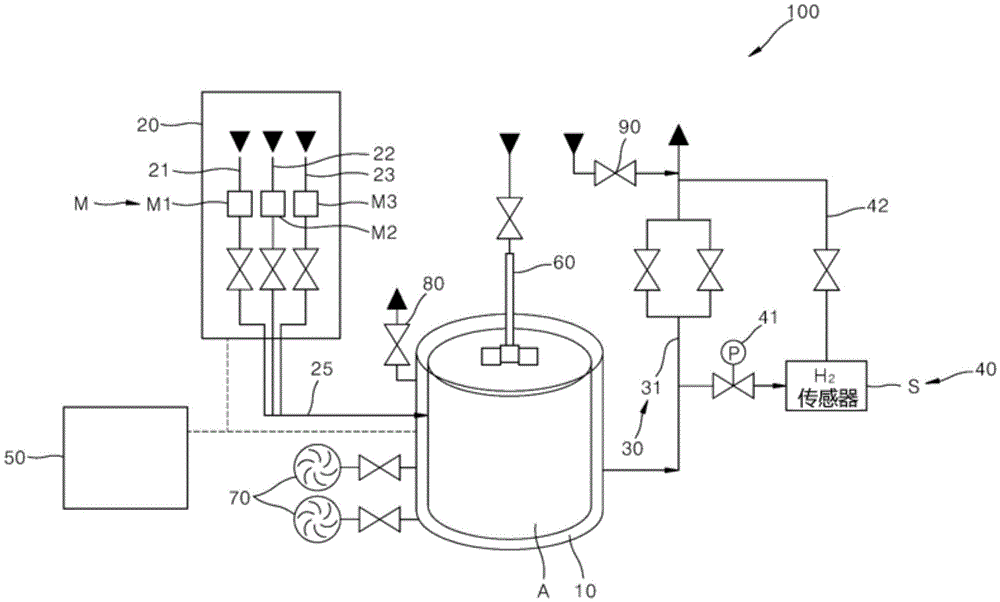
本发明涉及一种氮化设备及氮化方法,更具体地,涉及一种能够通过将诸如氮的硬化元素吸附并扩散到金属产品的表面上和金属产品的表面中而形成高浓度氮化层的氮化设备和氮化方法。
背景技术
铁的表面硬化包括通过施加热量使反应气体中的必要组成扩散到铁表面中来改变铁的表面的化学组成的热化学表面硬化以及通过淬火仅硬化铁的表面而不改变铁的表面的化学组成的物理表面硬化。通常,热化学表面硬化的示例包括碳化、氮化、硫化和硼化,物理表面硬化的示例包括感应硬化和火焰硬化。
作为热化学表面硬化的一种,氮化是指将氮原子扩散到铁表面中的方法,与诸如碳化的其他表面处理方法相比,氮化可以在不引起尺寸或形状变形的情况下实现精度。在氮化中,诸如熔炉的反应室被装载由钢制成的产品并且被加热到一定温度,然后包含诸如氨(NH3)的反应气体的处理气体被注入反应室中。注入的氨被解离成氮和氢,氮扩散到钢的表面中以在其上形成氮化层。处理气体是包含氨气的混合气体,除氨气之外,还包含二氧化碳气体、碳氢化合物气体、氮气等。
在这种情况下,由于肉眼看不到反应室中发生的氮化,因此可以测量氨分解率来测量金属产品的表面上的氮化程度。为了测量氨分解率,通常使用通过测量反应室内的氢的分压并且基于氢的分压计算氮化势(nitriding potential)来测量氮化程度的方法。氮化势是指氮化能力并且是用于确定氮化程度的最关键因素。在AMS2759-10A中如下定义了氮化势KN。
其中,表示氨的分压,表示氢的分压。
技术实现要素:
技术问题
然而,根据上述现有的氮化设备和氮化方法,氨气与其他气体(例如,二氧化碳气体和氮气,或碳氢化合物和氮气)以固定比例混合的处理气体被注入到反应室中,因此需要单独的气体分解炉来控制能够控制氮化程度的氮化势。例如,可以通过在单独的气体分解炉中使氨气分解以产生包括氮和氢的混合物的分解氨气,并控制供应到反应室的分解氨气的量,来控制氮化势。
这样,根据现有的氮化设备和氮化方法,由于另外需要高价的氨分解炉来产生氢以控制氮化势,因此氮化设备的成本增加,需要较大的安装空间,氮化所消耗的处理气体量过度增加。
本发明提供一种氮化设备和氮化方法,其能够通过在金属氮化处理中将反应室用作氨分解炉,容易地控制反应室中金属产品的氮化程度,并且通过使用在反应室中通过热分解处理气体中包括的氨气产生的氢气来控制氮化势。然而,本发明的范围不限于此。
技术方案
根据本发明的一个方面,提供一种氮化设备。
氮化设备包括:反应室,所述反应室包括在其中对金属进行氮化的处理空间;处理气体供应器,所述处理气体供应器用于向反应室供应包含氨气的处理气体;排放器,所述排放器用于排放在反应室中分解或未分解的处理气体;传感器,所述传感器用于感测反应室内的氢的分压;以及控制器,所述控制器用于通过从传感器接收氢的分压来计算反应室内的氮化势,并且基于氮化势控制反应室的内部温度和供应给反应室的处理气体的流速。
控制器可以在氨气注入到反应室中之后关闭处理气体供应器,使反应室的内部温度升高到预设温度以分解注入的氨气,并且通过控制处理气体供应器的打开或关闭来控制注入到反应室中的处理气体的流速,以在内部温度达到预设温度之后使氮化势保持在预设的基准值。
氮化设备可以通过反应室中的氨气的分解来产生氢,并且可以不包括除了反应室之外的单独的氨分解炉。
控制器可以基于[式1]计算氮化势。
控制器可以提供控制以在反应室的内部压力小于预设压力时关闭排放器,并且在内部压力大于或等于预设压力时打开排放器。
控制器可以通过基于开/关控制或比例-积分-微分(PID)控制来控制处理气体供应器,对处理气体的流速进行控制。
传感器可以包括:氢传感器;泵,所述泵用于泵送通过气体排放管线排放的处理气体并且将处理气体供应给氢传感器;以及排气管线,所述排气管线用于将已经通过氢传感器的处理气体排出到气体排放管线。
根据本发明的另一方面,提供一种使用包括处理空间的反应室的氮化方法,包含氨气的处理气体被注入到处理空间中以氮化金属。
氮化方法可以包括:将氨气通过处理气体供应器注入到反应室中的步骤;关闭处理气体供应器,然后通过使反应室的内部温度升高到预设温度来分解氨气从而产生氢气的步骤;在反应室的内部温度达到预设温度后,通过使用传感器计算反应室内的氮化势的步骤;以及氮化势控制步骤,当计算出的氮化势达到预设基准值时,通过控制处理气体供应器以将反应室内的氮化势保持在预设基准值,来控制注入到反应室中的氨气的流速。
可以基于[公式1]计算氮化势。
[公式1]中的氢的分压PH2可以基于由注入到反应室中的氨气的分解产生的氢。
预设温度可以具有450℃至650℃的范围。
当反应室的内部压力小于预设压力时,用于排放在反应室中分解或未分解的处理气体的排放器可以关闭,并且当内部压力大于或等于预设压力时,用于排放在反应室中分解或未分解的处理气体的排放器可以打开。
通过基于开/关控制或比例-积分-微分(PID)控制来控制处理气体供应器,可以对氨气的流速进行控制。
有益效果
根据本发明的上述实施例,反应室可以用作金属氮化处理中的氨分解炉,因此可以使用通过在反应室中热分解处理气体中包含的氨气产生的氢容易地控制氮化势。
这样,可以在不使用单独的氨分解炉的情况下容易地控制在氮化设备的反应室中氮化金属产品的程度。然而,本发明的范围不限于上述效果。
附图说明
图1是根据本发明的实施例的氮化设备的示意图。
图2是图1的氮化设备的处理气体供应器的示意图。
图3是根据本发明的另一实施例的氮化设备的示意图。
图4是根据本发明的又一实施例的氮化方法的流程图。
图5是示出根据图4的氮化方法控制反应室的内部温度和氮化势的工序的图。
图6包括示出在根据本发明的各个实施例的氮化设备和氮化方法中通过控制氮化势来控制金属产品的氮化程度的结果的图像。
具体实施方式
在下文中,将通过参照附图解释本发明的实施例来详细描述本发明。
然而,本发明可以以许多不同的形式来体现,并且不应被解释为限于本文所阐述的实施例;相反,提供这些实施例是为了使本公开全面和完整,并将本发明的概念充分传达给本领域的普通技术人员。在附图中,为了清楚和便于说明,夸大了层的厚度或尺寸。
本文参考本发明的理想化实施例(和中间结构)的示意图来描述本发明的实施例。这样,可以预期由于例如制造技术和/或公差而导致的图示形状的变动。因此,本发明的实施例不应被解释为限于本文所示区域的特定形状,而是包括例如由制造引起的形状偏差。
图1是根据本发明的实施例的氮化设备100的示意图。图2是图1的氮化设备100的处理气体供应器20的示意图。图3是根据本发明的另一实施例的氮化设备200的示意图。
最初,如图1所示,根据本发明的实施例的氮化设备100可以包括反应室10、处理气体供应器20、排放器30、传感器40、控制器50、气流风扇60、冷却器70、真空部80和燃烧气体供应器90。
如图1所示,反应室10可以是一种熔炉,该熔炉包括在其中氮化金属产品的处理空间A。具体地,反应室10可以接收包括氨气并且从下面将描述的处理气体供应器20供应的处理气体,并且通过使用设置在一侧的加热器将处理空间A的内部温度保持在一定温度一定时间来氮化其中的金属产品的表面。在这种情况下,可以以各种方式控制内部温度和保持时间,以在反应室10中将氮化层形成至期望的厚度。
此外,气流风扇60可以安装在反应室10的顶部上,以通过使用在处理空间A中旋转的风扇引起处理气体在处理空间A中的流动,形成处理气体在处理空间A中的均匀扩散和分布。为了防止在处理空间A中旋转的气流风扇60的风扇被处理气体污染,可以通过气流风扇60朝向风扇精细地喷射氮气来净化风扇。
排气管线80和冷却器70可以连接到反应室10,排气管线80连接到真空泵以通过排出处理空间A内的空气来形成真空气氛,并且冷却器70能够在金属产品被氮化后排出处理空间A内的热量。
如图1和图2所示,处理气体供应器20可以将处理气体供应给反应室10。具体地,处理气体可以是包含氮气(N2)、氨气(NH3)、二氧化碳(CO2)气体、一氧化碳(CO)气体和碳氢化合物气体中的至少一种的混合气体,并且处理气体供应器20可以包括:用于供应氮气的第一气体供应管线21;用于供应氨气的第二气体供应管线22;用于供应二氧化碳气体、一氧化碳气体或碳氢化合物气体的第三气体供应管线23;以及第四气体供应管线25,第四气体供应管线25连接到第一气体供应管线21、第二气体供应管线22、第三气体供应管线23以向反应室10供应处理气体。
处理气体供应器20的第一气体供应管线21、第二气体供应管线22和第三气体供应管线23中的每一个可以设置有质量流速控制器(MFC)M,并且MFC M的打开或关闭可以通过控制器50控制以精细地控制供应给反应室10的每种处理气体。
例如,如图2所示,用于供应氮气的第一气体供应管线21可以包括高压氮气供应管线21b以快速增加反应室10的处理空间A的压力,并且通过高压氮气供应管线21b在高压下将氮气填充到处理空间A中。当处理空间A的压力通过高压氮气供应管线21b达到一定压力时,可以通过主氮气供应管线21a精确地供应氮气,并且可以通过安装在主氮气供应管线21a上的第一MFC M 1精确地控制氮气的流速。可以进一步提供氮气旁路管线21c,氮气旁路管线21c用作当在氮化处理过程中发生错误时将反应室10的处理空间A内的处理气体排出的安全装置。
电磁阀V可以安装在第一气体供应管线21的每条管线21a、21b或21c上以控制其打开或关闭,并且压力传感器P和压力计G可以设置在一侧以适当地控制第一气体供应管线21的压力。此外,压力调节器R可以安装在主氮气供应管线21a的上游侧处,以精确地控制通过主氮气供应管线21a供应的氮气的压力。
第二气体供应管线22可以包括主氨气供应管线22a和氨气旁路管线22b,主氨气供应管线22a能够通过第二MFC M2将氨气精确地供应给反应室10的处理空间A,氨气旁路管线22b用作由手动阀控制的旁路管线并且可以在第二MFC M2发生故障时使用。可以在主氨气供应管线22a上安装电磁阀V以控制主氨气供应管线22a的打开或关闭,并且可以在一侧设置压力传感器P和压力计G以适当地控制第二气体供应管线22的压力。
在这种情况下,当在氮化处理后氨气被填充到第二气体供应管线22和第二MFC M2中时,可能会发生液化而引起第二MFC M2或电磁阀V的故障。因此,处理气体供应器20可以包括净化管线24,净化管线24被连接在主氮气供应管线21a与第二气体供应管线22的一侧之间,以通过将氮气供应给第二气体供应管线22来净化第二气体供应管线22。这样,在氮化处理之后,第二气体供应管线22可以通过供应给净化管线24的氮气净化和清洁。
第三气体供应管线23可以包括主供应管线23a和旁路管路23b,主供应管线23a能够通过第三MFC M3将二氧化碳气体、一氧化碳气体和碳氢化合物气体精确地供应给反应室10的处理空间A,旁路管路23b用作由手动阀控制的旁路管路并且在第三MFC M3发生故障时可用。可以在主供应管线23a上安装电磁阀V以控制其打开或关闭,并且可以在一侧设置压力传感器P和压力计G以适当地控制第三气体供应管线23的压力。
如图1所示,排放器30可以通过气体排放管线31排放在反应室10中分解或未分解的处理气体。燃烧气体供应器90可以连接到排放器30的后端,以通过将液化石油气(LPG)或液化天然气(LNG)注入到排放器30中来燃烧排出的氨气。
传感器40可以包括安装在连接在反应室10与排放器30之间的气体排放管线31上的氢传感器S以感测反应室10内的氢的分压。具体地,传感器40可以包括:泵41,泵41用于泵送通过气体排放管线31排放的处理气体并将处理气体供应给氢传感器S;以及排气管线42,排气管线42用于将已经通过氢传感器S的处理气体排出到气体排放管线31。
控制器50可以电连接到反应室10、处理气体供应器20、排放器30和传感器40以控制每个元件,通过从传感器40的氢传感器S接收感测到的氢的分压来计算反应室10内的氮化势,并控制反应室10的内部温度、供应给反应室10的处理气体的流速以及排放器30的打开或关闭。
例如,控制器50可以在氨气通过处理气体供应器20注入到反应室10之后关闭处理气体供应器20以在反应室10中形成氨气氛,并且将反应室10的内部温度升高至预设温度。在这种情况下,预设温度是氨气可以分解的温度,并且可以具有例如450℃至650℃的范围。当反应室10的内部温度升高时,氨气分解并且在反应室10中产生氢气。当在反应室10中产生氢气时,反应室10的内部压力增大并且氮化势开始改变。
控制器50可以在反应室10的内部温度达到预设温度后从传感器40接收氢的分压,并基于接收到的氢的分压来计算氮化势。控制器50将计算出的氮化势与预设的基准氮化势进行比较,并提供控制以使计算出的氮化势与基准氮化势之差最小化,以将反应室10内的氮化势保持在基准氮化势。具体地,控制器50可以通过控制处理气体供应器20中包括的每个气体供应管线的打开或关闭来控制注入到反应室10中的处理气体(例如,氨气)的流速。
为了防止当由于氨气分解产生的氢气导致反应室10的内部压力增大到一定压力以上时发生诸如反应室10爆炸的问题,控制器50可以从安装在反应室10上的压力传感器(未示出)接收内部压力,并且控制排放器30的打开或关闭以使内部压力不增大到预设压力以上。
因此,控制器50在氨气分解的早期阶段提供控制以关闭处理气体供应器20和排放器30这两者并升高反应室10的内部温度,但是当内部压力达到一定基准压力时提供控制以打开排放器30使得不增大反应室10的内部压力。
在这种情况下,控制器50可以根据金属产品的氮化的所需的精度而选择性地使用开/关控制或比例-积分-微分(PID)控制。
根据本发明,在控制器50的控制下执行氮化处理之前,在与外部环境密封的反应室10中分解氨气并产生氢气,因此反应室10不仅用作执行氮化处理的处理空间,而且还用作氨气分解以产生用作用于控制氮化势的基础的氢气的熔炉。
本发明人已经发现,当使用由AMS2759-10A定义的现有公式计算反应室10内的氮化势时,可能无法有效地实施根据本发明的控制。因此,本发明人通过多次实验提出了[公式1]作为针对本发明的控制方法优化的氮化势计算公式。
[公式1]
Kn:氮化势
X:氨分解率
氢的分压
本发明人能够通过基于[公式1]中所示的氮化势计算公式来控制氮化势,使用反应室10作为氨分解炉而不使用单独的氨分解炉,以非常高的精度控制氮化势。
例如,在金属产品的氮化处理中氮化势Kn的基准值被指定为C时,由于反应室10中的氨气的分解,氨气的量可以减少,并且氢气的量可以增加,并且氮化势可以降低到C以下。然后,控制器50可以仅控制处理气体供应器20的第二气体供应管线22,以仅将处理气体的氨气供应到反应室10一段时间。这样,反应室10中的氨气的量可以增加,并且氮化势可以再次增加到超过C。在这种情况下,当第二气体供应管线22再次关闭时,氨气可能再次分解,并且氮化势可能在有效值内细微地变化并持续地保持在基准值C。
反应室10内的氢的分压可以如上所述以循环方式测量,或者如在图3中所示根据本发明的另一个实施例的氮化设备200中那样测量,传感器40可以直接安装在反应室10上以测量氢的分压。
例如,如图3所示,氢传感器S可以直接安装在反应室10的一侧,因此可以直接测量反应室10的处理空间A内的氢的分压。这样,可以在氮化处理的过程中持续地实时监测反应室10内的氢的分压。如上所述,还可以基于实时感测到的氢的分压来实时监测氮化势。
现在将详细描述使用上述氮化设备的氮化方法。
图4是根据本发明的又一实施例的氮化方法的流程图,图5是示出图4的流程图所示的氮化方法中反应室10的内部温度随时间的变化和氮化势Kn的随时间变化的图。
参考图4和5,氮化方法可以依次包括氨注入步骤S10、氨分解步骤S20、氮化势计算步骤S30和氮化势控制步骤S40。
在氨注入步骤S10中,可以通过打开处理气体供应器20将氨气注入到反应室10中。在这种情况下,反应室10的内部温度T1可以具有氨气基本上不分解的范围,例如室温至400℃的范围。
之后,在氨分解步骤S20中,可以关闭处理气体供应器20和排放器30,然后可以使反应室10的内部温度T1升高到预设温度T2。预设温度T2是氨气可以分解的温度,并且可以具有例如450℃至650℃的范围。
这样,当反应室10的内部温度T1升高到预设温度T2时,反应室10中的氨气分解为氢气和氮气。由于在该步骤中产生氢气,如图5所示,氮化势Kn开始降低。
然后,在氮化势计算步骤S30中,在反应室10的内部温度T 1达到预设温度T2之后,基于由传感器40的氢传感器S感测到的氢的分压,如[公式1]所示,计算反应室10内的氮化势Kn。
具体地,在氮化势计算步骤S30中,通过在氨分解步骤S20之后持续地关闭处理气体供应器20和排放器30,由反应室10中的氨气的分解产生的氢可以累积在反应室10中,而不排放到外部。这样,可以增大反应室10内的氢的分压以逐渐降低氮化势Kn,在这种情况下,可以通过使用氢传感器S实时地感测反应室10内的氢的分压,来实时地感测氮化势Kn的变化。在某些情况下,当在该步骤中产生过量氢气并因此反应室10的内部压力增加到基准压力以上时,可以通过打开排放器30而将内部压力控制为保持在基准压力以下。
然后,当感测到的反应室10内的氮化势Kn降低到预设基准值时,在氮化势控制步骤S40中,可以通过控制处理气体供应器20的打开或关闭,适当地控制注入反应室10中的氨气的流速,以将反应室10内的氮化势Kn持续地保持在基准值。
在氮化势控制步骤S40中,可以通过根据氮化金属的所需精度,选择性地使用开/关控制或PID控制来控制氨气的流速。
例如,如图5所示,基于开/关控制,虽然氮化势Kn基于基准值持续地细微变化,但由于装置配置简单并且处理成本低,因此,在不需要高精度的时候可以使用开/关控制。
另一方面,当需要高精度的氮化时,可以使用PID控制。在这种情况下,可以基于从氢传感器S传输的氢的分压的变化,以高精度极其细微地控制注入反应室10中的氨气的流速,因此可以非常精确地控制氮化势Kn,如图5所示。
在根据本发明的各种实施例的氮化设备和氮化方法中,反应室10可以用作金属氮化处理中的氨分解炉,因此可以使用通过在反应室10中热分解处理气体中包括的氨气产生的氢来容易地控制氮化势。
这样,不额外需要高价氨分解炉来产生用于控制氮化势的氢气,并且可以减少处理气体的消耗量,因为可以通过仅控制处理气体的氨气的供应量来控制氮化势。此外,可以在不使用额外的设备的情况下通过控制氮化势容易地控制在反应室10中将金属产物氮化的程度。
本发明的上述氮化设备和氮化方法可以控制在金属氮化处理中氮化层的氮化浓度,因此可以应用于需要耐磨性和抗振动冲击韧性的汽车部件,例如齿轮、轮毂和轴。
现在将描述本发明的实验例。然而,以下实验例仅用于更好地理解本发明,本发明不限于此。
使用图1所示的氮化设备100对低碳钢进行氮化。实验例中使用的低碳钢的组成如表1所示。
[表1]
用于氮化处理的反应室10的温度保持在520℃,对于氮化处理的气氛,通过适当地控制氮(N2)、氨(NH3)和二氧化碳(CO2)的比例,在氮化势控制步骤中将氮化势Kn控制为0.3、1、2和7。在这种情况下,使用PID控制来控制注入反应室10中的氨的流速。图6包括示出在0.3、1、2和7的氮化势下低碳钢的表面的图像。
参考图6,通过在氮化处理中改变氮化势,在具有α相的低碳钢表面上形成具有不同相的氮化层。
具体地,当氮化势保持在0.3时,形成γ’相。当氮化势增大并保持在1时,与氮化势为0.3的情况相比,γ’相在表面上形成得更厚。当氮化势增大并保持在2时,形成γ’相,并且在其上也形成ε相,当氮化势进一步增大并保持在7时,ε相形成得更厚直至γ’相的下部区域。因此,如图6所示,可以通过精确地控制氮化势来控制在低碳钢的表面上形成的氮化层的相。
虽然本发明已经参照其实施例进行了具体展示和描述,但是本领域普通技术人员将理解,在不脱离由以下权利要求定义的本发明的范围的情况下,可以对其中的形式和细节进行各种改变。
工业应用性
根据本发明的上述实施例,因为可以实现这样的氮化设备:该氮化设备能够通过在金属氮化处理中使用反应室作为氨分解炉来对金属产品进行氮化,而无需使用单独的氨分解炉,所以可以减少氮化设备的安装空间并且也可以降低处理成本。
本文用于企业家、创业者技术爱好者查询,结果仅供参考。