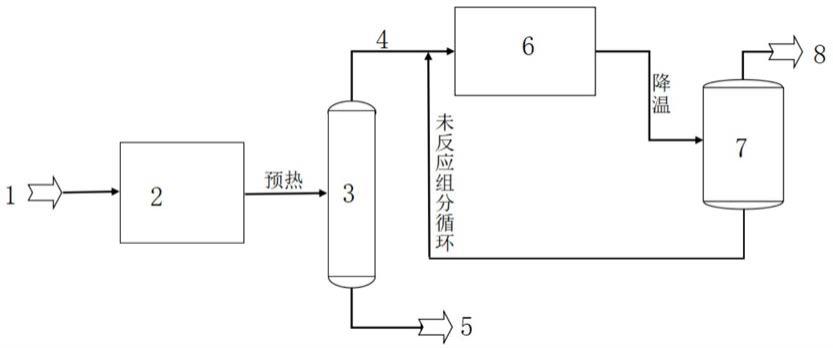
1.本发明属于原油催化裂化技术领域,具体涉及一种微波驱动原油催化裂解制 轻质烯烃的方法。
背景技术:
2.作为生产塑料、橡胶等高分子材料的关键组成单元,乙烯和丙烯等轻质烯烃 在石油化工行业中发挥着至关重要的作用。据权威报告预测,全球对乙烯和丙烯 等轻质烯烃需求在2030年之前仍将保持每年3%的速度快速增长。这种不断增长 的需求将促使生产商采用新技术来不断拓展轻质烯烃的原料范围,同时降低烯烃 的生产成本。目前,全球近50%的乙烯和丙烯仍采用石脑油在800~850℃的高温 下蒸气裂解生产的工艺,由于蒸汽裂解装置需要通过化石燃料燃烧来提供能量, 从而导致石脑油蒸气裂解工艺生产每吨乙烯、丙烯的co2排放量高达1.6~2吨。 此外,常规蒸汽裂解工艺的高温操作和裂解炉管积炭对裂化设备的建造及长周期 安全运行带来巨大挑战。
3.因此,为降低轻质烯烃的生产成本,以埃克森美孚为代表的多家跨国石化公 司正大力开发原油经过一次闪蒸后直接热裂解制烯烃的技术和装置。原油直接裂 解制烯烃技术拓宽了烯烃原料的来源同时缩短了工艺流程,相比于以石脑油和瓦 斯油为原料的传统蒸气热裂解工艺显示出巨大的经济潜力。
4.与此同时,在全球努力控制co2排放的大背景下,利用低碳的能源方式驱动原油裂解制 轻质烯烃对显著降低co2排放具有重要意义。微波可由电能以约90%的高效率产生,因此, 在风、光可再生电能资源储量丰富并且拥有巨量原油资源的区域(比如沙特阿拉伯),开发 以微波驱动的原油裂解制轻质烯烃技术对实现绿色高效可持续的轻质烯烃生产并助力碳中 和具有重要的价值。
技术实现要素:
5.本发明的目的是提供一种微波驱动原油催化裂解制轻质烯烃的方法,利用微 波作为能量源驱动原油催化裂化制轻质烯烃。
6.为实现上述目的,本发明采用的技术方案如下:一种微波驱动原油催化裂解 制轻质烯烃的方法,包括以下步骤:
7.原油原料首先进入脱水及金属离子单元,经脱水和脱金属离子后,预热进入 到原油闪蒸单元,控制进料温度为200~350℃,压力为70~150kpa;
8.在原油闪蒸单元中,原油被切割为重馏分和轻馏分,重馏分从闪蒸单元的底 部采出,轻馏分从闪蒸单元的顶部采出后进入微波催化裂化反应单元;
9.在微波催化裂化反应单元中,轻馏分蒸气与催化剂接触并在微波辐照下被加 热至100~350℃,进行催化裂化反应而生成c2
‑
c4轻质烯烃主产物,同时副产一 定量的h2、c1
‑
c4烷烃,经微波催化裂化反应后的混合气流进入产品粗分离及 未反应馏分循环单元;
10.在产品粗分离及未反应馏分循环单元中,混合气流被降温并实现初步分离, 其中
c2
‑
c4轻质烯烃和副产的h2、c1
‑
c4烷烃以气态形式从该单元采出并送至 后续的烯烃精制处理,未反应的组分以液态形式循环至微波催化裂化单元的入 口,并与闪蒸单元采出的轻馏分蒸气按一定的比例混合后进入微波催化裂化单元 进行反应,实现未反应组分的循环利用。
11.优选的,所述原油闪蒸单元的设备选用板式闪蒸塔,闪蒸塔的理论板数为 3~6块,等温闪蒸操作,操作压力为2~10kpa,操作温度为270~310℃。
12.优选的,所述微波催化裂化反应单元的设备选用立式固定床反应器,微波频 率为900mhz;或者所述微波催化裂化反应单元的设备选用立式流化床反应器, 微波频率为2.45ghz。
13.优选的,采用固定床反应器时,轻馏分蒸气从反应器的顶部进入而从上至下 流动,催化裂化反应的质量空速保持在0.4~2h
‑1之间,反应器内对应的微波辐照 强度控制在5~10000kw/m3,优选50~3000kw/m3。
14.优选的,采用流化床反应器时,轻馏分蒸气从反应器的底部进入而自下而上 流动,催化剂粉体从反应器顶部喷入而自上而下流动与轻馏分蒸气形成逆流流 动,轻馏分蒸气与催化剂粉体的质量流量之比控制在0.1~2之间,停留时间控制 在0.1~10s,且反应器内对应的微波辐照强度控制在50~20000kw/m3,优选 100~5000kw/m3。
15.优选的,微波催化裂化单元所采用的催化剂为活性炭、炭黑或负载型碳催化 剂,所述负载型碳催化剂的载体为zsm
‑
5分子筛、sic、zro2、al2o3、mgo、 cr2o3、v2o5及锰氧化物(mnox)中的一种或多种,负载型碳催化剂中碳的负 载量控制在0.5~2.5wt.%。
16.优选的,所述催化剂的粒径控制在320~50目。
17.优选的,所述产品粗分离及未转化馏分循环单元的设备选用闪蒸罐,在 10~40℃范围内的等温闪蒸,操作压力控制在50~500kpa。
18.与现有技术相比,本发明具有如下有益效果:
19.1.本发明利用微波作为能量源驱动沙特轻质原油在特殊催化材料上高选择 性裂解生成乙烯、丙烯等轻质烯烃,可实现c2
‑
c4轻质烯烃总选择性不低于71% 且轻质烯烃单程收率不低于31%的优良结果。
20.2.本发明相比于现有的石脑油蒸气裂解工艺,省去了原油蒸馏以获取石脑 油原料的步骤,可大幅缩短石油基轻质烯烃生产的工艺流程并降低设备投资。另 外在本发明中,原油中比石脑油馏分更重的组分也能够作为裂解制轻质烯烃的原 料,拓宽了轻质烯烃的原料来源,使得原油中更多的馏分能够高效高选择性转化 为相比于燃料具有更高价值的烯烃化学品,有助于提升原油的利用价值。
21.3.本发明利用微波驱动原油催化裂解制轻质烯烃的催化反应单元操作温度 在350℃以下即可实现,相比于石脑油蒸气热裂解过程的800~850℃高温有大幅 降低,过程温度的大幅降低有利于减少过程升降温而带来的大量能量损失,有利 于提升过程的能量效率。
22.4.本发明相比于现有技术最大的有益效果在于,可使轻质烯烃生产过程中 高耗能的传统加热裂解过程实现电力驱动。在当前可再生电能快速增长的机遇 下,以源自可再生电能的微波驱动轻质烯烃的生产过程,规避了传统加热裂解过 程通过化石燃料燃烧提供热量而大量排放co2的情形,因而极有利于实现碳中 和。
附图说明
23.图1是本发明微波驱动原油催化裂解制轻质烯烃的方法工艺流程图。
24.图2是固定床模式下微波驱动原油中各代表组分催化裂解气态产品组成及 对应的反应温度。
25.图3是固定床模式下微波驱动原油中各代表组分催化裂解产品的c2
‑
c4烯 烃及总轻质烯烃选择性。
26.图4是固定床模式下微波驱动原油中各代表组分催化裂解产品的c2
‑
c4烯 烃及总烯烃收率及各个组分的单程转化率。
27.图5是流化床模式下微波驱动原油中轻混合组分(石脑油)循环催化裂解气 态产品的组成及体积。
28.图6是流化床模式下微波驱动原油中轻混合组分(石脑油)循环催化裂解气 态产品的c2
‑
c4烯烃及总轻质烯烃选择性。
29.图7是流化床模式下微波驱动原油中常压沸点440℃之前馏分循环催化裂解 的气态产品组成及体积。
30.图8是流化床模式下微波驱动原油中常压沸点440℃之前馏分循环催化裂解 的气态产品中c2
‑
c4烯烃及总轻质烯烃选择性。
31.图1中,1.原油,2.脱水及金属离子单元,3.原油闪蒸单元,4.轻馏分, 5.重馏分,6.微波催化裂化反应单元,7.产品粗分离及未反应馏分循环单元, 8.c2
‑
c4轻质烯烃和副产的h2、c1
‑
c4烷烃。
具体实施方式
32.下面结合附图和具体实施例对本发明作进一步详细说明。
33.本发明提供一种微波驱动原油催化裂解制轻质烯烃的方法,如图1所示,包 括以下步骤:
34.原油1原料首先进入脱水及金属离子单元2,经脱水和脱金属离子后,预热 进入到原油闪蒸单元3,控制进料温度为200~350℃,压力为70~150kpa;
35.在原油闪蒸单元3中,原油1被切割为重馏分5、轻馏分4,重馏分5从闪 蒸单元的底部采出,轻馏分4从闪蒸单元的顶部采出后进入微波催化裂化反应单 元6;
36.在微波催化裂化反应单元6中,轻馏分蒸气与催化剂接触并在微波辐照下被 加热至100~350℃,进行催化裂化反应而生成c2
‑
c4轻质烯烃主产物,同时副产 一定量的h2、c1
‑
c4烷烃,经微波催化裂化反应后的混合气流进入产品粗分离 及未反应馏分循环单元7;
37.在产品粗分离及未反应馏分循环单元7中,混合气流被降温并实现初步分 离,其中c2
‑
c4轻质烯烃和副产的h2、c1
‑
c4烷烃8以气态形式从该单元采出 并送至后续的烯烃精制处理,未反应的组分以液态形式循环至微波催化裂化单元 6的入口,并与原油闪蒸单元3采出的轻馏分蒸气按一定的比例混合后进入微波 催化裂化单元6进行反应,实现未反应组分的循环利用。
38.实施例1
39.考虑到原油的复杂性,首先将原油划分为代表性组分如石脑油馏分 (naphtha)、c6
‑
c27的链烷烃而逐一进行微波驱动下的催化裂解评估,最后以沙 特轻质原油440℃之前
的馏分(crude oil)为原料模拟真实的原油催化裂解制轻 质烯烃。
40.本实施例中,原料在进入闪蒸单元之前压力控制在100kpa,预热温度为 250℃。
41.原油闪蒸单元的设备选用板式闪蒸塔,闪蒸塔的理论板数为5块,等温闪蒸 操作,操作压力控制在10kpa,操作温度为270℃;
42.微波催化裂化反应单元的设备选用立式固定床反应器,微波频率为 900mhz,微波辐照强度为1000kw/m3,催化剂为120目sic粉体负载2wt.%的 碳,轻馏分蒸气从反应器的顶部进入而从上至下流动,催化裂化反应的质量空速 保持在0.4h
‑1;
43.产品粗分离及未转化馏分循环单元的设备选用闪蒸罐,在30℃等温闪蒸, 操作压力控制在100kpa。
44.在间歇反应器中以0.5g催化剂在5min内催化裂化0.2g的各原油组分样品, 以此模拟固定床模式下的微波驱动原油催化裂解制烯烃过程,实施结果如图2
‑ꢀ
图4所示。
45.图2
‑
图4的结果说明,在合适的微波辐照和催化剂作用下,原油中各代表性 组分均可在60s内以低于350℃的温和条件高选择性地裂解为轻质烯烃。所有的 组分在微波下转化为轻质烯烃的选择性不低于71%,轻质烯烃单程收率不低于 31%。值得注意的是,对直链烷烃组分,轻质烯烃的选择性高达85%且对应的单 程收率可达到69%左右,体现了微波驱动的原油催化裂解制烯烃高效快速的优 势。
46.实施例2
47.以原油中代表性组分(石脑油,石脑油终馏点为205℃)为微波催化裂化反 应单元的进料模拟原油中的轻混合组分催化裂解制轻质烯烃。
48.本实施例中,原料在进入闪蒸单元之前压力控制在70kpa,预热温度为200℃。
49.原油闪蒸单元的设备选用板式闪蒸塔,闪蒸塔的理论板数为3块,等温闪蒸 操作,操作压力控制在50kpa,操作温度为220℃;
50.微波催化裂化反应单元的设备选用立式流化床反应器,微波频率为 2.45ghz,微波辐照强度为1500kw/m3,催化剂为120目sic粉体负载2wt.%的 碳;轻馏分蒸气从反应器的底部进入而自下而上流动,催化剂粉体从反应器顶部 喷入而自上而下流动与轻馏分蒸气形成逆流流动,轻馏分蒸气与催化剂粉体的质 量流量之比控制在0.4。
51.产品粗分离及未转化馏分循环单元的设备选用闪蒸罐,在20℃等温闪蒸, 操作压力控制在200kpa。
52.以0.2g混合组分样品将0.5g催化剂样品浸润,且该混合体系置于一端封口 且内径为8mm的石英反应管底部,石英管开口一端连接集气装置供收集裂解气 体产物使用,通过体积计量和色谱分析可以确定气体产物的量和组成。通过控制 石英管中催化剂装填区通过微波辐照区域的速度来控制停留时间(即反应时间) 为10s,从而达到模拟流化床操作模式的目的,实施结果如图5
‑
图6所示。
53.从图5
‑
图6的结果可知,催化材料可很好地维持催化性能,其中c2
‑
c4的 烯烃总选择性维持在71%以上,结合物料衡算数据计算得到轻质烯烃的总收率在 催化剂经过6次循环使用仍能保持在57%附近。
54.实施例3
55.以沙特轻质原油中常压沸点在440℃之前的所有馏分作为微波催化裂化反 应单元的进料来模拟真实全混合馏分原油催化裂解制轻质烯烃的过程。
56.本实施例中,原料在进入闪蒸单元之前压力控制在130kpa,预热温度为 300℃。
57.原油闪蒸单元的设备选用板式闪蒸塔,闪蒸塔的理论板数为5块,等温闪蒸 操作,操作压力控制在3kpa,操作温度为300℃;
58.微波催化裂化反应单元的设备选用立式流化床反应器,微波频率为 2.45ghz,微波辐照强度为3000kw/m3,催化剂为300目mnox粉体负载0.5wt.% 的碳;轻馏分蒸气从反应器的底部进入而自下而上流动,催化剂粉体从反应器顶 部喷入而自上而下流动与轻馏分蒸气形成逆流流动,轻馏分蒸气与催化剂粉体的 质量流量之比控制在0.8。
59.产品粗分离及未转化馏分循环单元的设备选用闪蒸罐,在30℃等温闪蒸, 操作压力控制在50kpa。
60.以0.4g混合组分样品将0.5g催化剂样品浸润,且该混合体系置于一端封口 且内径为8mm的石英反应管底部,石英管开口一端连接集气装置供收集裂解气 体产物使用,通过体积计量和色谱分析可以确定气体产物的量和组成。通过控制 石英管中催化剂装填区通过微波辐照区域的速度来控制停留时间5s,模拟实现 了流化床操作模式,实施结果如图7
‑
图8所示。
61.从图7
‑
图8的结果可知,催化材料可很好地维持催化性能,其中c2
‑
c4的 烯烃总选择性维持在76%以上,结合物料衡算数据计算得到轻质烯烃的单程总收 率在催化剂经过5次循环使用仍能保持在40.6%及以上。
再多了解一些
本文用于企业家、创业者技术爱好者查询,结果仅供参考。