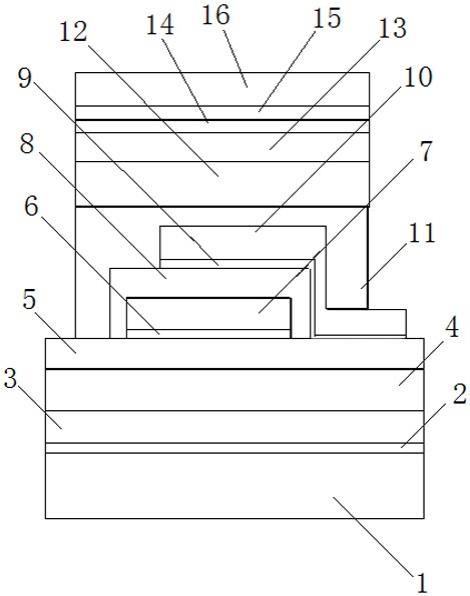
1.本实用新型涉及一种基于金属基底的嵌入式压电传感器结构,属于压电传感器技术领域。
背景技术:
2.随着工业互联网及智能制造的产业升级,制造过程实时监控已经变得越来越重要,一方面不仅可以通过制造过程中关键工艺参数的获取来改进产品质量、提升生产效率,同时还可以提前发现问题并及时进行干预从而避免恶性事故的发生。力作为重要的工艺参数,在过程监控过程中起着十分重要的作用。人们尝试使用压电传感器对力进行监测。
3.但是,常规基于硅基底的压电传感器由于基底材料的脆性和不耐高温等缺点,很难应用到高温、高压、大应变以及腐蚀性的场合。同时为了应对外界环境中的刮擦、磨损等破坏,还需对传感器进行防护,通常的办法是采用物理气相沉积或化学气相沉积等工艺在传感器上淀积一层防护层。然而基于工艺的限制,淀积的防护层很薄,防护强度有限,想要淀积具有一定厚度和足够强度的防护层需要花费大量的时间和成本。
技术实现要素:
4.为了克服上述现有技术的不足,本实用新型提供一种基于金属基底的嵌入式压电传感器。
5.为了实现上述技术目的,本实用新型采用的技术方案是:一种基于金属基底的嵌入式压电传感器,在金属基底层上设置粘接层,在粘接层上设置第一绝缘层,在第一绝缘层上依次设置第二绝缘层、第三绝缘层,在第三绝缘层上设置面积小于第三绝缘层的下电极粘接层,下电极层设置在下电极粘接层上,在下电极层上设置压电层,压电层底部与第三绝缘层连接,并覆盖除下电极层焊盘之外的部分,在压电层上设置上电极粘接层,上电极粘接层上设置上电极层,在上电极层上设置上电极绝缘层,上电极层的焊盘和下电极层的焊盘均位于第三绝缘层上,上电极绝缘层底部与第三绝缘层连接,覆盖上电极层、压电层和下电极层,上电极层和下电极层的焊盘除外,在上电极绝缘层上依次设置第四绝缘层、第五绝缘层、上粘接层、种子层、封装金属层。
6.进一步的,所述粘接层为一层厚5~100nm的金属钛或铬层;所述下电极粘接层为一层厚5~100 nm的金属钛或铬层,下电极层为一层厚50~500nm的金层;所述上粘接层为一层厚5~100nm的金属钛或铬层,上电极层为一层厚50~500nm的金层,上电极层的面积小于压电层的面积。
7.进一步的,所述第一绝缘层为一层厚0.2~5um的氧化铝层;所述第二绝缘层为一层厚10~500 nm的氧化铝层,或一层厚0.5~5 um的氮化硅层;所述第三绝缘层为一层厚0.2~5 um的氧化铝层。
8.进一步的,所述压电层为一层厚500~1000纳米的氮化铝层,压电层面积大于下电极层,覆盖住除下电极层焊盘之外的部分。
9.进一步的,所述上电极绝缘层为一层厚0.5~5 um的氧化铝层。
10.进一步的,所述第四绝缘层为一层厚1~5 um的氮化硅绝缘层或一层厚10~500 nm的氧化铝层;所述第五绝缘层为一层厚0.5~5 um的氧化铝层。
11.进一步的,所述上粘接层为一层厚5~100 nm的金属钛或铬层,所述种子层为一层厚10~500 nm的镍层,种子层为电镀工艺的种子层,在种子层上,通过电镀沉积厚度5~5000 um封装金属层,完成传感器的嵌入式封装。
12.本实用新型的有益技术效果是:
13.1、常规基于硅基底的压电传感器由于基底材料的脆性和不耐高温等缺点,很难应用到高温、高压、大应变以及腐蚀性的场合,本实用新型将金属基底的传感器封装到金属里面形成的嵌入式结构,使得传感器得到了完全的保护,从而使其能够用于较为恶劣的环境中;
14.2、本实用新型的防护层更厚,强度更高,防护效果更好,同时能充分应对外界环境中的刮擦、磨损等破坏;
15.3、实现嵌入式封装所采用的工艺简单,时间短、成本低。
附图说明
16.下面结合附图对本实用新型进一步说明。
17.图1为本实用新型的结构示意图;
18.图2为本实用新型的俯视示意图。
19.图中:1、金属基底层,2、粘接层,3、第一绝缘层,4、第二绝缘层,5、第三绝缘层,6、下电极粘接层,7、下电极层,8、压电层,9、上电极粘接层,10、上电极层,11、上电极绝缘层,12、第四绝缘层,13、第五绝缘层,14、上粘接层,15、种子层,16、封装金属层。
具体实施方式
20.如图1、2所示,一种基于金属基底的嵌入式压电传感器,在金属基底层1上设置粘接层2,在粘接层2上设置第一绝缘层3,在第一绝缘层3上依次设置第二绝缘层4、第三绝缘层5,在第三绝缘层5上设置面积小于第三绝缘层的下电极粘接层6,下电极层7设置在下电极粘接层6上,在下电极层7上设置压电层8,压电层8底部与第三绝缘层5连接,并覆盖除下电极层焊盘之外的部分,在压电层8上设置上电极粘接层9,上电极粘接层9上设置上电极层10,在上电极层10上设置上电极绝缘层11,上电极层10的焊盘和下电极层7的焊盘均位于第三绝缘层5上,上电极绝缘层11底部与第三绝缘层5连接,覆盖上电极层10、压电层8和下电极层7,上电极层10和下电极层7的焊盘除外,在上电极绝缘层11上依次设置第四绝缘层12、第五绝缘层13、上粘接层14、种子层15、封装金属层16。
21.所述基于金属基底的嵌入式压电传感器,其制备方法,步骤如下:
22.将金属基底层进行清洗(丙酮、异丙醇和去离子水)、氮气吹干,准备好金属基底;
23.通过溅射(sputtering)工艺在金属基底上电极5
‑
100nm的钛或者铬层,用于与后续的绝缘层进行粘接;
24.通过电子束蒸发工艺(e
‑
beam evaporation)在金属基底上淀积一层0.2~5微米(um)的氧化铝(al2o3)绝缘层;
25.通过原子层堆积工艺(ald)在上步淀积的氧化铝绝缘层上淀积一层10~500纳米(nm)的氧化铝绝缘层,或者以等离子增强物理气相沉积(pecvd)再淀积一层0.5~5微米(um)的氮化硅(si3n4),用于覆盖通过电子束蒸发工艺(e
‑
beam evaporation)淀积的氧化铝绝缘层中存在的针孔;
26.通过电子束蒸发工艺再在原子层堆积工艺制备的氧化铝绝缘层上或者在等离子增强物理气相沉积制备的氮化硅绝缘层上再淀积一层0.2~5 um的氧化铝绝缘层;
27.通过光刻、电子束蒸发以及剥离工艺,在氧化铝绝缘层上淀积一层5~100 nm的金属钛(ti)及50~500 nm的下金(au)电极层,其中钛层用于提高绝缘层与金电极之间的粘接性;
28.通过光刻,等离子辅助物理气相沉积(papvd)原理的直流反应溅射以及剥离工艺,在下金电极上淀积一层500~1000纳米的氮化铝,覆盖住下金电极(氮化铝面积大于下电极,但电极的焊盘应裸露出来);
29.通过光刻、电子束蒸发以及剥离工艺,在氮化铝上淀积一层5~100 nm的金属钛及50~500 nm的上金电极层,其中钛层用于提高氮化铝压电层与金电极之间的粘接性;上金电极覆盖范围小于氮化铝覆盖范围;
30.借助金属掩膜版,通过电子束蒸发工艺在除传感器电极焊盘外的区域上,淀积一层0.5~5 um的氧化铝绝缘层;
31.借助金属掩膜版,通过等离子增强化学气相淀积工艺(pecvd)在氧化铝绝缘层上淀积一层1~5 um的氮化硅绝缘层;或者通过原子层堆积工艺(ald)在上步淀积的氧化铝绝缘层上淀积一层10~500 nm的氧化铝绝缘层;(传感器电极的焊盘应该裸露出来,不被氮化硅/氧化铝绝缘层覆盖)
32.借助金属掩膜版,通过电子束蒸发工艺在氮化硅绝缘层/氧化铝绝缘层上淀积一层0.5~5 um的氧化铝绝缘层(传感器电极的焊盘应该裸露出来,不被氧化铝绝缘层覆盖);
33.通过溅射(sputtering)工艺在氧化铝绝缘层上先后沉积5~100 nm的钛层和10~500 nm的镍层(ni),其中钛层起到绝缘层与金属镍层(ni)之间的粘结作用,镍层(ni)是作为电镀工艺的种子层;(传感器电极的焊盘应该裸露出来,不被溅射金属层覆盖);然后通过电镀工艺沉积金属层,如镍、铜、镍钴等,厚度:5~5000 um,完成传感器的嵌入式封装。(传感器电极的焊盘应该裸露出来,不被电镀金属层覆盖)。
34.本实用新型与现有技术相比:
35.1、常规基于硅基底的压电传感器由于基底材料的脆性和不耐高温等缺点,很难应用到高温、高压、大应变以及腐蚀性的场合,本实用新型将金属基底的传感器封装到金属里面形成的嵌入式结构,使得传感器得到了完全的保护,从而使其能够用于较为恶劣的环境中;
36.2、本实用新型的防护层更厚,强度更高,防护效果更好,同时能充分应对外界环境中的刮擦、磨损等破坏;
37.3、实现嵌入式封装所采用的工艺简单,时间短、成本低,然而基于工艺的限制,淀积的防护层很薄,防护强度有限,想要淀积具有一定厚度和足够强度的防护层需要花费大量的时间和成本。
38.上述实施例仅仅作为对本实用新型技术方案的解释,并不能作为对本实用新型技
术方案的限制,凡是在本实用新型基础上的简单改进,均属于本实用新型的保护范围。
再多了解一些
本文用于企业家、创业者技术爱好者查询,结果仅供参考。