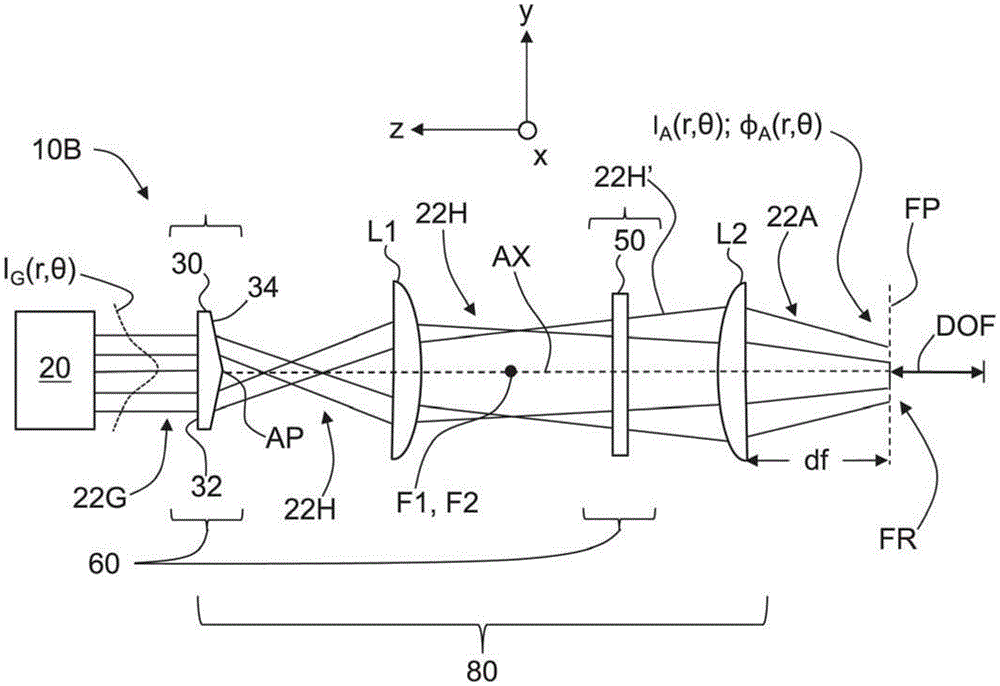
本申请根据35 U.S.C.§119主张在2019年3月21日申请的美国临时申请第62/821,667号的优先权权益,该美国临时申请的内容以全文引用方式并入本文。
技术领域
本公开涉及形成微孔,并且尤其涉及用于使用环形涡旋激光束在基于玻璃的物体中形成微孔的系统及方法。
背景技术
发现基于玻璃的材料(例如,玻璃、玻璃陶瓷及晶体)正越来越多地用于诸如显示器、电视、膝上型计算机、GPS装置及智能电话的商用装置中。基于玻璃的材料具有与热膨胀、电绝缘、光透射、强度、化学稳定性及(例如,至硅的)结合能力相关的许多物理性质,这些物理性质使这些基于玻璃的材料成为与特定商用装置的电气及机械组件组合的极佳选择。基于玻璃的材料可用于限定不同类型的装置组件,诸如显示器的保护屏幕或平板、光学波导、光学互连件、混合式光学电气互连件等。
在商用装置中使用基于玻璃的组件常常需要在组件中或贯穿组件形成高质量微孔以作为装置制造工艺的部分。微孔直径可在几微米至几百微米的范围内,而微孔深度可在几十纳米至几毫米的范围内。这些微孔的密度可在每平方厘米几个至上千个的范围内。在需要相对高密度微孔的情况下,能够快速地且非常准确且精确地形成微孔对于确保令人满意的产品吞吐量变得重要。
技术实现要素:
本公开的方面涉及包括波束形成系统的微孔形成系统。该波束形成系统被配置成用于将常规高斯激光束(“高斯束”)转换成涡旋激光束,该涡旋激光束具有环形横截面形状(“剖面”)且具有大于对应常规高斯绕射波束的焦点深度(例如,作为非限制性示例,从至少大1.1X直至至少大2X或直至大3X或直至大5X或直至大10X)。具有环形截面的涡旋激光束(“环形涡旋波束”)是具有拓扑电荷m(整数)的非绕射光束,该拓扑电荷m限定当波束传播时该波束围绕该波束的中心轴线的旋转量。该环形涡旋波束是以如下方式形成,该方式赋予该波束与传统高斯束相比相对较大的焦点深度,同时也提供比贝色束大的直径。该环形涡旋波束用于使用单步或两步方法在基于玻璃的物体中形成微孔。通过任一工艺形成的这些微孔可视给定应用而为封闭式的(例如,凹部)或开放式的(贯穿孔洞)。
在单步方法中,该环形涡旋波束具有足够能量(例如,在110TW/cm2至480TW/cm2范围内的峰值强度)以便经由烧蚀该基于玻璃的材料而在该基于玻璃的物体的主体中形成空心圆柱形区域。烧蚀工艺在该基于玻璃的物体的该主体中产生环形间隙或孔洞。在该环形间隙不一直延伸穿过该玻璃物体的主体(即,自顶部表面至底部表面,或自外表面至内表面,等)的情况下,存在由该间隙围绕的中心部分。在该环形间隙穿过该基于玻璃的物体的该主体延伸足够远的情况下,容易去除该中心部分而不需要用于形成贯穿孔洞的任何另外实质处理。在该环形间隙达到底部表面的情况下,该中心部分变得与该基于玻璃的物体的该主体的剩余部分分离,且仅脱落或容易去除。
不同于在单一步骤中利用该环形涡旋波束直接形成环形间隙,两步工艺依赖于利用该环形涡旋波束照射该基于玻璃的物体以在该基于玻璃的物体的该主体内形成经修改环形区域。在一示例中,该经修改环形区域中的玻璃材料改变(例如,由于致密化受损),使得该玻璃材料相对于该主体的未转变(未照射)部分优先蚀刻,该部分诸如该中心部分或在该经修改环形区域外的该主体的部分。接着使用蚀刻工艺(例如,酸蚀刻)以去除该经修改区域以形成微孔。
与单步工艺相比,两步工艺通常使用较低激光功率及较短激光处理时间,但使用额外步骤。当额外步骤包含蚀刻时,两步工艺可具有去除可通过用该环形涡旋波束照射诱发的表面瑕疵及微裂痕的增加益处。单步方法及两步方法两者可对基于玻璃的物体(例如,面板)使用而以高吞吐量(例如,对于随后是60分钟蚀刻(同时对所有孔洞进行蚀刻)的两步工艺,3000个微孔/秒激光处理时间,或对于单步工艺,1个微孔/秒激光处理时间)形成大量微孔,而不危害面板强度。这些微孔可具有几十微米至几百微米的直径及至多几毫米的贯穿厚度。
本公开的一实施例涉及一种在具有限定对置的第一及第二表面的主体的基于玻璃的物体中形成微孔的方法。该方法包含:a)形成具有相位分布的相位装置,该相位分布由φPD(r,θ)=φ1(r,θ) φ2(r,θ)限定,其中φ1(r,θ)是等于-k·r·sin(γ)的第一相位项且φ2(r,θ)是等于m·θ的第二相位项,其中(r,θ)是径向极坐标及角坐标,γ是在0.10°≤γ≤20°范围内的轴锥角,且m是在3≤m≤20范围内的拓扑电荷,其中m是整数;b)将高斯激光束引导至该相位装置以将该高斯束转换成环形涡旋波束,该环形涡旋波束具有该相位分布φPD(r,θ)、焦点深度DOF、波长λ及聚焦环,该聚焦环在该焦点深度DOF内且具有内径D1、外径D2及宽度WA=(D2–D1)/2;c)将该环形涡旋波束引导至该第一表面且穿过该基于玻璃的物体的该主体,藉此照射在该焦点深度内的该主体的环形区域以形成经照射环形区域,其中该照射:i)将该经照射环形区域变换成与该主体的尚未被该环形涡旋波束照射的一部分相比优先蚀刻的经修改环形区域;ii)通过烧蚀该经照射环形区域的一部分而将该经照射环形区域的该部分变换成封闭式环形微孔;或iii)通过烧蚀该经照射环形区域而将该经照射环形区域变换成微通孔。
本公开的另一实施例涉及一种在具有限定对置的第一及第二表面的主体的基于玻璃的物体中形成微孔的方法。这些方法包含:a)形成环形涡旋波束,该环形涡旋波束具有焦点深度DOF、波长λ及在该焦点深度DOF内的聚焦环,其中该聚焦环具有内径D1、外径D2及宽度WA=(D2–D1)/2;b)将该环形涡旋波束引导至该第一表面且穿过该基于玻璃的物体的该主体,藉此照射该主体的环形区域以将该环形区域变换成与尚未被该环形涡旋波束照射的该主体的一部分相比优先蚀刻的经修改环形区域;及c)蚀刻该基于玻璃的物体以去除该经修改环形区域以形成该微孔。
本公开的另一实施例涉及一种在具有限定对置的第一及第二表面的主体的基于玻璃的物体中形成微孔的方法。该方法包含:a)形成环形涡旋波束,该环形涡旋波束具有焦点深度DOF、波长λ及在该焦点深度DOF内的聚焦环,其中该聚焦环具有内径D1、外径D2及宽度WA=(D2–D1)/2;及b)将该环形涡旋波束引导至该第一表面且进入该基于玻璃的物体的该主体中及:i)自该第一表面烧蚀该主体的环形部分,但未到达该第二表面,以形成呈具有中心部分的封闭环形微孔的形式的该微孔;或ii)自该第一表面烧蚀该主体的环形部分至该第二表面以将该微孔形成为实质上圆柱形的微通孔。
本公开的另一实施例涉及一种用于在具有限定对置的第一及第二表面的主体的基于玻璃的物体中形成微孔的系统。该系统包含:a)激光源,该激光源被配置成用于产生高斯激光束;b)光学系统,该光学系统可操作地设置以接收及处理该高斯激光束,该光学系统包括经配置具有相位分布φPD(r,θ)=φ1(r,θ) φ2(r,θ)的相位装置,其中φ1(r,θ)是等于-k·r·sin(γ)的第一相位项且φ2(r,θ)是等于m·θ的第二相位项,其中(r,θ)是径向极坐标及角坐标,γ是在0.01°≤γ≤20°范围内的轴锥角,且m是在3≤m≤20范围内的拓扑电荷,其中m是整数;c)其中该高斯激光束是由该光学系统及该光学系统中的该相位装置处理以将该高斯激光束转换成沿着系统轴线退出该光学系统的环形涡旋波束,该环形涡旋波束具有该相位分布φPD(r,θ)、焦点深度DOF、波长λ及聚焦环,该聚焦环在该焦点深度DOF内且具有内径D1、外径D2及宽度WA=(D2–D1)/2;及d)支撑台,该支撑台被配置成用于相对于该环形涡旋波束可操作地支撑该基于玻璃的物体,使得该环形涡旋波束行进穿过该第一表面且穿过该基于玻璃的物体的该主体,藉此照射在该焦点深度内的该主体的环形区域以形成经照射环形区域,其中该照射:i)将该经照射环形区域变换成与该主体的尚未被该环形涡旋波束照射的一部分相比优先蚀刻的经修改环形区域;ii)通过烧蚀该经照射环形区域的一部分而将该经照射环形区域的该部分变换成封闭式环形微孔;或iii)通过烧蚀该经照射环形区域而将该经照射环形区域变换成微通孔。
本公开的另一实施例涉及一种基于玻璃的产品,该基于玻璃的产品是通过对具有限定对置的第一及第二表面的主体的基于玻璃的物体执行一工艺而形成。用于形成该基于玻璃的产品的该工艺包含:a)形成具有相位分布φPD(r,θ)=φ1(r,θ) φ2(r,θ)的相位装置,其中φ1(r,θ)是等于-k·r·sin(γ)的第一相位项且φ2(r,θ)是等于m·θ的第二相位项,其中(r,θ)是径向极坐标及角坐标,γ是在0.10°≤γ≤20°范围内的轴锥角,且m是在3≤m≤20范围内的拓扑电荷,其中m是整数;b)将高斯激光束引导至该相位装置以将该高斯束转换成环形涡旋波束,该环形涡旋波束具有该相位分布φPD(r,θ)、焦点深度DOF、波长λ及聚焦环,该聚焦环在该焦点深度DOF内且具有内径D1、外径D2及宽度WA=(D2–D1)/2;c)将该环形涡旋波束引导至该第一表面且穿过该基于玻璃的物体的该主体,藉此照射在该焦点深度内的该主体的第一环形区域以形成第一经照射环形区域,其中该照射将该第一经照射环形区域变换成与该主体的尚未被该环形涡旋波束照射的一部分相比优先蚀刻的第一经修改环形区域;及d)蚀刻该第一经修改环形区域以在该基于玻璃的物体的该主体中形成环形微孔。
本公开的另一实施涉及紧接上文描述的工艺产品,其中该照射包括形成在该第一经照射环形区域外且与该第一经照射环形区域同心的第二经照射环形区域,使得该蚀刻形成围绕该环形微孔的环形凹部。
本公开的另一实施例涉及一种基于玻璃的产品,该基于玻璃的产品是通过对具有限定对置的第一及第二表面的主体的基于玻璃的物体执行一工艺而形成。用于形成该基于玻璃的产品的该工艺包含:a)形成具有相位分布φPD(r,θ)=φ1(r,θ) φ2(r,θ)的相位装置,其中φ1(r,θ)是等于-k·r·sin(γ)的第一相位项且φ2(r,θ)是等于m·θ的第二相位项,其中(r,θ)是径向极坐标及角坐标,γ是在0.10°≤γ≤20°范围内的轴锥角,且m是在3≤m≤20范围内的拓扑电荷,其中m是整数;b)将高斯激光束引导至该相位装置以将该高斯束转换成环形涡旋波束,该环形涡旋波束具有该相位分布φPD(r,θ)、焦点深度DOF、波长λ及聚焦环,该聚焦环在该焦点深度DOF内且具有内径D1、外径D2及宽度WA=(D2–D1)/2;及c)将该环形涡旋波束引导至该第一表面且穿过该基于玻璃的物体的该主体,藉此照射在该焦点深度内的该主体的第一环形区域以形成第一经照射环形区域,其中该照射通过烧蚀该第一经照射环形区域的一部分而将该经照射环形区域的该部分变换成封闭式环形微孔。
本公开的另一实施例涉及紧接上文描述的工艺产品,其中该照射包括照射在该第一经照射环形区域外且与该第一经照射环形区域同心的第二经照射环形区域,其中该第二经照射环形区域的该照射烧蚀该第一经照射环形区域的一部分以形成围绕该环形微孔的环形凹部。
本公开的另一实施例涉及一种基于玻璃的产品,该基于玻璃的产品是通过对具有限定对置的第一及第二表面的主体的基于玻璃的物体执行一工艺而形成。用于形成该基于玻璃的产品的该工艺包含:a)形成具有相位分布φPD(r,θ)=φ1(r,θ) φ2(r,θ)的相位装置,其中φ1(r,θ)是等于-k·r·sin(γ)的第一相位项且φ2(r,θ)是等于m·θ的第二相位项,其中(r,θ)是径向极坐标及角坐标,γ是在0.10°≤γ≤20°范围内的轴锥角,且m是在3≤m≤20范围内的拓扑电荷,其中m是整数;b)将高斯激光束引导至该相位装置以将该高斯束转换成环形涡旋波束,该环形涡旋波束具有该相位分布φPD(r,θ)、焦点深度DOF、波长λ及聚焦环,该聚焦环在该焦点深度DOF内且具有内径D1、外径D2及宽度WA=(D2–D1)/2;及c)将该环形涡旋波束引导至该第一表面且穿过该基于玻璃的物体的该主体,藉此照射在该焦点深度内的该主体的第一及第二同心环形区域以形成第一及第二经照射环形区域,其中该照射通过烧蚀该第一经照射环形区域而将该第一经照射环形区域变换成微通孔且将该第二经照射环形区域变换成围绕该微通孔的环形凹部。
额外特征及优点在随后的实施例中陈述,且本领域技术人员将从该描述部分地了解这些额外特征及优点,或通过实践如在书面描述及其申请专利范围以及所附附图中描述的实施例来认识这些额外特征及优点。将理解,先前一般描述及随后的实施例仅为示例性的,且意欲提供概述或框架以理解申请专利范围的性质及特性。
附图说明
包括所附附图以提供进一步理解,且这些附图并入本说明书中且构成本说明书的一部分。这些附图示出一个或多个实施例,且与实施例一起用于解释各种实施例的原理及操作。因而,本公开将结合所附附图自以下的实施例更充分理解,在所附附图中:
图1A是如本文中所揭示的用于形成环形涡旋波束的波束形成系统的示意图,该环形涡旋波束用于在基于玻璃的物体中形成微孔;
图1B是图示轴锥角γ的示例轴锥透镜的特写横截面图。
图1C是环形涡旋波束在焦平面之后的区域中的特写y-z横截面图,示出了环形涡旋波束的焦点深度(depth of focus;DOF)。
图1D是环形涡旋波束的示例强度分布IA(r,θ)的特写理想化表示,其中特写插图图示聚焦环(最内部强度环)及聚焦环的各种关注尺寸,且也图示直接邻近(主)聚焦环的次聚焦环。
图2A类似于图1A且示出示例实施例,其中图1的相位装置不利用轴锥透镜,使得相位分布是完全由相位装置的相位组件限定。
图2B是由光透射性相位板及光反射性主动相位组件形成的相位组件的示例配置的示意图。
图3A是具有平面配置的示例基于玻璃的物体的立面图。
图3B是由可移动支撑台可操作地支撑的图3A的平面的基于玻璃的物体的侧视图。
图3C是示例微孔形成系统的示意图,该微孔形成系统包括波束形成系统以及可移动支撑台及控制该微孔形成系统的操作的控制器。
图3D类似于图1C且图示穿过基于玻璃的物体的主体的一部分的环形涡旋波束,且示出基于玻璃的物体完全驻留在环形涡旋波束的焦点深度内的示例。
图4A图示由输入高斯束通过轴锥透镜形成的空心束的示例仿真灰阶强度剖面IH(r,θ)。
图4B是结合轴锥透镜使用以限定相位装置的总体相位分布φPD(r,θ)的相位组件的示例相位分布φPE(r,θ),其中由相位组件引起的相位分布φPE(r,θ)仅由轴锥角γ=0°及拓扑电荷m=3限定。
图4C类似于图4A且示出相位组件的中心部分不透明,使得限定相位组件的相位特征仅在外部部分中形成的示例。
图4D是相位装置的灰阶相位分布φPE(r,θ),该灰阶相位分布由具有轴锥角γ=20°的转向镜相位及具有拓扑电荷m=3的图4B的相位板的组合限定。
图4E是如通过图4D的相位装置的相位分布φPD(r,θ)形成的环形涡旋波束在焦平面处的示例相位分布φV(r,θ)的仿真二维灰阶图像。
图5图示使用图4D的相位分布φPD(r,θ)的波束形成系统10B的环形涡旋波束及其中的聚焦环在18mm、19mm、20mm及21.5mm的各别距离df处的强度分布IA(r,θ)的四个仿真图像(A至D)。
图6是相位装置60的示例相位分布φPD(r,θ),其中角γ=20°且m=13。
图7类似于图5且图示使用图6的相位分布φPD(r,θ)的图2A的波束形成系统的环形涡旋波束及其中的聚焦环在18mm、19mm、20mm及21.5mm的各别距离df处的强度分布IA(r,θ)的四个仿真图像(A至D),其中图7的聚焦环由于较大拓扑电荷而实质上大于图5的聚焦环。
图8类似于图4C且图标相位装置的相位组件的相位分布φPE(r,θ)的示例,其中角γ=0°且m=13,且其中相位组件的中心部分是不透明的。
图9类似于图5及图7且图示使用图6的相位分布φPD(r,θ)的波束形成系统及图1A的波束形成系统的环形涡旋波束及其中的聚焦环在18mm、19mm、20mm及21.5mm的各别距离df处的强度分布IA(r,θ)的四个仿真图像(A至D)。
图10A是如通过本文中所揭示的波束形成系统形成的环形涡旋波束在微孔形成系统中在箭头AR的方向上引导穿过基于玻璃的物体的主体的特写示意图。
图10B是基于玻璃的物体的主体的经照射部分的特写x-z视图,示出了如何使用环形涡旋波束以通过烧蚀来形成环形微孔。
图10C类似于图10B且示出一示例,在该示例中,实现通过环形涡旋波束的照射,使得环形孔洞延伸穿过基于玻璃的基板的主体且经由去除该主体的中心部分而导致形成实质上圆柱形的微通孔。
图10D类似于图10A且图示图10C的实质上圆柱形的微通孔。
图10E及图10F类似于图10C及图10D且示出一实施例,在该实施例中,次聚焦环用于产生在物体的前表面中的与贯穿孔洞同心的环形凹部。
图10G及图10H类似于图10E且示出示例实施例,在这些实施例中,形成环形微孔而非微通孔,且其中环形微孔及环形凹部可具有不同的相对深度。
图11A及图11B类似于图10A及图10D且示出一实施例,在该实施例中,多个基于玻璃的物体可以堆叠式配置处理以在基于玻璃的物体的每一者中形成微孔。
图12A及图12B类似于图10A及图10D且示出一实施例,在该实施例中,来自环形涡旋波束的照射是用于在基于玻璃的物体的主体中形成环形经修改区域。
图12C是形成于基于玻璃的物体的主体中的环形经修改区域的特写x-z横截面图。
图12D类似于图12B且示出执行蚀刻工艺以去除环形经修改区域的步骤。
图12E类似于图12C且图示通过去除环形经修改区域形成的所得微通孔,连同由蚀刻掉环形经修改区域产生的中心部分。
图12F是基于玻璃的物体的立面图,图示通过两步方法形成的所得微通孔,两步方法是用环形涡旋波束照射以形成环形经修改区域,然后蚀刻环形经修改区域。
图12G及图12H类似于图12C及图12D且示出主及次聚焦环形成同心的环形经修改区域的示例,其中外部环形经修改区域是通过次聚焦环形成且不到达物体的后表面,使得蚀刻工艺可用于形成围绕中心微通孔的环形凹部。
图13是以形成于基于玻璃的物体中的微孔的特写插图阵列图标的示例基于玻璃的物体的立面图。
图14是针对轴锥角γ的不同值的聚焦环的面积AFR(μm)对拓扑电荷m的图表,示出了如何改变轴锥角γ及拓扑电荷m可用于改变聚焦环的大小且因此改变通过环形涡旋波束形成的微孔的大小。
具体实施方式
现在详细地参考本公开的各种实施例,在附图中示出这些实施例的示例。只要可能,在附图中使用相同或类似的参考数字及符号以指代相同或类似部分。附图未必按比例,且本领域技术人员将认识到附图已经简化以示出本公开的关键方面。
如下文陈述的申请专利范围被并入此实施例中且构成此实施例的部分。
坐标(例如,极坐标(r,θ)及笛卡尔坐标)在附图中的一些中图示以用于参考且不旨在对方向或定向的限制。如本领域中常规的,极坐标(r,θ)在(x,y)平面中。
术语“下游”及“上游”是用于描述组件或物体A及B相对于光的行进方向的相对位置,其中B在A下游意味着光在自A至B的方向上移动且在入射在B上之前入射在A上。
术语“基于玻璃”在本文中用于包括完全地或部分地由玻璃、玻璃陶瓷(包括非晶相及晶相)及结晶材料制成的任何物体。
使用本文中所描述的系统及方法形成的最终的基于玻璃的物体构成基于玻璃的产品或基于玻璃的对象。
本文中所使用的词组“P包含Q”及类似表述意味着包括作为特殊情况的“P由Q组成”。
缩写“μm”意味着为10-6米的“微米”或微米。
缩写“nm”意味着为10-9米的“纳米”。
前缀“TW”代表“太拉瓦特(terrawatt)”或1012瓦特。
波束形成系统
图1A是形成适合形成微孔的环形涡旋波束的波束形成系统10B的示例的示意图,如下文所述。波束形成系统10B包括沿着光轴AX布置的激光源20。激光源20沿着光轴AX发射具有高斯强度分布IG(r,θ)的激光束22G。激光束22G因此在下文中被称为“高斯束”22G。示例激光源以1030nm的波长λ操作。示例激光源是基于Yb的二极管泵激光,该激光发射短(例如,飞秒至皮秒)光脉冲LP(参见在下文引入且论述的图3C的特写插图)。诸如激光源的示例是可自立陶宛的Light Conversion of Vilnius获得的PHAROS激光。在其他示例中,激光源20可以800nm或1064nm的波长λ或脉冲激光操作所用的其他类似波长操作。在一示例中,激光源20可产生具有在200飞秒(fs)至20皮秒(ps)范围内的脉冲宽度的光脉冲LP。
图1A的示例波束形成系统10B也包括沿着光轴AX设置且在激光源20下游的轴锥透镜30。轴锥透镜30具有对置表面32及34,其中表面34具有顶点AP在光轴AX上的旋转对称的圆锥形状。图1B是示例轴锥透镜30的特写视图。轴锥透镜30是由角γ限定,该角在本文中被称为轴锥角。轴锥透镜30图示为具有平面表面34,但一般而言,此表面无需是平面的。在一示例中,轴锥透镜30是由熔融硅石形成且使用此项技术中已知的精确透镜形成技术塑形,使得表面32及34是精确表面。在一示例中,轴锥角γ可在0.10°≤γ≤20°范围内。
波束形成系统10B也包括第一及第二间隔隔开的正透镜L1及L2,这些透镜具有各别焦距f1及f2。在一示例中,f1=f2=f,且透镜L2与透镜L1的焦点F1间隔隔开一距离2f。相位组件50是沿着光轴AX设置在第一及第二透镜L1与L2之间,例如,与透镜L2相距距离f,使得第二透镜L2相对于相位组件50构成傅立叶透镜。另外,透镜L1及L2可以相对于轴锥透镜30的傅立叶布置彼此离开距离f1 f2而放置。轴锥透镜30、透镜组件L1及L2及相位组件50构成示例光学系统80。轴锥透镜30及相位组件50构成相位装置60的一示例。在下文论述相位装置60的其他配置。
相位装置60具有总体相位分布φPD(r,θ),而相位组件50具有相位分布φPE(r,θ)。在一示例中,相位组件50包含相位板。相位组件50也可包含主动相位组件(诸如空间光调变器(spatial light modulator;SLM),或可变形镜),该主动相位组件在一示例中是反射性的且折叠光轴AX。在一示例中,相位组件50可包含相位板及主动相位组件两者或SLM,如在下文引入且论述的图2B的示例中所示出。呈绕射光学组件(diffractive optical element;DOE)形式的合适相位板可自以色列耐斯兹敖那市(Ness Ziona,Israel)的HOLO/OR Ltd.获得。
波束形成系统10B具有与透镜L2相距距离df定位的焦平面FP。图1C是焦平面FP的特写视图且包括环形涡旋波束22A的示意性横截面图。涡旋波束形成,从而开始围绕以距离df定位的焦平面FP。涡旋波束22A的峰值强度在某一轴向距离处出现,该轴向距离在距离df之后,但在涡旋波束的焦点深度DOF内。用于在玻璃物体100中钻出微孔的环形涡旋波束22A的理想或“最佳”平面是在DOF内的一平面,使得峰值波束强度落在物体内。此距离可在dfa的最小值至dfb的最大值范围内。请注意,系统10B的焦平面FP的位置是以举例方式选择且便于对应于焦点深度DOF的近端(dfa),但要强调的是,焦平面也可选择为处于焦点深度内的任何位置,包括在焦点深度的中点或在远程(dfb)。
环形涡旋波束22A是实质上非绕射性的波束,该波束在焦平面FP处的行为不同于常规绕射波束。图1C中及其他图中对环形涡旋波束22A的描绘是示意性的且为了易于示出及解释本文中所揭示的设备及方法而有意地过度简化,包括环形涡旋波束的焦点深度DOF的概念。
再次参考图1A,在波束形成系统10B的一般操作中,高斯束22G穿过轴锥透镜32,该轴锥透镜将该高斯激光束转换成空心束22H。空心束22H行进至第一透镜L1,该透镜将空心束22H重新塑形以具有一选定直径。经重新塑形的空心束22H接着入射在相位组件50上,该相位组件将一选定相位赋予空心束22H以形成相位经更改的空心束22H'。相位经更改的空心束22H'接着由第二透镜L2聚焦以形成环形涡旋波束22A,该环形涡旋波束在焦平面FP处具有强度分布IA(r,θ)。强度分布IA(r,θ)的理想化示例图标于图1D中。强度分布IA(r,θ)包括一系列同心环,其中最内部强度环是最亮的且在本文中被称为聚焦环FR,如图1D所示。也图示了直接邻近(主)聚焦环FR的次聚焦环FR'。次聚焦环FR'通常具有实质上小于(主)聚焦环FR的强度,尽管在一些实施例中,可使次聚焦环FR'具有足够强度以在基于玻璃的物体100中形成特征,如下文所述。
环形聚焦环FR具有外径D2及内径D1及环形宽度WA。在一示例中,外径D2可在5μm至60μm范围内,而环形宽度WA可在2μm至9μm范围内。
环形聚焦环FR在焦点深度DOF内可在大小上有微小变化。一般地,诸如涡旋波束的非绕射性波束的焦点深度DOF是由区域限定,穿过该区域,波束的最大强度保持高于一特定强度阈值值或最大强度值的强度阈值百分比。例如,环形涡旋波束22A的焦点深度DOF可限定为最大波束强度不降至环形涡旋波束的最大强度的25%的下的轴向区域。替代地,焦点深度可限定为最大强度不降至物体100的材料烧蚀或材料修改所需的阈值强度的下的轴向区域,如下文所论述。
图2A类似于图1A且示出波束形成系统10B的一示例,其中相位装置60仅包含相位组件50,即,不存在驻留在相位组件上游的单独轴锥透镜30。在一示例中,轴锥透镜30可用扩束器40替换,该扩束器自输入高斯束22G形成扩张高斯束22GE。相位组件50位于透镜L2的前焦平面FF2处,而系统10B的焦平面FP位于透镜L2的后焦平面FB2处。
在图2A的实施例中,相位组件50可包含相位板、主动相位组件或主动相位组件与相位板的组合,其中相位组件经编码具有转向镜波束形成性质(即,轴锥角γ),使得退出相位组件50的波束是调相空心束22H',如下文所解释。在下文论述使轴锥透镜30设置在相位组件50上游以使空心束22H入射在相位组件50上的优点。在一示例中,波束阻断器BB可直接布置在相位装置60下游以帮助阻断任何杂散光,杂散光可由于相位装置60的中心的奇异性或相位调变中的不完全而停留在相位经编码的空心束22H'的中心部分中。
图2B是示出示例相位组件50的特写示意图,该相位组件包含主动相位组件APE及相位板PP。如上所述,主动相位组件可包含SLM。为易于示出,图示折叠镜FM以便于折叠光轴AX且保持相位组件50相对紧凑。主动相位组件APE可操作地连接至APE控制器56,该APE控制器被配置成用于控制主动相位组件的操作(例如,配置主动相位组件中的光调变组件,未图标),如此项技术中已知的。图2B的相位组件50可视相位组件的特定配置而包括一个或多个额外光学组件(例如,透镜等)。在图2B的实施例中,扩张高斯束22GE入射在主动相位组件APE上,该主动相位组件限定空心束22H。此空心束接着经引导至相位板PP,该相位板形成环形涡旋波束22A。在一示例中,透镜L1及L2可以傅立叶布置停留在相位板PP的相对侧上,其中主动相位组件APE或相位板PP如关于图1A所论述。可使用相位组件50的其他配置,诸如单一相位板PP,或经编码具有限定空心束的转向镜性质的主动相位组件APE。
图2A的波束形成系统10B的操作方法类似于图1A的操作方法。如上所述,输入高斯束22G可通过扩束器40扩张以形成扩张高斯束22GE。扩张高斯束22GE入射在相位装置60上。接着将扩张高斯束22GE转换成调相空心束22H'。接着如上文结合图1A的实施例所描述地通过透镜L2使调相空心束22H'聚焦在焦平面FP(该焦平面是由透镜L2的后焦平面FB2限定)处以形成环形涡旋波束22A。
示例基于玻璃的物体及支撑台
图3A是示例基于玻璃的物体(“物体”)100的立面图,该物体可设置于焦平面FP处以由波束形成系统10B形成期待在该物体中形成微孔的微孔形成系统,如下文更详细地解释。在一示例中,物体100具有主体101,该主体限定前表面102、后表面104、侧面106。主体101具有厚度TH。在一示例中,物体100如所示地是平面的,使得厚度TH是实质上恒定的。在一示例中,厚度TH可在0.3mm至2mm范围内。请注意,物体100无需为平面的,且可具有负责使用本文中所描述的系统及方法来形成微孔的任何合理形状及/或大小及/或厚度。
图3B是由可移动支撑台200支撑的物体100的示意性侧视图。物体100图标为搁置在该可移动支撑台的上表面202上。可移动支撑台200能够可操作地连接至台控制器210,该台控制器被配置成用于控制支撑台且因此由该支撑台支撑的物体100的移动。
图3C是微孔形成系统10M连同可移动支撑台200的示意图,微孔形成系统10M利用图1A或图2A的波束形成系统10B。微孔形成系统10M藉助于示例图标为以垂直配置布置且包括可移动支撑台200,物体100以水平定向支撑在该可移动支撑台上。也可使用微孔形成系统10M的水平定向。
微孔形成系统10M包括主控制器90,该主控制器可操作地连接至光学系统80及台控制器210。主控制器90被配置成用于控制微孔形成系统10M的整体操作。在相位装置60包含主动相位组件APE的示例中,主控制器90可连接至APE控制器(图2B)且将指令提供至该APE控制器以用于配置主动相位组件。主控制器90可包含计算机、微计算机、微控制器等,该计算机、微计算机、微控制器等被配置成用于实行体现于非暂时性计算机可读媒体(例如,计算机软件或韧体)中的指令以用于实行本文中所揭示的方法,包括在下文更详细地论述的微孔形成方法。
图3D类似于图1C且图示可操作地设置于微孔形成系统10M内的物体100的轴上部分,以及穿过物体的主体101的环形涡旋波束22A。省略支撑物体的可移动支撑台200以便于图示。图3D示出一示例,其中物体100的厚度TH小于环形涡旋波束22A的焦点深度DOF,或换言之,物体100完全留在焦点深度DOF内。
波束形成模拟及实验结果
相位装置60的相位分布φPD(r,θ)可表示为
φPD(r,θ)=φ1(r,θ) φ2(r,θ)=-k·r·sin(γ) m·θ [等式1]
其中φ1(r,θ)是第一相位项且等于-k·r·sin(γ)且φ2(r,θ)是等于m·θ的第二相位项,其中k是真空中的波向量,r是径向极坐标,θ是角极坐标,γ是前述轴锥角且m是贝色阶数(Bessel order)或拓扑电荷,m是一整数且在一示例中可在3≤m≤20范围内。等式1中的第一相位项φ1(r,θ)是与产生空心束22H的轴锥透镜30相关联的相位分布,而第二相位项φ2(r,θ)是给予环形涡旋波束其涡性质的方位角相位分布。
在诸如图1A所示的一个示例中,轴锥透镜30是用于限定等式1中的第一相位项φ1(r,θ),而相位组件50可具有仅限定等式1中的第二相位项φ2(r,θ)的相位分布φPE(r,θ)。在另一示例中,相位装置60不包括轴锥透镜30,在该情况下,将等式1的第一及第二相位项φ1(r,θ)及φ2(r,θ)两者并入至相位组件50中(即,由相位组件50限定),使得φPD(r,θ)=φPE(r,θ)。在此情况下,轴锥角γ是理解为并非来自单独转向镜组件30,而改为利用复制轴锥透镜的功能性的相位区域或特征51并入(相位编码)至相位组件50中。换言之,此实施例中的轴锥角γ可被视为有效轴锥角。
因为轴锥透镜30具有简单的锥形配置,所以在一些实施例中,使用图1A的波束整形系统10B的实施例且在将涡旋形成(即,贝色束特征)降级至相位组件50的同时使用轴锥透镜限定空心束22H可是较佳的。此可使形成相位装置60的相位组件部分更容易。
使用用于指导微孔制造实验的计算机模型化来实行对波束形成系统10B的操作及环形涡旋波束22A的形成的模拟。使用基于数学的软件(来自Python Software Foundation的PythonTM软件,及来自Mathworks,Inc.(Natick,Massachussetts)的软件)连同使用光线追踪软件(来自Zemax LLC(Kirkland,Washington)的透镜设计软件)作为确定近似波束直径的指导来实行基于傅立叶变换的波束传播模拟。
图4A图示由输入高斯束22G通过轴锥透镜30形成且入射在相位组件50上的空心束22H的示例模拟强度剖面IH(r,θ)。轴锥透镜30具有轴锥角γ=20°。透镜L1及L2具有相等焦距f且间隔隔开一距离2f以限定关于相位组件50的傅立叶配置。
图4B是用于使用图1A的波束形成系统10B的示例配置形成环形涡旋波束22A的示例的相位组件50的示例相位分布φPE(r,θ)。相位分布φPE(r,θ)以灰阶图标,其中π相位由白色表示且-π相位由黑色表示,灰色的等级表示中间相位值。轴锥角γ=20°,而拓扑电荷m=3。
图4C类似于图4B且示出一示例,其中相位分布的中心部分52是不透明的(以交叉影线图示),这是因为空心束22H不穿过相位组件50的中心部分。
图4D是相位装置的灰阶相位分布φD(r,θ),该相位分布由具有轴锥角γ=20°的轴锥透镜及具有拓扑电荷m=3(且无经编码轴锥角,即,γ=0°)的图4B的相位板限定。该相位分布是需要编码至图2A的波束形成系统10B的单一相位组件50上的相同相位分布,这是因为不存在上游轴锥透镜。
图4E是如使用图4D的相位装置60的相位分布φPD(r,θ)在处于距离df=20mm的焦平面FP处形成的环形涡旋波束22A的相位分布φA(r,θ)的相位等高线图表。图4E中的相位等高线清楚地图示两个分布分量,即如由轴锥透镜30限定的相等地隔开的同心环,及由相位组件50的拓扑电荷m确定的多个螺旋涡。
图5图示使用图3B的相位分布φE(r,θ)的波束形成系统10B的通过在18mm、19mm、20mm及21.5mm的各别距离df处计算的同心环强度剖面IA(r,θ)限定的环形聚焦环FR的四个仿真图像(A至D)。聚焦环FR的直径D2(参见图1D)分别测量为16μm、17μm、17μm及18μm。这是在距离Δdf=3.5mm中的约10%的聚焦环FR的直径D2的变化。距离Δdf可被视为波束形成系统10B的示例配置的焦点深度DOF的一个测量,其中直径D2改变不超过10%或诸如7.5%或5%的某一其他选定百分比公差。
在一些情况下,调整通过环形涡旋波束22A形成的聚焦环FR的直径D2可以是期望的。在示例中,可通过将聚焦透镜L2与具有一不同焦距的另一聚焦透镜L2调换或通过改变相位组件50的相位分布φPE(r,θ)来进行此调整。当替换聚焦透镜L2时,可能有必要改变第一透镜L1且重新定位新的第二透镜L2或透镜L1及L2两者。当改变相位组件50时,通常不需要重新配置(例如,重新定位)波束形成系统10B中的其他组件。
在一示例中,可通过增大用于限定相位组件50的相位分布φPE(r,θ)的拓扑电荷m的值来增大聚焦环FR的直径D2。图6是轴锥角γ=20°且拓扑电荷m=13情况下的相位装置60的相位分布φPD(r,θ)的图表。拓扑电荷的此变化使聚焦环FR的直径D2与m=3的上文示例相比增大至约3倍。
图7图示使用图2A的波束形成系统10B(即,无轴锥透镜30)中的图6的相位分布φPD(r,θ)通过同心环强度剖面限定且在用于模拟的18mm、19mm、20mm及21.5mm的各别距离df处计算的环形聚焦环FR的四个仿真图像(A至D)。聚焦环FR的直径D2是分别测量为54μm、56μm、58μm及61μm。这是在距离Δdf=3.5mm中的约10%的聚焦环FR的直径D2的变化。距离Δdf可被视为波束形成系统10B的示例配置的焦点深度DOF的一个测量,其中直径D2改变不超过10%或诸如7.5%或5%的另一选定百分比公差。
能够在不调整其他波束形成系统参数或组件的情况下通过改变相位组件50的相位分布φPE(r,θ)来改变聚焦环FR的直径对于灵活制造系统有利,在柔性制造系统中,存在允许该系统在有变化(预期或未预期的)的情况下作出反应的一定灵活性。因此,利用单微孔形成系统10M可处理多种物体10。
图8是用于图1A的波束形成系统中的示例相位组件50的相位分布φPE(r,θ)的示例图,其中轴锥角γ=0且拓扑电荷m=13,使得相位分布仅由拓扑电荷m限定。请注意,与图4C类似,不需要相位分布φPE(r,θ)的中心(轴上)部分52且可使该中心(轴上)部分变得不透明(以交叉影线图示),这是因为入射在相位组件50上且如通过上游轴锥透镜30形成的空心束22H不穿过该中心部分。这是相位组件50的一有利特征,这是因为制造相位组件的中心部分52通常需要形成具有与剩余外部部分54(例如,大约十微米)相比相对高的空间频率的相位特征51(例如,大约一微米)。无需形成高分辨率相位特征51节约用于形成相位组件52的制造工艺的时间及成本。另外,相位组件50的中心52处的奇异性可防止任何制造工艺能够准确地再现所要相位。
图9图示使用图1A的波束形成系统中的图8的相位分布φPE(r,θ)通过同心环强度剖面限定且在用于模拟的18mm、19mm、20mm及21.5mm的各别距离df处计算的环形聚焦环FR的四个仿真图像(A至D)。聚焦环FR的直径D2分别测量为53μm、55μm、58μm及60μm。这是在距离Δdf=3.5mm中的约10%的聚焦环FR的直径D2的变化。距离Δdf可被视为波束形成系统10B的示例配置的焦点深度DOF的一个测量,其中最小直径D2MIN改变不超过10%或诸如上文陈述的百分比范围中的一者的另一选定百分比公差。
请注意,图7的仿真图像A至D使用图8的相位组件与上游轴锥透镜30的一组合以使用图1A的波束形成系统10B的配置来形成空心束22H,而图9的仿真图像A至D是使用单一相位组件50形成,该单一相位组件50使用图2的波束形成系统10B的配置每次编码轴锥角γ及拓扑电荷m两者。
形成微孔
本公开的一方面涉及使用图3C的微孔形成系统10M以形成环形涡旋波束22A且使用该环形涡旋波束以在物体100中形成一个或多个微孔220(参见图3C的特写插图)。揭示了两种主要示例方法,即单步方法及两步方法。
单步方法
图10A是如通过本文中所揭示的波束形成系统10B形成的环形涡旋波束22A在微孔形成系统10M中在箭头AR的方向上引导穿过物体100的主体101的特写示意图。物体100是使用可移动台200(参见图3C)设置于图像平面IP处。在下文论述用于由选定材料制成的物体100的激光源110的激光功率的示例量。选择激光源110的激光功率,使得环形涡旋波束22A的功率密度(例如110TW/cm2的峰值强度)足以烧蚀物体的材料。
烧蚀工艺最初形成封闭式环形微孔220A,如图10B的特写x-z横截面图所示。环形微孔220限定物体100的主体101中的圆柱形中心部分108。在一示例中,微孔形成工艺由于具有深度DH(“微孔深度”)的环形微孔220A的形成而在此停止,该深度DH是从物体100的前表面102测量。微孔(外部)直径是DM且实质上等于环形涡旋波束的直径D2。
此单步微孔形成工艺可在物体100的其他位置处重复(例如,通过可移动台200的受控移动)以形成环形微孔阵列(参见图13)。微孔深度DH可基于环形涡旋波束22A的功率密度及环形涡旋波束22A照射物体100的时间tE(曝光时间)的量来选择。因为环形涡旋波束22A的曝光时间tE及功率密度可仔细地控制(例如,通过控制入射在物体100上的光脉冲LP的数目),所以微孔深度DH也可仔细地控制在例如若干微米内。
在另一示例中,环形涡旋波束22A继续照射样本10,使得主体101的经照射部分继续被烧蚀,由此使环形孔洞220朝向物体100的后表面104加深(即,微孔深度DH增大),如生长箭头AG所示出。此工艺继续,直至环形微孔220A达到后表面104,如图10C所示。此时,圆柱形中心部分108自主体101的邻近部分分离。分离的圆柱形部分108自己掉落(例如,当自可移动台200提起物体100时)或经去除(例如,通过施加将圆柱形部分拉出的真空)。
图10D类似于图10A且图示基于单步微孔形成工艺形成为物体100中的微通孔220T的所得微孔220。在此,微孔深度DH与形成微通孔220T的位置处的物体厚度TH相同。在一示例中,微通孔220T具有实质上圆柱形的形状。
图10E及图10F类似于图10C及图10D且示出一实施例,在该实施例中,使用次聚焦环FR'以产生在物体100的前表面102中且与微通孔220T同心的环形凹部221。环形凹部221可充当用于碎片收集的位置且也可形成表面纹理。
图10G类似于图10E且示出形成环形微孔220A而非形成微通孔220T的一示例实施例。在此实施例中,环形凹部221与环形微孔220A是同心的。图10H类似于图10G,且图示环形微孔220A及环形凹部221可具有多种不同的相对大小,包括具有实质上相同的大小。
图11A及图11B类似于图10A及图11D且示出多个物体100可以堆叠配置处理以在物体中的每一者中形成微孔220的一实施例。在图11A中所示的一示例中,指数匹配流体225可设置在两个示例堆叠式物体100的面对表面之间以减少反射,减少反射反过来可减小当环形涡旋波束22A进入堆叠中的最下面物体时的环形涡旋波束22A的强度。
方法的堆叠式实施例可用于提高经处理物体100的吞吐量。堆叠式实施例由于例如在2mm与40mm之间的极大(长)焦点深度DOF而变得可能。这允许环形涡旋波束22A在多个堆叠式物体100中形成相对均匀的微孔220。例如,对于2.5mm的焦点深度DOF,堆叠式实施例可容纳四层呈平面片材形式的物体100,每一平面片材具有0.6mm的厚度。这导致吞吐量与处理厚度TH为0.6mm的单一平面片材相比提高至4倍。
两步方法
图12A至图12E示出用于形成微孔220的一示例两步方法。图12A类似于图10A且示出两步工艺中的第一步骤,在第一步骤中,微孔形成系统10M的环形涡旋波束22A在箭头AR的方向上照射物体100。在此实施例中,环形涡旋波束22A的功率密度小于烧蚀组成物体100的材料所需的功率密度。
参考图12B及图12C的特写x-y横截面图,通过图10A的环形涡旋波束22A照射物体100在物体的主体101内形成环形经修改区域111。环形经修改区域111也限定类似于单步实施例中的由环形微孔220A限定的中心部分的中心部分108,其中,中心部分108保持未被修改。环形经修改区域111中的主体101的材料经历结构变化,该结构变化使材料相对于其初始形式变弱。这些结构变化可包括空隙及裂痕的形成,以及材料的整体致密化。此类型的结构变化使环形经修改区域111比包括中心部分108在内的周围未修改区域更容易蚀刻。请注意,环形经修改区域111具有直径与环形涡旋波束22A的直径D2实质上相同的环形形状。
图12D示出两步工艺的第二步骤,其中具有经修改区域111的物体100经受蚀刻工艺250以去除环形经修改区域中的材料。在一示例中,蚀刻工艺250包含酸蚀刻。在一示例中,酸蚀刻工艺包含将图12A的经照射物体100浸没在酸浴(溶液)中以去除环形经修改区域111中的材料。如上所述,环形经修改区域111比物体10的主体101的非经修改区域蚀刻更快。在一示例中,蚀刻工艺可包括使用超声波(例如,超声波浴)及热(经由加热器)以提高蚀刻速率。在一示例中,用作蚀刻剂的酸溶液包括以下酸中的至少一者:HF、HCl。此外,在该示例中,酸溶液也可包括诸如HNO3、H2SO4的其他酸。
如同单步方法,堆叠式实施例可在两步方法中使用。在一个示例中,以堆叠式配置形成环形经修改区域111,且也以堆叠式配置实行蚀刻工艺250。在另一示例中,可将堆叠分离成单一物体100,接着对每一物体分开地实行蚀刻工艺250。
图12E类似于图12C且图示当去除中心部分108时的微通孔220T的形成。微通孔220T具有宽度DM及等于物体100的厚度TH的深度DH。图12F是物体100的立面图,该图图示出所得的微通孔220T。
图12G及图12H类似于图12C及图12D且示出主及次聚焦环FR及FR'形成同心的环形经修改区域的一示例,其中外部环形经修改区域111是通过次聚焦环形成且不到达物体100的后表面104。蚀刻工艺250作用于外部环形经修改区域以形成前述的环形凹部221,使得所得物体100与图10F中所示的物体实质上相同。
微孔阵列
图13是示出物体100的一示例的立面图,微孔220的阵列222在物体100中形成。微孔220可以是环形微孔220A或微通孔220T。示例微孔220可具有在10μm至500μm范围内的直径DM。邻近微孔220之间的间隔可与微孔直径DM的一部分一样小。在一示例中,对于具有10μm直径的微孔220,20μm的中心至中心间隔允许每平方毫米约2500个微孔的孔洞密度。
微孔形成的示例
使用如本文中所揭示且在上文详细论述的图2A的波束形成系统10B对选定类型的玻璃物体100实行微孔形成的实验。激光源110是超快脉冲激光,该超快脉冲激光具有可在0.5瓦特(W)与6W之间调整的功率、一脉冲频率(即,可在3kHz与200kHz之间调整的光脉冲LP的频率、可在0.256皮秒(ps)与10ps之间调整的脉冲宽度及1030nm的操作波长λ。相位装置60是由并入有(经编码的)轴锥角γ及拓扑电荷m的SLM限定。由于轴锥透镜30未用于形成相位装置60,因此波束阻断器BB直接放置在SLM下游以阻断相位经编码空心束22H'的中心部分中的零阶绕射及杂散光,如图示为图2A的波束形成系统10B的示例实施例中的选项。
使用诸如SLM的主动相位组件以形成相位装置60的益处是能够通过在无需换出波束形成系统内的其他光学组件的情况下测试轴锥角γ与拓扑电荷的几个组合来执行不同实验。
在一个实验中,物体100是用于主动矩阵平板显示器的类型的碱土硼铝硅酸盐熔融拉制的玻璃片。该玻璃片具有0.7mm的厚度TH。用具有不同量功率的环形涡旋波束22A照射该玻璃片。分析经照射玻璃片,且发现,激光功率在1500毫瓦至6000毫瓦范围内且基于SLM的相位装置60经程序化具有0.01°的轴锥角γ及m=5的拓扑电荷,形成适合于蚀刻以根据上述的两步工艺形成微孔220的环形经修改区域111。
一旦用于达成该玻璃片的材料修改的基础激光及相位装置参数被确定,则组装图1A的示例波束形成系统10B。波束形成系统10B的相位装置60是使用轴锥角γ为9.5°的精确轴锥透镜30及作为相位组件50的相位板形成,其中该相位板具有0°的轴锥角γ(由上游轴锥透镜的使用引起)及m=3的拓扑电荷。第一及第二透镜L1及L2各自具有焦距f=52mm。根据上文设定激光源110以提供足够电力用于形成环形经修改区域111,使得微孔220可使用上述两步工艺形成。聚焦环FR在70mm的焦距df处具有约25μm的直径D2。焦点深度DOF估计为约40mm。聚焦环FR的峰值强度在df=70mm,但在与此位置相距±20mm处发现类似的直径及强度剖面。在此距离内,聚焦环FR的直径D2仅改变1.4μm,而强度改变33%。请注意,焦点深度DOF可以认为取决于聚焦环的直径D2的大小而小于或大于40mm,且聚焦环的强度可针对给定的微孔形成应用改变。
在一示例中,焦点深度DOF可通过以下操作确定:在环形涡旋波束的传播的方向上以递增步长收集实际环形涡旋波束22A的一系列图像以获得不同轴向位置处的波束强度剖面,接着将这些图像拼接在一起以获得传播方向上的波束强度剖面。具有最高强度(例如,高于选定强度阈值值)的波束强度剖面的部分限定焦点深度DOF。
焦点深度DOF也可通过用环形涡旋波束22A照射物体100且在监测等离子体在该物体上形成的同时轴向地移动该物体(或波束形成系统10B)以改变该物体相对于波束形成系统的焦平面FP的位置来评估。等离子体的形成是微孔形成的指示,使得焦点深度DOF可定义为微孔形成出现经过的距离,或等效地等离子体形成出现经过的距离。如上所述,可通过改变输入射束直径、轴锥角γ及透镜L1及/或L2的焦距中的至少一者来调整焦点深度DOF。
对示例波束形成系统10B执行额外仿真,其中拓扑电荷自m=3增加至m=6,而光学系统80的透镜L1及L2具有各别焦距f1=52mm及f2=26mm以提供50%缩小以将聚焦环FR的直径D2维持在25μm。结果是焦点深度DOF为10mm(自m=3情况减少至4分的一),而聚焦环FR的强度增加至4倍。
为了确定形成微孔需要多少激光曝光,执行一实验,其中使用6000mW、1ps、3kHz的高斯激光束对厚度TH为0.7mm厚的玻璃(可自Corning,Inc.(Corning,New York)获得)的样本进行测试。激光损伤图标为在暴露于一系列1000次拍摄(333ms)至50,000拍摄(16.67s)时出现。
在另一实验中,使厚度TH=0.7mm的碱土硼铝硅酸盐熔融拉制的玻璃片的25mm长乘以25mm宽的样本暴露于具有各种激光参数的激光束,这些激光参数诸如3kHz及200kHz的频率、在1500mW至5500mW范围内的激光功率、30秒至120秒的曝光时间及256fs至10ps的脉冲宽度。接着用10%HF、15%硝酸、75%水(按体积计)的酸溶液蚀刻经照射玻璃片。在90分钟的静态蚀刻之后,形成微通孔。在另一30分钟具有超声波辅助的蚀刻之后,使用60秒及120秒激光曝光时间,形成直径为50μm的微通孔。
上述蚀刻剂溶液的标称蚀刻速率测量为1.6μm/分钟,从而在120分钟后产生192μm的预期蚀刻。在厚度方向上观测到此蚀刻速率,最终厚度为约0.5mm。表面孔洞直径为近似170μm且贯穿孔洞直径为近似75μm,归因于在蚀刻期间的孔洞区域中的废料的阻抗,这两个直径低于标称蚀刻速率。
图14是针对轴锥角γ的不同值(即γ=0.10°、0.25°及0.75°)的聚焦环FR的测量面积AFS(μm2)对拓扑电荷m的图表。轴锥角γ的相对小范围是由在构建示例波束形成系统10B时所使用的光学组件中的限制引起。即使轴锥角γ值小,但图14的图表示出聚焦环FR的大小与环形涡旋波束参数γ及m之间的关系,更高的拓扑电荷m及更低的轴锥角γ产生最大聚焦环面积。这些关系可用于限定聚焦环FR的所要大小且因此限定使用环形涡旋波束22A形成微孔220的所要大小。
优点
本文中所揭示的系统及方法具有许多优点。这些优点包括例如2mm至40mm的相对较大焦点深度DOF,使得不需要波束重新聚焦以用于在基于玻璃的物体中形成厚度至多为约2mm的微孔。另外,可处理相对厚的物体,且在一些示例中,可堆叠多个物体,接着以堆叠式配置处理这些物体。
另一优点是能够视可用激光功率的量及聚焦环的功率密度而使用单步工艺或两步工艺。在物体的主体中形成经修改区域且接着蚀刻物体以形成微孔允许仅必须去除物体主体的已经过照射的环形形状区段。经修改区域的优先蚀刻性质使蚀刻步骤与使用蚀刻工艺形成微孔的常规方法相比相对较快(例如,快10倍至1000倍)。
另一优点是改变聚焦环的大小可通过替换相位组件来完成,在一个示例中,该替换可涉及交换一个相位板与另一相位板,而在另一示例中,该替换可涉及重新程序化主动相位组件。此灵活性在制造中特别地有利,这是因为波束形成系统的改变可快速地进行。
本领域技术人员容易了解,在不脱离如在所附权利要求范围中限定的本公开的精神或范围的情况下,可作出对如本文中所描述的本公开的较佳实施例的各种修改。因此,本公开覆盖这些修改及变化,条件为这些修改及变化在所附申请专利范围及其等同的范围内。
本文用于企业家、创业者技术爱好者查询,结果仅供参考。