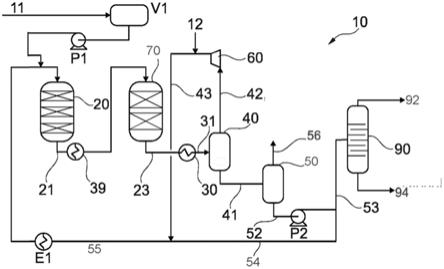
1.提供了一种用于含氧化合物原料的加氢处理单元,所述单元包括:加氢处理反应器;第一冷却单元;高压分离器和低压闪蒸单元。加氢处理单元被布置成将来自高压分离器的富氢流的至少一部分进料至加氢处理反应器;加氢处理单元被布置成将来自所述低压闪蒸单元的脱气的富烃流的一部分作为烃再循环流进料至加氢处理反应器。还提供了一种使用所述加氢处理单元对含氧化合物原料进行加氢处理的方法。
背景技术:
2.含氧化合物加氢处理单元通常使用液体再循环来控制加氢处理反应器中的温度。该液体再循环可能含有轻杂质,当它们被送回加氢处理反应器时,它们会降低加氢处理反应器中气相的纯度。反复再循环会产生不期望的轻杂质堆积。具体的杂质包括co、co2、c1、c3和其他轻质气体。
3.为了将含氧化合物原料转化为烃运输燃料,将原料与氢气一起引导与在加氢处理(尤其是加氢脱氧)中有催化活性的材料接触。为了缓和热量的释放,可以添加液态烃,例如液体再循环流或外部稀释剂进料。所得的产物流将是包含烃类(通常为正链烷烃)和酸性气体(例如co、co2、h2o和h2s)的加氢处理的中间产物流。
4.美国专利9447339涉及生物柴油燃料和共混物的加氢处理。ep2121876涉及一种生产链烷烃的方法。
5.本技术试图解决与已知加氢处理单元和技术相关的问题,主要是这些单元成本高且效率低。
6.发明概述
7.因此提供了一种用于含氧化合物原料的加氢处理单元,所述单元包括:
[0008]-加氢处理反应器;所述加氢处理反应器被布置成接收所述含氧化合物原料并将其转化为加氢处理的第一烃流;
[0009]-第一冷却单元,其被布置成接收来自所述加氢处理反应器的所述加氢处理的第一烃流并将其冷却成冷却的第二烃流;
[0010]-高压分离器,其被布置成接收来自所述第一冷却单元的冷却的第二烃流并将其至少分离成富烃流和富氢流;
[0011]-低压闪蒸单元,所述低压闪蒸单元被布置成接收来自所述高压分离器单元的富烃流并将其脱气;从而提供尾气和脱气的富烃流,
[0012]-其中所述加氢处理单元被布置成将来自高压分离器的富氢流的至少一部分进料至加氢处理反应器;且
[0013]-其中所述加氢处理单元被布置成将来自所述低压闪蒸单元的脱气的富烃流的一部分作为烃再循环流进料至加氢处理反应器,
[0014]
相关的益处是提供具有高气体纯度的再循环配置。
[0015]
在另一个实施方案中,加氢处理单元还包括位于所述加氢处理反应器和所述第一冷却单元之间的加氢异构化段;并且被布置成接收来自所述加氢处理反应器的所述加氢处理的第一烃流,进行所述加氢处理的第一烃流的催化加氢异构化并向所述第一冷却单元提供脱蜡的第一烃流,相关的益处是提供具有良好冷流性质的脱蜡的烃流。
[0016]
在另一个实施方案中,加氢处理单元还包括位于所述加氢处理反应器和所述加氢异构化段之间的所述加氢处理的第一烃流中的第二加热或冷却单元,相关的益处是在所述加氢异构化段中提供最佳的条件。
[0017]
在加氢处理单元的另一个实施方案中,所述加氢处理单元被布置成提供来自所述低压闪蒸单元的脱气的富烃流的一部分作为烃产物流,相关的益处是从加氢处理单元提供商业产品。
[0018]
在加氢处理单元的另一个实施方案中,所述尾气包含h2、co2、c1和c3气态组分,相关的益处是排出一定量的co2、c1和c3而不是将其引导至加氢处理反应器。
[0019]
在进一步的实施方案中,加氢处理单元还包括h2补充进料,该h2补充进料被布置成与所述富h2流合并以提供处理气体,相关的益处是在处理气体中提供大量h2。
[0020]
在另一个实施方案中,加氢处理单元还包括被布置成压缩富h2流的第一压缩机,相关的益处是在与加氢处理单元中的压力匹配的高压条件下提供富h2流。
[0021]
在进一步的实施方案中,加氢处理单元被布置成将所述富h2流或所述处理气体与所述烃再循环流合并,以提供进料至加氢处理反应器的合并流,相关的益处是为加氢处理单元中的反应提供h2。
[0022]
在进一步的实施方案中,加氢处理单元被布置成将至少一定量的所述合并流与至少一部分含氧化合物原料合并,然后进料至加氢处理反应器,相关的益处是为加氢处理单元中的反应提供h2,以及通过在反应器中的中间点处添加一定量的冷却的合并流来分步控制反应器温度。
[0023]
另一方面涉及包括加氢处理单元和分离单元的柴油设备,所述柴油设备被布置成使得将所述脱气的富烃流的至少一部分从所述加氢处理单元进料至所述分离单元并纯化,以提供烃产品,例如柴油产品、喷气燃料或石油化学工厂的原料。
[0024]
另一方面涉及使用加氢处理单元对含氧化合物原料进行加氢处理的方法,包括以下步骤:
[0025]
i.将所述含氧化合物原料进料至加氢处理反应器;并将其转化为加氢处理的第一烃流;
[0026]
ii.将来自所述加氢处理反应器的所述加氢处理的第一烃流进料至所述第一冷却单元并将其冷却成冷却的第二烃流;
[0027]
iii.将来自所述第一冷却单元的冷却的第二烃流进料至所述高压分离器,并将其至少分离成富烃流和富氢流;
[0028]
iv.将来自所述高压分离器的富烃流进料至所述低压闪蒸单元,并将其脱气;从而提供尾气和脱气的富烃流,
[0029]
v.将来自高压分离器的富氢流的至少一部分进料至加氢处理反应器;
[0030]
vi.将来自低压闪蒸单元的脱气的富烃流分离成烃产物流和烃再循环流;和
[0031]
vii.将所述烃再循环流进料至加氢处理反应器。
[0032]
在该方法的另一个实施方案中,低压闪蒸单元在环境压力至30barg(优选环境压力至15barg)的压力下操作,相关的益处是从脱气的富烃流中分离出包含h2以外的其他气体以及中等量的h2的尾气。
[0033]
在该方法的另一个实施方案中,高压分离器在20-100barg(优选30-80barg)的压力下操作,相关的益处是从富烃流中分离出包含中等量的氢气以外的其他气体的富氢流,例如80vol%或更多的h2。
[0034]
在另一个实施方案中,该方法还包括对来自所述加氢处理反应器的加氢处理的第一烃流进行催化加氢异构化,并向所述第一冷却单元提供将脱蜡的第一烃流的步骤,相关的益处是在硫的存在下在硫化贱金属催化剂上进行加氢异构化。
[0035]
在该方法的另一实施方案中,将来自高压分离器的富氢流在另一冷的高压分离器中进一步冷却和分离,然后引导至加氢处理反应器;相关的益处是,富氢流包含比富烃流更少量的氢气以外的其他气体,例如80vol%或更多的h2。冷的高压分离器的液体可以在低压分离器中进一步分离,并可作为烃再循环流被引导至加氢处理反应器或被引导至分馏器以分离成产物。
[0036]
图例
[0037]
图1显示了仅具有高压分离器的单元的简化示图。
[0038]
图2显示了具有高压分离器和低压闪蒸单元的单元的简化示图。
[0039]
发明详述
[0040]
在下文中,缩写%vol将用于表示气体的体积百分比。
[0041]
提供了一种用于含氧化合物原料的加氢处理单元。术语“加氢处理单元”包括各种反应器、分离器或其他处理单元,根据需要由各种进料供应并根据需要通过管道、阀门、连接器等连接,从而提供合适的产物流。加氢处理单元通常是可再生燃料设备(例如可再生柴油设备)中的一个单元。
[0042]
含氧化合物原料可以包含一种或多种选自甘油三酯、脂肪酸、树脂酸、酮、醛或醇的含氧化合物,其中所述含氧化合物源自生物来源、气化过程、热解过程、fischer-tropsch合成、基于甲醇的合成或进一步的合成过程。其中一些原料可能含有芳烃;特别是来自热解过程的产品或来自例如煎炸油的废品。优选地,含氧化合物原料是可再生的含氧化合物原料,例如从可再生来源的原材料中获得的那些,例如源自植物、藻类、动物、鱼类、植物油精炼、生活垃圾或工业有机废物(例如妥尔油或黑液)。
[0043]
加氢处理去除许多与可再生原料相关的杂质,例如含氧、含硫或含氮的杂质。此类杂质会影响后续过程,例如加氢异构化。
[0044]
加氢处理通常在负载型催化剂上进行,通常是负载在载体材料上的金属催化剂。催化剂通常包含活性金属(硫化贱金属,如镍、钴、钨和/或钼,但也可能是元素贵金属,如铂和/或钯)和耐火载体(如氧化铝、二氧化硅或二氧化钛,或其组合)。
[0045]
加氢处理单元包括:
[0046]-加氢处理反应器;
[0047]-第一冷却单元;
[0048]-高压分离器;和
[0049]-低压闪蒸单元。
[0050]
加氢处理反应器是加氢处理单元中进行加氢处理步骤的部分。因此,其被布置成接收含氧化合物原料并将其转化为加氢处理的第一烃流。加氢处理反应器包括一个或多个反应器容器,每个反应器容器包含1个或多个上述负载型催化剂的催化剂床(通常为3-4个催化剂床)。加氢处理反应器需要氢气进料,如本文所述,其可以至少部分地由富h2流提供。
[0051]
加氢处理条件通常涉及250-400℃区间的温度、30-150barg区间的压力和0.1-2区间的液时空速(lhsv)。加氢处理通常是放热的,并且在大量含氧化合物的存在下,该过程可能涉及中间冷却,例如通过用冷的氢气、进料、烃再循环或产品进行骤冷。原料可优选地含有一定量的硫以确保金属的硫化,从而保持它们的活性。如果原料包含少于10、50或100ppmw的硫,则可以向进料中添加硫化物供体,例如二甲基二硫化物(dmds)。
[0052]
对于含氧化合物的加氢处理,所需的氢气量很高,因为原料中的氧的量可能高于5wt%或10wt%,对于来自例如来自例如热解过程的特定原料甚至高达40wt%。这要求富h2处理气体和含氧化合物进料流之间的比率非常高,例如200nm3/m3、500nm3/m3或甚至1000nm3/m3以上。加氢处理中具有重要化学意义的压力是氢分压,这实际上意味着降低气相纯度将需要增加气相压力。对于如此高的气流,增加气相压力的成本自然很重要。
[0053]
第一冷却单元被布置成接收来自加氢处理反应器的加氢处理的第一烃流并将其冷却成冷却的第二烃流。冷却单元中的冷却可以通过与加氢处理单元中的一种或多种其它流进行热交换来进行。冷却单元中的冷却也可以通过公用设施流(例如冷却水或制冷剂)或空气进行。
[0054]
高压分离器被布置成接收来自第一冷却单元的冷却的第二烃流并将其至少分离成富烃流和富氢流。
[0055]
高压分离器是将第二烃流分离成气态流、液态烃流和任选的水流的容器。该容器可配备有有助于相分离的装置,例如挡板、除雾器或填料。
[0056]
低压闪蒸单元被布置成接收来自所述高压分离器单元的富烃流并在低于高压分离器的压力下将其脱气;从而提供尾气和脱气的富烃流。低压闪蒸单元可配备有有助于相分离的装置,例如挡板、除雾器或填料。
[0057]
加氢处理单元被适当地布置以提供来自低压闪蒸单元的脱气的富烃流的一部分作为烃产物流。
[0058]
低压闪蒸单元在环境压力至30barg(优选环境压力至15barg)的压力下操作。该闪蒸单元的压力选择将因地而异,并取决于闪蒸尾气被送到哪里。如果被送到火炬系统,则只需要低压(约0.3barg)。如果作为燃料气体输送,则3-5barg的压力将是合适的。如果被送至h2回收,则25-30barg的压力将是合适的。
[0059]
来自(热的)高压分离器的富氢气体流可以在另一冷的高压分离器中进一步冷却和分离,然后被引导至加氢处理反应器以进一步纯化。
[0060]
冷的高压分离器的液体可以在低压闪蒸单元中进一步分离并且可以作为烃再循环流被引导至加氢处理反应器或被引导至分馏器以分离成产物。
[0061]
通常,热的高压分离器中的温度将在200℃至300℃的范围内,并且如果存在的话,冷的高压分离器将在100℃以下运行。
[0062]
来自该闪蒸单元的尾气通常包含h2、co、co2、c1和c3气态组分。尾气中也可能存在一定量的c2和c4 轻质烃。
[0063]
来自高压分离器和低压闪蒸单元的各种流被再循环到加氢处理单元的更上游位置。这有助于控制加氢处理反应器中的温度。
[0064]
因此,加氢处理单元被布置成将来自高压分离器的富氢流的至少一部分进料至加氢处理反应器。任选地,将来自高压分离器的全部富氢流进料至加氢处理反应器。
[0065]
如附图中所示,优选如下布置:将h2补充进料与富h2流合并以提供处理气体。然后将处理气体进料至加氢处理反应器。
[0066]
此外,加氢处理单元可以被布置成将来自低压闪蒸单元的脱气的富烃流的一部分作为烃再循环流进料至加氢处理反应器。值得注意的是,仅将该流的一部分再循环,而将其余部分作为来自该单元的烃产物流提供。
[0067]
在将该富h2流和烃再循环流“进料至加氢处理反应器”中,这意味着将它们进料至加氢处理反应器的入口侧。可以将富h2流和烃再循环流单独进料至加氢处理反应器,即不与其他气体流混合。然而,将富h2流和烃再循环流彼此混合并且与其他气体流或液体流混合然后进料至加氢处理反应器可能是有利的。可以将再循环流送到加氢处理反应器中的中间点,例如催化剂床之间,或送到不同的反应器容器。
[0068]
当烃再循环被加热时,h2的存在通常对于防止焦炭的形成是有利的。因此,在一方面,加氢处理单元被布置成将所述富h2流或所述处理气体与所述烃再循环流合并以提供进料至加氢处理反应器的合并流。
[0069]
因此,各种流(富h2流;处理气体和烃再循环流)可以单独进料至加氢处理反应器,即不与其他流合并。或者,加氢处理单元被适当地布置成将富h2流或处理气体与所述烃再循环流合并以提供进料至加氢处理反应器的合并流。
[0070]
加氢处理单元可以被布置成将任何流(富h2流;处理气体和烃再循环流)或合并流与含氧化合物原料合并,然后进料至加氢处理反应器。
[0071]
加氢处理单元优选包括加氢异构化段。加氢异构化段可以作为单独的反应器位于加氢处理反应器和所述第一冷却单元之间。或者,加氢异构化段可以是加氢处理反应器内的附加段(其中加氢异构化催化剂位于加氢处理催化剂的下游)。
[0072]
加氢异构化段被布置成接收来自所述加氢处理反应器的所述加氢处理的第一烃流,进行所述流的催化加氢异构化并向所述冷却单元提供脱蜡的第一烃流。加氢异构化段包含加氢异构化催化剂,其通常包含活性金属(元素贵金属,例如铂和/或钯;或硫化贱金属,例如镍、钴、钨和/或钼)、酸性载体(通常为具有高形状选择性的分子筛,并具有拓扑结构,例如mor、fer、mre、mww、ael、ton和mtt)和典型的无定形耐火载体(例如氧化铝、二氧化硅或二氧化钛,或其组合)。催化活性材料可以包含其他组分,例如硼或磷。
[0073]
加氢异构化条件通常涉及250-350℃区间的温度、20-100barg区间的压力和0.5-8区间的液时空速(lhsv)。
[0074]
第二加热或冷却单元可以位于加氢处理反应器和加氢异构化反应器之间的加氢处理的第一烃流中。
[0075]
在低压闪蒸单元中进行低压脱气之后,可能必须升高各种流的压力,然后再循环到加氢处理反应器。例如,加氢处理单元还可以包括被布置成压缩富h2流的第一压缩机。图2显示了位于h2补充进料上游的第一压缩机。还可以布置第二泵以压缩进料至加氢处理反应器的合并流。
[0076]
在第二方面,提供了一种可再生柴油设备,其包括本文所述的加氢处理单元和分离单元。柴油设备被布置成使得将所述脱气的富烃流的至少一部分从加氢处理单元(更准确地,从低压闪蒸单元)的进料至分离单元并纯化,以提供至少柴油产品。分离单元还提供轻质产品。
[0077]
上面列出的加氢处理单元的所有细节经适当修改后适用于本发明的可再生柴油设备。
[0078]
在第三方面,提供了一种使用本文所述的加氢处理单元对含氧化合物原料进行加氢处理的方法。该方法包括以下一般步骤:
[0079]
i.将所述含氧化合物原料进料至加氢处理反应器;并将其转化为加氢处理的第一烃流;
[0080]
ii.将来自所述加氢处理反应器的所述加氢处理的第一烃流进料至所述冷却单元并将其冷却成冷却的第二烃流;
[0081]
iii.将来自所述冷却单元的冷却的第二烃流进料至所述高压分离器,并将其至少分离成富烃流和富氢流;
[0082]
iv.将来自所述高压分离器的富烃流进料至所述低压闪蒸单元,并将其脱气;从而提供尾气和脱气的富烃流,
[0083]
v.将来自高压分离器的富氢流的至少一部分作为富h2流进料至加氢处理反应器;
[0084]
vi.将来自低压闪蒸单元的脱气的富烃流分离成烃产物流和烃再循环流;和
[0085]
vii.将所述烃再循环流进料至加氢处理反应器。
[0086]
上面列出的加氢处理单元的所有细节经适当修改后适用于本发明的方法。
[0087]
特别地,低压闪蒸单元可以在环境压力至30barg(优选环境压力至15barg)的压力下操作。类似地,高压分离器可以在20-100barg(优选30-80barg)的压力下操作。
[0088]
该方法还可以包括对来自所述加氢处理反应器的加氢处理的第一烃流进行催化加氢异构化,并向冷却单元提供脱蜡的第一烃流的步骤。合适的加氢异构化催化剂和条件如上所述。
[0089]
附图详述
[0090]
图1显示了含氧化合物烃原料11。该流被送到进料缓冲罐v1,然后通过泵p1进料至高压系统。将原料与加热的烃再循环流和富氢再循环气体流(55)合并,然后送到加氢处理反应器(20)。该第一反应器含有对加氢处理有活性的催化剂,并且该催化剂催化烃原料中存在的氧转化为水、co2和co,以及其他反应,如烯烃饱和为链烷烃、氮转化为氨以及硫转化为硫化氢。加氢处理的产物流(21)任选地通过热交换器(39)加热或冷却,然后送到加氢异构化反应器(70)。该第二反应器含有对加氢异构化有活性的催化剂,并且该催化剂将具有高倾点的直链烷烃转化为具有较低倾点的支链异链烷烃,从而改善流的冷流性质。加氢异构化产物(23)通过在冷却单元(30)中与其他工艺流、冷却水和/或环境空气进行热交换而冷却,并且冷却的流(31)被送到高压分离器(40)。该分离器将加氢处理和加氢异构化的产物分成富氢气体流(42)、富烃液体流(52)和任选的富水液体流(未显示)。将富氢流送到再循环气体压缩机(60),将再压缩的气体流与氢气补充气体(12)合并为处理气体(43),然后与再循环烃流(54)合并。富烃液体流(52)通过泵p2,然后被分成液体再循环烃流(54)和烃产物流(53)。将液体再循环烃流(54)与处理气体(43)合并,并在热交换器e1中加热,以在加
氢处理反应器(20)中达到合适的反应温度。将烃产物流(53)送到分离单元(90),在那里通过除去轻质组分(92)如石脑油、lpg和燃料气而使主要的液体产物柴油(94)稳定。
[0091]
图2显示了含氧化合物烃原料11。该流被送到进料缓冲罐v1,然后通过泵p1进料至高压系统。将原料与加热的烃再循环流和富氢再循环气体流(55)合并,然后送到加氢处理反应器(20)。该第一反应器含有对加氢处理有活性的催化剂,并且该催化剂催化烃原料中存在的氧转化为水、co2和co,以及其他反应,如烯烃饱和为链烷烃、氮转化为氨以及硫转化为硫化氢。加氢处理的产物流(21)任选地通过热交换(39)加热或冷却,然后送到加氢异构化反应器(70)。该第二反应器含有对加氢异构化有活性的催化剂,并且该催化剂将具有高倾点的直链烷烃转化为具有较低倾点的支链异链烷烃,从而改善流的冷流性质。加氢异构化产物(23)通过在冷却单元(30)中与其他工艺流、冷却水和/或环境空气进行热交换而冷却,并且冷却的流(31)被送到高压分离器(40)。该分离器将加氢处理和加氢异构化的产物分成富氢气体流(42)、富烃液体流(41)和任选的富水液体流(未显示)。将富氢流送到再循环气体压缩机(60),将再压缩的气体流与氢气补充气体(12)合并为处理气体(43),然后与液体再循环烃流(54)合并。将富烃液体流(41)通过阀门减压并送到低压闪蒸罐(50)。通过降低压力,一定量的轻质组分作为蒸气尾气流(56)从液体流中释放出来。剩余的液体流(脱气的富烃流52)现在含有较少量的轻质组分。它通过泵p2,并被分成液体再循环烃流(54)和烃产物流(53)。将液体再循环烃流(54)与处理气体(43)合并,并在热交换器e1中加热,以在加氢处理反应器(20)中达到合适的反应温度。将烃产物流(53)送到分离塔(90),在那里通过除去轻质组分(92)如石脑油、lpg和燃料气而使主要的液体产物柴油(94)稳定。
实施例1
[0092]
基于以下计算了各种流中的气体组成:
[0093]
1.仅hp分离器,仅在915psig下(按照图1)(仅hp),和
[0094]
2.相同的hp分离器,然后是在150psig下的lp分离器(闪蒸罐)(如图2所示)(hp lp分离):
[0095][0096]
[0097]
来自hp分离器的富h2流(42)
[0098]
处理气体(43)(即与补充进料12混合的富h2流42)。
[0099]
如果目标是使氢气分压为50bar,则在h2补充进料和富h2流的混合点,两种情况下的系统压力将为:
[0100]
仅hp:50bar/0.7835=63.8bar
[0101]
hp lp分离:50bar/0.8605=58.1bar
[0102]
因此,看到设计压力降低了10%,相当于节省了大约10%的材料和成本。
[0103]
尽管已经参考多个方面、实施例和实施方案描述了本发明,但是这些方面、实施例和实施方案可以由本领域技术人员组合,同时保持在本发明的范围内。
再多了解一些
本文用于企业家、创业者技术爱好者查询,结果仅供参考。