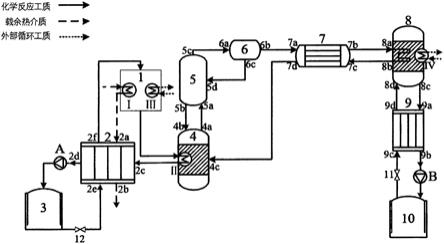
1.本发明涉及一种基于化学提质蓄热的低温余热增焓储热系统,属于储能技术领域。
背景技术:
2.当前,我国能源利用存在着利用效率低、经济效益差和生态环境压力大等问题。节能减排、降低能耗、提高能源综合利用率作为能源发展战略规划的重要内容,是解决我国能源问题的根本途径,处于优先发展的地位。
3.我国工业领域能源消耗量约占全国能源消耗总量的70%,主要工业产品单位能耗比国际先进水平高出30%左右。除了生产工业相对落后、产业结构不合理的因素外,工业余热利用率低,能源没有得到充分综合利用是造成能耗高的重要原因,我国能源利用率仅为33%左右,比发达国家低约10%,至少50%的工业耗能以各种形式的余热被直接抛弃。因此从另一个角度看,我国工业余热资源丰富,广泛存在于工业各行业生产过程中,余热资源约占其燃料消耗总能的17%
‑
67%,其中可回收率达60%,余热利用率提升空间大,节能潜力巨大。如果能设计合适的储热方案,将这一部分废热、余热的热量加以储存并利用,不仅可以提高能源的利用率,还能带来巨大的经济和环境效益。
4.储热方式有显热储热、潜热储热和化学储热,目前在储热领域,显热储热和潜热储热应用较为广泛,但是显热储热放热不恒温、储热密度小以及储热装置庞大等缺点已经限制了其进一步应用;潜热储热即相变储热,受到材料相变温度的影响较大而且技术难度大;化学储热是利用一对正逆吸/放热的化学反应,将热能以化学能的形式储存起来,储能密度明显大于显热储热和潜热储热,而且可用催化剂或者反应物对反应过程进行控制,可实现热量长期储存而几乎没有损失,因此可基于利用化学储热对热量进行储存,但化学储热和显热储热以及潜热储热类似,受到换热温差以及换热器面积的限制,在储热过程中必然伴随着热能品位的降低,导致储热效率下降,缩小了热量的应用范围,降低了能源的利用率。
技术实现要素:
5.本发明针对现有技术的不足和缺陷,提出一种基于化学提质蓄热的低温余热增焓储热系统,基于化学提质蓄热原理,将化学储热与化学提质相结合,系统依次进行中低温余热存储、化学提质以及中高温蓄热,在储热的同时提升中低温余热的品位,扩大了热能的应用范围,而且与传统的储热方式相比,具有热能密度高,热损失小,系统热效率高,经济效益好,并能实现热能品位的提升等特点。
6.本发明的技术方案如下:
7.一种基于化学提质蓄热的低温余热增焓储热系统,其特征在于:可实现中低温余热存储,并对部分已储存的中低温余热进行化学提质,最后将提质后的中高温热能存储于系统内,从而将低品位的余热转变为高品位热能并储存,所述系统包括中低温余热存储单元、化学热泵提质单元、中高温蓄热单元。
8.一种基于化学提质蓄热的低温余热增焓储热系统,其特征在于:首先,由所述中低温余热存储单元完成中低温余热存储过程;然后,由所述化学热泵提质单元完成化学提质过程;最后,由所述中高温蓄热单元完成中高温蓄热过程。
9.其中,所述中低温余热存储单元包括中低温余热化学存储装置、中低温储热装置、中低温生成物储罐、吸热反应装置和压气机,所述中低温余热化学存储装置内部填充基于化学储热原理的反应原料,该反应原料可发生正向吸热反应(其逆向反应为放热反应)。
10.其中,所述化学热泵提质单元包括吸热反应装置、精馏塔、分离装置、回热器和中高温热能化学存储装置,所述吸热反应装置内部填充基于化学储热原理的反应原料,该反应原料可在低温环境中发生正向吸热反应(在高温环境中发生逆向反应,该逆向反应为放热反应)。
11.其中,所述中高温蓄热单元,包括中高温热能化学存储装置、中高温储热装置、中高温生成物储罐和压气机,所述中高温热能化学存储装置内部填充基于化学储热原理的反应原料,该反应原料可发生正向吸热反应(其逆向反应为放热反应)。
12.其中,所述中低温余热存储单元的中低温余热化学存储装置的内部换热器出口通过管道与中低温储热装置的载余热介质热源入口连接;所述中低温余热化学存储装置的反应产物出口通过管道经吸热反应装置的内部换热器、中低温储热装置及压气机与中低温生成物储罐的入口连接;所述中低温生成物储罐的出口通过管道、阀门经中低温储热装置与中低温余热化学存储装置的反应产物入口连接。
13.其中,所述化学热泵提质单元的吸热反应装置的反应原料
‑
反应产物出口通过管道经精馏塔的反应原料
‑
反应产物通道与分离装置的反应原料
‑
反应产物入口连接:所述分离装置的反应产物出口通过管道经回热器的反应产物通道与中高温热能化学存储装置的内部反应器管道入口连接;所述中高温热能化学存储装置的内部反应器管道出口通过管道经回热器的反应原料通道与吸热反应装置的反应原料入口连接;所述分离装置的反应原料出口通过管道与精馏塔的反应原料入口连接;所述精馏塔的反应原料出口通过管道与吸热反应装置的反应原料入口连接。
14.其中,所述中高温蓄热单元的中高温热能化学存储装置的反应产物出口通过管道经中高温储热装置的反应产物通道、压气机与中高温生成物储罐的入口连接;所述中高温生成物储罐的出口通过管道、阀门经中高温储热装置的反应产物通道与中高温热能化学存储装置的反应产物入口连接。
15.一种基于化学提质蓄热的低温余热增焓储热系统,其特征在于包括储热和释热两种运行模式:
16.在储热模式下,所述中低温余热存储单元中,具有一定温度的载余热介质进入中低温余热化学存储装置的内部换热器进行换热,换热后载余热介质温度降低并进入中低温储热装置进一步释放热量,随后排至外界环境。中低温余热化学存储装置内部存储的反应原料通过内部换热器吸收来自载余热介质的热量,反应原料吸热升温,在合适的温度及压力下发生正向吸热反应,反应产物中包含有固态、气态或液态的生成物,随后根据生成物相态及密度的不同,将生成物分离,密度大的固态生成物留在中低温余热化学存储装置中;具有一定温度且密度小的气态或液态生成物在压气机的作用下进入吸热反应装置的内部换热器进行换热,换热后具有一定温度且密度小的气态或液态生成物温度降低并进入中低温
储热装置进一步释放热量,随后经压气机送入中低温生成物储罐进行储存,从而完成中低温余热存储过程。
17.在储热模式下,所述化学热泵提质单元中,吸热反应装置内部的反应原料通过内部换热器吸收来自中低温余热化学存储装置的具有一定温度且密度小的气态或液态生成物的热量,反应原料吸热升温,在合适的温度及压力下发生正向吸热反应,反应产物与部分未反应的反应原料被输送至精馏塔。在所述精馏塔中,根据反应产物和反应原料沸点的不同,将反应产物与反应原料进行分离,沸点较高的大部分反应原料留在精馏塔中,随后被排回至吸热反应装置;经分离得到的具有一定温度且沸点较低的反应产物和少量反应原料温度降低并进入分离装置。在所述分离装置中,将反应原料和反应产物进行进一步分离,得到高纯度反应产物,被分离出的反应原料回到精馏塔;高纯度反应产物进入回热器。在所述回热器中,高纯度反应产物吸热升温,随后进入中高温热能化学存储装置的内部反应器管道。在所述中高温热能化学存储装置的内部反应器管道中,高纯度反应产物在合适的温度及压力下发生逆向放热反应,放出的热量被中高温热能化学存储装置的内部反应器管道外部填充的反应原料吸收,同时逆向放热反应生成的具有一定温度的反应原料以及未反应的反应产物排回至回热器。在所述回热器中,具有一定温度的反应原料以及未反应的反应产物与来自分离装置的高纯度反应产物进行换热,具有一定温度的反应原料以及未反应的反应产物放热降温并排回至吸热反应装置,从而完成化学提质过程。
18.在储热模式下,所述中高温蓄热单元中,中高温热能化学存储装置的内部反应器管道外部填充的反应原料吸收热量后升温,在合适的温度及压力下发生正向吸热反应,反应产物中包含固态、气态或液态的生产物,随后根据生成物相态及密度的不同,将生成物分离,密度大的固态生成物留在中高温热能化学存储装置中;具有一定温度且密度小的气态或液态的生成物在压气机的作用下进入中高温储热装置进行换热,换热后具有一定温度且密度小的气态或液态生成物温度降低并经压气机送入中高温生成物储罐进行储存,从而完成中高温蓄热过程。
19.在释热模式下,所述中低温余热存储单元中,中低温生成物储罐中之前储存的气态或液态的生成物释放并进入中低温储热装置进行换热,被预热至一定温度后进入中低温余热化学存储装置,在合适的温度及压力下与中低温余热化学存储装置中原有的固态生成物发生逆向放热反应,外部循环工质通过中低温余热化学存储装置的内部换热器吸收化学反应放出的热量,然后用于其他工业生产或日常生活用途;同时,所述中高温蓄热单元中,中高温生成物储罐中之前储存的气态或液态的生成物释放并进入中高温储热装置进行换热,被预热至一定温度后进入中高温热能化学存储装置,在合适的温度及压力下与中高温热能化学存储装置中原有的固态生成物发生逆向放热反应,外部循环工质通过中高温热能化学存储装置的内部换热器吸收化学反应放出的热量,然后用于其他工业生产或日常生活用途。
20.本发明具有以下优点及突出性技术效果:
21.1.本发明基于化学储热原理,将工业生产及日常生活中的低品位余热存储于一种基于化学提质蓄热的低温余热增焓储热系统,储热密度明显高于显热储热和潜热储热,而且可以实现热量长时间储存而几乎没有损失,储热效率高。
22.2.本发明基于化学提质原理,对部分已储存的低品位余热进行提质,热能品位得
到提高,并将提质后的中高温热能进行储存,扩大了热能的应用范围。
23.3.本发明基于化学提质蓄热原理,将化学储热与化学提质相结合,系统依次进行中低温余热存储、化学提质以及中高温蓄热,实现了中低温余热的中低温储存、化学提质以及中高温储存和释放,在储热的同时提升了中低温余热的品位,扩大了热能的应用范围,并且系统储热密度高、热损失小、储热效率高、经济效益好。
附图说明
24.为了更清楚地说明本发明实施例或现有技术中的技术方案,下面对实施例中所需要使用的附图作简单地介绍,显而易见地,下面描述中的附图仅仅是本发明的一些实施例,对于本领域的普通技术人员来讲,在不付出创造性劳动性的前提下,还可以根据这些附图获得其他的附图。
25.附图1为本发明的提供的一种基于化学提质蓄热的低温余热增焓储热系统的原理结构示意图。
26.图中各标号清单为:1
‑
中低温余热化学存储装置;2
‑
中低温储热装置;3
‑
中低温生成物储罐;4
‑
吸热反应装置;5
‑
精馏塔;6
‑
分离装置;7
‑
回热器;8
‑
中高温热能化学存储装置; 9
‑
中高温储热装置;10
‑
中高温生成物储罐;11,12
‑
阀门;i,ii,iii,iv
‑
换热器;a,b
‑
压气机。
具体实施方式
27.下面结合附图对本发明的原理和具体实施作进一步的说明。
28.附图为本发明提供的一种基于化学提质蓄热的低温余热增焓储热系统的原理结构示意图。所述系统组成实现及连接方式如下:所述系统包括中低温余热存储单元、化学热泵提质单元和中高温蓄热单元。
29.其中,所述中低温余热存储单元,包括中低温余热化学存储装置1、中低温储热装置2、中低温生成物储罐3和吸热反应装置4和压气机a,所述中低温余热化学存储装置1内部填充基于化学储热原理的反应原料,该反应原料可发生正向吸热反应(其逆向反应为放热反应)。
30.其中,所述化学热泵提质单元,包括吸热反应装置4、精馏塔5、分离装置6、回热器 7和中高温热能化学存储装置8,所述吸热反应装置4内部填充基于化学储热原理的反应原料,该反应原料可在低温环境中发生正向吸热反应(在高温环境中发生逆向反应,该逆向反应为放热反应)。
31.其中,所述中高温蓄热单元,包括中高温热能化学存储装置8、中高温储热装置9、中高温生成物储罐10和压气机b,所述中高温热能化学存储装置8内部填充基于化学储热原理的反应原料,该反应原料可发生正向吸热反应(其逆向反应为放热反应)。
32.其中,所述中低温余热存储单元的中低温余热化学存储装置1的内部换热器i的出口通过管道与中低温储热装置2的载余热介质热源入口2a连接;所述中低温余热化学存储装置 1的反应产物出口通过管道与吸热反应装置4的内部换热器ii的入口连接;所述吸热反应装置4的内部换热器ii的出口通过管道与中低温储热装置2的反应产物热源入口2c连接;所述中低温储热装置2的反应产物热源出口2d通过管道与压气机a的入口连接;所述压
气机 a的出口通过管道与中低温生成物储罐3的入口连接;所述中低温生成物储罐3的出口通过管道、阀门12与中低温储热装置2的反应产物冷源入口2e连接;所述中低温储热装置2的反应产物冷源出口2f通过管道与中低温余热化学存储装置1的反应产物入口连接。
33.其中,所述化学热泵提质单元的吸热反应装置4的反应原料
‑
反应产物出口4a通过管道与精馏塔5的反应原料
‑
反应产物入口5a连接;所述精馏塔5的反应原料出口5b通过管道与吸热反应装置4的反应原料入口4b连接,精馏塔5的反应原料
‑
反应产物出口5c通过管道与分离装置6的反应原料
‑
反应产物入口6a连接;所述分离装置6的反应产物出口6b通过管道与回热器7的反应产物入口7a连接,分离装置6的反应原料出口6c通过管道与精馏塔5 的反应原料入口5d连接;所述回热器7的反应原料出口7d通过管道与吸热反应装置4的反应原料入口4c连接,回热器7的反应产物出口7b通过管道与中高温热能化学存储装置8的内部反应器管道入口8a连接;所述中高温热能化学存储装置8的内部反应器管道出口8b通过管道与回热器7的反应原料入口7c连接。
34.其中,所述中高温蓄热单元的中高温热能化学存储装置8的反应产物出口8c通过管道与中高温储热装置9的热源入口9a连接;所述中高温储热装置9的热源出口9b通过管道与压气机b的入口连接;所述压气机b的出口通过管道与中高温生成物储罐10的入口连接;所述中高温生成物储罐10的出口通过管道、阀门11与中高温储热装置9的冷源入口9c连接;所述中高温储热装置9的冷源出口9d通过管道与中高温热能化学存储装置8的反应产物入口8d连接。
35.一种基于化学提质蓄热的低温余热增焓储热系统,特征在于包括储热和释热两种运行模式:
36.在储热模式下,所述中低温余热存储单元中,110℃
‑
120℃的载余热介质(如水、烟气等)进入中低温余热化学存储装置1的内部换热器i进行换热,换热后载余热介质温度降低并进入中低温储热装置2中进一步释放热量,随后排至外界环境。中低温余热化学存储装置 1内部存储的化学储热介质(储氢合金naalh4)通过内部换热器i吸收来自载余热介质的热量,储氢合金naalh4在105℃左右的温度下发生正向吸热分解反应,反应公式为:δh=37kj/mol反应生成105℃左右的氢气,随后氢气在压气机a的作用下进入吸热反应装置4的内部换热器ii进行换热,换热后氢气温度降低并进入中低温储热装置2进一步释放热量,随后经压气机a送入中低温生成物储罐3进行储存,从而完成中低温余热存储过程。
37.在储热模式下,所述化学热泵提质单元中,吸热反应装置4中的化学储热介质(液态异丙醇)通过内部换热器ii吸收来自中低温余热化学存储装置1的105℃左右的氢气的热量,液态异丙醇吸热升温蒸发,在90℃左右的温度下发生正向吸热分解反应,催化剂为zno/cuo 复合催化剂,反应公式为:(ch3)2choh(l)
→
(ch3)2choh(g) δh=45.4kj/mol(ch3)2choh(g)
→
(ch3)2co(g) h2(g) δh=55.0kj/mol反应生成90℃左右的丙酮和氢气,随后,丙酮、氢气的混合气体以及部分未反应的气态异丙醇进入精馏塔5。在所述精馏塔5中,根据丙酮、氢气的混合气体和气态异丙醇沸点的不同,将大部分气态异丙醇冷凝液化从而与丙酮、氢气的混合气体进行分离,经冷凝液化
得到的液态异丙醇随后被排回至吸热反应装置4;经分离得到的氢气、丙酮的混合气体以及少量未被冷凝液化的气态异丙醇温度降至80℃左右并进入分离装置6。在所述分离装置6中,剩余气态异丙醇被分离并排回至精馏塔5;同时得到高纯度丙酮、氢气混合气体,随后,高纯度丙酮、氢气混合气体进入回热器7。在所述回热器7中,高纯度丙酮、氢气混合气体吸收热量,升温至200℃左右,随后,进入中高温热能化学存储装置8的内部反应器管道。所述中高温热能化学存储装置8的内部反应器管道中填充固体催化剂(雷尼镍),高纯度丙酮、氢气混合气体通过固体催化剂(雷尼镍)催化,在200℃的温度下发生逆向放热化合反应,反应生成 250℃左右的气态异丙醇,反应公式为:(ch3)2co(g) h2(g)
→
(ch3)2choh(g) δh=
‑
55.0kj/mol反应放出的热量被中高温热能化学存储装置8的内部反应器管道外部填充的反应原料(储氢合金mg2nih4)吸收,随后气态异丙醇和未反应的氢气、丙酮混合气体排回至回热器7。在所述回热器7中,气态异丙醇和未反应的氢气、丙酮与来自分离装置6的高纯度丙酮、氢气混合气体进行换热,换热后气态异丙醇和未反应的氢气、丙酮混合气体温度降至90℃左右并排回至吸热反应装置4,从而完成化学提质过程。
38.在储热模式下,所述中高温蓄热单元中,中高温热能化学存储装置8的内部反应器管道外部填充的反应原料(储氢合金mg2nih4)吸收热量后逐渐升温,在240℃的温度下发生正向吸热分解反应,反应公式为:mg2nih4(s)
→
mg2ni(s) 2h2(g) δh=65kj/mol反应生成240℃左右的氢气,随后氢气在压气机b的作用下进入中高温储热装置9进行换热,换热后氢气温度降低并经压气机b送入中高温生成物储罐10进行储存,从而完成中高温蓄热过程。
39.在释热模式下,所述中低温余热存储单元中,中低温生成物储罐3中之前储存的氢气释放并进入中低温储热装置2进行换热,换热后氢气被预热至95℃左右并进入中低温余热化学存储装置1,在90℃的温度下与其中原有的固态生成物na3alh6、al发生逆向化合放热反应,反应公式为:δh=
‑
37kj/mol外部循环工质通过中低温余热化学存储装置1的内部换热器iii吸收化学反应放出的热量,然后用于其他工业生产或日常生活用途;所述中高温蓄热单元中,中高温生成物储罐10中之前储存的氢气释放并进入中高温储热装置9进行换热,换热后氢气被预热至220℃左右并进入中高温热能化学存储装置8,在210℃的温度下与其中原有的固态生成物mg2ni发生逆向化合放热反应,反应公式为:mg2ni(s) 2h2(g)
→
mg2nih4(s) δh=
‑
65kj/mol外部循环工质通过中高温热能化学存储装置8的内部换热器iv吸收化学反应放出的热量,然后用于其他工业生产或日常生活用途。
40.200℃左右的余热可用于工业生产中的干燥物料、制冷、发电等,也可用于生活中采暖等,90℃左右的余热可用于生活用水的加热。
41.最后说明的是,以上实施例只是用于帮助理解本发明的方法及其核心思想;同时,对于本领域的一般技术人员,依据本发明的思想,在具体实施方案及应用范围上均会有改
变之处。综上所述,本发明说明书内容不应理解为对本发明的限制。
再多了解一些
本文用于企业家、创业者技术爱好者查询,结果仅供参考。