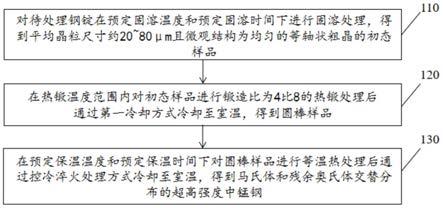
1.本技术涉及中锰钢的热处理及制备领域,特别涉及超高强度中锰钢及其制备方法。
背景技术:
2.优异力学性能是结构材料设计的首要目标,超高强度与适当韧/塑性的理想匹配,不仅提升材料的结构应用安全性,还减少材料用量,实现轻量化和节能减排,在中锰汽车钢领域,抗拉强度与断后伸长率的乘积(定义为强塑积,单位:积gpa
·
%)是其加工成形性和综合力学性能的关键评价指标。研究表明,中锰钢的强塑积由残余奥氏体含量及稳定性决定,如何获得大量亚稳残余奥氏体对于中锰钢实现强度-塑性优异匹配具有重要意义。
3.目前,中锰钢中的亚稳残余奥氏体通常采用逆相变处理、淬火-配分处理、以及多道次带温轧制并后续退火处理等热机械加工方法引入。通常,当残余奥氏体含量超过20%~35%时,相对显著的相变诱导塑性(trip)效应,从而获得较为可观的强塑积(25~40gpa
·
%)。但有限的均匀塑性仍无法满足超高强度结构的应用。然而,残余奥氏体含量的增加同时也会造成强度下降,仍旧很难满足超高强度结构应用的需要。同时,这种逆相变热机械加工处理方法,通常需要较长时间逆转变处理,因而加工周期较长、工艺的批次稳定性差。
4.此外,残余奥氏体含量及稳定性还可以通过合金成分优化设计,如增加c、mn、al、si等合金元素含量来加以实现,尤其7~12%mn以及0.15~0.5%c(质量分数)成分范围内的合金优化,使trip效应有效增强,中锰钢获得强塑性匹配得以进一步提高。然而,这种合金优化方法造成了原材料及其冶炼、加工成本的显著增加。
技术实现要素:
5.本技术的目的在于本发明提出一种超高强度中锰钢及其制备方法,该制备方法为一种超高强度中锰钢的控冷淬火方法,通过短时高温逆相变保温后控制冷却速度淬火处理,优化薄膜状残余奥氏体的体积分数,并调控高密度异质界面分布,制备形成异质层片结构。在使役/变形过程中,异质层片结构诱导产生额外加工硬化效应,实现强塑性协同提高。异质层片结构中锰钢具有较低的原材料和生产成本,可以通过常规生产工艺加工,适合于超高强度(拉伸屈服强度≥1.4gpa)结构应用。
6.本技术的实施例是这样实现的:
7.第一方面,本技术提供一种超高强度中锰钢的控冷淬火处理方法,其包括:
8.对待处理钢锭在预定固溶温度和预定固溶时间下进行固溶处理,得到平均晶粒尺寸约20~80μm且微观结构为均匀的等轴状粗晶的初态样品;
9.在热锻温度范围内对所述初态样品进行锻造比为4~8的热锻处理后通过第一冷却方式冷却至室温,得到圆棒样品;
10.在预定保温温度和预定保温时间下对所述圆棒样品进行等温热处理后通过控冷
淬火处理方式冷却至室温,得到马氏体和残余奥氏体交替分布的超高强度中锰钢。
11.可以理解,本技术公开了一种超高强度中锰钢的控冷淬火处理方法,将待处理钢锭经过热机械变形后进行等温热处理和冷却处理,获得马氏体和微量残余奥氏体交替分布的超高强度中锰钢,实现了约2gpa的抗拉强度和10%-18%的断后延伸率的优异力学性能。整个工艺过程仅通过简单的热机械加工、等温热处理和冷却处理,大幅度降低了生产难度,同时廉价的原材料也高度节约了成本,非常适合推广应用到工业生产。
12.在本技术可选的实施例中,所述待处理钢锭包括碳元素、锰元素、磷元素、硫元素和氮元素;所述碳元素体积分数为0.2%,所述锰元素体积分数为5%,所述磷元素体积分数为0.008%,所述硫元素体积分数为0.002%,所述氮元素体积分数为0.003%。
13.其中,上述待处理钢锭可以在25公斤真空感应炉中经过熔炼和铸锭而成。
14.在本技术可选的实施例中,所述固溶温度为1100℃~1250℃,所述预定固溶时间为2-6小时。
15.在本技术可选的实施例中,所述热锻温度范围为850℃~1200℃。
16.在本技术可选的实施例中,所述第一冷却方式为空冷方式。
17.在本技术可选的实施例中,所述圆棒样品的截面直径为16mm。
18.在本技术可选的实施例中,所述控冷淬火冷却速率ν为0.5℃/s~50℃。
19.图2中,ν3为炉冷方式实现的最慢冷速约为0.5℃/s,ν1为随炉冷却方式实现的最快冷速约为50℃/s。所述控冷淬火冷却速率ν的设置范围在0.5℃/s≤ν≤50℃/s温度区间内。
20.在本技术可选的实施例中,所述预定保温温度与所述奥氏体化开始温度的差值在差值范围内,所述差值范围为20℃~50℃;所述等温热处理的持续时长在1小时至4小时范围内。
21.第二方面,本技术提供一种,该超高强度中锰钢由第一方面任一项所述的方法制成,其包括:交替分布的马氏体和奥氏体;所述奥氏体的体积分数小于5%。
22.可以理解,本技术公开了一种超高强度中锰钢,包括:交替分布的马氏体和奥氏体,其微观组织为镶嵌薄膜状奥氏体的异质层状马氏体组织。不同于将传统的块状或者板条结构,异质层片结构中细小的相间距表明较高的异质界面密度,同时微量残余奥氏体提供了可观的塑性。
23.有益效果:
24.本技术公开了一种超高强度中锰钢的制备方法,将待处理钢锭经过热机械变形后进行等温热处理和控冷淬火处理,获得马氏体和微量残余奥氏体交替分布的超高强度中锰钢。将传统的块状或者板条结构转化为异质层片结构,保留基体强度的异质界面,利用异质变形诱导加工硬化行为和尺度效应,获得低成本、超高强度中锰钢。整个工艺过程仅通过简单的热机械加工、等温热处理和控冷淬火处理,大幅度降低了生产难度,同时廉价的原材料也高度节约了成本,非常适合推广应用到工业生产。
25.本技术公开了一种超高强度中锰钢,包括:交替分布的马氏体和奥氏体,其微观组织为镶嵌薄膜状奥氏体的异质层状马氏体组织。不同于将传统的块状或者板条结构,异质层片结构中细小的相间距表明较高的异质界面密度,同时微量残余奥氏体提供了可观的塑性。
26.为使本技术的上述目的、特征和优点能更明显易懂,下文特举可选实施例,并配合
所附附图,作详细说明如下。
附图说明
27.为了更清楚地说明本技术实施例的技术方案,下面将对实施例中所需要使用的附图作简单地介绍,应当理解,以下附图仅示出了本技术的某些实施例,因此不应被看作是对范围的限定,对于本领域普通技术人员来讲,在不付出创造性劳动的前提下,还可以根据这些附图获得其他相关的附图。
28.图1是本技术提供的一种超高强度中锰钢制备方法的流程示意图;
29.图2是图1所示的一种超高强度中锰钢制备方法的温度控制流程示意图;
30.图3是残余奥氏体的体积分数为1.5%的超高强度中锰钢的扫描电子显微镜图像;
31.图4是残余奥氏体的体积分数为1.5%的超高强度中锰钢的亮场透射电子显微镜图像;
32.图5是残余奥氏体的体积分数为1.5%的超高强度中锰钢的暗场透射电子显微镜图像;
33.图6是图1方法所制备的超高强度中锰钢的拉伸工程应力-应变曲线示意图。
具体实施方式
34.下面将结合本技术实施例中的附图,对本技术实施例中的技术方案进行清楚、完整地描述,显然,所描述的实施例仅仅是本技术一部分实施例,而不是全部的实施例。基于本技术中的实施例,本领域普通技术人员在没有作出创造性劳动前提下所获得的所有其他实施例,都属于本技术保护的范围。
35.如图1所示,本技术提供一种超高强度中锰钢制备方法,其包括:
36.110、对待处理钢锭在预定固溶温度和预定固溶时间下进行固溶处理,得到平均晶粒尺寸约20~80μm且微观结构为均匀的等轴状粗晶的初态样品。
37.在本技术可选的实施例中,如表1所示,待处理钢锭包括碳元素、锰元素、磷元素、硫元素和氮元素;碳元素体积分数为0.2%,锰元素体积分数为5%,磷元素体积分数为0.008%,硫元素体积分数为0.002%,氮元素体积分数为0.003%。
38.表1待处理钢锭所包含的元素的体积分数
[0039][0040]
其中,上述待处理钢锭可以在25公斤真空感应炉中经过熔炼和铸锭而成。
[0041]
如图2所示,待处理钢锭在0时刻至t1时刻之间由室温t1升高至固溶温度t5进行固溶处理,固溶处理从时刻t1持续到时刻t2。在本技术可选的实施例中,固溶温度t5可以为1100℃-1250℃,固溶处理的持续时间可以为2-6小时。
[0042]
可以理解,待处理钢锭经过热处理可以转变为微观结构为均匀等轴状粗晶的初态
样品。
[0043]
120、在热锻温度范围内对初态样品进行锻造比为4比8的热锻处理后通过第一冷却方式冷却至室温,得到圆棒样品。
[0044]
步骤120为后续在保温相变引入充足的形变储能。
[0045]
如图2所示,在热锻温度范围(t4至t5)内对初态样品进行锻造比为4比8的热锻处理后通过第一冷却方式冷却至室温t1。在本技术可选的实施例中,第一冷却方式为空冷方式。
[0046]
在本技术可选的实施例中,热锻温度范围为850-1200℃,锻造比为4比8,圆棒样品的截面直径为16mm。
[0047]
130、在预定保温温度和预定保温时间下对圆棒样品进行等温热处理后通过控冷淬火处理方式冷却至室温,得到马氏体和残余奥氏体交替分布的超高强度中锰钢。
[0048]
在本技术可选的实施例中,控冷淬火冷却速率ν为0.5℃/s~50℃。
[0049]
图2中,ν3为炉冷方式实现的最慢冷速约为0.5℃/s,ν1为随炉冷却方式实现的最快冷速约为50℃/s。控冷淬火冷却速率ν的设置范围在0.5℃/s≤ν≤50℃/s温度区间内。在本技术可选的实施例中,预定保温温度与奥氏体化开始温度的差值在差值范围内,差值范围为20℃~50℃;等温热处理的持续时长在1小时至4小时范围内。
[0050]
可以理解,奥氏体经冷却后会发生马氏体转变,等温热处理后的圆棒样品经过冷却后,其中部分奥氏体会发生马氏体转变,未发生马氏体转变的即为残余奥氏体。由于冷却速度不同,因此采用不同的冷却方式可以制成残余奥氏体含量不同的超高强度中锰钢。
[0051]
如图3至图6所示,图3是残余奥氏体含量为1.5%的超高强度中锰钢的扫描电子显微镜(scanning electron microscope,sem)图像;图4是残余奥氏体含量为1.5%的超高强度中锰钢的亮场(bf)透射电子显微镜(transmission electron microscope,tem)图像;图5是残余奥氏体含量为1.5%的超高强度中锰钢的暗场(df)透射电子显微镜图像。可以看出残余奥氏体含量(体积分数)为1.5%的超高强度中锰钢的均匀超细马氏体板条和沿板条边界分布的薄膜状残余奥氏体。
[0052]
如图6所示,图6是图1方法所制备的超高强度中锰钢的拉伸工程应力-应变曲线示意图。其中,曲线500为冷轧量为86%的超细晶样品;曲线600为热锻态样品。主要参看曲线601,曲线601代表残余奥氏体体积分数为1.5%的超高强度中锰钢的拉伸工程应力-应变曲线。可以看出采用本方法制备的超高强中锰钢实现了约2gpa的抗拉强度和10%的断后延伸率的优异力学性能。
[0053]
可以理解,本技术公开了一种超高强度中锰钢的制备方法,将待处理钢锭经过热机械变形后进行等温热处理和冷却处理,获得马氏体和微量残余奥氏体交替分布的超高强度中锰钢。将传统的块状或者板条结构转化为异质层片结构,保留基体强度的异质界面,利用异质变形诱导加工硬化行为和尺度效应,获得低成本、超强高塑的超高强度中锰钢。整个工艺过程仅通过简单的热机械加工、等温热处理和冷却处理,大幅度降低了生产难度,同时廉价的原材料也高度节约了成本,非常适合推广应用到工业生产。
[0054]
本技术提供一种超高强度中锰钢,该超高强度中锰钢由第一方面任一项的方法制成,其包括:交替分布的马氏体和奥氏体;奥氏体的体积分数小于5%。
[0055]
可以理解,本技术公开了超高强度中锰钢,包括:交替分布的马氏体和奥氏体,其微观组织为镶嵌薄膜状奥氏体的异质层状马氏体组织。不同于将传统的块状或者板条结
构,异质层片结构中细小的相间距表明较高的异质界面密度,同时微量残余奥氏体提供了可观的塑性。
[0056]
本技术中的各个实施例均采用递进的方式描述,各个实施例之间相同相似的部分互相参见即可,每个实施例重点说明的都是与其他实施例的不同之处。尤其,对于装置、设备和介质类实施例而言,由于其基本相似于方法实施例,所以描述的比较简单,相关之处参见方法实施例的部分说明即可,这里就不再一一赘述。
[0057]
至此,已经对本主题的特定实施例进行了描述。其它实施例在所附权利要求书的范围内。在一些情况下,在权利要求书中记载的动作可以按照不同的顺序来执行并且仍然可以实现期望的结果。另外,在附图中描绘的过程不一定要求示出的特定顺序或者连续顺序,以实现期望的结果。在某些实施方式中,多任务处理和并行处理可以是有利的。
[0058]
在本公开的各种实施方式中所使用的表述“第一”、“第二”、“所述第一”或“所述第二”可修饰各种部件而与顺序和/或重要性无关,但是这些表述不限制相应部件。以上表述仅配置为将元件与其它元件区分开的目的。例如,第一用户设备和第二用户设备表示不同的用户设备,虽然两者均是用户设备。例如,在不背离本公开的范围的前提下,第一元件可称作第二元件,类似地,第二元件可称作第一元件。
[0059]
当一个元件(例如,第一元件)称为与另一元件(例如,第二元件)“(可操作地或可通信地)联接”或“(可操作地或可通信地)联接至”另一元件(例如,第二元件)或“连接至”另一元件(例如,第二元件)时,应理解为该一个元件直接连接至该另一元件或者该一个元件经由又一个元件(例如,第三元件)间接连接至该另一个元件。相反,可理解,当元件(例如,第一元件)称为“直接连接”或“直接联接”至另一元件(第二元件)时,则没有元件(例如,第三元件)插入在这两者之间。
[0060]
以上描述仅为本技术的可选实施例以及对所运用技术原理的说明。本领域技术人员应当理解,本技术中所涉及的发明范围,并不限于上述技术特征的特定组合而成的技术方案,同时也应涵盖在不脱离上述发明构思的情况下,由上述技术特征或其等同特征进行任意组合而形成的其它技术方案。例如上述特征与本技术中公开的(但不限于)具有类似功能的技术特征进行互相替换而形成的技术方案。
[0061]
以上所述仅为本技术的可选实施例而已,并不用于限制本技术,对于本领域的技术人员来说,本技术可以有各种更改和变化。凡在本技术的精神和原则之内,所作的任何修改、等同替换、改进等,均应包含在本技术的保护范围之内。
再多了解一些
本文用于企业家、创业者技术爱好者查询,结果仅供参考。