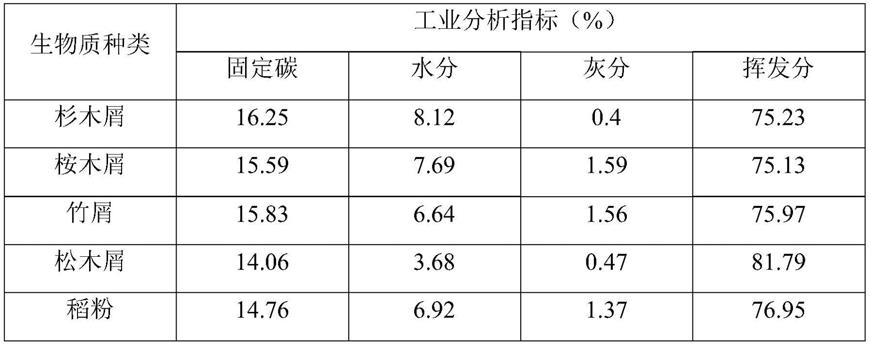
1.本发明属于固体废弃物资源化利用技术领域。更具体地,涉及一种生物质磁化焙烧铁尾矿的方法。
背景技术:
2.近年来世界铁矿石供应日益紧张,铁矿石价格大幅上涨,而我国铁尾矿累计堆存量超50亿吨,含有大量可回收的铁资源。现有常用磁化焙烧的方法来回收铁资源,磁化焙烧是把弱磁性铁矿物(如赤铁矿、褐铁矿、菱铁矿和黄铁矿等)转化为强磁性的磁铁矿,再通过弱磁选等分离技术实现强磁性铁矿物和脉石矿物的分离,进而获得铁精矿的方法。磁化焙烧低品位弱磁性铁矿石是合理有效综合利用或回收铁资源的工艺,对合理利用自然资源、保护生态环境有着十分积极的作用。
3.天然植物生物质具有普遍性、丰富性和可再生性等优点,主要由碳、氢和氧组成,且氮、硫和灰分含量较低,其热解会产生h2、co、co2、ch4等多种气体,其中的h2、co、ch4都具有较强的还原性,可用于铁尾矿的还原焙烧。因此,用天然植物生物质来替代化石能源,不仅可减少焚烧处理生物质产生的温室气体co2的排放,还可减少因使用化石燃料产生的so2和no
x
等污染物的排放。此外,天然植物生物质属于碳中性物质,完全燃烧生成的co2与其生长过程中吸收co2量相同,因此天然植物生物质常被认为是一种清洁能源,对其进行综合利用可有利于碳减排。
4.现有常用生物质热解产生的还原性气体来磁化焙烧铁尾矿,如专利cn201010034534.8公开了一种生物质磁化还原褐铁矿生产铁精矿的方法,该专利将褐铁矿和生物质粉碎后混合均匀后进行焙烧,将褐铁矿还原成磁性铁氧化物,再行磁选得到铁精矿,但该方法中,生物质热解产生的生物质油会团聚在铁尾矿表面,影响铁尾矿内部进一步还原和后续磁选分离工作,导致无法同时兼顾铁尾矿的回收率和品位,因此,亟需寻找一种磁化焙烧铁尾矿的方法,使生物质热解产生的生物质油不会影响铁尾矿的还原和后续磁选操作,以得到铁回收率和铁品位均较高的铁精矿。
技术实现要素:
5.本发明针对上述现有磁化焙烧铁尾矿方法的不足,提供一种生物质磁化焙烧铁尾矿的方法,将铁尾矿与生物质分别进行磁化焙烧,使生物质热解产生的生物质油不会影响铁尾矿的还原和后续磁选操作,以得到高铁品位和高铁回收率的磁铁精矿。
6.本发明上述目的通过以下技术方案实现:
7.本发明提供了一种生物质磁化焙烧铁尾矿的方法,包括如下步骤:
8.s1.将铁尾矿破碎、研磨至
‑
0.074mm,得到铁尾矿粉;
9.s2.将所述生物质破碎,得到生物质粉;
10.s3.将步骤s1所述铁尾矿粉与步骤s2所述生物质粉分开放置于同一耐热密闭容器内不同部位,在600~750℃下进行磁化焙烧;
11.s4.将焙烧后的铁尾矿粉冷却、研磨、磁选得到磁铁精矿。
12.本发明将铁尾矿与生物质分别进行磁化焙烧,有效避免了生物质热解油与铁尾矿的粘结团聚,防止对铁尾矿还原和后续磁选分离工作产生影响,有助于实现磁铁精矿的高铁品位和高铁回收率。
13.本发明利用生物质热解产生的h2、co等还原性气体在脱去结晶水的同时,还将铁尾矿中的赤铁矿等弱磁性的氧化物转化为强磁性的磁铁矿,即将铁尾矿中的fe2o3还原成fe3o4,再通过研磨、磁选等工艺脱去硅、铝等杂质,得到高铁品位和高铁回收率的磁铁精矿。
14.最优选地,步骤s3所述焙烧的温度为660℃,见实施例6。
15.优选地,步骤s3所述焙烧的时间为10~30min。
16.焙烧时间过长不仅浪费资源,还可能产生过还原现象,使fe2o3被过还原成feo,而feo没有磁性,无法被磁选出来,导致铁回收率下降。
17.最优选地,所述焙烧的时间为15min,见实施例6。
18.优选地,步骤s1所述研磨为用行星式球磨机进行研磨。
19.优选地,所述铁尾矿粉与生物质粉的质量比0~10且不为0。
20.更优选地,所述铁尾矿粉与生物质粉的质量比为10:1~2.5。
21.最优选地,所述铁尾矿粉与生物质粉的质量比为5:1,见实施例6。
22.优选地,步骤s3所述耐热密闭容器为可耐750℃的密闭容器。
23.优选地,步骤s3所述耐热密闭容器为管式炉。
24.进一步优选地,不同部位为管式炉内的不同瓷舟上。
25.本发明用同一加热源对生物质粉和铁尾矿粉同时进行加热,相较于两个加热源,可以显著降低加热能耗。
26.优选地,步骤s2所述生物质破碎至
‑
0.15mm。
27.优选地,步骤s2所述生物质粉包括杉木屑、松木屑、桉木屑、竹屑或稻粉的一种或几种。
28.优选地,步骤s1所述铁尾矿中铁元素含量为30~40%。
29.优选地,步骤s3所述焙烧为在惰性氛围中进行焙烧。
30.优选地,步骤s4所述冷却为通入惰性气体冷却。
31.采用惰性气体冷却是为了防止磁铁矿的氧化。
32.优选地,步骤s4所述研磨为将焙烧后的铁尾矿粉研磨至
‑
0.074mm。
33.优选地,步骤s4所述磁选采用的是湿法磁选。
34.进一步优选地,所述湿法磁选进行三次。
35.进一步优选地,所述湿法磁选的磁感应强度为0.1~0.2t。
36.最优选地,所述湿法磁选的磁感应强度为0.1t,见实施例6。
37.优选地,步骤s4所述磁选后还进行烘干。
38.作为一种优选地可实施方式,所述生物质磁化焙烧铁尾矿的方法步骤如下:
39.s1.将铁元素含量为30~40%的铁尾矿破碎后,用行星式球磨机研磨至
‑
0.074mm,得到铁尾矿粉;
40.s2.将所述生物质破碎至
‑
0.15mm,得到生物质粉;
41.s3.将质量比为10:1~2.5的步骤s1铁尾矿粉与步骤s2所述生物质粉分别放置在
同一管式炉内的两个瓷舟上,并同时在惰性氛围、600~750℃下进行磁化焙烧10~30min;
42.s4.向所述管式炉内通入惰性气体,待磁化焙烧后的铁尾矿粉冷却后,用行星式球磨机研磨至
‑
0.074mm,再以0.1~0.2t的磁感应强度进行三次湿法磁选后,烘干得到磁铁精矿。
43.本发明具有以下有益效果:
44.1.本发明将铁尾矿与生物质分别进行磁化焙烧,有效避免了生物质热解油与铁尾矿的粘结团聚,防止对铁尾矿还原和后续磁选分离工作产生影响,有助于实现磁铁精矿的高铁品位(高达61.56%)和高铁回收率(高达99.63%)。
45.2.本发明利用生物质热解产生的h2、co等还原性气体在脱去结晶水的同时,还将铁尾矿中的赤铁矿等弱磁性的氧化物转化为强磁性的磁铁矿,即将铁尾矿中的fe2o3还原成fe3o4,再通过研磨、磁选等工艺脱去硅、铝等杂质,得到高铁品位和高铁回收率的磁铁精矿。
46.3.本发明在铁尾矿的磁化焙烧中,用天然植物生物质来替代化石能源,不仅可减少焚烧处理生物质产生的温室气体co2的排放,还可减少因使用化石燃料产生的so2和no
x
等污染物的排放,实现了绿色可持续发展。
具体实施方式
47.以下结合具体实施例来进一步说明本发明,但实施例并不对本发明做任何形式的限定。除非特别说明,本发明采用的试剂、方法和设备为本技术领域常规试剂、方法和设备。
48.除非特别说明,以下实施例所用试剂和材料均为市购。
49.本发明所用原料的主要化学成分及含量如表1和表2所示:
50.表1铁尾矿化学组成
51.fe2o3sio2al2o3so3k2ozno其他51.07%24.73%18.58%3.81%0.53%0.25%1.03%
52.表2生物质工业分析
[0053][0054]
实施例1一种生物质磁化焙烧铁尾矿的方法
[0055]
s1.将铁尾矿在105℃的鼓风干燥箱中干燥24h,冷却后破碎,再用行星式球磨机研磨至
‑
0.074mm(过200目筛网),得到铁尾矿粉;
[0056]
s2.将桉木在105℃的鼓风干燥箱中干燥24h,冷却后,在破碎机中破碎至
‑
0.15mm(过100目筛网),得到桉木屑;
[0057]
s3.向管式炉中通入氮气,置换出炉腔及其连接处的空气,同时在出气端设置两个洗气瓶,一个洗气瓶装水防止空气倒吸进入,另一个空置防止在降温过程中水倒吸进入管式炉;将10g铁尾矿粉与1.5g桉木屑分别置于2个瓷舟上,待管式炉在氮气氛围中升至660℃时打开进气端,迅速放入2个瓷舟并关闭进气端和氮气输入,焙烧15min;
[0058]
s4.向所述管式炉内通入氮气,待所述铁尾矿粉冷却后,用行星式球磨机研磨至
‑
0.074mm(过200目筛网),称取5g研磨后的铁尾矿粉,加入500ml去离子水和50ml无水乙醇,再以0.1t的磁感应强度进行三次湿法磁选后,抽滤,并在60℃的鼓风干燥箱中干燥24h,得到磁铁精矿。
[0059]
实施例2一种生物质磁化焙烧铁尾矿的方法
[0060]
同实施例1的方法,区别在于,步骤s2用松木替代桉木;步骤s3松木屑的用量为1g。
[0061]
实施例3一种生物质磁化焙烧铁尾矿的方法
[0062]
同实施例1的方法,区别在于,步骤s2用杉木替代桉木;步骤s3杉木屑的用量为2.5g;步骤s4所述湿法磁选的磁感应强度为0.2t。
[0063]
实施例4一种生物质磁化焙烧铁尾矿的方法
[0064]
同实施例1的方法,区别在于,步骤s2用竹子替代桉木;步骤s3所述焙烧的温度为750℃,时间为10min。
[0065]
实施例5一种生物质磁化焙烧铁尾矿的方法
[0066]
同实施例1的方法,区别在于,步骤s2用水稻秸秆替代桉木;步骤s3所述焙烧的温度为600℃,时间为30min。
[0067]
实施例6一种生物质磁化焙烧铁尾矿的方法
[0068]
同实施例1的方法,区别在于,步骤s3中桉木屑的质量为2g。
[0069]
实施例7一种生物质磁化焙烧铁尾矿的方法
[0070]
同实施例1的方法,区别在于,步骤s3中桉木屑的质量为3.5g。
[0071]
对比例1
[0072]
同实施例1的方法,区别在于,步骤s3中桉木屑的质量为0.5g。
[0073]
对比例2
[0074]
同实施例1的方法,区别在于,步骤s3所述焙烧的温度为500℃。
[0075]
对比例3
[0076]
同实施例1的方法,区别在于,步骤s3所述焙烧的温度为850℃。
[0077]
对比例4
[0078]
同实施例1的方法,区别在于,步骤s3所述焙烧的时间为5min。
[0079]
对比例5
[0080]
同实施例1的方法,区别在于,步骤s4不进行研磨。
[0081]
对比例6
[0082]
同实施例1的方法,区别在于,步骤s3中将铁尾矿粉与桉木屑混合后,置于同个瓷舟上进行焙烧。
[0083]
实验例
[0084]
将实施例1~7和对比例1~6所得的磁铁精矿进行全铁含量测定,采用的方法为gb/t 6730.65
‑
2009《铁矿石全铁含量的测定三氯化钛还原重铬酸钾滴定法》,铁品位和铁
回收率结果如表3所示。
[0085]
表3磁铁精矿铁品位和铁回收率结果
[0086] 铁品位(%)铁回收率(%)实施例161.4492.94实施例261.5687.62实施例359.5998.68实施例459.7598.72实施例560.0896.43实施例660.7499.4实施例759.5599.63对比例163.3722.87对比例260.362.1对比例356.2273.52对比例462.4120.52对比例556.3164.56对比例652.5383.75
[0087]
从表3可知,实施例1~7所得磁铁精矿的铁品位达到了59.55~61.56%,铁回收率达到了87.62~99.63%;而对比例1~5的的铁品位虽然达到了56.22~63.37,但其铁回收率仅有2.1~73.52%,显著差于实施例1~7的铁回收率;对比例6的铁回收率虽然达到了83.75%,但其铁品位仅有52.53%,显著差于实施例1~7的铁品位。可见,实施例1~7制备得到了高铁品位和高铁回收率的磁铁精矿,而对比例1~6均无法同时兼顾铁品位和铁回收率,表明本发明的方法可有效提高制得的磁铁精矿的铁品位和铁回收率。
[0088]
综上所述,本发明利用生物质热解产生的h2、co等还原性气体将铁尾矿中的赤铁矿等弱磁性的氧化物转化为强磁性的磁铁矿,通过将生物质和铁尾矿分开焙烧防止团聚,以及特定条件的研磨、磁选等工艺脱去硅、铝等杂质,有效提高了磁铁精矿的铁品位和铁回收率。
[0089]
上述实施例为本发明较佳的实施方式,但本发明的实施方式并不受上述实施例的限制,其他的任何未背离本发明的精神实质与原理下所作的改变、修饰、替代、组合、简化,均应为等效的置换方式,都包含在本发明的保护范围之内。
再多了解一些
本文用于企业家、创业者技术爱好者查询,结果仅供参考。