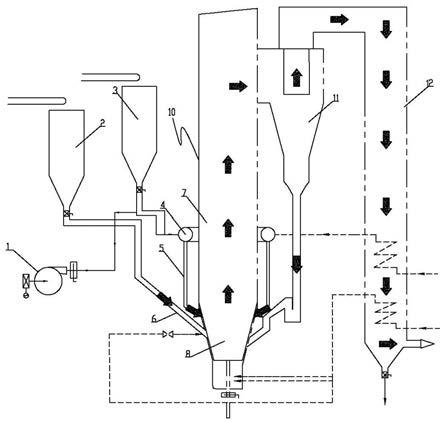
1.本发明属于循环流化床锅炉脱硫系统领域,具体涉及一种循环流化床锅炉炉内喷钙深度脱硫系统和工艺。
背景技术:
2.随着国家对污染物排放的要求日益严格,电站锅炉和工业锅炉对清洁能源技术的需求也逐步增加,循环流化床燃烧技术作为一种先进的低品位燃料清洁高效燃烧利用技术,受到了越来越多的关注,并在近年来得到了迅猛发展。
3.锅炉脱硫系统是循环流化床锅炉中重要的组成部分,其属于锅炉环保专业的一部分,脱硫的主要作用是将锅炉燃烧后产生的含so2浓度较高的烟气通过炉内吸收反应后变成较低的含so2烟气排出锅炉,达到脱硫的目的。循环流化床烟气脱硫的主要化学反应如下:cao+so2+2h2o
→
caso3·
2h2ocaso3·
2h2o+1/2o2→
caso4·
2h2o(石膏)由于循环流化床锅炉在燃烧产物中,会产生so2含量较大的烟气,烟气排入大气中形成污染,对环境和生态造成较大的危害。早期的炉内喷钙技术,为了及时有效的将锅炉燃烧烟气中的so2含量降低,在每台锅炉下部都配置了若干加炉内石灰石的接口。常用的脱硫剂有:石灰石( caco
3 )、石灰( cao)、白云石( caco
3 · mgco
3 )和含有一定量cao 或ca( oh )2的油页岩。从经济角度来说,大都采用石灰石作脱硫剂。 当采用白云石或含有少量mgco3的石灰石作脱硫剂时,其中mgco
3 在炉膛内煅烧成的mgo量很少,通常可不予考虑。石灰石加入炉膛内后,首先进行煅烧分解反应:caco3→ꢀ
cao co
2 ‑ꢀ
1781 .5 kj/ k g。经试验证明:炉膛燃烧温度为850℃左右时,可获得最大的脱硫效率。随着国家推行严格的环保要求,循环流化床锅炉都在采用全新的设计理念,以保证锅炉原始的氮氧化物排放达到国家管控要求。在这种新型循环流化床锅炉的运行中,在锅炉no
x
原始排放得到了极大地改善,同时锅炉炉膛内的燃烧温度也得到了相应的降低,运行时炉膛温度约在850℃~880℃,此温度场也正是炉内喷钙脱硫的最佳反应温度。但由于以往的炉内喷钙工艺及石灰石颗粒度不能满足高效脱硫的要求,使得即使钙硫比大于3,脱硫效率也仅有60%左右,会造成烟气中so2含量不能满足国家环保要求的排放数据。所以目前为确保so2达到国家要求的排放标准内,往往都采尾部炉外采用大湿法脱硫。但大湿法脱硫存在种种弊端已日益显现,如:初始投资大,运行费用高,耗水量大,占地面积大等,后期因为还会产生污水等造成二次污染,炉内高效喷钙脱硫的技术显得尤为重要。
技术实现要素:
4.为了解决现有炉内脱硫效率低,为满足低硫环保要求而导致投资运行成本高,容易造成二次污染的问题,本发明提供了一种循环流化床锅炉炉内喷钙深度脱硫系统及工艺,其能够满足锅炉烟低硫的环保要求,同时可节省用户炉后脱硫的投资运行成本及解决
二次污染的问题。
5.其技术方案是这样的:一种循环流化床锅炉炉内喷钙深度脱硫系统,其包括炉膛,所述炉膛通过给煤管和给煤机连接煤仓,所述煤仓内放置有煤和石灰石颗粒,所述煤和所述石灰石颗粒进入所述炉膛的下部密相区,所述炉膛连接分离器的进口,所述分离器的烟气出口连接尾部烟道、灰渣出口通过返料管连接炉膛,其特征在于,其还包括石灰粉仓,所述石灰粉仓内放置有1
‑
80um的石灰石粉,所述石灰粉仓的出料口连接二次风箱,所述石灰石粉通过连接所述二次风箱的二次风管进入所述炉膛的上部稀相区。
6.其进一步特征在于,所述二次风箱连接气力输送风机;所述炉膛的前后墙分别间隔布置至少两个所述二次风管。
7.一种循环流化床锅炉炉内喷钙深度脱硫工艺,其特征在于,将粒度为0.1mm~1.5mm的石灰石颗粒掺入煤中混合进入炉膛的下部密相区,石灰石颗粒进入炉膛后在下部密相区与大颗粒的床料、循环物料混合反应脱硫,去除密相区so2;将1
‑
80um的石灰石粉经过二次风箱,随二次风进入炉膛的上部稀相区,炉膛温度在850℃
‑
880℃,石灰石粉在炉膛停留时间大于3秒,炉膛内总体钙硫比控制在2.8
‑
3.2,满足石灰石进行完全脱硫反应。
8.采用本发明后,在给煤中掺入 0.1mm~1.5mm 粒度的石灰石颗粒,同时维持1
‑
80um的石灰石粉输送进入二次风,严格控制石灰石粉粒度,总体钙硫比约为3,脱硫效率大幅提高,最高可以达到97%以上,相较于传统仅有60%左的右脱硫效率,脱硫效果优异,对于硫份在1%以内的煤种可直接达到超低排放标准,工艺过程简单,节省材料,较炉后湿法脱硫的工艺,省去了庞大复杂的湿法脱硫设备,节省了用户炉后脱硫的投资运行成本及解决二次污染的问题。
附图说明
9.图1为本发明系统原理图;图2为二次风管布置示意图。
具体实施方式
10.见图1,图2所示,一种循环流化床锅炉炉内喷钙深度脱硫系统,其包括炉膛10,炉膛10通过给煤管6和给煤机9连接煤仓2,煤仓2内放置有煤和石灰石颗粒,煤和石灰石颗粒进入炉膛10的下部密相区8,炉膛10连接分离器11的进口,分离器11的烟气出口连接尾部烟道12、灰渣出口通过返料管13连接炉膛,石灰粉仓3内放置有颗粒度为10μm左右的石灰石粉,石灰粉仓3的出料口连接二次风箱4,二次风箱连接气力输送风机1,石灰石粉通过二次风管5经气力输送进入炉膛10的上部稀相区7。
11.一种循环流化床锅炉炉内喷钙深度脱硫工艺,将粒度为0.1mm~1.5mm的石灰石颗粒掺入煤中混合进入炉膛的下部密相区,石灰石颗粒可以在炉内停留较长时间,与炉内大颗粒进行脱硫反应石灰石颗粒进入炉膛后在下部密相区与大颗粒的床料、循环物料混合反应脱硫,去除密相区so2;将1
‑
80um的石灰石粉经过二次风箱,随二次风进入炉膛的上部稀相区,炉膛温度在850℃~880℃,保证了脱硫反应的最佳温度。从而确保锅炉no
x
低排放的同时做到so2低排放,使新型环保流化床锅炉氮氧化物和二氧化硫同时达到双低排放的环保性能,使燃烧产物更清洁,由于石灰石粉颗粒很小,炉膛停留时间短,因此石灰石石进入炉
膛的分布面积对炉内脱硫影响较大,炉膛10的前后墙分别间隔布置至少两个二次风管5,尽可能覆盖整个炉膛的截面,混合效果好,让石灰石粉在炉膛停留时间大于3秒,炉膛内总体钙硫比控制在3左右,满足石灰石进行完全脱硫反应,超细粉分散均匀,接触良好,脱硫效果明显,且运行稳定,对锅炉二次风量、风压均无影响;而且二次风箱内空气流速速较高,大于石灰石粉沉降速度,无超细粉沉积的问题。
12.本发明使用气力输送向炉膛内喷入超细石灰石粉,依托炉内流态,超细石灰石粉的给入充分发挥比表面积大、易于化学反应的优势,以实现 cfb 锅炉的深度脱硫。解决了超细粉炉膛停留时间短未能反应等问题,保证了本新工艺的技术可行性和深度炉内脱硫的效果。
技术特征:
1.一种循环流化床锅炉炉内喷钙深度脱硫系统,其包括炉膛,所述炉膛通过给煤管和给煤机连接煤仓,所述煤仓内放置有煤和石灰石颗粒,所述煤和所述石灰石颗粒进入所述炉膛的下部密相区,所述炉膛连接分离器的进口,所述分离器的烟气出口连接尾部烟道、灰渣出口通过返料管连接炉膛,其特征在于,其还包括石灰粉仓,所述石灰粉仓内放置有1
‑
80um的石灰石粉,所述石灰粉仓的出料口连接二次风箱,所述石灰石粉通过连接所述二次风箱的二次风管进入所述炉膛的上部稀相区。2.根据权利要求1所述的一种循环流化床锅炉炉内喷钙深度脱硫系统,其特征在于,所述二次风箱连接气力输送风机。3.根据权利要求1所述的一种循环流化床锅炉炉内喷钙深度脱硫系统,其特征在于,所述炉膛的前后墙分别间隔布置至少两个所述二次风管。4.一种循环流化床锅炉炉内喷钙深度脱硫工艺,其特征在于,将粒度为0.1mm~1.5mm的石灰石颗粒掺入煤中混合进入炉膛的下部密相区,石灰石颗粒进入炉膛后在下部密相区与大颗粒的床料、循环物料混合反应脱硫,去除密相区so2;将1
‑
80um的石灰石粉经过二次风箱,随二次风进入炉膛的上部稀相区,炉膛温度在850℃
‑
880℃,石灰石粉在炉膛停留时间大于3秒,炉膛内总体钙硫比控制在2.8
‑
3.2,满足石灰石进行完全脱硫反应。
技术总结
本发明属于循环流化床锅炉脱硫系统领域,具体涉及一种循环流化床锅炉炉内喷钙深度脱硫系统和工艺,其能够满足锅炉烟低硫的环保要求,同时可节省用户炉后脱硫的投资运行成本及解决二次污染的问题,其包括炉膛,所述炉膛通过给煤管和给煤机连接煤仓,所述煤仓内放置有煤和石灰石颗粒,所述煤和所述石灰石颗粒进入所述炉膛的下部密相区,所述炉膛连接分离器的进口,所述分离器的烟气出口连接尾部烟道、灰渣出口通过返料管连接炉膛,其还包括石灰粉仓,所述石灰粉仓内放置有1
技术研发人员:夏胜
受保护的技术使用者:无锡华光环保能源集团股份有限公司
技术研发日:2021.09.16
技术公布日:2021/12/6
再多了解一些
本文用于企业家、创业者技术爱好者查询,结果仅供参考。