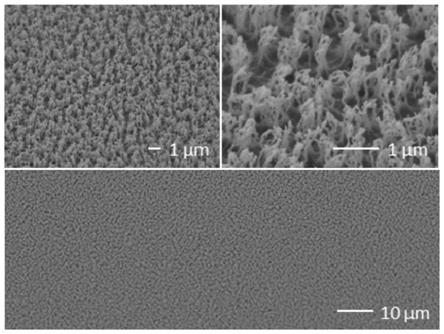
1.本发明涉及微纳加工领域与滤膜领域,具体涉及一种在聚合物材料表面制备纳米纤毛结构的方法。
背景技术:
2.表面工程是微纳加工技术的一个重要的应用方向。材料表面的纳米结构可以用于亲疏水改性或纳米目标物俘获等。
3.申请号为201510124275.0的发明专利公开了一种高深宽比柔性结构制造方法,包括:在硅基纳米纤毛阵列的基础上通过压印制备聚二甲基硅氧烷(pdms)模具,再利用pdms模具通过压印制备基于紫外光固化胶ormostamp材料的高深宽比柔性纳米纤毛。该方法需要制备模具、并经历两次压印,操作复杂,且未说明纳米纤毛具体尺寸信息。该方法需要通过改变硅基纳米纤毛阵列(即模具)的结构特征来调控纳米纤毛的长度和分布密度。这种调控方法成本高,所需时间长。
4.申请号为201710337687.1的发明专利公开了一种具有纤毛结构的复合涂层的制备方法,通过先将底涂涂覆在基底表面,再将面涂通过氧化铝多孔棒在涂层上连续滚动压印并固化涂覆在底涂上得到防水垢涂覆制品。氧化铝多孔棒为通过表面抛光、氧化等步骤获得的表面具有蜂窝状小孔的氧化铝棒。小孔的深度和分布密度决定了纤毛的长度和分布密度。因此,调控纤毛的长度和分布密度同样需要改变氧化铝多孔棒的结构特征。这种调控方法成本高,所需时间长。
5.申请号为cn202010628869.6的发明专利公开了一种微纳分级结构的聚合物材料及其制备方法,该方法包括:制备具有微纳分级结构的氧化铝模板,其中,在所述氧化铝模板上形成阵列化的微米孔并在所述微米孔内形成纳米孔结构;在所述氧化铝模板上进行聚合物的原位聚合,使聚合物充满所述氧化铝模板上的微米孔和纳米孔,以复制所述氧化铝模板的微纳分级结构;通过腐蚀液溶解去除所述氧化铝模板,得到具有微纳分级结构的聚合物材料。该方法同样需要通过改变氧化铝模板的结构特征(即微米孔和纳米孔的深度和分布密度)来调控微纳分级结构的长度和分布密度,同样成本高,所需时间长。
6.因此,需要开发一种在聚合物材料表面制备纳米纤毛结构的方法,其能够简单、快速且低成本地调控纳米纤毛的长度和分布密度。
技术实现要素:
7.本发明的目的是克服现有技术的缺点,提供一种在聚合物材料表面制备纳米纤毛结构的方法,该方法可简单、快速且低成本地调控纳米纤毛的长度和密度分布。
8.为了实现以上目的,本发明提供如下技术方案。
9.一种在聚合物材料表面制备纳米纤毛结构的方法,包括:
10.在金属衬底上设置聚合物薄膜,得到复合结构;
11.对所述复合结构整体进行反应离子刻蚀,从而形成纳米纤毛结构,或者,首先对所
述复合结构中的金属衬底进行溅射,然后对其中的聚合物薄膜进行刻蚀,从而形成纳米纤毛结构;以及
12.形成纳米纤毛结构后,去除所述金属衬底,从而得到表面具有纳米纤毛结构的聚合物材料。
13.本发明还提供通过上述方法获得的表面具有纳米纤毛结构的聚合物材料作为滤膜的用途。
14.本发明还提供一种增强聚合物材料表面粘附性的方法,包括:
15.通过上述方法在聚合物材料表面形成纳米纤毛结构。
16.本发明还提供一种超疏水表面的制备方法,包括:
17.对通过上述方法获得的表面具有纳米纤毛结构的聚合物材料进行表面疏水化改性处理。
18.与现有技术相比,本发明达到了以下技术效果:
19.本发明提供一种在聚合物材料表面制备纳米纤毛结构的方法,该方法的工艺参数高度可控,可简单、快速且低成本地调控纳米纤毛的长度和密度分布。本发明方法适用于大规模工业化生产。
20.本发明方法可在聚合物材料表面形成纳米纤毛结构,使得聚合物材料表面具有超亲水性(接触角接近于0
°
)。通过对具有纳米纤毛结构的聚合物材料进行表面疏水化改性处理,可进一步形成超疏水表面(接触角为150
°
以上)。本发明方法实际上也是一种对聚合物材料表面进行亲疏水改性的方法,纳米纤毛修饰可以实现对聚合物材料表面的亲疏水性扩展。本发明还可以通过在聚合物pvd金属前进行纳米纤毛结构修饰,增强金属与聚合物粘附性。
21.本发明的表面具有纳米纤毛结构的聚合物材料可实现对亚微米尺寸的目标物的俘获,因此可作为滤膜用于亚微米尺寸目标物(例如纳米颗粒、细菌、真菌或细胞外囊泡等)的分离。
附图说明
22.通过阅读下文优选实施方式的详细描述,各种其他的优点和益处对于本领域普通技术人员将变得清楚明了。附图仅用于示出优选实施方式的目的,而并不认为是对本发明的限制。而且在整个附图中,用相同的参考符号表示相同的部件。在附图中:
23.图1为本发明通过反应离子刻蚀“一步”制备纳米纤毛的原理示意图。
24.图2为本发明实施例1制得的表面具有纳米纤毛结构的聚对二甲苯c薄膜(具有微孔结构)的不同视角的电子扫描显微镜图。
25.图3为本发明实施例2制得的表面具有纳米纤毛结构的聚对二甲苯c薄膜(无微孔结构)的电子扫描显微镜图。
26.图4为无纳米纤毛结构且无微孔结构的聚对二甲苯c薄膜的电子扫描显微镜图。
27.图5为本发明实施例2制得的表面具有纳米纤毛结构的聚对二甲苯c薄膜(无微孔结构)的接触角测量照片。
28.图6为本发明实施例2制得的表面具有纳米纤毛结构的聚对二甲苯c薄膜(无微孔结构)经fdts表面改性处理后的接触角数据图。
29.图7为经fdts表面改性处理后的无纳米纤毛结构且无微孔结构的的聚对二甲苯c薄膜的接触角测量照片。
30.图8为未经fdts表面改性处理的无纳米纤毛结构且无微孔结构的聚对二甲苯c薄膜的接触角测量照片。
31.图9为实施例2制得的表面具有纳米纤毛结构的聚合物材料在俘获ps颗粒后的不同区域的电子扫描显微镜图。
32.附图标记说明
33.100为金属衬底,200为聚合物薄膜,300为溅射出的金属,400为金属微掩膜,500为纳米纤毛结构。
具体实施方式
34.以下,将参照附图来描述本公开的实施例。但是应该理解,这些描述只是示例性的,而并非要限制本公开的范围。此外,在以下说明中,省略了对公知结构和技术的描述,以避免不必要地混淆本公开的概念。
35.在附图中示出了根据本公开实施例的各种结构示意图。这些图并非是按比例绘制的,其中为了清楚表达的目的,放大了某些细节,并且可能省略了某些细节。图中所示出的各种区域、层的形状以及它们之间的相对大小、位置关系仅是示例性的,实际中可能由于制造公差或技术限制而有所偏差,并且本领域技术人员根据实际所需可以另外设计具有不同形状、大小、相对位置的区域/层。
36.在本公开的上下文中,当将一层/元件称作位于另一层/元件“上”时,该层/元件可以直接位于该另一层/元件上,或者它们之间可以存在居中层/元件。另外,如果在一种朝向中一层/元件位于另一层/元件“上”,那么当调转朝向时,该层/元件可以位于该另一层/元件“下”。
37.由于现有的纳米纤毛结构的制备方法通常需要通过改变模具或模板的结构特征来调控纳米纤毛的长度和分布密度,这导致成本高,所需时间长。为此,本发明提供一种新的在聚合物材料表面制备纳米纤毛结构的方法,具体包括如下步骤。
38.首先,在金属衬底上设置聚合物薄膜,得到复合结构;
39.所述金属衬底可以是钛、金、铂或铜。金属与聚合物薄膜的结合能力决定了其作为金属微掩模的可行性。常用的溅射靶材金属中,钛和聚合物的粘附性强于其它金属,因此,钛相比于其它金属更容易在聚合物表面形成微掩膜。
40.本发明对于所述聚合物薄膜没有特别限制,可以是任何表面需要形成纳米纤毛结构的的聚合物薄膜。例如,所述聚合物薄膜可以是聚对二甲苯(parylene)或聚酰亚胺(pi)。所述聚对二甲苯可以是聚对二甲苯c、聚对二甲苯d或聚对二甲苯n。薄膜形态包括但不限于平整薄膜、微孔薄膜、柔性弯曲薄膜等。
41.在一个具体实施方案中,将预先制备好的聚合物薄膜直接置于金属衬底上。在另一个具体实施方案中,在金属衬底上原位聚合形成聚合物薄膜。所述聚合物薄膜可根据本领域的常规技术手段制备。
42.接下来,对所述复合结构整体进行反应离子刻蚀,从而形成纳米纤毛结构,或者,首先对所述复合结构中的金属衬底进行溅射,然后对其中的聚合物薄膜进行刻蚀,从而形
成纳米纤毛结构。
43.在本发明中,可通过反应离子刻蚀“一步”形成纳米纤毛结构,或者可通过溅射和刻蚀的结合“二步”形成纳米纤毛结构。
44.反应离子刻蚀是以物理溅射为主并兼有化学反应的过程。在“一步”形成纳米纤毛结构的过程中,在刻蚀开始后,金属片溅射出的金属随机落在聚合物薄膜表面,形成随机的金属微掩膜,从而保护该位置的聚合物不被刻蚀;而没有被金属微掩膜保护的聚合物表面则被刻蚀。优选地,反应离子刻蚀的刻蚀气体为氧气。通过控制刻蚀射频功率、氧气流量和时间等,可控制纳米纤毛的长度和分布密度。通常纳米纤毛的长度越长,其分布密度越小;反之,纳米纤毛的长度越短,其分布密度越大。在一个具体实施方案中,反应离子刻蚀的刻蚀射频功率为30-350w,优选50-300w,更优选100-200w;氧气流量为10-90sccm,优选30-80sccm,更优选50-70sccm;刻蚀时间为20-500s,优选20-300s,更优选50-100s。
45.在“二步”形成纳米纤毛结构的过程中,溅射可为等离子体溅射或离子束溅射,优选为等离子体溅射,更优选为氧等离子体溅射。通过控制溅射的工艺参数如溅射功率、氧气流量等,可以控制图形化的金属微掩膜在聚合物薄膜上的分布密度,从而控制纳米纤毛的分布密度。溅射过程中,金属片溅射出的金属随机落在聚合物薄膜表面,形成图形化的金属微掩膜,保护了该位置的聚合物不被刻蚀;而没有被钛保护的聚合物表面则会被刻蚀。由于溅射出的金属尺寸极小且分布均匀,因此可以在聚合物薄膜表面形成均匀的纳米纤毛阵列,实现了聚合物表面的纳米结构功能化修饰。
46.溅射完成后,对所述聚合物薄膜进行刻蚀,从而形成纳米纤毛结构。
47.本发明对于刻蚀方法没有特别限制,任何刻蚀速率可控的刻蚀方法均适用于本发明。例如,刻蚀可为离子铣刻蚀、等离子刻蚀或深反应离子刻蚀。通过控制刻蚀功率和刻蚀时间等,可以控制纳米纤毛的长度。
48.本发明的纳米纤毛长度为0.3-2μm,优选0.3-1.2μm。
49.本发明通过反应离子刻蚀制备纳米纤毛的原理示意图如图1所示。从金属衬底100上溅射出的金属300随机落在聚合物薄膜200表面,形成图形化的金属微掩膜400,从而保护该位置的聚合物不被刻蚀;而没有被金属微掩膜保护的聚合物表面则被刻蚀,从而形成纳米纤毛结构500。
50.本发明通过在聚合物材料表面形成纳米纤毛结构,使得聚合物材料表面具有超亲水性(接触角接近于0
°
),为聚合物材料表面亲水改性提供了新的思路。
51.形成纳米纤毛结构后,去除所述金属衬底,从而得到表面具有纳米纤毛结构的聚合物材料。
52.本发明方法的工艺参数高度可控,可简单、快速且低成本地调控纳米纤毛的长度和密度分布。本发明方法可用于制备聚合物超亲水表面或超疏水表面。本发明方法适用于大规模工业化生产。
53.本发明还提供一种超疏水表面的制备方法,包括:
54.对通过上述制备方法获得的表面具有纳米纤毛结构的聚合物材料进行表面疏水化改性处理。
55.本发明对于表面疏水化改性处理的方法没有特别限制,例如可采用1h,1h,2h,2h-全氟癸基三氯硅烷(fdts)进行表面疏水化改性处理。经表面疏水化改性处理后,可得到接
触角为150
°
以上的超疏水表面。
56.本发明的纳米纤毛修饰可以实现对聚合物材料表面的亲疏水性扩展。材料表面的粗糙纳米结构能够增强其亲疏水特性,即,使亲液表面更亲液,疏液表面更疏液。这种现象的本质是表面粗糙结构的存在使得表观接触角与本征接触角之间出现一定的偏离,可用wenzel模型和cassie-baxter模型来解释。
57.由于本发明的表面具有纳米纤毛结构的聚合物材料可实现对亚微米尺寸的目标物的俘获,因此可作为滤膜用于亚微米尺寸目标物(例如纳米颗粒、细菌、真菌或细胞外囊泡等)的分离。
58.下面结合具体实施例对本发明作进一步说明,但本发明不限于此。
59.实施例1
60.首先,将预先制备好的具有微孔结构的聚对二甲苯c薄膜(孔径为8μm)放置在钛片衬底上,得到复合结构。
61.然后,对复合结构整体进行反应离子刻蚀,从而形成纳米纤毛结构,其中刻蚀气体为氧气,氧气流量为60sccm,刻蚀射频功率为150w,刻蚀时间为300s。所得纳米纤毛的长度约为1.2μm。
62.最后,去除钛片衬底,得到表面具有纳米纤毛结构的聚合物材料,其不同视角的电子扫描显微镜图如图2所示。
63.实施例2
64.按照实施例1的方法进行,不同之处在于,用预先制备好的无微孔结构的聚对二甲苯c薄膜替换具有微孔结构的聚对二甲苯c微孔薄膜。所得纳米纤毛的长度约为1.2μm。所制得的表面具有纳米纤毛结构的聚合物材料(无微孔结构)的电子扫描显微镜图如图3所示。无纳米纤毛结构且无微孔结构的聚对二甲苯c薄膜(即预先制备好的无微孔结构的聚对二甲苯c薄膜)的电子扫描显微镜图如图4所示。
65.测试表面具有纳米纤毛结构的聚合物材料与水的接触角,结果约为0
°
。这表明该聚合物材料经过纳米纤毛修饰后成为超亲水表面。该聚合物材料的接触角测量照片如图5所示。
66.实施例3
67.利用1h,1h,2h,2h-全氟癸基三氯硅烷(fdts)对实施例2制得的表面具有纳米纤毛结构的聚合物材料进行表面改性处理。具体地,利用原子层沉积表面改性设备(rpx-540,integrated surface technologies,usa)对所述聚合物材料表面进行疏水改性,其工作原理如下:首先将1h,1h,2h,2h-全氟癸基三氯硅烷(fdts)上的-cl替换为-oh(副产物hcl);随后,使fdts上的-oh与待修饰所述聚合物材料表面的-oh反应(副产物h2o),fdts与待修饰表面通过si-o键结合;最终,fdts上携带的大量-f基团将使材料表面疏水。
68.测试经fdts表面改性处理后的聚合物材料与水的接触角,结果为约160
°
。这表明经fdts表面改性处理后的聚合物材料具有超疏水表面,液滴可在薄膜表面自由滚动。经fdts表面改性处理后的聚合物材料的接触角测量照片如图6所示。
69.实施例4
70.利用实施例1制得的表面具有纳米纤毛结构的聚合物材料来俘获500nm聚苯乙烯颗粒。具体步骤如下。将500μl含有10
10
个500nm聚苯乙烯颗粒的溶液,经过孔径为8μm的微孔
滤膜(即实施例1制得的表面具有纳米纤毛结构的聚合物材料)(过滤面积为0.28cm2)过滤,在数秒的快速过滤过程中,滤膜表面的纳米纤毛结构可以俘获大量500nm聚苯乙烯颗粒。
71.俘获ps颗粒后的聚合物材料的电子扫描显微镜图如图9所示。可以看出,过滤过程中,本发明的表面具有纳米纤毛结构的聚合物材料可以俘获样本中大量亚微米目标物,这是表面没有纳米纤毛结构的微孔滤膜所难以实现的。
72.实施例5
73.本实施例所用到的聚合物材料为:实施例2中所使用的预先制备好的无微孔结构的聚对二甲苯c薄膜,以及实施例2制得的表面具有纳米纤毛结构的聚合物材料(无微孔结构)。
74.通过物理气相沉积法在上述两种聚合物材料表面分别沉积一层金属膜。之后,利用纳米划痕仪测试聚合物材料对金属的粘附性。
75.测试结果显示,预先制备好的无微孔结构的聚对二甲苯c薄膜与金属膜的粘附性为0.75mn,表面具有纳米纤毛结构的聚合物材料与金属膜的粘附性为5.45mn。可见,实施例2制得的表面具有纳米纤毛结构的聚合物材料与金属膜的粘附性可增大10倍左右,纳米划痕仪的测试数据下。
76.对比例1
77.利用1h,1h,2h,2h-全氟癸基三氯硅烷(fdts)对实施例2中使用的预先制备好的无微孔结构的聚对二甲苯c薄膜进行表面改性处理。
78.测试经fdts表面改性处理后的非微孔结构的聚对二甲苯c薄膜与水的接触角,结果为约90
°
。经fdts表面改性处理后的非微孔结构的聚对二甲苯c薄膜的接触角测量照片如图7所示。
79.测试未经fdts表面改性处理的非微孔结构的聚对二甲苯c薄膜与水的接触角,结果约为71
°
。非微孔结构的聚对二甲苯c薄膜的接触角测量照片如图8所示。
80.通过比较实施例2、实施例3和对比例1,如下表1所示,可以看出纳米纤毛修饰可以实现对聚对二甲苯c薄膜表面的亲疏水性扩展。
81.表1
[0082][0083]
以上所述,仅为本发明较佳的具体实施方式,但本发明的保护范围并不局限于此,任何熟悉本技术领域的技术人员在本发明揭露的技术范围内,可轻易想到的变化或替换,都应涵盖在本发明的保护范围之内。因此,本发明的保护范围应以所述权利要求的保护范围为准。
再多了解一些
本文用于企业家、创业者技术爱好者查询,结果仅供参考。