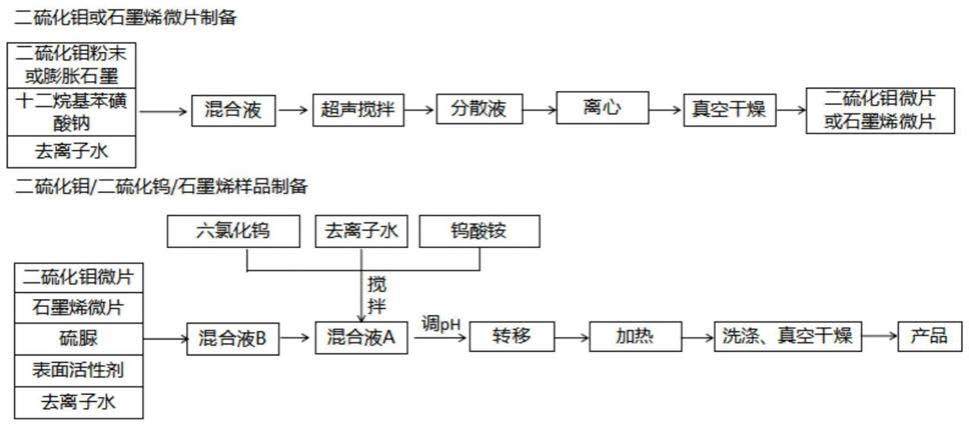
1.本发明属于二硫化钨her催化剂材料技术领域,涉及一种二硫化钨/二硫化钼/石墨烯复合材料及其制备方法、应用,尤其涉及一种具有层状结构的二硫化钨/二硫化钼/石墨烯复合材料及其制备方法、应用。
背景技术:
2.氢能是理想、清洁和高效的二次能源。电催化、光电催化分解水是氢气的重要来源之一,而高性能的电催化剂是电解水及光电分解水的核心。目前,广泛应用的水电解催化剂主要采用贵金属pt及其合金作为her催化剂,但是,pt基her催化剂的高成本及资源稀缺性严重制约了其作为her催化剂的广泛应用。寻找廉价、高活性、酸稳定的析氢催化剂已经是现在的研究热点。
3.二维过渡金属硫化物的化学式是mx2,m是指过渡金属元素(例如:钼、钨、铌、铼、钛),x是指硫族元素(例如:硫、硒、碲)。其具有的强自旋-轨道耦合作用与结构的多样性赋予这类材料许多新奇的物理性质,如在少数层1td相的wte2中观测到量子自旋霍尔效应,在少数层2h相的mos2与nbse2中观测到伊辛超导电性等。这些发现使得mx2材料成为当前凝聚态物理学和材料科学研究的一个热点。而且通常,单层过渡金属硫化物呈现一种x-m-x的三明治结构。层间的范德华力很弱,然而平面内有很坚固的共价键。块材过渡金属硫化物可以像石墨烯一样,被剥离成单层或者多层的纳米片。许多二维过渡金属硫化物的能带间隙在1~2ev范围内,随着层数的减少,能带间隙增加。一些二维过渡金属硫化物,例如钼和钨构成的硫族化合物,当材料为多层结构时,能带是间接带隙,当材料剥离成单层时,能带结构转变成了直接带隙。单层的二维过渡金属硫化物拥有直接带隙能带结构,可以提高光发射效率,为制备高性能光电器件带来了契机。
4.更值得注意的是,过渡金属二硫化物,例如mos2、ws2、mose2和wse2已被许多科学家催化使用氢气析出反应(her)。过渡金属二硫化合物具有独特的催化作用并且地球含量较多,这将成为生产氢气的一种简便且低成本的方式。虽然ws2是稳定的her的高活性催化剂,但是还需要进一步的提高,特别是传统方法制备的ws2,催化性能却并不理想,很多研究人员通过构建特殊的结构以及与其他材料复合来提高其催化性能。然而传统制备复合催化剂的方法主要有分步溶剂热法、cvd法、高温煅烧法等这些方法及工艺,成本高、复杂而繁琐。
5.因此,如何找到一种简单的复合方式,同时找到一种更为适宜的二硫化钨复合催化剂,能够利用简单的方法,改变ws2的催化活性,适于工业化推广和应用,已成为诸多一线研究人员和科研型企业亟待解决的问题之一。
技术实现要素:
6.有鉴于此,本发明要解决的技术问题在于提供一种二硫化钨/二硫化钼/石墨烯复合材料及其制备方法、应用,特别是一种具有层状结构的二硫化钨/二硫化钼/石墨烯复合
材料。本发明提供的二硫化钨复合材料,具有特定的层状结构,大大提高了二硫化钨催化活性的能力,从而提高了her性能,而且制备方法简单、条件温和,易操作以及成本低,能够更好的推动二硫化钨复合催化剂的商业化应用。
7.本发明提供了一种二硫化钨/二硫化钼/石墨烯复合材料,所述复合材料具有层状结构;
8.片状二硫化钨、片状二硫化钼和石墨烯片复合,形成层状结构。
9.优选的,所述片状二硫化钼和片状二硫化钨复合在所述石墨烯片层上;
10.所述片状二硫化钼包括二硫化钼微纳片;
11.所述片状二硫化钨包括二硫化钨微纳片;
12.所述石墨烯片包括石墨烯微纳片;
13.所述石墨烯片与所述片状二硫化钨的质量比为(0.5~2):10;
14.所述片状二硫化钼与片状二硫化钨的质量比为(0.5~2):1;
15.所述石墨烯片的片径为5~15μm。
16.优选的,所述石墨烯片的厚度为1~10nm;
17.所述片状二硫化钼的片径为5~10μm;
18.所述片状二硫化钼的厚度为5~12nm;
19.所述片状二硫化钨的片径为2~7μm;
20.所述片状二硫化钨的厚度为1~12nm;
21.所述复合包括层叠。
22.优选的,所述复合为通过静电吸附作用复合;
23.所述片状二硫化钼和片状二硫化钨分别复合在所述石墨烯片层上和/或所述片状二硫化钼和片状二硫化钨层叠复合在所述石墨烯片层上;
24.所述片状二硫化钼复合在所述片状二硫化钨和石墨烯片层之间;
25.所述复合材料具有褶皱的微观形貌;
26.所述褶皱包括山脉状褶皱和/或波浪状褶皱;
27.所述片状二硫化钨、片状二硫化钼和石墨烯片之间具有空隙。
28.本发明提供了一种二硫化钨/二硫化钼/石墨烯复合材料的制备方法,包括以下步骤:
29.1)将二硫化钼粉末、第一表面活性剂和水经过分散后,得到分散液,再通过离心和研磨后,得到二硫化钼微纳片;
30.将膨胀石墨、第二表面活性剂和水经过分散混合后,得到分散液,再通过离心和研磨后,得到石墨烯微纳片;
31.将六氯化钨、钨酸铵和水混合后,得到混合液a;
32.2)将上述步骤得到的二硫化钼微纳片、石墨烯微纳片、硫源、第三表面活性剂和水再次分散后,得到混合液b;
33.3)将上述步骤得到的混合液b和混合液a再次混合后,调节ph值,进行反应后,得到二硫化钨/二硫化钼/石墨烯复合材料。
34.优选的,所述第一表面活性剂包括十二烷基苯磺酸钠、n-月桂酰肌氨酸钠、十二烷基硫酸钠、脂肪醇醚硫酸钠和醇酰磷酸盐中的一种或多种;
35.所述二硫化钼粉末和第一表面活性剂的质量比为(1~5):100;
36.所述二硫化钼粉末与水的质量比为(0.5~3):100;
37.所述第二表面活性剂包括乙二胺、十八烷基三甲基氯化铵、聚醚酰亚胺、十六烷基二甲基烯丙基氯化铵、十四烷基二甲基苄基氯化铵、十二烷基二甲基羟乙基氯化铵和十二烷基三甲基氯化铵中的一种或多种;
38.所述膨胀石墨和第二表面活性剂的质量比为(1~5):100;
39.所述膨胀石墨与水的质量比为(0.5~3):100;
40.所述分散和分散混合的方式包括超声搅拌分散;
41.所述离心的过程具体为:先低速离心取上层液,再高速离心取下层液;
42.所述离心后还包括干燥步骤。
43.优选的,所述超声搅拌分散的超声频率为20~40khz;
44.所述超声搅拌分散的转速为300~500rpm;
45.所述超声搅拌分散的时间为120~360min;
46.所述低速离心的转速为500~1000rpm;
47.所述低速离心的时间为3~5min;
48.所述高速离心的转速为3000~5000rpm;
49.所述高速离心的时间为5~10min;
50.所述干燥为真空干燥。
51.优选的,所述干燥的温度为40~80℃;
52.所述干燥的时间为6~24h;
53.所述研磨的时间为30~60min;
54.所述研磨的转速为1000~1500rpm;
55.所述石墨烯微纳片和二硫化钼微纳片的细度为10~30μm;
56.所述六氯化钨与钨酸铵的摩尔比为(0.2~1):1;
57.所述二硫化钼微纳片与所述石墨烯微纳片的质量比为10:(0.5~2);
58.所述六氯化钨和钨酸铵的总摩尔数与所述硫源的摩尔比为1:(2.5~3);
59.所述硫源包括硫、硫脲、硫醇、三硫化铵、硫代乙酰胺和l-半胱氨酸中的一种或多种。
60.优选的,所述第三表面活性剂包括十六烷基三甲基溴化铵、十八烯、聚乙烯吡咯烷酮和f127中的一种或多种;
61.所述二硫化钼微纳片与所述第三表面活性剂的质量比为(1~10):100;
62.所述再次分散的方式为超声分散;
63.所述再次分散的时间为10~30min;
64.所述再次混合的方式为缓慢加入;
65.所述ph值为5~7;
66.所述反应的温度为160~240℃;
67.所述反应的时间为12~24h。
68.本发明还提供了上述技术方案任意一项所述的二硫化钨/二硫化钼/石墨烯复合材料或上述技术方案任意一项所述的制备方法所制备的二硫化钨/二硫化钼/石墨烯复合
材料在析氢反应方面的应用。
69.本发明提供了一种二硫化钨/二硫化钼/石墨烯复合材料,所述复合材料具有层状结构;片状二硫化钨、片状二硫化钼和石墨烯片复合,形成层状结构。与现有技术相比,本发明针对现有的ws2的催化性能还需要进一步提高,而且传统方法制备的ws2,催化性能并不理想,通过构建特殊的结构以及与其他材料复合来提高其催化性能。又存在方法及工艺复杂而繁琐,成本高的问题。
70.本发明创造性的设计了一种特殊结构的二硫化钨复合材料,本发明提供的二硫化钨复合材料,通过静电吸附作用,将二硫化钨、二硫化钼和石墨烯进行复合,具有特定的层状结构,是一种二硫化钨/二硫化钼/石墨烯层状复合材料,可以提供更多的活性部位和更高的活性表面积,大大提高了二硫化钨催化活性的能力,从而提高了her性能,表现出优异的催化析氢性能,有效的解决了单一过渡金属二硫化钨,只有边界处有催化活性而表面无催化活性的缺陷。
71.本发明提供的制备方法,相比传统的分步溶剂热法、cvd法、高温煅烧法,制备方法简单、条件温和,易操作以及成本低,能够更好的推动二硫化钨复合催化剂的商业化应用。本发明不仅为析氢领域提供了一种优良的催化剂,解决了传统析氢催化剂主要是pt等贵金属,成本高阻碍其大规模应用和商业化发展的桎梏,并且为制备复合型二维催化剂的合成提供了一个新的思路。
72.实验结果表明,本发明制备的二硫化钨/二硫化钼/石墨烯复合催化剂具有较小的tafel斜率(104mv/dec),表现出优异的析氢催化性能。
附图说明
73.图1为本发明实施例提供的二硫化钨/二硫化钼/石墨烯复合材料的具体制备工艺的流程简图;
74.图2为本发明实施例1制备的二硫化钨/二硫化钼/石墨烯复合材料的tem透射电镜图;
75.图3为本发明实施例2制备的二硫化钨/二硫化钼/石墨烯复合材料的hr-tem高倍透射电镜图;
76.图4为本发明实施例3制备的二硫化钨微纳片的tem透射电镜图;
77.图5为本发明实施例1制备的二硫化钨复合材料制备的催化剂和实施例3制备的二硫化钨制备的催化剂的极化曲线图;
78.图6为本发明实施例1制备的二硫化钨复合材料制备的催化剂和实施例3制备的二硫化钨制备的催化剂的塔菲尔曲线图;
79.图7为本发明实施例1制备的二硫化钨复合材料制备的催化剂和实施例3制备的二硫化钨制备的催化剂的电化学阻抗曲线图。
具体实施方式
80.为了进一步理解本发明,下面结合实施例对本发明优选实施方案进行描述,但是应当理解,这些描述只是为了进一步说明本发明的特征和优点,而不是对发明权利要求的限制。
81.本发明所有原料,对其来源没有特别限制,在市场上购买的或按照本领域技术人员熟知的常规方法制备的即可。
82.本发明所有原料,对其纯度没有特别限制,本发明优选采用分析纯或锂硫电池隔膜制备领域内使用的常规纯度。
83.本发明提供了一种二硫化钨/二硫化钼/石墨烯复合材料,所述复合材料具有层状结构;
84.片状二硫化钨、片状二硫化钼和石墨烯片复合,形成层状结构。
85.本发明原则上对所述复合的具体结构关系没有特别限制,本领域技术人员可以根据实际应用情况、产品要求及质量要求进行选择和调整,本发明为更好的保证复合材料特定的结构和形貌,提供更多的活性部位和更高的活性表面积,进而提高her性能,所述片状二硫化钼和片状二硫化钨优选复合在所述石墨烯片层上;更具体的,所述片状二硫化钼和片状二硫化钨优选分别复合在所述石墨烯片层上和/或所述片状二硫化钼和片状二硫化钨层叠复合在所述石墨烯片层上,更优选为片状二硫化钼和片状二硫化钨层叠复合在所述石墨烯片层上,更具体的,所述片状二硫化钼优选复合在所述片状二硫化钨和石墨烯片层之间。
86.本发明使用不同的表面活性剂对二硫化钼和石墨烯进行修饰,使二硫化钼片和石墨烯片表面分别带负电荷和正电荷,当修饰后的二硫化钼片和石墨烯片混合,石墨烯片会负载上二硫化钼,当再加入钨源后,钨正离子通过电荷作用会负载在二硫化钼的另一面,(由于石墨烯表面带正电荷会与钨正离子排斥,所以,大部分钨正离子不会负载在石墨烯片表面),在通过水热反应形成二硫化钨纳米片,得到二硫化钨/二硫化钼/石墨烯复合材料。
87.本发明原则上对所述复合的具体方式没有特别限制,本领域技术人员可以根据实际应用情况、产品要求及质量要求进行选择和调整,本发明为更好的保证复合材料特定的结构和形貌,提供更多的活性部位和更高的活性表面积,进而提高her性能,所述复合优选为通过静电吸附作用复合。
88.本发明原则上对所述复合的具体种类没有特别限制,本领域技术人员可以根据实际应用情况、产品要求及质量要求进行选择和调整,本发明为更好的保证复合材料特定的结构和形貌,提供更多的活性部位和更高的活性表面积,进而提高her性能,所述复合优选包括层叠。
89.本发明原则上对所述片状二硫化钼的具体参数没有特别限制,本领域技术人员可以根据实际应用情况、产品要求及质量要求进行选择和调整,本发明为更好的保证复合材料特定的结构和形貌,提供更多的活性部位和更高的活性表面积,进而提高her性能,所述片状二硫化钼优选包括二硫化钼微纳片。所述片状二硫化钼的片径优选为5~10μm,更优选为6~9μm,更优选为7~8μm。所述片状二硫化钼的厚度优选为5~12nm,更优选为6~11nm,更优选为7~10nm,更优选为8~9nm。
90.本发明原则上对所述片状二硫化钨的具体参数没有特别限制,本领域技术人员可以根据实际应用情况、产品要求及质量要求进行选择和调整,本发明为更好的保证复合材料特定的结构和形貌,提供更多的活性部位和更高的活性表面积,进而提高her性能,所述片状二硫化钨优选包括二硫化钨微纳片。所述片状二硫化钨的片径优选为2~7μm,更优选为3~6μm,优选为4~5μm。所述片状二硫化钨的厚度优选为1~12nm,更优选为3~10nm,更
优选为5~8nm。
91.本发明原则上对所述石墨烯片的具体参数没有特别限制,本领域技术人员可以根据实际应用情况、产品要求及质量要求进行选择和调整,本发明为更好的保证复合材料特定的结构和形貌,提供更多的活性部位和更高的活性表面积,进而提高her性能,所述石墨烯片优选包括石墨烯微纳片。所述石墨烯片的片径优选为5~15μm,更优选为7~13μm,优选为9~11μm。所述石墨烯片的厚度优选为1~10nm,更优选为3~8nm,更优选为5~6nm。
92.本发明原则上对所述复合材料中所述石墨烯片的比例没有特别限制,本领域技术人员可以根据实际应用情况、产品要求及质量要求进行选择和调整,本发明为更好的保证复合材料特定的结构和形貌,提供更多的活性部位和更高的活性表面积,进而提高her性能,所述石墨烯片与所述片状二硫化钨的质量比优选为(0.5~2):10,更优选为(0.8~1.7):10,更优选为(1.1~1.4):10。
93.本发明原则上对所述复合材料中所述片状二硫化钼的比例没有特别限制,本领域技术人员可以根据实际应用情况、产品要求及质量要求进行选择和调整,本发明为更好的保证复合材料特定的结构和形貌,提供更多的活性部位和更高的活性表面积,进而提高her性能,所述片状二硫化钼与片状二硫化钨的质量比优选为(0.5~2):1,更优选为(0.8~1.7):1,更优选为(1.1~1.4):1。
94.本发明原则上对所述复合材料的形貌没有特别限制,本领域技术人员可以根据实际应用情况、产品要求及质量要求进行选择和调整,本发明为更好的保证复合材料特定的结构和形貌,提供更多的活性部位和更高的活性表面积,进而提高her性能,所述复合材料优选具有褶皱的微观形貌,所述褶皱优选包括山脉状褶皱和/或波浪状褶皱,更优选为山脉状褶皱和波浪状褶皱。所述片状二硫化钨、片状二硫化钼和石墨烯片之间优选具有空隙。
95.本发明还提供了一种二硫化钨/二硫化钼/石墨烯复合材料的制备方法,包括以下步骤:
96.1)将二硫化钼粉末、第一表面活性剂和水经过分散后,得到分散液,再通过离心和研磨后,得到二硫化钼微纳片;
97.将膨胀石墨、第二表面活性剂和水经过分散混合后,得到分散液,再通过离心和研磨后,得到石墨烯微纳片;
98.将六氯化钨、钨酸铵和水混合后,得到混合液a;
99.2)将上述步骤得到的二硫化钼微纳片、石墨烯微纳片、硫源、第三表面活性剂和水再次分散后,得到混合液b;
100.3)将上述步骤得到的混合液b和混合液a再次混合后,调节ph值,进行反应后,得到二硫化钨/二硫化钼/石墨烯复合材料。
101.本发明首先将二硫化钼粉末、第一表面活性剂和水经过分散后,得到分散液,再通过离心和研磨后,得到二硫化钼微纳片;
102.将膨胀石墨、第二表面活性剂和水经过分散混合后,得到分散液,再通过离心和研磨后,得到石墨烯微纳片;
103.将六氯化钨、钨酸铵和水混合后,得到混合液a。
104.本发明原则上对所述第一表面活性剂的种类没有特别限制,本领域技术人员可以根据实际应用情况、产品要求及质量要求进行选择和调整,本发明为更好的保证复合材料
特定的结构和形貌,提供更多的活性部位和更高的活性表面积,进而提高her性能,所述第一表面活性剂优选包括十二烷基苯磺酸钠、n-月桂酰肌氨酸钠、十二烷基硫酸钠、脂肪醇醚硫酸钠和醇酰磷酸盐中的一种或多种,更优选包括十二烷基苯磺酸钠、n-月桂酰肌氨酸钠、十二烷基硫酸钠、脂肪醇醚硫酸钠或醇酰磷酸盐。
105.本发明原则上对所述第一表面活性剂的比例没有特别限制,本领域技术人员可以根据实际应用情况、产品要求及质量要求进行选择和调整,本发明为更好的保证复合材料特定的结构和形貌,提供更多的活性部位和更高的活性表面积,进而提高her性能,所述二硫化钼粉末和第一表面活性剂的质量比优选为(1~5):100,更优选为(1.5~4.5):100,更优选为(2~4):100,更优选为(2.5~3.5):100。
106.本发明原则上对所述水的比例没有特别限制,本领域技术人员可以根据实际应用情况、产品要求及质量要求进行选择和调整,本发明为更好的保证复合材料特定的结构和形貌,提供更多的活性部位和更高的活性表面积,进而提高her性能,所述二硫化钼粉末与水的质量比优选为(0.5~3):100,更优选为(1~2.5):100,更优选为(1.5~2):100。
107.本发明原则上所述第二表面活性剂的种类没有特别限制,本领域技术人员可以根据实际应用情况、产品要求及质量要求进行选择和调整,本发明为更好的保证复合材料特定的结构和形貌,提供更多的活性部位和更高的活性表面积,进而提高her性能,所述第二表面活性剂包括乙二胺、十八烷基三甲基氯化铵、聚醚酰亚胺、十六烷基二甲基烯丙基氯化铵、十四烷基二甲基苄基氯化铵、十二烷基二甲基羟乙基氯化铵和十二烷基三甲基氯化铵中的一种或多种,更优选为乙二胺、十八烷基三甲基氯化铵、聚醚酰亚胺、十六烷基二甲基烯丙基氯化铵、十四烷基二甲基苄基氯化铵、十二烷基二甲基羟乙基氯化铵或十二烷基三甲基氯化铵。
108.本发明原则上对所述第二表面活性剂的比例没有特别限制,本领域技术人员可以根据实际应用情况、产品要求及质量要求进行选择和调整,本发明为更好的保证复合材料特定的结构和形貌,提供更多的活性部位和更高的活性表面积,进而提高her性能,所述膨胀石墨和第二表面活性剂的质量比优选为(1~5):100,更优选为(1.5~4.5):100,更优选为(2~4):100,更优选为(2.5~3.5):100。
109.本发明原则上对所述水的比例没有特别限制,本领域技术人员可以根据实际应用情况、产品要求及质量要求进行选择和调整,本发明为更好的保证复合材料特定的结构和形貌,提供更多的活性部位和更高的活性表面积,进而提高her性能,所述膨胀石墨与水的质量比优选为(0.5~3):100,更优选为(1~2.5):100,更优选为(1.5~2):100。
110.本发明原则上对所述分散和分散混合的方式没有特别限制,本领域技术人员可以根据实际应用情况、产品要求及质量要求进行选择和调整,本发明为更好的保证复合材料特定的结构和形貌,提供更多的活性部位和更高的活性表面积,进而提高her性能,所述分散的方式优选包括超声搅拌分散。本发明所述分散混合的方式优选包括超声搅拌分散。
111.本发明原则上对所述超声搅拌分散的具体参数没有特别限制,本领域技术人员可以根据实际应用情况、产品要求及质量要求进行选择和调整,本发明为更好的保证复合材料特定的结构和形貌,提供更多的活性部位和更高的活性表面积,进而提高her性能,所述超声搅拌分散的超声频率优选为20~40khz,更优选为22~38khz,更优选为25~35khz,更优选为28~32khz。所述超声搅拌分散的转速优选为300~500rpm,更优选为330~480rpm,
更优选为350~450rpm,更优选为380~430rpm。所述超声搅拌分散的时间优选为120~360min,更优选为150~330min,更优选为180~300min,更优选为210~270min。
112.本发明原则上对所述离心的具体过程和参数没有特别限制,本领域技术人员可以根据实际应用情况、产品要求及质量要求进行选择和调整,本发明为更好的保证复合材料特定的结构和形貌,提供更多的活性部位和更高的活性表面积,进而提高her性能,所述离心的过程具体为:先低速离心取上层液,再高速离心取下层液。其中,所述低速离心的转速优选为500~1000rpm,更优选为600~900rpm,更优选为700~800rpm。所述低速离心的时间优选为3~5min,更优选为3.3~4.7min,更优选为3.6~4.4min,更优选为3.9~4.1min。所述高速离心的转速优选为3000~5000rpm,更优选为3300~4700rpm,更优选为3600~4400rpm,更优选为3900~4100rpm。所述高速离心的时间优选为5~10min,更优选为6~9min,更优选为7~8min。
113.本发明为完整和细化整体制备工艺,更好的保证复合材料特定的结构和形貌,提供更多的活性部位和更高的活性表面积,进而提高her性能,所述离心后优选还包括干燥步骤,所述干燥优选为真空干燥。具体的,所述干燥的温度优选为40~80℃,更优选为45~75℃,更优选为50~70℃,更优选为55~65℃。所述干燥的时间优选为6~24h,更优选为9~21h,更优选为12~18h。
114.本发明原则上对所述研磨的具体过程和参数没有特别限制,本领域技术人员可以根据实际应用情况、产品要求及质量要求进行选择和调整,本发明为更好的保证复合材料特定的结构和形貌,提供更多的活性部位和更高的活性表面积,进而提高her性能,所述研磨的时间优选为30~60min,更优选为35~55min,更优选为40~50min。所述研磨的转速优选为1000~1500rpm,更优选为1100~1400rpm,更优选为1200~1300rpm。
115.本发明原则上对所述研磨后的石墨烯微纳片的细度没有特别限制,本领域技术人员可以根据实际应用情况、产品要求及质量要求进行选择和调整,本发明为更好的保证复合材料特定的结构和形貌,提供更多的活性部位和更高的活性表面积,进而提高her性能,所述石墨烯微纳片的细度优选为10~30μm,更优选为12~28μm,更优选为15~25μm,更优选为17~22μm。
116.本发明原则上对所述研磨后的二硫化钼微纳片的细度没有特别限制,本领域技术人员可以根据实际应用情况、产品要求及质量要求进行选择和调整,本发明为更好的保证复合材料特定的结构和形貌,提供更多的活性部位和更高的活性表面积,进而提高her性能,所述二硫化钼微纳片的细度优选为10~30μm,更优选为12~28μm,更优选为15~25μm,更优选为17~22μm。
117.本发明原则上对所述六氯化钨与钨酸铵的摩尔比没有特别限制,本领域技术人员可以根据实际应用情况、产品要求及质量要求进行选择和调整,本发明为更好的保证复合材料特定的结构和形貌,提供更多的活性部位和更高的活性表面积,进而提高her性能,所述六氯化钨与钨酸铵的摩尔比优选为(0.2~1):1,更优选为(0.3~0.9):1,更优选为(0.4~0.8):1,更优选为(0.5~0.7):1。
118.本发明随后,将上述步骤得到的二硫化钼微纳片、石墨烯微纳片、硫源、第三表面活性剂和水再次分散后,得到混合液b。
119.本发明原则上对所述硫源的种类没有特别限制,本领域技术人员可以根据实际应
用情况、产品要求及质量要求进行选择和调整,本发明为更好的保证复合材料特定的结构和形貌,提供更多的活性部位和更高的活性表面积,进而提高her性能,所述硫源优选包括硫、硫脲、硫醇、三硫化铵、硫代乙酰胺和l-半胱氨酸中的一种或多种,更优选为硫、硫脲、硫醇、三硫化铵、硫代乙酰胺或l-半胱氨酸。
120.本发明原则上对所述硫源的加入量没有特别限制,本领域技术人员可以根据实际应用情况、产品要求及质量要求进行选择和调整,本发明为更好的保证复合材料特定的结构和形貌,提供更多的活性部位和更高的活性表面积,进而提高her性能,所述六氯化钨和钨酸铵的总摩尔数与所述硫源的摩尔比优选为1:(2.5~3),更优选为1:(2.6~2.9),更优选为1:(2.7~9)。
121.本发明原则上对所述二硫化钼微纳片与所述石墨烯微纳片的比例没有特别限制,本领域技术人员可以根据实际应用情况、产品要求及质量要求进行选择和调整,本发明为更好的保证复合材料特定的结构和形貌,提供更多的活性部位和更高的活性表面积,进而提高her性能,所述二硫化钼微纳片与所述石墨烯微纳片的质量比优选为10:(0.5~2),更优选为10:(0.8~1.7),更优选为10:(0.8~1.7)。
122.本发明原则上对所述第三表面活性剂的种类没有特别限制,本领域技术人员可以根据实际应用情况、产品要求及质量要求进行选择和调整,本发明为更好的保证复合材料特定的结构和形貌,提供更多的活性部位和更高的活性表面积,进而提高her性能,所述第三表面活性剂优选包括十六烷基三甲基溴化铵、十八烯、聚乙烯吡咯烷酮和f127中的一种或多种,更优选为十六烷基三甲基溴化铵、十八烯、聚乙烯吡咯烷酮或f127。
123.本发明原则上对所述二硫化钼微纳片与所述第三表面活性剂的质量比没有特别限制,本领域技术人员可以根据实际应用情况、产品要求及质量要求进行选择和调整,本发明为更好的保证复合材料特定的结构和形貌,提供更多的活性部位和更高的活性表面积,进而提高her性能,所述二硫化钼微纳片与所述第三表面活性剂的质量比优选为(1~10):100,更优选为(3~8):100,更优选为(5~6):100。
124.本发明原则上对所述再次分散的过程和参数没有特别限制,本领域技术人员可以根据实际应用情况、产品要求及质量要求进行选择和调整,本发明为更好的保证复合材料特定的结构和形貌,提供更多的活性部位和更高的活性表面积,进而提高her性能,所述再次分散的方式优选为超声分散,更具体的,所述再次分散的时间优选为10~30min,更优选为13~27min,更优选为16~24min,更优选为19~21min。
125.本发明最后,将上述步骤得到的混合液b和混合液a再次混合后,调节ph值,进行反应后,得到二硫化钨/二硫化钼/石墨烯复合材料。
126.本发明原则上对所述ph值没有特别限制,本领域技术人员可以根据实际应用情况、产品要求及质量要求进行选择和调整,本发明为更好的保证复合材料特定的结构和形貌,提供更多的活性部位和更高的活性表面积,进而提高her性能,所述ph值优选为5~7,更优选为5.3~6.7,更优选为5.6~6.4,更优选为5.9~6.1。
127.本发明原则上对所述反应的参数没有特别限制,本领域技术人员可以根据实际应用情况、产品要求及质量要求进行选择和调整,本发明为更好的保证复合材料特定的结构和形貌,提供更多的活性部位和更高的活性表面积,进而提高her性能,所述反应的温度优选为160~240℃,更优选为170~230℃,更优选为180~220℃,更优选为190~210℃。更具
体的,所述反应的时间优选为12~24h,更优选为14~22h,更优选为16~20h。
128.本发明为完整和细化整体制备工艺,更好的保证复合材料特定的结构和形貌,提供更多的活性部位和更高的活性表面积,进而提高her性能,上述二硫化钨/二硫化钼/石墨烯复合材料的制备方法具体可以为以下步骤:
129.将一定量的二硫化钼粉末、第一表面活性剂加入到去离子水中,经过超声分散形成分散液;然后通过低速离心,取上层液,再经过高速离心取下层,最后真空干燥烘干、研磨,形成二硫化钼微纳片;
130.将一定量的膨胀石墨、第二表面活性剂加入到去离子水中,经过超声分散形成分散液;然后通过低速离心,取上层液,再经过高速离心取下层,最后真空干燥烘干、研磨,形成石墨烯微纳片;
131.将一定质量的六氯化钨和钨酸铵加入到去离子水中,磁力搅拌,形成混合a溶液;
132.将一定质量的二硫化钼微纳片、石墨烯微纳片、硫源以及第三表面活性剂加入到水中,超声分散,形成混合溶液b;
133.混合溶液b缓慢加入到a溶液中,调节ph值,然后转移到内衬为聚四氟乙烯的不锈钢反应釜中,加热反应一段时间,自然冷却,离心、去离子水及无水乙醇洗涤三次、最后在真空干燥,研磨得到二硫化钨/二硫化钼/石墨烯复合材料。
134.参看图1,图1为本发明实施例提供的二硫化钨/二硫化钼/石墨烯复合材料的具体制备工艺的流程简图。
135.本发明还提供了上述技术方案任意一项所述的二硫化钨/二硫化钼/石墨烯复合材料或上述技术方案任意一项所述的制备方法所制备的二硫化钨/二硫化钼/石墨烯复合材料在析氢反应方面的应用。
136.本发明上述步骤提供了一种具有层状结构的二硫化钨/二硫化钼/石墨烯复合材料及其制备方法、应用。本发明提供的具有特殊层状结构的二硫化钨复合材料,本发明提供的二硫化钨复合材料,通过静电吸附作用,将二硫化钨、二硫化钼和石墨烯进行复合,具有特定的层状结构,特别能够形成二硫化钨/二硫化钼/石墨烯有序层叠的复合材料,可以提供更多的活性部位和更高的活性表面积,大大提高了二硫化钨催化活性的能力,从而提高了her性能,表现出优异的催化析氢性能,有效的解决了单一过渡金属二硫化钨,只有边界处有催化活性而表面无催化活性的缺陷。
137.本发明提供的制备方法,相比传统的分步溶剂热法、cvd法、高温煅烧法,制备方法简单、条件温和,易操作以及成本低,能够更好的推动二硫化钨复合催化剂的商业化应用。本发明不仅为析氢领域提供了一种优良的催化剂,解决了传统析氢催化剂主要是pt等贵金属,成本高阻碍其大规模应用和商业化发展的桎梏,并且为制备复合型二维催化剂的合成提供了一个新的思路。
138.实验结果表明,本发明制备的二硫化钨/二硫化钼/石墨烯复合催化剂具有较小的tafel斜率(104mv/dec),表现出优异的析氢催化性能。
139.为了进一步说明本发明,以下结合实施例对本发明提供的一种二硫化钨/二硫化钼/石墨烯复合材料及其制备方法、应用进行了详细描述,但是应当理解,这些实施例是在以本发明技术方案为前提下进行实施,给出了详细的实施方式和具体的操作过程,只是为进一步说明本发明的特征和优点,而不是对本发明权利要求的限制,本发明的保护范围也
不限于下述的实施例。
140.实施例1
141.将一定量的二硫化钼粉末、十二烷基硫酸钠加入到去离子水中,二硫化钼粉与去离子水质量比为1:100,形成混合液,经过超声分散120min,形成分散液;随后先低速500rmp/min离心5min,取上层溶液,再通过高速离心,速率为5000r/min,离心10min,取下层溶液、洗涤;然后放在60℃真空干燥中过夜烘干、研磨,形成二硫化钼微纳片。
142.将一定量的膨胀石墨、十八烷基三甲基氯化铵加入到去离子水中,膨胀石墨与去离子水质量比为1:100,形成混合液,经过超声分散120min,形成分散液;随后先低速500rmp/min离心5min,取上层溶液,再通过高速离心,速率为5000r/min,离心10min,取下层溶液、洗涤;然后放在60℃真空干燥中过夜烘干、研磨,形成石墨烯微纳片。
143.将1.1896g六氯化钨和0.8517g钨酸铵加入到36ml去离子水中,磁力搅拌10min,形成混合a溶液;
144.将0.7439g二硫化钼微纳片、0.0744g石墨烯微纳片、2.2836g硫脲以及一定质量的聚乙烯吡咯烷酮加入到36ml去离子水中,超声分散30min,形成混合溶液b;
145.混合溶液b缓慢加入到a溶液中,调节ph值5~7,然后转移到内衬为聚四氟乙烯的不锈钢反应釜中,200℃反应24h,自然冷却,离心、去离子水和无水乙醇洗涤三次、最后在真空干燥,研磨得到二硫化钨/二硫化钼/石墨烯复合材料。
146.对本发明实施例1制备的二硫化钨/二硫化钼/石墨烯复合材料进行表征。
147.参见图2,图2为本发明实施例1制备的二硫化钨/二硫化钼/石墨烯复合材料的tem透射电镜图。
148.由图2结合后续图4可知,本发明制备的二硫化钨/二硫化钼/石墨烯复合材料具有明显的层叠结构,层状的二硫化钨微纳片、层状的二硫化钼微纳片以及石墨烯片层有序的层叠在一起,三种层状材料具有微米级的片径和纳米级的厚度,而且复合材料整体具有类似与山脉或波浪式的褶皱微观形貌。进一步基于常识判断,片状二硫化钨、片状二硫化钼和石墨烯片之间应具有空隙,更多的都是不规则形状的空隙。
149.对本发明实施例1制备的二硫化钨/二硫化钼/石墨烯复合材料进行性能检测。具体检测结果参见后续实施例3中的对比检测结果。
150.实施例2
151.将一定量的二硫化钼粉末、十二烷基硫酸钠加入到去离子水中,二硫化钼粉与去离子水质量比为1:100,形成混合液,经过超声分散120min,形成分散液;随后先低速500rmp/min离心5min,取上层溶液,再通过高速离心,速率为5000r/min,离心10min,取下层溶液、洗涤;然后放在60℃真空干燥中过夜烘干、研磨,形成二硫化钼微纳片。
152.将一定量的膨胀石墨、十八烷基三甲基氯化铵加入到去离子水中,膨胀石墨与去离子水质量比为1:100,形成混合液,经过超声分散120min,形成分散液;随后先低速500rmp/min离心5min,取上层溶液,再通过高速离心,速率为5000r/min,离心10min,取下层溶液、洗涤;然后放在60℃真空干燥中过夜烘干、研磨,形成石墨烯微纳片。
153.将1.1896g六氯化钨和0.8517g钨酸铵加入到36ml去离子水中,磁力搅拌10min,形成混合a溶液;
154.将0.7439g二硫化钼微纳片、0.0744g石墨烯微纳片、2.2836g硫脲以及一定质量的
聚乙烯吡咯烷酮加入到36ml去离子水中,超声分散30min,形成混合溶液b;
155.混合溶液b缓慢加入到a溶液中,调节ph值5~7,然后转移到内衬为聚四氟乙烯的不锈钢反应釜中,160℃反应24h,自然冷却,离心、去离子水和无水乙醇洗涤三次、最后在真空干燥,研磨得到二硫化钨/二硫化钼/石墨烯复合材料。
156.对本发明实施例2制备的二硫化钨/二硫化钼/石墨烯复合材料进行表征。
157.参见图3,图3为本发明实施例2制备的二硫化钨/二硫化钼/石墨烯复合材料的hr-tem高倍透射电镜图。
158.由图3可知,本发明制备的二硫化钨/二硫化钼/石墨烯复合材料具有明显的层叠结构,层状的二硫化钨微纳片、层状的二硫化钼微纳片以及石墨烯片层有序的层叠在一起,三种层状材料具有微米级的片径和纳米级的厚度,而且复合材料整体具有类似与山脉或波浪式的褶皱微观形貌。进一步基于常识判断,片状二硫化钨、片状二硫化钼和石墨烯片之间应具有空隙,更多的都是不规则形状的空隙。
159.实施例3
160.将1.1896g六氯化钨和0.8517g钨酸铵加入到36ml去离子水中,磁力搅拌10min,形成混合a溶液;
161.2.2836g硫脲以及一定质量的聚乙烯吡咯烷酮加入到36ml去离子水中,超声分散30min,形成混合溶液b;
162.混合溶液b缓慢加入到a溶液中,然后转移到内衬为聚四氟乙烯的不锈钢反应釜中,220℃反应24h,自然冷却,离心、去离子水和无水乙醇洗涤三次、最后在真空干燥,研磨得到二硫化钨材料。
163.对本发明实施例3制备的二硫化钨材料进行表征。
164.参见图4,图4为本发明实施例3制备的二硫化钨微纳片的tem透射电镜图。
165.对本发明实施例1制备的二硫化钨/二硫化钼/石墨烯复合材料与实施例3制备的二硫化钨材料进行对比性能检测。
166.电极的制备
167.制备的复合材料催化剂涂覆在玻碳电极上作为电催化产氢电极,用于电催化析氢。
168.旋转圆盘玻碳电极作为工作电极,使用氧化铝溶液对其表面进行抛光预清理后自然晒干。将复合材料催化剂与酒精水溶液(v/v=7:3)混合,超声分散均匀后(每次使用都需要超声均匀),用数字电动移液器量取14.5μl混合液,涂覆在旋转圆盘玻碳电极上,在洁净环境中自然晾干,进行电化学测试。
169.电化学测试方法
170.催化剂的电化学性能是通过电化学工作站来测量的。电化学工作站通过三电极体系与h型电解槽连接,电解质为1m koh水溶液,同时外接电脑设备将电信号及时传输到电脑中,通过分析具体数据得到材料的性能指标。
171.参见图5,图5为本发明实施例1制备的二硫化钨复合材料制备的催化剂和实施例3制备的二硫化钨制备的催化剂的极化曲线图。
172.由图5可以看出,本发明制备的二硫化钨复合材料催化剂,析氢催化活性最好。
173.参见图6,图6为本发明实施例1制备的二硫化钨复合材料制备的催化剂和实施例3
制备的二硫化钨制备的催化剂的塔菲尔曲线图。
174.由图6可以看出,塔菲尔斜率作为评价电催化剂优劣的固有性质的基准,实施例1制备的催化剂和纯二硫化钨催化剂样品的tafel斜率(104和207mv/dec)。随着过电位的增大,实施例1制备的催化剂的电流密度增加的越快,会容易的达到更快的析氢反应速率,较小的塔菲尔斜率,表明实施实例1制备的催化剂具有优越的催化性能。
175.对本发明实施例1制备的二硫化钨/二硫化钼/石墨烯复合材料与实施例3制备的二硫化钨材料进行对比电化学性能检测。
176.参见图7,图7为本发明实施例1制备的二硫化钨复合材料制备的催化剂和实施例3制备的二硫化钨制备的催化剂的电化学阻抗曲线图。
177.由图7可以看出,本发明制备的复合材料催化剂交流阻抗曲线的半圆半径小于与纯二硫化钨催化剂的交流阻抗曲线的半圆半径,说明实施例1制备的催化剂电子传输速率好。
178.实施例4
179.将一定量的二硫化钼粉末、十二烷基硫酸钠加入到去离子水中,二硫化钼粉与去离子水质量比为1:100,形成混合液,经过超声分散120min,形成分散液;随后先低速500rmp/min离心5min,取上层溶液,再通过高速离心,速率为5000r/min,离心10min,取下层溶液、洗涤;然后放在60℃真空干燥中过夜烘干、研磨,形成二硫化钼微纳片。
180.将一定量的膨胀石墨、十八烷基三甲基氯化铵加入到去离子水中,膨胀石墨与去离子水质量比为1:100,形成混合液,经过超声分散120min,形成分散液;随后先低速500rmp/min离心5min,取上层溶液,再通过高速离心,速率为5000r/min,离心10min,取下层溶液、洗涤;然后放在60℃真空干燥中过夜烘干、研磨,形成石墨烯微纳片。
181.将1.1896g六氯化钨和0.8517g钨酸铵加入到36ml去离子水中,磁力搅拌10min,形成混合a溶液;
182.将0.7439g二硫化钼微纳片、0.0372g石墨烯微纳片、2.2836g硫脲以及一定质量的聚乙烯吡咯烷酮加入到36ml去离子水中,超声分散30min,形成混合溶液b;
183.混合溶液b缓慢加入到a溶液中,调节ph值5~7,然后转移到内衬为聚四氟乙烯的不锈钢反应釜中,200℃反应24h,自然冷却,离心、去离子水和无水乙醇洗涤三次、最后在真空干燥,研磨得到二硫化钨/二硫化钼/石墨烯复合材料。
184.对本发明实施例4制备的二硫化钨/二硫化钼/石墨烯复合材料进行表征。
185.结果表明,实施例4制备的二硫化钨/二硫化钼/石墨烯复合材料具有相似的有序层叠复合的层状形貌。
186.实施例5
187.将一定量的二硫化钼粉末、十二烷基硫酸钠加入到去离子水中,二硫化钼粉与去离子水质量比为1:100,形成混合液,经过超声分散120min,形成分散液;随后先低速500rmp/min离心5min,取上层溶液,再通过高速离心,速率为5000r/min,离心10min,取下层溶液、洗涤;然后放在60℃真空干燥中过夜烘干、研磨,形成二硫化钼微纳片。
188.将一定量的膨胀石墨、十八烷基三甲基氯化铵加入到去离子水中,膨胀石墨与去离子水质量比为1:100,形成混合液,经过超声分散120min,形成分散液;随后先低速500rmp/min离心5min,取上层溶液,再通过高速离心,速率为5000r/min,离心10min,取下层
溶液、洗涤;然后放在60℃真空干燥中过夜烘干、研磨,形成石墨烯微纳片。
189.将1.1896g六氯化钨和0.8517g钨酸铵加入到36ml去离子水中,磁力搅拌10min,形成混合a溶液;
190.将0.7439g二硫化钼微纳片、0.1498g石墨烯微纳片、2.2836g硫脲以及一定质量的聚乙烯吡咯烷酮加入到36ml去离子水中,超声分散30min,形成混合溶液b;
191.混合溶液b缓慢加入到a溶液中,调节ph值5~7,然后转移到内衬为聚四氟乙烯的不锈钢反应釜中,160℃反应24h,自然冷却,离心、去离子水和无水乙醇洗涤三次、最后在真空干燥,研磨得到二硫化钨/二硫化钼/石墨烯复合材料
192.对本发明实施例5制备的二硫化钨/二硫化钼/石墨烯复合材料进行表征。
193.结果表明,实施例5制备的二硫化钨/二硫化钼/石墨烯复合材料具有相似的有序层叠复合的层状形貌。
194.以上对本发明提供的一种具有层状结构的二硫化钨/二硫化钼/石墨烯复合材料及其制备方法、应用进行了详细的介绍,本文中应用了具体个例对本发明的原理及实施方式进行了阐述,以上实施例的说明只是用于帮助理解本发明的方法及其核心思想,包括最佳方式,并且也使得本领域的任何技术人员都能够实践本发明,包括制造和使用任何装置或系统,和实施任何结合的方法。应当指出,对于本技术领域的普通技术人员来说,在不脱离本发明原理的前提下,还可以对本发明进行若干改进和修饰,这些改进和修饰也落入本发明权利要求的保护范围内。本发明专利保护的范围通过权利要求来限定,并可包括本领域技术人员能够想到的其他实施例。如果这些其他实施例具有不是不同于权利要求文字表述的结构要素,或者如果它们包括与权利要求的文字表述无实质差异的等同结构要素,那么这些其他实施例也应包含在权利要求的范围内。
再多了解一些
本文用于企业家、创业者技术爱好者查询,结果仅供参考。