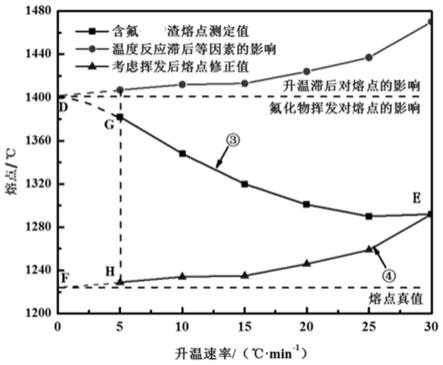
1.本发明属于冶金工程领域,具体涉及一种含易挥发组元炉渣挥发对熔点影响的评价方法。
背景技术:
2.火法冶金是大宗金属的主要制备方法,2020年的钢产量达到了10.53亿吨,有色金属铅产量达到664.3万吨,锌产量达到642.5万吨,有色金属铅锌产量达到1306.8万吨。火法冶金过程涉及大量不同的冶金熔体,包括金属熔体、熔融炉渣、熔锍、熔盐等。熔体的组成、物化性能不仅是冶金工艺控制的重要依据。以冶金炉渣为例,其成分及其物理化学性能对熔炼过程的温度控制、界面反应特性、夹杂物去除、甚至是熔炼过程顺行均息息相关。炉渣性能主要包括熔点、粘度、结晶性能和表面张力等,其中熔点是性能控制中最关键的参数。
3.如果炉渣中含有易挥发组元,在利用传统方法进行熔点测定时,升温和保温往往需要数个小时,会造成渣中的易挥发组元的大量挥发,据相关测定,部分钢铁冶金炉渣中的氟化物挥发量可达30%以上;铅及其化合物的挥发量可达40%以上,折算成挥发组元的挥发率将更加惊人。由此可知,这样的挥发对炉渣组成及性能的影响是十分明显的。在高温条件下这些挥发组元会持续挥发,导致炉渣组分不断发生变化,进而引起炉渣物性参数的变化,最终无法获得准确的炉渣熔化温度,即所谓的炉渣熔化温度“测不准”。高温挥发量较大的冶金熔体种类众多,典型的包括碱金属碱土金属及其合金、铅锌镉等及其合金、高锰合金、铅锌及其合金、含铅锌渣、含氟化物及钾钠氧炉渣、熔盐、富磷砷炉渣等。另,在部分特种冶金中,由于温度非常高,挥发问题也会凸显,对合金高温性能测定也会面临同样问题。所以本问题是一个涉及面广、影响范围宽的有待解决的共性基础理论问题。在挥发性火法冶金炉渣中,黑色金属冶炼过程尤以含氟炉渣显著;有色金属冶炼过程中尤以铅锌冶炼炉渣挥发组元最为显著。因此使用传统方法无法适应该类炉渣的熔点测定。
技术实现要素:
4.本发明的目的在于提供一种含易挥发组元炉渣挥发对熔点影响的评价方法,以解决火法冶金过程中使用含易挥发组元炉渣导致熔点测定不准确技术问题,从而获得更加准确的熔点,为涉及含有易挥发组元炉渣的火法冶金工艺控制及优化提供支撑。
5.为实现上述目的,本发明采用如下技术方案:
6.一种含易挥发组元炉渣挥发对熔点影响的评价方法,包括以下步骤:
7.测定不同升温速率下,同一含易挥发组元炉渣的熔点,得到含易挥发组元炉渣熔点与升温速率的对应关系曲线;
8.测定不同升温速率下,同一无易挥发组元炉渣的熔点,得到无易挥发组元炉渣熔点与升温速率的对应关系曲线;
9.根据无易挥发组元炉渣熔点与升温速率的对应关系曲线外推到升温速率为0时,得到升温速率趋向于零的无挥发炉渣熔点测定值;
10.根据含易挥发组元炉渣熔点与升温速率的对应关系曲线外推到升温速率为0时,得到升温速率趋向于零的易挥发炉渣熔点测定值;
11.将无易挥发组元炉渣熔点与升温速率的对应关系曲线下移至无挥发炉渣熔点测定值与易挥发炉渣熔点测定值重合,相同升温速率对应的两个炉渣熔点的差值为炉渣挥发对炉渣熔点的影响值;
12.将含易挥发组元炉渣熔点与升温速率的对应关系曲线的熔点减去炉渣挥发对炉渣熔点的影响值,得到不受挥发影响的熔点与升温速率的对应关系曲线,再外推出升温速率为0时,得到含易挥发组元炉渣的熔点理论值。
13.本发明的进一步改进在于:测定炉渣熔点与升温速率的对应关系时,采用半球点熔点测定法。
14.本发明的进一步改进在于:测定炉渣熔点与升温速率的对应关系时,采用差热分析、灰熔点测定法或锥形试样测定法中的一种。
15.本发明的进一步改进在于:所述升温速率的范围为5~30℃/min。
16.本发明的进一步改进在于:所述升温速率在5~30℃/min范围内,取4个或者4个以上的升温速率值进行升温。
17.本发明的进一步改进在于:所述升温速率最大为30℃/min或35℃/min。
18.本发明的进一步改进在于:所有熔点测定前后对待测炉渣进行试样称重,得到炉渣中挥发组元的含量变化,根据炉渣中挥发组元的含量变化和炉渣挥发对炉渣熔点的影响值评价含易挥发组元炉渣挥发对炉渣熔点的影响。
19.本发明的进一步改进在于:对待测炉渣进行试样称重时采用测量精度大于等于0.0001g的天平。
20.本发明的进一步改进在于:测定挥发性强的含易挥发组元炉渣熔点时,提高升温速率。
21.与现有技术相比,本发明至少具有以下有益效果:
22.1、充分考虑炉渣挥发组元对炉渣熔点的影响,获得更准确的熔点,实现炉渣挥发性组元对熔点的影响测定与评价。
23.2、可以利用现行的火法冶金用含易挥发组元炉渣熔点测定装置及测定方法,可以最大限度地利用已有的相关测定结果,降低测量难度。
24.3、对含易挥发组元炉渣对炉渣熔点的影响进行评价,并根据评价结果对测量的炉渣熔点进行处理,得到更加准确的熔点理论值。
附图说明
25.构成本发明的一部分的说明书附图用来提供对本发明的进一步理解,本发明的示意性实施例及其说明用于解释本发明,并不构成对本发明的不当限定。在附图中:
26.图1为使用半球点熔点测定法测定炉渣的示意图;
27.图2为无氟炉渣与含氟炉渣炼钢时温度反映滞后及成渣对熔点的影响评价示意图;
28.图3为无氟炉渣与含氟炉渣炼钢时炉渣中挥发性组元对熔点的影响评价示意图;
29.图4为无氟炉渣与含氟炉渣炼钢时挥发后的炉渣熔点理论值测算示意图。
具体实施方式
30.下面将参考附图并结合实施例来详细说明本发明。需要说明的是,在不冲突的情况下,本发明中的实施例及实施例中的特征可以相互组合。
31.以下详细说明均是示例性的说明,旨在对本发明提供进一步的详细说明。除非另有指明,本发明所采用的所有技术术语与本发明所属领域的一般技术人员的通常理解的含义相同。本发明所使用的术语仅是为了描述具体实施方式,而并非意图限制根据本发明的示例性实施方式。
32.本发明一种含易挥发组元炉渣挥发对熔点影响的评价方法,包括:
33.对炉渣熔点即熔化温度进行测量时采用半球点熔点测定法,即按照成分要求配制火法冶金用含易挥发组元炉渣,压制柱状试样,干燥后放入测定装置,然后按照一定的升温速率连续升温,观察试样形状变化。如图1所示,以cqkj—ⅱ型矿渣熔化温度特性测定仪测定为例,采用φ3
×
3mm的圆柱形试样,以设定速度(5~30℃/min)缓慢升温。当试样高度降低1/6,试样投影角部开始变圆时可将其对应温度作为初融温度;当其高度下降一半、试样上投影轮廓呈近似半球状时的对应温度称为半球点温度或熔化温度,以下统称半球点温度为熔点,而将高低降低为原试样高度的1/3或1/4称为完全熔化温度或流动温度。
34.基本测定方法:测定仍然采用常规冶金炉渣熔点yb/t186-2014《炉渣熔点的测定》的基本方法,但需要改变升温速率并进行无挥发组元炉渣对此样及挥发性炉渣的熔点测定。其它熔点测定方法,如差热分析、灰熔点测定方法、锥形试样(耐火锥)测定方法等也可使用。
35.所述的改变升温速率的步骤包括:
36.在5~30℃/min的升温速率范围内,采用常规半球点炉渣熔点测定方法,对同一炉渣试样分别进行不同升温速率下的熔点测定,得到熔点与升温速率的对应关系曲线,如图2中曲线2、曲线3所示。为了使得外推更加准确,升温速率应取不少于4个点,且最大升温速率应为30℃/min或35℃/min。在测定过程中,分别对测定前后的炉渣试样进行称重计量;
37.由于含易挥发组元炉渣挥发性存在差异。针对挥发性强的炉渣,升温速率低意味高温段持续时间久,挥发量大。因此针对挥发性强炉渣需要适当提高升温速率。
38.例如5℃/min-15℃/min升温速率下,强挥发性炉渣完全挥发。此时测定炉渣熔点非常相似;而在20℃/min升温速率下,炉渣未完全挥发,出现熔点差异。因此在测定挥发性强的炉渣熔点时,要适当提高升温速率。
39.所述的无挥发组元炉渣对此样的熔点测定步骤包括:
40.选取一组无挥发组元的炉渣,配制炉渣物料的粒度等应尽可能与含易挥发组元炉渣一致,在5~30℃/min的升温速率范围内,采用常规半球点冶金炉渣熔点测定方法,分别进行不同升温速率下的熔点测定,得到熔点与升温速率的对应关系曲线,如图2中曲线2所示。为了使得外推更加准确,升温速率应取不少于4个点,且最大升温速率应不低于30℃/min。在测定过程中,分别对测定前后的炉渣试样进行称重计量。
41.测定过程温度反映滞后、成渣及分熔等综合影响的评价:将得到的图2中曲线2外推到升温速率为零,得到一个升温速率趋向于零的熔点测定值,此值为炉渣升温速率无穷小,也就是无测定过程温度滞后的一个熔点测定值。以此值作水平线1,此直线1和曲线2之间的阴影区域就是炉渣熔点测定过程温度滞后带来的影响。以升温速率25℃/min为例,线
段ab对应的温度差就是升温速率为25℃/min,由于温度反映滞后引起的熔点测定偏差值。对同一渣样,随着升温速率的升高,熔点测定值升高,分熔也会导致测定结果偏高。因此利用绘制的曲线2与直线1可以对测定过程的温度反映滞后及分熔等的影响进行评价。如在熔点测定值中扣除温度反映滞后的影响值,则可得到不随升温速率变化而变化的该不挥发炉渣熔点理论值。
42.挥发影响的评价:对图2中的曲线3外推,得到点d,为挥发性炉渣升温速率趋向无穷小时的熔点测定值,此点可反映出挥发性炉渣在挥发组元充分挥发后所得到的熔点测定值,此时的炉渣其实组成已经发生零明显变化,而曲线3的其它点,则反映的是炉渣挥发、温度反映滞后、炉渣分熔等综合作用的结果。将曲线2及直线1一起平移,使得其在温度趋向于零的点与d点重合,得到图3所示的结果。此时平移后的曲线2和直线3之间的阴影部分可表示出挥发性炉渣温度反映滞后及分熔的影响,考虑采用同类物质配制炉渣,且粒度、压实程度等相同,测定过程的滞后等效应基本一致。曲线3和曲线2之间的距离则反映出挥发对测定结果的影响,即考虑“滞后 分熔”的影响为曲线2,考虑“挥发 滞后 分熔”的影响为曲线1,二者之差为“挥发”的影响。同样以升温速率25℃/min为例,线段ab对应的温度差就是升温速率为25℃/min由于温度反映滞后及分熔引起的熔点测定值变化,线段ac对应的温度差就是升温速率为25℃/min由于挥发可导致的熔点测定值变化。
43.理论熔点的测算:既然考虑到挥发,也就是说由于升温速率升高,高温下停留时间缩短,导致零挥发减少,进而使得熔点测定值下降的值为线段ac的对应值,那么如果能有效抑制炉渣挥发的熔点测定值就应该对曲线3上的对应点进行一定补偿,对应点下移加上挥发影响的结果,即曲线4所示的结果。也就是说升温速率越慢,挥发越多,补偿也越多。升温速率30℃/min左右,曲线2和曲线3之间的距离基本不变,也就是说此点挥发的影响基本为零,此时不用补偿。升温速率越低,补偿越多。为此,将图3中温度反应滞后等影响线下移,以图4中的e点对齐(也就是说此点不用补偿)。以升温速率5℃/min为例,如果能有效抑制挥发,其熔点的表观测定值应为h点对应值,但由于挥发组元挥发,导致熔点升高,采用常规半球点炼钢炉渣熔点测定方法测定的熔点值为g点,二者出现了明显的偏差,线段gh即为偏差,也就是应该给予的补偿值。进一步,如剔除温度反映滞后等的影响,熔点的值应为图直线对应的点,即f点对应的温度,此温度应为对应炉渣(原始组成)理论熔点,抑制挥发且没有反应温度滞后。该熔点值不随升温速率及组元挥发的变化而变化。
44.(5)对挥发量的评价:熔点测定前后进行炉渣试样称重,可以估算炉渣中挥发组元的含量变化,根据炉渣中挥发组元的含量变化和炉渣挥发对炉渣熔点的影响值评价含易挥发组元炉渣挥发对炉渣熔点的影响。为了保证称量准确,应采用万分之一以上精度天平。
45.以下为具体应用实施例:
46.实施例1
47.电渣重熔用中氟渣熔点测定中挥发的影响评价及结果修正
48.选用炉渣及常规熔点测定
49.电渣重熔用中氟渣,炉渣组成如表1所示。均为采用化学纯试剂配制的混合渣。
50.表1 电渣重熔用中氟渣的炉渣成分(wt/%)
51.炉渣al2o3mgosio2caf2cao中氟渣29.332.579.1530.1228.83
无氟渣18-42-40
52.采用半球点测定,升温速率为10℃/min,测定得到中氟渣半球点为1351℃,无氟渣对应熔点为1432℃。
53.应用方式
54.按照本发明方法,分别采用5℃/min、10℃/min、15℃/min、20℃/min和30℃/min 5个升温速率测定了两种炉渣的半球点温度,绘制了熔点随升温速率的变化曲线,通过耦合、外推,分别得到无氟渣的“温度 成渣反应 分熔”等综合影响值,及对应中氟渣的“温度 成渣反应 分熔”和“挥发影响”分别影响值。进而外推得到了中氟渣和无氟渣的熔点理论值。
55.应用结果
56.依照上述方法,得到“温度 成渣反应 分熔”等综合影响值随着升温速率由5℃/min、逐步升高到30℃/min时,对无氟渣测定得到的表观熔点值由1432℃逐步升高到1501℃;而中渣测定得到的表观熔点值由1380℃逐步降低到1288℃,挥发的影响最大可达212℃。进一步修正得到中氟渣的熔点理论值为1225℃,与采用同样化学组成的预熔渣(预熔渣的挥发远远小于混合渣)的测定值1240℃基本接近,证明了其可信性。
57.实施例2
58.电渣重熔用高氟渣熔点测定中挥发的影响评价及结果修正
59.选用炉渣及常规熔点测定
60.电渣重熔用高氟渣,炉渣组成如表2所示,均采用化学纯试剂配制的混合渣。
61.表2 电渣重熔用高氟渣熔点的炉渣成分(wt/%)
62.炉渣al2o3sio2caf2cao高氟渣28.892.9968.12-无氟渣1842-40
63.采用半球点测定,升温速率为10℃/min,测定得到高氟渣半球点为1351℃,无氟渣对应熔点为1432℃。
64.应用方式
65.按照本发明方法,分别采用5℃/min、10℃/min、15℃/min、20℃/min和30℃/min5个升温速率测定了两种炉渣的半球点温度,绘制了熔点随升温速率的变化曲线,通过耦合、外推,分别得到无氟渣的“温度 成渣反应 分熔”等综合影响值,及对应中氟渣的“温度 成渣反应 分熔”和“挥发影响”分别影响值。进而外推得到了中氟渣和无氟渣的熔点理论值。
66.应用结果
67.依照上述方法,得到“温度 成渣反应 分熔”等综合影响值随着升温速率由5℃/min、逐步升高到30℃/min时,对无氟渣测定得到的表观熔点值由1432℃逐步升高到1501℃;而中渣测定得到的表观熔点值由1351℃逐步降低到1270℃,挥发的影响最大可达81℃。进一步修正得到高氟渣的熔点理论值为1201℃。
68.实施例3
69.炼钢含氟保护渣熔点测定中挥发的影响评价及结果修正
70.选用炉渣及常规熔点测定
71.同一化学组成的两种连铸保护渣,其中一个为采用化学纯试剂配制的混合渣,另一个为预熔渣(去除碳后)。炉渣组成如表3所示,
72.表3 炼钢含氟保护渣的炉渣成分(wt/%)
[0073][0074]
采用半球点测定,升温速率为10℃/min,测定得到含氟保护渣混合渣半球点温度为1125℃,预熔渣对应半球点温度为1032℃。无氟保护渣的熔点1170℃。
[0075]
应用方式
[0076]
按照本发明方法,分别采用5℃/min、10℃/min、15℃/min、20℃/min和30℃/min 5个升温速率测定了三种炉渣的半球点温度,绘制了熔点随升温速率的变化曲线,通过耦合、外推,分别得到无氟保护渣的“温度 成渣反应 分熔”等综合影响值,及对应含氟渣的“温度 成渣反应 分熔”和“挥发影响”分别影响值。进而外推得到了含氟保护渣混合渣熔点理论值,并和含氟渣预熔渣的熔点测定结果进行了比较。
[0077]
应用结果
[0078]
依照上述方法,得到“温度 成渣反应 分熔”等综合影响值随着升温速率由5℃/min、逐步升高到30℃/min时,对无氟保护渣测定得到的表观熔点值由1170℃逐步升高到1211℃;而含氟混个渣测定得到的表观熔点值由1125℃逐步降低到1061℃,以此可推断挥发的影响最大可达64℃左右。进一步修正得到含氟保护渣混合渣的熔点理论值为1020℃,与采用同样化学组成的预熔渣(预熔渣的挥发远远小于混合渣)的测定值1032℃基本接近,证明了其可信性。
[0079]
实施例4 铅直接还原中铅渣熔点测定中挥发的影响评价及结果修正
[0080]
选用炉渣及常规熔化温度测定
[0081]
铅直接还原中铅炉渣组成如表4所示。均为采用化学纯试剂配制的混合渣。
[0082]
表4 铅直接还原中铅渣的炉渣成分(wt/%)
[0083]
成分pboznocaofeosio2中铅渣201012.3537.0620.59无铅渣-12.5015.4446.3325.74
[0084]
采用半球点测定,升温速率为10℃/min,测定得到中铅渣半球熔化温度为1226℃,无铅渣对应熔化温度为1292℃。
[0085]
应用方式
[0086]
按照本发明方法,分别采用5℃/min、10℃/min、15℃/min、20℃/min和30℃/min 5个升温速率测定了两种炉渣的半球点温度,绘制了熔化温度随升温速率的变化曲线,通过耦合、外推,分别得到无铅渣的“温度 成渣反应 分熔”等综合影响值,及对应中铅渣的“温度 成渣反应 分熔”和“挥发影响”分别影响值,可以实现对挥发及其它因素的影响评价,进
而外推得到了中铅渣和无铅渣的熔化温度理论值。
[0087]
应用结果
[0088]
依照上述方法,得到“温度 成渣反应 分熔”等综合影响值随着升温速率由5℃/min、逐步升高到30℃/min时,对无铅渣测定得到的表观熔化温度值由1286℃逐步升高到1359℃;而中铅渣测定得到的表观熔化温度值由1263℃逐步降低到1151℃,挥发的影响最大可达208℃。进一步修正得到中铅渣的熔化温度理论值为1075℃,与采用同样化学组成的预熔渣(预熔渣的挥发远远小于混合渣)的测定值1056℃基本接近,证明了其可信性。
[0089]
实施例5
[0090]
铅直接还原中高铅渣熔点测定中挥发的影响评价及结果修正
[0091]
选用炉渣及常规熔化温度测定
[0092]
铅直接还原中高铅炉渣组成如表5所示。均为采用化学纯试剂配制的混合渣。
[0093]
表5 铅直接还原中高铅渣的炉渣成分(wt/%)
[0094]
成分pboznocaofeosio2中铅渣4069.5328.5815.88无铅渣-10.0015.8847.6326.47
[0095]
采用半球点测定,升温速率为10℃/min,测定得到高铅渣半球熔化温度为1206℃,无铅渣对应熔化温度为1296℃。
[0096]
应用方式
[0097]
按照本发明方法,分别采用5℃/min、10℃/min、15℃/min、20℃/min、30℃/min等5个升温速率测定了两种炉渣的半球点温度,绘制了熔化温度随升温速率的变化曲线,通过耦合、外推,分别得到无铅渣的“温度 成渣反应 分熔”等综合影响值,及对应中铅渣的“温度 成渣反应 分熔”和“挥发影响”分别影响值,可以实现对挥发及其它因素的影响评价,进而外推得到了中铅渣和无铅渣的熔化温度理论值。
[0098]
应用结果
[0099]
依照上述方法,得到“温度 成渣反应 分熔”等综合影响值随着升温速率由5℃/min、逐步升高到30℃/min时,对无铅渣测定得到的表观熔化温度值由1291℃逐步升高到1364℃;而中铅渣测定得到的表观熔化温度值由1261℃逐步降低到1130℃,挥发的影响最大可达234℃。进一步修正得到中铅渣的熔化温度理论值为1053℃,与采用同样化学组成的预熔渣(预熔渣的挥发远远小于混合渣)的测定值1020℃基本接近,证明了其可信性。
[0100]
实施例6
[0101]
铅直接还原初期高铅渣熔点测定中挥发的影响评价及结果修正
[0102]
选用炉渣及常规熔化温度测定
[0103]
铅直接还原初期高铅炉渣组成如表6所示。均为采用化学纯试剂配制的混合渣。
[0104]
表6 铅直接还原初期高铅渣的炉渣成分(wt/%)
[0105]
成分pboznocaofeosio2中铅渣61.269.173.4819.995.26无铅渣-24.209.1852.7413.88
[0106]
采用半球点测定,升温速率为10℃/min,测定得到高铅渣半球熔化温度为1113℃,无铅渣对应熔化温度为1215℃。
[0107]
应用方式
[0108]
按照本发明方法,分别采用5℃/min、10℃/min、15℃/min、20℃/min、30℃/min等5个升温速率测定了两种炉渣的半球点温度,绘制了熔化温度随升温速率的变化曲线,通过耦合、外推,分别得到无铅渣的“温度 成渣反应 分熔”等综合影响值,及对应中铅渣的“温度 成渣反应 分熔”和“挥发影响”分别影响值,可以实现对挥发及其它因素的影响评价,进而外推得到了中铅渣和无铅渣的熔化温度理论值。
[0109]
应用结果
[0110]
依照上述方法,得到“温度 成渣反应 分熔”等综合影响值随着升温速率由5℃/min、逐步升高到30℃/min时,对无铅渣测定得到的表观熔化温度值由1205℃逐步升高到1314℃;而高铅渣测定得到的表观熔化温度值由1168℃逐步降低到955℃,挥发的影响最大可达359℃。进一步修正得到高铅渣的熔化温度理论值为842℃,与采用同样化学组成的预熔渣(预熔渣的挥发远远小于混合渣)的测定值812℃基本接近,证明了其可信性。
[0111]
由技术常识可知,本发明可以通过其它的不脱离其精神实质或必要特征的实施方案来实现。因此,上述公开的实施方案,就各方面而言,都只是举例说明,并不是仅有的。所有在本发明范围内或在等同于本发明的范围内的改变均被本发明包含。
[0112]
最后应当说明的是:以上实施例仅用以说明本发明的技术方案而非对其限制,尽管参照上述实施例对本发明进行了详细的说明,所属领域的普通技术人员应当理解:依然可以对本发明的具体实施方式进行修改或者等同替换,而未脱离本发明精神和范围的任何修改或者等同替换,其均应涵盖在本发明的权利要求保护范围之内。
再多了解一些
本文用于企业家、创业者技术爱好者查询,结果仅供参考。