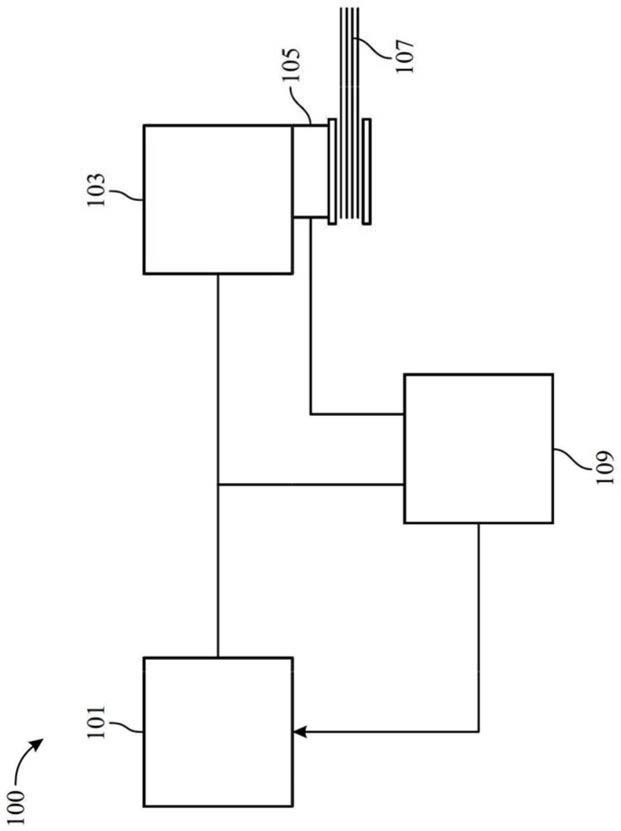
1.本发明涉及一种用于无损检测超声波焊接质量的方法、一种测量装置和一种超声波焊接设备。
背景技术:
2.在超声波焊接中,焊接质量由微观表面决定,在该微观表面中,由于焊接而在待焊接部件之间实现了材料结合连接。材料结合连接的形成无法量化。如果不对焊接进行破坏性试验,也无法确定是否存在材料结合连接,在所述破坏性试验中,将焊接成员分开所需的最大断裂力用作焊接质量的标准。这种类型的随机破坏性试验在生产中在统计学过程控制的范围内用作质量保证。由于此类随机样本的批量通常较小,因此无法以统计方式正确地实施过程控制。通常,定期并且在各种事件(例如班次变更或更换工装)之后进行例如5个样本的破坏性试验,所述破坏性实验的断裂力必须都在通常任意确定的控制极限之上。
3.在当前设备中,仅测量焊接时间作为监测标准。通过示教,在给定的焊接参数的情况下设定额定时间不得超过确定数值。
4.焊接设备产生可靠的高质量焊接的能力会受到多种影响。振荡系统的部件(例如压电致动器)可能会出现缓慢的磨损现象,在所述磨损现象中,不清楚的是,在统计学过程控制的范围中通过断裂测试使这种质量下降变得可见之前,该磨损已经损害了个别焊接的焊接质量多久了。另外,也无法从断裂测试推断出质量下降的原因。因此,在生产中无法确定,在得出不利结果的断裂测试之前的焊接是否已经存在缺陷。在具有后续加工工艺的生产线中,无法分拣出且在某些情况下无法找到这些潜在的有缺陷的焊接。
5.装备错误也会影响质量。由于日产量的小批量,设备经常需要更换工装。由此,通常有相当大的时间压力。尽管更换工装过程后通过规定的断裂测试可以注意到焊接质量缺陷,但质量下降的原因尚不清楚。
技术实现要素:
6.本发明要解决的技术问题是提供一种用于检测超声波焊接质量的改进概念。
7.对表征焊接工艺中振荡过程的参量进行测量和评价,可以对焊接过程进行全面而有效的评估。
8.根据第一方面,该技术问题通过一种用于无损检测通过焊接过程进行的超声波焊接质量的方法解决,包括
9.在一时间段内采集与时间相关的测量参量,其中所述测量参量用于表征待检测的焊接工艺的机械的或电的振荡特性;
10.通过傅立叶分析的应用,评价所采集的与时间相关的测量参量的测量参量曲线;
11.将评价结果与参考值进行比较,以便检测超声波焊接的质量。
12.通过傅立叶分析的应用,评价所采集的与时间相关的测量参量。将评价结果与参考值进行比较,以检测焊接质量。参考值可以看作是额定值,即参考值规定了评价结果应该
如何。与时间相关的测量参量是与焊接工艺相关的可测量物理参量。超声波焊接的质量可以是超声波焊接的品质。这意味着超声波焊接的质量描述了实施超声波焊接的安全性或良好程度及其耐用性。
13.焊接设备可以包括超声波发生器,该超声波发生器被设置为产生用于产生超声波振荡的控制信号。控制信号可以是能够激励压电致动器进行机械振动的电信号。超声波焊头可以与压电致动器机械耦合,以便将压电致动器的超声波振荡以机械方式传递到工件。
14.与时间相关的测量参量可以是与时间相关的变量。由于通常在不同条件下所实施的焊接在整个焊接过程中其平均值或单个傅立叶变换没有显著差异,而仅在其曲线形状上有显著差异,因此如果随时间记录物理参量,则有利的是,依据时间变化采集测量参量。
15.傅立叶分析的应用可以包括应用短期傅立叶分析,从中能够确定振幅、频率或其他参量的时间相关性。短期傅立叶分析的各个窗口部分可以应用合适的窗口函数,特别是在计算幅度时应用平顶窗口,或者在计算频率或相位时应用矩形窗口。也可以使用补零和插值,特别是在应用带有小窗口参量的短期傅立叶分析中计算频率时。
16.振荡分析的目的是实现100%的过程控制,用于可靠地分类和分拣出不良焊接。因此,应用是检测与焊接强度相关的所有限制。可以根据降低的工作频率将各种类型的污染物(油脂、护手霜等)与“良好”焊接区分开来,这些污染物会降低焊接部件之间的摩擦力。表面特性(粗糙度、氧化层)对工作频率的调控也有同样的影响。
17.由于批次变更后焊接的断裂强度会部分地显著改变,这也应反映在振荡分析中。实验表明,由于阻抗增加和有功功率降低并因而无功功率升高,强度下降变得明显。不同的工件,尤其是不同的电缆结构,例如具有高度柔性的绞线或标准绞线,会对许多物理参量的时间进程产生影响。这表明对整个时间进程的分析是有利的。同样,影响绞线刚度的其他属性,例如剥线长度,也可以在振荡分析中看到。然而,导线长度并未在测量数据中体现出来,因为待焊接部件尺寸的影响仅在可能形成驻波的刚体的情况下起作用。绞合电缆对此有太多衰减。然而,在接触部件的情况下,如果它们在固有频率方面具有关键设计,则可能会发生共振效应。通过振荡分析,可确定在此类共振情况下是否因应力过大而出现裂纹。
18.作为除分拣不良焊接之外的其它应用,可以使用振荡分析来优化参数。可以优化以获得最大的断裂力。利用振动分析,可用于有效优化特定的电的或机械的标称曲线。
19.此外,振荡分析还为查找焊接质量差的原因提供支持。如果仅存在较低的断裂力,则无法说明原因。目视检查可以区分欠焊和过焊。另一方面,振荡分析使焊接工艺的完整动力学可见。
20.本发明的优点在于,除了偏转之外,还可以测量其他测量参量,特别是电流和电压,由此可以计算相位关系和由此导出的参量,例如阻抗和功率,且所有这些参量可以计算为整个焊接过程中的时间相关的参量,而不是每个焊接只计算两个标量数值。偏转尤其可以通过涡流传感器来测量。通过振荡分析进行100%的过程控制,磨损迹象在振动动力学变化中变得明显。振荡分析可以实现故障定位,从而提高更换工装过程中的效率。
21.在一个实施例中,所述时间段对应于焊接工艺的持续时间。
22.可以在整个焊接时间(即焊接工艺的持续时间)内测量所有测量参数。在多阶段焊接工艺的情况下,因此也可以对各个阶段进行评估。在这些情况下,可以获得额外的信息,因为对于振荡设备在各个阶段期间在待焊接区域存在不同的物理条件,因此对于振荡设备
适用不同的边界条件。例如,焊接细分为预声、压实声、焊接声和后声。特别是在铝焊接工艺的情况下,所有四个阶段都经过,间隔清晰,没有声音激励;在铜焊接工艺的情况下,预声和焊接声就足够了。
23.在一个实施方式中,测量参量用于表征焊接工艺的机械的振荡特性并且包括超声波焊头的剪切力和/或偏转。
24.偏转的测量可以在设备中的不同点进行。尽可能靠近超声波焊头的耦合表面的测量点可以直接得出关于待焊接区域中的运动的结论。出于空间原因,特别是为了避免干扰工人,还可以测量与超声波焊头的耦合表面对置的端部,并且可以得出关于耦合表面上的运动的结论,特别是在线性焊接期间。
25.能够以各种测量方法进行偏转的测量。偏转可以对应于速度。例如,可以用这样的装置测量偏转,在该装置中,涡流传感器尽可能靠近超声波焊头表面,该表面与运动方向正交并因此与耦合表面成直角。测量点应尽可能靠近耦合表面,以便在待焊接区域中获得运动的最准确测量。涡流传感器特别适合这项任务,因为它可以相对容易地被附接到振荡系统的不同点。与如激光测振仪等,以激光光学系统进行的测量相比,对工人的限制可能更少。
26.如果已知超声波焊头的法向力,则可以在固定触点上以多个力传感器来评估剪切力。
27.在一个实施方式中,测量参量用于表征焊接工艺的电振荡特性是表征性的并且包括用于驱动压电致动器的电流和/或用于驱动压电致动器的电压。
28.电测量参量的测量并不复杂,且提供了精确的结果,并对制造过程的干扰很小。
29.电测量参量的测量可以用高压测头和/或电流探针在发生器和压电致动器之间的电流路径中进行,特别是在高频电缆上。测量也可以直接集成到超声波发生器中,在那里同样也能够在控制回路的范围内在输出级上实施这一测量。
30.由此,能够以振荡测量在振荡系统的一端(尤其是在压电致动器上)测量电流和电压作为测量参量和/或在振荡系统的另一端(尤其是在超声波焊头的耦合表面上)测量与速度测量对应的剪切力和偏转作为测量参量,并且以傅里叶分析方法进行评价。尤其是能够在整个焊接工艺中对测量参量进行测量。可以测量上述测量参量中的一个。如果测量了多个上述测量参量,则可以增加分析的效力。电的测量可以容易地实施。机械测量可以提供有关待焊接区域中发生的振荡情况的信息。
31.在一个实施方式中,采集测量参量包括采集差异参量和采集流量参量。
32.在一个实施方式中,评价包括计算在两个所采集的测量参量之间的相位关系、用于操作超声波焊头的工作频率、所采集的测量参量的相位幅度和/或用于操作超声波焊头的工作频率的幅度。
33.此外,在一个实施方式中,评价包括从两个所采集的测量参量计算出的相位关系导出功率参量,特别是视在功率、有功功率、无功功率和/或阻抗参量,特别是视在阻抗、电阻、电抗。
34.差异参量和流量参量的测量可以以电气方式进行,特别是通过电压的测量和/或电流电流的测量,或以机械方式进行,特别是通过力的测量和/或速度的测量。
35.从相关的差异参量和流量参量的测量值,特别是电压和电流,可以推导出四个参
量:它们的相位关系、工作频率和相应的振幅,特别对于所有四个测量参量振幅的曲线是相同的,因此它们可以从所有测量参量中被导出。从这四个基本参量中,可以导出功率参量,特别是视在功率、有功功率、无功功率和阻抗参量,特别是导出视在阻抗、电阻、电抗。
36.在一个实施方式中,所述评价基于所采集的测量参量的基波和/或谐波。
37.上述测量参量不仅可以用于基波计算,还可以用于谐波计算,即原则上针对在给定采样率下仍然可以计算的每个谐波。已经表明,在高次谐波处可以使效果更加明显。
38.在一个实施方式中,所述比较包括比较工作频率和/或用于驱动压电致动器的电流和电压之间的相位差。
39.在一个实施方式中,所述采集在参考值确定之前并且基于测试系列和/或基于自学习算法,特别是利用神经网络。
40.通过这种方式,可以实现质量监测。如果可以通过试验证明所确定的待焊接部件或焊接的质量缺陷与根据上述方法确定的、所分析参量的对应时间进程之间存在联系,则可以确定标准,根据该标准在生产中,分拣出与不良焊接具有足够相似的表征曲线的焊接。如果没有发现充分区别不良焊接的时间进程与良好焊接的时间进程的标准,则可以通过记录焊接时间,以与现有焊接监控类似的手段来实现质量监测。与此类似,其中示教了标称焊接时间并且后续焊接仅允许偏离一定量,此处也可以通过与示教的标称曲线进行比较来实现监测。可以想到的是由示教所确定的频带,在此频带内,焊接具有足够的断裂力并因此被归类为“良好”,并且后续焊接的曲线必须位于其中以便本身被归类为“良好”。如果曲线位于此频带内,则可以通过统计上的确定性得出结论,这些焊接也具有与在示教阶段进行破坏性试验的焊接相同的质量。
41.某些物理参量非常适合作为区分良好焊接和不良焊接的标准。这些参量中包括在电流和电压之间的相位差和工作频率,以及由此得出的电抗和有功功率,以及电流测量的失真系数。特别是,可以确定减少待焊接部件之间摩擦的污染,例如油脂或护手霜,从而导致材料结合连接不充分,即焊接具有低的断裂力,导致整个焊接工艺的工作频率降低。对于铝焊接,这适用于压实声和焊接声。在受控地施加油脂或护手霜的情况下,频率的降低已经具有统计学意义,并且在短的调控时间后在整个焊接工艺上约为50hz(各个随机样本的平均值到平均值),在施加大量污染的情况下高达100hz。
42.通过质量监控,可以将焊接适当地分类为良好焊接和不良焊接,以便尽可能可靠地识别质量缺陷。由于提供破坏性试验的最大断裂力目前是形成材料结合连接的唯一质量标准,通过振荡分析的分类应尽可能与通过破坏性试验的分类一致。断裂力低于控制极限的焊接应通过振荡分析尽可能可靠地被检测为不良焊接。
43.可以从一个或多个物理测量参量的时间进程中分离出标准,所述标准作为二元分类器具有尽可能最少数量的分类错误,特别是高灵敏度或选择度即避免第2类错误的高概率,即将不良焊接归类为良好焊接。除了高的灵敏度,也值得努力的是高的选择性即避免第1类错误,即将良好焊接归类为不良焊接。
44.选择性可以通过给定的限度、显著性水平来控制。由于灵敏度和选择性不能同时最大化,对于足够的选择度,平均值的最大可能差异和要分类的分布的低离散度是有利的。也可以进一步提高选择度,例如通过在示教时增加随机样本数量,因为由此会降低标准误差。但是,在生产过程中,目标是保持用于示教的样本数量尽可能少。
45.例如,这些先决条件在针对工作频率以受控方式涂有护手霜的接触部件的测试中给出。平均值与相应的标准偏差之间的差异导致了允许可靠的分类的高选择度,而不会表现出干扰生产的低选择性,即不会由于被错误地分类为不良焊接导致频繁的废品。
46.作为所提出方法的扩展,也可以通过自学习算法的模式识别来实现分类器。因此,可以通过神经网络以在振荡分析所分析的参量的时间进程上的大量数据和相关断裂力的时间进程的大量数据,来实现分类器。如果在长的时间段上并且关于整个设备,数据可以可靠地区分良好和不良焊接,则可以省去示教阶段。
47.在一个实施方式中,该方法包括基于比较结果调控焊接工艺。由此可以在操作期间进行焊接设备的调整。
48.在一个实施方式中,该方法包括基于比较结果调整实施焊接工艺的焊接设备的参数。
49.在上述方法中,可以分析设备的调控过程的结果,特别是由发生器用作调节参量的频率,以便将焊接分类为良好焊接和不良焊接。然而,所描述的方法也可以集成到焊接设备的调控中。关于质量,分析不再是为了分类,而是为了改进。换句话说,不再是识别不良焊接,而是避免它们。
50.在一个实施方法中,该方法包括基于比较的振荡分析,以显示焊接工艺的动力学,以便检测欠焊或过焊。
51.根据第二方面,所述技术问题通过一种用于无损检测超声波焊接质量的测量装置来解决,该测量装置被设置为在一时间段内采集测量参量,其中该测量参量用于表征待测试的焊接工艺的电的或机械的振荡特性;通过傅立叶分析的应用来评价所采集的与时间相关的测量参量;并将评价结果与参考值进行比较,以便检测焊接质量。
52.根据第三方面,所述技术问题通过一种超声波焊接设备来解决,该超声波焊接设备包括用于在工件上施加机械力的超声波焊头;被设置为用于将电控制信号转换为机械振动并将其传输到超声波焊头的压电致动器;被设置为用于提供电控制信号的超声波发生器;以及根据第二方面的测量装置。
53.恰好是在磨损明显并因此对焊接质量产生影响时,设备状态的表征和与之相关的损坏检测能够有针对性地更换磨损部件。由此,固定规定的或根据为设备更换工装者慎重考虑而执行的更换时间可以被灵活的、以需求为导向的并因此更具成本效益的更换时间所取代。
54.此外,可以确保,振荡系统的所有工具和组件从振荡的角度来看始终正常工作,并且不会因设备磨损而产生有缺陷的焊接。在无人监督的情况下,在发现设备损坏之前,可能进行大量焊接。这样就无法预测利用有缺陷的设备已经焊接了多长时间,也无法预测这些焊接质量是否受到任何影响。
55.可以的是,在明显地出现故障或其原因不是已知的焊接质量下降的情况下,将上述方法和上述测量装置用作用于故障诊断和故障定位的系统。
56.通过设备状态的表征,能够直接地或间接地进行焊接设备的质量的连续监测。
57.通过焊接过程中的电压和电流或力和偏转的测量,可以对设备状态进行间接分析,如上文所述,用于监测焊接质量。测量参量的振幅、相位差和工作频率是描述设备的振荡系统的振动动力学的基本参量。在这些参量的时间进程中,一定的磨损迹象和装备错误
变得明显并因此可以被检测到。一个很容易检测到的设备状况恶化的例子是压电致动器上与老化相关的磨损迹象。在这里,调控可以将调节参量调整到显著的值,以便达到期望的物理条件。例如,这可以从对于焊接应用来说异常小的在电流和电压之间相位差中看出。由于老化相关的磨损逐渐发生,在焊接尚未出现质量下降的时间点,可以通过更换压电致动器来做出有针对性的响应。
58.可检测到的装备错误的一个例子是未正确设置的超声波焊头的的高度限位器,或者没有拧紧的且由于振动可能移动到不同的位置高度限位器。在振动分析中,随着高度限位器设置得越来越高,所述高度限位器会过早地阻止超声波焊头的向下运动,一旦焊接的断裂力开始急剧下降,若干测量参量的明显移动就会变得明显。特别地,这是电流幅度的和/或在电流与电压之间的相位差的减小。因此,无功功率尤其会急剧下降。
59.其他装备错误涉及振荡系统的拧紧扭矩、有缺陷的支承或夹紧、通过有缺陷的弹簧导致的有缺陷的垂直单元、未良好固定的固定触点。
附图说明
60.下面基于示例性实施例和附图更详细地描述本发明。其中:
61.图1是示出了根据一个实施例的焊接设备的示意图;
62.图2是示出了根据一个实施例的方法的流程图;
63.图3a是示出了根据一个实施例的频率曲线图;
64.图3b是示出了根据另一实施例的频率曲线图;
65.图3c是示出了根据实施例的电流曲线图;
66.图4是示出了根据另一实施例的电流振幅曲线图;和
67.图5是示出了根据实施例的超声波焊头的偏转的振幅曲线图。
具体实施方式
68.图1示出了根据示例性实施例的焊接设备100的示意图。焊接设备100是超声波焊接设备。焊接设备100具有超声波发生器101。超声波发生器101是被设置为产生电信号的信号发生器。例如,电信号根据电压进行调节,并映射超声波振荡。
69.焊接设备100具有压电致动器103。压电致动器103与超声波发生器101电耦合并且被设置为将来自超声波发生器101的电信号转换为机械振动。为此,焊接设备100利用压电效应。
70.超声波焊头105与压电致动器103机械耦合。在另一个实施例中,超声波焊头105包括压电致动器103。
71.压电致动器103的机械超声振荡通过在超声波焊头105和压电致动器103之间的机械耦合传递到超声波焊头105。
72.工件,特别是电缆包107,可以插入到超声波焊头105中。在此,电缆包107的各个电缆的剥开的裸露端插入到超声波焊头105中。
73.当焊接设备100投入运行时,超声波发生器101产生电信号,压电致动器103将电信号转换成机械振动,所述机械振动通过超声波焊头107传递到电缆包107。
74.在此,电缆包107的各个电缆彼此焊接到一起。
75.焊接设备100包括测量装置109。测量装置109被设置为测量超声波发生器101的电信号。测量装置109被设置为测量超声波焊头107上的机械振动参量。在电信号的情况下,测量装置109采集电压和电流。使用变压器以非侵入方式测量电流。在另一示例性实施例中,通过电流测量电阻器测量电流。机械偏转由涡流传感器测量。
76.为了获得参考曲线,即参考值或额定值,将电缆包107配备以干扰装置或在没有额外措施的情况下焊接,并且记录测量参量。然后我们通过额外的测试来检测焊接质量,特别是破坏性地检测焊接质量。
77.以这种方式得到可以与良好的或不良的测量对应的参考曲线。
78.对随时间测量的参量进行傅立叶分析,特别是短期傅立叶分析。在该评价中,可以在操作期间采集焊接设备100的时间特性。
79.通过这种振荡分析,可以检测到有缺陷的焊接和设备状态。在这种情况下,有缺陷意味着所产生的焊接具有低于公差极限的断裂力。断裂力是为参考曲线指定的。在操作中,所评价的测量参量与参考曲线(即参考值或额定值)的比较可用于确定焊接的好坏,而无需实施断裂测试。
80.对于不同的焊接设备100,很难定义适用于在全设备范围并永久作为良好焊接和不良焊接之间区分标准的全局特征值。相反,必须在每个测试过程中焊接样本并测试其断裂力,尤其是在批次变更、更换工装过程或班次变更之后。在这里可以确定良好焊接。从这些良好焊接的曲线进程定义了一个公差带,用于分类。带外的焊接被归类为不良焊接。
81.这种借助示教的方法源于这样一个事实,即每次更换工装后曲线都不同,尽管焊接的质量没有改变。电流振幅以及所有导出的电参量也因更换工装过程而异。在所有示例中,只有应力振幅保持不变。
82.因此,可以在每次更换工装过程后实施新的示教过程。同样按照一定的时间间隔。在24小时后制作的10个焊接样本中,设备未更换工装并且未被使用,工作频率的曲线虽然保持不变,但相位差能够显著减小。
83.如果在更换工装过程中或一定时间间隔后,通过10个焊接样本进行示教,所有样本均达到规定的断裂力,则可以定义公差带,未来的良好焊接的所有曲线应位于该公差带内或附近。可以不使用示教曲线,而是以示教带的形式以图形方式显示。这种带显示在图3a到图3c中。
84.在所描述的实施例中,仅使用了10个样本。在另一个实施例中,该数量可以变化。如果将其曲线位于带之外的所有焊接都归类为“不良”焊接,这意味着选择性太小,即许多良好焊接被错误地归类为不良焊接。因此,实际用于分类的公差带必须比此带更宽。所述带的确定可以以统计方法进行,特别是在每个时间点扩大10个测量值的一个或两个标准偏差。
85.在某些情况下,用于示教焊接的物理条件与用于批量生产中后续焊接的物理条件不同。特别地,在示教期间,电缆包107的导线长度明显更短,并且时钟频率且由此模具温度也可能不同。必须确保这些差异对所测量得曲线没有影响。
86.即使波动很大,时钟频率对任何测量曲线几乎没有影响。工作频率受影响最大。
87.图2示出了根据实施例的方法的流程图200。
88.在第一步骤201中,采集测量参量。在此,在一时间段内,尤其是在整个焊接工艺
内,采集电的表征性振荡参量和机械的表征性振荡参量。在另一实施例中,仅采集电的或仅采集机械的测量参量。
89.在步骤203中,评价所采集的测量参量。以傅立叶分析的方式来评价所采集的用于测量参量的时间进程。
90.在步骤205中,将评价结果与参考值,特别是标称曲线进行比较。在此,参考值代表曲线进程允许位于其中的带。
91.为了确定导线长度的影响,用3个导线长度、分别2个样本实施调查。在不同的长度上,工作频率位于一个最大宽度为30hz的频带中,这大约对应于用于更换工装过程的试验中的频带宽度。此外,13cm的短的导线长度的曲线与其他的不同,但在生产中,在过程控制中使用30cm导线,其曲线与较长导线的曲线几乎没有区别。因此不能假设导线长度有显著影响。
92.在每次批次变更后,都会在生产中实施破坏性测试以进行过程控制。这些焊接也可用于示教过程。这是必要的,因为通过批次变更,曲线可以显著变化,而不必伴随断裂力的变化。以三批名义上相同的导线为例,每批分别10个焊接样本,在工作频率、电流幅度和相位差以及所有导出的参量中,得到明显不同的公差带。失真系数的差异也很明显。
93.图3a示出了根据实施例的频率曲线图。时间绘制在横坐标轴上,频率绘制在纵坐标轴上,此处在上面是20250hz和下面是20450hz的范围内。
94.焊接质量下降的一个现实例子是焊接表面由护手霜污染。在这个实验中,部分焊接表面通过模板有针对地由护手霜污染。
95.曲线301对应于涂覆0%护手霜,曲线303对应于涂覆5%护手霜,曲线305对应于涂覆20%护手霜,曲线307对应于涂覆30%护手霜。
96.在工作频率处非常清楚地表明,所述工作频率随着护手霜污染的增加而降低。看不出其他参量的变化。仅在高次谐波的非常特定的参量和部分中识别出一种趋势,例如在压实声期间相位差中的二次谐波和在焊接声期间电压振幅中的二次谐波,然而,它们不适合作为可靠的分类器,最多通过工作频率支持分类。
97.利用以受控方式护手霜污染的试验也证明了个别曲线具有与断裂力的相关性。如果将焊接样本按断裂力进行分组,可以看出工作频率是一个很好的分类器,能够借助振荡分析将具有小于100n断裂力的非常差的样本与具有大于109n断裂力的良好样本分开。通过这种方式,能够检测非常关键的焊接。
98.图3b示出了根据另一实施例的频率曲线图。时间绘制在横坐标轴上,频率绘制在纵坐标轴上,此处在下面是20250hz和上面是20450hz的范围内。
99.曲线309、311和313示出了焊接样本根据其断裂力的划分。在曲线309的情况下,使用超过200n的断裂力以便破坏样本。在曲线311的情况下,使用100n和200n之间的断裂力以破坏样本。在曲线313的情况下,使用小于100n的断裂力以破坏样本。
100.振荡分析可以识别焊接设备100中的缺陷。如果换能器发生损坏,则可以在曲线上非常清楚地看到。电流振幅急剧下降,相位差增大。结果,换能器不再能够将足够的功率带入待焊接区域,这也会显著增加焊接时间并且不能产生材料结合连接。
101.图3c示出了根据实施例的电流曲线图。时间绘制在横坐标轴上,电流绘制在纵坐标轴上,这里的范围是从低的0a到高的5a。
102.曲线315示出了新的换能器的电流曲线,曲线317示出了完好的使用过的换能器的电流分布,曲线319显示了有缺陷的使用过的换能器的电流分布。可以清楚地看到曲线319急剧下降。因此可以采集换能器的状态。
103.还可以检测到导致振荡边界条件发生变化的装备错误。例如,如果在更换工装时忘记拧紧高度限位器,所述高度限位器会在多次焊接过程中向上滑动,并且在焊接过程中超声波焊头105位于限位器上并应继续对焊接节点施加正常压力。在某些情况下这不能借助焊接高度监测和焊接时间监测显示,尽管断裂力已经显著降低。
104.图4示出了根据实施例的电流分布曲线图。时间绘制在横坐标轴上,电流绘制在纵坐标轴上,这里的范围是从低的0a到高的5a。
105.此处,随时间绘制了10条曲线401至410。曲线402到406靠近在一起并且电流增加。然而,曲线407至410急剧下降。由此可以推断,在这些运行期间,高度限位器设置不正确。
106.通过机械振动测量,即借助超声波焊头105的偏转测量,能够检测焊接设备100中的设备缺陷。在由此所启动的设备检测之后,发现弹簧断裂。
107.图5示出了根据实施例的超声波焊头偏转的振幅曲线图。曲线501示出了新弹簧的进程。曲线503示出了断裂弹簧的进程。可以清楚地看到振幅的下降。
108.在机械振动分析中,也必须注意,不同的焊接设备100显示不同的曲线,即设备特定的参考曲线对于分析是有利的。与电的振荡分析一样,示教过程有利于检测不良焊接质量。不同的导线批次已经导致显著变化的曲线。然而,接触部件批次在该实验中没有影响。
109.附图标记列表
110.100 焊接设备
111.101 超声波发生器
112.103 压电致动器
113.105 超声波焊头
114.107 电缆包
115.109 测量装置
116.200 流程图
117.201
‑
205 方法步骤
118.301
‑
319 曲线
119.401
‑
410 曲线
120.501、503 曲线
再多了解一些
本文用于企业家、创业者技术爱好者查询,结果仅供参考。