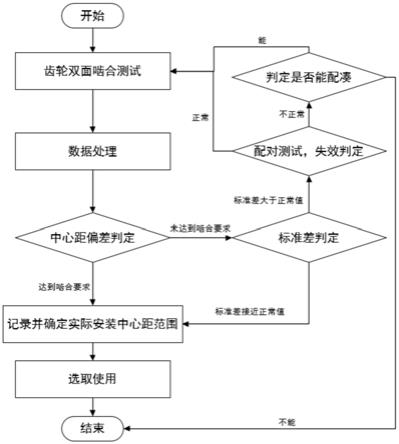
1.本发明涉及齿轮技术领域,特别是涉及一种齿轮双面啮合检测方法。
背景技术:
2.齿轮双面啮合测试是指将被测圆柱齿轮与标准件测量齿轮或测量蜗杆,通过所述齿轮双面啮合测试仪上的弹性压紧装置,使其作无间隙的双面啮合并以径向移动或摆动的方式,调整被测圆柱齿轮与标准件的中心距,采用标尺或指示表类器具测量取值,以评定齿轮的运动精度工作平稳性和齿侧间隙等的方法。
3.但该方法存在如下问题:一、通常需要提供一个比被测齿轮精度高2
‑
3级甚至更高精度的齿轮作为标准齿轮,测试过程中会对标准齿轮产生磨损,经过长时间测试后,测试精度会下降,故需要定时检测和更换标准齿轮,高精度齿轮成本较高,批量检测会造成大量高精度齿轮损坏;二、测试对象为单个齿轮,为被测齿轮与标准齿轮啮合,但实际应用阶段是两个普通齿轮的啮合,必须根据实际装配情况,进行齿轮配对工作,当齿轮测试厂家与应用厂家并非同一家时,配对工作很难完成。
技术实现要素:
4.基于此,本发明的目的在于,提供一种齿轮双面啮合检测方法,其具有避免使用高精度齿轮、降低不良品率的优点。
5.齿轮双面啮合检测方法,所述方法包括如下步骤:
6.步骤s1,齿轮双面啮合测试,选取两个被测齿轮组成被测齿轮组,根据实际使用情况将所述两个被测齿轮分别确定为主动齿轮和从动齿轮;将所述被测齿轮组安装在齿轮双面啮合测试仪上,使两被测齿轮做无侧隙双面啮合,确定所述主动齿轮旋转周期的起始角度和终止角度,并在所述旋转周期中选取i个采样角度,控制所述主动齿轮由起始角度转至终止角度,测出所述采样角度对应的测试双面啮合中心距,重复进行多次测试,记第n(n≥1)个旋转周期的测试双面啮合中心距为a
n
(θ),θ为所述采样角度;
7.步骤s2,进行数据处理,对各旋转周期中同一采样角度的测试双面啮合中心距的数值取平均值,得到所述旋转周期中各采样角度对应的双面啮合中心距平均值
8.步骤s3,对中心距偏差进行判定,当时,则判定这对齿轮达到啮合要求,进行下一步骤,否则为未达到啮合要求,其中a为标准齿轮双面啮合中心距,f
a
为中心距极限偏差;
9.步骤s4,记录并计算得出该对齿轮实际安装中心距范围,将所述被测齿轮组记录在标准齿轮测试数据库中,其主要参数特征为双面啮合中心距平均值;
10.步骤s5,选取使用,根据设计从标准齿轮测试数据库中选择所述实际安装中心距范围合适的齿轮组。
11.本发明所述的一种齿轮双面啮合检测方法,直接对两个需检测齿轮进行测试,与应用场景直接对接,以实际啮合中心距为配对标准,避免使用高精度齿轮,且测试完成后即
可记录入库,实现从检测到应用一步到位,避免磨损,成本低。
12.进一步地,在步骤s2中,对每个所述旋转周期测得的测试双面啮合中心距进行对比,当某个旋转周期的数据与其它旋转周期的数据相差过大时,则该旋转周期的数据出现异常,对其采取平均值替代或重新测试直至数据正常;当每组旋转周期的数据都正常时,再进行取平均值。所述步骤可提高数据的准确性。
13.进一步地,在步骤s2中,将每个所述旋转周期测得的测试双面啮合中心距绘制成曲线图,当某个旋转周期的曲线与其它旋转周期的曲线相差过大时,则该旋转周期的数据出现异常,对其采取平均值替代或重新测试直至数据正常;当每组旋转周期的曲线都正常时,再进行取平均值。所述步骤将中心距绘制成曲线,将数据可视化,便于进行数据处理。
14.进一步地,在步骤s3中,当所述被测齿轮组未达到啮合要求时,进行标准差判定,计算双面啮合总平均中心距和双面啮合中心距的标准差当σ接近正常值,且高于或低于a时,测试齿轮齿廓误差正常但齿轮实际齿廓发生偏差,继续进行步骤s4;当σ大于正常值,则被测齿轮中存在坏齿或单面齿廓误差较大,需对被测齿轮分别进行配对测试。对未达到啮合要求的齿轮进行判定,提高不合格品的利用率。
15.进一步地,所述配对测试为将所述两个被测齿轮分别与第三个齿轮进行配对测试,查找具体失效齿轮,若齿轮配对测试为正常,则该被测齿轮返回步骤s1继续进行测试,否则该被测齿轮为失效齿轮,进行中心距配凑。该步骤将正常齿轮筛选出,提高产品合格率。
16.进一步地,所述第三个齿轮为齿廓偏差检测合格的齿轮或高精度标准齿轮。所述第三个齿轮提高测试的准确度。
17.进一步地,所述失效齿轮配凑完成后,需使配凑后的齿轮组回到步骤1中进行双面啮合测试。保证失效齿轮的配对亦满足要求。
18.进一步地,在步骤s4中,计算双面啮合总平均中心距所述被测齿轮与侧隙j
bn
存在函数关系,故设a
w
=f(j
bn
),则所述被测齿轮的实际安装中心距范围为
19.进一步地,所述一个齿轮旋转周期为主动齿轮旋转一整圈或整圈的整数倍。便于对数据进行测量。
20.进一步地,所述采样角度的选取由光栅采样频率确定。提高测量效率。
21.为了更好地理解和实施,下面结合附图详细说明本发明。
附图说明
22.图1为本发明所述一种齿轮双面啮合检测方法的流程示意图。
具体实施方式
23.请参阅图1,图1为本发明所述一种齿轮双面啮合检测方法的流程示意图。本发明公开了一种齿轮双面啮合检测方法,可在对单个齿轮无测试要求的情况下,探究两个被测
齿轮组成的齿轮组的性能参数,其检测步骤包括:
24.步骤s1、齿轮双面啮合测试,选取两个被测齿轮组成被测齿轮组,根据实际使用情况将所述两个被测齿轮分别确定为主动齿轮和从动齿轮。将所述被测齿轮组安装在齿轮双面啮合测试仪的工位上,通过所述齿轮双面啮合测试仪上的弹性压紧装置,使两被测齿轮做无侧隙啮合。由于齿轮存在径向误差,所述主动齿轮和从动齿轮的啮合中心距会不断发生变化。确定所述主动齿轮旋转周期的起始角度和终止角度,并在所述旋转周期中选取i个采样角度,控制所述主动齿轮由起始角度转至终止角度,测出所述采样角度对应的双面啮合中心距,重复进行多次测试,记第n(n≥1)个旋转周期的测试双面啮合中心距为a
n
(θ),θ为所述采样角度。所述一个齿轮旋转周期为主动齿轮旋转一整圈或整圈的整数倍,采样角度的选取可由光栅采样频率确定。
25.步骤s2、进行数据处理,对每个旋转周期测得的测试双面啮合中心距进行对比,当某个旋转周期的数据与其它旋转周期的数据相差过大时(实际一般会把测试双面啮合中心距的变化绘制成曲线,每个周期一般来说曲线是差不多的,如果肉眼上就能判断出两个周期曲线不一样,那就认为是相差过大,也可根据采样频率、周期时间、测试速度、齿轮参数等做方差分析),则该旋转周期的数据出现异常,对其采取平均值替代或重新测试直至数据正常(所述平均值替代可采用附近采样角度的数据进行平均值替代,若附近采样角度的数据也有异常,可采用其它旋转周期对应的采样角度数据进行平均值替代);当每组旋转周期的数据都正常时,则对各旋转周期中同一采样角度的测试双面啮合中心距数值取平均值,得到所述旋转周期中各采样角度对应的双面啮合中心距平均值
26.步骤s3、对中心距偏差进行判定,当时,则判定这对齿轮达到啮合要求,进行下一步骤,否则为未达到啮合要求,其中a为标准齿轮双面啮合中心距,中心距极限偏差f
a
的推荐值参考标准“gb 10095
‑
88渐开线圆柱齿轮精度”相关表格。
27.当未达到啮合要求时,需对被测齿轮进行进一步判断:计算双面啮合总平均中心距计算双面啮合中心距的标准差未达到啮合要求的被测齿轮组通常有以下两种情况:
28.情况一、当σ大于正常值(该情况也可直接通过双面啮合中心距曲线图进行判断),则被测齿轮中存在坏齿或单面齿廓误差较大,造成某个或几个个例点存在啮合中心距偏差过大。此时,需要将两个被测齿轮分别与第三个齿轮(最好为齿廓偏差检测合格的齿轮,甚至可以是高精度标准齿轮)进行配对测试,查找具体失效齿轮。若齿轮配对测试为正常,则返回步骤s1继续进行测试。
29.而对失效齿轮,根据配凑中心距的原则,查找与其对应的失效齿轮。例如,对于部分轮齿齿廓向内偏移的,可尝试查找存在对应数量轮齿齿廓向外偏移的齿轮进行配对,比如若失效齿轮的第五个轮齿向外偏移,那么如果存在另一个齿轮,能够保证与第五个齿啮合的齿是向内偏移,那么可以尝试进行配对。配对完成后,则返回步骤s1继续进行测试,但并非所有失效齿轮均能实现配凑。
30.情况二、当σ接近正常值,且高于或低于a时,测试齿轮齿廓误差正常,但由于齿轮加工过程中,刀具位置、刀具磨损、夹具误差等原因造成齿轮实际齿廓发生偏差,使得齿轮
啮合的中心距会发生变化。该情况由于能根据实际设计或实际加工出来的齿轮安装中心距来配对,因此可以进行下一步骤。
31.步骤s4、记录并得出该对齿轮实际安装中心距范围,将这对齿轮记录在标准齿轮测试数据库中,其主要参数特征为双面啮合中心距平均值。一般情况下,除非特殊要求,齿轮在实际应用中并非采用双面啮合的形式,装配中心距通常比双面啮合中心距稍大,存在侧隙j
bn
,参考论文《渐开线圆柱齿轮中心距与侧隙的关系》,可得到以下计算公式:
32.j
bt
=p
b
‑
(s
b1
s
b2
) 2(r
b1
r
b2
)invα
ωt
[0033][0034]
j
bn
=j
bt
·
cosβ
b
[0035]
式中,p
b
为齿间距,r
b1
、r
b2
为主动齿轮和从动齿轮的基圆半径,s
b1
、s
b2
为主动齿轮和从动齿轮的基圆齿厚,a
w
为标准装配中心距,α
ωt
为啮合角,β
b
为基圆螺旋角,j
bt
为端面法向侧隙。
[0036]
由上式可知标准圆柱齿轮中心距与侧隙存在函数关系,两者之间可以相互转换,故可设:
[0037]
a
w
=f(j
bn
)
[0038]
且间隙j
bn
越大,标准装配中心距a
w
也越大(式中存在渐开线反函数计算,需要借助计算机辅助计算);
[0039]
故对所述被测齿轮,在实际装配时也需要预留间隙,以标准齿轮在最小侧隙下的标准装配中心距与标准齿轮双面啮合中心距的比值作为参考值,要求配对的实际安装中心距a
az
为:
[0040][0041]
计算双面啮合总平均中心距即对于双面啮合总平均中心距为的被测齿轮,要求配对到实际安装中心距为a
az
需满足:
[0042][0043]
此外,由于齿轮侧隙过大会存在齿轮出现冲击、噪音等异常现象,故齿轮也存在最大侧隙要求(详见国标“gbz 18620.2
‑
2008圆柱齿轮检验实施规范第2部分径向综合偏差、径向跳动、齿厚和侧隙的检验”),同样,按照上述计算,存在如下要求:
[0044][0045]
综上,对所述被测齿轮的实际安装中心距有如下要求:
[0046][0047]
步骤s5、根据设计从标准齿轮测试数据库中选择实际安装中心距范围合适的齿轮组。
[0048]
也可利用该方法对含有三个及以上被测齿轮的齿轮组进行啮合测试,即先对其中
两个被测齿轮进行啮合测试,再以其中的从动齿轮作为主动齿轮,以第三被测齿轮为从动齿轮进行啮合测试,以此类推。
[0049]
本发明所述的一种齿轮双面啮合检测方法,直接对两个需检测齿轮进行测试,与应用场景直接对接,以实际啮合中心距为配对标准,避免使用高精度齿轮,且测试完成后即可记录入库,实现从检测到应用一步到位,避免磨损,成本低。对于部分齿轮的径向偏差不合格,可以通过配对进行不良品再利用,降低齿轮的不良率。
[0050]
以上所述实施例仅表达了本发明的几种实施方式,其描述较为具体和详细,但并不能因此而理解为对发明专利范围的限制。应当指出的是,对于本领域的普通技术人员来说,在不脱离本发明构思的前提下,还可以做出若干变形和改进,则本发明也意图包含这些改动和变形。
再多了解一些
本文用于企业家、创业者技术爱好者查询,结果仅供参考。