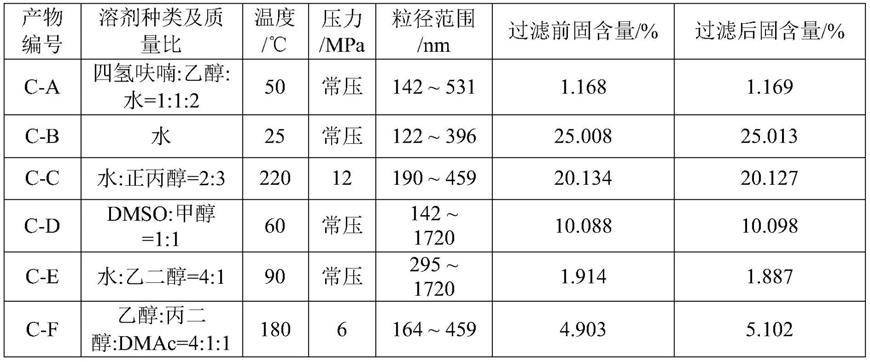
1.本发明涉及全氟磺酸树脂应用领域,具体而言,涉及一种全氟磺酸树脂的纯化方法及得到的全氟磺酸树脂。
背景技术:
2.目前新型商业化的质子交换膜是以膨体聚四氟乙烯微孔膜(简称“e-ptfe”)为支撑层,支撑层与改性全氟磺酸树脂制得的复合质子交换膜。通常将全氟磺酸树脂分散在溶剂中得到分散液,将分散液与e-ptfe复合干燥成型即得到复合质子交换膜。全氟磺酸树脂分散液是制备高性能的质子交换膜和催化剂浆料的基础。
3.目前已公开的浓缩全氟磺酸树脂分散液的方法是通过加热挥发溶剂,降低分散液中溶剂含量实现的(比如申请号为201310074511.3、201910320776.4的中国专利申请)。这种方法效率低,能耗高,产生大量废气。
4.全氟磺酸树脂在制备使用过程中会残留或引入各类杂质,这些杂质应该设计相应的提纯方案。现有技术主要是提纯全氟磺酸树脂固体,对分散液的提纯较少。提纯全氟磺酸树脂固体的过程复杂,且会使用到浓硫酸、双氧水等强酸性、强氧化性管制类化学品。且上述提纯方法不能有效除去小分子量杂质,包括乳化剂、有机和/或无机盐或无机酸、未反应的引发剂残余物和/或分解产物、稳定剂、分子量调节剂、单体、加工助剂和低聚物。
5.三爱富公司在中国专利申请cn112608494a中使用离心机分离分散液中的微小颗粒,提高了分散液的存储稳定性,最终的分散液产物静置半年不会析出沉淀物。离心分离除去全氟磺酸树脂分散液中的大粒径颗粒有助于提高分散液的稳定性。但该方法只能除去密度大的颗粒,不能有效控制除去颗粒的粒径,也不能去除小分子量杂质,导致全氟磺酸树脂的黄变指数较高。
技术实现要素:
6.本发明的主要目的在于提供一种全氟磺酸树脂的纯化方法及得到的纯化的全氟磺酸树脂,以解决现有技术中全氟磺酸分散液浓缩过程中能耗高和产生大量废气的问题。
7.为了实现上述目的,根据本发明的一个方面,提供了一种全氟磺酸树脂的纯化方法,该纯化方法包括:步骤s1,将全氟磺酸树脂分散于溶剂中,得到分散液a,分散液a中具有粒径大于10μm的大尺寸杂质、粒径小于2nm的小尺寸杂质和粒径在2nm~2μm之间的颗粒;步骤s2,通过第一分离去除分散液a中的大尺寸杂质,得到分散液b,第一分离的手段为离心、过滤和/或第一微滤;步骤s3,通过第二分离去除分散液b中的小尺寸杂质,得到全氟磺酸树脂浓缩物c,第二分离的手段为超滤和/或第二微滤。
8.进一步地,溶剂选自水、乙二醇、乙醇胺、三乙醇胺、聚乙二醇200、丙三醇、正丁醇、异丁醇、丁二醇、甲酰胺、六甲基磷三酰胺、n,n-二甲基甲酰胺、n,n-二甲基乙酰胺、二甲基亚砜、n-甲基吡咯烷酮、四氢呋喃、甲醇、乙醇、正丙醇、异丙醇中的一种或者多种,优选分散液a、分散液b中的溶剂的质量含量为30%~99.9%,分散液a、分散液b的粘度为1000mpa
·s以下,优选800mpa
·
s以下,进一步优选500mpa
·
s以下,更进一步优选200mpa
·
s以下。
9.进一步地,步骤s2包括:步骤s21,采用孔径为20~150μm的滤布对分散液a进行过滤,得到分散液a-1,优选过滤在重力作用下或1kpa~0.5mpa静压差下实施,进一步优选过滤在5kpa~0.2mpa静压差下实施,更优选在10kpa~0.1mpa静压差下实施;步骤s22,采用孔径为0.22~10μm的微滤膜和/或滤纸对分散液a-1进行第一微滤,得到分散液b,优选第一微滤的压力为0.05~0.5mpa,优选步骤s22包括:采用孔径为8~10μm的微滤膜和/或滤纸对分散液a-1进行初次微滤,得到分散液b-1;然后采用孔径为0.22~8μm的微滤膜对分散液b-1进行再次微滤,得到分散液b,优选再次微滤所用微滤膜的孔径为0.45~8μm,进一步优选为1~8μm,更优选为2~8μm。
10.进一步地,步骤s2包括:采用孔径为20~30μm的滤布对分散液a进行过滤,得到分散液b,优选过滤在重力作用下或1kpa~0.5mpa静压差下实施,进一步优选过滤在5kpa~0.2mpa静压差下实施,更优选在10kpa~0.1mpa静压差下实施;纯化方法还包括步骤s4,步骤s4包括:步骤s41,采用溶剂将全氟磺酸树脂浓缩物c稀释后,得到分散液c,优选分散液c中的溶剂的质量含量为30%~99.9%;步骤s42,采用孔径为0.22~10μm的微滤膜和/或滤纸对分散液c进行第一微滤,得到全氟磺酸树脂分散液d,优选第一微滤的压力为0.05~0.5mpa,优选步骤s42包括:采用孔径为8~10μm的微滤膜和/或滤纸对分散液c进行初次微滤,得到分散液c-1;采用孔径为0.22~8μm的微滤膜对分散液c-1进行再次微滤,得到分散液d,优选再次微滤所用微滤膜的孔径为0.45~8μm,进一步优选为1~8μm,更优选为2~8μm。
11.进一步地,步骤s3包括:采用孔径小于或等于0.22μm的第二微滤膜对分散液b进行第二微滤,得到全氟磺酸树脂浓缩物c;优选第二微滤膜的孔径≤0.12μm,进一步优选≤0.1μm,优选第二微滤的压力≤3mpa。
12.进一步地,步骤s3包括:采用超滤膜对分散液b进行超滤,得到全氟磺酸树脂浓缩物c,超滤膜的孔径为2nm~50nm,优选超滤的压力≤10mpa。
13.进一步地,溶剂为n-甲基吡咯烷酮,且分散液b中n-甲基吡咯烷酮的质量含量高于95%时,超滤膜的孔径为2nm~50nm;或者,溶剂为二甲基亚砜、n,n-二甲基乙酰胺或n,n-二甲基乙酰胺,且分散液b中溶剂的质量含量高于95%时,超滤膜的孔径为5nm~50nm;或者,溶剂为乙二醇、丙三醇或聚乙二醇200时,超滤膜的孔径为10nm~50nm;或者,溶剂为水、甲醇、乙醇、四氢呋喃、甲醇、乙醇、正丙醇或异丙醇,且分散液b中溶剂的质量含量超过20%时,超滤膜的孔径为20nm~50nm。
14.进一步地,纯化方法还包括对全氟磺酸树脂浓缩物c稀释后重复步骤s3一次或多次的过程。
15.进一步地,步骤s3包括:步骤s31,对分散液b进行一级分离,得到一级渗透物和一级保留物;步骤s32,对一级渗透物进行二级分离,得到二级渗透物和二级保留物;步骤s33,重复步骤s32的操作对n级渗透物进行n 1级分离,得到n 1级渗透物和n 1级保留物,n为整数,且2≤n≤10,优选2≤n≤8,更优选2≤n≤6,第m级分离所用分离膜孔径大于第m 1级分离所用分离膜孔径,1≤m≤n,优选一级分离的分离膜孔径为0.1μm~10μm,优选为0.22μm~4μm,更优选为0.45μm~2μm;最后一级分离的分离膜为孔径小于0.1μm的微滤膜或者孔径大于5nm的超滤膜。
16.根据本发明的另一方面,提供了一种纯化的全氟磺酸树脂,该纯化的全氟磺酸树脂采用上述的任一种纯化方法处理得到。
17.应用本发明的技术方案,既能除去全氟磺酸树脂分散液中的大粒径杂质,也能除去粒径较小的低分子量聚合物和小分子杂质,包括乳化剂、有机和/或无机盐或无机酸、未反应的引发剂残余物和/或分解产物、稳定剂、分子量调节剂、单体、加工助剂和低聚物,获得的氟磺酸树脂纯分散液在室温下可以长期稳定储存。由于小分子杂质的脱除,全氟磺酸树脂分散液的黄度得到改善,且提高了全氟磺酸树脂固体材料的热稳定性以及高温处理后黄度指数的稳定性。另外,采用本技术的全氟磺酸树脂纯化方法,与采用挥发溶剂浓缩提纯全氟磺酸树脂分散液相比,效率更高,不会产生大量废气,更为环保。采用经上述纯化方法得到的全氟磺酸树脂分散液制得的纯化的全氟磺酸树脂,黄度明显降低,且热处理后保持良好的色相,同时具备较好的质子传导率。
附图说明
18.构成本技术的一部分的说明书附图用来提供对本发明的进一步理解,本发明的示意性实施例及其说明用于解释本发明,并不构成对本发明的不当限定。在附图中:
19.图1示出了根据本发明的实施例3的薄膜m-h-3的dsc升温曲线;
20.图2示出了根据本发明的实施例3的薄膜m-h-1的dsc升温曲线;
21.图3示出了根据本发明的实施例3的钠型nafion117离子交换膜的dsc升温曲线;
22.图4示出了根据本发明的实施例3的酸型nafion117离子交换膜、薄膜m-h-2和薄膜m-h-4在80℃,95%相对湿度下的质子传导率;
23.图5示出了根据本发明的实施例5的全氟磺酸树脂分散液c-m的粒径分布;
24.图6示出了根据本发明的实施例5的微滤膜过滤后全氟磺酸树脂分散液h-m的粒径分布;
25.图7示出了根据本发明的实施例6的全氟磺酸树脂分散液c-m分级得到不同分散液的粒径分布;
26.图8示出了根据本发明的实施例7的全氟磺酸树脂分散液c-n的粒径分布;以及
27.图9示出了根据本发明的实施例7的氟磺酸树脂分散液c-n分级后得到的不同分散液的粒径分布。
具体实施方式
28.需要说明的是,在不冲突的情况下,本技术中的实施例及实施例中的特征可以相互组合。下面将参考附图并结合实施例来详细说明本发明。
29.如本技术背景技术所分析的,现有技术中全氟磺酸树脂分散液通过加热挥发溶剂的方式提纯,具有能耗高和产生大量污染气体的问题,为了解决该问题,本技术提供了一种全氟磺酸树脂的纯化方法及得到的纯化全氟磺酸树脂。
30.在本技术的一种典型的实施方式中,提供了一种全氟磺酸树脂的纯化方法,该纯化方法包括:步骤s1,将全氟磺酸树脂分散于溶剂中,得到分散液a,分散液a中具有粒径大于10μm的大尺寸杂质、粒径小于2nm的小尺寸杂质和粒径在2nm~2μm之间的全氟磺酸树脂颗粒;步骤s2,通过第一分离去除分散液a中的大尺寸杂质,得到分散液b,第一分离的手段
为离心、过滤和/或第一微滤;步骤s3,通过第二分离去除分散液b中的小尺寸杂质,得到全氟磺酸树脂浓缩物c,第二分离的手段为超滤和/或第二微滤。
31.本技术的全氟磺酸树脂纯化方法,既能除去全氟磺酸树脂分散液中的大粒径杂质,也能除去粒径较小的低分子量聚合物和小分子杂质,包括乳化剂、有机和/或无机盐或无机酸、未反应的引发剂残余物和/或分解产物、稳定剂、分子量调节剂、单体、加工助剂和低聚物,获得的氟磺酸树脂纯分散液在室温下可以长期稳定储存。由于小分子杂质的脱除,全氟磺酸树脂分散液的黄度得到改善,且提高了全氟磺酸树脂固体材料的热稳定性以及高温处理后黄度指数的稳定性。另外,采用本技术的全氟磺酸树脂纯化方法,与采用挥发溶剂浓缩提纯全氟磺酸树脂分散液相比,效率更高,不会产生大量废气,更为环保。
32.用于分散全氟磺酸树脂的溶剂可以参照现有技术进行选择。经研究发现,全氟磺酸树脂在n-甲基吡咯烷酮等非质子溶剂中表现出真溶液的特点,但在乙醇、正丙醇、水等溶剂中以高度溶剂化的颗粒存在,在本技术中,将全氟磺酸树脂与溶剂组成的体系定义为“全氟磺酸树脂分散液”。在本技术的一些实施例中,为了实现更佳的溶解分散效果,并精确控制全氟磺酸树脂颗粒的粒径,从而更彻底地将小尺寸杂质和大尺寸杂质去除,溶剂选自水、乙二醇、乙醇胺、三乙醇胺、聚乙二醇200、丙三醇、正丁醇、异丁醇、丁二醇、甲酰胺、六甲基磷三酰胺、n,n-二甲基甲酰胺(dmf)、n,n-二甲基乙酰胺(dmac)、二甲基亚砜(dmso)、n-甲基吡咯烷酮(nmp)、四氢呋喃、甲醇、乙醇、正丙醇、异丙醇中的一种或者多种,优选分散液a中、分散液b中的溶剂的质量含量为30%~99.9%。
33.另外,分散液a和分散液b的粘度受树脂化学组成、溶剂组成、分散液中树脂含量、溶解分散前固体树脂的结晶度以及溶解工艺等多种因素影响,分散液粘度过高流会导致流动性差,无法过滤,为了便于过滤、微滤或超滤,优选控制分散液a、分散液b的粘度为1000mpa
·
s以下,优选800mpa
·
s以下,进一步优选500mpa
·
s以下,更进一步优选200mpa
·
s以下。
34.上述步骤s2可以除去粒径大于20μm的大尺寸杂质,由于分散液中的大尺寸杂质,容易导致微滤膜或者孔径较小的过滤元件发生堵塞,在本技术的一些实施例中步骤s2包括:步骤s21,采用孔径为20~150μm的滤布对分散液a进行过滤,除去大尺寸杂质,得到分散液a-1,上述孔径的滤布目数为100目~625目。优选过滤在重力作用下或1kpa~0.5mpa静压差下实施,进一步优选过滤在5kpa~0.2mpa静压差下实施,更优选在10kpa~0.1mpa静压差下实施,提高过滤效率。然后步骤s22,采用孔径为0.22~10μm的微滤膜和/或滤纸对分散液a-1进行第一微滤,除去较大尺寸的杂质,得到分散液b,优选第一微滤的压力为0.05~0.5mpa。为了更彻底地去除大尺寸的杂质或大粒径的全氟磺酸树脂溶剂化颗粒,优选上述步骤s22包括:采用孔径为8~10μm的微滤膜和/或滤纸对分散液a-1进行初次微滤,得到分散液b-1;采用孔径为0.22~8μm的微滤膜对所述分散液b-1进行再次微滤,得到分散液b,优选再次微滤所用微滤膜的孔径为0.45~8μm,进一步优选为1~8μm,更优选为2~8μm。
35.经过上述两个步骤过滤除去大尺寸杂质后,分散液b具有良好的存储稳定性,可在室温下长期储存不析出沉淀。经过上述步骤s2处理后,所得到的具备良好储存稳定性的分散液b的粒径为2000nm以下,优选为1500nm以下,进一步优选为1200nm以下。然后再进行后续的步骤s3。
36.在本技术的一些实施例中,步骤s2包括:采用孔径为20~150μm的滤布对分散液a
进行过滤,除去大尺寸杂质,得到分散液a-1,上述孔径的滤布目数为100目~625目。优选过滤在重力作用下或1kpa~0.5mpa静压差下实施,进一步优选过滤在5kpa~0.2mpa静压差下实施,更优选在10kpa~0.1mpa静压差下实施,提高过滤效率。然后进行步骤s3去除小尺寸杂质。在完成小尺寸杂质去除后,进行步骤s4,步骤s4包括:步骤s41,采用溶剂将全氟磺酸树脂浓缩物c稀释后,得到分散液c,优选分散液c中的溶剂的质量含量为30%~99.9%;步骤s42,采用孔径为0.22~10μm的微滤膜和/或滤纸对分散液c进行第一微滤,得到全氟磺酸树脂分散液d,优选第一微滤的压力为0.05~0.5mpa。为了进一步彻底去除大尺寸杂质和大粒径全氟磺酸树脂溶剂化颗粒,优选步骤s42包括:采用孔径为8~10μm的微滤膜和/或滤纸对分散液c进行初次微滤,得到分散液c-1;采用孔径为0.22~8μm的微滤膜对分散液c-1进行再次微滤,得到分散液d,优选再次微滤所用微滤膜的孔径为0.45~8μm,进一步优选为1~8μm,更优选为2~8μm。也就是说,通过初次微滤和再次微滤再进一步对全氟磺酸树脂浓缩物进行纯化,进一步提高其纯度。分散液c中的溶剂和前述分散液a和分散液b中的溶剂优选相同,以有利于延续其中的全氟磺酸树脂的粒径。
37.通过步骤s3实现对小尺寸杂质的分离,可利用现有的微滤或者超滤手段进行,在一些实施例中,采用孔径小于或等于0.22μm的第二微滤膜对所述分散液b进行第二微滤,得到全氟磺酸树脂浓缩物c;优选第二微滤膜的孔径≤0.12μm,进一步优选≤0.1μm,优选第二微滤的压力≤3mpa。孔径越小,被去除的小尺寸杂质的粒径越小。在此步骤中,小于上述孔径的小尺寸杂质随着溶液透过微滤膜或超滤膜,全氟磺酸树脂被浓缩。
38.在本技术的一些实施例中,采用超滤膜对分散液b进行超滤,得到全氟磺酸树脂浓缩物c,超滤膜的孔径为2nm~50nm,优选超滤的压力≤10mpa,以提高超滤的效率。
39.全氟磺酸树脂分散液在生产过程中,会产生大量低固含量的废液,主要是清洗设备产生的。尽管通过加入大量水进行稀释能够达到废液处理标准,但这种方法不环保,且造成了树脂的浪费。这类低固含量(小于1%)的树脂分散液中,溶剂化颗粒间距离远,难以团聚,粒径小,难以使用微滤膜进行有效的截留。使用超滤膜对低固含量树脂分散液进行浓缩富集能够有效减少污染物的产生和生产过程中树脂的损耗。
40.由于全氟磺酸树脂在不同的溶剂中呈现的形式不同,选择不同的溶剂时,提供相应孔径的超滤膜能够提高超滤的效率和全氟磺酸树脂的回收率,在本技术的一些实施例中,溶剂为n-甲基吡咯烷酮,且分散液b中n-甲基吡咯烷酮的质量含量高于95%时,超滤膜的孔径为2nm~50nm。在一些实施例中,溶剂为二甲基亚砜、n,n-二甲基乙酰胺或n,n-二甲基乙酰胺,且分散液b中溶剂的质量含量高于95%时,超滤膜的孔径为5nm~50nm。
41.在一些实施例中,溶剂为乙二醇、丙三醇或聚乙二醇(200)时,超滤膜的孔径为10nm~50nm;在一些实施例中,溶剂为水、甲醇、乙醇、四氢呋喃正丙醇或异丙醇,且分散液b中溶剂的质量含量超过20%时,超滤膜的孔径为20nm~50nm。
42.在经过上述处理后,在一些时实施例中,可以纯化得到的全氟磺酸树脂浓缩物c粒径分布为5nm~7μm,以质量计,全氟磺酸树脂的含量为5%~50%,溶剂的含量为50%~95%时。由于浓缩过程中,渗透物带走了部分小分子杂质,分散液的黄度指数降低,浓缩物c的黄度指数为0.5以下,优选为0.3以下,甚至为0.2以下。
43.在本技术的一些实施例中,纯化方法还包括对全氟磺酸树脂浓缩物c稀释后重复步骤s3一次或多次的过程,通过多次的稀释和过滤过程,将全氟磺酸树脂中的小尺寸杂质
去除的更为彻底,进而提高对全氟磺酸树脂的纯度,其黄度指数和热稳定性均会明显改善。
44.在一些实施例中,在经过多次过滤后,所得全氟磺酸树脂浓缩物的粒径分布为5nm~7μm。以质量计,全氟磺酸树脂的含量为5%~50%,溶剂的含量为50%~95%。根据实施例中的方法测定分散液的黄度指数,由于杂质的减少,全氟磺酸树脂浓缩物的黄度指数为0.4以下,优选为0.2以,更优选为0.1以下。脱除溶剂后的全氟磺酸树脂固体的黄度指数为10以下,或者为5以下,甚至为2以下;将该全氟磺酸树脂固体在150℃处理30min,热处理后固体的黄度指数为20以下,或者为10以,甚至为5以下。通过多次过滤,还可以将全氟磺酸树脂分散液中不同粒径的全氟磺酸树脂分子分离出来,在本技术的一些实施例中,步骤s3包括:步骤s31,对分散液b进行一级分离,得到一级渗透物和一级保留物;步骤s32,对一级渗透物进行二级分离,得到二级渗透物和二级保留物;步骤s33,重复步骤s32的操作对n级渗透物进行n 1级分离,得到n 1级渗透物和n 1级保留物,n为整数且2≤n≤10,优选2≤n≤8,更优选2≤n≤6;其中,第m级分离所用分离膜孔径大于第m 1级分离所用分离膜孔径,1≤m≤n。大粒径的颗粒,包括大粒径的溶剂化的全氟磺酸树脂颗粒对于全氟磺酸树脂分散液,都是不利于存储、加工和直接使用的杂质,在一些实施例中,优选一级分离的分离膜孔径为0.1μm~10μm,优选为0.22μm~4μm,更优选为0.45μm~2μm;最后一个过滤单元可用于分离不同粒径的溶剂化全氟磺酸树脂颗粒,也可用于分离溶剂化全氟磺酸树脂颗粒与小分子杂质,最后一级分离的分离膜为孔径小于0.1μm的微滤膜或者孔径大于5nm的超滤膜。
45.利用两个以上不同孔径的超滤和/或微滤单元处理全氟磺酸树脂分散液,一方面可以实现对不同粒径全氟磺酸树脂分散液颗粒的层层分离,精确获得某一确定粒径分布范围的颗粒分散液;另一方面不同粒径分散液的加工性能、分散液物化性质和干燥成型后全氟磺酸树脂固体物化性质有一定差异,可根据应用领域精确选择合适粒径的分散液进行后续的加工与使用。例如,在制备以多孔聚合物材料为支撑层的复合离子交换膜中,可根据分散液的粒径选择合适的支撑层,也可根据支撑层的孔径选择合适粒径分布的全氟磺酸树脂分散液。
46.上述各实施例中所用微滤膜材料可以在现有技术中进行选择,例如微滤膜材料种类为醋酸纤维、硝化纤维素及其混合物、聚酰胺、聚偏氟乙烯、聚丙烯腈、聚碳酸酯或磷脂酰胆碱、聚醚砜、聚苯乙烯、聚丙烯、聚乙烯或磷脂酰乙醇胺、e-ptfe、聚酯和无机陶瓷材料(氧化锆、氧化铝、氧化钛、氧化硅等),还可利用铝、钨、银、不锈钢和增强的碳纤维作为膜材料。
47.超滤膜材料也可以在现有技术中进行选择,例如:天然高分子类,包括醋酸纤维、硝化纤维素及其混合物、壳聚糖;聚砜类,聚砜类材料是主链上含有砜基和芳环的高分子化合物,主要包括双酚a型聚砜、聚醚砜、酚酞型聚醚砜、磺化聚砜、聚砜酰胺等;聚烯烃类,主要有低密度聚乙烯、高密度聚乙烯、聚丙烯、聚丙烯腈、聚氯乙烯、聚偏氟乙烯、e-ptfe等;无机材料类有陶瓷、金属、沸石及碳素等。
48.本技术的全氟磺酸树脂既可以为酸型全氟磺酸树脂,也可以为碱金属型全氟磺酸树脂,其中酸型全氟磺酸树脂的结构通式为:
[0049][0050]
其中,m=0~6,n=2~5;
[0051]
碱金属型全氟磺酸树脂的结构通式为:
[0052][0053]
其中m=0~6,n=2~5,m为锂、钠、钾、铷、铯。
[0054]
在本技术的另外一种典型的实施方式中,提供了一种纯化的全氟磺酸树脂,该纯化的全氟磺酸树脂采用上述的任一种纯化方法处理得到。
[0055]
本技术的全氟磺酸树脂纯化方法,既能除去全氟磺酸树脂分散液中的大粒径杂质,也能除去粒径较小的低分子量聚合物和小分子杂质,包括乳化剂、有机和/或无机盐或无机酸、未反应的引发剂残余物和/或分解产物、稳定剂、分子量调节剂、单体、加工助剂和低聚物,获得的氟磺酸树脂纯分散液在室温下可以长期稳定储存。由于小分子杂质的脱除,全氟磺酸树脂分散液的黄度得到改善,且提高了全氟磺酸树脂固体材料的热稳定性以及高温处理后黄度指数的稳定性。另外,采用本技术的全氟磺酸树脂纯化方法,与采用挥发溶剂浓缩提纯全氟磺酸树脂分散液相比,效率更高,不会产生大量废气,更为环保。采用经上述纯化方法得到的全氟磺酸树脂分散液制得的纯化的全氟磺酸树脂,黄度明显降低,且热处理后保持良好的色相,同时具备较好的质子传导率。
[0056]
下面将结合实施例,进一步说明本技术提供的全氟磺酸树脂的纯化方法及得到的纯化全氟磺酸树脂的有益效果。
[0057]
本发明实施例中全氟磺酸树脂x中,m=0,n=2;全氟磺酸树脂y中,m=0,n=4。nafion117离子交换膜中,m=1,n=2。
[0058]
实施例1
[0059]
将全氟磺酸树脂x溶解分散在溶剂中,溶解分散时间为8h,依次使用500目滤布、10μm孔径微滤膜、5μm微滤膜和2μm微滤膜过滤除去大尺寸杂质,得到待浓缩处理的分散液,过滤压力均为0.1mpa,溶剂种类、溶解分散的温度及压力、分散液固含量及粒径分布见表1。
[0060]
表1
[0061][0062]
过滤前后的固含量是作为参考数据,由于过滤过程中,大颗粒杂质脱除会导致固含量减少,但是过滤过程也伴随着溶剂的挥发导致固含量增加,因此固含量的多少不是表征过滤是否成功的参数。
[0063]
使用微滤膜过滤全氟磺酸树脂x分散液,得到全氟磺酸树脂x的浓缩物,微滤膜的孔径、过滤的压力、浓缩产物粒径分布及固含量见表2。其中,透过微滤膜的渗透物液体的固含量均小于0.12%,浓缩前后分散液中全氟磺酸树脂质量损失小于0.2%。
[0064]
表2
[0065]
浓缩产物编号原分散液孔径/μm压力/mpa粒径范围/nm固含量/%d-ac-a0.083142~5315.045d-bc-b0.0562122~39640.133d-cc-c0.11190~53130.054d-dc-d0.10.5142~172020.305d-ec-e0.220.1295~172020.35d-fc-f0.10.4164~53120.52
[0066]
实施例2
[0067]
将1质量份的全氟磺酸树脂y在80℃溶解分散于9质量份nmp溶剂中,依次使用10μm和1μm的微滤膜在0.1mpa压力下过滤得到未经浓缩处理的全氟磺酸树脂y分散液c-g,分散液c-g的粒径为2.7nm~15.7nm。使用孔径为2nm的超滤膜,在2mpa压力下过滤分散液c-g,保留物为浓缩产物,亦即分散液d-g。
[0068]
分散液d-g的粒径为5.61nm~18.2nm,固含量为20.052%。透过微滤膜的渗透物液体的固含量小于0.08%,浓缩前后分散液中全氟磺酸树脂质量损失小于0.1%。
[0069]
实施例3
[0070]
将1质量份商业化的钠型nafion117离子交换膜、9.5质量份水和9.5质量份正丙醇混合,在高压釜中升温溶解分散,温度为240℃,压力为10mpa,溶解时间为6h,得到固含量为5.01%的钠型nafion117分散液。依次使用300目滤布、5μm和1μm的微滤膜在0.1mpa压力下过滤除去大尺寸杂质,得到待提纯处理的分散液c-h。分散液c-h中全氟磺酸树脂的粒径为220nm~615nm,黄度指数为0.38。
[0071]
将分散液c-h通过旋蒸浓缩得到固含量为20.06%的分散液c-h-1。将c-h-1分散液倒入到超平培养皿在80℃干燥成型得到厚度为178μm的薄膜m-h-1。薄膜m-h-1与商业化的
钠型nafion117离子交换膜厚度一致,均为178μm,薄膜m-h-1的黄度指数为2.57。将薄膜m-h-1在150℃热处理30min,黄度指数为9.35。薄膜m-h-1的dsc升温曲线见附图2,从120℃开始出现曲线的明显抖动,这种抖动从120~210℃都存在,测试曲线在较宽的温度范围内都没能回到正常基线水平,并且测试完成后的样品颜色明显加深,表明该样品从120℃处开始出现杂质的分解。附图3中钠型nafion117离子交换膜样品从140℃处开始出现杂质的分解。根据图1至3的曲线对比可以发现,dsc升温曲线在提纯前后发生变化,说明其对杂质是比较敏感的,进而证明本技术对小分子杂质提纯是有效的。
[0072]
将钠型nafion117离子交换膜和薄膜m-h-1分别浸泡在2mol/l的硫酸溶液中,各自在60℃搅拌1h,将钠离子置换为氢离子,用去离子水冲洗掉多余的酸得到酸型nafion117离子交换膜和m-h-2薄膜。酸型nafion117离子交换膜和m-h-2薄膜的质子传导率见附图4。
[0073]
使用孔径为1μm的微滤膜,在0.5mpa的压力下过滤分散液c-h,得到固含量为20.032%的c-h-1分散液,加入水/正丙醇溶剂(水:正丙醇=1:1)稀释c-h-1分散液使固含量降至5%
±
0.1%。重复浓缩-稀释操作5次得到5.02%固含量的分散液f-h-1。分散液f-h-1的黄度指数为0,粒径为220nm~615nm。
[0074]
将分散液f-h-1用孔径为0.1μm的微滤膜,在1mpa的压力下浓缩,得到固含量为35.08%的分散液f-h-2。分散液f-h-2的黄度指数为0,粒径为220nm~615nm。
[0075]
将分散液f-h-2倒入超平培养皿,在80℃下干燥成型,得到厚度为178μm的薄膜m-h-3。薄膜m-h-3与商业化的钠型nafion117离子交换膜厚度一致,均为178μm,薄膜m-h-3的黄度指数为0。将薄膜m-h-3在150℃热处理30min,黄度指数为0。薄膜m-h-3的dsc升温曲线见图1,测试仪器吸热峰设定为向下的峰,正常基线走向为微倾斜向下。图1中能够看到曲线线性平整光滑,仅有一个提纯处理过程造成结晶度改变后样品出现的微弱的冷结晶峰,出峰结束后能观察到明显的微斜向下的基线,未发现杂质的分解峰。
[0076]
将薄膜m-h-3浸泡在2mol/l的硫酸溶液中,在60℃搅拌1h,将钠离子置换为氢离子,用去离子水冲洗掉多余的酸,得到m-h-4薄膜。m-h-4薄膜的质子传导率见图4。
[0077]
通过对上述结果对比发现:经过微滤提纯后的分散液f-h-2和固体m-h-4黄度指数低,色相更好,热处理后固体m-h-4制品黄度指数无变化保持良好色相,而未经过微滤提纯的固体制品m-h-2薄膜黄度指数增加,色相变差。同时经过微滤提纯前后固体的dsc升温曲线也验证了经过微滤提纯后固体中杂质的有效脱除,经过微滤提纯后树脂制备的质子交换膜具备更高的质子传导率。即使没有经过微滤提纯,经过大分子杂质去除后,制得的离子交换膜的质子传导率也有改善。
[0078]
实施例4
[0079]
将1质量份的全氟磺酸树脂x在80℃溶解分散于9质量份单一溶剂中,单一溶剂分别为nmp、dmso、dmac和dmf,得到四种初始分散液,将各初始分散液依次使用20μm滤纸、10μm和2μm的微滤膜在0.1mpa压力下对初始分散液进行过滤,然后使用0.22μm的微滤膜在0.2mpa过滤,得到未经浓缩提纯处理除去小尺寸杂质的全氟磺酸树脂x分散液c-i、c-j、c-k和c-l,分散液c-i、c-j、c-k和c-l的黄度指数分别是0.41、0.35、0.31和0.36。
[0080]
利用超滤膜在一定压力下将单一溶剂全氟磺酸树脂x分散液c-i、c-j、c-k和c-l浓缩至30%
±
0.1%,加入溶剂稀释使固含量降至5%
±
0.1%。重复浓缩-稀释操作3次,得到浓缩至20%
±
0.1%的提纯后的单一溶剂全氟磺酸树脂x分散液,其中超滤膜孔径和压力以
及所得分散液的各项性质见表3。
[0081]
表3
[0082][0083]
可见,提纯后的分散液黄度指数低,色相更好,表明杂质被有效脱除。
[0084]
实施例5
[0085]
将1质量份的全氟磺酸树脂y加入到2质量份的水与3质量份的甲醇中,室温下溶解分散,得到的分散液依次使用500目滤布和10μm孔径的微滤膜在0.05mpa过滤得到全氟磺酸树脂分散液c-m。分散液c-m的粒径分布见附图5,呈现双峰分布,平均粒径为543.7nm。将分散液c-m分出一部分,于室温静置180天,出现凝胶状沉淀物,说明其中还有一部分容易引起凝胶的颗粒没有被去除。
[0086]
使用1μm的微孔滤膜过滤其余部分分散液c-m得到分散液h-m,粒径分布见附图6,呈现单峰分布,平均粒径为300.7nm。
[0087]
将分散液h-m室温静置180天未发现沉淀物析出或分层现象。可见,过滤除去粒径在1μm以上大粒径颗粒的分散液具备更好的存储稳定性。
[0088]
实施例6
[0089]
使用5个过滤单元处理实施例5得到的分散液c-m,5个过滤单元均为微滤膜,过滤压力为0.2mpa,其中第一过滤单元孔径为2μm,截留粒径大于2000nm的大颗粒,不截留分散液;第二过滤单元孔径为0.6μm,截留得到分散液j-m-2;第三过滤单元孔径为0.45μm,截留得到分散液j-m-3;第四过滤单元孔径为0.22μm,截留得到分散液j-m-4;第五过滤单元孔径为0.08μm,截留得到分散液j-m-5,透过第五过滤单元的液体为k-m-5。
[0090]
分级得到的分散液粒径分布见附图7,液体k-m-5未检测到粒径分布,第一过滤单元截留物为无法测试粒径的凝胶。通过不同孔径的微滤膜对全氟磺酸树脂分散液c-m的粒径进行了层层分级,得到了窄分布的分散液。
[0091]
实施例7
[0092]
将1质量份全氟磺酸树脂x加入到8质量份dmso和1质量份甲醇中,在室温下溶解分散,使用平均孔径为30μm的滤纸在0.1mpa压力下过滤,再用5μm的微滤膜在0.2mpa压力下过滤得到分散液c-n。分散液c-n的粒径分布见图8。
[0093]
使用2个过滤单元处理分散液c-n,第一过滤单元为微滤膜,孔径为0.22μm,过滤压力为0.1mpa,截留得到分散液j-n-1;第二过滤单元为超滤膜,孔径为16nm,过滤压力为1mpa,截留得到分散液j-n-2,透过第二过滤单元的液体为k-n-2。
[0094]
分级得到的分散液粒径分布见图9,液体k-n-2未检测到粒径分布。透过不同粒径的过滤单元对全氟磺酸树脂分散液c-n的粒径进行了层层分级得到了窄分布的分散液。
[0095]
实施例8
[0096]
将全氟磺酸树脂x溶解分散在不同溶剂中,配置固含量为0.1%
±
0.03%的分散液模拟低固含量废液,使用不同孔径的超滤膜,在0.5mpa压力下,经过2次超滤过程将其固含量浓缩至5%
±
0.1%,其中第1次超滤过程后分散液的固含量为1%
±
0.1%,第2次超滤过程后的固含量为5
±
0.1%。树脂的收率为浓缩后的分散液中树脂的质量与浓缩前分散液中树脂的质量之比。
[0097]
随着分散液固含量的增加,分散液中颗粒的粒径增大,使用较小孔径的超滤膜仍可进行浓缩,但是效率偏低,因此选用孔径更大的超滤膜进行第2次超滤浓缩。
[0098]
分散液溶剂组成,超滤膜的孔径以及浓缩后树脂的收率见表4。
[0099]
表4
[0100][0101]
对比例1
[0102]
将1质量份实施例3中的钠型nafion117加入到2质量份水和2质量份正丙醇中在高压釜中升温溶解分散,温度为240℃,压力为10mpa,溶解时间为6h,得到凝胶状产物。无法通过直接溶解分散的方法得到20%固含量的分散液。与实施例3对比可以发现,通过微滤技术浓缩稀分散液可以得到高固含量的分散液,而直接溶解分散制备高固含量分散液会形成凝胶。
[0103]
从以上的描述中,可以看出,本发明上述的实施例实现了如下技术效果:采用本技术的全氟磺酸树脂纯化方法,既能除去全氟磺酸树脂分散液中的大粒径杂质,也能除去粒径较小的低分子量聚合物和小分子杂质,包括乳化剂、有机和/或无机盐或无机酸、未反应的引发剂残余物和/或分解产物、稳定剂、分子量调节剂、单体、加工助剂和低聚物,获得的氟磺酸树脂纯分散液在室温下可以长期稳定储存。由于小分子杂质的脱除,全氟磺酸树脂分散液的黄度得到改善,且提高了全氟磺酸树脂固体材料的热稳定性以及高温处理后黄度指数的稳定性。另外,采用本技术的全氟磺酸树脂纯化方法,与采用挥发溶剂浓缩提纯全氟磺酸树脂分散液相比,效率更高,不会产生大量废气,更为环保。采用经上述纯化方法得到的全氟磺酸树脂分散液制得的纯化的全氟磺酸树脂,黄度明显降低,且热处理后保持良好的色相,同时具备较好的质子传导率。
[0104]
以上仅为本发明的优选实施例而已,并不用于限制本发明,对于本领域的技术人员来说,本发明可以有各种更改和变化。凡在本发明的精神和原则之内,所作的任何修改、等同替换、改进等,均应包含在本发明的保护范围之内。
再多了解一些
本文用于企业家、创业者技术爱好者查询,结果仅供参考。