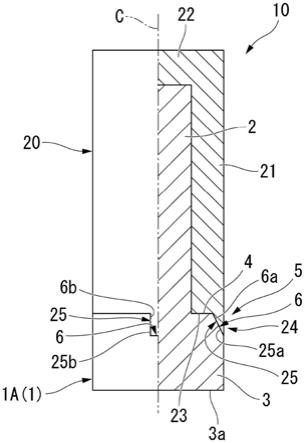
1.本发明涉及一种硬质烧结体用基材、硬质烧结体及切削工具。
2.本技术基于2019年3月26日在日本技术的专利申请2019
‑
058625号主张优先权,在此引用其内容。
背景技术:
3.以往,已知有例如立铣刀、铰刀及钻头等切削工具。切削工具对圆柱状工具坯料实施磨削加工,从而形成排屑槽和切削刃等来制造。工具坯料是将构成刃部的硬质烧结体与硬质合金制柄部通过钎焊进行接合而制作的。
4.硬质烧结体具备多级圆柱状基材和覆盖基材的小径部的圆筒状筒部。基材为硬质合金制,筒部为多晶金刚石(pcd)制或多晶立方晶氮化硼(pcbn)制。基材与筒部烧结成一体而成为硬质烧结体。作为现有的硬质烧结体,例如已知有专利文献1、2。
5.专利文献1:日本专利第3055803号公报
6.专利文献2:日本专利第5906355号公报
7.在硬质烧结体中,基材的线膨胀系数(热膨胀系数)与筒部的线膨胀系数大不相同。例如,在基材为硬质合金制且筒部为pcd制的情况下,筒部的线膨胀系数为基材的线膨胀系数的一半左右。因此,当将硬质烧结体与柄部钎焊时,有时因热应力而在筒部与基材的界面附近等产生裂纹。
技术实现要素:
8.鉴于上述情况,本发明的目的在于提供一种能够抑制在硬质烧结体上产生裂纹的硬质烧结体用基材、硬质烧结体及切削工具。
9.本发明的一方式为一种硬质烧结体用基材,其为具有中心轴并在所述中心轴的轴向上延伸的多级柱状硬质烧结体用基材,所述硬质烧结体用基材具备:小径部;大径部,外径大于所述小径部;基材端面,位于所述大径部的外周面的轴向一侧的端部与所述小径部的轴向另一侧的端部之间,并且朝向轴向一侧;及第1倾斜部,在所述大径部的外周面与所述基材端面连接的环状角部中配置于圆周方向的至少一部分,所述第1倾斜部随着趋向轴向一侧而位于径向内侧。
10.并且,本发明的硬质烧结体的一方式,具备:上述硬质烧结体用基材;筒部,呈覆盖所述小径部的筒状,与所述硬质烧结体用基材相比,线膨胀系数小且硬度高,并与所述硬质烧结体用基材烧结成一体,所述筒部的内周面与所述小径部的外周面接合,所述筒部的朝向轴向另一侧的筒部端面与所述基材端面接合,所述筒部具有第2倾斜部,所述第2倾斜部在所述筒部的外周面与所述筒部端面连接的环状角部中配置于圆周方向的至少一部分,所述第2倾斜部随着趋向轴向一侧而位于径向内侧,并与所述第1倾斜部接合。
11.并且,本发明的切削工具的一方式具备:刃部,在上述硬质烧结体的外周部上设置有在轴向上延伸的排屑槽及切削刃;及柄部,在轴向上与所述刃部连接,所述切削刃配置于
所述筒部。
12.根据本发明的硬质烧结体用基材、硬质烧结体及切削工具,第1倾斜部位于基材的大径部的外周面与基材端面连接的角部。并且,在与基材烧结成一体的筒部上设置与第1倾斜部接合的第2倾斜部。现有结构不同于本发明,未设置第1倾斜部及第2倾斜部,与现有结构相比,在本发明中通过设置第1倾斜部及第2倾斜部,基材的体积减小,并且筒部的体积增大。即,基材的体积被抑制得较小,可以确保筒部的体积较大。由此,当将硬质烧结体与柄部钎焊时,能够减小筒部从基材承受的热应力。并且,配合该热应力减小的效果,通过增大基材与筒部的接触面积,还可以获得基材与筒部的接合强度增大的效果。
13.将硬质烧结体与柄部钎焊时产生的热应力作用于与基材的中心轴垂直的方向上。即,当钎焊时,容易产生沿基材端面及筒部端面的面方向的剪切力。在本发明中,设置有从基材端面向轴向凹陷的第1倾斜部,并且设置有从筒部端面向轴向突出的第2倾斜部。因此,当钎焊时,与中心轴垂直的剪切方向的热应力减小相当于在与第1倾斜部及第2倾斜部垂直的方向上释放的力的量。
14.从而,根据本发明,能够设为在钎焊时可以承受热应力的硬质烧结体,并且能够抑制在硬质烧结体上产生裂纹。而且,能够有效且稳定地制造将该硬质烧结体使用于刃部的切削工具。
15.在上述硬质烧结体用基材中,在沿所述中心轴的纵截面视图中,与所述中心轴垂直的假想平面与所述第1倾斜部之间的角度为10
°
以上且75
°
以下。
16.在纵截面视图中,若与中心轴垂直的假想平面与第1倾斜部之间的角度为10
°
以上,则可以确保第1倾斜部从基材端面向轴向凹陷的深度较大,并且基材的体积稳定地被抑制得较小。由此,能够稳定地减小当与基材烧结成一体的筒部在钎焊时从基材承受的热应力。并且,当钎焊时,在与第1倾斜部垂直的方向上容易释放应力,能够更稳定地抑制在硬质烧结体上产生裂纹。
17.在纵截面视图中,若与中心轴垂直的假想平面与第1倾斜部之间的角度为75
°
以下,则可抑制第1倾斜部过度靠近大径部的朝向轴向另一侧的端面。即,能够抑制第1倾斜部过度靠近硬质烧结体与柄部的钎焊部位(接合部)。由此,在与基材烧结成一体的筒部中,与第1倾斜部接合的第2倾斜部在钎焊时远离感应加热用热源而配置,可抑制第2倾斜部的材料的特性发生变化。具体而言,例如在筒部为pcd制的情况下,能够抑制构成第2倾斜部的金刚石粒子因热源而石墨化造成强度降低的不良现象。
18.优选为,在上述硬质烧结体用基材中,所述第1倾斜部从所述大径部的外周面向径向内侧凹陷的最大深度为所述大径部的直径的5%以上、且为所述大径部的半径与所述小径部的半径的差值以下。
19.若第1倾斜部从大径部的外周面向径向内侧凹陷的最大深度为大径部的直径的5%以上,则可以确保第1倾斜部的径向长度较大,从而基材的体积稳定地被抑制得较小。由此,能够稳定地减小当与基材烧结成一体的筒部在钎焊时从基材承受的热应力。并且,当钎焊时,在与第1倾斜部垂直的方向上容易释放应力,能够更稳定地抑制在硬质烧结体上产生裂纹。
20.若第1倾斜部从大径部的外周面向径向内侧凹陷的最大深度为大径部的半径与小径部的半径的差值以下,则可以抑制第1倾斜部干涉小径部,从而能够稳定地制造该基材。
21.优选为,在上述硬质烧结体用基材中,所述第1倾斜部为随着趋向轴向一侧而径向深度变深的凹状,所述第1倾斜部在圆周方向上以彼此隔开间隔的方式在所述角部设置为多个。
22.在该情况下,第1倾斜部例如为槽状(狭缝状)等凹状,在大径部的外周面与基材端面连接的角部,在圆周方向上以隔开等间隔或不等间隔的方式设置有多个第1倾斜部。因此,配置第1倾斜部的自由度增大,可以容易应对使用于各种切削工具的各种硬质烧结体。
23.另外,在上述结构中,当对硬质烧结体赋予排屑槽和切削刃的形状而形成切削工具的刃部时,可以通过磨削加工而去除多个第1倾斜部中的几个。
24.优选为,在上述硬质烧结体用基材中,所述第1倾斜部的圆周方向长度为所述大径部的直径的10%以上且80%以下。
25.若第1倾斜部的圆周方向长度为大径部的直径的10%以上,则可以确保在基材的大径部的外周面与基材端面连接的角部中凹陷的第1倾斜部的容量较大,基材的体积稳定地被抑制得较小。由此,能够稳定地减小当与基材烧结成一体的筒部在钎焊时从基材承受的热应力。并且,当钎焊时,通过容量大的第1倾斜部而容易释放应力,并且能够更稳定地抑制在硬质烧结体上产生裂纹。
26.若第1倾斜部的圆周方向长度为大径部的直径的80%以下,则确保能够在圆周方向上配置在角部中凹陷的凹状第1倾斜部的数量,从而可以确保多个第1倾斜部的朝向圆周方向的壁面部分的总面积较大。由此,可以确保多个第1倾斜部与多个第2倾斜部在圆周方向上接触的总面积较大,并且更容易承受钎焊时产生的热应力。
27.优选为,在上述硬质烧结体用基材中,所述第1倾斜部具有:倾斜面,随着趋向轴向一侧而位于径向内侧;及一对侧壁面,连接于所述倾斜面的圆周方向的两端部,并且在圆周方向上以彼此隔开间隔的方式对置配置。
28.在该情况下,与例如第1倾斜部由两个壁面形成为v字形截面等的情况相比,能够确保第1倾斜部的容量较大,并且基材的体积相应地被抑制得较小。由此,能够稳定地减小当与基材烧结成一体的筒部在钎焊时从基材承受的热应力。并且,当钎焊时,通过容量大的第1倾斜部而容易释放应力,并且能够更稳定地抑制在硬质烧结体上产生裂纹。
29.优选为,在上述硬质烧结体用基材中,所述一对侧壁面随着趋向径向外侧而在圆周方向上彼此远离。
30.在该情况下,能够确保第1倾斜部的容量更大,并且基材的体积被抑制得更小。
31.优选为,在上述硬质烧结体用基材中,所述第1倾斜部配置于所述角部的整周。
32.在该情况下,第1倾斜部呈环状,并且在大径部的外周面与基材端面连接的角部设置于圆周方向的整个区域。因此,能够稳定地确保第1倾斜部的容量较大,基材的体积相应地被抑制得较小。由此,能够稳定地减小当与基材烧结成一体的筒部在钎焊时从基材承受的热应力。并且,当钎焊时,通过容量大的第1倾斜部而容易释放应力,并且能够更稳定地抑制在硬质烧结体上产生裂纹。
33.优选为,在上述硬质烧结体用基材中,所述第1倾斜部具有凹曲面形状的凹曲面部。
34.在该情况下,能够确保构成第1倾斜部的壁面的表面积较大,并且第1倾斜部和与基材烧结成一体的筒部的第2倾斜部的接合强度提高。并且,在第1倾斜部的壁面附近不易
产生热应力集中的部位,能够进一步抑制在硬质烧结体上产生裂纹。并且,可以容易确保第1倾斜部的容量更大。
35.优选为,在上述硬质烧结体用基材中,所述第1倾斜部具有凸曲面形状的凸曲面部。
36.在该情况下,能够确保构成第1倾斜部的壁面的表面积较大,并且第1倾斜部和与基材烧结成一体的筒部的第2倾斜部的接合强度提高。并且,在第1倾斜部的壁面附近可以不易产生热应力集中的部位,能够进一步抑制在硬质烧结体上产生裂纹。
37.优选为,在上述硬质烧结体中,所述硬质烧结体用基材的杨氏模量为300gpa以上,所述筒部的杨氏模量为600gpa以上。
38.若硬质烧结体用基材的杨氏模量为300gpa以上,则在将该基材使用于例如立铣刀等切削工具的情况下,能够稳定地确保刚性。
39.并且,若筒部的杨氏模量为600gpa以上,则在将该筒部使用于例如立铣刀等切削工具的情况下,能够稳定地确保耐磨损性。
40.优选为,在上述硬质烧结体中,所述硬质烧结体用基材是硬质合金制、金属陶瓷制及陶瓷制中的任一种,所述筒部是多晶金刚石制及多晶立方晶氮化硼制中的任一种。
41.根据本发明的一方式的硬质烧结体用基材、硬质烧结体及切削工具,能够抑制在硬质烧结体上产生裂纹。
附图说明
42.图1是表示第1实施方式的硬质烧结体的俯视图。
43.图2是表示第1实施方式的硬质烧结体的侧视图及侧截面图(纵截面图)。
44.图3是表示第1实施方式的硬质烧结体用基材的俯视图。
45.图4是表示第1实施方式的硬质烧结体用基材的侧视图及侧截面图(纵截面图)。
46.图5是表示第1实施方式的硬质烧结体用基材的立体图。
47.图6是表示第1实施方式的切削工具的侧视图。
48.图7是表示第1实施方式的硬质烧结体用基材的第1变形例的立体图。
49.图8是表示第1实施方式的硬质烧结体用基材的第1变形例的俯视图。
50.图9是表示第1实施方式的硬质烧结体用基材的第2变形例的立体图。
51.图10是表示第1实施方式的硬质烧结体用基材的第2变形例的俯视图。
52.图11是表示第1实施方式的硬质烧结体用基材的第3变形例的立体图。
53.图12是表示第1实施方式的硬质烧结体用基材的第3变形例的俯视图。
54.图13是表示第1实施方式的硬质烧结体用基材的第4变形例的立体图。
55.图14是表示第1实施方式的硬质烧结体用基材的第4变形例的俯视图。
56.图15是表示第1实施方式的硬质烧结体用基材的第5变形例的立体图。
57.图16是表示第1实施方式的硬质烧结体用基材的第5变形例的俯视图。
58.图17是表示第2实施方式的硬质烧结体用基材的侧视图。
59.图18是表示第2实施方式的硬质烧结体用基材的变形例的侧视图。
具体实施方式
60.<第1实施方式>
61.以下,参考图1~图6对本发明的第1实施方式的硬质烧结体用基材1a(1)、硬质烧结体10及切削工具50进行说明。图1及图2表示本实施方式的硬质烧结体10。图3~图5表示本实施方式的硬质烧结体用基材1a。图6表示本实施方式的切削工具50。
62.另外,在以下说明中,有时将硬质烧结体用基材1a简称为基材1a。并且,硬质烧结体10可以改称为超硬质烧结体10或超高硬度烧结体10。
63.如图1及图2所示,硬质烧结体10具备硬质烧结体用基材1a和与硬质烧结体用基材1a烧结成一体的筒部20。基材1a的杨氏模量为300gpa以上。基材1a是硬质合金制、金属陶瓷制及陶瓷制中的任一种。筒部20的杨氏模量为600gpa以上。筒部20是多晶金刚石(pcd)制及多晶立方晶氮化硼(pcbn)制中的任一种。与基材1a相比,筒部20的线膨胀系数小且硬度高。硬质烧结体用基材1a的杨氏模量优选为550gpa以上且650gpa以下,筒部20的杨氏模量优选为800gpa以上且950gpa以下。
64.硬质烧结体10通过在未图示的圆筒状容器中填充将被做成压坯成型体的基材1a原料和粉末状的筒部20原料,并在超高温超高压条件下进行烧结而制造。
65.如图1~图5所示,基材1a具有中心轴c,并且呈在中心轴c的轴向上延伸的多级柱状。具体而言,基材1a呈以中心轴c为中心的多级圆柱状。基材1a具备小径部2、大径部3、基材端面4、角部5及第1倾斜部6。
66.在本实施方式中,将基材1a的中心轴c延伸的方向(沿中心轴c的方向)称为轴向。在轴向上,小径部2和大径部3配置于彼此不同的位置。在轴向中,将从大径部3朝向小径部2的方向称为轴向一侧,将从小径部2朝向大径部3的方向称为轴向另一侧。
67.将与中心轴c正交的方向称为径向。在径向中,将靠近中心轴c的方向称为径向内侧,将远离中心轴c的方向称为径向外侧。
68.将围绕中心轴c环绕的方向称为圆周方向。在圆周方向中,将规定的旋转方向称为圆周方向一侧,将与规定的旋转方向相反的旋转方向称为圆周方向另一侧。
69.基材1a的中心轴c、硬质烧结体10的中心轴c及切削工具50的中心轴c为通用轴,彼此同轴配置。
70.轴向一侧在图6所示的切削工具50中相当于前端侧(图6的上侧)。轴向另一侧在切削工具50中相当于后端侧(图6的下侧)。
71.在圆周方向中,有时将切削加工时由机床的主轴等使切削工具50旋转的方向称为工具旋转方向t,将与该工具旋转方向t相反的旋转方向称为工具旋转方向t的反方向(工具旋转反方向)。在本实施方式中圆周方向一侧相当于工具旋转方向t,圆周方向另一侧相当于工具旋转方向t的反方向。
72.在图1~图5中,小径部2呈在轴向上延伸的圆柱状。
73.大径部3呈在轴向上延伸的圆柱状。大径部3的外径大于小径部2。在本实施方式中,大径部3的外径(直径)d为小径部2的外径d的大致两倍。大径部3的轴向长度小于小径部2的轴向长度。在本实施方式中,大径部3的轴向长度l1为小径部2的轴向长度l2的大致1/3倍。大径部3的朝向轴向另一侧的端面3a呈在与中心轴c垂直的方向上扩展的平面状。端面3a呈圆形状。
74.基材端面4位于大径部3的外周面的轴向一侧的端部与小径部2在轴向另一侧的端部之间,并且朝向轴向一侧。基材端面4配置于大径部3的外周面的轴向一侧的端部与小径部2的外周面的轴向另一侧的端部之间。基材端面4呈以中心轴c为中心的圆环状。在本实施方式中,基材端面4呈在与中心轴c垂直的方向上扩展的平面状。
75.如图5所示,基材端面4可以在基材端面4中的与小径部2连接的内周部具有角部凹曲面部4a。角部凹曲面部4a是以中心轴c为中心的圆环状凹曲面。角部凹曲面部4a随着趋向径向内侧而位于轴向一侧。在沿中心轴c的纵截面视图中,角部凹曲面部4a呈凹曲线状,并且朝向径向内侧及轴向另一侧凹陷。
76.角部5是大径部3的外周面与基材端面4连接的凸状部分。角部5呈以中心轴c为中心的环状,并且在圆周方向上延伸。角部5呈圆环状。角部5可以改称为基材角部5。
77.第1倾斜部6在角部5中配置于圆周方向的至少一部分。第1倾斜部6随着趋向轴向一侧而位于径向内侧。即,第1倾斜部6随着趋向轴向一侧而向径向内侧延伸。具体而言,在第1倾斜部6中位于径向内侧的内侧部,即作为第1倾斜部6的底部的表面部或谷部随着趋向轴向一侧而位于径向内侧,并且相对于中心轴c倾斜地延伸。
78.如图4所示,在沿中心轴c的纵截面视图中,与中心轴c垂直的假想平面vp与第1倾斜部6之间的角度θ为10
°
以上且75
°
以下。具体而言,在该纵截面视图中,角度θ是在假想平面vp与在第1倾斜部6中位于径向内侧的内侧部之间形成的锐角及钝角中的锐角的角度。
79.在沿中心轴c的纵截面视图中,与中心轴c垂直的假想平面vp与第1倾斜部6之间的角度θ优选为45
°
以上且60
°
以下。
80.在本实施方式中,第1倾斜部6呈在角部5中凹陷的凹状,在图示例中呈槽状(狭缝状)。第1倾斜部6在轴向及径向上延伸。第1倾斜部6从基材端面4向轴向另一侧凹陷,并且从大径部3的外周面向径向内侧凹陷。第1倾斜部6在圆周方向上以彼此隔开间隔的方式在角部5中设置为多个。在图示例中,多个(八个)第1倾斜部6在圆周方向上以彼此隔开等间隔的方式(以等间距)配置。然而,并不限定于此,多个第1倾斜部6可以在圆周方向上以彼此隔开不等间隔的方式(以不等间距)配置。
81.第1倾斜部6随着趋向径向外侧而轴向深度变深。第1倾斜部6随着趋向轴向一侧而径向深度变深。如图3所示,第1倾斜部6从大径部3的外周面向径向内侧凹陷的最大深度(槽深度)gd为大径部3的直径d的5%以上、且为大径部3的半径d/2与小径部2的半径d/2的差值(d/2
‑
d/2)以下。最大深度gd可以改称为第1倾斜部6的轴向一侧的端部上的径向长度。
82.第1倾斜部6从大径部3的外周面向径向内侧凹陷的最大深度gd优选为大径部3的直径d的10%以上且大径部3的直径d的20%以下。
83.第1倾斜部6的圆周方向长度(槽宽)gw为大径部3的直径d的10%以上且80%以下。另外,如图3所示,在本实施方式中,从轴向观察基材1a时,第1倾斜部6的圆周方向长度gw相当于第1倾斜部6的径向外端部上的开口尺寸。
84.第1倾斜部6的圆周方向长度gw优选为大径部3的直径d的10%以上且20%以下。
85.如图3~图5所示,第1倾斜部6具有第1倾斜面(倾斜面)6a和一对第1侧壁面(侧壁面)6b。
86.第1倾斜面6a随着趋向轴向一侧而位于径向内侧。在本实施方式中,第1倾斜面6a呈平面状。第1倾斜面6a朝向径向外侧及轴向一侧。第1倾斜面6a呈四边形形状。
87.一对第1侧壁面6b连接于第1倾斜面6a的圆周方向的两端部,并且在圆周方向上以彼此隔开间隔的方式对置配置。在本实施方式中,第1侧壁面6b呈在与圆周方向垂直的方向(轴向及径向)上扩展的平面状。第1侧壁面6b呈三角形形状。
88.如图1及图2所示,筒部20呈覆盖小径部2的筒状。筒部20呈以中心轴c为中心的圆筒状,并且在轴向上延伸。在本实施方式中,筒部20呈有顶筒状。筒部20具有周壁部21、顶壁部22、筒部端面23、角部24及第2倾斜部25。
89.周壁部21呈在轴向上延伸的圆筒状。周壁部21在径向上从外侧包围小径部2。周壁部21的内周面固定到小径部2的外周面。周壁部21的内周面(即筒部20的内周面)与小径部2的外周面接合。
90.顶壁部22连接于周壁部21的轴向一侧的端部。顶壁部22呈以中心轴c为中心的圆板状。顶壁部22的一对板面朝向轴向。顶壁部22的朝向轴向另一侧的板面固定到小径部2的朝向轴向一侧的端面。顶壁部22的朝向轴向另一侧的板面与小径部2的朝向轴向一侧的端面接合。
91.筒部端面23位于周壁部21的轴向另一侧的端部,并且朝向轴向另一侧。筒部端面23呈以中心轴c为中心的圆环状。在本实施方式中,筒部端面23呈向与中心轴c垂直的方向扩展的平面状。筒部端面23固定到基材端面4。筒部端面23与基材端面4接合。
92.角部24是周壁部21的外周面(即筒部20的外周面)与筒部端面23连接的凸状部分。角部24呈以中心轴c为中心的环状,并且在圆周方向上延伸。角部24呈圆环状。角部24可以改称为筒部角部24。
93.第2倾斜部25在角部24中配置于圆周方向的至少一部分。第2倾斜部25随着趋向轴向一侧而位于径向内侧。具体而言,在第2倾斜部25中位于径向内侧的内侧部即在第2倾斜部25中朝向径向内侧的表面部或棱部随着趋向轴向一侧而位于径向内侧,并且相对于中心轴c倾斜地延伸。第2倾斜部25固定到第1倾斜部6。第2倾斜部25与第1倾斜部6接合。
94.在本实施方式中,第2倾斜部25呈在角部24中突出的凸状,具体而言,呈突起状或肋状。第2倾斜部25在轴向及径向上延伸。第2倾斜部25从筒部端面23向轴向另一侧突出。从轴向观察时,第2倾斜部25的位于径向外侧的外侧部(外周面)与周壁部21的外周面重叠。第2倾斜部25的位于径向外侧的外侧部配置成与周壁部21的外周面在同一面上。
95.第2倾斜部25在圆周方向上以彼此隔开间隔的方式在角部24上设置为多个。在图示例中,多个(八个)第2倾斜部25在圆周方向上以彼此隔开等间隔的方式(以等间距)配置。然而,并不限定于此,多个第2倾斜部25也可以在圆周方向上以彼此隔开不等间隔的方式(以不等间距)配置。
96.在沿中心轴c的纵截面视图中,与中心轴c垂直的假想平面vp与第2倾斜部25之间的角度为与上述角度θ相同的值(10
°
以上且75
°
以下)。具体而言,在该纵截面视图中,所述角度是在假想平面vp与在第2倾斜部25中位于径向内侧的内侧部之间形成的锐角及钝角中的锐角的角度。
97.第2倾斜部25随着趋向径向外侧而轴向长度(高度)变大。第2倾斜部25随着趋向轴向一侧而径向长度变大。第2倾斜部25的径向最大长度为与上述第1倾斜部6的最大深度gd相同的值。第2倾斜部25的径向最大长度与从周壁部21的外周面至第2倾斜部25的径向内端部的径向长度相等。第2倾斜部25的径向最大长度可以改称为第2倾斜部25的轴向一侧的端
部上的径向长度。
98.第2倾斜部25的圆周方向长度(突起宽度、肋宽度)为与上述第1倾斜部6的圆周方向长度gw相同的值。
99.第2倾斜部25具有第2倾斜面25a和一对第2侧壁面25b。
100.第2倾斜面25a随着趋向轴向一侧而位于径向内侧。在本实施方式中,第2倾斜面25a呈平面状。第2倾斜面25a朝向径向内侧及轴向另一侧。第2倾斜面25a呈四边形形状。第2倾斜面25a具有与第1倾斜面6a相同的形状。第2倾斜面25a与第1倾斜面6a接合。
101.一对第2侧壁面25b连接于第2倾斜面25a的圆周方向的两端部,并且在圆周方向上以彼此隔开间隔的方式背对背配置。在本实施方式中,第2侧壁面25b呈向与圆周方向垂直的方向(轴向及径向)扩展的平面状。第2侧壁面25b呈三角形形状。第2侧壁面25b具有与第1侧壁面6b相同的形状。第2侧壁面25b与第1侧壁面6b接合。
102.切削工具50是旋转切削工具(滚削工具),具体而言,是立铣刀、铰刀及钻头等。如图6所示,本实施方式的切削工具50是立铣刀。
103.切削工具50具备在上述硬质烧结体10的外周部上设置有在轴向上延伸的排屑槽55及切削刃(外周刃)56的刃部51和在轴向上与刃部51连接的柄部52。即,刃部51通过在硬质烧结体10的外周部上由磨削砂轮等对排屑槽55及切削刃56进行磨削加工而制作。即,硬质烧结体10是用于制作刃部51的坯料,并且是在切削工具50的制造过程中制作的刃部51的中间体。刃部51的外周面配置于筒部20的周壁部21。
104.另外,当对硬质烧结体10赋予排屑槽55和切削刃56的形状而形成切削工具50的刃部51时,可以通过磨削加工选择性地去除多个第1倾斜部6中的几个及多个第2倾斜部25中的几个。
105.柄部52为硬质合金制。柄部52呈在轴向上延伸的圆柱状。刃部51与柄部52通过例如使用ag钎料的在真空下感应加热下的钎焊而彼此接合。即,刃部51的朝向轴向另一侧的端面(大径部3的端面)3a与柄部52的朝向轴向一侧的端面52a通过钎焊彼此接合。
106.在切削工具50中,柄部52可装卸地安装于未图示的机床的主轴等,并通过机床的主轴等围绕中心轴c进行旋转,由此对被切削材料进行切削加工(滚削加工)。被切削材料例如是金属制。
107.排屑槽55从切削工具50的外周面向径向内侧凹陷,并且在轴向上延伸。在本实施方式中,排屑槽55从切削工具50的轴向一侧的端部(前端部)随着趋向轴向另一侧(后端侧)而向与工具旋转方向t相反的方向呈螺旋状延伸。然而,并不限定于此,排屑槽55也可以与中心轴c平行地在轴向上延伸。
108.在切削工具50中设置有至少一个排屑槽55。在本实施方式中,排屑槽55设置为多个。多个排屑槽55在圆周方向上以彼此隔开间隔的方式配置。在本实施方式中,多个排屑槽55以相对于中心轴c处于旋转对称位置的方式在切削工具50的外周上沿圆周方向以彼此隔开等间隔的方式(以等间距)配置。另外,多个排屑槽55也可以在圆周方向上以彼此隔开不等间隔的方式(不等间距)配置。
109.切削刃56配置于刃部51,并且在轴向上延伸。切削刃56形成于排屑槽55的朝向工具旋转方向t的壁面与刃部51的外周面的交叉棱线上。切削刃56从刃部51的轴向一侧的端部(前端部)随着趋向轴向另一侧而向与工具旋转方向t相反的方向呈螺旋状延伸。然而,并
不限定于此,切削刃56也可以与中心轴c平行地在轴向上延伸。
110.切削刃56的数量与排屑槽55的数量相同。在本实施方式中,切削刃56设置为多个。各个切削刃56沿着各个排屑槽55延伸。在本实施方式中,多个切削刃56以相对于中心轴c处于旋转对称位置的方式在刃部51的外周上沿圆周方向以彼此隔开等间隔的方式(以等间距)配置。另外,多个切削刃56也可以沿圆周方向以彼此隔开不等间隔的方式(以不等间距)配置。
111.切削刃56配置于硬质烧结体10的筒部20的周壁部21,并构成刃部51的外周部的一部分。
112.排屑槽55配置于筒部20的周壁部21及小径部2。在排屑槽55的朝向工具旋转方向t的壁面中,与切削刃56相邻的外周部即切削刃56的前刀面配置于筒部20的周壁部21。
113.在刃部51的外周面中,与切削刃56相邻的部分即切削刃56的后刀面配置于筒部20的周壁部21。
114.本实施方式的刃部51除了排屑槽55及切削刃56以外,还具有中心槽57和底刃58。中心槽57位于排屑槽55的轴向一侧的端部。中心槽57呈在径向上延伸的槽状。在多个排屑槽55分别设置有中心槽57。
115.底刃58配置于刃部51的轴向一侧的端部,并且在径向上延伸。底刃58在圆周方向上以彼此隔开间隔的方式设置为多个。底刃58也可以配置于筒部20的顶壁部22。
116.根据以上说明的本实施方式的硬质烧结体用基材1a、硬质烧结体10及切削工具50,第1倾斜部6位于基材1a的大径部3的外周面与基材端面4连接的角部5。并且,在与基材1a烧结成一体的筒部20上设置有与第1倾斜部6接合的第2倾斜部25。与不同于本实施方式而未设置第1倾斜部6及第2倾斜部25的现有结构相比,在本实施方式中通过设置第1倾斜部6及第2倾斜部25,基材1a的体积减小,并且筒部20的体积增大。即,基材1a的体积被抑制得较小,并且可以确保筒部20的体积较大。由此,当将硬质烧结体10与柄部52钎焊时,能够减小筒部20从基材1a承受的热应力。并且,配合减小该热应力的效果,通过增大基材1a与筒部20的接触面积,还可以获得基材1a与筒部20的接合强度增大的效果。
117.将硬质烧结体10与柄部52钎焊时产生的热应力作用于与基材1a的中心轴c垂直的方向上。即,当钎焊时,容易产生沿基材端面4及筒部端面23的面方向的剪切力。在本实施方式中,设置有从基材端面4向轴向凹陷的第1倾斜部6,并且设置有从筒部端面23向轴向突出的第2倾斜部25。因此,当钎焊时,与中心轴c垂直的剪切方向的热应力减小相当于在与第1倾斜部6及第2倾斜部25垂直的方向上释放的力的量。
118.从而,根据本实施方式,能够形成当钎焊时可以承受热应力的硬质烧结体10,并且能够抑制在硬质烧结体10上产生裂纹。而且,能够有效且稳定地制造将该硬质烧结体10使用于刃部51的切削工具50。
119.在本实施方式中,在沿中心轴c的纵截面视图中,与中心轴c垂直的假想平面vp与第1倾斜部6之间的角度θ为10
°
以上且75
°
以下。
120.在纵截面视图中,若假想平面vp与第1倾斜部6之间的角度θ为10
°
以上,可以确保第1倾斜部6从基材端面4向轴向凹陷的深度较大,并且基材1a的体积稳定地被抑制得较小。由此,能够稳定地减小当与基材1a烧结成一体的筒部20在钎焊时从基材1a承受的热应力。并且,当钎焊时,在与第1倾斜部6垂直的方向上容易释放应力,能够更稳定地抑制在硬质烧
结体10上产生裂纹。
121.在纵截面视图中,若假想平面vp与第1倾斜部6之间的角度θ为75
°
以下,则抑制第1倾斜部6过度靠近大径部3的朝向轴向另一侧的端面3a。即,能够抑制第1倾斜部6过度靠近硬质烧结体10与柄部52的钎焊部位(接合部)。由此,在与基材1a烧结成一体的筒部20中,与第1倾斜部6接合的第2倾斜部25在钎焊时远离感应加热用热源而配置,可以抑制第2倾斜部25的材料的特性发生变化。具体而言,例如在筒部20为pcd制的情况下,能够抑制构成第2倾斜部25的金刚石粒子因热源而石墨化造成强度降低的不良现象。
122.在本实施方式中,第1倾斜部6从大径部3的外周面向径向内侧凹陷的最大深度gd为大径部3的直径d的5%以上、且为大径部3的半径d/2与小径部2的半径d/2的差值(d/2
‑
d/2)以下。
123.若第1倾斜部6从大径部3的外周面向径向内侧凹陷的最大深度gd为大径部3的直径d的5%以上,则可以确保第1倾斜部6的径向长度较大,从而基材1a的体积稳定地被抑制得较小。由此,能够稳定地减小当与基材1a烧结成一体的筒部20在钎焊时从基材1a承受的热应力。并且,当钎焊时,在与第1倾斜部6垂直的方向上容易释放应力,能够更稳定地抑制在硬质烧结体10上产生裂纹。
124.若第1倾斜部6从大径部3的外周面向径向内侧凹陷的最大深度gd为大径部3的半径d/2与小径部2的半径d/2的差值(d/2
‑
d/2)以下,则可以抑制第1倾斜部6干涉小径部2,从而能够稳定地制造该基材1a。
125.在本实施方式中,第1倾斜部6例如呈槽状等凹状,在大径部3的外周面与基材端面4连接的角部5中,在圆周方向上以隔开等间隔或不等间隔的方式设置有多个第1倾斜部6。因此,配置第1倾斜部6的自由度增大,可以容易应对使用于各种切削工具50的各种硬质烧结体10。
126.另外,在上述结构中,当钎焊时在设置为多个的第1倾斜部6及第2倾斜部25的组中的规定组中产生裂纹的情况下,当对硬质烧结体10赋予排屑槽55和切削刃56的形状而形成切削工具50的刃部51时,也可以通过磨削加工选择性地去除产生裂纹的所述规定组。
127.在本实施方式中,第1倾斜部6的圆周方向长度gw为大径部3的直径d的10%以上且80%以下。
128.若第1倾斜部6的圆周方向长度gw为大径部3的直径d的10%以上,则可以确保在基材1a的大径部3的外周面与基材端面4连接的角部5中凹陷的第1倾斜部6的容量较大,并且基材1a的体积稳定地被抑制得较小。由此,能够稳定地减小当与基材1a烧结成一体的筒部20在钎焊时从基材1a承受的热应力。并且,当钎焊时,通过容量大的第1倾斜部6而容易释放应力,并且能够更稳定地抑制在硬质烧结体10上产生裂纹。
129.若第1倾斜部6的圆周方向长度gw为大径部3的直径d的80%以下,则可以确保能够在圆周方向上配置在角部5中凹陷的凹状第1倾斜部6的数量,从而可以确保多个第1倾斜部6的朝向圆周方向的壁面部分(第1侧壁面6b)的总面积较大。由此,可以确保多个第1倾斜部6与多个第2倾斜部25在圆周方向上接触的总面积较大,并且更容易承受钎焊时产生的热应力。
130.在本实施方式中,第1倾斜部6具有第1倾斜面(倾斜面)6a和一对第1侧壁面(侧壁面)6b。
131.在该情况下,与例如第1倾斜部6由两个壁面形成为v字形截面等的情况相比,能够确保第1倾斜部6的容量较大,并且基材1a的体积相应地被抑制得较小。由此,能够稳定地减小当与基材1a烧结成一体的筒部20在钎焊时从基材1a承受的热应力。并且,当钎焊时,通过容量大的第1倾斜部6而容易释放应力,并且能够更稳定地抑制在硬质烧结体10上产生裂纹。
132.在本实施方式中,硬质烧结体用基材1a的杨氏模量为300gpa以上,烧结后的筒部20的杨氏模量为600gpa以上。
133.若硬质烧结体用基材1a的杨氏模量为300gpa以上,则在将该基材1a如本实施方式那样使用于立铣刀等切削工具50的情况下,能够稳定地确保刚性。
134.并且,若筒部20的杨氏模量为600gpa以上,则在将该筒部20如本实施方式那样使用于立铣刀等切削工具50的情况下,能够稳定地确保耐磨损性。
135.图7及图8表示本实施方式的第1变形例的硬质烧结体用基材1b(1)。在该第1变形例中,第1倾斜部6的一对第1侧壁面(侧壁面)6b随着趋向径向外侧而在圆周方向上彼此远离。
136.根据该第1变形例,能够确保第1倾斜部6的容量更大,并且基材1b的体积被抑制得更小。
137.图9及图10表示本实施方式的第2变形例的硬质烧结体用基材1c(1)。在该第2变形例中,第1倾斜部6的第1倾斜面(倾斜面)6a具有平面部6c和一对凹面部6d。
138.平面部6c呈平面状,并且随着趋向轴向一侧而位于径向内侧。
139.一对凹面部6d配置于平面部6c的圆周方向的两侧。一对凹面部6d与一对第1侧壁面6b连接。凹面部6d呈凹曲面形状,并且随着趋向轴向一侧而位于径向内侧。
140.根据该第2变形例,由于第1倾斜面6a具有一对凹面部6d,因此在第1倾斜部6的内表面(壁面)附近可以不易产生热应力集中的部位,能够进一步抑制在硬质烧结体10上产生裂纹。
141.图11及图12表示本实施方式的第3变形例的硬质烧结体用基材1d(1)。在该第3变形例中,第1倾斜部6具有凹曲面形状的凹曲面部6e。在与中心轴c垂直的横截面视图中,凹曲面部6e呈向径向内侧凹陷的凹曲线状。
142.根据该第3变形例,在第1倾斜部6的内表面(壁面)附近可以不易产生热应力集中的部位,能够进一步抑制在硬质烧结体10上产生裂纹。
143.图13及图14表示本实施方式的第4变形例的硬质烧结体用基材1e(1)。在该第4变形例中,第1倾斜部6具有一对壁面部6f。一对壁面部6f在圆周方向上彼此连接。一对壁面部6f随着趋向径向外侧而在圆周方向上彼此远离。壁面部6f呈平面状。壁面部6f呈三角形形状。
144.第1倾斜部6的径向内侧的内侧部是一对壁面部6f彼此连接的谷部。第1倾斜部6的谷部随着趋向轴向一侧而位于径向内侧。
145.根据该第4变形例,能够简化成型第1倾斜部6的工序,并且容易制造。
146.图15及图16表示本实施方式的第5变形例的硬质烧结体用基材1f(1)。在该第5变形例中,第1倾斜部6具有第1壁面部6g和第2壁面部6h。第1壁面部6g与第2壁面部6h在圆周方向上彼此连接。
147.第1壁面部6g呈向与圆周方向垂直的方向(轴向及径向)扩展的平面状。第1壁面部6g呈三角形形状。
148.第2壁面部6h随着趋向径向外侧而在圆周方向上远离第1壁面部6g。第2壁面部6h呈平面状。第2壁面部6h呈三角形形状。
149.第1倾斜部6的径向内侧的内侧部是第1壁面部6g与第2壁面部6h连接的谷部。第1倾斜部6的谷部随着趋向轴向一侧而位于径向内侧。
150.根据该第5变形例,能够简化成型第1倾斜部6的工序,并且容易制造。
151.<第2实施方式>
152.接着,参考图17对本发明的第2实施方式的硬质烧结体用基材1g(1)进行说明。另外,在第2实施方式中,对与第1实施方式相同的构成要件标注相同的符号,并省略其说明。
153.在本实施方式的基材1g中,第1倾斜部6配置于角部5的整周。第1倾斜部6具有锥面6i。锥面6i呈随着趋向轴向一侧而位于径向内侧的锥形形状。
154.在本实施方式中,第1倾斜部6呈以中心轴c为中心的环状,并且在大径部3的外周面与基材端面4连接的角部5上设置于圆周方向的整个区域。因此,能够稳定地确保第1倾斜部6的容量(即,第1倾斜部6从在图17中由双点划线表示的假想的角部5的外形凹陷的容量)较大,基材1g的体积相应地被抑制得较小。并且,能够确保烧结时填充在第1倾斜部6上的第2倾斜部25的容量较大,从而可以确保筒部20的体积较大。由此,能够稳定地减小与基材1g烧结成一体的筒部20在钎焊时从基材1g承受的热应力。并且,当钎焊时,通过容量大的第1倾斜部6而容易释放应力,并且能够更稳定地抑制在硬质烧结体10上产生裂纹。
155.图18表示本实施方式的变形例的硬质烧结体用基材1h(1)。在该变形例中,第1倾斜部6具有凹曲面形状的凹曲面部6j和凸曲面形状的凸曲面部6k。
156.凹曲面部6j呈以中心轴c为中心的圆环状。在沿中心轴c的纵截面视图中,凹曲面部6j呈朝向径向内侧及轴向另一侧凹陷的凹曲线状。凹曲面部6j随着趋向轴向一侧而位于径向内侧。凹曲面部6j在轴向上以彼此隔开间隔的方式设置为多个。
157.凸曲面部6k呈以中心轴c为中心的圆环状。在沿中心轴c的纵截面视图中,凸曲面部6k呈朝向径向外侧及轴向一侧突出的凸曲线形状。凸曲面部6k随着趋向轴向一侧而位于径向内侧。凸曲面部6k在轴向上以彼此隔开间隔的方式设置为多个。
158.凹曲面部6j与凸曲面部6k在轴向上交替排列。
159.在该变形例中,能够确保构成第1倾斜部6的壁面(凹曲面部6j及凸曲面部6k)的表面积较大,并可以提高第1倾斜部6和与基材1h烧结成一体的筒部20的第2倾斜部25的接合强度。并且,在第1倾斜部6的壁面及第2倾斜部25的壁面附近不易产生热应力集中的部位,并且能够进一步抑制在硬质烧结体10上产生裂纹。另外,通过设置凹曲面部6j,容易确保第1倾斜部6的容量更大。
160.另外,本发明并不限定于前述实施方式,例如如下述说明那样,在不脱离本发明的主旨的范围内,可以进行结构的变更等。
161.在前述实施方式中,例举出切削工具50是立铣刀的例子,但是并不限定于此。切削工具50也可以是除了立铣刀以外的铰刀、钻头及除此以外的旋转切削工具等。例如,在切削工具50是钻头的情况下,刃部51除了排屑槽55及切削刃56以外,还具备前端刃、修磨横刃、刃带及铲背面等。
162.此外,在不脱离本发明的主旨的范围内,可以将前述实施方式、变形例及写“另外”的部分中已说明的各个结构(构成要件)进行组合,并且也可以进行结构的附加、省略、替换及其他变更。并且,本发明并不限定于前述实施方式,而仅限于权利要求书。
163.实施例
164.以下,由实施例对本发明进行具体说明。然而,本发明并不限定于该实施例。
165.作为本发明的实施例及比较例(不具有第1倾斜部6的例子),分别准备了基材。在实施例及比较例中通用的结构,如下所述。
166.·
基材的材质
…
硬质合金制
167.·
基材的杨氏模量
…
570gpa
168.·
大径部3的直径d
…
12mm
169.·
小径部2的直径d
…
6mm
170.·
大径部3的轴向长度l1
…
7mm
171.·
小径部2的轴向长度l2
…
21mm
172.·
角部凹曲面部4a的曲率半径
…
1mm
173.关于实施例1~9,设为前述第1实施方式或第2实施方式的结构,如下述表1所示,分别设定有第1倾斜部6的形状(槽(数量)或整周)、角度θ、最大深度gd、槽宽gw。另外,由三维形状测定器测定出基材的各个尺寸。
174.使用在美国专利第5031484号说明书中公开的方法,将具有实施例1~9及比较例的各个基材的形状的压坯成型体与粉末状筒部原料一同进行烧结,分别制作出硬质烧结体。烧结后的筒部的杨氏模量为920gpa。用电火花线切割机、圆筒磨削机等加工机将硬质烧结体的外周修整为圆筒形状之后,用平面磨床将大径部3的朝向轴向另一侧的端面(底面)3a磨削约0.2mm,从而形成为与中心轴c垂直的平面。
175.将ag钎料涂布于硬质合金制柄部52的朝向轴向一侧的端面(接合面)52a,在该端面52a上粘接硬质烧结体的端面3a,并使用高频钎焊装置在真空下且在760℃的温度下进行了接合。
176.关于使用实施例1~9及比较例的各个基材的各个硬质烧结体的评价,进行荧光探伤检查,确认在硬质烧结体上是否产生裂纹。在产生裂纹的情况下,对作为产品能够使用(可用作产品)及无法使用(不可用作产品)进行了评价。将结果示于表1中。
177.表1
178.[0179][0180]
如表1所示,使用本发明的实施例1~9的基材1的硬质烧结体10均可用作产品。具体而言,关于在第1倾斜部6的槽的一部分或圆周方向的一部分发现裂纹或组织变差的硬质烧结体10,当对硬质烧结体10进行磨削加工而形成刃部51时,通过去除具有不良问题的部分作为排屑槽55而可以应对。并且,在实施例1~9中,关于实施例5、6、8,未发现裂纹的产生而得到良好的结果。
[0181]
另一方面,在比较例中,在圆周方向的整周产生裂纹,不可用作产品。
[0182]
产业上的可利用性
[0183]
根据本发明的硬质烧结体用基材、硬质烧结体及切削工具,能够抑制在硬质烧结体上产生裂纹。从而,具有产业上的可利用性。
[0184]
符号说明
[0185]
1(1a、1b、1c、1d、1e、1f、1g、1h)基材
[0186]
2小径部3大径部
[0187]
4基材端面5角部(基材角部)
[0188]
24角部(筒部角部)6第1倾斜部
[0189]
6a第1倾斜面(倾斜面)6b第1侧壁面(侧壁面)
[0190]
6e、6j凹曲面部6k凸曲面部
[0191]
10硬质烧结体20筒部
[0192]
23筒部端面25第2倾斜部
[0193]
50切削工具51刃部
[0194]
52柄部55排屑槽
[0195]
56切削刃c中心轴
[0196]
d大径部的外径(直径)gd第1倾斜部的径向最大深度
[0197]
gw第1倾斜部的圆周方向长度vp假想平面
[0198]
θ角度
再多了解一些
本文用于企业家、创业者技术爱好者查询,结果仅供参考。