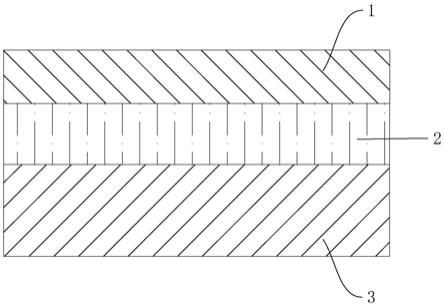
1.本技术涉及柔性电路板技术领域,更具体地说,它涉及一种高性能硅丙纯胶膜及其制备方法。
背景技术:
2.近年来电子行业发展讯速,在行业中柔性电路板的使用愈发广泛,随着电子产品朝着精细化方向发展,对于柔性电路板(fpc板)的性能提出了更高的要求。
3.纯胶膜作为fpc板中不可或缺的一部分,纯胶膜主要应用于各类补强板及多层板的粘接,势必会对纯胶膜的各项性能要求更高。
4.目前市场上的纯胶膜主要分为环氧纯胶膜及常规的纯丙纯胶膜两大类:环氧纯胶膜存在储存条件苛刻(需低温冷藏)、生产成本高、对环境污染大、操作性差、溢胶量难控制等诸多缺陷,所以环氧纯胶膜难以推广应用;而常规的纯丙纯胶膜虽是目前市场上使用较多的,却因为存在耐热性差、剥离强度偏低、稳定性差等诸多缺陷导致越发不能满足行业要求。显然市场上的两类纯胶膜的缺陷较多,已然无法契合行业发展趋势。故很有必要提高一种各项性能优异,契合行业发展的纯胶膜。
5.针对上述中的相关技术,发明人认为现有的纯胶膜在实际应用中耐热性差、剥离强度低、不够稳定。
技术实现要素:
6.为了尽量解决现有的纯胶膜存在耐热性差、剥离强度低以及不够稳定的问题,本技术的目的是提供一种高性能硅丙纯胶膜及制备方法。
7.第一方面,本技术提供的一种高性能硅丙纯胶膜及采用如下的技术方案:一种高性能硅丙纯胶膜,其特征在于:包括载胶层、胶黏剂层和保护层,所述胶黏剂层涂布在载胶层上,所述保护层覆盖在胶黏剂层上;所述胶黏剂层为硅丙胶黏剂,所述硅丙胶黏剂由以下重量份的原料制备而成:硅丙乳液80~120份;无机填料1~8份;甲阶酚醛固化剂4~12份;去离子水5~20份;氨水0.5~3.0份;所述硅丙乳液由以下重量份的原料制备而成:硬单体18~38份;软单体50~80份;功能单体2~10份;有机硅单体1~9份;乳化剂0.5~5份;
引发剂0.2~3份;去离子水150~450份。
8.通过采用上述技术方案,首先将硬单体、软单体、功能单体以及有机硅单体混合后加入乳化剂、引发剂制成乳液,使得有机硅单体能够均匀分散在乳液中,然后加入无机填料、固化剂、去离子水等进行聚合反应,形成硅丙胶黏剂;硬单体的均聚物玻璃化温度较高,能够提高硅丙胶黏剂的硬度和拉伸强度,软单体的均聚物玻璃化温度较低,赋予了硅丙胶黏剂一定的柔韧性和延伸性;软单体和硬单体的结合作用叠加,使得硅丙胶黏剂的综合性能提升,功能单体一般具有功能基团,如抗污染、耐溶剂性、耐水等性能,能够提高胶黏剂的粘接强度及稳定性;通过加入疏水性的有机硅单体,有机硅单体参与共聚在聚丙烯酸酯高分子侧链中引入含硅基团,胶层吸水率大幅度降低,对气候的稳定性增强,耐高温性大幅度提升,剥离强度也大幅度提高。
9.可选的,所述有机硅单体为乙烯基硅油、乙烯基三甲氧基硅烷、乙烯基三乙氧基硅烷、3~(甲基丙烯酰氧)丙基三甲氧基硅烷)、乙烯基三(β~甲氧基乙氧基)硅烷中的一种或多种。
10.通过采用上述技术方案,利用了有机硅单体的双功能性,既能与无机填料反应,提升物理性能,增强稳定性;又能与有机物发生反应,提高硅丙胶黏剂的粘结力,增强剥离强度以及耐热性,而乙烯基硅油、乙烯基三甲氧基硅烷、乙烯基三乙氧基硅烷、3~(甲基丙烯酰氧)丙基三甲氧基硅烷)、乙烯基三(β~甲氧基乙氧基)硅烷是有机硅单体中性能较为优异,而且廉价易得的物质。
11.可选的,所述甲阶酚醛固化剂由苯酚和甲醛溶液在三乙胺的催化作用下制得。
12.通过采用上述技术方案,选择苯酚、甲醛以及催化剂三乙胺进行合成甲阶酚醛固化剂,其一是因为甲阶酚醛固化剂本身储藏不稳定,现配现用效果更突出,另外由于其有良好的耐热、耐介质等性能,既能固化硅丙胶黏剂,还能提升硅丙纯胶膜的耐热性能。
13.可选的,所述硬单体为苯乙烯、甲基丙烯酸甲酯、丙烯酸甲酯、丙烯腈中的一种或多种。
14.通过采用上述技术方案,苯乙烯、甲基丙烯酸甲酯、丙烯酸甲酯、丙烯腈这几种硬单体的均聚物玻璃化温度高,参与聚合反应时能够明显的提高硅丙胶黏剂的硬度和拉伸强度。
15.可选的,所述软单体为丙烯酸乙酯、丙烯酸丁酯、丙烯酸异丁酯、丙烯酸异辛酯中的一种或多种。
16.通过采用上述技术方案,丙烯酸乙酯、丙烯酸丁酯、丙烯酸异丁酯、丙烯酸异辛酯这几种软单体的均聚物玻璃化温度较低,在聚合时能够显著的提升硅丙胶黏剂的柔韧性和延伸性。
17.可选的,所述功能单体丙烯酸、甲基丙烯酸、丙烯酸羟乙酯、丙烯酸羟丙酯中的一种或多种。
18.通过采用上述技术方案,丙烯酸、甲基丙烯酸、丙烯酸羟乙酯、丙烯酸羟丙酯这几种物质易聚合,均具有高粘结强度,而且耐热性好,有一定的增稠作用,即能够提高硅丙胶黏剂的剥离强度,耐热性。
19.可选的,所述胶黏剂层的厚度为13~60μm。
20.通过采用上述技术方案,胶黏剂层的厚度过厚不利于补强板和/或多层板与fpc板的连接,占用空间较大,厚度太薄粘结力不够,容易剥落,通过实验所得,厚度在13~60μm之间不会妨碍与fpc板的粘接,也保证了胶黏剂层的剥离强度。
21.可选的,所述载胶层的离型力大于所述保护层的离型力。
22.通过采用上述技术方案,在实际应用中,首先需将保护层撕开,将胶黏剂层与所需要粘接的物体(如fpc板)进行粘接,而后再撕去载胶层与另一粘接物体相粘接,为防止在撕掉保护层的时候,将胶黏剂层从载胶层上撕落,故需设置载胶层的离型力大于保护层的离型力。
23.可选的,所述载胶层的厚度为25~100μm,保护层的厚度为12.5~25μm。
24.通过采用上述技术方案,纯胶膜的应用需要适配fpc板的具体工艺,视具体应用场景不同,对于载胶层和保护层的厚度有不同要求,然而将载胶层的厚度设置为25~100μm,保护层的厚度设置为12.5~25μm,能够满足大部分应用场景,利于市场推广。
25.第二方面,本技术提供的高性能硅丙纯胶膜的制备方法采用如下的技术方案,包括以下制备步骤:步骤一、制备硅丙胶黏剂:制备硅丙乳液;1)预乳化,取重量份的硬单体、软单体、有机硅单体、功能单体、乳化剂、引发剂和去离子水进行搅拌乳化,搅拌速率在500~1000rpm/min,搅拌形成均一稳定的预乳化液;2)初步反应,取1)中5%~40%的预乳化液,逐步升温至80~85℃反应直至冷凝器无回流,保持温度不变开始连续滴加预乳化液进行反应,控制总加料时间在1h至1.5h之间;3)完全反应,维持温度不变20min至40min,然后继续加入占预乳化液总量0.1%~1%的引发剂,升温至85~90℃继续反应1.5~2h;4)冷却过滤,反应完成后冷却至室温,加入氨水调节ph值到6.2~7.8,然后过滤即得硅丙乳液;制备甲阶酚醛固化剂:取重量份的苯酚、甲醛溶液及三乙胺,升温至50℃搅拌反应1~1.5h,搅拌速率为500~1000rpm/min,再次升温至70℃继续反应1.5~2h,反应结束冷却至室温出料,制得甲阶酚醛固化剂制备硅丙胶黏剂:取重量份的硅丙乳液、二氧化硅填料、甲阶酚醛固化剂、去离子水以及氨水混合后进行搅拌,搅拌速率为500~1000rpm/min,搅拌分散均匀后砂磨制得硅丙胶黏剂;步骤二、制备高性能硅丙纯胶膜:将硅丙胶黏剂均匀涂布在载胶层上,然后进行干燥,干燥温度由70℃梯度升温至130℃,总干燥时间控制在2~4min,干燥后将保护层热压合在远离载胶层的硅丙胶黏剂一面上,最后收卷即得高性能硅丙纯胶膜。
26.通过采用上述技术方案,采取预乳化的前处理方式,使得后续聚合反应稳定进行,聚合反应分两步进行,首先加入部分的预乳化液进行反应,后续边滴加剩余的预乳化液边搅拌,使得聚合反应能够充分进行,最后补加引发剂进一步确保聚合反应完全进行,制得剥离强度高、耐热性好的硅丙胶黏剂;制备硅丙乳液时加入氨水是为了中和乳液中的丙烯酸,中和后乳液更稳定;制备硅丙胶黏剂时加入氨水是为了增稠,便于后续涂布。
27.综上所述,本技术包括以下至少一种有益技术效果:1.由于有机硅单体本身是一种双功能物质,既可与无机填料反应,也能与有机高分子反应,加入有机硅单体,与无机填料以及加入的软单体、硬单体等反应,一方面使得这
些物质能够充分聚合在一起,促进了它们之间的粘合作用,进而提高了纯胶膜的剥离强度,其次改善了纯胶膜的耐热性差的问题,也能保护纯胶膜的界面不受潮气侵蚀即提高了稳定性;具体原理是有机硅单体具有疏水性,有机硅单参与聚合反应,在聚丙烯酸酯高分子侧链中引入含硅基团,胶层吸水率大幅度降低,对气候的稳定性增强,耐高温性大幅度提升,剥离强度也大幅度提高。
28.2.本技术的硅丙纯胶膜在288℃条件下浸锡10s连续3次不会分层起泡,吸湿率在2%以内,剥离强度在2.5kgf/cm以上,在85℃,湿度85%的条件下96h剥离强度衰减在30%以下,操作性好;该硅丙纯胶膜性能优于市售的纯丙纯胶膜,有更为广泛的应用范围,利于市场推广。
附图说明
29.图1是本技术高性能硅丙纯胶膜的结构示意图;图2是本技术高性能硅丙纯胶膜制备方法的流程示意图。
30.附图标记说明:1、载胶层;2、胶黏剂层;3、保护层。
具体实施方式
31.以下结合附图1和2和实施例对本技术作进一步详细说明。予以特殊说明的是:以下实施例中未注明具体条件者按照常规条件或制造商建议的条件进行,以下实施例中所用原料除特殊说明外均可来源于普通市售。
32.制备例甲阶酚醛固化剂制备取13.2g苯酚,26.8g甲醛溶液及0.3g三乙胺加入至反应罐升温至50℃搅拌反应60min,搅拌速率为800rpm/min,再次升温至70℃继续反应90min,反应结束冷却至室温出料,制得甲阶酚醛固化剂。
实施例
33.实施例1步骤一、制备硅丙胶黏剂:硅丙乳液制备称取150g去离子水,0.94g十二烷基硫酸钠,64.5g丙烯酸正丁酯,26.5g丙烯腈,5g丙烯酸,4.4g丙烯酸异辛酯和1g乙烯基三(β~甲氧基乙氧基)硅烷加入至乳化罐搅拌乳化90min,搅拌速率为1000rpm/min,在乳化完成前10min加入0.5g过硫酸钠制得预乳化液;取5%的预乳化液加入聚合罐开起搅拌,并逐步升温至82℃反应直至泠凝器无回流,然后开始连续添加剩余的预乳化液并逐步升温至85℃,加料时间控制在60min,添加完毕后保持原温继续反应30min,反应结束补加0.1g过硫酸钠至聚合罐,升温至88℃熟化90min,熟化结束冷却至室温加入氨水中和,反应30min,调节ph值到7.1,出料过滤制得硅丙乳液。
34.硅丙胶黏剂配制将二氧化硅4g、固化剂6g、去离子水15g、氨水1.5g加入至制得的硅丙乳液100g中搅拌,进行预分散20min,搅拌速率为800rpm/min,预分散结束后,用砂磨机继续研磨分散,
制得硅丙胶黏剂。
35.步骤二、高性能硅丙纯胶膜的制备将硅丙胶黏剂均匀涂布在载胶层1上,然后过隧道炉干燥,炉温由70℃梯度升温至130℃,总干燥时间控制在3min,干燥后将保护层3热压合在远离载胶层1的硅丙胶黏剂一面上,最终将材料收成卷制得胶黏剂层2厚度为13μm、25μm、50μm和60μm的硅丙纯胶膜。梯度升温具体为:70℃~80℃~90℃~100℃~110℃~120℃~130℃~60℃。本技术实施例高性能硅丙纯胶膜的工艺流程图见图1,所制得的纯胶膜结构示意图见图2。
36.值得注意的是,在本实施例中选择十二烷基硫酸钠作为乳化剂,在其他实施例中可以选择十二烷基磺酸钠、十二烷基苯磺酸钠、辛基苯基聚氧乙烯醚、任基酚聚氧乙烯醚硫酸铵中的任意一种或几种组合。在本实施例中选择过硫酸钠作为引发剂,在其他实施例中还可以选择过硫酸铵、过硫酸钠、过硫酸钾中的一种或几种组合。
37.另外在本实施例中硬单体选择丙烯腈,在其他实施例中可以选择苯乙烯、甲基丙烯酸甲酯、丙烯酸甲酯中的一种或多种;软单体选择的是丙烯酸异辛酯和丙烯酸丁酯,在其他实施例中还可以选择丙烯酸乙酯、丙烯酸异丁酯等;功能单体使用的是丙烯酸,在其他实施例中可以选择甲基丙烯酸、丙烯酸羟乙酯、丙烯酸羟丙酯中的一种或多种组合;有机硅单体选择的是乙烯基三(β~甲氧基乙氧基)硅烷,在其他实施例中可以选择乙烯基硅油、乙烯基三甲氧基硅烷、乙烯基三乙氧基硅烷、3~(甲基丙烯酰氧)丙基三甲氧基硅烷)中的一种或多种组合,无机填料本技术选择的是二氧化硅,在其他实施例中还可以是氧化铝、碳酸钙与滑石粉中的一种或多种组合。
38.实施例2本实施例与实施例1的不同之处在于,加入的乙烯基三(β~甲氧基乙氧基)硅烷重量份为3g,其它操作与实施例1相同,得到胶黏剂层2厚度为13μm、25μm、50μm和60μm的硅丙纯胶膜。
39.实施例3本实施例与实施例1的不同之处在于,加入的乙烯基三(β~甲氧基乙氧基)硅烷重量份为7g,其它与实施例1相同,得到胶黏剂层2厚度为13μm、25μm、50μm和60μm的硅丙纯胶膜。
40.实施例4本实施例与实施例1的不同之处在于,加入的乙烯基三(β~甲氧基乙氧基)硅烷重量份为9g,其它与实施例1相同,得到胶黏剂层2厚度为13μm、25μm、50μm和60μm的硅丙纯胶膜。
41.实施例5本实施例与实施例1的不同之处在于各原料的加入量不同,以及在制备硅丙乳液时调节ph值为6.2,原料的添加量详见表1。得到胶黏剂层2厚度为13μm、25μm、50μm和60μm的硅丙纯胶膜。
42.实施例6本实施例与实施例1的不同之处在于各原料的加入量不同,以及在制备硅丙乳液时调节ph值为7.8,原料的添加量详见表1。得到胶黏剂层2厚度为13μm、25μm、50μm和60μm的硅丙纯胶膜。
43.对比例对比例1本对比例与实施例1的不同之处在于,未加入有机硅单体即乙烯基三(β~甲氧基乙氧基)硅烷,其它与实施例1相同,得到胶黏剂层2厚度为13μm、25μm、50μm和60μm的硅丙纯胶膜。
44.对比例2本对比例与实施例1的不同之处在于,得到的胶黏剂层2厚度为10μm和70μm。
45.表1:各实施例对比例原料添加情况表性能检测试验依据《fpc技术测试规范》对上述实施例和制备例得到的胶膜进行性能测试,具体测试实验包括:剥离强度测试、耐热性测试、吸水率测试。
46.1、剥离强度测试仪器设备:拉力试验机测试样条制作覆贴:离型膜+胶+离型膜:撕去离型膜与单面板pi面贴合,放入护贝机(温度120
±
5℃);撕去离型膜与单面板pi面相贴合,放入护贝机(温度120
±
5℃);快压:温度180℃压力,120kg/cm2(表压),预热时间10s,压着时间80s;熟化:160℃
×
90min;熟化后试片裁切md/td1cm
×
18cm三条;高温高湿处理:将测试样条在85%rh/85℃环境处理96h测试条件:速度:50mm/min,宽度:10mm,删除左右极限之测试值:5mm,测试距离:70mm,90度角以滚轮试验测试方法:将样条纯胶膜层撕开,将其中一侧单面板固定在90度角滚轮上,另一侧单面板用夹具夹住保持竖直状态,拉取剥离强度数值,数值稳定后读取数值记录为测试结
果。
47.计算公式:剥离强度=拉力/试条宽度;剥离强度衰减率=(常温常湿剥离强度—高温高湿)/常温常湿剥离强度。
48.2、耐热性测试仪器设备:高温锡炉,测试条件:288℃*10s*3次;265℃*10s*3次,测试方法:将样片浸入设定温度的锡铅液中,10s后观察外观,重复操作3次,判定基准:三片样片外观均无起泡分层则判定为该纯胶膜能耐受该温度,反之则不能耐受。
49.3、吸水率测定仪器设备:分析天平感量0.0001g;测试样片制备:裁取纯胶膜10cm
×
10cm三片,撕去保护层与同尺寸质量为m0聚四氟乙烯板贴合,放入护贝机(温度120
±
5℃);撕去载胶层160℃熟化90min,熟化完毕后冷却至室温,得到测试样片;测试条件:85%rh/85℃处理24h;测试方法:将制备完成的测试样片称重并记录为m1,称重完毕后将测试样片85%rh/85℃处理24h,处理结束用吸水纸吸干样片表面水珠,迅速称重并记录为m2;吸水率计算公式:吸水率=(m2~m1)/(m1~m0)
×
100%;备注:最终结果取三片样片的平均值。
50.性能测试结果采取上述测试方法将实施例1~6和对比例1~2所得的纯胶膜进行测试所得结果归纳如表2所示:表2:各实施例对比例性能检测结果对比表
由表2所述的纯胶膜评价结果可知:实施例1与对比例1相比,实施例多加了有机硅单体,结合表2的性能测试结果,可得,有机硅单体的加入使得硅丙纯胶膜的耐热性、剥离强度以及吸水率大幅增强,效果十分显著。
51.实施例1、2、3中随着有机硅单体含量的增加纯胶膜的性能有上升趋势,但加入过多的有机硅单体如实施例4,其各项性能略有下降。
52.对比实施例1和实施例5和6,其区别在于所加入的原料量不同,而实施例1的各项性能均小优于实施例5和6,所以可知实施例1的原料配比优于实施例5和6。
53.对比实施例1和对比例2,其差别在于胶黏剂层的厚度不一样,明显在13~60um之间的厚度,其性能更优。
54.本具体实施例仅仅是对本技术的解释,其并不是对本技术的限制,本领域技术人员在阅读完本说明书后可以根据需要对本实施例做出没有创造性贡献的修改,但只要在本技术的权利要求范围内都受到专利法的保护。
再多了解一些
本文用于企业家、创业者技术爱好者查询,结果仅供参考。