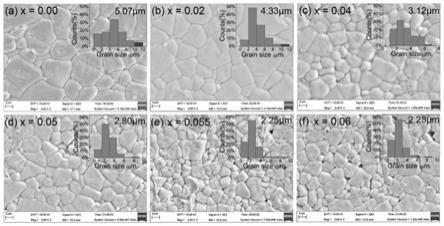
1.本发明涉及陶瓷材料,特别是一种高储能特性铌酸银基反铁电储能陶瓷及其低温烧结方法。
背景技术:
2.固体电介质陶瓷由于其功率密度高、充放电速度快等特点在智能电网、电动动力汽车以及先进武器装备等领域有极大的应用需求。电介质陶瓷根据其介电常数与电场强度的关系分为线性电介质与非线性电介质。线性电介质通常具有介电常数低、介电损耗低以及击穿场强高的特点。非线性电介质主要分为顺电材料、铁电材料、反铁电材料和弛豫铁电材料,其介电常数与电场强度存在一定的函数关系,且其介电常数比线性电介质材料要高。
3.电介质的储能密度主要与其介电常数和击穿场强有关,高的介电常数和击穿场强有利于储能的增加。反铁电内部相邻晶格内存在互相反平行的偶极子,对外不显示极性,在高电场作用下偶极子重新平行排列,出现可逆反铁电相到铁电相的转变,获得有利于介电储能的双电滞回线。反铁电材料由于其具有滞后低、饱和极化强度大、剩余极化强度低和储能密度高等特征,是一种优良的电介质储能材料。
4.目前市面上商用的反铁电储能材料以铅基陶瓷为主,铅基陶瓷在其制备过程中产出的含铅物质对环境造成很大的污染,因此开发出一种性能较好的无铅反铁电储能陶瓷具有非常重要的意义。目前对于无铅储能材料的研究热点集中在钛酸钡基、铌酸钠基和铌酸银基材料,其中铌酸银基材料由于其高的极化强度及双电滞回线在众多无铅储能材料里方面有着很大的优势,然而其也存在着击穿场强低、制备工艺复杂、反铁电相不稳定等问题限制着储能密度的提升。
5.铌酸银是一种典型的钙钛矿(abo3)结构材料。目前,对铌酸银基反铁电储能陶瓷的研究主要从稳定其反铁电相,提高其击穿场强两个方面来入手。具体实施方案即通过离子掺杂减小容忍因子t,稳定其反铁电相,提升其相变场强;或借此减小样品的晶粒以提高其击穿场强。根据离子掺杂取代位置的不同,对铌酸银基陶瓷的改性主要分为:a位取代,b位取代,a/b位共同取代三种方式。对于a位取代的研究,比较有代表性的ag
0.94
la
0.02
nb
o3
体系的储能达到4.4j/cm3,效率达到73%;对于b位取代,agnb
0.85
ta
0.15
o3体系储能达到4.2j/cm3,效率达到69%;对于a/b位共同取代,ag
0.97
nd
0.01
ta
0.20
nb
0.80
o3体系储能达到6.5j/cm3,效率达到71%。然而,在铌酸银基反铁电储能陶瓷制备过程中通常需要在1100℃
‑
1200℃的高温和氧气氛围下保温4
‑
6h,相比于其他无铅储能陶瓷在制备工艺上要复杂很多。
6.由此可见,如何在保证高储能特性的前提下,简化铌酸银基反铁电储能陶瓷的制备工艺,成为该技术领域的一道难题。
技术实现要素:
7.针对上述情况,为解决现有技术之缺陷,本发明之目的就是提供一种高储能特性铌酸银基反铁电储能陶瓷及其低温烧结方法,可有效解决现有技术击穿场强低、制备工艺
复杂、反铁电相不稳定的问题。
8.本发明解决的技术方案是,本发明以组分(1
‑
x)agnbo3
‑
x(sr
0.7
bi
0.2
)hfo3‑
0.01bcb(简称(1
‑
x)an
‑
xsbh
‑
y bcb)为基础,采用传统的固相反应法,将高纯的ag2o粉体、nb2o5粉体、srco3粉体、bi2o3粉体和hfo2粉体作为基体材料;以ba(oh)2·
8h2o粉体、h3bo3粉体和cuo粉体按摩尔比1:2:1制备而成的bacu(b2o7)作为烧结助剂,通过简单、易于实现的工艺制备出高储能密度,高储能效率并具有良好温度稳定性的铌酸银基反铁电储能陶瓷。
9.具体包括以下步骤:
10.1)先按照摩尔比计算x=0、0.02、0.04、0.05、0.055和0.06时各原料的质量并分别称取ag2o粉体、nb2o5粉体、srco3粉体、bi2o3粉体和hfo2粉体,其中ag2o粉体(国药沪试)的纯度为≥99.7%,nb2o5粉体(国药沪试)的纯度为≥99.99%,srco3粉体(国药沪试)的纯度为≥99.00%,bi2o3粉体(国药沪试),hfo2粉体(麦克林)的纯度为99.9%;
11.2)先将步骤1)称取的ag2o粉体、nb2o5粉体、srco3粉体、bi2o3粉体和hfo2粉体混合球磨形成第一基体粉料;
12.3)将步骤2)得到的基体粉料依次进行烘干、煅烧(预烧)及冷却处理,得到第一预制基体粉料;
13.4)按摩尔比1:2:1计算称量ba(oh)2·
8h2o粉体、h3bo3粉体和cuo粉体,其中ba(oh)2·
8h2o粉体(国药沪试)的纯度为≥98.00%;h3bo3粉体(国药沪试)的纯度为≥99.80%;cuo粉体(国药沪试)的纯度为≥99.00%;
14.5)先将步骤4)称取的ba(oh)2·
8h2o粉体、h3bo3粉体和cuo粉体混合球磨形成第二基体粉料;
15.6)将步骤5)得到的第二基体粉料依次进行烘干、煅烧及冷却处理,得到预制bcb粉料;
16.7)将步骤3)得到的第一预制基体粉料进行第二次球磨并烘干后与步骤6)得到的预制bcb粉料进行混合继续球磨,依次进行球磨及烘干处理,得到预制混合干粉料;
17.8)先配制pva溶液,并将配制的pva溶液加入步骤7)得到的预制混合干粉料进行造粒,形成粉粒;之后将造好的粉粒过筛,剔除大粉粒和小粉粒;最后将过筛后得到的粉粒压制成胚体;
18.9)对步骤8)得到胚体依次进行排胶、降温后自然冷却处理、冷等静压处理及煅烧处理,得到bcb作为助烧剂的铌酸银基反铁电储能陶瓷。
19.所述的步骤2)中,具体将步骤1)称取的ag2o粉体、nb2o5粉体、srco3粉体、bi2o3粉体和hfo2粉体混合形成待球磨粉料,将待球磨粉料和磨球一起添加到球磨罐中,并向球磨罐中加入无水乙醇作为球磨介质,开启行星球磨机进行球磨处理,得到第一基体粉料;待球磨粉料、磨球、无水乙醇按质量比1:1.5:1的比例加入球磨罐中;磨球采用的是0.3g/个的氧化锆球,球磨时间为24h。
20.所述的步骤3)中,待步骤2)完成后,取出球磨罐中的第一基体粉料,然后将第一基体粉料放置于鼓风干燥箱中进行烘干处理,得到第一基体干粉料,烘干的温度控制为:90
‑
110℃;将得到的混合干粉料放入瓷舟中,并将混合干粉料在瓷舟中压实,再将瓷舟放置于管式炉中,于氧气气氛及900℃温度条件下恒温煅烧瓷舟内的基体干粉料,煅烧时间控制为6h;煅烧完成后,将瓷舟从管式炉中取出,使瓷舟自然冷却到室温(23℃
±
2℃),瓷舟内形成
第一预制基体粉料。
21.所述的步骤4)中,称取的ba(oh)2·
8h2o粉体、h3bo3粉体和cuo粉体混合形成待球磨粉料,将待球磨粉料和磨球一起添加到球磨罐中,并向球磨罐中加入去离子水作为球磨介质,开启行星球磨机进行球磨处理,得到第二基体粉料;待球磨粉料、磨球、去离子水按质量比1:1.5:1的比例加入球磨罐中;磨球采用的是0.3g/个的氧化锆球,球磨时间为24h。
22.所述的步骤6)中,待步骤5)完成后,取出球磨罐中的第二基体粉料,然后将第二基体粉料放置于鼓风干燥箱中进行烘干处理,得到第二基体干粉料;烘干的温度控制为:100℃左右;将得到的第二基体干粉料放入坩埚中,并将第二基体干粉料在坩埚中压实并盖上盖子,再将坩埚放置于马弗炉中,于大气气氛及810℃温度条件下恒温煅烧坩埚内的第二基体干粉料,煅烧时间控制为4h;煅烧完成后,将坩埚从马弗炉中取出,使坩埚自然冷却到室温,坩埚内形成预制bcb粉料。
23.所述的步骤7)中,将步骤3)得到的第一预制基体粉料倒入球磨罐中和磨球及无水乙醇进行第二次球磨,之后烘干得到预制混合粉料a;将得到的预制混合粉料a和步骤6得到的预制bcb粉料以及磨球一起放入球磨罐中进行球磨处理,并在球磨处理过程中添加无水乙醇作为球磨介质,得到预制混合粉料b;将得到的预制混合粉料b烘干,得到预制混合干粉料;
24.所述的预制混合粉料a中,第一预制基体粉料、磨球、无水乙醇按质量比1:1.5:1的比例加入球磨罐中;磨球采用的是0.3g/个的氧化锆球,球磨时间为24h;在烘干过程中采用鼓风干燥箱烘干,且烘干温度控制为:90
‑
110℃;
25.所述的预制混合粉料b中,预制混合粉料a和预制bcb粉料、磨球、无水乙醇按质量比1:1.5:1的比例加入球磨罐中,预制bcb粉料的摩尔量为预制混合粉料a摩尔量的1%;磨球采用的是0.3g/个的氧化锆球,球磨时间为24h;在烘干过程中采用鼓风干燥箱烘干,且烘干温度控制为:90
‑
110℃。
26.所述的步骤8)中,pva溶液为称取pva溶解于去离子水中,配制出质量百分比浓度为5%的pva溶液;
27.所述的步骤8)中,每克预制混合干粉料中要加入0.1ml~0.2ml的pva溶液;
28.所述的步骤8)中,过筛后得到的粉粒于150mpa的压力下单轴压压制成胚体;
29.所述的步骤8)中,筛子的规格为:平均孔径60目~100目;
30.所述的步骤8)中,胚体为横截面直径为10mm,高度0.8mm~1.0mm的圆柱型胚体(0.3g/个)。
31.所述的步骤9)中,在600℃条件下,对步骤8)得到胚体进行排胶,之后再降温至室温(23℃
±
2℃);
32.所述的步骤9)中,排胶具体的过程为:在大气气氛下,以5℃/min的速率将马弗炉升温至600℃,恒温煅烧胚体2h,之后以5℃/min的速率降温至50℃,然后冷却到室温;
33.所述的步骤9)中,将自然冷却处理后的胚体放于橡胶套中抽真空后置于冷等静压机中在300mpa的压力下进行冷等静压处理;
34.所述的步骤9)中,将冷等静压处理后的胚体放入管式炉中,在氧气气氛下,以5℃/min的速率将管式炉升温至1000℃
‑
1030℃,恒温煅烧胚体2h,即得到bcb作为助烧剂的铌酸银基反铁电储能陶瓷。
35.利用本发明选取bcb作为助烧剂的铌酸银基反铁电储能陶瓷制备方法制备得到的铌酸银基反铁电储能陶瓷其化学计量式为(1
‑
x)agnbo3
‑
x(sr
0.7
bi
0.2
)hfo3‑
y bcb为例(简称(1
‑
x)an
‑
x sbh
‑
y bcb)具体其中x=0.02~0.06;y=0.01;y为bcb与(1
‑
x)an
‑
x sbh的摩尔比,本发明在保证高储能特性的前提下,简化铌酸银基反铁电储能陶瓷的制备工艺,制备出高储能密度,高储能效率并具有良好温度稳定性的铌酸银基反铁电储能陶瓷,是铌酸银基反铁电储能陶瓷制备方法上的创新。
附图说明
36.图1为本发明铌酸银基反铁电储能陶瓷的sem图片和平均晶粒尺寸图。
37.图2为本发明铌酸银基反铁电储能陶瓷的实际密度(ρ)、理论密度(ρ
t
)和相对密度(ρ
r
)随sbh掺杂含量的变化趋势图。
38.图3(a)为本发明铌酸银基反铁电储能陶瓷的击穿场强、(b)平均晶粒尺寸和(c)带隙随sbh掺杂含量的变化趋势图。
39.图4为本发明铌酸银基反铁电储能陶瓷的(a)升温介电常数、(b)相图、(c)介电损耗和(d)电模量虚部随sbh掺杂含量的变化趋势图。
40.图5为本发明x=0.00和0.06铌酸银基反铁电储能陶瓷的o1s的xps图谱和氧空位含量随sbh掺杂含量的变化趋势图。
41.图6为本发明铌酸银基反铁电储能陶瓷的(a)电滞回线、(b)储能密度及效率在常温下随sbh掺杂含量的变化趋势图和x=0.055铌酸银基反铁电储能陶瓷的(c)储能密度及(d)效率随温度的变化趋势图。
具体实施方式
42.以下结合附图和实施例对本发明的具体实施方式作进一步详细说明。
43.实施例1
44.本发明在具体实施时,具体包括以下步骤:
45.1)先按照摩尔比计算x=0.02时各原料的质量,并分别称取ag2o粉体、nb2o5粉体、srco3粉体、bi2o3粉体和hfo2粉体;其中,ag2o粉体(国药沪试)的纯度为≥99.70%;nb2o5粉体(国药沪试)的纯度为≥99.99%;srco3粉体(国药沪试)的纯度为≥99.00%;bi2o3粉体(国药沪试);hfo2粉体(麦克林)的纯度为99.9%;
46.2)将称取的ag2o粉体、nb2o5粉体、srco3粉体、bi2o3粉体和hfo2粉体混合均匀,形成待球磨粉料,然后添加到球磨罐中,并向球磨罐中加入无水乙醇作为球磨介质,开启球磨罐进行球磨处理,得到第一基体粉料;在球磨处理过程中,待球磨粉料、磨球、无水乙醇按质量比1:1.5:1的比例加入球磨罐中,磨球采用的是0.3g/个的氧化锆球,球磨时间为24h;
47.3)取出步骤2中球磨罐中的第一基体粉料,然后将第一基体粉料放置于鼓风干燥箱中100℃进行烘干处理,得到第一基体干粉料;将第一基体干粉料放入瓷舟中并压实,将瓷舟放置于管式炉中,于氧气气氛下900℃煅烧坩埚内的第一基体干粉料,煅烧时间控制为6h;待煅烧完成后,将瓷舟从管式炉中取出,使瓷舟自然冷却到室温,瓷舟内形成第一预制基体粉料;
48.4)按摩尔比1:2:1计算称量ba(oh)2·
8h2o粉体,h3bo3粉体和cuo粉体。其中,ba
(oh)2·
8h2o粉体(国药沪试)的纯度为≥98.00%,h3bo3粉体(国药沪试)的纯度为≥99.80%,cuo粉体(国药沪试)的纯度为≥99.00%;
49.5)将称取的ba(oh)2·
8h2o粉体、h3bo3粉体和cuo粉体混合形成待球磨粉料和锆球一起添加到球磨罐中,并向球磨罐中加入去离子水作为球磨介质,开启行星球磨机进行球磨处理,得到第二基体粉料;在球磨处理过程中,待球磨粉料、磨球、去离子水按质量比1:1.5:1的比例加入球磨罐中,磨球采用的是0.3g/个的氧化锆球,球磨时间为24h;
50.6)取出步骤5中球磨罐中的第二基体粉料,然后将第二基体粉料放置于鼓风干燥箱中100℃左右进行烘干处理,得到第二基体干粉料;将第二基体干粉料放入坩埚中,并压实盖上盖子,再将坩埚放置于马弗炉中,于空气气氛中810℃恒温煅烧坩埚内的第二基体干粉料,煅烧时间控制为4h;待煅烧完成后,将坩埚从马弗炉中取出,使坩埚自然冷却到室温,坩埚内形成预制bcb粉料;
51.7)将步骤3)得到的第一预制基体粉料倒入球磨罐中和磨球及无水乙醇进行第二次球磨,之后烘干得到预制混合粉料a,第一预制基体粉料、磨球、无水乙醇按质量比1:1.5:1的比例加入球磨罐中;磨球采用的是0.3g/个的氧化锆球,球磨时间为24h;在烘干过程中采用鼓风干燥箱烘干,且烘干温度控制为:90
‑
110℃;然后将预制混合粉料a和预制bcb粉料放入球磨罐中和磨球一起进行球磨处理(预制bcb粉料的摩尔量为预制混合粉料a摩尔量的1%),并在球磨处理过程中添加无水乙醇作为球磨介质,得到预制混合粉料b;所述的预制混合粉料b中,预制混合粉料a和预制bcb粉料、磨球、无水乙醇按质量比1:1.5:1的比例加入球磨罐中;磨球采用的是0.3g/个的氧化锆球,球磨时间为24h;在烘干过程中采用鼓风干燥箱烘干,且烘干温度控制为:90
‑
110℃;
52.8)称取pva溶解于去离子水中,配制出质量百分比浓度为5%的pva溶液;将经pva溶液添加到预制混合干粉料中进行造粒处理,得到粉粒;其中,每克预制混合干粉料中要加入0.1ml的pva溶液;完成造粒处理后,将成形的粉粒过筛子,剔除其中粒径较大的粉粒和较小的粉粒;筛子的规格为:平均孔径为60目
‑
100目,取60目
‑
100目之间的粉粒进行压片;将过筛后得到的粉粒于150mpa的压力下经单轴压压制成胚体;该胚体为横截面直径为10mm,高度0.8mm~1.0mm的圆柱型胚体(0.3g/个);
53.9)于600℃条件下,对步骤8得到胚体进行排胶,排胶具体的过程为:在空气气氛下,以5℃/min的速率将马弗炉升温至600℃,恒温煅烧胚体2h,之后以5℃/min的速率降温至50℃,然后自然冷却到室温,即得到排胶后的胚体;将排胶后的胚体放入橡胶套中抽真空后置于冷静压机中在150mpa的压力下进一步致密化,将等静压后的胚体放入管式炉中,在氧气气氛下,以5℃/min的速率将马弗炉升温至1030℃,恒温煅烧胚体2h,即得到bcb作为助烧剂的铌酸银基反铁电储能陶瓷。
54.如图1所示,通过低温烧结工艺制备的(1
‑
x)an
‑
xsbh
‑
ybcb铌酸银基反铁电储能陶瓷样品晶粒尺寸均匀。随着sbh掺杂含量的增加,样品平均晶粒尺寸由x=0.00组分的5.07μm逐渐减小到x=0.06组分的2.23μm。同时,所制备的样品相对密度均高于98%(图2)。晶粒尺寸的减小同时伴随着击穿场强的提升(如图3a和b所示),进而有利于储能密度的提高。通过紫外可见吸收光谱测试(uv
‑
vis)可以发现,随着sbh掺杂含量的增加,体系的带隙也逐渐增加,由x=0.00组分的2.71ev逐渐增加到x=0.06组分的2.77ev(如图3c所示)。
55.随着sbh掺杂含量的增加,(1
‑
x)an
‑
xsbh
‑
ybcb铌酸银基反铁电储能陶瓷的相变温
度(m1‑
m2、m2‑
m3和m2‑
m3)逐渐向低温移动,如图4a和b所示。其中,当sbh掺杂含量高于0.04时,m1‑
m2相变温度已降低至
‑
150℃以下,表明室温下反铁电相的稳定性逐渐增强。同时,m2‑
m3相变峰也逐渐弥散,表明sbh掺杂增强了材料的弛豫特性,进而有利于储能效率的提高。图4c为(1
‑
x)an
‑
xsbh
‑
ybcb铌酸银基反铁电储能陶在
‑
150℃~450℃温度范围内的介电损耗(插图为室温下各组分的介电损耗)。室温下的介电损耗由x=0.00组分的0.00989减小到x=0.06组分的0.00016。图4d为(1
‑
x)an
‑
xsbh
‑
ybcb铌酸银基反铁电储能陶在400℃下的电模量虚部随sbh掺杂含量的变化趋势图。在测试频率范围内,所有组分均呈单峰特性,表明样品的电均匀性良好。
56.图5为x=0.00和0.06陶瓷的o1s xps图谱和氧空位含量随sbh掺杂含量的变化趋势图。o1s峰可以拟合为两个峰,较低结合能和较高结合能处的峰分别代表晶格氧(o
l
)和空位氧(o
v
)。随着sbh掺杂含量的增加,空位氧(o
v
)的含量逐渐降低,如图5c所示。
57.随着sbh掺杂含量的增加,平均晶粒尺寸的减小,介电损耗的降低,带隙的增加和空位氧(o
v
)含量的降低,均有利于击穿场强的增加。同时,随着室温下反铁电相的稳定性逐渐增强,(1
‑
x)an
‑
xsbh
‑
ybcb铌酸银基反铁电储能陶表现出良好的储能特性和温度稳定性,如图6所示。随着sbh含量的增加,相变场强逐渐向高场移动,同时保持了较高的最大极化强度,如图6a所示。当x=0.055时,储能密度达到6.1j/cm3,储能效率达到73%(图6b)。图6c和d为x=0.055组分在290kv/cm电场下不同温度时(25℃~120℃)的电滞回线和储能特性。x=0.055组分的储能密度和储能效率随温度的变化量分别为3.8%和1.5%,具有优异的温度稳定性。
58.本发明以bacu(b2o7)作为烧结助剂,通过简单、易于实现的工艺制备出高储能密度,高储能效率并具有良好温度稳定性的铌酸银基反铁电储能陶瓷,利用本发明制备出的铌酸银基反铁电陶瓷在智能电网、电动动力汽车以及绿色新能源技术等领域有广泛的需求,由于其无铅的环境友好特性,在未来储能电容器领域有极好的应用前景,具有良好的经济和社会效益。
再多了解一些
本文用于企业家、创业者技术爱好者查询,结果仅供参考。