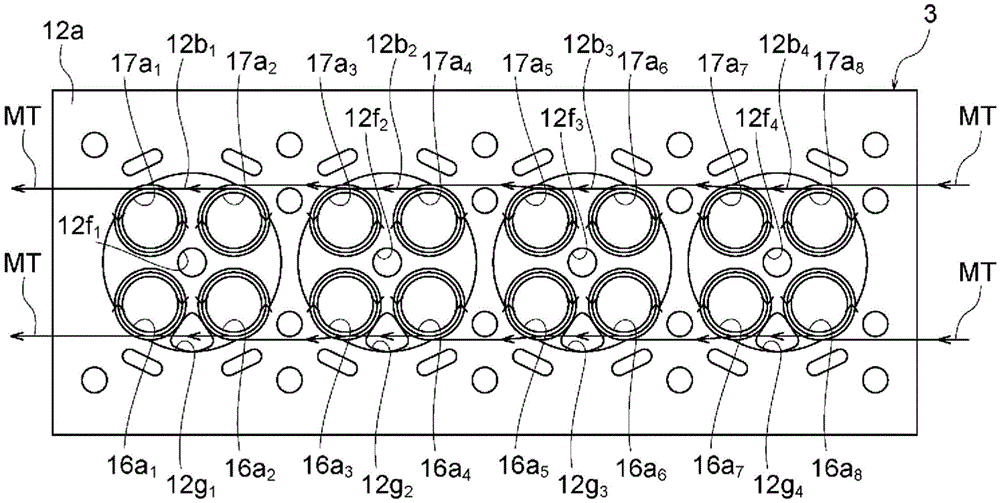
本发明涉及一种基于冷喷法的成膜方法。
背景技术
公知有如下滑动构件的制造方法:通过利用冷喷法向发动机气门的落座部吹送金属等的原料粉末,能够形成具有优异的高温耐磨性的气门座(专利文献1)。
现有技术文献
专利文献
专利文献1:国际公开第2017/022505号说明书
技术实现要素:
发明要解决的问题
汽车用发动机由于多气门化而具备多个进气门和排气门。因此,在利用冷喷法在多个气门的落座部形成气门座的情况下,需要使气缸盖和冷喷装置的喷嘴相对地移动而使多个落座部和喷嘴依次相对,并且,从喷嘴向与喷嘴相对的落座部喷出并吹送原料粉末。
冷喷装置若中断原料粉末的喷射,则直到再次稳定地吹送原料粉末为止需要几分钟的待机时间。因此,期望的是,不中断而尽量连续地进行原料粉末的喷射。然而,在形成一个气门座膜的情况下,以描绘360°的圆的方式使喷嘴和气缸盖相对移动,但在圆轨迹的成膜起点和成膜终点处产生了重叠部分,或者为了从成膜终点起形成下一个气门座膜,产生了喷嘴的移动速度成为零的折返点。
在此,在折返点产生在重叠部分的第1层的轨迹中,第1层的起点的表面的倾斜角度变得陡峭,若向此处喷射第2层,则阻碍原料粉末的扁平化,成为疏松的覆膜。
本发明要解决的问题在于提供一种能够抑制形成疏松的覆膜的冷喷涂式的成膜方法。
用于解决问题的方案
本发明通过如下方案解决上述问题:一种成膜方法,在该成膜方法中,沿着由相对于不相互连续的多个被成膜部的轨迹和连结该相对于多个被成膜部的轨迹的连接轨迹构成的连续的移动轨迹连续地喷射原料粉末,形成覆膜,其中,将移动轨迹中的工件与喷嘴之间的相对速度变低的折返点设定于连接轨迹上。
发明的效果
根据本发明,移动轨迹中的工件与喷嘴之间的相对速度变低的折返点设定于连接轨迹上,因此,折返点不会成为重叠部的第1层的覆膜。其结果,能够抑制形成疏松的覆膜。
附图说明
图1是表示使用本发明的冷喷装置来形成气门座膜的气缸盖的剖视图。
图2是图1的气门周边的放大剖视图。
图3是表示本发明的冷喷装置的一实施方式的构成图。
图4是表示本发明的冷喷装置的一实施方式的喷枪的主视图。
图5是沿着图4的V-V线的剖视图。
图6是表示使图4的喷枪偏置了的状态的主视图。
图7是表示包括本发明的冷喷装置的成膜工厂的主视图。
图8是图7的俯视图。
图9是表示使用本发明的冷喷装置来制造气缸盖的顺序的工序图。
图10是使用本发明的冷喷装置来形成气门座膜的气缸盖毛坯的立体图。
图11是沿着图10的XI-XI线的表示进气口的剖视图。
图12是表示利用切削工序在图11的进气口形成有环状气门座部的状态的剖视图。
图13是表示在图12的进气口形成气门座膜的状态的剖视图。
图14是表示形成有气门座膜的进气口的剖视图。
图15是表示图9的精加工工序后的进气口的剖视图。
图16是表示在本发明的成膜方法中冷喷装置的喷嘴在端口的开口部上移动之际的移动轨迹的一个例子的气缸盖毛坯的俯视图。
图17是表示相对于图16的一个进气口的移动轨迹的俯视图。
图18是表示以图17的移动轨迹进行了成膜的情况的覆膜截面的图。
图19是表示相对于一个进气口的移动轨迹的另一个例子的俯视图。
图20是表示在成膜起点与成膜终点的重叠部设定折返点而进行了成膜的比较例的移动轨迹的图。
图21是表示以图20的比较例的移动轨迹进行了成膜的覆膜截面的图。
具体实施方式
以下,基于附图说明本发明的一实施方式。首先,对优选适用本实施方式的冷喷装置的、具备气门座膜的内燃机1进行说明。图1是内燃机1的剖视图,主要表示气缸盖周围的结构。
内燃机1具备气缸体11和组装到气缸体11的上部的气缸盖12。该内燃机1例如是直列4气缸的汽油发动机,气缸体11具有在附图进深方向上排列着的4个气缸11a。各气缸11a收纳沿图中的上下方向往复移动的活塞13,各活塞13借助连杆13a与在附图进深方向上延伸的曲轴14连结。
在气缸盖12的向气缸体11安装的安装面12a的与各气缸11a相对应的位置形成有构成各气缸的燃烧室15的4个凹部12b。燃烧室15是用于使燃料与吸入空气的混合气体燃烧的空间,由气缸盖12的凹部12b、活塞13的顶面13b、以及气缸11a的内周面构成。
气缸盖12具备连通燃烧室15和气缸盖12的一侧面12c的进气口16。进气口16设为弯曲的大致圆筒形状,向燃烧室15内引导来自与侧面12c连接着的进气歧管(未图示)的吸入空气。另外,气缸盖12具备连通燃烧室15和气缸盖12的另一侧面12d的排气口17。排气口17与进气口16同样地设为弯曲的大致圆筒形状,向与侧面12d连接着的排气歧管(未图示)排出在燃烧室15产生的排气。此外,本实施方式的内燃机1针对1个气缸11a设置有两个进气口16和两个排气口17。
气缸盖12具备使进气口16相对于燃烧室15开闭的进气门18和使排气口17相对于燃烧室15开闭的排气门19。进气门18和排气门19分别具备圆棒状的气门杆18a、19a和设置到气门杆18a、19a的顶端的圆盘状的气门头18b、19b。气门杆18a、19a滑动自如地贯穿大致圆筒形状的气门引导件18c、19c,该大致圆筒形状的气门引导件18c、19c组装到气缸盖12。由此,进气门18和排气门19分别相对于燃烧室15沿着气门杆18a、19a的轴向移动自如。
在图2中放大地表示燃烧室15与进气口16之间的连通部分、和燃烧室15与排气口17之间的连通部分。进气口16在与燃烧室15之间的连通部分设置有大致圆形的开口部16a。在该开口部16a的环状缘部形成有与进气门18的气门头18b抵接的环状的气门座膜16b。并且,若进气门18沿着气门杆18a的轴向向上方移动,则气门头18b的上表面与气门座膜16b抵接而封堵进气口16。相反,若进气门18沿着气门杆18a的轴向向下方移动,则在气门头18b的上表面与气门座膜16b之间形成间隙而使进气口16开放。
排气口17与进气口16同样地在与燃烧室15之间的连通部分设置有大致圆形的开口部17a,在该开口部17a的环状缘部形成有与排气门19的气门头19b抵接的环状的气门座膜17b。并且,若排气门19沿着气门杆19a的轴向向上方移动,则气门头19b的上表面与气门座膜17b抵接而封堵排气口17。相反,若排气门19沿着气门杆19a的轴向向下方移动,则在气门头19b的上表面与气门座膜17b之间形成间隙而使排气口17开放。此外,进气口16的开口部16a的直径设定得比排气口17的开口部17a的直径大。
在4循环的内燃机1中,在活塞13下降时仅打开进气门18,由此,从进气口16向气缸11a内导入混合气体(进气冲程)。接下来,设为使进气门18和排气门19关闭了的状态,使活塞13上升到大致上止点而压缩气缸11a内的混合气体(压缩冲程)。然后,在活塞13到达了大致上止点时,利用火花塞对压缩后的混合气体点火而使该混合气体爆燃。由于该爆燃,活塞13下降到下止点,借助所连结的曲轴14将爆燃转换成旋转力(燃烧·膨胀冲程)。最后,若活塞13到达下止点并再次开始上升,则仅打开排气门19,向排气口17排出气缸11a内的排气(排气冲程)。内燃机1通过反复进行以上的循环而产生输出。
气门座膜16b、17b是利用冷喷法在气缸盖12的开口部16a、17a的环状缘部直接形成的。冷喷法是指如下方法:使比原料粉末的熔点或软化点低的温度的工作气体成为超音速流,将由输送气体输送来的原料粉末投入工作气体中并从喷嘴顶端喷射,使该原料粉末以固相状态直接与基材碰撞,利用原料粉末的塑性变形形成覆膜。该冷喷法与使材料熔融并附着于基材的喷镀法相比具有如下特性:获得没有在大气中氧化的致密的覆膜,对材料颗粒的热影响较少,因此,热变质被抑制,成膜速度较快,能够厚膜化,附着效率较高。特别是由于成膜速度较速,能够形成厚膜,所以适于作为内燃机1的气门座膜16b、17b这样的构造材料的用途。
图3是示意性地表示在上述的气门座膜16b、17b的形成中所使用的本实施方式的冷喷装置2的图。本实施方式的冷喷装置2具备:气体供给部21,其供给工作气体和输送气体;原料粉末供给部22,其供给气门座膜16b、17b的原料粉末;以及喷枪23,其使用原料粉末的熔点以下的工作气体以超音速流喷射该原料粉末;以及制冷剂循环回路27,其冷却喷嘴23d。
气体供给部21具备压缩气瓶21a、工作气体管线21b以及输送气体管线21c。工作气体管线21b和输送气体管线21c分别具备压力调整器21d、流量调节阀21e、流量计21f以及压力计21g。压力调整器21d、流量调节阀21e、流量计21f以及压力计21g提供于来自压缩气瓶21a的工作气体和输送气体各自的压力和流量的调整。
在工作气体管线21b设置有带状加热器等加热器21i,通过借助供电线21j、21j从电力源21h向该加热器21i供给电力,该加热器21i加热工作气体管线21b。工作气体在被加热器21i加热成比原料粉末的熔点或软化点低的温度之后导入向喷枪23的腔室23a内。在腔室23a设置有压力计23b和温度计23c,借助各信号线23g、23g检测到的压力值和温度值向控制器(未图示)输出,提供于压力和温度的反馈控制。
另一方面,原料粉末供给部22具备原料粉末供给装置22a以及附设于该原料粉末供给装置22a的计量器22b和原料粉末供给管线22c。来自压缩气瓶21a的输送气体经由输送气体管线21c导入原料粉末供给装置22a。由计量器22b计量后的预定量的原料粉末经由原料粉末供给管线22c向腔室23a内输送。
喷枪23利用工作气体从喷嘴23d的顶端以超音速流喷射由输送气体输送到腔室23a内的原料粉末P,以固相状态或固液共存状态使该原料粉末P与基材24碰撞而形成覆膜24a。在本实施方式中,适用气缸盖12作为基材24,利用冷喷法向该气缸盖12的开口部16a、17a的环状缘部喷射原料粉末P,从而形成了气门座膜16b、17b。
喷嘴23d在其内部设置有供水等制冷剂流动的流路(未图示)。喷嘴23d在其顶端设置有向流路导入制冷剂的制冷剂导入部23e,在其基端设置有排出流路内的制冷剂的制冷剂排出部23f。喷嘴23d从制冷剂导入部23e向流路导入制冷剂,使制冷剂向流路内流动,从制冷剂排出部23f排出制冷剂,从而冷却喷嘴23d。
使制冷剂向喷嘴23d的流路循环的制冷剂循环回路27具备:罐271,其积存制冷剂;导入管274,其与上述的制冷剂导入部23e连接起来;泵272,其与导入管274连接,使制冷剂在罐271与喷嘴23d之间流动;冷却器273,其冷却制冷剂;以及排出管275,其与制冷剂排出部23f连接起来。冷却器273例如包括换热机等,使喷嘴23d冷却而温度上升了的制冷剂与空气、水、气体等制冷剂之间换热而冷却制冷剂。
制冷剂循环回路27利用泵272抽吸已积存到罐271的制冷剂,经由冷却器273向制冷剂导入部23e供给制冷剂。供给到制冷剂导入部23e的制冷剂在喷嘴23d内的流路中从前端侧朝向后端侧流动,在这期间内与喷嘴23d换热,从而冷却喷嘴23d。流动到流路的后端侧的制冷剂从制冷剂排出部23f向排出管275排出,返回罐271。如此,制冷剂循环回路27一边冷却制冷剂一边使制冷剂循环而冷却喷嘴23d,因此,能够抑制原料粉末P向喷嘴23d的喷射通路附着。
针对气缸盖12的气门座要求能经得住来自燃烧室15内的气门的敲击输入的较高的耐热性和耐磨性、燃烧室15的冷却用的较高的导热性。针对这些要求,根据由例如析出硬化型铜合金的粉末形成的气门座膜16b、17b,能够获得比由铸件用铝合金形成的气缸盖12硬、且耐热性和耐磨性优异的气门座。
另外,气门座膜16b、17b直接形成于气缸盖12,因此,与将独立零部件的座圈压入端口开口部而形成的以往的气门座相比,能够获得较高的导热性。进而,与利用独立零部件的座圈的情况相比,除了能够谋求与冷却用的水套之间的接近化之外,还能够获得由进气口16和排气口17的喉径的扩大、端口形状的最佳化带来的滚流的促进等次要的效果。
作为在气门座膜16b、17b的形成中所使用的原料粉末P,优选是比铸件用铝合金硬质、且能获得气门座所需要的耐热性、耐磨性以及导热性的金属,例如,优选使用上述的析出硬化型铜合金。另外,作为析出硬化型铜合金,也可以使用含有镍和硅的科森合金、含有铬的铬铜、含有锆的锆铜等。而且,例如,也能够适用含有镍、硅以及铬的析出硬化型铜合金、含有镍、硅以及锆的析出硬化型铜合金、含有镍、硅、铬以及锆的析出硬化型合金、含有铬和锆的析出硬化型铜合金等。
另外,也可以混合多种原料粉末、例如第1原料粉末和第2原料粉末而形成气门座膜16b、17b。在该情况下,第1原料粉末优选使用比铸件用铝合金硬质、且能获得气门座所需要的耐热性、耐磨性以及导热性的金属,例如,优选使用上述的析出硬化型铜合金。另外,作为第2原料粉末,优选使用比第1原料粉末硬质的金属。该第2原料粉末例如也可以适用铁基合金、钴基合金、铬基合金、镍基合金、钼基合金等合金、陶瓷等。另外,也可以单独使用这些金属的1种、或适当组合使用两种以上。
混合第1原料粉末和比第1原料粉末硬质的第2原料粉末而形成的气门座膜能够获得比仅由析出硬化型铜合金形成的气门座膜优异的耐热性、耐磨性。认为获得这样的效果的原因在于,存在于气缸盖12的表面的氧化覆膜被第2原料粉末去除而暴露形成新生界面,气缸盖12与金属覆膜之间的密合性提高。另外,也认为其原因在于,由于由第2原料粉末嵌入气缸盖12带来的锚固效果,气缸盖12与金属覆膜之间的密合性提高。还认为其原因在于,在第1原料粉末碰撞到第2原料粉末时,其动能的一部分转换成热能,或者由于第1原料粉末的一部分在塑性变形的过程中所产生的热,用作第1原料粉末的析出硬化型铜合金的一部分的析出硬化被更加促进。
本实施方式的冷喷装置2将形成有气门座膜16b、17b的气缸盖12固定于基座45,另一方面,使喷枪23的喷嘴23d的顶端沿着气缸盖12的开口部16a、17a的环状缘部旋转,从而喷射原料粉末。不使气缸盖12旋转,因此,无需较大的占有空间,并且,喷枪23的惯性矩比气缸盖12的惯性矩小,因此,旋转的过渡特性、响应性优异。不过,如图3所示,在喷枪23连接有构成工作气体管线21b的高压配管(高压软管),因此,存在由使喷枪23旋转了时的工作气体管线21b的软管的扭转导致的变形刚性阻碍旋转的过渡特性、响应性的可能性。因此,本实施方式的冷喷装置2如图4~图8所示这样构成,从而提高旋转的过渡特性、响应性。
图4是表示本发明的冷喷装置2的一实施方式的喷枪23的主视图,图5是沿着图4的VI-VI线的剖视图,图6是表示使图4的喷枪23偏置了的状态的主视图,图7是表示包括本发明的冷喷装置2的成膜工厂的主视图,图8是图7的俯视图。
作为工件的气缸盖12以预定的姿势载置于图7~图8所示的成膜工厂4的成膜室42的基座45。例如,如图13所示,以气缸盖12的凹部12b成为上表面的方式将气缸盖12固定于基座45,以进气口16的开口部16a的中心线或排气口17的开口部17a的中心线处于铅垂方向的方式使基座45倾斜。
此外,成膜工厂4具备输送室41和执行成膜处理的成膜室42,在成膜室42设置有用于载置气缸盖12的基座45和用于保持喷枪23的产业用机器人25。并且,在成膜室42的前段设置有输送室41,与外部之间的气缸盖12的输入·输出通过门43进行,输送室41与成膜室42之间的气缸盖12的输入·输出通过门44进行。例如,于在成膜室42中对一个气缸盖12进行着成膜处理的期间内,将之前结束了处理的气缸盖12从输送室41向外部输出。由冷喷装置2进行的成膜处理产生由超音速流的冲击波导致的噪音、或者原料粉末飞散,因此,通过设置输送室41并关闭门44来进行成膜处理,能够与成膜处理同时进行处理后的气缸盖12的输出、处理前的气缸盖12的输入等其他作业。
喷枪23以能够旋转的方式安装固定于底板26,该底板26固定于在图7~图8所示的成膜工厂4的成膜室42设置的产业用机器人25的手251。以下,一边参照图4~图6一边对本实施方式的喷枪23的结构进行说明。首先,如图4所示,在产业用机器人25的手251固定有支架252,相对于该支架252以能够旋转的方式安装底板26,在该底板26固定有喷枪23。
更详细而言,如图4和图5所示,在产业用机器人25的手251固定有支架252,在该支架252固定有马达29的主体,马达29的驱动轴291借助未图示的带轮以及带与第1底板261连接,使该第1底板261相对于支架旋转。马达29在例如最大360°的范围内往复旋转。例如,使驱动轴291相对于一个进气口16的开口部16a顺时针旋转360°之后,就使驱动轴291相对于下一个进气口16的开口部16a逆时针旋转360°,以后,反复进行此动作。
底板26包括第1底板261和第2底板262,这些第1底板261和第2底板262设置为借助线性引导件281能够在与旋转轴线C正交的方向(图4的左右方向)上滑动。并且,通过驱动液压缸282,调节第2底板262相对于第1底板261的偏置量,设定膜形成材料的喷射径D。
在第2底板262安装固定有罩263,在该罩263的下端部固定有喷枪23。喷枪23以喷嘴23d的喷射方向朝向旋转轴线C的方式借助罩263固定于第2底板262。不过,第2底板262利用上述的线性引导件281和液压缸282能够相对于第1底板261偏置,因此,能够相对于旋转轴线C在水平方向上调节喷枪23的喷嘴23d的顶端的位置。
如此,若将喷嘴23d的顶端的位置从图4所示的旋转轴线C的线上如图6所示这样设定成与旋转轴线C分开的位置,则在枪距相同的情况下,喷射径D变小。进气口16的开口部16a与排气口17的开口部17a相比为大径,因此,在将气门座膜16b形成于进气口16的开口部16a的情况下,设为图4所示的旋转轴线C侧的位置,在将气门座膜17b形成于排气口17的开口部17a的情况下,设为图6所示的与旋转轴线C分开的位置即可。
向喷枪23引导从图3所示的压缩气瓶21a供给的3MPa~10MPa的高压气体的工作气体管线21b与随后论述的其他配管类一起设为一个管束20,且如图7所示这样从安装固定到产业用机器人25的手251的底板26的上部垂下,达到喷枪23。在其间的底板26的附近,如图4所示,借助回转环接头等旋转接头21k分离连接,在其下部设置有加热器21i。图4所示的从旋转接头21k到腔室23a的工作气体管线21b由能经得住3MPa~10MPa的高压的高压软管构成,如该图4所示,沿着旋转轴线C以包围该旋转轴线C的方式布置。工作气体管线21b也可以以包围旋转轴线C的方式预先成形加工成例如螺旋状,但能经得住3MPa~10MPa的高压的高压软管较硬而具有形状保持性,因此,也可以将形状保持模具设置于外周,以使高压软管与螺旋形状相仿。
向喷枪23引导从图3所示的原料粉末供给装置22a供给的原料粉末的原料粉末供给管线22c作为图7所示的管束20布置于产业用机器人25的周围,从底板26的上部垂下,达到喷枪23。在其间的底板26的下方,如图4所示,原料粉末供给管线22c由包括金属管和金属接头的配管构成,与喷枪23的腔室23a连接。
向加热器21i引导从图3所示的电力源21h供给的电力的供电线21j、21j作为图7所示的管束20布置于产业用机器人25的周围,从底板26的上部垂下,与加热器21i连接。另外,向控制器(未图示)输出来自图3所示的压力计23b的检测信号的信号线23g和向控制器(未图示)输出来自温度计23c的检测信号的信号线23h在从喷枪23的腔室23a起贯穿了包括金属管和金属接头的配管之中的状态下从喷枪23的腔室23a向第2底板262引导,与其他工作气体管线21b、原料粉末供给管线22c、供电线21j等一起从底板26的上部向产业用机器人25的周围布置。
向喷枪23的喷嘴23d引导从图3所示的制冷剂循环回路27供给的制冷剂的导入管274和排出管275作为图7所示的管束20布置于产业用机器人25的周围,从底板26的上部垂下,与喷嘴23d的顶端的制冷剂导入部23e和喷嘴23d的基端的制冷剂排出部23f连接。在其间的底板26的下方,如图4所示,导入管274和排出管275由包括金属管和金属接头的配管构成,与喷枪23的喷嘴23d连接。
如上所述,由较硬而变形刚性较高的高压软管构成的工作气体管线21b以其旋转接头21k如图4所示这样配置于旋转轴线C的线上、且比旋转接头21k靠下方的部分沿着旋转轴线C以包围该旋转轴线C的方式布置。另外,如图5所示,除了工作气体管线21b以外的供电线21j、21j、原料粉末供给管线22c、制冷剂的导入管274和排出管275、信号线23g、23h配置于旋转轴线C的周围且包围工作气体管线21b的位置。
接着,说明具备气门座膜16b、17b的气缸盖12的制造方法。图9是表示本实施方式的气缸盖12的制造方法中的气门部位的加工工序的工序图。如该图9所示,本实施方式的气缸盖12的制造方法具备铸造工序S1、切削工序S2、包覆工序S3、以及精加工工序S4。此外,为了说明的简化,省略除了气门部位以外的加工工序。
在铸造工序S1中,使铸件用铝合金流入已安放有砂芯的模具,铸造成形在主体部形成有进气口16、排气口17等的气缸盖毛坯。进气口16和排气口17由砂芯形成,凹部12b由模具形成。图10是从安装于气缸体11的安装面12a侧观察在铸造工序S1中铸造成形的气缸盖毛坯3的立体图。气缸盖毛坯3具备4个凹部12b以及在各凹部12b设置的两个进气口16和两个排气口17。各凹部12b的两个进气口16和两个排气口17在气缸盖毛坯3内集合成1根,与在气缸盖毛坯3的两侧面设置的开口分别连通。
图11是沿着图10的XI-XI线的气缸盖毛坯3的剖视图,表示进气口16。在进气口16设置有暴露到气缸盖毛坯3的凹部12b内的圆形的开口部16a。
在接下来的切削工序S2中,对气缸盖毛坯3实施由端铣刀、球形端铣刀等进行的铣削加工,如图12所示,在进气口16的开口部16a形成环状气门座部16c。环状气门座部16c是成为气门座膜16b的基础形状的环状槽,形成于开口部16a的外周。在本实施方式的气缸盖12的制造方法中,利用冷喷法向环状气门座部16c喷射原料粉末P而形成覆膜,基于该覆膜而形成气门座膜16b。因此,环状气门座部16c以比气门座膜16b大一圈的尺寸形成。
在包覆工序S3中,利用本实施方式的冷喷装置2向气缸盖毛坯3的环状气门座部16c喷射原料粉末P,形成气门座膜16b。更具体而言,在该包覆工序S3中,如图13所示,将气缸盖毛坯3固定而使喷枪23以一定速度旋转,以便一边将环状气门座部16c和喷枪23的喷嘴23d以相同的姿势保持一定距离,一边向环状气门座部16c的整周吹送原料粉末P。
喷枪23的喷嘴23d的顶端在固定到基座45的气缸盖12的上方保持于产业用机器人25的手251。如图4所示,基座45或产业用机器人25以要形成气门座膜16b的进气口16的中心轴线Z垂直、且与旋转轴线C重叠的方式设定气缸盖12或喷枪23的位置。在该状态下,一边从喷嘴23d向环状气门座部16c吹送原料粉末P,一边利用马达29使喷枪23绕C轴旋转,在环状气门座部16c的整周形成覆膜。
在实施着该包覆工序S3的期间内,喷嘴23d从制冷剂导入部23e向流路导入从制冷剂循环回路27供给的制冷剂。制冷剂在从形成于喷嘴23d的内部的流路的前端侧朝向后端侧流动的期间冷却喷嘴23d。流动到流路的后端侧的制冷剂被制冷剂排出部23f从流路排出而被回收。
若喷枪23绕C轴旋转1圈而气门座膜16b的形成结束,则暂时停止喷枪23的旋转。在该旋转停止过程中,产业用机器人25以接下来要形成气门座膜16b的进气口16的中心轴线Z与产业用机器人25的基准轴线一致的方式使喷枪23移动。马达29在由产业用机器人25进行的喷枪23的移动结束后再次开始喷枪23的旋转,在下一个进气口16形成气门座膜16b。以后,通过反复进行该动作,在气缸盖毛坯3的全部进气口16和排气口17形成气门座膜16b、17b。此外,在气门座膜的形成对象在进气口16与排气口17之间切换之际,利用基座45变更气缸盖毛坯3的倾斜。
另外,图16是表示在本发明的成膜方法中冷喷装置2的喷嘴23d在进气口16和排气口17各自的开口部处移动之际的移动轨迹MT的一个例子的气缸盖毛坯3的俯视图。使喷嘴23d沿着以箭头表示的移动轨迹MT相对于图16所示的气缸盖毛坯3的8个进气口16的开口部16a和8个排气口17的开口部17a相对移动。此外,以下,说明相对于进气口16的移动轨迹MT,但相对于排气口17的移动轨迹也同样地设定。
如上所述,喷嘴23d相对于一个进气口16顺时针旋转360°之后,就相对于下一个进气口16逆时针旋转360°。然后,喷嘴23d相对于8个进气口16一边反复进行顺时针旋转和逆时针旋转一边移动。即,喷嘴23d相对于图16所示的4个进气口的开口部16a8、16a6、16a4、16a2逆时针旋转,相对剩余的4个进气口的开口部16a7、16a5、16a3、16a1顺时针旋转。
其中,相对于8个进气口16的移动轨迹MT由相对于各进气口16的各环状气门座部16c的圆形的轨迹T和将相邻的圆形的轨迹T彼此连接的连接轨迹CT构成,设为一连串的连续的轨迹。并且,一边从喷嘴23d不中断而连续地喷射原料粉末,一边使喷嘴23d沿着移动轨迹MT移动。此外,相对于一个环状气门座部16c的圆形的轨迹T从成膜起点开始,在顺时针或逆时针移动了之后,在成膜起点处重叠,并将该重叠部设为成膜终点。
图20是放大地表示相对于位于图16的右下的一个进气口16的开口部16a8的比较例的移动轨迹MT的俯视图。使喷嘴23d相对于该进气口16的开口部16a8的环状气门座部16c逆时针旋转,因此,图20所示的比较例的移动轨迹MT是如下轨迹:使喷嘴23d从该图20的右端向左呈直线状移动到环状气门座部16c,在以此为成膜起点而以圆形的轨迹T使喷嘴23d逆时针旋转了之后,在与成膜起点重叠的成膜终点处改变朝向,使喷嘴23d向图20的左方向移动。在这样的比较例的移动轨迹MT中,在环状气门座部16c的成膜起点处产生喷嘴23d的移动速度成为零的折返点TP1,在成膜终点处产生喷嘴23d的移动速度成为零的折返点TP2。此外,折返点TP1、TP2是指喷嘴23d的移动速度变低到零或接近零的值的移动轨迹MT上的点,且是指移动轨迹呈直角或锐角(≤90°)变化的点。
图21是表示以图20的比较例的移动轨迹MT进行了成膜的情况的重叠部的覆膜截面的图。在产生于成膜起点的第1次的折返点TP1处,喷嘴23d的速度一时成为零,但继续原料粉末的喷射,因此,如图21所示这样构成第1层的气门座膜16b1的端部倾斜S变得陡峭。冷喷法用于使原料粉末以超音速并以固相状态直接与基材碰撞而塑性变形,因此,若将第2层喷射于端部倾斜S陡峭的第1层的面上,则第2层的原料粉末未充分扁平化,第2层的气门座膜16b2的层内的空孔径变大。对于由这种扁平率不足导致的空孔率的增加的不良情况,原因在于构成第1层的气门座膜16b1的端部倾斜S变得陡峭。换言之,若在作为被成膜部的环状气门座部16c的圆形的轨迹中的从成膜起点到成膜终点的范围(包括端点)内,在第1层包括折返点,则端部倾斜S在该折返点处变得陡峭。不过,即使在重叠部的第2层的轨迹中包含折返点,只要第1层的气门座膜16b2的端部倾斜S不陡峭,也不产生扁平率不足的问题。
因此,在本实施方式的成膜方法中,将折返点TP1不是设定于圆形的轨迹T之上,而是设定于连接轨迹CT之上,以便在圆形的轨迹T的第1层不包括折返点TP1。图17是表示相对于图16的一个进气口16的开口部16a8的移动轨迹MT的俯视图。图17所示的本例的移动轨迹MT是如下轨迹:使喷嘴23d从该图17的右端朝向左呈直线状移动到环状气门座部16c的左下方的、气缸盖毛坯3安装于气缸体11的安装面12a,将此设定成第1层的折返点TP1。然后,在该折返点TP1处改变朝向,在使喷嘴23d朝向环状气门座部16c向斜右上方向移动了之后,将此设为成膜起点而以圆形的轨迹T使喷嘴23d逆时针旋转,将与成膜起点重叠的成膜终点设为第2层的折返点TP2而改变朝向,使喷嘴23d向图20的左方向移动。
图18是表示以图17的移动轨迹MT进行了成膜的情况的重叠部的覆膜截面的图。若观察该环状气门座部16c的重叠部,则在第1层的气门座膜16b1的成膜起点处,喷嘴23d的移动速度成为不是零的速度,因此,第1层的气门座膜16b1的表面被平坦地成膜。因而,即使成为成膜终点的第2层的气门座膜16b2重叠于该气门座膜16b1之上,碰撞方向也与第1层的气门座膜16b1的表面大致垂直,因此,第2层的原料粉末充分扁平化,气门座膜16b2的层内的空孔径充分变小。此外,可能成为重叠部的第1层的折返点TP1、即设定于比环状气门座部16c的成膜起点靠上游侧的位置的折返点设定于连接轨迹CT之上,但成为重叠部的第2层的折返点TP2的端部倾斜S可以变得陡峭,因此,该折返点TP2设定于圆形的轨迹T之上。
顺带说下,在使喷嘴23d沿着图17所示的本例的移动轨迹MT相对移动的情况下,也可以在设定到连接轨迹CT之上的折返点TP1处增大喷嘴23d与气缸盖毛坯3的安装面12a之间的距离、所谓的枪距。在该情况下,也可以是,在随着靠近折返点TP1而逐渐增大了枪距之后,随着远离折返点TP1而逐渐恢复成原来的枪距。通过增大喷嘴23d与安装面12a之间的枪距,在安装面12a形成的多余覆膜的膜厚变薄,因此,能够使精加工工序S4中的多余覆膜的去除深度变浅。
图19是表示相对于一个进气口16的开口部16a8的移动轨迹MT的另一个例子的俯视图。在图17所示的移动轨迹MT中,将第2层的折返点TP2设定到相对于环状气门座部16c的圆形的轨迹T之上,但与第1层的折返点TP1同样地,如图19所示,也可以设定于气缸盖毛坯3的安装面12a之上。
返回图9,在精加工工序S4中,进行气门座膜16b、17b、进气口16以及排气口17的精加工。在气门座膜16b、17b的精加工中,通过使用了球形端铣刀的铣削加工切削气门座膜16b、17b的表面,将气门座膜16b调整成预定形状。另外,在进气口16的精加工中,将球形端铣刀从开口部16a插入进气口16内,沿着图14所示的加工线PL切削进气口16的开口部16a侧的内周面。加工线PL是原料粉末P飞散并附着到进气口16内而成的多余覆膜SF形成得比较厚的范围,更具体而言是多余覆膜SF形成为厚到给进气口16的进气性能带来影响的程度的范围。
如此,利用精加工工序S4消除由铸造成形导致的进气口16的表面粗糙,并且,能够去除在包覆工序S3中所形成的多余覆膜SF。在图15中表示精加工工序S4后的进气口16。此外,排气口17与进气口16同样地经由由铸造成形进行的小径部在排气口17内的形成、由切削加工进行的环状气门座部的形成、对环状气门座部进行的冷喷、精加工而形成气门座膜17b。因此,针对气门座膜17b相对于排气口17的形成步骤,省略详细的说明。
如上所述,本实施方式的使用了冷喷装置2的成膜方法是如下成膜方法:一边使具有不相互连续的多个环状气门座部16c的气缸盖毛坯3和冷喷装置2的喷嘴23d沿着由相对于环状气门座部16c的圆形的轨迹T和连结该多个圆形的轨迹T的连接轨迹CT构成的连续的移动轨迹MT相对地移动,一边从喷嘴23d连续地喷射原料粉末,利用冷喷法向多个环状气门座部16c分别喷射原料粉末而形成气门座膜16b,在该成膜方法中,将移动轨迹MT中的气缸盖毛坯3与喷嘴23d之间的相对速度变低到零或接近零的值的折返点TP1不是设定于圆形的轨迹T之上,而是设定于连接轨迹CT之上。由此,即使成为成膜终点的第2层的气门座膜16b2重叠于气门座膜16b1之上,碰撞方向也与第1层的气门座膜16b1的表面大致垂直,因此,第2层的原料粉末充分扁平化,气门座膜16b2的层内的空孔径充分变小。
在本实施方式的使用了冷喷装置2的成膜方法中,气缸盖12的进气口16或排气口17的开口部16a、17a的整周作为被成膜部,将折返点TP1设定于气缸盖毛坯3的安装于气缸体11的安装面12a。由此,沿着连接轨迹CT在气缸盖毛坯3的安装于气缸体11的安装面12a形成的多余覆膜能够在作为后工序的精加工工序S4中与其他部分一起容易地去除。
根据本实施方式的使用了冷喷装置2的成膜方法,在折返点TP1处增大喷嘴23d与气缸盖毛坯3之间的枪距,因此,在安装面12a形成的多余覆膜的膜厚变薄,能够使精加工工序S4中的多余覆膜的去除深度变浅。
根据本实施方式的使用了冷喷装置2的成膜方法,设定于环状气门座部16c的成膜终点的折返点TP2设定于相对于环状气门座部16c的圆形的轨迹T之上。设定于比环状气门座部16c的成膜起点靠上游侧的位置的折返点设定于连接轨迹CT之上,但处于重叠部的第2层的折返点TP2的端部倾斜S可以变得陡峭,因此,该折返点TP2能够设定于圆形的轨迹T之上。
上述环状气门座部16c相当于本发明的被成膜部。
附图标记说明
1、内燃机;11、气缸体;11a、气缸;12、气缸盖;12a、安装面;12b、凹部;12c、12d、侧面;13、活塞;13a、连杆;13b、顶面;14、曲轴;15、燃烧室;16、进气口;16a、开口部;16b、气门座膜;16c、环状气门座部;17、排气口;17a、开口部;17b、气门座膜;18、进气门;18a、气门杆;18b、气门头;18c、气门引导件;19、排气门;19a、气门杆;19b、气门头;19c、气门引导件;2、冷喷装置;21、气体供给部;21a、压缩气瓶;21b、工作气体管线;21c、输送气体管线;21d、压力调整器;21e、流量调节阀;21f、流量计;21g、压力计;21h、电力源;21i、加热器;21j、供电线;21k、旋转接头;22、原料粉末供给部;22a、原料粉末供给装置;22b、计量器;22c、原料粉末供给管线;23、喷枪;23a、腔室;23b、压力计;23c、温度计;23d、喷嘴;23e、制冷剂导入部;23f、制冷剂排出部;23g、信号线;24、基材;24a、覆膜;25、产业用机器人;251、手;252、支架;26、底板;261、第1底板;262、第2底板;263、罩;27、制冷剂循环回路;271、罐;272、泵;273、冷却器;274、导入管;275、排出管;28、偏置机构;281、线性引导件;282、液压缸;29、马达;291、驱动轴;3、气缸盖毛坯;4、成膜工厂;41、输送室;42、成膜室;43、44、门;45、基座;MT、移动轨迹;T、被成膜部的轨迹;CT1、CT2、连接轨迹;TP1、TP2、折返点;S、端部倾斜。
本文用于企业家、创业者技术爱好者查询,结果仅供参考。