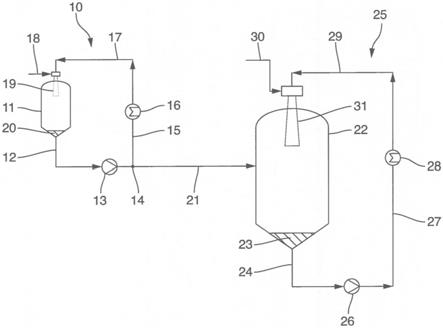
1.本发明的主题是用于生产加合物的方法,该加合物是通常在存在催化剂的情况下在至少一个第一反应器中由含有至少一种活性或不稳定氢原子的至少一种起始材料与比如环氧烷的至少一种单体离析物反应,并且随后将第一反应器的产物通入到至少一个第二反应器以进行进一步反应得到。在单体离析物是环氧烷类的成员的情况下,所得到的加合物称为烷氧基化物,反应过程称为烷氧基化。
背景技术:
2.在烷氧基化物(包括聚醚多元醇)的分批生产中,“生长比”定义为最终批次体积(包括通过一种或多种起始材料与一种或多种环氧烷反应产生的加合物)除以在添加任何环氧烷之前起始材料的最小可能体积。
3.因此,对于任何给定的最终反应体积(批次尺寸),可以实现的最大生长比取决于能够处理的起始材料的最小体积。对于任何给定的反应器,期望小的最小起始体积,因为其促进高生长比产物的生产。
4.通常,用于进行烷氧基化反应的反应器装置包括容纳反应物并且为反应进行至完成提供停留时间的一个或多个反应容器、使反应物彼此紧密接触的一个或多个混合装置、以及去除反应热的一个或多个热交换装置。
5.先进反应器系统(所谓的喷射回路反应器)将混合和除热功能结合在一个或多个外部循环回路中,其中来自反应容器的流体被输送到泵,该泵提供动力以使所述流体循环通过热交换装置去除热量,循环通过喷射混合器,该喷射混合器诱导来自反应容器顶部空间的气流与循环流体紧密接触,并且返回到反应容器。通常,将为每个反应容器提供至少一个泵、至少一个热交换器和至少一个喷射混合器。喷射回路反应器相对于不太先进的反应器系统的主要优点包括气相和液相的更强烈的混合,因此更好的质量和热传递,其能够实现更快的反应时间和更好的冷却;强制循环和反应器气相与反应器液相的连续再混合,其最小化未反应的环氧烷在反应器顶部空间中的积聚,从而提高反应器安全性和产品质量;以及安装比单独将冷却盘管直接附接到反应器壳上可能的传热面积大得多的传热面积的能力。在某些情况下,在容器内安装机械搅拌器以补充喷射混合器的作用。
6.通常,最小启动体积由泵吸入要求和外部循环回路(包括泵、热交换器、喷射混合器和相关管道系统)的体积控制。特别地,起始体积必须足以填充外部回路,使得泵吸入口连续地供应有再循环液体。这种限制是反应器的典型特征,其依赖于外部冷却回路来供应或去除反应热。在没有外部冷却回路的反应器的情况下,最小起始体积可以替代地由有效冷却和搅拌反应器容器底部中的材料的能力来控制。
7.具有单个外部液体循环回路的典型喷射回路反应器能够实现约1:10至1:20范围内的生长比。
8.如聚乙二醇(pegs)、甲氧基聚氧化烯二醇(mpegs)和聚丙烯二醇(ppgs)以及许多聚醚多元醇和其他聚氧化烯二醇产物等高分子量烷氧基化物需要的生长比远远超过在典
型的喷射回路反应器或搅拌釜反应器中可达到的生长比。有几种技术用于实现更高的生长比,这些技术在本领域中是公知的并且在工业中实践如下:
9.低于最终目标分子量的一定体积的“预聚物”可以首先通过一种或多种起始材料与一种或多种单体离析物在反应器中的反应制备,其一部分被取出,剩余部分随后返回到相同的反应器中,以添加足够量的一种或多种另外的单体离析物以达到最终目标分子量。这种方法有几个缺点:必须制备比单个最终批次所需体积更大的预聚物。因此,过量的预聚物必须被剥离,清除残余的氧化物,进行冷却,并且储存以备以后使用。这显著地增加了批次处理时间,并且需要外部存储容量。在储存期间有引入预聚物的热降解或氧化降解的可能性。
10.在喷射回路反应器(或配备有外部冷却回路的其他类型的反应器)的情况下,除了初级回路之外,还可以安装包括泵、热交换器、喷射混合器和相关管道的一个或多个次级外部循环回路。与初级回路相比,次级回路中的至少一个较小(具有相应较小的起始体积)。在小的次级回路上开始反应,直到有足够的体积可用于使大的初级回路能够被调试。这有时被称为“双回路”运行。双回路运行可以实现高达60或甚至更高的最大生长比,但具有若干缺点。
11.在次级回路的初始运行期间,初级回路是空闲的(没有液体循环和冷却)。因此,单体离析物(特别是在环氧乙烷的情况下)到大回路中的任何泄漏都将是非常危险的,这是由于可能存在自反应并可能导致局部过热和随后的分解。
12.环氧烷到闲置的大回路中的潜在泄露也可能促进低分子量低聚物(比如1,4-二氧己环和二氧戊环)的形成,所述低分子量低聚物对产品质量高度有害。
13.在双回路运行的情况下,为了仅在小回路上的初始运行期间将初级回路与次级回路可靠地隔离,在工业中实践为在一个或多个外部回路上安装高完整性隔离阀(并且可选地保持所述隔离阀之间的高压氮缓冲器)。由于大回路管道的尺寸(其直径可达450mm或甚至更大)和系统设计压力(其可高达45barg或甚至更高),这些阀非常昂贵。此外,额外的管道、阀门和致动器导致反应器周围的布局非常拥挤。
14.当在双回路模式下运行时,批次时间显著延长,这是因为由于循环、混合和冷却速率大大减小,在次级小回路上的初始运行与主回路相比非常慢。ep 2 285 867 b1描述了使用包括第一连续流动回路的第一反应器和包括第二连续流动回路的第二反应器制备聚醚多元醇的连续方法,其中,两个反应器各自包括能够运行来泵送反应物流通过相应的连续流动回路的泵。第二反应器可以包括与第一反应器的产物出口流体连通的产物入口,并且包含第一反应产物的第一反应流的至少一部分从第一流回路被输送到第二流回路。然而,在现有技术已知的该方法中,包括连续流动回路的两个反应器各自具有相同的反应器尺寸。在该文献中没有暗示提供两个彼此连接的连续反应器,其中,第一反应器具有比第二主反应器更小的体积。此外,ep 2 285 867 b1教导了连续方法而不是分批方法,并且限于与双金属氰化物(dmc)催化剂一起使用。该文献中的第一反应回路不具有预处理容器的意义,而更具有多级反应器(如cstr级联)中的阶段的意义。
技术实现要素:
15.本发明的目的是提供一种具有高生长比的用于生产根据上述定义的烷氧基化物
的改进的方法。
16.上述目的的解决方案由根据具有独立权利要求1中所列举特征的上述定义的烷氧基化物的生产方法限定。
17.根据本发明,设置有第一循环回路的第一反应器包括比设置有第二循环回路的第二反应器更小的体积,并且在第一反应器中产生预聚物,该预聚物随后通入第二反应器,在第二反应器中产生期望的聚合物,并且其中,第一反应器或第二反应器中的至少一者是喷射回路反应器。
18.其中,所述反应器组合中的至少一个不是喷射回路反应器的反应器的不同组合没有抓住喷射反应器技术的优点(特别是液相和气相的强制循环,其中,喷射混合器连续地从反应器顶部空间抽取气体并且将所述气体与循环液体再混合),因此不能实现用本文所述喷射反应器技术可获得的高传质速率、高产品质量和更短的批次时间。
19.本发明的解决方案基于以下一般考虑,即大致这样的技术是可能的,其中,在第一反应器(或预反应器)中生产一定体积的预聚物,所述第一反应器(或预反应器)具有足够的最终批次体积以满足第二(或主)反应器的起始体积。预反应器的起始体积小于主反应器的起始体积。在第一反应器中完成预反应之后,将全部体积的预聚物转移到第二反应器中,在第二反应器中进行进一步的反应以生产具有所需分子量的最终聚合物。预反应器和主反应器的组合可以实现高达1:100或甚至更大生长比;可以避免在外部储存预聚物的需要;并且通过将整个反应分成同时在第一或预反应器中生产预聚物和在第二或主反应器中生产最终聚合物,可以非常显著地减少总批次时间(和提高系统生产率)。
20.根据本发明的第一反应器可以可选地在预反应之前进行各种预处理步骤,包括但不限于加热、催化、干燥和混合起始材料。
21.根据本发明,第一反应器或第二反应器中的至少一者为喷射回路反应器。优选地,至少较大的第二反应器为喷射回路反应器。
22.最优选地,不仅第二循环回路中的较大反应器为喷射回路反应器,而且制备预聚物的第一循环回路中的较小反应器也是喷射回路反应器。其两个或多个分批反应器中的至少一者为喷射回路反应器并且每个喷射回路反应器在循环回路中包含至少一个喷射混合器的这类方法使得可以实现比之前公开的现有技术更高的生长比。
23.本发明的另一实施例在起始材料为高粘性或包括以下起始材料的混合物的情况下是优选的:所述起始材料中的一种或多种在环境温度下为固体,或在反应条件下为高粘性,比如但不限于熔融山梨醇,或蔗糖和/或山梨醇与丙三醇单独或与其他液体起始材料混合的混合物。由于高固体含量和/或高粘度,这样的混合物最初可能难以泵送通过外部循环回路,直到足够的环氧烷反应以降低固体含量和/或粘度,从而使反应混合物易于泵送。因此,较小的第一反应器可以可选地装配有搅拌器来代替喷射混合器,或优选地除了喷射混合器之外还装配有搅拌器,以使得初始反应物质可以有效地混合并通过附接到反应器容器的内部或外部传热盘管去除反应热,直到外部回路可以投入使用为止。
24.根据本发明的可选实施例,其中,可以代替预处理容器安装或者除了预处理容器之外还安装制备预聚物的较小的第一反应器。单独的预处理容器、加上用于生产预聚物的单独的预反应器、以及用于生产最终聚合物的主反应器的这种组合需要稍微更高的投资,但也可以提供更大的灵活性和进一步减少批次时间。
25.本发明将搅拌罐预反应器的概念扩展到喷射反应器方法方案,以进行高生长比的烷氧基化物和聚醚多元醇生产。
26.根据本发明的优选实施例,至少一个第二反应器的体积是至少一个较小的第一反应器的体积的两倍以上,优选至少四倍。
27.根据本发明更优选的实施例,至少一个第二反应器的体积是至少一个较小的第一反应器的体积的至少六倍,优选至少八倍。
28.根据本发明的再一个更优选的实施例,至少一个第二反应器的体积是至少一个较小的第一反应器的体积的至少九倍,优选约十倍。
29.而在具有双回路设计的用于生产烷氧基化物的常规技术中,其中,使用单独的预处理容器来加热、催化、干燥和混合一种或多种起始材料,所述预处理容器通常具有与主反应器大约相同的尺寸,而根据本发明,可以可选地进行预处理运行的较小的第一反应器优选地比现有技术的预处理容器小得多。
30.根据本发明的优选实施例,较小的第一反应器中的反应以起始材料的最小起始体积开始,该最小起始体积对应于在较小的第一反应器中生产的预聚物的总体积的五分之一体积部分至二十分之一体积部分,优选对应于八分之一体积部分至十二分之一体积部分,更优选九分之一部分至十一分之一部分。
31.本发明的一般概念是首先在存在催化剂的情况下,在集成到第一循环回路中的较小的第一反应器中使较小体积的起始材料与一种或更多种环氧烷的仅一部分反应,并且在所述循环回路中循环反应混合物直到所提供的环氧烷全部反应,从而制备预聚物,然后将所述预聚物通过至少一条管线转移到整合到第二循环回路中的较大的第二反应器中。所述较大的第二反应器在整个过程中用作主反应器。因此,所述一种或更多种环氧烷的(剩余的)主要部分被添加到整合到第二循环回路中的较大的第二反应器中,并且在较大的第二反应器内与预聚物反应,以制备所需的最终聚合物产物。
32.根据本发明的优选实施例,将在较小的第一反应器中生产的预聚物的体积的主要部分、优选在较小的第一反应器生产的预聚物的基本全部体积转移到第二反应器。
33.根据本发明的优选实施例,在较小的第一反应器中生产的预聚物的体积为在较大的第二反应器中生产的聚合物的总体积的八分之一体积部分至十二分之一体积部分,优选九分之一体积部分至十一分之一体积部分。
34.根据本发明的优选实施例,一种或多种单体离析物在较小的第一反应器中进行反应,并且一种或多种单体离析物在较大的第二反应器中进行反应,其中,在较小的第一反应器中反应的离析物的总体积为在较大的第二反应器中反应的离析物总体积的八分之一重量部分至十二分之一重量部分,优选九分之一重量部分至十一分之一体积部分。
35.根据本发明的优选实施例,在较小的第一反应器中进行至少以下方法步骤:
36.预加热和混合一种或多种起始材料,添加催化剂或催化剂的混合物,干燥来去除水分,加热至反应温度,添加一种或多种单体离析物,获得预聚物,随后将获得的预聚物转移至较大的第二反应器。应当理解,在使用多于一种起始材料的情况下,催化剂添加可以在已经添加一种或多于一种这样的起始材料之后进行。
37.根据本发明的方法的一个优点是,与现有技术已知的常规方法相比,可以获得更高的生长比。优选地,根据本发明限定为最终批次体积除以起始材料的最小初始体积的生
长比为至少80:1,优选至少90:1,更优选至少100:1。
38.根据本发明的优选实施例,用于在较小的第一反应器中制备预聚物的典型起始材料为选自含有至少一种不稳定或活性氢的复合物的组中的一种或多种,所述复合物例如但不限于醇、酸、酯、二醇、三醇、多元醇、胺、酰胺、单糖、二糖和多糖,特别是选自包括以下各项的组中至少一者:甲醇、丙三醇,单乙二醇、二乙二醇、一丙醇、二丙二醇、三羟甲基丙烷、乙二胺、甲苯二胺、山梨醇、甘露醇、季戊四醇、二季戊四醇和蔗糖。
39.根据本发明的优选实施例,一种或多种单体离析物包括一种或多种从环醚类中抽取的物质,例如一种或多种环氧烷,特别是环氧乙烷、环氧丙烷、环氧丁烷和四氢呋喃中的一种或多种。
40.根据本发明的另一个实施例,一种或多种单体原料可以相继地或以其组合的形式连续地、间歇地、单独地、以任何比例同时地定量给料到反应质量中。
41.本发明的方法一般可以应用于生产宽范围的不同类型的烷氧基化物的聚合方法,其中,该方法包括至少一种环氧烷与合适的起始材料即化合物的反应,更特别地是与上文中提到的作为起始材料的至少一种化合物的反应。根据本发明的优选实施例,聚合物产物为聚醚多元醇。
42.通常,反应在至少一种合适的催化剂存在下进行,该催化剂可以为例如碱性催化剂,例如无机氢氧化物,如koh、naoh等。
43.可选地,特别是在干燥可能由于起始材料的挥发性而不可行的情况下,或者在其他方面将水排除到最大可行程度是有利的(例如在甲氧基聚氧化烯二醇(所谓的mpegs)的生产中),固体(无水)碱金属醇盐或碱土金属醇盐可用作催化剂,例如甲醇钠或甲醇钾。在一定程度上自催化的胺起始剂的情况下,可以在不添加单独的催化剂的情况下开始反应,但是在反应过程中可以可选地在预反应器或较大的主反应器中随后添加单独的催化剂。本发明的另一个实施例是可以可选地向第二反应容器中添加另外的催化剂。
44.本发明的主题进一步是特别用于实施根据上述描述的烷氧基化物的生产方法的设备,其包括至少一个较小的第一预反应器和至少一个第二主反应器,该至少一个较小的第一预反应器配备有第一循环回路,所述第一循环回路包括至少循环泵和热交换装置,至少一个第二主反应器配备有循环回路,该循环回路包括至少循环泵和热交换装置,该至少一个较小的第一预反应器和该至少一个第二主反应器以较小的第一反应器的内容物可被转移到较大的第二反应器的方式连接,并且其中至少一个循环回路包括喷射式注入器喷嘴。
45.优点来自甚至在第一循环回路中使用至少一个喷射回路反应器的事实,因为喷射回路反应器能够实现高的传质速率。这种喷射回路通常包括集成到循环回路中的至少一个反应器、将反应介质和/或至少一种单体化合物注入到所述反应器中的至少一个喷射装置、在所述循环回路中输送反应介质的至少一个泵和可选地至少一个冷却装置,特别是在所述循环回路中的至少一个热交换器,以便在反应介质再循环到反应器中之前冷却反应介质。
46.根据本发明的优选实施例,设备包括至少一个管线,其从所述第一循环回路的泵下游和所述加热器/冷却器上游的第一循环回路的分支处起始,并且将第一循环回路与主循环回路中的较大的第二反应器连接。
47.根据本发明的优选实施例,所述第二循环回路中的主反应器是喷射回路反应器,
这意味着设备的两个循环回路中的每一个内的至少一个反应器是喷射回路反应器类型的反应器,包括将反应介质和/或至少一种单体离析物分别注入第一反应器和第二反应器的至少一个喷射装置,优选所述第二主循环回路包括第二循环回路中的至少一个喷射回路反应器、至少一个泵和至少一个加热器/冷却器。最优选地,两个反应器,即第一循环回路中较小的第一反应器以及第二循环回路中较大的第二反应器,分别是喷射回路反应器。
附图说明
48.下面将参照附图进一步说明本发明的优选实施例,其中,
49.图1是根据本发明的可能实施例的包括较小和较大的喷射回路反应器的示例性设备的简化示意图;
50.图2是示出根据本发明的示例性实施例的质量平衡的框图。
具体实施方式
51.下面参照图1说明本发明的优选实施例。附图进行了简化,仅示出了有助于理解本发明的设备的那些主要部件。该设备包括用于制备预聚物并且配备有第一循环回路10的较小的第一反应器11。所述第一循环回路10包括较小的第一反应器11、从较小的第一反应器11的底部开始的输出管线12,输出管线12用于通过泵13在循环回路10内输送反应混合物。泵13在第一循环回路10内输送反应混合物,第一循环回路10包括分支连接部14,第一管线15从分支连接部14通向指定用于冷却反应混合物的热交换器/冷却器16,该反应混合物在第一循环回路内经由输出管线12、泵13、管线15、热交换器16和管线17循环回到反应器11的顶部。
52.因此,只要分支连接部14通向管线15,反应混合物就在封闭的循环回路10内循环,这是在制备预聚物的第一反应阶段中的情况。在较小的第一反应器11中的反应开始时提供例如约0.5m3的小体积的起始材料20,其可以例如为较小的第一反应器11的总体积的约十分之一。此后,经由管线18添加一种或多种单体离析物,并且在第一反应器11内制备预聚物。所述反应器11优选为喷射回路反应器,其包括注入装置19,所述注入装置19具有喷射喷嘴并且设计成将单体离析物和在管线17中流动的循环反应混合物注入到第一反应器中。第一反应阶段包括预加热起始材料20(引发剂)、添加催化剂、干燥、加热至反应温度、经由管线18相继添加指定的计算量的一种或更多种单体离析物、以及使反应混合物在回路10内循环直到所有单体离析物都已经与预聚物反应。此后,关闭通向管线15的分支连接部14,并且打开替代管线21,优选地通过替代管线21将全部量的所得预聚物转移到较大的第二反应器22中,较大的第二反应器22配备有较大的第二循环回路25,并且可以被认为是根据本发明的方法中的主反应器。在所述较大的第二循环回路25内,如上所述在较小的第一循环回路10中获得的预聚物反应为最终指定的聚合物。较大的第二反应器22的体积可以例如为较小的第一反应器11的体积的大约十倍。因此,例如在较小的第一循环回路10中制备的约5m3体积的预聚物可以经由管线21转移到较大的第二反应器22中,较大的第二反应器22可以具有例如约50m3的总反应器体积。
53.较大的第二主反应器22配备有较大的第二循环回路25,其中,提供了预先在较小的第一反应器11中制备的预聚物23。较大的第二循环回路25还包括从较大的第二反应器22
的底部开始的管线24、所述管线中的泵26,泵26用于将较大的第二循环回路25内的反应混合物经由管线27输送通过热交换器/冷却器28以冷却反应混合物,然后该反应混合物经由管线29再循环至主反应器22的顶部。
54.另外的量的一种或多种单体离析物经由管线30连续添加到第二注入装置31中,第二注入装置31包括喷嘴和混合装置,用于将在管线29内流动的反应混合物与经由管线30添加的单体化合物混合,并且将所述混合物在顶部区域注入到主反应器22中。因此,较大的第二循环回路25也是喷射循环回路,其充分混合反应组分,并且优选地以高速和精细分散的方式经由喷嘴将其注入到较大的第二反应器22中。在第二循环回路25内循环反应混合物,直到所提供的全部体积的预聚物23都已经与所添加的单体复合物(一种或多种)反应成具有特定分子量的指定聚合物复合物。在已经经由管线30添加了全部量的一种或更多种单体离析物之后,反应完成。这里要提到的是,这些一种或更多种的离析物可以与之前在第一循环回路中用于制备预聚物的离析物相同。然而,这不是强制性的,因为可选地,可以在较大的第二循环回路中执行的反应阶段中添加不同的单体离析物。
55.在下文中,参考图2的框图,更详细地说明本发明的示例性实施例。该框图被简化并且仅示出了有助于理解根据本发明的方法的主要质量流。例如,在较小的第一反应器11内制备预聚物的方法的第一步骤中,使用约700kg/批次的甘油作为起始材料20。向甘油中添加例如溶解在90kg/批次水中的约90kg/批次koh作为催化剂32。现在对原料进行干燥,并且水作为来自真空干燥的废物经由管线33排放到水收集装置34。例如,将约4300kg/批次的环氧丙烷(propylene oxide)作为单体原料18添加到较小的第一循环回路中的第一反应器11中。
56.将在较小的第一反应器11中生产的约5000kg/批次预聚物通入较大的第二喷射反应器22。将6700kg/批次的环氧乙烷(ethylene oxide)和33000kg/批次的环氧丙烷的量作为另外的单体离析物添加到较大的第二反应器22中(见30)。通过使这些另外的量的单体离析物30与预聚物在较大的第二反应器22中反应,例如在较大的第二反应器中产生约45000kg/批次的多元醇产物(polyol product)。该多元醇产物可以通过经由管线36添加至后处理反应器39的中和剂35来进行后处理39。此后,约45000kg/批次的最终多元醇产物可以经由管线37输送至过滤装置38,多元醇产物在过滤装置38中进行纯化。
57.附图标记表
58.10
ꢀꢀ
第一循环回路
59.11
ꢀꢀ
较小的第一反应器
60.12
ꢀꢀ
输出管线
61.13
ꢀꢀ
泵
62.14
ꢀꢀ
分支连接部
63.15
ꢀꢀ
管线
64.16
ꢀꢀ
热交换器
65.17
ꢀꢀ
管线
66.18
ꢀꢀ
管线
67.19
ꢀꢀ
注入装置
68.20
ꢀꢀ
起始材料
69.21
ꢀꢀ
替代管线
70.22
ꢀꢀ
较大的第二反应器
71.23
ꢀꢀ
预聚物
72.24
ꢀꢀ
管线
73.25
ꢀꢀ
第二循环回路
74.26
ꢀꢀ
泵
75.27
ꢀꢀ
管线
76.28
ꢀꢀ
热交换器/冷却器
77.29
ꢀꢀ
管线
78.30
ꢀꢀ
管线
79.31
ꢀꢀ
注入装置
80.32
ꢀꢀ
催化剂
81.33
ꢀꢀ
管线
82.34
ꢀꢀ
收集装置
83.35
ꢀꢀ
中和剂
84.36
ꢀꢀ
管线
85.37
ꢀꢀ
管线
86.38
ꢀꢀ
过滤装置
87.39
ꢀꢀ
后处理反应器
再多了解一些
本文用于企业家、创业者技术爱好者查询,结果仅供参考。