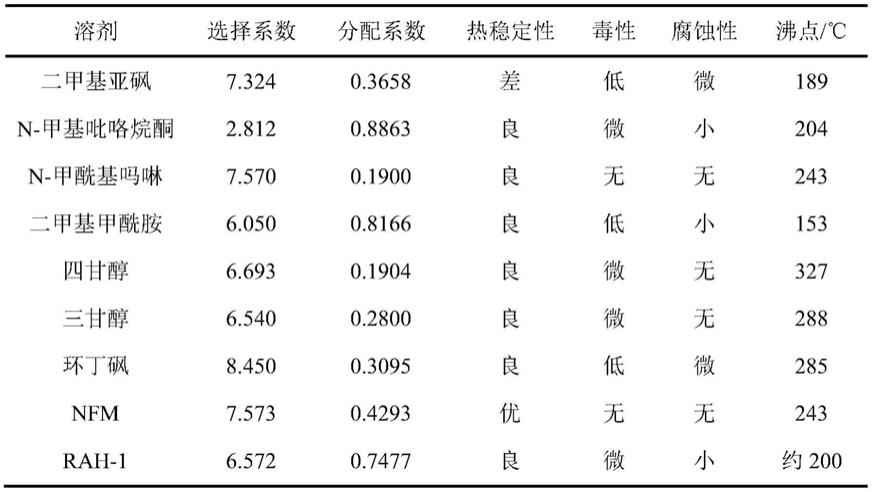
一种用离子液体的催化柴油稠环芳烃多级逆流
‑
错流组合抽提装置及方法
技术领域
1.本发明涉及一种用离子液体的催化柴油稠环芳烃多级逆流
‑
错流组合抽提装置及方法。离子液体萃取剂可以是单一离子液体、混合离子液体、离子液体与传统有机溶剂的混合物或功能型离子液体;属于化工分离纯化技术领域。
背景技术:
2.在发展低碳循环经济、实现环境可持续发展的大趋势下,柴油品质升级步伐明显加快,尤其是对十六烷值和多环芳烃指标的限制将会越来越严格。我国原油大部分较重,缺少生产芳烃和烯烃轻质原料。催化裂化是重油轻质化的重要手段,具有原料适应性强、转化率高、成本低等优势,在石油炼制过程中占据举足轻重的地位。该工艺技术的特点是对进料中的链烷烃和环烷烃进行裂解,对芳烃基本不具备破环能力。因此,在催化柴油中通常富集了大量稠环芳烃,当原料中渣油比例大时这一缺点则更为突出。目前,受环保要求的限制和市场需求的推动,国内fcc柴油加氢改质的技术得到快速的发展,但是加氢改质工艺的操作费用高、操作条件苛刻,导致柴油的生产成本大幅攀升。溶剂抽提技术可以有效分离非芳烃与芳烃,该工艺过程可应用于炼油厂各种物流:汽油、煤油、柴油和重质馏分。目前,世界范围内已经有多种溶剂应用于芳烃抽提工业化装置,常见的有三甘醇、四甘醇、环丁砜、二甲基亚砜、n
‑
甲基吡咯烷酮、n
‑
甲酰基吗啉等(常见抽提溶剂如表1所示)。但是,这些溶剂不适用于催化柴油芳烃抽提,因为它们的沸点处于催化柴油的馏程范围(180
‑
350℃)之内,不能采用常规的蒸馏方法回收而导致其循环使用困难;另一方面,用于润滑油抽提的糠醛、n,n
‑
二甲基甲酰胺(dmf)等溶剂的沸点虽然不处于催化柴油的馏程范围之内,但是因其与催化柴油中的许多组分形成共沸物,亦不能采用常规的蒸馏方法回收溶剂。用离子液体取代难以循环回收利用的常规溶剂作为催化柴油稠环芳烃抽提的新型分离剂,创造性地提出了功能型离子液体稠环芳烃抽提新技术,拓宽了离子液体在化工分离中的应用范围,强化稠环芳烃抽提过程。因此,如何经济、高效的处理催化劣质柴油,提高十六烷值,降低多环芳烃含量已成为建设有催化装置企业面临的一项重要技术攻关。
3.中国专利cn102021024a公开了一种制备高质量柴油的系统及其方法,该系统包括抽提装置,通过溶剂抽提脱除柴油中的一部分芳烃,抽余油经过加氢处理得到高质量柴油,抽提出的芳烃出系统。该发明处理的原料多样化,可以是各种柴油,将芳烃从柴油中分离出来,大大提高了柴油的十六烷值,降低了柴油凝点。
4.中国专利cn102443436a公开了一种渣油加氢处理、催化裂化与柴油芳烃抽提组合方法。在此方法中,渣油在氢气和加氢催化剂存在下进行加氢处理,流出物分离得到气相和液相产物,液相产物不经分馏直接进入催化裂化装置进行反应,反应流出物分离得到干气、液化气、催化裂化汽油、催柴及重馏分油,催柴经过芳烃抽提,抽出油与催化裂化重馏分油经过过滤后循环至加氢处理装置,抽余油出装置得高十六烷值柴油。此方法中,加氢裂化反应流出物不经分馏直接进催化裂化装置反应,无疑增大了催化裂化装置的负荷,影响了装
置的处理能力;其次加氢裂化反应流出物中含有一定量轻组分,这部分轻组分进入催化裂化装置后会发生二次反应,致使轻质馏分油减少,而气体产率增大,造成一定的经济损失。
5.表1常规萃取剂主要物性参数
[0006][0007]
本发明通过萃取剂多级逆流
‑
错流组合抽提方法,采用基于离子液体的萃取剂萃取剂,实现了催化柴油稠环芳烃混合物的高效分离,降低了装置能耗,同时减少了设备费用。
技术实现要素:
[0008]
本发明的目的是提供一种用离子液体的催化柴油稠环芳烃多级逆流
‑
错流组合抽提装置及方法。可降低溶剂比,同时克服溶剂与待分离混合物的混溶问题,能够提高柴油芳烃分离效率及提高十六烷值柴油产品的品质。
[0009]
本发明是通过下述技术方案实现的。
[0010]
一种用离子液体的催化柴油芳烃多级逆流
‑
错流组合抽提装置,其特征在于,装置主要包含以下部分:
[0011]
第一混合萃取塔(c1)、第二混合萃取塔(c2)、萃余液闪蒸罐(s1)、萃取液闪蒸罐(s2);
[0012]
其中待分离催化裂化柴油芳烃从塔的中下部进入第一混合萃取塔(c1),第一离子液体萃取剂(a1)从塔顶萃取剂进料口进入第一混合萃取塔(c1),第一混合萃取塔(c1)顶部流出物料与第二混合萃取塔(c2)的底部连接,第二离子液体萃取剂(a2)从塔顶萃取剂进料口进入第二混合萃取塔(c2);
[0013]
第二混合萃取塔(c2)塔顶流出物料连接萃余液闪蒸罐(s1)中部进行闪蒸分离;
[0014]
来自第一混合萃取塔(c1)和第二混合萃取塔(c2)塔底的采出物流均连接到萃取液闪蒸罐(s2)中部进行闪蒸分离;
[0015]
萃余液闪蒸罐(s1)和萃取液闪蒸罐(s2)底部萃取剂出口连接在第一混合萃取塔(c1) 萃取剂进料口上进行萃取剂循环;萃余液闪蒸罐(s1)顶部流出非芳烃成分(烷烃、烯
烃等),萃取液闪蒸罐(s2)顶部流出芳烃成分(包括稠环芳烃)。
[0016]
进一步根据需要萃取液闪蒸罐(s2)顶部流出芳烃成分(包括稠环芳烃)还设有部分回流管路与第一混合萃取塔(c1)的中下部连接,进行部分回流,形成多级逆流
‑
错流
‑
回流组合抽提装置。
[0017]
采用上述装置进行基于离子液体的溶剂多级逆流
‑
错流组合抽提分离催化柴油稠环芳烃的方法,主要包括以下步骤:
[0018]
(1)第一离子液体萃取剂从塔顶进入第一混合萃取塔(c1),待分离的催化柴油芳烃从第一混合萃取塔(c1)中下部进入第一混合萃取塔(c1),经过高效分离,第一混合萃取塔(c1)顶部采出液进入第二混合萃取塔(c2)底部,第一混合萃取塔(c1)底部富含离子液体的采出液进入萃取液闪蒸罐(s2)中部;
[0019]
(2)第二离子液体萃取剂从第二混合萃取塔(c2)塔顶进入第二混合萃取塔(c2),第二混合萃取塔(c2)底部采出液进入萃取液闪蒸罐(s2)中部,经过萃取液闪蒸罐(s2)高效分离,在萃取液闪蒸罐(s2)顶部获得芳烃(包括稠环芳烃),在萃取液闪蒸罐(s2)底部获得离子液体萃取剂;
[0020]
(3)第二混合萃取塔(c2)塔顶的采出物连接到萃余液闪蒸罐(s1)中部进行闪蒸分离,经过萃余液闪蒸罐(s1)高效分离,在萃余液闪蒸罐(s1)顶部获得非芳烃(烷烃、烯烃等),在萃余液闪蒸罐(s1)底部获得离子液体萃取剂;
[0021]
(4)萃余液闪蒸罐(s1)和萃取液闪蒸罐(s2)底部获得的离子液体萃取剂物流出口混合成一体然后分别与第一混合萃取塔(c1)和第二混合萃取塔(c2)的塔顶萃取剂进料口连接进行离子液体萃取剂循环利用。
[0022]
若萃取液闪蒸罐(s2)顶部流出芳烃成分(包括稠环芳烃)进行部分回流,则回流芳烃(包括稠环芳烃)与系统采出芳烃的质量比为0.1~9。
[0023]
根据本发明的另一优选实施方式,其特征在于所述第一混合萃取塔(c1)的操作压力为1~5atm,理论塔板数(n)为3~15块,优选5~10块,操作温度为20℃~100℃,催化柴油芳烃在第一混合萃取塔(c1)的进料位置为第(n
‑
1)~n块,萃取剂进料位置为第1~2 块,n为最后一块进料板;
[0024]
第二混合萃取塔(c2)的操作压力为1~5atm,理论塔板数(n)为3~15块,优选5~10 块,操作温度为20℃~100℃,第一混合萃取塔(c1)顶部采出液在塔底进入第二混合萃取塔(c2),进料位置为第(n
‑
1)~n块,萃取剂进料位置为第1~2块,n为最后一块进料板。
[0025]
根据本发明的另一优选实施方式,其特征在于所述萃余液闪蒸罐(s1)和萃取液闪蒸罐(s2)的操作压力为0.1~0.5atm,操作温度为50~150℃。
[0026]
根据本发明的另一优选实施方式,其特征在于所述催化芳烃混合物可以以任意比例混合。
[0027]
根据本发明的另一优选实施方式,其特征在于所述第一离子液体萃取剂和第二离子液体萃取剂相同,均为单一离子液体、混合离子液体或离子液体与传统有机溶剂的混合物。
[0028]
根据本发明的另一优选实施方式,其特征在于第一混合萃取塔(c1)和第二混合萃取塔(c2)每一混合塔离子液体与待分离柴油芳烃的体积之比为0.5~3:1。
[0029]
根据本发明的另一优选实施方式,其特征在于,当柴油芳烃中正十六烷与1
‑
甲基
萘的质量比例为(7~9):(1~3),分离后正十六烷的回收率为98.50%~99.99%,1
‑
甲基萘回收率为96%~99.9%。
[0030]
本发明与现有技术相比,主要有以下有益效果:
[0031]
(1)本发明工艺简单,操作方便,成功分离了催化柴油芳烃混合物,提高了柴油产品的十六烷值,降低了油品中多环芳烃含量。
[0032]
(2)该方法采用基于离子液体的萃取剂,强化了抽提工艺的分离效果,萃取剂回收过程简单,降低了工艺过程的能耗,进而降低了工艺过程成本。
附图说明
[0033]
图1为本发明一种用离子液体的催化柴油稠环芳烃多级逆流
‑
错流组合抽提的工艺装置流程图。
[0034]
图2为多级逆流
‑
错流
‑
回流组合抽提的工艺装置流程图。
[0035]
图中,c1
‑
混合萃取塔;c2
‑
混合萃取塔;s1
‑
萃余液闪蒸罐;s2
‑
萃取液闪蒸罐;f
‑ꢀ
待分离催化裂化柴油芳烃;a1
‑
第二离子液体萃取剂,a2
‑
第二离子液体萃取剂,l1
‑
第一混合萃取塔顶部采出液,l2
‑
第二混合萃取塔顶部采出液,r1
‑
第一混合萃取塔顶底部部采出液,r2
‑
第二混合萃取塔底部采出液,r3
‑
回流管,il1
‑
萃余液闪蒸罐底部获得离子液体萃取剂,il2
‑
萃取液闪蒸罐底部获得离子液体萃取剂。
具体实施方式
[0036]
下面结合实施例,进一步说明本发明,但本发明并不限于下述实施例,在不脱离前后所述宗旨的范围下,变化实施例都包含在本发明的技术范围内。
[0037]
以下实施例中混合萃取塔(c1)和混合萃取塔(c2)的操作条件均为常温常压。萃余液闪蒸罐(s1)和萃取液闪蒸罐(s2)的操作压力为0.5atm,温度为100℃。
[0038]
实施例1:
[0039]
采用普通离子液体(具体是[bmim][bf4])作为萃取剂。
[0040]
进料流量为100kg/h,进料中含正十六烷70%(质量分数)、1
‑
甲基萘30%(质量分数)。混合萃取塔(c1)的理论板数为6块,柴油芳烃混合物的进料位置为第6块,单一离子液体的进料位置为第1块,混合萃取塔(c1)塔顶采出液从塔底进入混合萃取塔(c2),单一离子液体从塔顶进入混合萃取塔(c2),混合萃取塔(c2)塔顶的采出物流连接到萃余液闪蒸罐(s1)中部进行闪蒸分离,来自混合萃取塔(c1)和混合萃取塔(c2)塔底采出液进入萃取液闪蒸罐(s2)中部进行闪蒸分离,每一级萃取过程中单一离子液体与柴油芳烃待分离物进料的体积比为1:1,经过多级分离后正十六烷的回收率为99.60%,1
‑
甲基萘的回收率为99.00%。萃取液中正十六烷的纯度为99.83%(质量分数),萃余液中1
‑
甲基萘的纯度为98.69%(质量分数)。
[0041]
实施例2:
[0042]
采用混合离子液体(具体是[bmim][bf4]和[emim][bf4],体积比为1:1)作为萃取剂。
[0043]
进料流量为100kg/h,进料中含正十六烷80%(质量分数)、1
‑
甲基萘20%(质量分数)。逆流混合萃取塔(c1)的理论板数为5块,柴油芳烃混合物的进料位置为第5块,混合离
子液体的进料位置为第2块,混合萃取塔(c1)塔顶采出液从塔底进入混合萃取塔(c2),混合离子液体从塔顶进入混合萃取塔(c2),混合萃取塔(c2)塔顶的采出物流连接到萃余液闪蒸罐(s1)中部进行闪蒸分离,来自混合萃取塔(c1)和混合萃取塔(c2)塔底采出液进入萃取液闪蒸罐(s2)中部进行闪蒸分离,每一级萃取过程中混合离子液体与柴油芳烃待分离物进料的体积比为1:1,经过多级分离后正十六烷的回收率为99.47%,1
‑
甲基萘的回收率为98.59%。萃取液中正十六烷的纯度为99.67%(质量分数),萃余液中1
‑
甲基萘的纯度为98.38%(质量分数)。
[0044]
实施例3:
[0045]
采用普通离子液体(具体是[bmim][bf4]) 有机溶剂(具体是环丁砜)的混合溶液(离子液体与有机溶剂的体积比为3:7)作为萃取剂。
[0046]
进料流量为100kg/h,进料中含正十六烷75%(质量分数)、1
‑
甲基萘25%(质量分数)。逆流混合萃取塔(c1)的理论板数为6块,柴油芳烃混合物的进料位置为第6块,混合萃取剂的进料位置为第1块,混合萃取塔(c1)塔顶采出液从塔底进入混合萃取塔(c2),混合萃取剂从塔顶进入混合萃取塔(c2),混合萃取塔(c2)塔顶的采出物流连接到萃余液闪蒸罐(s1)中部进行闪蒸分离,来自混合萃取塔(c1)和混合萃取塔(c2)塔底采出液进入萃取液闪蒸罐(s2)中部进行闪蒸分离,每一级萃取过程中混合萃取剂与柴油芳烃待分离物进料的体积比为1.5:1,经过多级分离后正十六烷的回收率为99.82%,1
‑
甲基萘的回收率为99.21%。萃取液中正十六烷的纯度为99.87%(质量分数),萃余液中1
‑
甲基萘的纯度为98.79%(质量分数)。
[0047]
实施例4:
[0048]
采用羟基功能化离子液体(具体是[hocmim][pf6])作为萃取剂。
[0049]
进料流量为100kg/h,进料中含正十六烷70%(质量分数)、1
‑
甲基萘30%(质量分数)。混合萃取塔(c1)的理论板数为6块,柴油芳烃混合物的进料位置为第6块,羟基功能化离子液体的进料位置为第1块,混合萃取塔(c1)塔顶采出液从塔底进入混合萃取塔(c2),羟基功能化离子液体从塔顶进入混合萃取塔(c2),混合萃取塔(c2)塔顶的采出物流连接到萃余液闪蒸罐(s1)中部进行闪蒸分离,来自混合萃取塔(c1)和混合萃取塔(c2)塔底采出液进入萃取液闪蒸罐(s2)中部进行闪蒸分离,每一级萃取过程中羟基功能化离子液体与柴油芳烃待分离物进料的体积比为1:1,经过多级分离后正十六烷的回收率为99.90%, 1
‑
甲基萘的回收率为99.60%。萃取液中正十六烷的纯度为99.85%(质量分数),萃余液中1
‑
甲基萘的纯度为99.7%(质量分数)。
[0050]
实施例5:
[0051]
采用氨基功能化离子液体(具体是[hnc2mim][pf6])作为萃取剂。
[0052]
进料流量为100kg/h,进料中含正十六烷70%(质量分数)、1
‑
甲基萘30%(质量分数)。混合萃取塔(c1)的理论板数为6块,柴油芳烃混合物的进料位置为第6块,氨基功能化离子液体的进料位置为第1块,混合萃取塔(c1)塔顶采出液从塔底进入混合萃取塔(c2),氨基功能化离子液体从塔顶进入混合萃取塔(c2),混合萃取塔(c2)塔顶的采出物流连接到萃余液闪蒸罐(s1)中部进行闪蒸分离,来自混合萃取塔(c1)和混合萃取塔(c2)塔底采出液进入萃取液闪蒸罐(s2)中部进行闪蒸分离,每一级萃取过程中氨基功能化离子液体与柴油芳烃待分离物进料的体积比为1:1,经过多级分离后正十六烷的回收率为99.90%, 1
‑
甲基萘
的回收率为99.55%。萃取液中正十六烷的纯度为99.86%(质量分数),萃余液中1
‑
甲基萘的纯度为99.65%(质量分数)。
[0053]
实施例6:
[0054]
采用芳基功能化离子液体(具体是[buphim][bf4])作为萃取剂。
[0055]
进料流量为100kg/h,进料中含正十六烷70%(质量分数)、1
‑
甲基萘30%(质量分数)。混合萃取塔(c1)的理论板数为6块,柴油芳烃混合物的进料位置为第6块,胆碱基功能化离子液体的进料位置为第1块,混合萃取塔(c1)塔顶采出液从塔底进入混合萃取塔 (c2),胆碱基功能化离子液体从塔顶进入混合萃取塔(c2),混合萃取塔(c2)塔顶的采出物流连接到萃余液闪蒸罐(s1)中部进行闪蒸分离,来自混合萃取塔(c1)和混合萃取塔(c2) 塔底采出液进入萃取液闪蒸罐(s2)中部进行闪蒸分离,每一级萃取过程中胆碱基功能化离子液体与柴油芳烃待分离物进料的体积比为1:1,经过多级分离后正十六烷的回收率为99.9%,1
‑
甲基萘的回收率为99.55%。萃取液中正十六烷的纯度为99.86%(质量分数),萃余液中1
‑
甲基萘的纯度为99.6%(质量分数)。
[0056]
实施例7:
[0057]
采用普通离子液体(具体是[bmim][bf4])作为萃取剂,并带有回流。
[0058]
进料流量为100kg/h,进料中含正十六烷70%(质量分数)、1
‑
甲基萘30%(质量分数)。混合萃取塔(c1)的理论板数为6块,柴油芳烃混合物的进料位置为第3块,单一离子液体的进料位置为第1块,混合萃取塔(c1)塔顶采出液从塔底进入混合萃取塔(c2),单一离子液体从塔顶进入混合萃取塔(c2),混合萃取塔(c2)塔顶的采出物流连接到萃余液闪蒸罐(s1)中部进行闪蒸分离,来自混合萃取塔(c1)和混合萃取塔(c2)塔底采出液进入萃取液闪蒸罐(s2)中部进行闪蒸分离,每一级萃取过程中单一离子液体与柴油芳烃待分离物进料的体积比为1:1,萃取液闪蒸罐(s2)顶部采出液中回流芳烃(包括稠环芳烃) 与采出系统芳烃的质量比为0.45,回流位置为第5块,经过多级分离后正十六烷的回收率为99.72%,1
‑
甲基萘的回收率为99.21%。萃取液中正十六烷的纯度为99.83%(质量分数),萃余液中1
‑
甲基萘的纯度为98.70%(质量分数)。
[0059]
实施例8:
[0060]
采用混合离子液体(具体是[bmim][bf4]和[emim][bf4],体积比为1:1)作为萃取剂,并带有回流。
[0061]
进料流量为100kg/h,进料中含正十六烷80%(质量分数)、1
‑
甲基萘20%(质量分数)。逆流混合萃取塔(c1)的理论板数为5块,柴油芳烃混合物的进料位置为第3块,混合离子液体的进料位置为第2块,混合萃取塔(c1)塔顶采出液从塔底进入混合萃取塔(c2),混合离子液体从塔顶进入混合萃取塔(c2),混合萃取塔(c2)塔顶的采出物流连接到萃余液闪蒸罐(s1)中部进行闪蒸分离,来自混合萃取塔(c1)和混合萃取塔(c2)塔底采出液进入萃取液闪蒸罐(s2)中部进行闪蒸分离,每一级萃取过程中离子液体与柴油芳烃待分离物进料的体积比为1:1,萃取液闪蒸罐(s2)顶部采出液中回流芳烃(包括稠环芳烃) 与采出系统芳烃的质量比为0.25,回流位置为第4块,经过多级分离后正十六烷的回收率为99.8%,1
‑
甲基萘的回收率为99.0%。萃取液中正十六烷的纯度为99.85%(质量分数),萃余液中1
‑
甲基萘的纯度为98.70%(质量分数)。
[0062]
实施例9:
[0063]
采用普通离子液体(具体是[bmim][bf4]) 有机溶剂(具体是环丁砜)的混合溶液(离子液体与有机溶剂的体积比为3:7)作为萃取剂,并带有回流。
[0064]
进料流量为100kg/h,进料中含正十六烷75%(质量分数)、1
‑
甲基萘25%(质量分数)。逆流混合萃取塔(c1)的理论板数为6块,柴油芳烃混合物的进料位置为第3块,混合萃取剂的进料位置为第1块,混合萃取塔(c1)塔顶采出液从塔底进入混合萃取塔(c2),混合萃取剂从塔顶进入混合萃取塔(c2),混合萃取塔(c2)塔顶的采出物流连接到萃余液闪蒸罐(s1)中部进行闪蒸分离,来自混合萃取塔(c1)和混合萃取塔(c2)塔底采出液进入萃取液闪蒸罐(s2)中部进行闪蒸分离,每一级萃取过程中混合萃取剂与柴油芳烃待分离物进料的体积比为1.5:1,萃取液闪蒸罐(s2)顶部采出液中回流芳烃与采出系统芳烃的质量比为0.55,回流位置为第5块,经过多级分离后正十六烷的回收率为99.86%,1
‑ꢀ
甲基萘的回收率为99.25%。萃取液中正十六烷的纯度为99.85%(质量分数),萃余液中1
‑
甲基萘的纯度为98.95%(质量分数)。
[0065]
实施例10:
[0066]
采用羟基功能化离子液体(具体是[hocmim][pf6])作为萃取剂,并带有回流。
[0067]
进料流量为100kg/h,进料中含正十六烷70%(质量分数)、1
‑
甲基萘30%(质量分数)。混合萃取塔(c1)的理论板数为6块,柴油芳烃混合物的进料位置为第3块,羟基功能化离子液体的进料位置为第1块,混合萃取塔(c1)塔顶采出液从塔底进入混合萃取塔(c2),羟基功能化离子液体从塔顶进入混合萃取塔(c2),混合萃取塔(c2)塔顶的采出物流连接到萃余液闪蒸罐(s1)中部进行闪蒸分离,来自混合萃取塔(c1)和混合萃取塔(c2)塔底采出液进入萃取液闪蒸罐(s2)中部进行闪蒸分离,每一级萃取过程中羟基功能化离子液体与柴油芳烃待分离物进料的体积比为1:1,萃取液闪蒸罐(s2)顶部采出液中回流芳烃 (包括稠环芳烃)与采出系统芳烃的质量比为0.45,回流位置为第5块,经过多级分离后正十六烷的回收率为99.9%,1
‑
甲基萘的回收率为99.65%。萃取液中正十六烷的纯度为99.9%(质量分数),萃余液中1
‑
甲基萘的纯度为99.55%(质量分数)。
[0068]
实施例11:
[0069]
采用氨基功能化离子液体(具体是[hnc2mim][pf6])作为萃取剂,并带有回流。
[0070]
进料流量为100kg/h,进料中含正十六烷70%(质量分数)、1
‑
甲基萘30%(质量分数)。混合萃取塔(c1)的理论板数为6块,柴油芳烃混合物的进料位置为第3块,氨基功能化离子液体的进料位置为第1块,混合萃取塔(c1)塔顶采出液从塔底进入混合萃取塔(c2),氨基功能化离子液体从塔顶进入混合萃取塔(c2),混合萃取塔(c2)塔顶的采出物流连接到萃余液闪蒸罐(s1)中部进行闪蒸分离,来自混合萃取塔(c1)和混合萃取塔(c2)塔底采出液进入萃取液闪蒸罐(s2)中部进行闪蒸分离,每一级萃取过程中氨基功能化离子液体与柴油芳烃待分离物进料的体积比为1:1,萃取液闪蒸罐(s2)顶部采出液中回流芳烃与采出系统芳烃的质量比为0.45,回流位置为第5块,经过多级分离后正十六烷的回收率为99.9%,1
‑
甲基萘的回收率为99.55%。萃取液中正十六烷的纯度为99.85%(质量分数),萃余液中1
‑
甲基萘的纯度为99.4%(质量分数)。
[0071]
实施例12:
[0072]
采用芳基功能化离子液体(具体是[buphim][bf4])作为萃取剂,并带有回流。
[0073]
进料流量为100kg/h,进料中含正十六烷70%(质量分数)、1
‑
甲基萘30%(质量分
数)。混合萃取塔(c1)的理论板数为6块,柴油芳烃混合物的进料位置为第3块,胆碱基功能化离子液体的进料位置为第1块,混合萃取塔(c1)塔顶采出液从塔底进入混合萃取塔 (c2),胆碱基功能化离子液体从塔顶进入混合萃取塔(c2),混合萃取塔(c2)塔顶的采出物流连接到萃余液闪蒸罐(s1)中部进行闪蒸分离,来自混合萃取塔(c1)和混合萃取塔(c2) 塔底采出液进入萃取液闪蒸罐(s2)中部进行闪蒸分离,每一级萃取过程中胆碱基功能化离子液体与柴油芳烃待分离物进料的体积比为1:1,萃取液闪蒸罐(s2)顶部采出液中回流芳烃与采出系统芳烃的质量比为0.45,回流位置为第5块,经过多级分离后正十六烷的回收率为99.9%,1
‑
甲基萘的回收率为99.45%。萃取液中正十六烷的纯度为99.9% (质量分数),萃余液中1
‑
甲基萘的纯度为99.5%(质量分数)。
[0074]
从上述数据可以看出,利用本发明分离后的产品纯度高,回收率高,大大提高了柴油产品的十六烷值。得到的高纯度芳烃可以用于下游生产。
再多了解一些
本文用于企业家、创业者技术爱好者查询,结果仅供参考。