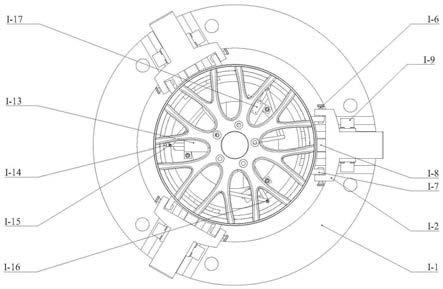
1.本发明涉及轮毂加工技术领域,尤其涉及一种汽车轮毂夹具、加工设备及生产线。
背景技术:
2.汽车轮毅正朝着多元化、个性化方向发展,所以,造成了轮毂的形成了多规格、多尺寸、变批量的轮毂生产模式。对于不同规格尺寸的轮毅在加工时往往要有不同的加工设备来满足其对加工的需要,随着轮毂种类的增加,对设备的需求也在随之增加。轮毂夹具是轮毂加工的必要工具,其对轮毂加工生产线的生产效率、生产质量有非常重要的影响。
3.发明人发现,目前轮毂夹具存在定位精度不能满足加工要求、不能适应多规格轮毂加工对生产效率的要求等问题,例如,现有技术公开了一种轮毂夹具,该夹具的设计体现出了一定程度的灵活性,但是夹具在即将使用时,前期准备工作太过麻烦;当面临多规格尺寸轮毅的生产任务时,需要进行不断地调节,无法适应自动化的需求。现有技术还公开了一种汽车轮毂夹具,其设计了具有一定的弹性以及活动范围的弧形夹紧垫,从而进一步扩大了对不同轮毂进行限位的范围;但此夹具不能实现不同轮毂厚度的夹紧,且未在夹紧前实现自定位,可能因毛坯的质量问题导致夹紧时定心错误,造成偏差过大,使得后续加工误差逐渐放大,最终损害工件,发生不必要损失。
4.另外,目前轮毂机加工设备基本还停留在老式的、人工操作三台机床的岛式加工,其润滑方式为浇注式润滑。传统的浇注式就是在机床加工时将大量的切削液持续的喷射到加工区,将切削产生的大量热量与切屑带走。但是在加工过程中,浇注式由于大量浇注切削液,会造成切削液飞溅,由于工人操作机床,切削液会对工人的身体健康造成影响,且切削液对环境危害极大,处理成本又极高,增大成本。而且,轮毂岛式加工未对机加工中的粗加工、半精加工和精加工进行区别,使得他们的定位基准相同,导致加工精度较低。
5.对于轮毂加工生产线,除了夹具定位、机加工环节的问题,还存在上下料过程不能有效衔接、轮毂一次运输数量较少等问题,导致生产线不能满足轮毂对质量和效率的要求。
技术实现要素:
6.针对现有技术存在的不足,本发明的目的是提供一种汽车轮毂夹具、加工设备及生产线,夹具通过设置定位装置,能够实现轮毂自定位,能够适应多尺寸、多规格轮毂的夹紧;机加工嵌入了微量润滑加工,能够满足轮毂机加工的要求,保证加工质量;轮毂从毛坯传输到加工输出过程有效衔接,提高加工效率。
7.为了实现上述目的,本发明是通过如下的技术方案来实现:
8.第一方面,本发明的实施例提供了一种汽车轮毂夹具,包括:
9.夹具主体,包括固定平台、沿固定平台周向间隔布置的多个夹紧爪,夹紧爪用于夹紧轮毂外圈;多个夹紧爪通过连杆机构连接驱动件,在驱动件作用下能够使夹紧爪沿固定平台径向移动;
10.定位装置,包括与夹紧爪滑动连接的活动平台,活动平台安装有用于定位轮毂内
圈或外圈的定位模块。
11.作为进一步的实现方式,所述夹紧爪包括主体,主体一端连接有能够与轮毂表面贴合的夹持件,夹持件与主体之间设置垫片;
12.所述固定平台、活动平台分别沿周向对应开设安装槽,夹紧爪与安装槽滑动连接。
13.作为进一步的实现方式,所述定位模块包括安装于活动平台的内充架,内充架周向与多个内充件滑动连接;内充架中心安装连接轴,连接轴与连接架转动连接;
14.所述连接架通过连杆与内充件相连,内充件与气缸相连以改变内充件相对内充架的伸出长度。
15.作为进一步的实现方式,所述活动平台沿径向对称开设滑槽,所述定位模块包括设置于滑槽中的定位块;两个定位块通过连杆机构相连,其中一个定位块连接气缸,在气缸作用下改变两个定位块的距离以贴合轮毂外圈。
16.作为进一步的实现方式,所述定位模块包括定位板、连接件,连接件垂直于活动平台,且连接件通过若干长度不同的弹簧与定位板连接,以使定位板形成设定倾斜角度。
17.第二方面,本发明实施例还提供了一种汽车轮毂加工设备,包括所述的夹具,所述夹具安装于机床上,所述机床还安装有微量润滑装置。
18.第三方面,本发明实施例还提供了一种汽车轮毂加工生产线,包括所述的加工设备,还包括上料系统、上下料机械手和出料辊道,所述加工设备设置多个,上料系统设置于加工设备一侧,上下料机械手用于将上料系统输送的轮毂放置于加工设备,并将加工后的轮毂放置于出料辊道。
19.作为进一步的实现方式,所述上料系统包括依次设置的第一辊道、第二辊道、第三辊道和第四辊道,
20.第一辊道用于传输装有轮毂的可分离料架,第二辊道设于第一辊道输出端,其底部安装升降台;所述第一辊道上方设有料架分离装置,料架分离装置用于将拆分后的可分离料架放置于第三辊道;
21.所述第三辊道与第四辊道之间设置轮毂抓取机械手。
22.作为进一步的实现方式,所述料架分离装置包括支撑框架,支撑框架顶部通过同步带传输机构安装料架插取装置,在同步带传输机构的作用下料架插取装置能够沿支撑框架长度方向移动。
23.作为进一步的实现方式,所述第四辊道的输出端设有定位辊道。
24.本发明的有益效果如下:
25.(1)本发明的夹具包括多个夹紧爪,夹紧爪通过气缸带动的连杆机构配合滑块调整夹紧爪的位置,从而适应不同尺寸不同规格的轮毂;活动平台可通过调整高度与夹紧爪配合实现不同宽度的夹紧;夹紧爪设置有缓冲垫片,可以避免夹紧时对工件表面造成损坏。
26.(2)本发明的自定位装置能够实现对轮毂内圈或外圈的定位,第一种自定位装置通过连杆机构带动的内充件实现定位轮毂内心,通过较小的接触面积保证精度;第二种定位装置通过连杆带动定位块实现对轮毂外圈的定位;第三种定位装置设置定位板和弹簧,通过轮毂的重力与安装弹簧的弹力作用,通过静力平衡实现定位;从而能够根据轮毂实际定位要求选择不同的定位装置,提高夹具的适应性。
27.(3)本发明的加工设备为装有微量润滑装置的机床,使用机床时根据不同的转速
对机床进行不同的供液,即可保证加工的精度与质量,又能减少资源浪费。
28.(4)本发明的轮毂加工生产线设置上下料机械手、轮毂抓取机械,上下料机械手可以完成机床上轮毂的连续上下料,轮毂定位辊道与上下料机械手配合完成辊道与机床的轮毂有效输送,实现机加工过程中轮毂的搬运输送的自动化以及高效性;轮毂抓取机械手可以完成上料装置与机加工装置衔接,使得生产线的加工中,能够实现不停歇的上料。
29.(5)本发明的上下料机械手形成两个夹持空间,通过连杆机构实现夹持装置的两端同时运行,对轮毂实现抓取;上下料时,机床车门打开后,空的夹持空间可以将已加工完成的轮毂拿下,另一端夹持空间将未加工的轮毂放上,可以实现上下料的持续进行,提高搬运效率。
30.(6)本发明的轮毂抓取机械手设置有y轴移动装置,轮毂抓取机械手从料架上抓取轮毂后,可以让支撑架从升降台上方移开,防止支撑架对升降台的升降造成影响。
31.(7)本发明的上料系统包括可分离料架、料架分离装置、多个辊道,可分离料架由多个可拆卸的料架单元构成,通过料架分离装置将可分离料架拆成料架单元,并将装有轮毂的料架单元放置于传输辊道;通过料架分离装置与辊道的配合,实现毛坯轮毂的高效传输。
附图说明
32.构成本发明的一部分的说明书附图用来提供对本发明的进一步理解,本发明的示意性实施例及其说明用于解释本发明,并不构成对本发明的不当限定。
33.图1是本发明实施例一的夹具俯视图;
34.图2是本发明实施例一的夹具立体图;
35.图3是本发明实施例一的夹具剖视图;
36.图4是本发明实施例一的固定平台立体图;
37.图5是本发明实施例一的夹具主体纵向剖视图;
38.图6是本发明实施例一的固定平台俯视剖视图;
39.图7是本发明实施例一的自定位装置立体图;
40.图8是本发明实施例一的自定位装置俯视剖视图;
41.图9是本发明实施例二的自定位装置立体图;
42.图10是本发明实施例二的自定位装置俯视图;
43.图11是本发明实施例三的自定位装置立体图;
44.图12是本发明实施例四的加工设备结构示意图;
45.图13是本发明实施例四的微量润滑装置结构示意图;
46.图14是本发明实施例五的生产线立体图;
47.图15是本发明实施例五的上料系统立体图;
48.图16是本发明实施例五的定位辊道立体图;
49.图17是本发明实施例五的料架分离装置立体图;
50.图18是本发明实施例五的轮毂抓取机械手立体图;
51.图19是本发明实施例五的轮毂抓取机械手俯视图;
52.图20是本发明实施例五的上下料机械手立体图;
53.图21是本发明实施例五的上下料机械手的机械手爪立体图;
54.其中,i、夹具,ⅱ、机床,iii、上下料机械手,iv、第四辊道,v、轮毂,vi、轮毂抓取机械手,vii可分离料架,viii、料架分离装置,ix、第一辊道,x、第二辊道,xi、升降台,xii、微量润滑装置,xiii、定位辊道,xiv、第三辊道,xv、出料辊道;
55.i
‑
1、固定平台,i
‑1‑
1、轨道,i
‑1‑
2、支撑架;i
‑
2、夹紧爪,i
‑2‑
1、轨道槽,i
‑2‑
2、主体,i
‑2‑
3、轨道,i
‑
3、连接销,i
‑
4、连杆,i
‑
5、定位装置,i
‑5‑
1、活动平台,i
‑5‑
2、活动平台,i
‑5‑
3、活动平台,i
‑
6、连接钉,i
‑
7、夹持件,i
‑
8、垫片,i
‑
9、活动件,i
‑
10、连接件,i
‑
11、气缸,i
‑
12、气缸,i
‑
13、压力传感器,i
‑
14、内充件,i
‑
16、连杆,i
‑
17、位移传感器,i
‑
18、连接架,i
‑
19、连接轴,i
‑
20、气缸,i
‑
25、第二连杆,i
‑
26、定位块,i
‑
27、气缸,i
‑
28、第一连杆,i
‑
29、连接销,i
‑
31、位移传感器,i
‑
31、定位板,i
‑
33、连接件,i
‑
34、弹簧;
56.iii
‑
1、机械臂,iii
‑
2、机械手爪,iii
‑2‑
1、夹持件,iii
‑2‑
2夹持板,iii
‑2‑
4、安装板,iii
‑2‑
5、连接架,iii
‑2‑
4、安装板,iii
‑2‑
6、滑轨槽,iii
‑2‑
7、第五连杆,iii
‑2‑
8、第四连杆,iii
‑2‑
9、第三连杆,iii
‑2‑
10、连接销,iii
‑2‑
12、连接件;vi
‑
1、底板,vi
‑
2、支撑框架,vi
‑
3、机械爪,vi
‑
9同步带机构,vi
‑
10、驱动电机,vi
‑
11、轨道,vi
‑
12、支撑架,vi
‑
18、同步带机构,vi
‑
19、连接架,vi
‑
20、连接件,vi
‑
26、驱动电机;viii
‑
1、支撑框架,viii
‑
2、料架插取装置;xii
‑
1、气体过滤器,xii
‑
2、气压表,xii
‑
3、气泵,xii
‑
4、箱体,xii
‑
5、油箱,xii
‑
6、油泵,xii
‑
7、输油管,xii
‑
8、输出管,xii
‑
9、油气混合装置,xii
‑
10、输气管;xiii
‑
1、支撑腿,xiii
‑
2、底板,xiii
‑
3、辊轮,xiii
‑
4、第一安装板,xiii
‑
5、定位块,xiii
‑
6、滚轮,xiii
‑
12、第二安装板。
具体实施方式
57.实施例一:
58.本实施例提供了一种汽车轮毂夹具,如图1
‑
图3所示,包括夹具主体和定位装置i
‑
5,定位装置i
‑
5用于定位轮毂v,夹具主体用于夹紧轮毂v。
59.具体的,夹具主体包括固定平台i
‑
1、夹紧爪i
‑
2、连杆机构等,夹紧爪i
‑
2沿固定平台i
‑
1周向安装多个,夹紧爪i
‑
2通过连杆机构与气缸i
‑
12连接,通过气缸i
‑
12带动连杆机构使夹紧爪i
‑
2夹紧或松开轮毂v。
60.进一步的,如图4
‑
图6所示,固定平台i
‑
1用于连接机床主轴,其周向均匀开设多个安装槽,安装槽的两侧对称安装轨道i
‑1‑
1,夹紧爪i
‑
2垂直安装于安装槽中,且与轨道i
‑1‑
1滑动连接。在本实施例中,固定平台i
‑
1的横截面设置为圆形,安装槽沿固定平台i
‑
1的径向开设三个,以安装三个夹紧爪i
‑
2,使夹持稳定。当然,在其他实施例中,安装槽也可以多于三个。
61.所述气缸1
‑
12垂直安装于固定平台i
‑
1底部,气缸杆穿过固定平台i
‑
1中心的通孔与连杆机构相连。在气缸i
‑
12的作用下,三个夹紧爪i
‑
2同时向心收放完成对轮毂v的夹紧与松开。固定平台i
‑
1的上表面中心位置安装支撑架i
‑1‑
2,通过支撑架i
‑1‑
2安装气缸i
‑
11,气缸i
‑
11的缸杆穿过支撑架i
‑1‑
2与定位装置i
‑
5连接,通过气缸i
‑
11调整定位装置i
‑
5的高度。
62.进一步的,夹紧爪i
‑
2包括主体i
‑2‑
2,主体i
‑2‑
2一端两侧对称设置轨道槽i
‑2‑
1,所述轨道槽i
‑2‑
1与固定平台i
‑
1上的轨道i
‑1‑
1配合,形成移动副;主体i
‑2‑
2另一端对称
用于定位轮毂v,夹具主体用于夹紧轮毂v。其中,夹具主体结构与实施例一相同,此处不再赘述。
73.如图9和图10所示,定位装置i
‑
5包括活动平台i
‑5‑
2和定位模块,定位模块包括定位块i
‑
26、气缸i
‑
27、第一连杆i
‑
28、第二连杆i
‑
25等,活动平台i
‑5‑
2的形状与固定平台i
‑
1相适应,且活动平台i
‑5‑
2周向对应于固定平台i
‑
1的安装槽同样开设安装槽,活动平台i
‑5‑
2的安装槽与活动件i
‑
9形成移动副。
74.在本实施例中,活动平台i
‑5‑
2设置为圆台形,其凸起部分用于套入轮毂v内圈。活动平台i
‑5‑
2沿径向对称开设滑槽,两个滑槽中各设置一个定位块i
‑
26;定位块i
‑
26具有一定高度;所述活动平台i
‑5‑
2安装有用于检测定位块i
‑
26位移的位移传感器i
‑
31。
75.活动平台i
‑5‑
2的中心转动连接第一连杆i
‑
28,第一连杆i
‑
28的两端分别通过连接销i
‑
29与第二连杆i
‑
25的一端连接;第二连杆i
‑
25的另一端连接定位块i
‑
26。其中一个定位块i
‑
26连接气缸i
‑
27,在气缸i
‑
27的作用下,其中一个定位块i
‑
26向圆心内移动,通过第二连杆i
‑
25与第一连杆i
‑
28将动力传输给另一定位块i
‑
26,使得两个定位块i
‑
26同步向圆心内移动,以定位轮毂v外圈。
76.本实施例的定位块i
‑
26采用v型块,通过v型块能够确定圆心的原理,设计v型块向心收紧,实现对外表面圆心的定位。
77.实施例三:
78.本实施例提供了一种汽车轮毂夹具,包括夹具主体和定位装置i
‑
5,定位装置i
‑
5用于定位轮毂v,夹具主体用于夹紧轮毂v。其中,夹具主体结构与实施例一相同,此处不再赘述。
79.如图11所示,定位装置i
‑
5包括活动平台i
‑5‑
3和定位模块,定位模块包括定位板i
‑
31、弹簧i
‑
34,活动平台i
‑5‑
3的形状与固定平台i
‑
1相适应,活动平台i
‑5‑
3设置为圆台形,其凸起部分用于套入轮毂v内圈。活动平台i
‑5‑
3周向对应于固定平台i
‑
1的安装槽同样开设安装槽,活动平台i
‑5‑
3的安装槽与活动件i
‑
9形成移动副。
80.进一步的,所述活动平台i
‑5‑
3周向安装若干连接件i
‑
33,连接件i
‑
33对应于安装槽设置,所述连接件i
‑
33通过若干长度不同的弹簧i
‑
34与定位板i
‑
31连接,使定位板i
‑
31形成设定倾斜角度。其中,定位板i
‑
31与z轴方向的夹角呈锐角。
81.在本实施例中,定位板i
‑
31设置三个,轮毂v放置在活动平台i
‑5‑
3上,轮毂v与定位板i
‑
31接触,弹簧i
‑
34收缩对轮毂v产生推力,从而实现对轮毂v内圈的定位;通过轮毂v重力与弹簧i
‑
34的弹力作用,通过静力平衡实现定位。
82.实施例四:
83.本实施例提供了一种汽车轮毂加工设备,如图12所示,包括机床ii、夹具i、和微量润滑装置xii,夹具i和微量润滑装置xii安装在机床ii上,微量润滑的控制系统与机床相连。微量润滑装置xii为机床ii提供微量润滑的工况,以保证加工更为洁净,质量更好。所述夹具i采用实施例一或实施例二或实施例三所述的结构。
84.在本实施例中,机床ii为现有技术中的机床结构,此处不再赘述。
85.进一步的,夹具i与机床主轴相连,轮毂v被夹具i定位夹紧在机床ii上,机床ii上方的旋转刀塔对轮毂v进行机加工。
86.进一步的,如图13所示,微量润滑装置xii包括箱体xii
‑
4、油箱xii
‑
5、油泵xii
‑
6、
气体过滤器xii
‑
1、气压表xii
‑
2、气泵xii
‑
3等,油箱xii
‑
5安装于箱体xii
‑
4顶部,油泵xii
‑
6安装于箱体xii
‑
4内部,油箱xii
‑
5与油泵xii
‑
6的输入端相连,用于为油泵xii
‑
6供油。所述油泵xii
‑
6的输出端连接一根输油管xii
‑
7和一根输出管xii
‑
8,输油管xii
‑
7和输出管xii
‑
8通过油气混合装置xii
‑
9与输气管xii
‑
10相连。所述输气管xii
‑
10连接气泵xii
‑
3,气泵xii
‑
3安装于箱体xii
‑
4内。
87.所述气泵xii
‑
3与安装在箱体xii
‑
4外侧的气体过滤器xii
‑
1相连,气体过滤器xii
‑
1安装气压表xii
‑
2,用于检测系统气压。气泵xii
‑
3将加压后的气体,通过输气管xii
‑
10输送到油气混合装置xii
‑
9中,油箱xii
‑
5的微量润滑油通过输油管xii
‑
7先进入油泵xii
‑
6中,油泵xii
‑
6给予动力,将油输送给油气混合装置xii
‑
9,将微量润滑油与气体混合喷入工作区间,为工作起到润滑效果。
88.微量润滑技术为一种准干式润滑技术,它采用的切削液为绿色植物基,不仅不会对人体造成危害,且不会污染环境,可以进行生物分解,微量润滑方式能够满足轮毂机加工的要求,保证加工质量,且不造成污染。
89.实施例五:
90.本实施例提供了一种汽车轮毂加工生产线,如图14所示,包括上料系统、若干加工设备、若干上下料机械手iii、出料辊道xv,上料系统用于将轮毂毛坯运送到上料工位,由上下料机械手iii将轮毂毛坯放置于加工设备,经加工设备加工后的轮毂v再由上下料机械手iii放至出料辊道xv,由出料辊道xv输出。在本实施例中,上下料机械手iii设置多个,上料系统设置于首个上下料机械手iii的一侧,出料辊道xv设置于最后一个上下料机械手iii的另一侧。
91.其中,加工设备采用实施例四所述的结构,此处不再赘述。
92.进一步的,如图15所示,上料系统包括轮毂抓取机械手vi、可分离料架vii、料架分离装置viii、第一辊道ix、第二辊道x、第三辊道xiv、第四辊道iv、升降台xi、定位辊道xiii,第一辊道ix位于料架分离装置ⅱ的入料端,料架分离装置ⅱ架设于第一辊道ix上方,第一辊道ix的末端(输出端)设置第二辊道x;料架分离装置ⅱ的出料端设置第三辊道xiv,且第三辊道xiv的传输方向与第一辊道ix传输方向垂直。第三辊道远离第二辊道x的一侧设有第四辊道iv,第四辊道iv的传输方向与第三辊道xiv平行;第四辊道iv和第三辊道xiv之间设置轮毂抓取机械手vi。
93.进一步的,可分离料架vii由若干层可拆卸的料架单元构成,每层料架单元均可放置轮毂v,通过多层设计可增加轮毂v的传输数量。料架单元设置为矩形框架结构,相邻层料架单元采用插拔式结构,通过插拔式结构便于将料架单元彼此分离。
94.第二辊道x的底部安装升降台xi,通过升降台xi可以调整第二辊道x的高度;第二辊道x的末端设置限位板。装满轮毂v的可分离料架vii经第一辊道ix运输进入第二辊道x,通过升降台xi调整可分离料架vii的高度;定位后通过料架分离装置viii进行料架的分离,将可分离料架vii运输到另一端第三辊道xiv上,轮毂抓取机械手vi将轮毂v从第三辊道xiv抓取到第四辊道iv上,以输送进入加工设备部分。
95.进一步的,如图17所示,料架分离装置viii包括支撑框架viii
‑
1,所述支撑框架viii
‑
1顶部通过同步带传输机构安装料架插取装置viii
‑
2,在同步带传输机构的作用下料架插取装置viii
‑
2能够沿支撑框架viii
‑
1长度方向移动,支撑框架viii
‑
1的长度方向与第
一辊道ix的传输方向一致。
96.更进一步的,料架插取装置viii
‑
2包括插取板、与插取板连接的高度调节机构,插取板通过高度调节机构下放以对准料架单元以实现对料架单元的插取。在本实施例中,插取板侧面具有若干插取块,料架单元开设有与插取块对应的插取槽,从而实现插取动作。所述高度调节机构可采用现有技术实现,例如链条传动机构等。
97.进一步的,如图18和图19所示,轮毂抓取机械手vi包括底板vi
‑
1、安装于底板vi
‑
1上部的支撑框架vi
‑
2,支撑框架vi
‑
2内设置多个机械爪vi
‑
3;在本实施例中,设置两个机械爪vi
‑
3。机械爪vi
‑
3远离抓取端与轨道vi
‑
11滑动连接,轨道vi
‑
11安装于支撑架vi
‑
12上,支撑架vi
‑
12的设置方向与第一辊道ix的传输方向一致。两个机械爪vi
‑
3之间通过连接件vi
‑
20相连,连接件vi
‑
20与同步带机构vi
‑
18固定,同步带机构vi
‑
18连接驱动电机vi
‑
26,通过驱动电机vi
‑
26驱动同步带机构vi
‑
18,以使机械爪vi
‑
3沿轨道vi
‑
11移动,实现对轮毂v的抓取。
98.所述支撑架vi
‑
12顶部与连接架vi
‑
19连接,所述连接架vi
‑
19的两端分别连接同步带机构vi
‑
9,同步带机构vi
‑
9连接驱动电机vi
‑
10,同步带机构vi
‑
9与驱动电机vi
‑
10组成y轴移动装置,在驱动电机vi
‑
10驱动作用下,同步带机构vi
‑
9带动连接架vi
‑
19、支撑架vi
‑
12移动,以防止支撑架vi
‑
12影响升降台的升降动作。
99.进一步的,定位辊道xiii设置于第四辊道iv的输出端,如图16所示,定位辊道xiii包括底板xiii
‑
2、对称安装于底板xiii
‑
2两侧的第一安装板xiii
‑
4,底板xiii
‑
2底部安装多个支撑腿xiii
‑
1,两个第一安装板xiii
‑
4之间连接若干辊轮xiii
‑
3;底板xiii
‑
2上表面具有定位区域,在底板xiii
‑
2的定位区域设置两个第二安装板xiii
‑
12,第二安装板xiii
‑
12与第一安装板xiii
‑
4平行并间隔一定距离。第二安装板xiii
‑
12和第一安装板xiii
‑
4之间转动安装滚轮xiii
‑
6,两个第二安装板xiii
‑
12之间设置有定位块xiii
‑
5,定位块xiii
‑
5连接气缸,在气缸的作用下定位块xiii
‑
5能够沿第二安装板xiii
‑
12之间的空间移动,以实现对轮毂v侧面的定位。所述底板xiii
‑
2上间隔安装多个凸起块,凸起块与定位块xiii
‑
5配合实现对轮毂v的周向限位。
100.进一步的,如图20所示,上下料机械手iii包括机械臂iii
‑
1和机械手爪iii
‑
2,机械手爪iii
‑
2安装于机械臂iii
‑
1末端;其中,机械臂iii
‑
1采用现有结构,此处不再赘述。
101.如图21所示,机械手爪iii
‑
2包括连接架iii
‑2‑
5、安装板iii
‑2‑
4、滑轨槽iii
‑2‑
6、连杆机构、夹持件iii
‑2‑
1、夹持板iii
‑2‑
2,两个安装板iii
‑2‑
4相互平行设置,二者之间间隔安装有多个连接架iii
‑2‑
5,连接架iii
‑2‑
5垂直于安装板iii
‑2‑
4,连接架iii
‑2‑
5和安装板iii
‑2‑
4形成框架结构。在本实施例中,连接架iii
‑2‑
5为工字型结构,例如,设置三个连接架iii
‑2‑
5,位于中间的连接架iii
‑2‑
5安装有法兰连接件iii
‑2‑
14,法兰连接件iii
‑2‑
14与机械臂iii
‑
1可拆卸连接。
102.进一步的,滑轨槽iii
‑2‑
6安装于安装板iii
‑2‑
4相背一侧,每个滑轨槽iii
‑2‑
6滑动连接两个夹持板iii
‑2‑
2,两个夹持板iii
‑2‑
2之间通过连杆机构相连,通过两个夹持板iii
‑2‑
2改变两个夹持板iii
‑2‑
2的距离。所述夹持板iii
‑2‑
2的内侧(彼此靠近的一侧)间隔安装若干夹持件iii
‑2‑
1,夹持件iii
‑2‑
1为齿形结构,通过夹持件iii
‑2‑
1夹持轮毂v。两个相对设置的夹持板iii
‑2‑
2通过夹持件iii
‑2‑
1形成夹持空间,本实施例的机械手爪iii
‑
2具有两个相对的夹持空间,从而可以一次夹取两个轮毂v。
103.更进一步的,连杆机构包括第三连杆iii
‑2‑
9、第四连杆iii
‑2‑
8、第五连杆iii
‑2‑
7,第三连杆iii
‑2‑
9的中心通过连接销iii
‑2‑
10与安装在滑轨槽iii
‑2‑
6中间位置的连接件iii
‑2‑
12相连,第三连杆iii
‑2‑
9的两端分别通过一个第四连杆iii
‑2‑
8连接第五连杆iii
‑2‑
7的一端,所述第五连杆iii
‑2‑
7的另一端与夹持板iii
‑2‑
2连接。对于每个滑轨槽iii
‑2‑
6对应的两个夹持板iii
‑2‑
2,其中一个夹持板iii
‑2‑
2连接气缸,气缸驱动夹持板iii
‑2‑
2沿滑轨槽iii
‑2‑
6运动;通过连杆机构将动力传递至另一个夹持板iii
‑2‑
2,从而实现同一侧的两个夹持板iii
‑2‑
2同步动作,以实现对轮毂v的夹持或松开。
104.在本实施例中,机械臂iii
‑
1通过各关节实现自由移动及精准定位,调节位置。机械手爪iii
‑
2有两个可夹持轮毂v的夹持手爪(夹持空间),一端将已加工完的轮毂v取下,另一端将已加工完的轮毂v放在机床上,实现其连续性加工。夹持轮毂v时,首先气缸启动,带动夹持板iii
‑2‑
2向中心收缩,通过连杆机构将动力传输给另一端的夹持板iii
‑2‑
2,使得夹持板iii
‑2‑
2同时向内收缩,靠近轮毂v。夹持件iii
‑2‑
1与轮毂v接触,对轮毂v进行定位夹紧。夹紧后,机械臂iii
‑
1转动将轮毂v取出,并将另一侧夹持的轮毂v放入夹具i中。
105.以五台加工设备为例对本实施例的工作原理进行说明:
106.装满轮毂v的可分离料架vii运输过第一辊道ix进入第二辊道x,定位后通过料架分离装置viii进行料架的分离,通过升降台xi调整可分离料架vii的高度;通过料架分离装置viii将可分离料架vii移动到第三辊道上,轮毂抓取机械手vi将轮毂v抓取到第四辊道iv上,进入机加工装置部分。在第四辊道iv末端的定位辊道xiii对轮毂v进行定位,上下料机械手iii将轮毂v搬运到机床ii上,夹具i将轮毂v进行夹紧之后进行加工。
107.在机加工装置,五台机床ii包括四台立式车床、一台加工中心,对轮毂v进行五道工序。具体的,第一立式车床,用于粗车轮胎座、粗车前轮缘半径、粗车轮毂盖口装配处,第二立式车床,用于粗车轮毂后外缘、粗车中心孔直径、粗车安装面、半精车轮胎座、半精车轮毂后外缘、半精车中心孔直径、半精车安装面。第三立式车床,用于半精车前缘半径、半精车盖口装配处、精车轮胎座、精车前缘半径、精车盖口装配处。第四立式车床,用于精车轮胎座、精车轮毂后外缘、精车中心孔直径、精车安装面。加工中心,用于钻安装孔、钻气门孔。
108.上下料机械手iii共安装三台,第一台上下料机械手iii用于抓取第一辊道xiii上定位的轮毂v,第一立式车床的上料下料和第二立式车床的上料;第二台上下料机械手iii用于第二立式车床的下料,第三立式车床的上料下料和第四立式车床的上料;第三台上下料机械手iii用于第四立式车床的下料,加工中心的上料下料和将轮毂放置在出料辊道xv,结束加工。
109.以上所述仅为本技术的优选实施例而已,并不用于限制本技术,对于本领域的技术人员来说,本技术可以有各种更改和变化。凡在本技术的精神和原则之内,所作的任何修改、等同替换、改进等,均应包含在本技术的保护范围之内。
再多了解一些
本文用于企业家、创业者技术爱好者查询,结果仅供参考。