。本发明的实施方式中能够利用的液体的例子是矿物油或合成油等油剂。
46.目前,为了利用线锯切断粉末成型体,认为需要固着于构成线锯的金属线材的表面的硬磨粒与粉末成型体接触,通过摩擦削掉粉末成型体的一部分。但是,本发明人进行的实验的结果可知,当行进的金属线材与沉浸于液体中的粉末成型体相接触时,即使仅利用未固着磨粒的金属线材,也能够将粉末成型体研削并切断。发明人的研究的结果可知,在以规定范围的速度行进的金属线材和粉末成型体接触的区域及其附近,产生高速的液体流(喷射流),由此能够削掉构成粉末成型体的粉末颗粒。认为从粉末成型体削掉的粉末颗粒的一部分随着以高速流通的液体被夹于金属线材和粉末成型体之间,发挥与游离磨粒同样的研削功能,促进粉末成型体的切断。从在液体中锯线切断粉末成型体的机理来看,认为锯线的表面的形状和形态没有特别限定。换言之,锯线的表面也可以如普通的钢琴线那样平滑。
47.在切断工序中,锯线的行进速度优选为300m/分钟以上,此时的锯线的张力优选为3kgf(29.4n)以上,例如为15kgf(147n)以下。当锯线的行进速度低于300m/分钟时,得不到为了切断粉末成型体所需要的充分的流速,当锯线的张力低于3kgf时,锯线挠曲,切断面的
平坦性可能降低。当锯线的张力超过15kgf时,可能产生锯线断裂之类的问题。另外,在切断工序中,相对于锯线的行进方向正交的方向的切入速度(工件输送速度)优选为100mm/分钟以上。这是由于当切入速度低于100mm/分钟时,切断工序所需要的时间变长,生产效率降低。
48.此外,锯线的直径为200μm以上时,能够将锯线的行进速度设为500m/分钟以上。锯线的行进速度越高,越能够提高切入速度。例如,在锯线的直径为250μm,且将锯线的行进速度设为500m/分钟以上的情况下,能够将切入速度设为250mm/分钟以上。
49.在液体中切断粉末成型体的优点之一在于,能够抑制粉末成型体和线锯接触的部分中的摩擦热引起的温度上升,产生的热也容易在液体中分散。如果在大气中,由于产生的摩擦热而成为高温的粉末成型体会与大气中的氧或水蒸气反应,导致最终得到的烧结磁体中的氧浓度的上升和磁体特性的劣化,在本实施方式中,能够避免这种问题。
50.在液体中切断粉末成型体的另一优点在于,通过线锯从粉末成型体削掉的粉末颗粒沉淀于液体中,容易回收。在优选的实施方式中,准备粉末成型体的工序包括通过湿式压制将粉末成型的步骤。在该情况下,湿式压制优选通过将与切断工序中的液体相同种类的液体添加到上述粉末中而进行。这是由于容易从液体中回收通过切断工序从粉末成型体削掉的粉末的颗粒并进行再利用。
51.另外,可知即使将线锯的切入速度朝向水平横向,如果在液体中,则也能够切断粉末成型体。在粉末成型体的表面上,至少一部分(例如上表面)有时由于粉末压制工序而具有凹凸,需要通过烧结工序后的加工进行切削或研磨。根据本发明的实施方式,能够去掉这种进行切削或研磨的工序,因此,能够维持高性能磁体的特性,并且能够实现制造成本的降低。
52.参照图2说明能够用于上述的制造方法的线锯装置的构成例。图2是表示本发明的实施方式的线锯装置100的构成例的立体图。为了参考,图中表示了相互正交的x轴、y轴和x轴。在该例中,xy平面为水平,z轴朝向铅直方向。
53.图2的线锯装置100具有:以旋转的中心轴相互平行的方式排列的辊30a、30b、30c;和一根连续的锯线40。辊30a、30b、30c各自被支承装置50可旋转地支承。支承装置50能够通过未图示的驱动装置在上下纵向(z轴的正和负的方向)上移动。驱动装置可以通过液压缸得到驱动力,也可以通过电动机进行动作。另外,沿着后述的水平横向(x轴方向)进行切断,因此,支承装置50也可以在水平横向上移动。
54.成型工序(s20)中制作的粉末成型体10通过未图示的夹具部被固定于固定用基座20,并配置于储存液体60的槽70的内部。图2中,槽70以虚线表示,液体60的表面的高度以点线表示。在图2的例子中,粉末成型体10的全体浸渍于液体60中。此外,也可以代替支承装置50在上下纵向和水平横向上移动,而构成为固定用基座20在上下纵向和水平横向上移动。
55.后面叙述制作粉末成型体10的工序的具体例。这里注意的点在于,粉末成型体10不是烧结体,而是烧结之前的粉末的成型体(生坯,green compact)。粉末成型体通过将r-t-b系烧结磁体用合金(r为稀土元素,必须包含选自nd、pr和ce中的至少一种,t为过渡金属的至少一种,必须包含fe,b为硼)的粉末在取向磁场中通过湿式压制或干式压制进行成型而获得。
56.在从与x轴平行的方向观察时,辊30a、30b、30c以旋转中心的轴位于三角形的顶点
的方式,隔开规定的间隔而配置。在辊30a、30b、30c各自的侧面设置有多个槽。锯线40依次绕设于辊30a、30b、30c的多个槽。多个槽的中心间隔(间距)规定通过线锯进行切断而被分割的元件的宽度。锯线40的两端卷绕于例如未图示的回收线轴上。
57.本发明的实施方式的锯线40是在表面上未固着磨粒的金属线材。在现有的线锯技术中,锯线具有线材(芯线)和位于线材的外周面的磨粒。磨粒的平均粒径例如为数μm~数十μm。这种磨粒的典型例为人工金刚石,具有比稀土合金的硬度高的硬度。与这种现有的锯线不同,本实施方式的锯线40由例如碳钢等金属材料形成,即使在切断工序中赋予例如3kgf以上的张力,也能够不伸长地使用。能够用于锯线40的金属线材可以是例如钢琴线、高张力钢丝等。也可以对锯线40的表面进行镀敷。锯线40的直径例如处于100μm以上350μm的范围,优选处于200μm以上300μm以下的范围。当锯线40的直径低于100μm时,存在由于强度不足,锯线40在切断中延长的问题。锯线40的直径越大,越提高切削粉的排出性,但切削粉的量会增加,因此优选为350μm以下。
58.在切断时,辊30a、30b、30c和回收线轴进行旋转。辊30a、30b、30c的旋转方向依赖于它们的配置和锯线40的悬挂方式。在图2所示的线锯装置100中,辊30a、30b、30c在同一方向上旋转。
59.如果将规定长度的锯线40卷取在一个回收线轴上,则使回收线轴和辊30a、30b、30c反向旋转。由此,通过锯线40反方移动,反复进行该动作,能够使锯线40进行往复运动(移动)。
60.在本实施方式中,通过锯线40切断粉末成型体10的工序在将粉末成型体10沉浸于液体60中的状态下实施。在粉末成型体10为通过湿式压制而形成的粉末成型体的情况下,液体60的优选的例子是与湿式压制中使用的油剂(矿物油或合成油)等分散介质相同种类的油剂。
61.利用这种线锯装置100加工粉末成型体10时,构成粉末成型体10的粉末颗粒成为切削粉而从由锯线40切削的部分脱落。这些切削粉是构成粉末成型体10的粉末颗粒从粉末成型体10脱落的部分,各个颗粒并不具有金属的切削粉(切削屑)那样粗糙的断裂面。构成通过锯线从烧结前的粉末成型体削落的切削粉的颗粒的形状和尺寸与粉末成型体10的制作中所使用的粉末颗粒的形状和尺寸相同。本发明人研究了再利用该切削粉。在对烧结粉末成型体而得到的硬的烧结体进行切削的情况下,该切削粉是通过烧结而粒生长或组成由于化学反应而变化的颗粒,或颗粒的结合物。因此,即使将它们与稀土磁体的粉末混合并再利用,磁体特性劣化的可能性也高。与之相对,如果是由烧结前的粉末成型体得到的切削粉,则与粉末成型体所包含的其他颗粒相比,组成和尺寸也相同,因此,容易再利用。
62.根据本发明人的研究可知,在使用了带磨粒的现有锯线的情况下,回收从粉末成型体10削掉的稀土合金的粉末颗粒,由包含回收的粉末颗粒的稀土合金的粉末成型体制作烧结磁体时,有时磁体特性劣化。其原因在于,在回收的粉末中包含从锯线40脱落的磨粒。磨粒的材料的典型例为金刚石,由碳构成。可知金刚石颗粒的混入在烧结工序中产生气孔(空洞),能够使磁体特性(特别是耐腐蚀性)劣化。但是,使用没有磨粒的金属线材的锯线40时,在回收的粉末(切削粉)中不包含磨粒,能够成品率良好地制造高性能的磁体。
63.另外,在通过湿式压制制作粉末成型体10的情况下,如果在与分散剂同种的油剂中进行线锯加工,则能够将回收的粉末(切削粉)直接用于湿式压制,生产效率上升。
64.以下,详细地说明本实施方式的r-t-b系烧结磁体的制造方法。
65.s10:粉碎工序
66.在粉碎工序(s10)中,准备r-t-b系烧结磁体用合金的粉末。以下,依次说明r-t-b系烧结磁体用合金的组成、合金的制造工序和准备合金的粉末的工序。
67.<r-t-b系烧结磁体用合金的组成>
68.r为稀土元素,必须包含选自nd、pr和ce中的至少一种。优选使用以nd-dy、nd-tb、nd-dy-tb、nd-pr-dy、nd-pr-tb、nd-pr-dy-tb、nd-ce-dy、nd-ce-tb、nd-ce-dy-tb、nd-pr-ce-dy、nd-pr-ce-tb、nd-pr-ce-dy-tb所示的稀土元素的组合。
69.r中,特别是dy和tb在提高h
cj
的方面发挥效果。除了上述元素以外,也可以含有la等其他的稀土元素,也能够使用铈合金(mischmetal)或钕镨混合物。另外,r也可以不是纯元素,也可以在工业上可获得的范围内含有制造上不可避免的杂质。含量例如为27质量%以上35质量%以下。优选r-t-b系烧结磁体的r含量为31质量%以下(27质量%以上31质量%以下,优选为29质量%以上31质量%以下)。通过将r-t-b系烧结磁体的r含量设为31质量%以下,且将氧的含量设为500ppm以上3500ppm以下(优选为500ppm以上3200ppm以下,进一步优选为500ppm以上2500ppm以下),能够得到更高的磁特性。
70.t包含铁(也包含t实际上由铁构成的情况),也可以以质量比计将其50%以下利用钴(co)置换(包含t实际上由铁和钴构成的情况)。co在提高温度特性、提高耐腐蚀性的方面是有效的,合金粉末也可以包含10质量%以下的co。t的含量可以占据r和b或r、b和后述的m的剩余部分。
71.关于b的含量,可以是公知的含量,例如,0.9质量%~1.2质量%是优选的范围。如果低于0.9质量%,则有时得不到高的h
cj
,当超过1.2质量%时,br有时降低。此外,b的一部分能够利用c(碳)进行置换。
72.除了上述元素之外,为了提高h
cj
,可以添加m元素。m元素为选自al、si、ti、v、cr、mn、ni、cu、zn、ga、zr、nb、mo、in、sn、hf、ta和w中的一种以上。m元素的添加量优选为5.0质量%以下。这是由于当超过5.0质量%时,br有时降低。另外,也能够允许不可避免的杂质。
73.r-t-b系烧结磁体中的n(氮)的含量优选为50ppm以上600ppm以下。另外,r-t-b系烧结磁体中的c(碳)的含量优选为50ppm以上1000ppm以下。
74.<r-t-b系烧结磁体用合金的制造工序>
75.示例r-t-b系烧结磁体用合金的制造工序。能够通过将预先调整为上述的组成的金属或合金熔融并放入铸模的铸锭铸造法得到合金铸锭。另外,能够通过使熔液与单辊、双辊、旋转圆盘或旋转圆筒铸模等接触而骤冷,制作比通过铸锭法制成的合金薄的凝固合金的薄带连铸法或离心铸造法所代表的骤冷法制造合金薄片。
76.在本发明的实施方式中,也可以使用通过铸锭法和骤冷法的任一方法制造的材料,优选通过薄带连铸法等骤冷法制造。通过骤冷法制作的骤冷合金的厚度通常处于0.03mm~1mm的范围,为薄片形状。合金熔液从冷却辊的接触面(辊接触面)开始凝固,结晶从辊接触面向厚度方向柱状生长。骤冷合金与现有的利用铸锭铸造法(模具铸造法)制得的合金(铸锭合金)相比,在短时间内被冷却,因此组织微细化,结晶粒径小。另外,晶界的面积大。富r相在晶界内广泛扩展,因此利用骤冷法时富r相的分散性优异。因此,利用氢粉碎法,
容易在晶界断裂。通过对骤冷合金进行氢粉碎,能够使氢粉碎粉(粗粉碎粉)的尺寸成为例如1.0mm以下。例如利用喷射磨将如此操作得到的粗粉碎粉微粉碎。
77.<准备r-t-b系烧结磁体用合金的粉末的工序>
78.r-t-b系烧结磁体用的稀土合金的粉末为活性,且容易氧化。因此,作为喷射磨所使用的气体,为了避免发热、起火的危险性、降低作为杂质的氧含量且实现磁体的高性能化,能够使用例如氮、氩、氦等不活泼气体。
79.投入喷射磨的被粉碎物(粗粉碎粉)被粉碎成例如具有平均粒度(中位径:d50)为2.0μm以上4.5μm以下的粒度分布的微粉末之后,移动到旋风捕集装置。旋风捕集装置用于从运送粉末的气流中分离粉末。具体而言,r-t-b系烧结磁体用合金的粗粉碎粉被前段的喷射磨粉碎,粉碎而生成的微粉末与粉碎所利用的气体一起被供给至旋风捕集装置。不活泼气体(粉碎气体)与被粉碎后的微粉末的混合物形成高速的气流,被送往旋风捕集装置。旋风捕集装置用于将这些粉碎气体和微粉末分离。从粉碎气体中分离的微粉末被粉末捕集器回收。
80.s20:成型工序
81.在成型工序(s20)中,使用粉碎工序(s10)中得到的粉末制作粉末成型体。
82.在本实施方式中,通过磁场中压制,由上述的粉末制作粉末成型体。在利用磁场中压制时,从抑制氧化的观点出发,优选通过不活泼气体气氛中的压制或湿式压制形成粉末成型体。特别是湿式压制,构成粉末成型体的颗粒的表面被油剂等分散剂包覆,抑制了与大气中的氧或水蒸气的接触。因此,能够防止或抑制在压制工序前后或者在压制工序中颗粒被大气氧化。
83.在进行磁场中湿式压制的情况下,准备在微粉末中混有分散介质的浆料,向湿式压制装置的模具中的模腔供给,在磁场中进行压制成型。如此形成的粉末成型体例如具有4g/cm3以上5g/cm3以下的密度。
84.·
分散介质
85.分散介质是能够使合金粉末在其内部分散而得到浆料的液体。
86.作为本发明中使用的优选的分散介质,可以列举矿物油或合成油。矿物油或合成油的种类并没有特定,但在常温时的运动粘度超过10cst时,因粘性增大而使得合金粉末相互的结合力增强,有时会对磁场中湿式成型时的合金粉末的取向性造成不良影响。因此,矿物油或合成油的常温时的运动粘度优选为10cst以下。另外,在矿物油或合成油的分馏温度超过400℃时,得到成型体后的脱油变得困难,存在烧结体内的残余碳量增多而导致磁特性降低的情况。因此,矿物油或合成油的分馏温度优选为400℃以下。另外,作为分散介质也可以使用植物油。植物油是指从植物提取的油,植物的种类也并不限定为特定的植物。
87.·
浆料的制作
88.将所得到的合金粉末与分散介质混合而得到浆料。
89.合金粉末与分散介质的混合率没有特别限定,浆料中的合金粉末的浓度以质量比计优选为70%以上(即70质量%以上)。这是由于在20~600cm3/秒的流量下,能够高效地向模腔内部供给合金粉末、并且能够获得优异的磁特性的缘故。浆料中的合金粉末的浓度以质量比计优选为90%以下。合金粉末与分散介质的混合方法没有特别限定。可以分别准备合金粉末和分散介质,将两者称量规定量并混合而制造。另外,在利用喷射磨等对粗粉碎粉
进行干式粉碎而得到合金粉末时,可以在喷射磨等粉碎装置的合金粉末排出口配置装有分散介质的容器,将粉碎而得到的合金粉末直接回收至容器内的分散介质中,得到浆料。在这种情况下,优选容器内也形成由氮气和/或氩气构成的气氛,将所得到的合金粉末直接回收至分散介质中而不接触大气,制成浆料。另外,也可以使用振动磨、球磨机或磨碎机等,将粗粉碎粉以保持在分散介质中的状态进行湿式粉碎,得到由合金粉末和分散介质构成的浆料。
90.通过利用公知的湿式压制装置将如此操作得到的浆料成型,能够得到具有规定大小和形状的粉末成型体。在现有技术中,通常对该粉末成型体进行烧结而得到烧结体,但在本实施方式中,如以下所说明的那样,在烧结前利用线锯分割粉末成型体。
91.s30:切断工序
92.在切断工序(s30)中,将粉末成型体切断,分割成多个成型体片。
93.该工序中的粉末成型体的切断利用例如图2所示的线锯装置进行。图3a和图3b分别是用于说明利用锯线40切断沉浸于液体60中的粉末成型体10的工序的主视图。图3a表示开始切断工序之前的状态,图3b表示切断工序的途中的状态。图3b所示的粉末成型体10内的虚线示意性地表示切断粉末成型体10中的锯线40的位置。锯线40的以虚线表示的位置从粉末成型体10的上表面向下方移动,到达粉末成型体10的底面时,粉末成型体10被分割成多个成型体片。
94.在图示的例子中,锯线40以规定的速度在y轴方向上行进,同时向相对于锯线40的行进方向正交的方向(z轴的负的方向)移动。相对于锯线40的行进方向正交的方向是切入方向,该方向的速度(切入速度)被设定成例如100mm/分钟以上。在图3b所示的例子中,相对于静止的状态的粉末成型体10,行进的锯线40向z轴的负的方向移动,但粉末成型体10也可以与固定用基座20一起向z轴的正的方向升起。
95.图4a和图4b分别是用于说明利用锯线40切断沉浸于液体60中的粉末成型体10的工序的侧视图。图4a表示开始切断工序之前的状态,图4b表示切断工序的途中的状态。在图示的例子中,一个粉末成型体10分割成8个成型体片。
96.锯线40的直径例如为100μm以上350μm以下。锯线40的行进速度(锯线线速度)可设定成例如100m/分钟以上800m/分钟以下的范围。另一方面,切入速度(图2的z轴的负的方向上的、锯线相对于粉末成型体10的输送速度)可设定成例如100mm/分钟以上600mm/分钟以下的范围。施加于锯线40的张力例如为3kgf以上15kgf以下。张力可以通过例如调整辊30c相对于辊30a和辊30b的距离而进行调整。通过线锯切断,粉末成型体10可以分割成例如厚度1~10mm左右的成型体片。如图4b所示,成型体片的厚度根据锯线40的间隔和锯线40的直径决定。
97.通过在液体中进行线锯加工,还具有促进切削粉的排出的优点。另外,如上所述,通过在使粉末成型体10浸渍于通过湿式压制制作粉末成型体10时使用的分散介质(矿物油或合成油)中的状态下进行(油中切断),能够在线锯加工中回收沉淀于液体中的粉末颗粒,并将回收的粉末颗粒在成型工序中直接再利用。
98.图5a和图5b是用于说明利用锯线40在水平方向上切断沉浸于液体60中的粉末成型体10的工序的侧视图。在图示的例子中,在切断工序中,辊30a、30b、30c相对于粉末成型体10相对地在水平方向上移动。在进行参照图3a~图4b说明的工序之前,利用锯线40进行
水平方向的切入,由此能够使粉末成型体10的表面平坦。粉末成型体10的表面的至少一部分(例如上表面)有时由于粉末压制工序而具有凹凸。例如,在向粉末压制装置的冲模的孔填充粉末后,利用冲头挤压粉末之前,在冲头和粉末之间配置“滤布”,可以经由滤布排出分散剂(油剂)。在该情况下,可通过滤布在得到的粉末成型体的上表面上形成凹凸。
99.在本发明的实施方式中,将这种凹凸面在烧结工序前利用锯线切除,因此,能够在烧结工序后省略进行用于平坦化的切削或研磨的工序。
100.图6a~图6c是示意性地表示利用线锯形成于粉末成型体10的切断面的图。通过参照图5a和图5b说明的工序(第一处理工序),行进的锯线40相对于沉浸于液体60中的粉末成型体10沿着图6a的虚线11c进行移动,由此,较薄地切断粉末成型体10的粗糙的表面区域10t,形成与z轴方向正交的第一切断面11。然后,通过进行参照图4a和图4b说明的工序(第二处理工序),形成相对于第一切断面11交叉的多个第二切断面12。在第二处理工序中,第二切断面12通过行进的锯线沿着虚线12c进行移动而形成。第一处理工序和第二处理工序可以使用同一线锯装置进行,也可以使用不同的线锯装置进行。换言之,第二处理工序可以在沉浸于与第一处理工序中粉末成型体所沉浸的液体相同的液体中的状态下,利用相同的线锯切断,也可以在沉浸于不同的液体中的状态下利用不同的线锯切断。
101.在图6a~图6c所示的例子中,第一切断面11与水平面平行,第二切断面12与第一切断面11正交。第一切断面11和第二切断面12各自的方向不限定于该例。
102.s40:烧结工序
103.在烧结工序(s40)中,对多个成型体片中的各个成型体片进行烧结,制作多个烧结体。即,对通过上述的线锯工序而切断的各个成型体片进行烧结,得到r-t-b系烧结磁体(烧结体)。成型体片的烧结工序能够在例如0.13pa(10
-3
torr)以下、优选在0.07pa(5.0
×
10
-4
torr)以下的压力下,在例如温度1000℃~1150℃的范围内进行。为了防止烧结引起的氧化,气氛的残留气体可以通过氦、氩等不活泼气体进行置换。优选对得到的烧结体进行时效处理等附加热处理。通过这种热处理,能够提高磁特性。热处理温度、热处理时间等热处理条件能够采用公知的条件。对于这样得到的r-t-b系烧结磁体,根据需要实施研削、研磨工序、表面处理工序和磁化工序,完成最终的r-t-b系烧结磁体。
104.在一个优选的实施方式中,本发明的r-t-b系烧结磁体的制造方法还包括将重稀土元素rh(rh为tb、dy、ho中的至少一种)从烧结体的表面向内部扩散的扩散工序。当将重稀土元素rh从烧结体的表面向内部扩散时,能够有效地提高矫顽力。扩散工序的方法没有特别限制。能够采用公知的方法。
105.(实施例)
106.以达到nd:22.6%、pr:7.8%、b:0.9%、co:0.5%、al:0.1%、cu:0.2%、ga:0.4%(均为质量%)、剩余部分fe的组成的方式称重各元素的原料,通过薄带连铸法制作合金。将得到的合金进行氢粉碎,得到粗粉碎粉。
107.接着,向得到的粗粉碎粉中,添加相对于粗粉碎粉100质量%为0.04质量%的作为润滑剂的硬脂酸锌,进行混合之后,使用喷射磨在氮气流中进行干式粉碎,得到粒径d
50
为4μm的微粉碎粉(合金粉末)。将上述微粉碎粉在氮气氛中浸渍于分馏温度为250℃、室温下的运动粘度为2cst的矿物油中,准备浆料。浆料浓度为85质量%。将得到的浆料在磁场中进行成型(湿式成型),制作粉末成型体。粉末成型体的尺寸为80mm
×
45mm
×
60mm。
108.将上述粉末成型体利用直径250μm的线锯(由钢琴线构成的金属线材)分割成8个成型体片。利用线锯的切断在将粉末成型体沉浸于液体中(液体使用与成型时使用的上述矿物油相同的液体)的状态下进行。利用平行地行进的8根锯线(多锯线)切断各粉末成型体。在切断时对锯线施加的张力为10kg,辊间隔为250mm。
109.图7是表示锯线行进速度和切入速度对成型体片的形状造成如何的影响的图表。图表的横轴为锯线行进速度[m/分钟],纵轴为切入速度[mm/分钟]。该图表所示的
“×”
是指在通过线锯切断而分割的成型体片的一部分产生“裂纹”,“〇”是指在成型体片上未产生这种裂纹,能够分割成良好的形状的成型体片。
[0110]
在使用了直径250μm的锯线的情况下,若是300m/分钟的行进速度,则能够以100~150mm/分钟的切入速度得到没有裂纹的成型体片。另外,若是500m/分钟的行进速度,则能够以250mm/分钟的切入速度得到没有裂纹的成型体片。另外,若是700m/分钟的行进速度,则即使是400mm/分钟的切入速度,锯线也不会在切断中挠曲,能够得到没有裂纹的成型体片。
[0111]
此外,在使用了直径为160μm的锯线的情况下,在行进速度和切入速度两者较低的情况下,能够分割成良好的形成体片。锯线的直径越小,锯线越容易延长,且容易挠曲,因此,认为当施加高的张力而以高速度行进时,容易在粉末成型体的切断时产生裂纹或缺口。因此,锯线(金属线材)的直径优选为200μm以上。此外,锯线的直径越大,切削下料越增加,但能够进行正常的切断。
[0112]
另外,确认到为了比较,即使打算仅利用金属线材切断放置于大气中的粉末成型体,也不能正常地进行切断,行进的金属线材和粉末成型体的接触需要在液体(优选为油)中进行。
[0113]
图8表示如图5a和图5b所示那样,利用一根锯线将粉末成型体的上表面区域在水平横向上进行油中切断时的实验结果。“横向输送”为水平横向的切入速度,“线速度”为锯线的行进速度。在使用了直径250μm的锯线的情况下,若是300m/分钟的行进速度,则能够以100~300mm/分钟的切入速度得到没有裂纹的成型体片。另外,若是500m/分钟的行进速度,则能够以300mm~500/分钟的切入速度得到没有裂纹的成型体片。另外,即使是700m/分钟的行进速度,也能够以500mm/分钟的切入速度得到没有裂纹的成型体片。
[0114]
为了通过“横向输送”切取粉末成型体的上表面附近,优选粉末成型体具有充分的“硬度”。粉末成型体的硬度能够根据例如粉末成型时的成型压力或密度等进行评价。可知存在当处于空气中时(油等液体除外时)的粉末成型体的密度低于4g/cm3时,切断面变得不平滑之类的问题。因此,粉末成型体的密度优选为4g/cm3以上。
再多了解一些
本文用于企业家、创业者技术爱好者查询,结果仅供参考。