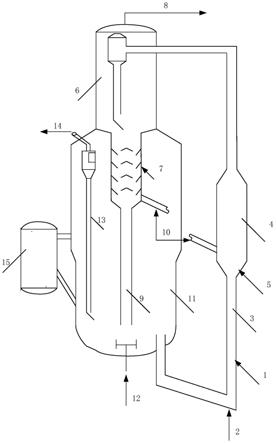
1.本发明涉及在不存在氢的条件下烃油的催化转化技术领域,具体涉及一种烃油转化的方法。
背景技术:
2.随着我国国民经济的增长和道路交通电气化进程等因素影响,近年来,国内成品油市场对柴油的需求量有所下降,为低品质柴油找到出路,日益成为炼油企业所需考虑的首要问题之一。同时,国内市场对芳烃产品的需求增长迅猛,向化工方向转型,增产以对二甲苯(px)为代表的高价值芳烃产品业已成为催化裂化技术发展的未来目标。在未来较长的一段时间内,国内对二甲苯供应仍不能满足国内需求。据估算2020年国内仍需进口1075万吨对二甲苯。预计2020-2025年间,国内市场对二甲苯供需年均缺口仍在740万吨以上。近年来,在炼油企业主力二次加工装置催化裂化上,增产对二甲苯为代表的芳烃产品,成为本领域技术人员关注的方向。
3.催化裂化是重油轻质化的重要技术手段之一,国内炼厂催化柴油对产品柴油的贡献亦超过20%。因此,对催化裂化装置的结构和操作的优化,是调整产品结构、降低柴油出厂压力的主要方法之一。
4.催化裂化装置使用终止剂技术,是调整反应苛刻度以适应产品要求的重要手段之一,国内80%的催化装置正在使用该技术。在催化装置上常用的终止剂介质有粗汽油、稳定汽油、酸性水、净化水、轻污油和焦化轻油等各种不同性能的组分。通过调整终止剂的注入位置和终止剂用量可有效控制提升管不同部位的反应苛刻度,促进有益的化学反应,以改善产品的性质和提高日的产物的选择性。
5.us5954942a公开了一种采用水或者可气化烃类作为终止介质的方法。将终止介质注入提升管后部,以强化重质烃类转化,改善产品结构。该方法给出了相应工况下不同终止剂用量和终止剂注入位置对产物分布的影响。但是该终止技术对产物的烃族组成,特别是对汽油中的烯烃含量未有提及。
6.us5217602a公开了一种通过极冷终止改善产品结构的方法。该方法先将催化剂和反应油气引出提升管后快速分离,催化剂进入汽提段而对反应油气进行极冷作业。该方法即可抑制二次裂化,又可避免对催化剂的极冷造成能耗增加。但是该方法只是定向的终止了二次裂化反应,对需要催化剂参与的油品改质等效果甚微。
7.cn1600832a公开了一种催化裂化过程中降低汽油烯烃含量的方法。该方法以多种惰性介质和轻质石油烃类为终止介质,给出了不同注入位置和注入终止剂量对催化过程和产物分布的影响。但是该方法公开的轻质石油烃类终止介质均为汽油馏分,含烯烃等易反应成分较高,在终止主反应的过程中自身均会发生裂化反应,难以控制焦炭增长等问题。
8.而将终止剂技术用于降低柴油负荷,同时增产高品质芳烃产品的技术则鲜有报道。
技术实现要素:
9.本发明的目的是为了克服现有技术的方法不能兼具降低柴油负荷,同时增产高品质芳烃产品的缺陷,提供一种烃油转化的方法,该方法既能够降低柴油负荷,同时又能增产高品质芳烃产品,特别是对二甲苯(px)产率得到显著提高。
10.为了实现上述目的,本发明提供一种烃油转化的方法,该方法包括:
11.(1)将加氢催化柴油原料与催化剂在第一反应区中进行催化裂化反应,得到物流i,所述第一反应区中含有提升管反应器;
12.(2)将烷基转移剂与所述物流i引入至第二反应区中进行烷基转移反应,得到物流ii;
13.(3)将所述物流ii进行分离,得到反应油气和待生催化剂。
14.与现有技术相比,本发明提供的烃油转化的方法通过设置用于烷基转移反应的第二反应区,且将加氢催化柴油的催化裂化反应与烷基转移反应分区进行,能够使得,其一,加氢催化柴油消减效果明显,加氢催化柴油的转化率高,可达加氢柴油原料处理量的70%以上;其二,得到的反应油气中的汽油中芳烃含量升高,辛烷值(ron)提高0.2-2个单位;其三,既能够降低柴油负荷,同时又能增产高品质芳烃产品,特别是对二甲苯(px)产率得到显著提高;其四,所述引入的第二反应区利于单独调变烷基转移反应过程中的催化剂藏量、反应温度等参数,操作更加灵活;其五、该方法所涉及的装置均为现有设备,炼油企业所需投入的改造资金少,成本低,见效快。
附图说明
15.图1是本发明的烃油转化流程示意图。
16.附图标记说明
17.1-原料
ꢀꢀꢀꢀꢀꢀꢀꢀꢀꢀꢀꢀꢀꢀꢀꢀ
2-提升蒸汽
ꢀꢀꢀꢀꢀꢀꢀꢀꢀꢀꢀꢀ
3-提升管反应器
18.4-第二反应区
ꢀꢀꢀꢀꢀꢀꢀꢀꢀꢀ
5-烷基转移剂
ꢀꢀꢀꢀꢀꢀꢀꢀꢀꢀ
6-沉降器
19.7-汽提器
ꢀꢀꢀꢀꢀꢀꢀꢀꢀꢀꢀꢀꢀꢀ
8-反应油气
ꢀꢀꢀꢀꢀꢀꢀꢀꢀꢀꢀꢀ
9-待生立管
20.10-循环斜管
ꢀꢀꢀꢀꢀꢀꢀꢀꢀꢀꢀ
11-再生器
ꢀꢀꢀꢀꢀꢀꢀꢀꢀꢀꢀꢀꢀ
12-再生器主风
21.13-旋风分离器
ꢀꢀꢀꢀꢀꢀꢀꢀꢀ
14-再生烟气
ꢀꢀꢀꢀꢀꢀꢀꢀꢀꢀꢀ
15-外取热器
具体实施方式
22.在本文中所披露的范围的端点和任何值都不限于该精确的范围或值,这些范围或值应当理解为包含接近这些范围或值的值。对于数值范围来说,各个范围的端点值之间、各个范围的端点值和单独的点值之间,以及单独的点值之间可以彼此组合而得到一个或多个新的数值范围,这些数值范围应被视为在本文中具体公开。
23.如前所述,本发明提供一种烃油转化的方法,该方法包括:
24.(1)将加氢催化柴油原料与催化剂在第一反应区中进行催化裂化反应,得到物流i,所述第一反应区中含有提升管反应器;
25.(2)将烷基转移剂与所述物流i引入至第二反应区中进行烷基转移反应,得到物流ii;
26.(3)将所述物流ii进行分离,得到反应油气和待生催化剂。
27.本发明采用油气接力分区转化的方法,在上述第一反应区中,主要发生加氢催化柴油原料环烷环的开环裂化反应,所得的物流i中含有大量多甲基单环芳烃;在上述第二反应区中,主要发生多甲基单环芳烃与缺甲基烷基转移剂之间的烷基转移反应,最大化生成中间碳数(c8)的二甲苯等高价值芳烃产品。
28.本发明中,所述待生催化剂是指反应完成后经过汽提器汽提后的催化剂。本发明对步骤(3)中所述的分离方法和分离设备没有限制,例如可以采用沉降器进行分离。
29.根据本发明,步骤(3)中得到的反应油气可以按照本领域的常规方法进行进一步处理,例如可以进入后续分离系统,分离出液化气、汽油馏分、柴油馏分等产品。
30.优选地,所述第二反应区中含有流化床反应器。
31.在本发明的一种优选实施方式中,该方法还包括:将至少部分所述待生催化剂引入至再生器中进行再生,并将得到的再生催化剂循环回所述第一反应区中参与所述催化裂化反应。该优选实施方式中,在进行所述再生之前,还可以包括对所述待生催化剂进行沉降和汽提的常规处理。
32.优选地,所述再生催化剂中的碳含量为0.01-0.1重量%。
33.在本发明的一种优选的实施方式中,该方法还包括:将剩余部分所述待生催化剂循环回所述第二反应区中参与所述烷基转移反应。进一步优选地,在该优选实施方式中,循环回所述第二反应区中的待生催化剂的量占步骤(3)中获得的全部所述待生催化剂的量的5-20重量%。
34.本发明对所述烷基转移剂的种类的可选范围较宽;为了获得高品质芳烃尤其是提高对二甲苯和二甲苯的产率,优选地,所述烷基转移剂选自苯和/或甲苯。
35.优选情况下,所述烷基转移剂与引入至第二反应区中的烃油组分的用量重量比为(0.015-0.5):1。本发明中,“引入至第二反应区中的烃油组分”是指步骤(1)中的所述加氢催化柴油原料与任选地被引入的汽油馏分的总和,所述汽油馏分为来自步骤(3)得到的反应油气经分离后得到的汽油馏分。
36.在本发明的一种优选实施方式中,该方法还包括:将步骤(3)中得到的反应油气进行分离以获得汽油馏分、柴油馏分。
37.进一步优选地,该方法还包括:将所述汽油馏分引入至所述第二反应区中与所述烷基转移剂一起参与所述烷基转移反应。采用该优选方案,利于调节第二反应区的催化剂藏量和反应温度。
38.在本发明的一种优选实施方式中,所述催化裂化反应的条件满足:反应温度为450-650℃,反应压力为100-450kpa,催化剂与加氢催化柴油原料的用量重量比为(2-20):1,水蒸汽与加氢催化柴油原料的用量重量比为(0.01-0.5):1,反应时间为0.1s-30s。
39.更优选地,所述催化裂化反应的条件满足:反应温度为500-550℃,反应压力为100-300kpa,催化剂与加氢催化柴油原料的用量重量比为(3-10):1,水蒸汽与加氢催化柴油原料的用量重量比为(0.02-0.3):1,反应时间为0.1s-10s。
40.本发明中,此处的水蒸汽是指提升蒸汽,所述加氢催化柴油原料在提升蒸汽的作用下引入第一反应区。所述的提升蒸汽为本领域技术人员公知的预提升介质,提升蒸汽的作用是使催化剂加速上升,在提升管反应器底部形成密度均匀的催化剂活塞流。提升蒸汽的用量为本领域的技术人员所公知,一般来说,提升蒸汽的用量占烃油总量的1-30重量%,
优选2-15重量%。
41.根据本发明,所述的催化剂可以为新鲜催化剂,新鲜催化剂指未经反应的催化剂,也可以为反应体系中的再生催化剂,优选为反应体系中的再生催化剂。所述的新鲜催化剂优选为含有或不含有分子筛的酸性催化裂化催化剂。所述分子筛优选选自含或不含稀土的y或hy型沸石、含或不含稀土的超稳y型沸石、zsm-5系列沸石或具有五元环结构的高硅沸石、β沸石、镁碱沸石中的至少一种,所述的催化剂优选为不含分子筛的酸性催化裂化催化剂,更优选为无定型硅铝催化剂。
42.优选情况下,所述烷基转移反应的条件满足:反应温度为450-500℃,反应压力为100-300kpa,催化剂与引入至第二反应区中的烃油组分的用量重量比为(6-10):1,水蒸汽与引入至第二反应区中的烃油组分的用量重量比为(0.02-0.5):1,反应时间为2s-12s。
43.本发明中,对所述加氢催化柴油原料没有限制,可以为任何催化裂化装置所产的催化柴油;优选地,所述加氢催化柴油原料满足以下条件:密度≤0.95g/cm3和/或氢含量≥10重量%。
44.更优选地,所述加氢催化柴油原料满足以下条件:密度≤0.92g/cm3和/或氢含量≥12重量%。
45.优选地,所述汽油馏分的初馏点为60-95℃,终馏点180-205℃。
46.根据本发明提供的一种特别优选的实施方式,所述烃油转化的方法包括:
47.(1)将加氢催化柴油原料与催化剂在第一反应区中进行催化裂化反应,得到物流i,所述第一反应区中含有提升管反应器;所述第一反应区中含有提升管反应器;
48.(2)将烷基转移剂与所述物流i引入至第二反应区中进行烷基转移反应,得到物流ii;所述第二反应区中含有流化床反应器;
49.(3)将所述物流ii进行分离,得到反应油气和待生催化剂;
50.将至少部分所述待生催化剂引入至再生器中进行再生,并将得到的再生催化剂循环回所述第一反应区中参与所述催化裂化反应;
51.将剩余部分所述待生催化剂循环回所述第二反应区中参与所述烷基转移反应。
52.现结合图1对本发明的前述特别优选的实施方式进行详细说明,如图1所示,所述烃油转化的方法包括:
53.(1)将加氢催化柴油原料1在提升蒸汽2的作用下引入第一反应区中的提升管反应器3内,与催化剂接触后上行,进行催化裂化反应,得到物流i;
54.(2)将烷基转移剂5与所述物流i引入至第二反应区4中的流化床反应器内,进行烷基转移反应,得到物流ii;
55.(3)将所述物流ii引入沉降器6内进行分离,得到反应油气8和待生催化剂;
56.将至少部分所述待生催化剂依次经汽提器7、待生立管9引入至再生器11中进行再生,并将得到的再生催化剂循环回所述第一反应区中参与所述催化裂化反应;
57.将剩余部分所述待生催化剂经循环斜管10循环回所述第二反应区4中参与所述烷基转移反应;循环回所述第二反应区4中的待生催化剂的量占步骤(3)中获得的全部所述待生催化剂的量的5-20重量%;
58.将步骤(3)中得到的反应油气8进行分离以获得汽油馏分、柴油馏分,所述汽油馏分的初馏点为60-95℃,终馏点180-205℃。任选地将所述汽油馏分引入至所述第二反应区
中与所述烷基转移剂一起参与所述烷基转移反应。
59.上述再生器11底部设置有再生器主风12,再生器主风12用于向再生器11内输送主风;再生器11内部侧面设置有旋风分离器13,旋风分离器13用于对再生器11内的待生催化剂进行再次沉降、分离,得到再生烟气14和所述再生催化剂;再生器11侧面设置有外取热器15。
60.本发明中,所述第一反应区和第二反应区为串联配置,共用一个沉降器、汽提器和再生器。
61.本发明中,所述再生器、沉降器、旋风分离器和外取热器均为本领域的常用设备,本发明对此没有限制,只要能实现所对应的功能即可,在此不再赘述。
62.本发明中,所述汽提器中的汽提介质优选采用水蒸汽进行汽提,其作用是将催化剂颗粒之间和颗粒孔隙内充满的油气置换出来,提高油品产率。用于汽提的水蒸汽的量为本领域的技术人员所公知。一般来说,用于汽提的水蒸汽量占催化剂循环量的0.1-0.8重量%,优选0.2-0.4重量%。
63.以下将通过实施例对本发明进行详细描述。以下实施例中,以下实施例中,所涉及原料除另有说明外均为市售品。
64.其中,原料:加氢催化柴油,购自中国石油化工集团公司燕山分公司,性质列于表2;
65.催化剂:cgp-ys催化剂,购自中国石化催化剂分公司,性质见表1;
66.烷基转移剂:甲苯。
67.下述实施例中,采用带有第二反应区的提升管反应器,所述第二反应区为扩径的圆桶状结构,直径100毫米。
68.下述对比例中,采用中型提升管反应器,所述提升管反应器为总高度为10米,直径为25毫米的圆柱体结构。
69.以下实施例中所述反应油气或汽油中的组成采用气相色谱仪测定。
70.实施例1
71.本实施例用于说明本发明的烃油催化转化的方法。
72.如图1所示,(1)将预热后的加氢催化柴油原料1在提升蒸汽2的作用下引入第一反应区中的提升管反应器3内,与新鲜的cgp-ys催化剂接触后上行,进行催化裂化反应,得到物流i;
73.(2)将烷基转移剂5与所述物流i引入至第二反应区4中的流化床反应器内,进行烷基转移反应,得到物流ii;
74.(3)将所述物流ii引入沉降器6内进行分离,得到反应油气8和待生催化剂;所述待生催化剂中的碳含量为1.12wt%;
75.将部分所述待生催化剂依次经汽提器7、待生立管9引入至再生器11中进行再生,并将得到的再生催化剂循环回所述第一反应区中参与所述催化裂化反应;所述再生催化剂中的碳含量为0.1wt%;
76.将剩余部分所述待生催化剂经循环斜管10循环回所述第二反应区4中参与所述烷基转移反应。循环回所述第二反应区4中的待生催化剂的量占步骤(3)中获得的全部所述待生催化剂的量的10重量%。
77.将步骤(3)中得到的反应油气进行分离以获得汽油馏分、柴油馏分,所述汽油馏分的馏程为71-202℃。
78.本实施例中所涉及的工艺参数见表3。所述反应油气的产品分布见表4,所述反应油气中汽油的组成见表5。
79.对比例1
80.将在200℃预热后的加氢催化柴油原料1a在预提升蒸汽作用下引入中型提升管反应器底部,与再生催化剂或新鲜催化剂混合,进行反应,然后向上流动至中型提升管反应器出口后进入沉降器,经旋风分离器分离得到待生催化剂和反应产物;其中,中型提升管反应器的反应温度为502℃,压力为140千帕;所述预提升蒸汽的用量为原料油的5wt%,剂油比(催化剂与原料油的重量比)为6,原料油在中型提升管反应器中的停留时间(即反应时间)为4秒。
81.所述反应产物进入后续分离系统分离得到产物油,所述带炭催化剂经汽提得到待生催化剂,待生催化剂进入再生器于670℃下烧焦再生后循环使用。
82.本实施例中所涉及的工艺参数见表3。所得产物油的产品分布见表4,所述产物油中汽油的组成见表5。
83.实施例2
84.按照实施例1的方法进行烃油转化,不同的是,所述第二反应区的原料为物流i、甲苯和汽油馏分的混合物,所述汽油馏分为步骤(3)中制得的反应油气经分离系统分离后的部分汽油馏分,所用部分汽油馏分占加氢催化柴油原料的50重量%;且所述加氢催化柴油:汽油馏分:甲苯的重量比为10:5:1。
85.实施例3-5
86.按照实施例1的方法进行烃油转化,不同的是,采用表3所示的工艺参数代替实施例1的工艺参数。
87.表1
[0088][0089][0090]
表2
[0091][0092]
表3
[0093][0094]
注:所述提升管反应器预提升蒸汽量是指相对于100重量份加氢催化柴油原料,水蒸气的重量份,所述第二反应区预提升蒸汽量是指相对于100重量份引入至第二反应区中的烃油组分,水蒸汽的重量份;所述提升管反应器和第二反应区分别指提升管反应器反应器和第二反应区反应器;所述提升管反应器剂油比是指提升管反应器内催化剂与加氢催化柴油原料的用量重量比;所述第二反应区剂油比是指第二反应区内催化剂与引入第二反应区内的油组分的用量重量比。
[0095]
表4
[0096]
[0097]
表5
[0098]
汽油组成,wt%实施例1实施例2对比例1实施例3实施例4实施例5实施例6正构烷烃13.615.513.512.913.416.723.9异构烷烃20.520.920.220.420.618.814.6烯烃14.414.514.315.113.912.210.4环烷烃16.615.016.416.516.718.920.3芳烃34.934.135.635.135.433.430.8二甲苯净产率,wt%15.316.18.615.616.212.39.1对二甲苯净产率,wt%3.64.12.13.84.22.42.3辛烷值(抽出二甲苯),wt%90.991.190.591.191.090.789.9
[0099]
由表3-表5可以看出,采用本发明提供的方法,且将第二反应区反应温度控制为低于提升管反应器反应温度,使得所制得的反应油气中汽油的改质效果较为明显,液化气产率至少提高0.1个百分点,其他产品收率也得到提高。
[0100]
由表5可以看出,采用本发明提供的方法,特别是在第二反应区进行引导性的促进低碳数烷基转移剂芳烃与重质芳烃发生烷基转移反应,使得反应油气中的汽油中,高价值的二甲苯和对二甲苯产率显著提高。
[0101]
以上详细描述了本发明的优选实施方式,但是,本发明并不限于此。在本发明的技术构思范围内,可以对本发明的技术方案进行多种简单变型,包括各个技术特征以任何其它的合适方式进行组合,这些简单变型和组合同样应当视为本发明所公开的内容,均属于本发明的保护范围。
再多了解一些
本文用于企业家、创业者技术爱好者查询,结果仅供参考。