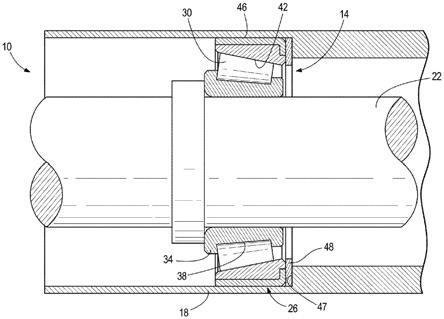
具有过盈配合的两件式复合圆锥滚子轴承外圈和制造方法
1.相关申请本技术请求保护于2019年7月15日提交的美国临时专利申请no. 62/874,139的权益,其全部内容以引用方式并入在此。
技术领域
2.本发明涉及圆锥滚子轴承,并且更具体地涉及圆锥滚子轴承的外圈。
背景技术:
3.用于圆锥滚子轴承的常规外圈由棒料机加工或锻造而成。然而,已经做出一些尝试来用金属板材形成外圈(当该过程更具成本效益时)。但是在使用金属板材的情况下,涉及到额外的技术挑战。例如,轴承设计的一个考虑因素包括以下的事实:由于金属板材外圈的薄的厚度,由金属板材制成的外圈本身可能不能够支撑一些轴承的高负载和高接触压力。一种用来提供足够支撑的方法涉及将金属板材外圈与可分离的背衬圈结合。
4.另外,由薄的金属板材冲压而成的外圈由于由薄的金属板材形成而典型地呈波纹状。这种波纹性阻止外圈与滚子和背衬圈保持一致的接触,并且因此引起在循环加载下反复变形。波纹状滚道也是噪音和振动的来源,其可显著地降低轴承的使用寿命。此外,背衬圈典型地被形成为轴承的壳体的一体部分,以降低成本。在背衬圈固定在壳体中的情况下,可能不能在壳体中轴向地调节外圈以为轴承提供正确的预负载。
5.另一种用于在没有背衬圈的情况下提供足够支撑的方法涉及形成具有厚横截面的外圈,使得外圈自身可支撑较高的负载和较高的接触压力。为了由金属板材形成这种尺寸的外圈,必须使用较厚的金属板材。然而,由具有小的直径厚度比的坯料(即,由较厚的金属板材)形成具有带有厚的横截面的背面的外圈(这正是正确地形成外圈的所需要的几何形状所需要的)是困难的。
技术实现要素:
6.本发明的实施例提供了一种用于圆锥滚子轴承的外圈,其可提供对施加在轴承上的工作负载的足够支撑,而不使用可分离的背衬圈或不由厚金属板材形成外圈。所述实施例还避免了由薄的钢板材冲压而成的座圈的波纹性,从而显著地消除在操作期间高噪音和高振动的风险。本发明的实施例还提供了一种外圈,该种外圈可在轴承的壳体内在轴向上调节,以提供正确的预负载。这通过单独地形成背衬构件和滚道构件并将这两个构件压配合在一起以形成整体化复合圆锥滚子轴承外圈来实现。
7.在一个方面中,本发明提供了一种用于轴承组件的外圈。该外圈包括环形背衬构件和环形座圈构件。环形背衬构件具有带有第一部分和第二部分的本体。该第一部分限定径向内表面和径向外表面。该第二部分以一角度延伸远离第一部分,并且限定面向轴向的基部表面和面向径向的端部表面。环形座圈构件具有径向外面、径向内面、第一轴向端面和第二轴向端面。每个轴向端面在径向外面和径向内面之间延伸。环形背衬构件处于与环形
座圈构件的压配合接合中,使得环形座圈构件的径向外面接合环形背衬构件的径向内表面,并且环形座圈构件的第二轴向端面接合环形背衬构件的面向轴向的基部表面,使得环形背衬构件和环形座圈构件被整体化。
8.在另一方面中,本发明提供了一种轴承组件。该种轴承组件包括壳体、与壳体接合的外圈、限定内座圈的内圈、多个滚动元件以及延伸穿过内圈的轴。外圈包括环形背衬构件和环形座圈构件。环形背衬构件具有带有第一部分和第二部分的本体。第一部分限定径向内表面和径向外表面。第二部分以一角度延伸远离第一部分,并且限定面向轴向的基部表面和面向径向的端部表面。环形座圈构件具有径向外面、径向内面、第一轴向端面和第二轴向端面。每个轴向端面在径向外面和径向内面之间延伸。环形背衬构件处于与环形座圈构件的压配合接合中,使得环形座圈构件的径向外面接合环形背衬构件的径向内表面,并且环形座圈构件的第二轴向端面接合环形背衬构件的面向轴向的基部表面,使得环形背衬构件和环形座圈构件被整体化。多个滚动元件与内座圈和外座圈滚动地接合,使得内圈被构造成相对于外圈旋转。轴联接到内圈,使得内圈被构造成与轴一起旋转。
9.在又一方面中,本发明提供了一种制造轴承组件的外圈的方法。该种方法包括形成环形背衬构件,该环形背衬构件具有本体,该本体具有:第一部分,其限定径向内表面和径向外表面;和第二部分,其以一角度延伸远离第一部分,并且限定面向轴向的基部表面和面向径向的端部表面。该方法还包括由金属板材坯料形成环形座圈构件,该环形座圈构件具有径向外面、径向内面、第一轴向端面和第二轴向端面,每个轴向端面在径向外面和径向内面之间延伸。该方法然后包括将环形背衬构件和环形座圈构件压配合在一起,使得环形背衬构件和环形座圈构件形成整体化外圈,其中环形座圈构件的径向外面接合环形背衬构件的径向内表面,并且环形座圈构件的第二轴向端面接合环形背衬构件的面向轴向的基部表面。
附图说明
10.图1是使用根据本发明的复合圆锥滚子轴承外圈的轴承组件的局部截面图。
11.图2是图1的整体化复合圆锥滚子轴承外圈的截面图。
12.图3是图1的复合圆锥滚子轴承外圈的座圈构件的截面图。
13.图4是图1的复合圆锥滚子轴承外圈的座圈构件的放大截面图。
14.图5是图1的复合圆锥滚子轴承外圈的背衬构件的截面图。
15.图6是图1的复合圆锥滚子轴承外圈的背衬构件的放大截面图。
具体实施方式
16.在详细解释本发明的任何实施例之前,应当理解,本发明在其应用中不限于在以下描述中阐述的或在以下附图中示出的部件的构造和布置的细节。本发明能够具有其他实施例并且能够以多种方式实践或实施。
17.参考图1,示出了轴承组件10。轴承组件10可在任何数量的应用中使用(一般包括工业和机动车应用),并且轴承组件10包括轴承14、壳体18和轴22。轴承14包括整体化复合外圈26、多个滚动元件30和内圈34。内圈34限定内滚道38,并且整体化复合外圈26限定外滚道42。多个滚动元件30与外滚道42和内滚道38两者滚动地接合,使得内圈34能够相对于整
体化复合外圈26旋转。轴22延伸穿过内圈34并联接到该内圈34,使得内圈34与轴22一起旋转。
18.整体化复合外圈26与壳体18的内表面46接合,使得轴向预负载力施加在整体化复合外圈26、滚动元件30和内圈34上。更具体地,壳体18的内表面46可包括肩部47,以支撑外圈26的面向轴向的端部表面。在肩部47和外圈26之间使用间隔件48来获得期望的预负载。可选择/改变间隔件48的厚度,以实现期望的轴承预负载。
19.预负载力的大小影响轴承组件10的性能。当预负载力的大小太小(这可在所安装的轴承内引起少量的轴向间隙(即端部游隙))时,整体化复合外圈26和内圈34不在滚动元件30上施加足够大的法向力。因为法向力太小,内圈34和整体化复合外圈26不在滚动元件30上施加足够大以引起滚动元件30沿着内滚道38和外滚道42滚动的摩擦力。在这种情况下,滚动元件30改为沿着内滚道38和/或外滚道42滑动,这负面地影响了轴承组件10的性能。当预负载力的大小太大(这可在所安装的轴承内引起轴向过盈量)时,整体化复合外圈26和内圈34在滚动元件30上施加过大的法向力。因为法向力太大,内圈34和整体化复合外圈26在滚动元件30上施加足够大以阻碍或阻止滚动元件30沿着内滚道38和外滚道42滚动的摩擦力。在这种情况下,滚动元件30不能沿着内滚道38和外滚道42恰当地移动,并且内圈34不能相对于整体化复合外圈26恰当地旋转。为了在所安装的轴承组件10中实现正确的轴承设置/预负载,可使用间隔件48来调节外圈26和内圈34之间的相对轴向位置。间隔件48的厚度可被容易地改变。在其他实施例中,在可通过其他手段(例如,通过调节轴22相对于内圈34的轴向位置)来调节轴承预负载的情况下,可不需要间隔件48。
20.在所示出的实施例中,轴向预负载力的大小可被调节,以确保轴承组件10的期望性能。为了调节轴向预负载力,整体化复合外圈26可经由间隔件48在壳体18内轴向地移动。整体化复合外圈26在壳体18内远离内圈34的轴向移动减小了预负载力的大小,而整体化复合外圈26在壳体18内朝向内圈34的轴向移动增加了预负载力的大小。因此,滚动元件30的滚动行为可被定制以实现轴承组件10的期望性能特性。
21.在所示出的实施例中,轴承14具有相对大的尺寸,并且因此在外圈26上施加相对较高的负载和相对较高的接触压力。为了更具成本效益,外圈26的至少部分由金属板材形成。为了在至少部分地由金属板材形成的同时支撑更高的负载和接触压力,在图2中所示出的外圈26包括环形座圈构件50和环形背衬构件54。环形座圈构件50与环形背衬构件54接合,以提供整体化复合外圈26。复合外圈26的厚度由复合外圈26针对特定轴承应用将接收的力和扭矩决定,以确保恰当的轴承性能,而不会引起外圈26的两个部件之间的任何相对运动,并且不会在所施加的作用力下屈服。
22.参考图3和图4,环形座圈构件50具有径向外面58、径向内面62、第一轴向端面66和第二轴向端面70。径向内面62限定外滚道42,滚动元件30在该外滚道42上滚动。在所示出的实施例中,径向内面62是倾斜的,使得轴承14是圆锥滚子轴承。径向内表面62相对于第二轴向端面70的斜率可根据应用而变化。第一轴向端面66和第二轴向端面70在径向外面58和径向内面62之间延伸。第二轴向端面70包括轴向地突出远离第一轴向端面66的台阶74,使得台阶74部分地由径向内面62限定,并且部分地由第二轴向端面70限定。台阶74包括面向轴向的台阶面78和面向径向的台阶面82。在所示出的实施例中,面向轴向的台阶面78是第二轴向端面70的部分,并且平行于第二轴向端面70的其余部分延伸,但是在其他实施例中,轴
向台阶面78可相对于第二轴向端面70的其余部分以一角度延伸。类似地,在所示出的实施例中,面向径向的台阶面82平行于径向外面58延伸,但是在其他实施例中,面向径向的台阶面82可相对于径向外面58以非平行的角度延伸。
23.参考图5和图6,环形背衬构件54具有带有第一部分90和第二部分94的本体86。第二部分94以角度a延伸远离第一部分90。在所示出的实施例中,角度a为90度,但是在其他实施例中,角度a可略微更小,例如89度或88度,以在环形座圈构件50与环形背衬构件54接合时,在环形座圈构件50和环形背衬构件54之间提供更好的接合。优选地,角度a不比90度尖锐很多,因为更尖锐的角度a使得环形座圈构件50与环形背衬构件54更难接合。同样优选地,角度a不大于90度,因为环形座圈构件50可从环形背衬构件54脱离并滑出。第一部分90限定径向内表面98、径向外表面102和面向轴向的前表面106。面向轴向的前表面106在径向内表面98和径向外表面102之间延伸,以限定径向厚度tr。第二部分94限定面向轴向的基部表面110、面向轴向的端部表面114和面向径向的端部表面118。径向外表面102在面向轴向的前表面106和面向轴向的端部表面114之间延伸,以限定轴向长度la。
24.面向径向的端部表面118在面向轴向的基部表面110和面向轴向的端部表面114之间延伸,以限定轴向厚度ta。在所示出的实施例中,面向径向的端部表面118平行于径向外表面102延伸,但是在其他实施例中,面向径向的端部表面118可相对于径向外表面102以非平行的角度延伸。轴向厚度ta和径向厚度tr必须足够厚,以在环形座圈构件50和环形背衬构件54被整体化的情况下在轴向方向和径向方向两者上支撑环形座圈构件50。在环形背衬构件54由金属板材制成的情况下,轴向厚度ta和径向厚度tr可相同,如在所示出的实施例中所示出的那样,并且可等于金属板材的厚度(该环形背衬构件54由该金属板材形成(例如,冲切、冲压或挤压))。在其他实施例中,轴向厚度可不同于径向厚度。例如,轴向厚度可比径向厚度更薄。类似地,在一些实施例中,轴向厚度和径向厚度可比金属板材的厚度更厚或更薄(该环形背衬构件54由该金属板材形成),这取决于环形背衬构件54是如何制造的。在轴承14被安装在轴承组件10中的情况下,径向外表面102接合壳体18,并且更具体地,接合壳体18的内表面46。
25.现在参考图3和图5,环形座圈构件50的径向外面58限定外径do,并且环形背衬构件54的径向内表面98限定内径di。内径di小于外径do,使得在组装外部构件54和座圈构件50时,内径di和外径do限定构件50、54之间的过盈配合。在环形座圈构件50与环形背衬构件54被整体化的情况下,过盈配合允许环形座圈构件50相对于环形背衬构件54在轴向上紧密地保持在适当位置。过盈配合必须足以防止环形座圈构件50由于作用在整体化复合外圈26上的轴向力或在轴承14操作期间轴承14内发生的温度变化而滑出环形背衬构件54。在环形座圈构件50与环形背衬构件54被整体化的情况下,过盈配合还允许环形座圈构件50相对于环形背衬构件54以旋转方式紧密地保持在适当位置。过盈配合还必须足以防止环形座圈构件50由于作用在整体化复合外圈26上的旋转力和扭矩或在轴承14操作期间轴承14内发生的温度变化而相对于环形背衬构件54旋转。
26.如在图2中所示出的那样,在环形座圈构件50与环形背衬构件54被整体化的情况下,环形座圈构件50的径向外面58接合环形背衬构件54的径向内表面98,以径向地支撑环形座圈构件50。环形座圈构件50的第二轴向端面70,并且更具体地,第二轴向端面70的不限定面向轴向的台阶78的部分,接合环形背衬构件54的面向轴向的基部表面110,以在轴向上
支撑环形座圈构件50。同样在整体化时,台阶74的面向径向的台阶面82接合环形背衬构件54的面向径向的端部表面118,以为环形座圈构件50提供额外的径向支撑。台阶74还允许座圈构件50的径向内面62沿着轴向长度la的全部长度延伸,使得环形背衬构件54一旦安装就不与且不能与滚动元件30接触。
27.另外,在整体化时,台阶74的面向轴向的台阶面78与环形背衬构件54的第二轴向端面114共面,以限定具有总径向长度fb的共面整体化外圈背面。整体化也使环形背衬构件54的面向轴向的前表面106与环形座圈构件50的第一轴向端面66共面,以限定具有总径向长度ff的共面整体化外圈前面。在其他实施例中,情况不必如此。为了确保环形背衬构件54的径向厚度tr和轴向厚度ta足够稳健以支撑环形座圈构件50,径向厚度tr的尺寸和面向轴向的基部表面110的径向长度优选地分别随外圈前面长度ff和外圈背面长度fb变化。
28.为了制造整体化复合外圈26,首先单独地制造环形座圈构件50和环形背衬构件54。为了制造环形座圈构件50,从金属板材中的相对薄的板材冲裁金属板材坯料,该金属板材中的相对薄的板材具有相对于第二轴向端面70的厚度更薄的厚度。在所示出的实施例中,可通过激光切割或冲压冲裁过程来制造金属板材坯料,但是可使用其他方法来冲裁金属板材。然后,金属板材坯料被冲压或被形成为环形座圈构件50。因为滚动元件30直接在环形座圈构件50上滚动并且以循环方式使环形座圈构件50加载,金属板材(由该金属板材形成环形座圈构件50)是高等级钢(例如,高碳钢)。高等级钢确保环形座圈构件50具有足够高的强度和足够长的使用寿命。在所示出的实施例中,使用冲头和模具来在一系列步骤中形成环形座圈构件50,但是也可使用其他形成方法。使用冲头和模具来形成环形座圈构件50包括但不限于冲裁、拉伸或挤压、压印(coining)或设定尺寸和/或穿孔的步骤。
29.在所示出的实施例中,环形背衬构件54以类似于环形座圈构件50的方式制造,尽管在其他实施例中,环形座圈构件50和环形背衬构件54可通过不同的方法形成。从金属板材中单独地冲裁第二金属板材坯料,并且利用冲头和模具将该第二金属板材坯料形成为环形背衬构件54。然而,金属板材(由该金属板材形成环形背衬构件54)不需要是高等级钢,因为环形背衬构件54不与滚动元件30接合。金属板材(由该金属板材形成环形背衬构件54)优选地为低等级钢(例如,低至中碳钢),以降低材料成本。在其他实施例中,环形背衬构件54甚至可不由金属板材形成,而是改为可由工程塑料、尼龙、玻璃纤维或具有高强度且成本低于金属板材的其他材料形成。在这种情况下,可通过机加工、注射成型或其他制造过程来形成环形背衬构件54。可使用任何制造方法来由任何材料形成环形背衬构件54,只要该环形背衬构件54具有足够的强度、硬度和热稳定性来支撑环形座圈构件50。
30.在大多数情况下,取决于应用和过程处理要求,构件50、54可为具有不同碳和合金含量的任何类型的普通碳钢或合金碳钢。低至中碳钢在冲压期间通常需要较小的形成力,因为这些钢具有较低的屈服强度,并且更容易塑性变形;因此,需要较小的冲压设备(诸如压力机)来从这些类型的钢制造部件。另一方面,高碳钢具有高强度,并且需要大得多的冲压设备。因此,对工具的强度的要求很高。如果高碳钢在冲压前没有被适当地处理,则在已形成部件中的开裂或断裂的风险将相当高。使用具有低至中碳含量的钢的所形成的部件通常利用渗碳过程来热处理,而使用具有高碳含量的钢的所形成的部件通常利用穿透硬化过程来热处理。对于某些类型的轴承,例如在食品和饮料行业中使用的轴承,可使用不锈钢。
31.材料厚度由复合外圈26的期望壁厚、形成方案和市场上材料的可获得性决定。较
厚的钢板材将可能产生较重的所形成的复合外圈26的壁,这可将该技术的适用性增加到更宽范围的圆锥滚子轴承外圈。然而,钢板材的最大厚度通常受到特定钢等级的可获得性和订购数量的限制。
32.在环形背衬构件54和环形座圈构件50两者都已经形成之后,环形座圈构件50可压配合到环形背衬构件54中,以形成整体化复合外圈26。这可与构件50、54的形成步骤一起完成或单独完成。一个示例性过程是将环形背衬构件54加热到经升高的温度,使得其膨胀成略大于过盈量,并且然后将环形座圈构件50安装到环形背衬构件54中。然后允许部件冷却。通过使用感应加热来快速加热环形背衬构件54,环形背衬构件54的这种加热可与冲压过程一起产生。加热环形背衬构件54的温度将取决于钢的热膨胀系数和所需要的过盈量。该过盈量被计算成使得所组装的部件可经受热处理过程而不会由于部件的不同热膨胀系数而分离,并且可经受轴承上的最高预期扭矩或力,以防止在环形背衬构件54和环形座圈构件50之间的在轴向上和周向上的任何相对移动。
33.如果环形背衬构件54也由钢制成,那么整体化复合外圈26经历硬化热处理程序,以增强整体化复合外圈26的材料性质,使得整体化复合外圈26能够支撑施加在轴承14上的高负载和高接触压力,并且具有足够的强度和使用寿命。然而,如果环形背衬构件54由除金属之外的材料制成,则环形座圈构件50在被压配合到环形背衬构件54中之前经历硬化热处理程序以增强环形座圈构件50的材料性质。有时,由于硬化热处理程序,整体化复合外圈26的尺寸可改变超过可接受的公差。在这种情况下,整体化复合外圈26经历后热处理设定尺寸步骤,以获得最终操作尺寸。例如,整体化复合外圈26可被放置在冲头和模具之间,并且被拉伸和设定尺寸以使整体化复合外圈26的尺寸在可接受的公差内。然后,可将尺寸正确且整体化的复合外圈26安装到整个组件10中。
34.在所附权利要求书中阐述了本发明的多种特征和方面。
再多了解一些
本文用于企业家、创业者技术爱好者查询,结果仅供参考。