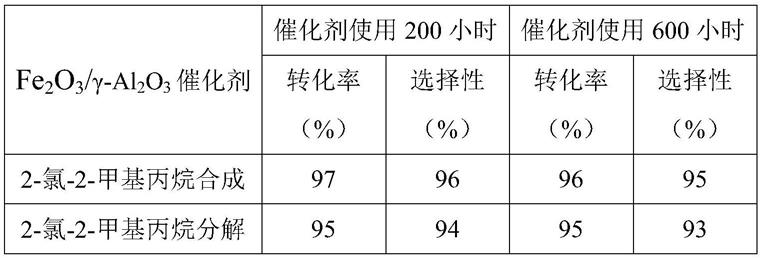
1.本发明属于工业废气处理领域,具体而言,涉及一种用于分离回收在氯代烯烃生产过程中产生的氯化氢气体的方法。该方法工艺简单,显著降低盐酸排放,提高氯资源使用率,极大地缓解了氯化氢存储、运输对设备的要求,同时更为安全、环保。
背景技术:
2.低碳(c
2-c6)烯烃和氯气反应是制备氯乙烯、氯丙烯等有机氯高分子单体化学品的典型合成方法,其中反应副产物之一为氯化氢气体,并与未反应的烯烃以混合气体的形式排出。目前,国内很多企业采用水洗工艺吸收烯烃气体中的氯化氢,以得到纯净的烯烃气体并加以利用。但是,水洗形成的盐酸不但附加值低、处理成本较高,并有产生二次污染物的弊端,同时氯化氢溶液(盐酸)因氯化氢在水中的解离很难再实现回收利用,造成氯资源大量浪费,产生较大的环境保护负担,严重制约了企业的发展。
3.特别是由于氯化氢为气体,具有强刺激性,吸水后有强烈的腐蚀性,需要包装于高压专用钢瓶中,处于液态。专用钢瓶为钢质无缝气瓶,瓶内需抛光处理,瓶阀为抗腐蚀不锈钢隔膜阀,钢瓶设计压力为12.5mpa,工作压力约5-6mpa,属于三类高压压力容器,并且运输和贮存过程必须符合《气瓶安全监督规程》、《气瓶安全监督规定》、《危险货物运输规则》等有关规定,同时运输装卸要求也较高。因工艺、安全、环保等要求,很多企业需要将氯化氢气体转运、储存至其它场所,较高的设备投入及存储、运输过程中的泄露等隐患都增加了企业的负担。因此,迫切需要开发从烯烃氯代反应混合尾气中实现氯化氢气体分离的技术,并降低氯化氢气体存储、运输的设备投入,消除氯化氢气体在存储、运输过程存在的泄露、腐蚀等安全隐患。
4.按照分子中质量占比计算,氯代烷烃中氯化氢含量高,是非常理想的氯化氢存储载体。例如,一分子的2-氯丙烷中氯化氢的质量占比高达46.4%,同时2-氯丙烷为液体,沸点36℃,无腐蚀性,易于储存、运输。氯化氢和低碳烯烃反应制备氯代烷烃,达到氯化氢气体从烯烃氯代反应混合气中分离的目的,又将氯化氢气体变为液体形式,实现氯化氢的高密度储存,液态氯代烷烃化合物无腐蚀性,非常便于储存,便于运输,可以节约庞大的气体存储、运输投入,能极大减少氯化氢气体储存、运输过程中的泄露等安全风险。另外,相比盐酸中氯化氢难以回收利用,氯代烷烃可以根据需要在其它时段或场所经分解后释放出氯化氢气体,非常方便的实现氯化氢气体的释放,分离后的氯化氢气体即可以作为原料直接使用,也可以经氧气氧化生成氯气,并与分离后的烯烃反应实现整个生产过程的原料循环,大大降低企业的废盐酸排放量,提高氯资源利用率,显著改善企业的经济效益、安全性和工艺的灵活性。
技术实现要素:
5.针对氯化氢气体从烯烃氯代反应混合气中分离困难,且存储、运输过程中存在的设备投入大、易泄露等问题,本发明的一个目的在于提供了一种用于分离回收氯代烯烃生
产中产生的氯化氢气体,并实现氯化氢安全储存、运输的方法。基于fe2o3负载于γ-al2o3的催化剂,在室温-120℃下可以实现低碳烯烃与氯化氢催化反应制备得到氯代烷烃,实现氯化氢从气体到液态氯代烷烃的存储,同时,在200-500℃条件下,氯代烷烃在该催化剂作用下也可以逆向分解产生低碳烯烃和氯化氢,实现氯化氢气体从液态氯代烯烃的释放。该催化剂具备氯代烷烃合成及分解的双重催化功能,达到氯化氢气体分离、存储、释放的目的,达到减少排放、节约资源的目的。
6.为了实现本发明的上述目的,所述用于分离、运输并回收在氯代烯烃生产中产生的氯化氢气体的方法包括以下步骤:
7.1)向含有催化剂的反应器1中通入烯烃氯化反应后的混合尾气,反应器出口连接冷阱收集氯代烷烃,剩余未反应烯烃回收利用,其中反应温度为50至120℃。
8.2)将步骤1)得到反应产物经少量固体碱处理后装入储罐,所述储罐为二类低压压力容器,容积:1.0-10.0m3,设计压力为≤1.0mpa,工作压力约0.1-0.5mpa,所述储罐也可用于铁路或公路运输的储罐。
9.3)向含有催化剂的反应器2中不经任何处理直接通入步骤2)中所述储罐中储存的氯代烷烃,反应器出口连接冷阱收集烯烃液体,反应器2的气体出口连接鼓泡吸收器吸收氯化氢气体,实现氯化氢的分离,其中反应温度为200至500℃。
10.优选地,步骤1)中所述混合尾气中烯烃与所述有氯化氢气体的体积比为2:1至100:1,更优选为4.5:1;并且所述混合尾气含有总体积比小于等于2%的c
2-c6的烷烃、c
2-c6烯烃、c
4-c
12
二烯烃及c
2-c6炔烃等杂质。
11.优选地,步骤1)中所述氯代烷烃包括氯代乙烷、1-氯代丙烷、2-氯代丙烷、2-氯-2-甲基丙烷,1,2-二氯代丙烷,1-氯代丁烷、2-氯代丁烷、3-氯代丁烷、1-氯代戊烷、2-氯代戊烷、3-氯代戊烷、1-氯代己烷、2-氯代己烷、3-氯代己烷、氯代环己烷。
12.优选地,步骤1)中所述催化剂为fe2o3负载于γ-al2o3载体上的负载型催化剂。
13.优选地,步骤2)中所述储罐可以为玻璃钢罐、pe塑料罐、聚四氟乙烯塑料罐或普通304不锈钢罐。
14.优选地,步骤2)中所述催化剂与步骤1)中的相同,为fe2o3负载于γ-al2o3载体上的负载型催化剂。
15.优选地,步骤1)和步骤2)中所述催化剂为fe2o3负载于γ-al2o3的催化剂,其中为fe2o3活性成分,γ-al2o3为载体,基于所述催化剂的总重量,其中fe2o3含量为0.1%至20%,所述γ-al2o3载体含量为80%至99.9%,所述γ-al2o3载体为球型颗粒,粒径为3-5.0mm,所述催化剂的比表面积为289.9至6.694m2/g,孔体积为0.49至0.008723ml/g。
16.所述催化剂按照如下方法制备:
17.1)取γ-al2o3载体颗粒于120℃干燥10小时,并自然冷却干燥备用;
18.2)取fe盐溶于超纯水中形成fe盐溶液,用量筒称取一定体积的γ-al2o3球型颗粒加入所述fe盐溶液并搅拌均匀,放置过夜;
19.3)将步骤1)中浸渍后的γ-al2o3球型颗粒过滤,然后120℃处理5小时,随后在500℃马弗炉氮气氛下煅烧5小时,冷却至室温后取出,得到所述fe2o3负载于γ-al2o3的催化剂产品。
20.优选地,所述fe盐选自硝酸铁和氯化铁。
qp2010及aoc-20i auto自动进样器测量;hplc通过使用waters 1525的2489uv-vis检测器和2707自动进样器测量;1h nmr通过使用bruker avance-iii 600mhz测量。纯度以gc的面积%计算。
31.在根据本公开的负载型催化剂中,以γ-al2o3为载体,其上沉积了fe2o3,所述载体起到支撑和分散所述双金属合金催化剂的作用,从而增加其表面积,通过防止烧结现象来稳定所述催化剂,并降低所述催化剂的价格。所述载体本身可能不具有活性,但是由于具有上述功能而影响催化剂的活性,即使使用相同的组合物,取决于金属催化剂负载的程度,催化剂活性的差异变大,因此,需要将所述载体的选择认为是非常重要的。
32.以下实施例仅是作为本发明的实施方案的例子列举,并不对本发明构成任何限制,本领域技术人员可以理解在不偏离本发明的实质和构思的范围内的修改均落入本发明的保护范围。除非特别说明,以下实施例中使用的试剂和仪器均为市售可得产品。
33.实施例1:
34.1)用量筒称取50ml的fe2o3负载于γ-al2o3载体上的负载型催化剂球型颗粒(φ:3-5.0mm,比表面积:13.697m2/g,孔体积:0.013ml/g),装填入内径3.0cm,长度40.0cm的石英反应器中。以200ml/min流量的n2吹扫5小时,后升温至110℃,氯代环己烯反应后尾气以100.0ml/min流量进入,其中氯化氢气体与环己烯占比≥98%,氯化氢气体与环己烯气体的体积比为1:4,并含有总体积比小于等于2%的烃类杂质,反应器出口连接截留罐(100℃)收集氯代环己烷,剩余未反应环己烯气体经低温冷却(0℃)为液体后导入不锈钢储罐备用。氯化氢的转化率98%,氯代环己烷收率97%。
35.2)将步骤1)得到的产物经简单的氢氧化钠固体碱处理后,注入不锈钢储罐(二类低压压力容器,304材质,容积:2000l,直径:1200mm,高度:2600mm,设计压力为≤1.0mpa,工作压力约0.1-0.3mpa)中备用。
36.3)用量筒称取10ml步骤1)中所述催化剂,装填入内径2.0cm,长度30.0cm的石英管反应器中。以100ml/min流量的n2吹扫5小时,后升温至250℃。以步骤2)储罐中的氯代环己烷为原料,不经任何处理直接使用,氯代环己烷进料速度0.1ml/min,经预热汽化(160℃)后以气体形式进入催化剂床层,反应器出口连接冷阱(-0℃)收集环己烯液体,气体出口连接鼓泡吸收器吸收氯化氢备定量滴定用。氯代环己烷的转化率97%,氯化氢收率96%。
37.实施例2:
38.1)取fe(no3)3.9h2o:22.7g溶于30ml超纯水中,用量筒称取100mlγ-al2o3球型颗粒(φ:3-5.0mm)加入并搅拌均匀,放置过夜,放入120℃烘箱处理5小时,后在500℃马弗炉煅烧5小时,冷却至室温后取出备用。所得fe2o3负载于γ-al2o3的催化剂比表面积:278.7m2/g,孔体积:0.48ml/g。
39.2)用量筒称取50ml步骤1)中制备的fe2o3负载于γ-al2o3的颗粒催化剂,装填入内径3.0cm,长度40.0cm的石英管反应器中。以200ml/min流量的n2吹扫5小时,后升温至60℃,切换气体为氯代丙烯反应后尾气混合气,其中氯化氢气体与烯烃气体占比≥98%,氯化氢气体与丙烯气体的体积比为1:4.3,并含有体积比≤2%的c
2-c6的烷烃、异构烯烃、二烯烃及炔类杂质,以500ml/min的流量进入催化剂床层,反应器出口连接玻璃冷阱(-10℃)收集2-氯丙烷,剩余未反应丙烯气体经气体压缩泵增压至2.0mpa,液化后导入储罐备用。氯化氢的转化率95%,2-氯丙烷收率93%。
40.3)将步骤1)得到的产物经简单的氢氧化钠固体碱处理后注入立式玻璃钢储罐(二类低压压力容器,玻璃钢材质,容积:2000l,直径:1000mm,直边高:2390mm,总高:2640mm,设计压力为≤1.0mpa,工作压力约0.3-0.5mpa)中备用。
41.4)用量筒称取10ml步骤1)中制备的fe2o3负载于γ-al2o3的颗粒催化剂,装填入内径2.0cm,长度30.0cm的石英管反应器中。以100ml/min流量的n2吹扫5小时,后升温至300℃。以步骤2)玻璃钢储罐中的2-氯丙烷为原料,不经任何处理直接使用,2-氯丙烷进料速度0.1ml/min,经预热汽化后(100℃)以气体形式进入催化剂床层,反应器出口连接玻璃冷阱(-60℃)收集丙烯液体,气体出口连接鼓泡吸收器吸收氯化氢备定量滴定用。2-氯丙烷的转化率99%,氯化氢收率97%。
42.实施例3:
43.1)用量筒称取50ml实施例2制备的fe2o3负载于γ-al2o3的颗粒催化剂,装填入内径3.0cm,长度40.0cm的石英管反应器中。以200ml/min流量的n2吹扫5小时,后升温至60℃,切换气体为包含质量含量为35%的氯化氢、65%的异丁烯混合气,以300ml/min的流量进入催化剂床层,反应器出口连接玻璃冷阱(0℃)收集2-氯-2-甲基丙烷,剩余未反应异丁烯气体经气体压缩泵增压至1.0mpa,液化后导入储罐备用。氯化氢的转化率98%,2-氯-2-甲基丙烷收率97%。
44.2)将步骤1)得到的产物直接关注入pe储罐(二类低压压力容器,聚乙烯材质,溶剂:1000l,直径:1200mm,直边高:950mm,总高度:1100mm,人孔:200mm,设计压力为≤1.0mpa,工作压力约0.1-0.3mpa)中备用。
45.3)用量筒称取10ml步骤1)中制备的fe2o3负载于γ-al2o3的颗粒催化剂,装填入在内径2.0cm,长度30.0cm的石英管反应器中。以100ml/min流量的n2吹扫5小时,后升温至300℃。以步骤2)pe储罐中的2-氯-2-甲基丙烷为原料,不经任何处理直接使用,2-氯-2-甲基丙烷进料速度0.2ml/min,经预热汽化后(100℃)以气体形式进入催化剂床层,反应器出口连接玻璃冷阱(-20℃)收集异丁烯液体,气体出口连接鼓泡吸收器吸收氯化氢备定量滴定用。2-氯-2-甲基丙烷的转化率95%,氯化氢收率94%。
46.实施例4:
47.1)按实施例3中步骤1)的条件进行反应,考察催化剂寿命及稳定性,结果如表1。
48.2)按实施例3中步骤2)的条件进行反应,考察催化剂寿命及稳定性,结果如表1。
49.表1
[0050][0051]
以上所述,仅为本发明的具体实施方式,但本发明的保护范围并不局限于此,任何熟悉本技术领域的技术人员在本发明揭露的技术范围内,可轻易想到变化或替换,都应涵盖在本发明的保护范围之内。因此,本发明的保护范围应所述以权利要求的保护范围为准。
再多了解一些
本文用于企业家、创业者技术爱好者查询,结果仅供参考。