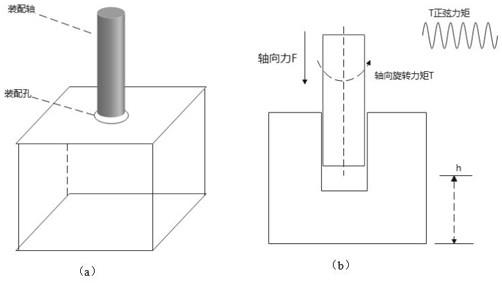
1.本发明涉及机器人力控装配领域,具体地,涉及机器人力控轴孔装配方法及系统。
背景技术:
2.在工业领域,大量零部件加工完成后需要进行装配,为满足自动化需求,工业机器人已经广泛用于装配领域。由于零件存在加工精度不高,一致性差的问题,使用传统工业机器人装配,容易装配失败,造成零件损坏问题。目前实现机器人柔顺装配的技术主要有主动柔顺和被动柔顺。被动柔顺主要是由机械结构实现。主动柔顺通过控制机器人与外界接触力实现。针对表面平整度不高或者有凸起的工件,如何提供一种力控装配方法,是当前需要解决的技术问题。
3.专利文献cn110449882b(申请号:201910713980.2)公开了一种结合力控的搜索装配方法,包括如下步骤:搭建柔性装配平台;将夹持工件的末端执行器的质量和惯性矩阵补偿给机器人控制器;协作机器人开始执行力控搜索装配,包括以下阶段:由协作机器人夹持第一工件到达待装配的第二工件上方的同轴心位置;将控制方式调整为力位混合控制,自动查找出第一工件的轴和第二工件的孔对齐的位置;将第一工件的轴和第二工件的孔对齐后,采用z方向力控模式,将第一工件的轴向下插入第二工件的孔中;通过检测z方向的位置判断是否装配完成,如果装配成功则协作机器人松开第一工件后退出。该专利与本发明相比,力控方法不同,该专利采用关节力矩传感器,成本较高。同时该专利在搜索阶段没有考虑搜索平面不平整的处理方法。
4.专利文献cn105643267a(申请号:201410632155.7)公开了一种机械手力控制装配装置及装配方法,其中机械手力控制装配装置包括:带有完整活动机构的机械手主体、控制系统、力传感器、夹手和设有夹具的装配平台;控制系统安装于机械手主体的内部;力传感器安装于机械手主体的端部且与控制系统连接;夹手安装于力传感器上;装配平台设于机械手主体的侧方,位于夹手的正下方。该专利与本发明相比,搜索路径为螺旋轨迹,螺旋轨迹中预设装配点。
5.专利文献cn106335057b(申请号:201610857074.6)公开了一种基于实时力控的装配机器人全空间柔顺插孔控制方法,步骤为:利用六维腕力传感器、实时通信软件包等搭建装配机器人螺栓插孔实时力控系统;采用基于标准位置的重力补偿方法,消除机器人全空间作业时重力分量对六维力传感器读数的影响;通过对插孔任务中接近、寻孔、插入与插入完成四个阶段的受力分析与力/位混合控制策略设计,避免螺栓插孔过程中常见的卡阻与契紧现象,提高机器人插孔作业成功率和效率;在多维力时间序列窗口中采用基于支持向量机的检测器实现寻孔完成状态自动检测,确保寻孔与插孔两个子任务的准确切换。该专利与现有技术相比,基于支持向量机的检测器自动检测寻孔完成状态。
6.专利文献cn109366488a(申请号:201811494757.5)公开了一种面向机器人装配的叠加振荡力笛卡尔阻抗控制方法,所述方法包括以下步骤:步骤一、针对装配组件的插入阶段,结合阻抗控制原理进行动力学建模;步骤二、在笛卡尔空间对机械臂的组件装配系统建
设置为0时,则工件轴轴心方向以恒力向下插入孔中。
14.根据本发明提供的一种机器人力控轴孔装配系统,包括:模块m1:搭建机器人轴孔装配平台,所述机器人轴孔装配平台包括机器人本体、机器人控制器、六维力传感器以及机器人末端执行器;模块m2:将机器人末端执行器和待装配轴的质量、质心参数传入机器人控制器;模块m3:机器人本体到达指定工位夹取待装配轴,然后开始执行力控轴孔装配;包括以下阶段:接近阶段、搜索阶段以及插入阶段;所述接近阶段:机器人通过位置控制的控制方式,利用机器人末端执行器夹持待装配轴移动到装配工件孔的上方;所述搜索阶段:控制机器人夹持工件轴在预设周围内以平面螺旋或圆弧路径运动,工件轴轴心方向以正弦力跳动搜索孔的位置,减小工件表面的阻塞;所述插入阶段:控制机器人夹持工件轴在工件轴轴心方向以恒力向下插入孔中,为了减少插入过程阻塞,绕工件轴的轴心方向设置正弦力矩。
15.优选地,所述机器人控制器控制机器人运行;所述六维力传感器采集装配的接触力;末端执行器夹持待装配轴。
16.优选地,所述搜索阶段采用:机器人控制方式切换为力位混合控制,机器人夹持工件轴的轴心方向设置力控模式,控制力模型设置为正弦力f;工件轴的圆周平面为位置控制模式,设置螺旋或者圆弧搜索路径;分别计算位置控制回路和力控制回路;力控制回路的控制力经过导纳控制器转化为位置偏差,将位置偏差叠加到位置控制回路,并输入至机器人控制器,机器人夹持工件轴在待装配孔圆周平面预设范围内搜索,当轴心方向的高度小于预设值,则机器人搜索到装配孔,工件轴的圆周平面搜索路径取消;所述正弦力f采用:f=offset amplitude*sin(period)其中,offset表示正弦力的偏置;amplitude表示正弦力的幅值;period表示正弦周期。
17.优选地,所述插入阶段采用:保留工件轴的轴心方向控制力,计算力控制回路的控制力和力矩,经过导纳控制器转化为位置偏差,将位置偏差叠加到位置控制回路得到轴插入装配孔路径,并将轴插入装配孔路径输入到机器人控制器,机器人夹持工件轴插入装配孔中,当轴心方向的高度小于预设值,机器人完成轴孔装配;所述力控制回路的力矩采用:torque=offset’ amplitude’*sin(period’)其中,torque表示绕工件轴的轴心方向设置的正弦力矩;offset’表示正弦力矩的偏置;amplitude’表示正弦力矩的幅值;period’为正弦周期;其中,amplitude’和period’设置为0时,则工件轴轴心方向以恒力向下插入孔中。
18.与现有技术相比,本发明具有如下的有益效果:1、本发明中力控搜索孔位方法,在搜索阶段轴向方向设置正弦跳动力,克服装配时接触面不平整造成搜索阻塞问题,提高装配成功率;2、本发明中力控插入孔位方法,在插入阶段轴心转动方向设置正弦力矩,克服装配插入时阻塞问题,提高装配成功率。
附图说明
19.通过阅读参照以下附图对非限制性实施例所作的详细描述,本发明的其它特征、目的和优点将会变得更明显:图1为力控示意图。
20.图2为搜索阶段示意图。
21.图3为插入阶段示意图。
具体实施方式
22.下面结合具体实施例对本发明进行详细说明。以下实施例将有助于本领域的技术人员进一步理解本发明,但不以任何形式限制本发明。应当指出的是,对本领域的普通技术人员来说,在不脱离本发明构思的前提下,还可以做出若干变化和改进。这些都属于本发明的保护范围。
23.实施例1根据本发明提供的一种机器人力控轴孔装配方法,如图1至3所示,包括:步骤s1:搭建机器人轴孔装配平台,所述机器人轴孔装配平台包括机器人本体、机器人控制器、六维力传感器以及机器人末端执行器;所述机器人控制器控制机器人运行;所述六维力传感器采集装配的接触力;末端执行器夹持待装配轴。
24.步骤s2:将机器人末端执行器和待装配轴的质量、质心参数传入机器人控制器;步骤s3:机器人本体到达指定工位夹取待装配轴,然后开始执行力控轴孔装配;包括以下阶段:接近阶段、搜索阶段以及插入阶段;所述接近阶段:机器人通过位置控制的控制方式,利用机器人末端执行器夹持待装配轴移动到装配工件孔的上方;所述搜索阶段:控制机器人夹持工件轴在预设周围内以平面螺旋或圆弧路径运动,工件轴轴心方向以正弦力跳动搜索孔的位置,减小工件表面的阻塞;具体地,所述搜索阶段采用:如图2所示,其中图2中(a)为搜索阶段示意图;图2中(b)为搜索阶段力控模式示意图;图2中(c)表示平面螺旋轨迹示意图;机器人控制方式切换为力位混合控制,机器人夹持工件轴的轴心方向设置力控模式,为了越过工件表面的凸起,减小搜索过程阻塞,控制力模型设置为正弦力f;工件轴的圆周平面为位置控制模式,设置螺旋或者圆弧搜索路径;分别计算位置控制回路和力控制回路;力控制回路的控制力经过导纳控制器转化为位置偏差,将位置偏差叠加到位置控制回路,并输入至机器人控制器,机器人夹持工件轴在待装配孔圆周平面预设范围内搜索,当轴心方向的高度小于预设值,即待装配轴的底部与装配孔底部之间的距离小于预设值时,则机器人搜索到装配孔,工件轴的圆周平面搜索路径取消。该搜索阶段轴向方向设置正弦跳动力,克服了装配时接触面不平整造成搜索阻塞问题,提高装配成功率。
25.具体地,所述正弦力f采用:f=offset amplitude*sin(period)其中,offset表示正弦力的偏置;amplitude表示正弦力的幅值;period表示正弦周期。
26.所述插入阶段:控制机器人夹持工件轴在工件轴轴心方向以恒力向下插入孔中,
为了减少插入过程阻塞,绕工件轴的轴心方向设置正弦力矩。
27.具体地,所述插入阶段采用:如图3所示,图3中(a)表示插入阶段示意图;图3中(b)表示插入阶段力控回路控制力和力矩示意图;保留工件轴的轴心方向控制力,计算力控制回路的控制力和力矩,经过导纳控制器转化为位置偏差,将位置偏差叠加到位置控制回路得到轴插入装配孔路径,并将轴插入装配孔路径输入到机器人控制器,机器人夹持工件轴插入装配孔中,当轴心方向的高度小于预设值,即待装配轴的底部与装配孔底部之间的距离小于预设值时,机器人完成轴孔装配;所述位置控制回路为取消掉螺旋或者圆弧搜索路径的回路;本发明在插入阶段轴心转动方向设置正弦力矩,克服装配插入时阻塞问题,提高装配成功率。
28.具体地,所述力控制回路的力矩采用:torque=offset’ amplitude’*sin(period’)其中,torque表示绕工件轴的轴心方向设置的正弦力矩;offset’表示正弦力矩的偏置;amplitude’表示正弦力矩的幅值;period’为正弦周期;其中,amplitude’和period’设置为0时,则工件轴轴心方向以恒力向下插入孔中。
29.本发明针对表面平整度不高或有凸起的工件,机器人能够自动搜索装配空位,完成装配任务。
30.本发明解决了由于工件表面平整度不高带来的装配阻塞过程问题。
31.根据本发明提供的一种机器人力控轴孔装配系统,包括:模块m1:搭建机器人轴孔装配平台,所述机器人轴孔装配平台包括机器人本体、机器人控制器、六维力传感器以及机器人末端执行器;所述机器人控制器控制机器人运行;所述六维力传感器采集装配的接触力;末端执行器夹持待装配轴。
32.模块m2:将机器人末端执行器和待装配轴的质量、质心参数传入机器人控制器;模块m3:机器人本体到达指定工位夹取待装配轴,然后开始执行力控轴孔装配;包括以下阶段:接近阶段、搜索阶段以及插入阶段;所述接近阶段:机器人通过位置控制的控制方式,利用机器人末端执行器夹持待装配轴移动到装配工件孔的上方;所述搜索阶段:控制机器人夹持工件轴在预设周围内以平面螺旋或圆弧路径运动,工件轴轴心方向以正弦力跳动搜索孔的位置,减小工件表面的阻塞;具体地,所述搜索阶段采用:机器人控制方式切换为力位混合控制,机器人夹持工件轴的轴心方向设置力控模式,为了越过工件表面的凸起,减小搜索过程阻塞,控制力模型设置为正弦力f;工件轴的圆周平面为位置控制模式,设置螺旋或者圆弧搜索路径;分别计算位置控制回路和力控制回路;力控制回路的控制力经过导纳控制器转化为位置偏差,将位置偏差叠加到位置控制回路,并输入至机器人控制器,机器人夹持工件轴在待装配孔圆周平面预设范围内搜索,当轴心方向的高度小于预设值,即待装配轴的底部与装配孔底部之间的距离小于预设值时,则机器人搜索到装配孔,工件轴的圆周平面搜索路径取消。该搜索阶段轴向方向设置正弦跳动力,克服了装配时接触面不平整造成搜索阻塞问题,提高装配成功率。
33.具体地,所述正弦力f采用:f=offset amplitude*sin(period)
其中,offset表示正弦力的偏置;amplitude表示正弦力的幅值;period表示正弦周期。
34.所述插入阶段:控制机器人夹持工件轴在工件轴轴心方向以恒力向下插入孔中,为了减少插入过程阻塞,绕工件轴的轴心方向设置正弦力矩。
35.具体地,所述插入阶段采用:保留工件轴的轴心方向控制力,计算力控制回路的控制力和力矩,经过导纳控制器转化为位置偏差,将位置偏差叠加到位置控制回路得到轴插入装配孔路径,并将轴插入装配孔路径输入到机器人控制器,机器人夹持工件轴插入装配孔中,当轴心方向的高度小于预设值,即待装配轴的底部与装配孔底部之间的距离小于预设值时,机器人完成轴孔装配;所述位置控制回路为取消掉螺旋或者圆弧搜索路径的回路;本发明在插入阶段轴心转动方向设置正弦力矩,克服装配插入时阻塞问题,提高装配成功率。
36.具体地,所述力控制回路的力矩采用:torque=offset’ amplitude’*sin(period’)其中,torque表示绕工件轴的轴心方向设置的正弦力矩;offset’表示正弦力矩的偏置;amplitude’表示正弦力矩的幅值;period’为正弦周期;其中,amplitude’和period’设置为0时,则工件轴轴心方向以恒力向下插入孔中。
37.本发明针对表面平整度不高或有凸起的工件,机器人能够自动搜索装配空位,完成装配任务。
38.本发明解决了由于工件表面平整度不高带来的装配阻塞过程问题。
39.在本技术的描述中,需要理解的是,术语“上”、“下”、“前”、“后”、“左”、“右”、“竖直”、“水平”、“顶”、“底”、“内”、“外”等指示的方位或位置关系为基于附图所示的方位或位置关系,仅是为了便于描述本技术和简化描述,而不是指示或暗示所指的装置或元件必须具有特定的方位、以特定的方位构造和操作,因此不能理解为对本技术的限制。
40.本领域技术人员知道,除了以纯计算机可读程序代码方式实现本发明提供的系统、装置及其各个模块以外,完全可以通过将方法步骤进行逻辑编程来使得本发明提供的系统、装置及其各个模块以逻辑门、开关、专用集成电路、可编程逻辑控制器以及嵌入式微控制器等的形式来实现相同程序。所以,本发明提供的系统、装置及其各个模块可以被认为是一种硬件部件,而对其内包括的用于实现各种程序的模块也可以视为硬件部件内的结构;也可以将用于实现各种功能的模块视为既可以是实现方法的软件程序又可以是硬件部件内的结构。
41.以上对本发明的具体实施例进行了描述。需要理解的是,本发明并不局限于上述特定实施方式,本领域技术人员可以在权利要求的范围内做出各种变化或修改,这并不影响本发明的实质内容。在不冲突的情况下,本技术的实施例和实施例中的特征可以任意相互组合。
再多了解一些
本文用于企业家、创业者技术爱好者查询,结果仅供参考。