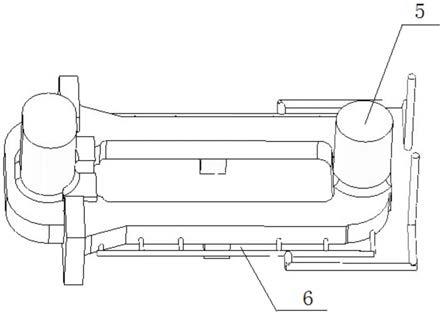
1.本发明涉及铸造技术领域,尤其涉及一种薄壁轧机机架的铸造方法。
背景技术:
2.不同类型的轧机机架,由于工作时承受的负荷较大,所以不仅对铸件的表面质量及尺寸精度要求都很严格,而且对铸件的内在质量要求更为严格,机架的所有加工表面都要进行超声波探伤检查和磁粉检查。铸件检查合格后,经粗加工,留一定的精加工余量方可。近年,我公司承揽了一批长度6040mm*宽度3500mm*高度350mm的机架,由于长度较长、高度较小,按照常规的铸造工艺方法,无法满足客户要求。时间紧,任务重,针对存在的制作难点,公司组织进行攻关,对铸造工艺上做了很大改进,打破了机架常规的铸造工艺生产方法。大型薄壁机架铸造的变形问题,一直困扰着机架的毛坯铸件的生产。
技术实现要素:
3.本发明的目的在于提供一种薄壁轧机机架的铸造方法,解决了机架长度过长,吊运过程中模型变形问题;保证机架木模的精度和质量要求;减少机架铸造制型过程中的变形尺差;降低了生产成本;提高了生产效率;提高铸件产品质量。
4.为了达到上述目的,本发明采用以下技术方案实现:
5.一种薄壁轧机机架的铸造方法,该方法包括:
6.1)分成四个部分制作木型结构:机架上部、机架下部、两个立柱部分;
7.2)木型实样整体外皮采用活皮结构,中间滑道芯利用实样直接打制而成,机架上部、机架下部与两个立柱部分之间采用燕尾槽结构配合连接;
8.3)木型实样分部分制作完成以后,在木型平台预装,木型实样上刻出十字中心线,并在实样外皮刻出中间芯的十字轮廓线;
9.4)使用酯硬化型砂舂≥500mm厚底平面,舂制机架底平面时使用φ12mm~φ16mm铁棍,制作网格密度为(200mm~300mm)*(200mm~300mm)的网格状铁骨架放置在底平面砂型中,在舂制底平面时,做砂型底排气,从型芯底部引出两个不小于φ108mm的排气管,排气管上间隔200mm~300mm均匀割出排气孔,排气管上缠草绳;酯硬化型砂水分要求≤ 2.0wt%;
10.5)将四部分木型实样按燕尾槽位置组装好,放置到校平后的砂型底平面上,根据外皮吃砂量的厚度,在机架木型实样外侧设置挡铁,制作木条支在木型实样外壁与挡铁之间,防止实样位置偏离;
11.6)先舂机架里侧中间芯,每层放砂厚度为200~250mm,捣砂紧实,同时在砂中放置 80mm~100mm的泡沫条若干个,并在中间芯的中心部位在舂型时填入干砂块;
12.7)舂完中间芯之后,舂机架外皮砂型,制作上箱前,距木型实样上表面20~30mm绑好网子;上箱扎排气孔,排气孔底部距木型实样上表面5mm~10mm,同时设明排气道;网子的网格密度为(200~300mm)*(200~300mm);
13.8)在大冒口底部铸件下表面网格状铁骨架下部放置条形外铁(700-900mm)* (1100-1200mm),防止冒口下部缩松缺陷产生,节约焊补精整费用,从而提高机架的使用寿命;
14.9)采用侧水口开放式浇注系统,直浇道φ150mm~φ160mm,横浇道φ110mm~φ120mm 环接,内浇道φ90mm~φ100mm,浇注系统全部采用陶瓷管;
15.10)浇注用钢水在电炉 lf精炼后,再经真空处理,排除其中大部分气体和非金属夹杂物;
16.11)采用φ90mm~φ100mm罐眼,浇注低温≤1550℃,浇注时间≤7分钟,冒口达到 1000mm~1100mm浇高后,用本炉钢水改由点冒口水口均匀点补冒口,本炉钢水点补冒口 20分钟以上。
17.所有面砂全部采用铬矿,厚度20~30mm;背砂采用酯硬化新硅砂,厚度200~300mm;其余全部采用酯硬化再生砂。
18.与现有技术相比,本发明的有益效果是:
19.1)减少厚大机架的裂纹缺陷;提高机架的使用寿命;节约焊补精整费用。
20.2)本发明所有面砂全部采用铬矿;背砂采用酯硬化新硅砂;其余全部采用酯硬化再生砂,降低了生产成本。
21.3)本发明简化了模型的制作和吊运过程,缩短了生产周期,提高了生产效率。
附图说明
22.图1是轧机机架的结构示意图。
23.图2是轧机机架铸造工艺图。
24.图3是图1中分割部位的截面图。
25.图中:1-机架上部、2-分割部位、3-立柱部分、4-机架下部、5-冒口、6-排气管。
具体实施方式
26.以下实施例用于具体说明本发明内容,这些实施例仅为本发明内容的一般描述,并不对本发明内容进行限制。
27.一种薄壁轧机机架的铸造方法,具体方法如下:
28.使用solidworks软件,将机架的订货机械零件图转化为三维立体图,使研究问题更直观化;
29.由于此机架长度过长(6060mm),而且厚度较低(360mm),按传统铸造工艺:实样 组芯的方案制作木型,会严重变形,无法吊运,不能保证铸件精度要求,因此重新设计铸造工艺方案:使用solidworks软件,将机架的订货机械零件图转化为三维立体图,使研究问题更直观化;根据机架结构重新制定机架铸造工艺,依据不同壁厚,冒口下部放置条形外冷铁,将机架补缩区域划分为三个热节待补缩区域,两侧头部厚壁部分设置两个保温冒口,中间部分设置两个冒口;使用magma软件进行最终的模拟确认,确定模拟后没有任何内部铸造缺陷,再进行生产。
30.1)分成四个部分制作木型结构:机架上部、机架下部、两个立柱部分。
31.2)木型实样整体外皮采用活皮结构,实样内外所有部位包括芯头都是活皮,活皮
最薄部位60mm,40稍度;机架上部、机架下部与两个立柱部分连接结构,采用燕尾槽结构连接形式配合。
32.四个部分均设置吊运装置,方便吊运运输,可以解决机架长度过长,吊运过程中木型变形的问题。注意实样部位的起吊装置要受力均匀,强度足够,保证起吊后模型不变形。
33.3)木型实样分部分制作完成以后,在木型平台预装,木型实样上刻出十字中心线,并在实样外皮刻出中间芯的十字轮廓线。
34.4)根据铸件木模尺寸,使用酯硬化型砂舂≥500mm厚底平面,酯硬化型砂水分要求≤2.0wt%,方可作业,舂制机架底平面时为了提高砂型强度,根据机架形状,使用φ12mm 铁棍,制作网格密度为200mm*200mm的网格状铁骨架放置在底平面砂型中,以此增加底平面砂型的强度,在舂制底平面时,做砂型底排气,从型芯底部均匀、对称的引出两个不小于φ108mm的排气管,排气管上间隔200mm均匀割出排气孔,排气管上缠草绳;舂实后,用木质板刮平,之后用远红外线水平测量仪校正底平面水平度。
35.5)将四部分木型实样按燕尾槽位置组装好,放置到校平后的砂型底平面上,根据外皮吃砂量的厚度(500mm~600mm),在机架木型实样外侧设置挡铁,替代专用砂箱为了防止舂里侧滑道芯时木模外涨,制作木条支在木型实样外壁与挡铁之间;同时按照木模中心线和砂型底平面中心线对齐的方法,来保证机架尺寸。
36.6)先舂机架中间芯,每层放砂厚度为200~250mm,捣砂紧实,同时放置80~100mm 的泡沫条数个,中间芯的中心部分在舂型时填干砂块,以此提高滑道芯的溃散性,防止机架因砂芯强度过硬收缩时而产生裂纹缺陷。
37.7)舂完里侧滑道芯之后,舂机架外皮砂型,距木型实样上表面20~30mm绑好网子;防止掉砂。网格密度为(200~300mm)*(200~300mm)。
38.8)上箱扎排气孔,排气孔底部距木型实样上表面5mm~10mm,同时设明排气道。
39.9)在大冒口底部铸件下表面网子下部放置条形外冷铁(700~900mm)*(1100~ 1200mm),防止冒口下部缩松缺陷产生,节约焊补精整费用,从而提高机架的使用寿命;
40.10)采用侧水口开放式浇注系统,直浇道φ150mm~φ160mm,横浇道φ110mm~φ 120mm环接,内浇道φ90mm~φ100mm,浇注系统全部采用陶瓷管。
41.11)合箱后,利用型腔探测仪检查砂型腔内是否有杂物;
42.12)保证钢水纯净度,除正常电炉 lf精炼外,钢水冶炼工艺,增加真空处理,最大限度的减少钢水中气体和夹杂物,提高钢水质量;
43.13)由于机架的高度仅360mm,为了保证机架的浇注速度,采用φ90mm~100mm罐眼,低温快浇,浇注温度≤1550℃,浇注时间≤7分钟,浇注冒口达到1000mm~1100mm浇高后,用本炉钢水改由点冒口水口均匀点补冒口,本炉钢水点补冒口20分钟以上,添加保温剂保温冒口,提高冒口补缩效果。
44.13)铸件打箱后,通过进行热处理工序的控制,对机架的装窑等方面进行质量控制;利用红外线水平仪初步校正机架的平面度;采用超声波ut探伤,保证内部无裂纹等超标缺陷。
45.14)采用超声波ut和磁粉探伤,保证内部和外部无裂纹等超标缺陷。
46.15)为了防止铸件表面粘砂,铸造工艺规定所有面砂全部采用铬矿砂,厚度20~30mm;背砂采用酯硬化新硅砂,厚度200~300mm;其余全部采用酯硬化再生砂。喷涂醇基涂
料2 遍,用煤气火表干;外冷铁需做好除锈,同时位置要准确。
47.本发明简化了特殊类型的机架铸件的铸造工艺过程,解决了该类型机架整体木模变形问题,保证了铸件精度。
再多了解一些
本文用于企业家、创业者技术爱好者查询,结果仅供参考。