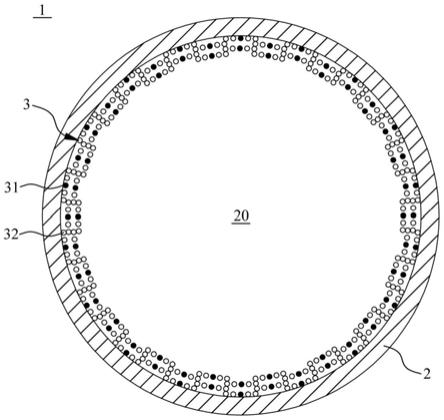
1.本发明关于一种热管及其制造方法,尤指一种可提供高散热功率的热管及其制造方法。
背景技术:
2.一般电子装置或机器设备于运转状态中产生高温,常见会利用热管来传热和排热,而热管运作原理利用内部工作流体的蒸发和凝结,来达成快速均温的效果。进一步说明,热管在高温端吸热后,内部工作流体蒸发而受蒸气压力的影响往低温区移动,在低温区中工作流体蒸气排热而凝结成液体之后,透过内部的毛细结构又回流至高温区,进行吸热而蒸发,以此不断地循环、排热。
3.然而,毛细结构的蓄水量、及排水能力是影响整个热管散热功率相当重要的因素。一般热管所采用常见的毛细结构包括沟槽式(groove)、网状与编织管(mesh heat pipe or fiber heat pipe)、以及粉末烧结式(sintered power),其中相较于沟槽式和粉末烧结式而言,编织管的蓄水力和排水力算的是相当优异的。但是,以网状与编织管作为毛细结构的技术发展至今,仍有存有许多缺陷和限制,仍为业界亟待改良的项目。
4.进一步说明,传统以金属网或编织网目作为毛细结构的制造方法请参见中国台湾发明专利公告第i295364号「金属网热管的烧结方法与装置」;该现有技术的制造方法简单说明如下:首先,将金属网植入铜管内;接着,将心棒插入该金属网,使金属网与铜管内壁紧贴;接着,加热该铜管与金属网,使金属网与铜管内壁烧结;最后,移除心棒。然而,此传统的烧结方式虽然能有效使金属网黏接并固定于铜管内壁,但烧结后金属网的空隙率将大打折扣,并显著影响金属网的蓄水力、及排水能力。
5.另一方面,现有技术中也发展出了以额外的支撑结构来撑开铜网,让铜网紧密贴合于金属管内壁的技术;请参见中国台湾专利公告第i558968号「一种热管」,其公开了利用位在金属网内的弹性件,该弹性件处于弹性压缩状态,故可向金属网施加径向向外的弹性力,使金属网紧密贴合于金属管的内壁。
6.然而,这一现有技术以螺旋弹簧作为弹性件,此举固然可以使金属网固定在金属管内,但仍然无法使金属网完整地贴附于金属管内壁,特别是没有接触到螺旋弹簧的地方,金属网有可能会隆起,此将显著影响了散热能力。而且,此配置的制造方法的工序复杂且良率不高,因为一般金属网的口径小,故要将螺旋弹簧穿过金属网恐非易事,且又要将螺旋弹簧均匀地撑开金属网更是难上加难。
技术实现要素:
7.本发明的主要目的在提供一种热管及其制造方法,俾能利用编织网目作为毛细结构,而无须额外支撑构件,亦非采用烧结固定,完全利用编织网目自身的撑张力,达成自支撑(self-supporting)效果,使毛细结构完整贴附于内管壁,且不论外管如何弯曲或变形,编织网目始终可完整且平顺地紧贴内管壁,维持优异的蓄水量和排水能力,进而显著地提
升散热功率。
8.为达成上述目的,本发明一种热管,其主要包括中空管体、毛细套管、以及工作流体;中空管体包括封闭腔室,毛细套管设置于封闭腔室内,且至少局部地环绕于中空管体的内壁面;工作流体则容设于封闭腔室内。其中,该毛细套管包括至少一个编织网目,其产生径向撑张力而自主地贴附于中空管体的内壁面。
9.承上所述,本发明的毛细套管采用编织网目,而编织网目本身因为具备大量的空隙,可容纳大量的凝结水,故传热、排热效率高,且可视实际需求弹性增减堆栈编织网目的数量,具有弹性设计上的优势。另外,本发明的编织网目自身具备径向回弹的特性,故方便穿入中空管体,具有制程工序上的便利性。此外,本发明的编织网目所产生的径向撑张力又可让编织网目完整地平贴接触于中空管体的内壁面,提供绝佳的热交换机制,故无需传统金属网式热管的烧结工序或添加额外的支撑结构,构成自支撑编织网目(self-supporting woven wire mesh)的毛细结构,不论中空管体如何弯折或变形,本发明自支撑编织网目始终紧紧贴附于内管壁,故可维持优异的蓄水和排水能力,特别适合于高功率的散热装置。
10.优选的是,本发明的至少一个编织网目可由至少一个第一金属线、及至少一个第二金属线编织而成,而至少一个第一金属线的径向弹性系数可大于至少一个第二金属线的径向弹性系数。换言之,径向弹性系数较大的第一金属线能提供较大的径向撑张力;另一方面,径向弹性系数较小的第二金属线则能提供较大的径向变形率。据此,本发明可借由搭配不同径向弹性系数的金属线,能让毛细套管同时兼具径向变形并回弹的特性、以及产生足够的径向撑张力。
11.再者,本发明的至少一个编织网目可由多个金属线束以平纹编织法或斜纹编织法编织而成,而每个金属线束可由至少一个第一金属线、及至少一个第二金属线所组成。亦即,每个金属线束中同时具备有第一金属线、及第二金属线,以此方式编织而成的编织网目可获得相当均匀的径向支撑力、以及径向变形率。
12.另一方面,本发明的至少一个编织网目亦可由多个经线束、及多个纬线束以平纹编织法或斜纹编织法编织而成,而多个经线束可由至少一个第一金属线所组成,且多个纬线束可由该至少一个第二金属线所组成。换言之,经线束可提供充分的径向支撑力,而纬线束则可提供适当的径向变形率;以此方编织而成的编织网目,同样可以获得相当均匀的径向支撑力、以及径向变形率,足以让毛细套管完整地贴附于中空管体的内壁面。
13.另外,本发明的毛细套管可包括第一编织网目、及第二编织网目,而第二编织网目可介于第一编织网目与中空管体的内壁面间;其中,第一编织网目可由至少一个第一金属线所组成,而第二编织网目可由至少一个第二金属线所组成。换言之,本发明的毛细套管可包括多层的编织网目,除了可倍增排水量之外,越接近内层的编织网目可由径向弹性系数较大的第一金属线编织而成,进而可提供充足的径向撑张力,来推抵较外层的编织网目,以确保所有的编织网目都能完整地平贴于中空套管的内壁面。
14.除此之外,毛细套管的编织网目亦可由多个金属线所编织而成;而于毛细套管的两侧端部处,彼此交迭的金属线可彼此接合。据此,于端部处彼此相邻且交迭的金属线,借由将其接合,则可大幅提升径向撑张力,且径向变形率、及轴向变形率亦可显著增加。又,本发明的至少一个编织网目的线径范围可介于0.02mm至0.2mm之间;而至少一个编织网目的空隙率可介于25%至75%之间。其中,编织网目的线径除了将影响变形量大小之外,也将影
响径向撑张力的大小;另外,编织网目的空隙率同样除了将影响变形量大小之外,也将影响排水量,亦即排热效率。
15.为达成上述目的,本发明一种热管的制造方法,包括以下步骤:首先,提供中空管体、及毛细套管;而毛细套管包括至少一个编织网目;接着,毛细套管穿入中空管体内,且毛细套管提供径向撑张力,而自主地贴附于中空管体的内壁面;最后,中空管体内部注入工作流体并脱气后,封闭中空管体而形成封闭腔室。
16.综上所述,本发明所提供的制造方法相当简便,其中较特殊之处仅将毛细套管穿入中空管体,并借助毛细套管自身的径向撑张力,让毛细套管可自主地固定于中空管体内部,且完整地接触并贴附中空管体内壁面。据此,本发明的创新制造方法相较于传统金属网式热管的制造方法,可省去烧结金属网的步骤,或安装额外支撑装置的步骤,制造效率可明显提升,而制造成本又可显著下降。
17.优选的是,毛细套管的原始管径可大于或等于中空管体的内径;且于上述穿入毛细套管的步骤中,可轴向拉伸毛细套管使其管径小于中空管体的内径,且于穿入中空管体后松开该毛细套管。换言之,可借助于毛细套管的弹性变形特性,先拉伸毛细套管使其管径缩小,以便于穿入中空管体,且穿入定位之后取消轴向拉伸的力,让毛细套管自然回弹扩张而顶抵中空管体的内壁,借此产生径向撑张力,使毛细套管紧紧地固定在中空管体的内壁上。
18.另一方面,在本发明所提供的热管制造方法中,毛细套管可包括第一编织网目、芯管、及第二编织网目,而第二编织网目可套设于芯管上,第一编织网目可容设于芯管内;且第一编织网目可由多个第一金属线所组成,第二编织网目可由多个第二金属线所组成。然而,于上述穿入毛细套管的步骤中,使第一编织网目、芯管、及第二编织网目穿入中空管体后移除芯管,而让第一编织网目、及第二编织网目脱离芯管,并固定于中空管体内;其中,第一编织网目脱离芯管后的径向扩张率(radial expansion ratio)超过110%。
19.也就是说,本发明所提供的制造方法中,毛细套管可采用多层编织网目,并利用芯管来固定该等编织网目,其可分设于芯管内、外;其中、芯管内部容设为,可提供较大径向撑张力的第一编织网目,而芯管外则套设第二编织网目。然而,于制造步骤中,将连同芯管的整个毛细套管穿入中空管体后,单单拉出芯管,而此时第一编织网目将因脱离芯管的束缚,自然回弹扩张并产生径向撑张力,而撑抵第二编织网于中空管体的内壁面上。
附图说明
20.图1a是本发明的热管的第一实施例的径向剖面示意图。
21.图1b是本发明第一实施例的编织网目的局部放大示意图。
22.图2是本发明第二实施例的编织网目的局部放大示意图。
23.图3是本发明第三实施例的编织网目的局部放大示意图。
24.图4a是本发明第四实施例的径向剖面示意图。
25.图4b是本发明第四实施例中另一型态的第一编织网目的放大示意图。
26.图5a、5b是分别显示本发明的制造方法中安装毛细套管过程中的中空套管的局部剖面示意图。
27.图6a、6b是分别显示本发明的另一制造方法中安装毛细套管的轴向剖面示意图。
具体实施方式
28.本发明的热管及其制造方法在本实施例中被详细描述之前,要特别注意的是,以下的说明中,类似的组件将以相同的附图标记来表示。再者,本发明的附图仅作为示意说明,其未必按比例绘制,且所有细节也未必全部呈现于附图中。
29.请先参阅图1a、及图1b,图1a是本发明的热管第一实施例的径向剖面示意图,图1b是本发明第一实施例的编织网目的局部放大示意图。如图中所示,本实施例的热管1主要包括中空管体2、毛细套管3、及工作流体(图中未示),中空管体2包括封闭腔室20,而毛细套管3设置于该封闭腔室20内,且环绕于中空管体2的整个内壁面,作为毛细结构以供冷凝后的工作流体回流;而工作流体同样容设于封闭腔室20内。
30.进一步说明,本实施例的毛细套管3由四层编织网目层迭组成,而每个编织网目由多个金属线束30以平纹编织法编织而成,且每个金属线束30包括一个第一金属线31、及四个第二金属线32并排所组成。此外,本实施例的第一金属线31和第二金属线32采用不同材质,而第一金属线31的径向弹性系数大于第二金属线32的径向弹性系数,且二者的径向弹性系数以超过1000kgf/mm2为宜。
31.进一步说明,径向弹性系数较大的第一金属线31能提供较大的径向撑张力,而径向弹性系数较小的第二金属线32则能提供较大的径向变形裕度,而且也具备较佳的热传导系数。在本实施例中,第一金属线31可选择硬钢线、钢琴线、或不锈钢线,线径范围介于0.02mm至0.2mm之间为宜;然而,本实施例主要采用线径0.1mm,在此线径条件下,硬钢线和钢琴线的径向弹性系数为8
×
103kgf/mm2,而sus631不锈钢线的径向弹性系数为7.5
×
103kgf/mm2。
32.另外,第二金属线32则可选择铍铜线、磷青铜线、洋白铜线、或黄铜线,其中于相同线径0.1mm的条件下,铍铜线的径向弹性系数为4.5
×
103kgf/mm2,磷青铜线的径向弹性系数为4.3
×
103kgf/mm2,洋白铜线、及黄铜线的径向弹性系数为4
×
103kgf/mm2。据此,本实施例借由搭配不同径向弹性系数的金属线,让毛细套管3同时兼具径向变形并回弹的特性、以及产生足够的径向撑张力,达成自支撑(self-supporting)的效果,更重要的是又可维持良好的热传能力、以及排水能力。
33.另一方面,为了顾及径向和轴向的变形量,每个编织网目的空隙率不宜太高,亦不宜太低,以介于25%至75%之间为佳,例如目数介于40目至200目之间即可;其中,若空隙率太高,排水效率受到影响,但若空隙率太低,编织网目则难以变形或恢复。此外,整体而言,本实施例的径向变形率可超过5%;也就是说,每个编织网目受到压缩或撑张时,径向截面积的变形裕度可超过
±
5%。
34.再者,又需要特别说明的是,如图1a所示,为了提高蓄水能力,层迭的网目彼此交错配置,即在金属线束的空隙之间配置下一层网目的金属线束。而且,更佳的是,不同层的编织网目可采用不同的编织方法,举例说明,第一层采用平纹编织法编织而成的编织网目,而第二层则采用斜纹编织法编织而成的编织网目,以此方式来层迭,可大幅缩小各层间的空隙的大小,进而大幅提升整个毛细套管3的蓄水、及排水效率。
35.接着请参阅图2,其是本发明第二实施例的编织网目的局部放大示意图。本实施例与前述第一实施例主要不同之处在于,编织网目的金属线束的组成不同。在本实施例中,如图中所示,编织网目由多个经线束301、及多个纬线束302以平纹编织法编织而成;其中,每
个经线束301由5个第一金属线31所组成,而每个纬线束302则同样由5条第二金属线32所组成。如同第一实施例,第一金属线31的径向弹性系数大于第二金属线32的径向弹性系数。据此,借由此配置,由第一金属线31构成的经线束301可提供充足的径向撑张力,由第二金属线32构成的纬线束302则可提供较大裕度的径向变形量。
36.又,请参阅图3,其是本发明第三实施例的编织网目的局部放大示意图。本实施例与前述实施例主要差异在于,本实施例的编织网目主要以多个金属线束30并利用平纹编织法编织而成,而每个金属线束30单纯以第二金属线32所组成。另外,在网目中间又穿插第一金属线31,亦即第一金属线31以径向环绕该中空管体2的内壁面的方式编入原本以第二金属线32所组成平纹编织网目。更简单地说,第一金属线31构成为类似环箍的构件,能够提供绝佳的径向撑张力,将整个毛细套管3紧紧地固定在中空管体的内壁面上,而且构成环箍的第一金属线31切割了平纹编织的每个中空网目,故又可进一步提升毛细套管3的排水能力。
37.请参阅图4a,其本发明第四实施例的径向剖面示意图。在本实施例中,同样采用多层的网目架构,其中包括一层第一编织网目33、及三层第二编织网目34,第一编织网目33由第一金属线31编织而成,第二编织网目34由第二金属线32编织而成;而且,三层的第二编织网目34层迭于第一编织网目33与中空管体2的内壁面间。据此,在本实施例中,越接近封闭腔室20轴心的第一编织网目33由径向弹性系数较大的第一金属线31编织而成,进而可提供充足的径向扩张的撑张力,来推抵较外层由第二金属线32编织而成的第二编织网目34,以确保所有的编织网目都能完整地平贴于中空套管2的内壁面上。
38.除此之外,请参阅图4b,其是本发明第四实施例中另一型态的第一编织网目的放大示意图。如图中所示,本实施例型态的第一编织网目33与前述由图4a所示的第一编织网目33主要差异在于,本实施型态的每一线束单元由单根金属线的方式来进行编织,且于第一编织网目33的端部处,本实施例特别将彼此相邻且彼此交迭的第一金属线31熔接成为接合点310。据此,透过此配置,第一金属线31所构成的编织网目的径向支撑力可提升超过1倍以上,又可减少第一金属线31的配置数量。不过需要特别陈明的是,本实施例型态的第一编织网目33并不以单根第一金属线31编织为限,亦可如同前述实施例以多个第一金属线31编织组成,以提供更佳的径向撑张力、及排水能力。此外,本发明亦可不局限于仅端部熔接,亦可于每个交迭编织的交点均透过熔接成为接合点,借此又可更大大地提升径向支撑力。
39.以下说明本发明的制造方法,请同时参阅图5a、5b,其是分别显示本发明的制造方法中安装毛细套管过程中的中空套管的局部剖面示意图。如图5a中所示,首先,提供中空管体2、及毛细套管3,毛细套管3可如前述实施例中任一者,而且毛细套管3的原始管径大于等于中空管体2的内径。接着,向毛细套管3的两端轴向施力拉伸,使毛细套管3的管径小于中空管体2的内径,且于穿入中空管体2并定位后,取消轴向施力而松开毛细套管3。
40.然而,因本实施例的毛细套管3具备径向压缩后回弹特性,故当取消轴向拉伸施力时,毛细套管将回弹至原始管径大小,且毛细套管3回弹后相较于拉伸状态的径向截面积的变形率可超过5%,优选是超过30%。此外,如前述实施例中所述,毛细套管3的原始管径大于中空管体2的内径,故当毛细套管3位在中空管体2内时,毛细套管3将产生径向撑张力,而紧紧地贴附于中空管体2的内壁面,即如图5b所示。
41.最后,对该中空管体2内部注入工作流体并脱气后,封闭该中空管体2两端而形成封闭腔室20;亦即,例如以加热或真空吸引或者是该等组合等的手段进行脱气后,再以铆
接、焊接、或扩散接合等手段封闭中空管体2两端的通孔而形成封闭腔室20,即完成本发明的热管装置。
42.承上所述,本发明所提供的热管制造方法相当简易,当然须搭配前述实施例中所提的毛细套管3,亦即借助于毛细套管3的弹性变形特性,先施力拉伸毛细套管3,使其管径缩小,以便于穿入中空管体2;接着,在穿入定位之后,随即取消拉伸的力,让毛细套管3自然回弹并扩张整体管径,借此一并产生径向撑张力,使毛细套管3紧紧地且完整地固定在中空管体的内壁上。
43.此外,本发明又提供另一制造方法,其特别适用于前述第四实施例的热管装置。进一步说明,请一并参阅图6a、及图6b,其是显示本发明的另一制造方法中安装毛细套管的轴向剖面示意图。此制造方法特别之处在于,预先准备好的毛细套管3包括第一编织网目33、芯管35、及第二编织网目34的三层结构,即径向弹性系数较小第二编织网目34套设于芯管35上,而径向弹性系数较大的第一编织网目33则预先容设于芯管35内。而且,整个毛细套管3的外径是小于中空管体2的内径,以便于穿入中空管体2。
44.然而,当欲将毛细套管3穿入中空管体2时,整个毛细套管3是包括第一编织网目33、芯管35、及第二编织网目34,以朝穿入方向di直接穿入中空管体2,如图6a所示。穿入定位之后,接着,先固定第一编织网目33、及第二编织网目34的一端,特别是穿入方向di的一端,并朝退出方向do直接拉出芯管35,让第一编织网目33解开芯管35的束缚,自动地撑开第二编织网目34,并产生径向撑张力而撑抵第二编织网34于中空管体2的内壁面上,如图6b所示。在本实施例中,第一编织网目33脱离芯管35后的径向扩张率(radial expansion ratio)超过110%,优选是超过130%;也就是说,第一编织网目33脱离芯管35的束缚后,相较于在芯管35内时,第一编织网目33的径向截面积膨胀了10%以上。
45.另外说明,上述制造方法虽然以芯管35内、外分别设置第一编织网目33、及第二编织网目34为例进行说明,不过本发明并不以此为限,亦可将第一编织网目33、及第二编织网目34都设在芯管35内。此外,此毛细套管3的配置同样也可以适用前述制造方法,也就是一边施力拉伸第一编织网目33、及第二编织网目34并脱离芯管35,且使二者的外径小于中空管体2的内径,并一边穿入中空管体2内。
46.上述实施例仅是为了方便说明而举例而已,本发明所主张的权利范围自应以权利要求范围所述为准,而非仅限于上述实施例。
47.附图标记说明
48.1:热管
49.2:中空管体
50.3:毛细套管
51.20:封闭腔室
52.30:金属线束
53.31:第一金属线
54.32:第二金属线
55.33:第一编织网目
56.34:第二编织网目
57.35:芯管
58.301:经线束
59.302:纬线束
60.310:接合点
61.di:穿入方向
62.do:退出方向。
再多了解一些
本文用于企业家、创业者技术爱好者查询,结果仅供参考。