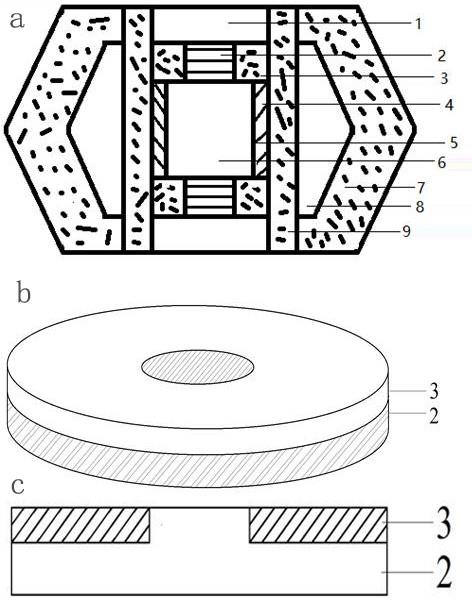
1.本发明属于超硬材料高温高压合成领域,特别是一种超高压/高温相变法制备纳米多晶氧化锆的方法。
背景技术:
2.纳米氧化锆具有高熔点、高硬度、相变增韧、耐氧化、抗酸抗碱、适合催化及用作催化载体等优良特性,是一种理想的功能性结构材料;制备方法通常是固相法、液相法、气相法,每一个方法都是在常压下、化学反应制备的;氧化锆在常温常压下为稳定的单斜相,在常温至其熔点2715 ℃之间会发生两种相变:1170 ℃ 时发生单斜相向四方相的相变,2370 ℃ 时出现向立方相的相变,这两种相变在常压下都是可逆的。通过加入稳定剂(y2o3、ceo、cao 等)形成固溶体的方式,可获得常温常压稳定的四方相和立方相,其中 y2o
3 稳定的四方相氧化锆多晶陶瓷材料因存在相变增韧现象而受到广泛关注;而cn201610882966.1、cn202010704273.x、cn202010071779.1、 cn201810916662.1等专利中纳米氧化锆的制备分别采用
ꢀ“
碱沉淀锆盐”固相法、凝胶法、醇法制备;都是在低温常压下制备的,都加入了不同量的化学试剂,工艺复杂,晶粒尺寸不均匀且容易造成化学污染等。
3.因此,急需一种既能工艺简单又能提高纳米氧化锆颗粒尺寸均匀性、一致性;又能极大减少了杂质物质引入带来的污染风险的纳米氧化锆制备新方法。
4.这种方法制备的纳米多晶氧化锆材料具有的优势:其一经过超高温高压合成制备的纳米多晶氧化锆,里面的结构是无数颗氧化锆紧密排列,中间没有增韧剂,自锐性、耐磨性更好;其二超高压条件可以抑制高温驱使的晶粒长大,成功解决了纳米晶粒在高温烧结过程中的长大等问题;其三合成结束回到常压下,氧化锆仍旧是立方相,不存在单斜相。
技术实现要素:
5.本发明的目的是提供一种纳米多晶氧化锆的合成方法。本发明利用微米级氧化锆微粉作为原材料制备。
6.为实现上述目的,本发明采用的技术方案为:一种超高压/高温相变法制备纳米多晶氧化锆的方法,过程如下:(1)将单斜相氧化锆微粉进行酸处理,用水冲洗至中性,烘干温度100~150℃;(2)将酸洗后的单斜相氧化锆微粉进行第一次真空处理,第一次真空处理后压制为圆柱体,进行第二次真空处理;(3)将第二次真空处理后的单斜相氧化锆微粉在1h~2h内匀速升温升压至1200~2500℃、8gpa~20gpa的环境下处理1~10h;再在1h~2h内匀速降温降压至800~900℃、5.5gpa~6.5gpa并在该温度和压力下保持1 h ~5h,最后在1h~2h内匀速降温降压至0;(4)取出样品将进行酸处理,过滤,洗涤,烘干温度100~150℃,即得。
7.进一步地,所述的酸处理是指将样品浸入质量比(3
‑
9):(0.5
‑
2)浓硫酸与浓硝酸的混合酸中,在300
‑
500℃处理1 h ~2h。
8.进一步地,所述第一次真空处理是指800~1500℃,真空度≥10
‑5mpa的环境下充入氢气真空反应1
‑
2h,然后降温至300
‑
700℃充入氩气或氮气后降温至室温。第一次真空处理后的单斜相氧化锆微粉可以直接加压合成,真空处理是为了处理表面处理后的单斜相氧化锆微粉表面粘附的挥发物,确保表面的纯净度。
9.进一步地,将表面处理以及真空处理后的单斜相氧化锆微粉压制成圆柱体,具体为,表面处理以及真空处理后的单斜相氧化锆微粉于压力为10~40mpa下压制成密度为4.5~5.2g/cm3的圆柱体。该步骤是为了方便六面顶压机对表面处理以及真空处理后的单斜相氧化锆微粉进行加压处理,将所述表面处理以及真空处理后的单斜相氧化锆微粉压制成圆柱体。再进行第二次真空处理,第二次真空处理均是指700~1300℃,真空度≥10
‑5mpa的环境下充入氢气真空反应1
‑
2h,然后降温至300
‑
700℃充入氩气或氮气后降温至室温;目的就是去除在压制过程中带入的金属和其余杂质;以便使用六面顶压机的作业方式。
10.进一步地,所述单斜相氧化锆微粉表面处理的具体过程为氧化锆于硫酸(质量分数为98.3%,密度为1.84g/cm3,浓度为18.4mol/l)与硝酸(质量分数为70%,密度为1.42g/cm3,浓度为15.8mol/l)按(3
‑
9):(0.5
‑
2)质量比加入烧杯中,加热温度为300
‑
500℃,时间为1
‑
3h,降温用蒸馏水冲洗呈中性并通过微波炉烘干,烘干温度为100~150℃,时间为1
‑
5h;即得单斜相氧化锆微粉,经过表面酸处理后,单斜相氧化锆微粉在酸洗可以处理掉表面存在金属离子,从而也就不会与氧化锆微粉表面发生反应,不会造成对单斜相氧化锆微粉的因表面杂质等反应造成的损失。最后就是剩余的纯净的单斜相氧化锆微粉。
11.进一步地,所述单斜相氧化锆微粉粒径≤150μm。为了提高合成效率和纯相纳米多晶氧化锆的品质,采用粒径不大于150μm的单斜相氧化锆微粉进行表面以及真空化处理,并进行后续的高温高压合成作业。之所以采用不大于150μm单斜相氧化锆微粉,原因是避免了以纳米晶粉末为初始材料,存在的团聚、吸附、难以分散的问题;避免了因原料问题制约烧结所得多晶材料的力学性能。因此它比氧化锆的硬度高,同时又兼有纳米材料超常的高强度和高韧性。其双重优点构成了其独一无二的物理性能。
12.进一步地,加压加温合成后的产物浸入质量比(3
‑
9):(0.5
‑
2)浓硫酸(质量分数为98.3%,密度为1.84g/cm3,量浓度为18.4mol/l)与浓硝酸(质量分数为70%,密度为1.42g/cm3,量浓度为15.8mol/l)的混合酸中,在300
‑
500℃处理1 h ~2h,过滤并洗净滤渣即得纯相纳米多晶氧化锆。受限于现有技术中的加热、加压方式,加压合成后的产物表面会一定程度地粘有加热管及传压介质杂质,所以需要利用浓硫酸(质量分数为98.3%,密度为1.84g/cm3,浓度为18.4mol/l)/硝浓酸(质量分数为70%,密度为1.42g/cm3,量浓度为15.8mol/l)与产物表面杂质反应,以去除相应杂质。
13.上述纯相多晶氧化锆的合成方法制得的纯相多晶氧化锆。
14.本发明的改进之处为:经过系统地研究发现,现有技术中的单斜相氧化锆微粉制备纳米多晶氧化锆的具体转变过程多为化学固相法,采用大量的化学试剂,造成环保压力很大,不需要掺杂任何增韧剂从而很容易实现立方相纳米多晶氧化锆。
15.与现有技术相比,本发明的有益效果为:(1)本发明合成方法是在高温高压条件下无任何添加剂,利用表面处理以及真空化的单斜相氧化锆微粉作为原材料直接转化而成。
16.(2)本发明合成方法制得的多晶氧化锆与常规法转化成的多晶氧化锆相比,不仅
解决了生长过程中晶粒长大问题,而且可以连续生产,从而大大降低了生产成本,节约了人力物力。
附图说明
17.图1为采用单斜相氧化锆微粉合成的纳米多晶氧化锆的组装体的结构示意图及异形碳片的结构示意图;(a)为组装体的结构示意图,(b)为异形碳片和mgo保温环组装后的结构示意图;(c)为(b)的剖视图。
18.图2为实施例1单斜相氧化锆微粉合成的纳米多晶氧化锆的合成工艺曲线;图3(a)为实施例1中使用单斜相氧化锆微粉的x射线衍射图谱;(b)为实施例1中使用单斜相氧化锆微粉制备的纳米多晶氧化锆微粉的x射线衍射图谱;图4 为实施例1中单斜相氧化锆微粉合成的纳米多晶氧化锆的扫描电镜图片(晶粒尺寸基本为100 nm以内);图5为实施例4单斜相氧化锆微粉合成的纳米多晶氧化锆第一次真空处理的温度变化曲线;图1中,1.硬质合金片,2.异形碳片,3.mgo保温环,4.石墨管,5.钼杯,6.单斜相氧化锆样品,7.mgo传压介质,8.碳化钨硬质合金增压体,9.白云石衬管,其中,硬质合金片材质是88wt%碳化钨 12wt%钴。
具体实施方式
19.以下结合附图和实施例对本发明的技术方案作进一步详细说明,但本发明的保护范围并不局限于此。
20.组装体的结构如图1所示,组装体的组装过程:内部组装过程是先将圆柱形的白云石衬管9放入,从下往上组装依次是下部的硬质合金片1,将下部的异性碳片2(异性碳片2为圆形,中部设有圆柱形凸起)的凸起朝上套上mgo保温环3,两者整体放在下部的硬质合金片1上,然后嵌入石墨管4,将装有单斜相氧化锆样品6的钼杯5放在石墨管4内,上面放入套上mgo保温环2的异性碳片2(异性碳片2的凸起朝下),放入上部的硬质合金片1,内部组装完毕,最后在外部组装碳化钨硬质合金增压体8和mgo传压介质7,整个组装体的侧面(除去上顶面和下底面)呈八面体,其中,在异性碳片2上套入mgo保温环3目的是阻止合成腔体里面的温度释放出来,起到保温作用。
21.下述实施例中浓硫酸均为质量分数为98.3%,密度为1.84g/cm3,浓度为18.4mol/l,浓硝酸均为质量分数为70%,密度为1.42g/cm3,浓度为15.8mol/l。
22.实施例1一种超高压/高温相变法制备立方相纳米多晶氧化锆的方法,过程如下:(1)取粒径0.5
‑
1μm单斜相氧化锆微粉100g,将单斜相氧化锆微粉浸入质量比例为3:0.5的硫酸与浓硝酸的混合酸中,加热至300℃并保温1h,降至室温,水冲洗至中性,烘干,烘干温度120℃,时间为1h;(2)第一次真空处理:将酸表面处理后的单斜相氧化锆在800℃、3*10
‑5mpa的真空炉内充入氢气保温1h,降温至300℃换氮气或氩气保护降至室温;(3)压制,第二次真空处理:将步骤(2)得到的单斜相氧化锆微粉于10
‑
40mpa压力
下压制成密度为4.5
‑
5.2 g/cm3、直径为7mm、高度为7mm的圆柱体,再于600℃、3*10
‑5mpa mpa的真空炉内充入氢气保温1h,降温至300℃换氮气或氩气保护并降至室温;(4)取出圆柱体按照图1的组装体进行组装,将组装体在六面顶压机上,如图2所示,先在1.5h内匀速升温、升压至1200℃、9gpa并在该温度和压力下保持6.5h,再在1h匀速降温降压至800℃、6gpa并在该温度和压力下保持5h,最后在1h内匀速降温降压至0,总合成时间为15h;(5)取出样品并浸入浓硫酸与浓硝酸质量比例为3:0.5的混酸中,300℃浸泡1h,过滤并洗净滤渣,120℃烘干,即得纯相纳米多晶氧化锆,图3为原料单斜相氧化锆微粉及目标产物纳米多晶氧化锆的扫描电镜图片,证实了纯相纳米多晶氧化锆的成功合成,且合成的纳米多晶氧化锆为立方相,图4为纳米多晶氧化锆的扫描电镜图片,由图4可知,产品粒径约为100nm。
23.实施例2一种超高压/高温相变法制备立方相纳米多晶氧化锆的方法,过程如下:(1)取粒径5
‑
10μm单斜相氧化锆微粉100g,将单斜相氧化锆微粉浸入质量比例为8:1的硫酸与浓硝酸的混合酸中,加热至500℃并保温1.5h,降至室温,水冲洗至中性,烘干,烘干温度100℃,时间为1.5h;(2)第一次真空处理:将酸表面处理后的单斜相氧化锆在1000℃、2*10
‑5mpa的真空炉内充入氢气保温1.2h,降温至500℃换氮气或氩气保护降至室温;(3)压制,第二次真空处理:将所述单斜相氧化锆微粉于10
‑
40mpa压力下压制成密度为4.5
‑
5.2 g/cm3、直径为7mm、高度为7mm的圆柱体,再于700℃、2*10
‑5mpa的真空炉内充入氢气保温1.5h,降温至500℃换氮气或氩气保护并降至室温;(4)取出圆柱体按照图1的组装体进行组装,将组装体在六面顶压机上,先在1.5h内匀速升温、升压至1400℃、10gpa并在该温度和压力下保持7h,再在1.5h匀速降温降压至900℃、6gpa并在该温度和压力下保持5h,最后在2h内匀速降温降压至0,总合成时间为17h;(5)取出样品,在质量比为8:1的浓硫酸与浓硝酸的混合酸中500℃浸泡1.5h,过滤并洗净滤渣,100℃烘干,即得纯相纳米多晶氧化锆,产品粒径约为50
‑
80nm。
24.实施例3一种超高压/高温相变法制备立方相纳米多晶氧化锆的方法,过程如下:(1)取粒径10
‑
20μm单斜相氧化锆微粉100g,先进行酸表面处理,将单斜相氧化锆微粉浸入质量比例为9:1的硫酸与硝酸的混合酸中,加热至500℃并在500℃保温1h,降至室温,水冲洗至中性,烘干,烘干温度150℃,时间为1.5h;(2)第一次真空处理:将酸表面处理后的单斜相氧化锆在1000℃、2*10
‑5mpa的真空炉内充入氢气保温1.3h,降温至450℃换氮气或氩气保护降至室温;(3)将所述单斜相氧化锆微粉于10
‑
40mpa压力下压制成密度为4.5
‑
5.2 g/cm3、直径为7mm、高度为7mm的圆柱体,再于700℃、2*10
‑5mpa mpa的真空炉内充入氢气保温1.5h,降温至500℃换氮气或氩气保护并降至室温;(4)取出圆柱体按照图1的组装体进行组装,将组装体在六面顶压机上,先在3h内匀速升温、升压至1600℃、15gpa并在该温度和压力下保持3h,再在1.5h匀速降温降压至900℃、6gpa并在该温度和压力下保持1h,最后在1.5h内匀速降温降压至0,总合成时间为10h;
(5)取出样品,在质量比为9:1的浓硫酸与浓硝酸的混合酸中500℃浸泡1h,过滤并洗净滤渣,150℃烘干,即得纯相纳米多晶氧化锆,产品粒径约为40
‑
70nm。
25.实施例4一种超高压/高温相变法制备立方相纳米多晶氧化锆的方法,过程如下:(1)取粒径30
‑
60μm单斜相氧化锆微粉100g,先进行酸表面处理,将单斜相氧化锆微粉浸入质量比例9:2的与硝酸的混合酸中,加热至500℃并在500℃保温3h,降至室温,水冲洗至中性,烘干,烘干温度125℃,时间为3h;(2)第一次真空处理:如图5所示,将酸表面处理后的单斜相氧化锆在1500℃、5*10
‑5mpa的真空炉内充入氢气保温3h,降温至600℃时换氮气或氩气保护降至室温;(3)压制,第二次真空处理:将所述单斜相氧化锆微粉于10
‑
40mpa压力下压制成密度为4.5
‑
5.2 g/cm3、直径为7mm、高度为7mm的圆柱体,再于1300℃、5*10
‑5mpa mpa的真空炉内充入氢气保温2h,降温至500℃时换氮气或氩气保护并降至室温;(4)取出圆柱体按照图1的组装体进行组装,将组装体在六面顶压机上,先在3h内匀速升温、升压至2200℃、19gpa并在该温度和压力下保持1h,再在2h匀速降温降压至900℃、6gpa并在该温度和压力下保持1h,最后在1 h内匀速降温降压至0,总合成时间为8h;(5)取出样品,在质量比为9:2的浓硫酸与硝酸的混合酸中500℃浸泡3h,过滤并洗净滤渣,130℃烘干,即得纯相纳米多晶氧化锆,产品粒径约为20
‑
60nm。
26.以上所述是本发明的优选实施方案,应当指出,对于本技术领域的普通技术人员来说,在不脱离本发明原理的前提下,还可以作出若干改进和润饰,这些改进和润饰也应该视为本发明的保护范围。
再多了解一些
本文用于企业家、创业者技术爱好者查询,结果仅供参考。