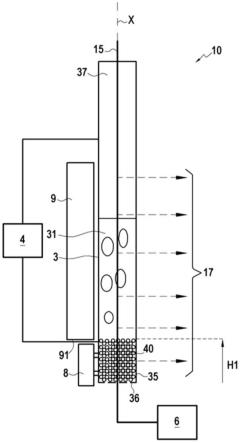
1.本发明涉及一种用于流化床化学气相沉积的设备以及此设备的用途,该设备允许在沉积过程中稳定流化床的温度。
背景技术:
2.流化床化学气相沉积的技术本身是已知的,并且允许微粒被适合于所希望的应用的各种涂层涂覆。
3.然而,希望的是改进流化床化学气相沉积技术的产率。
技术实现要素:
4.本发明涉及一种用于流化床化学气相沉积的设备,该设备至少包括:
[0005]-反应器,该反应器包括处理区域,在处理区域中旨在从气相进行流化床化学气相沉积;进口区域,气相旨在通过进口区域被引入到处理区域中;以及出口区域,气相旨在通过出口区域从处理区域被移除,
[0006]-加热系统,其被构造成加热处理区域,以及
[0007]-冷却系统,其被构造成冷却进口区域,
[0008]
所述设备的特征在于,所述设备还包括多孔热绝缘体,所述多孔热绝缘体存在于进口区域中,并且被构造成由气相穿过,所述多孔热绝缘体在20℃下具有小于或等于3.5w.m-1
.k-1
的有效热导率。
[0009]
在下文中,为了简明,表述“多孔热绝缘体”将用“绝缘体”指代。
[0010]
术语“绝缘体的有效热导率”应当意指由绝缘体所占据的体积(包括其孔隙中的间隙气体)的热导率,而不是构成绝缘体的材料的热导率。存在于绝缘体的孔隙中的间隙气体降低了其有效热导率,并且因此可限制在沉积过程中在被加热的处理区域与被冷却的进口区域之间的散热。这允许在处理区域中稳定流化床的温度,并且减少有效地进行沉积的有用区域的减少现象,从而改善沉积的产率。
[0011]
填充有热导率的气体的多孔热绝缘体的有效热导率λ
eff
可以通过验证以下关系式确定:
[0012]
[数学式1]
[0013][0014]
其中,
[0015]
在以上关系中,λs表示用于形成多孔热绝缘体的材料(即,在颗粒床形式的绝缘体的情况下,颗粒的材料)的热导率,φ表示多孔绝缘体的实心体积分数,或者(1-φ)表示该多孔绝缘体的体积孔隙比率。可以参见出版物gonzo(e.e.).
–
chem.eng.j.,90,第299页(2002)。
[0016]
在示例性实施方式中,多孔热绝缘体在20℃下具有小于或等于0.42w.m-1
.k-1
的有效热导率。
[0017]
这种特征有助于进一步提高涂层沉积操作的产率。
[0018]
特别地,多孔热绝缘体可以在20℃下具有小于或等于0.11w.m-1
.k-1
,例如基本上等于0.11w.m-1
.k-1
的有效热导率。
[0019]
在示例性实施方式中,形成多孔热绝缘体的材料在20℃下具有小于或等于40w.m-1
.k-1
的热导率。
[0020]
这种特征有助于进一步提高涂层沉积操作的产率。
[0021]
在这种情况下,绝缘体是由一种材料形成的,该材料本身是差的热传导体,这在沉积涂层的过程中仍进一步稳定流化床的温度。然而,在可以使用具有较高热导率的材料来形成绝缘体的情况下,这种情况仍然是可选的,因为填充有不良导热的间隙气体的绝缘体的孔隙将绝缘体的有效热导率降低到可接受的值,即使绝缘体由本质上相对导热的材料形成。
[0022]
特别地,形成多孔热绝缘体的材料可以在20℃下具有小于或等于4w.m-1
.k-1
,例如小于或等于3w.m-1
.k-1
的热导率。
[0023]
在示例性实施方式中,多孔热绝缘体的体积孔隙比率大于26%,例如大于或等于32%。
[0024]
这种特征有利地有助于仍进一步减小绝缘体的有效热导率,仍进一步稳定在涂层的沉积过程中的流化床的温度。在颗粒床的特定情况下,此类孔隙率值对应于“块体”或非紧密的填充状态。
[0025]
在示例性实施方式中,多孔热绝缘体是颗粒床。
[0026]
本发明还涉及一种使用如上所述的设备,用于涂覆微粒的方法,该方法至少包括:
[0027]-通过进口区域和多孔热绝缘体,将气相引入到处理区域中,
[0028]-从所引入的气相,将涂层沉积在流化床化学气相沉积的处理区域中存在的微粒上,以及
[0029]-在沉积涂层之后,回收涂覆的微粒。
[0030]
在示例性实施方式中,气相在20℃下具有小于或等于0.04w.m-1
.k-1
的热导率。
[0031]
在示例性实施方式中,在沉积涂层之后,回收涂覆的微粒与来自颗粒床的颗粒的混合物,并且将涂覆的微粒与所述颗粒分离。
附图说明
[0032]
图1示意性地和部分地示例了用于实施并非根据本发明的流化床化学气相沉积的设备。
[0033]
图2示出了在使用图1的设备进行的沉积的过程中,流化床的平均温度随时间的变化。
[0034]
图3示出了在使用图1的设备进行沉积的实施过程中,流化气体的归一化压力损失根据其速度的变化。
[0035]
图4比较了当实施图1的沉积时,对于不同速度的流化气体在沉积之前和之后获得的微粒床的高度。
[0036]
图5示意性地和部分地示出了用于实施根据本发明的流化床化学气相沉积的设备。
[0037]
图6示出了在使用图5的设备进行沉积的过程中,流化床的平均温度随时间的变化。
具体实施方式
[0038]
将参见图1描述不是根据本发明的和能够通过流化床化学气相沉积产生微粒涂层的设备1的结构。流化床化学气相沉积本身是已知的技术。
[0039]
设备1包括由壁限定的反应器3,可以由石英或制成该壁。反应器3包括处理区域31,其中旨在从气相进行流化床化学气相沉积。反应器3进一步包括与气相源6连通的进口区域35,意图将包括待形成的涂层的前体的气相通过该进口区域引入到处理区域31中。进口区域35包括多孔扩散器36,确保气相扩散到反应器3中。源自气相源6的气相通过扩散器36被引入到反应器3中。反应器3进一步包括出口区域37,气相旨在通过该出口区域从处理区域31被移除至反应器3外部。出口区域37与泵送系统(未示出)连通,以确保在反应器3中产生真空。源自气相源6的气相首先经由进口区域35,然后经由处理区域31穿过,然后通过穿过出口区域37被移除至反应器3的外部。反应器3可以沿着竖直轴线x延伸。进口区域35、处理区域31和出口区域37沿着轴线x彼此跟随。处理区域31存在于进口区域35与出口区域37之间。
[0040]
待处理的微粒床最初搁置在扩散器36上,并且气相被注入在扩散器36下方,并且从底部至顶部穿过微粒床。气体的这种向上移动支撑微粒床的重量,并且确保它们的流化状态。
[0041]
设备1包括加热系统9,该加热系统被构造成用于将处理区域31加热至允许在微粒上从包含在气相中的前体形成涂层的温度。加热系统9可以被构造成产生电阻加热,或者可替代地感应加热。加热系统9可以围绕处理区域31的整个圆周,或者仅围绕其一部分被布置。位于反应器3中心的套筒15内部的热电偶17被布置在反应器3中的各个位置处,并且允许在流化床中的各个高度处监测温度随时间的变化。设备1进一步包括被构造成冷却进口区域35的冷却系统8。冷却系统8可以包括回路,冷却流体在该回路中流动,控制在小于或等于50℃的温度,例如20℃。冷却系统8可以是冷却凸缘的形式。冷却流体可以是水。冷却系统8可以防止扩散器36的温度变得过高,以避免其由于从气相所产生的沉积而导致的堵塞。加热系统9沿着反应器3的轴线x偏离冷却系统8。加热系统9沿着反应器3的轴线x偏离扩散器36。
[0042]
为了进行涂层而被引入到反应器3中的气相取决于待获得的涂层的性质,并且本领域技术人员使用它们的常识来选择它,并且在温度压力和流速方面选择相关的沉积条件。气相通常包括惰性载气,如分子氮。可以在标准条件下使用气态前体,在这种情况下,它们可以在被引入到反应器3中之前与载气混合。也可以在标准条件下使用液态前体,在这种情况下,可以将载气起泡而进入到液态前体中,以便被富集,然后被引入到反应器3中。
[0043]
在热解碳涂层的沉积的非限制性实施例中,分子氮可以用作载气。用于将载气引入如图1所示的具有5厘米直径和1米高度的反应器3中的流速可以在500标准立方厘米/分钟与3000标准立方厘米/分钟之间,例如在750标准立方厘米/分钟与1250标准立方厘米/分
钟之间。施加在处理区域31中的温度可以是在850℃与1100℃之间,例如在925℃与1000℃之间。加热系统9可以位于扩散器36上方15厘米处。在该非限制性情况下,可以使用丙烷作为待沉积的热解碳的前体。其流速可以在载气流速的5%与30%之间,例如在载气流速的10%与20%之间。用于热解碳的其他前体的实施例包括甲烷/丙烷混合物或天然气作为气态前体。它们还可以包括液态前体,如甲苯、环己烷或乙醇。
[0044]
使用图1的设备1进行的沉积给出了令人满意的结果。尽管如此,发明人已经观察到流化床的平均温度在沉积过程中下降。实际上,在扩散器36处维持适中的温度,以便避免由于来自气相的沉积的阻塞,使得冷却的进口区域构成散热区域。反应器3的壁与流化床之间的热交换基本上通过微粒对流和辐射发生。因此,流化床容易地将热量释放至进口区域35中的反应器3的壁。这种散热导致在沉积过程中流化床内的平均温度降低,并且导致有效进行沉积的有用区域的减少,这导致产率下降。
[0045]
下面详细描述由发明人获得的已经允许实施这种现象的实验结果。
[0046]
发明人在具有以下特性的多孔氧化铝粉末上进行碳沉积操作:该粉末的微粒属于geldart分组a或b,这些微粒的直径d50是在4μm与20μm之间,这些微粒的比表面积是200m2/g,并且由这些原始微粒(在沉积之前)形成的固定床的初始空隙比率等于80%。
[0047]
在1000℃的处理区域31中的设定点温度以及400毫巴的反应器3中的压力下由丙烷沉积碳。在沉积过程中所使用的微粒的初始质量是290克,对应于23.3cm的流化床的初始高度。丙烷流速保持在200标准立方厘米/分钟,并且氮气流速保持在600标准立方厘米/分钟。
[0048]
在图2中示出了在沉积过程中流化床的平均温度随时间的变化。在这个图中,丙烷注入由虚线“a”表示,并且丙烷注入的结束由虚线“b”表示。观察到流化床内的平均温度倾向于在沉积过程中下降。微粒床的活性体积趋于减小,这导致沉积产率的降低。发明人已经观察到,这些热不稳定性伴随有管壁的外部温度的下降和在冷却系统8中循环的冷却流体的温度的增加。热监测还表明,在停止丙烷之后,所有的热干扰被衰减,并且流化床的温度倾向于再次增加,然而没有返回到它在沉积之前的值。
[0049]
图3示出了气体所经受的归一化压降(δp*)根据其速度,随时间的变化。
[0050]
δp*等于由穿过流化床的气体所经受的测量的压降与该压降的理论值之间的比率。根据以下关系式,由微粒床的重量相对于其表面积,计算理论值:
[0051]
[数学式2]
[0052][0053]
因此,δp*的值表示验证流化方案的质量的一种方式。δp*的值等于1表明所有微粒处于可以被描述为均质的流化状态。
[0054]
观察到获得了接近1的δp*的值,这表明在沉积之后这些粉末保持了均质地流化的能力。另一方面,观察到沉积后粉末床的膨胀高度的降低(参见图4)。在最低流化时粉末床的高度降低了大约13%。在图4中,十字示出了沉积之后微粒床的高度,并且圆示出了沉积之前微粒床的高度。
[0055]
所有这些结果证实了通过在冷却的进口区域35处的微粒对流的散热现象。
[0056]
在此观察之后,发明人已经提出了图1的设备1中的改变,该改变使得有可能减少在进口区域35中的热交换。在图5中提供了根据本发明的设备10的示图,该设备解决了这个问题。
[0057]
设备10包括与设备1相同的元件,并且它们以相同的方式进行了附图标记。为了减少在冷却的进口区域35中的散热,本发明提出向反应器3提供多孔热绝缘体40,该多孔热绝缘体具有如以上所指出的相对低的有效热导率。绝缘体40的孔隙允许气相通过,并且参与其有效热导率的降低。绝缘体40的体积孔隙比率可以在26%与48%之间,例如在34%与40%之间,例如基本上等于37%。绝缘体40的孔隙可以具有曲折形状。绝缘体40存在于扩散器36与处理区域31之间。绝热体40可以覆盖进口区域35的大于50%、或甚至至少75%、或甚至基本上全部高度而存在。绝热体40可以在冷却系统8在其上延伸的高度的大于50%、或甚至至少75%、或甚至基本上全部高度上而存在。绝热体40可以从扩散器36至少延伸到在高度h1处存在的加热系统9的下部91。加热系统9的下部91对应于位于进口区域35的侧面上的加热系统9的端部。然而,本领域技术人员将确保绝缘体40不会延伸超过加热系统9的下部部分91太高,以避免绝缘体40经受太高的温度,该太高的温度可能导致来自气相的沉积、堵塞其孔隙和阻碍气相的循环。通过他的常识,本领域技术人员知道确定绝缘体40必须延伸的高度,以便获得所寻求的优点。例如,本领域技术人员将选择绝缘体40的高度,以便在2小时沉积结束时获得20℃的流化床的平均温度的最大降低。如上所述,形成绝缘体40的材料可以导热或不导热。不良导热材料可以有利地用于形成绝缘体40,例如陶瓷材料,诸如氧化锆。形成绝缘体40的材料在20℃下的热导率可以在0.15w.m-1
.k-1
与418w.m-1
.k-1
之间,例如在0.15w.m-1
.k-1
与40w.m-1
.k-1
之间,例如在0.15w.m-1
.k-1
与4w.m-1
.k-1
之间,例如在0.15w.m-1
.k-1
与3w.m-1
.k-1
之间。绝缘体40可以是颗粒床的形式。在这种情况下,绝缘体40由颗粒的堆叠形成。形成绝缘体40的颗粒可以堆叠成块体(不规则堆叠)。绝缘体40可以由与待涂覆的微粒不同的材料形成。可替代地,可以使用由部分烧结的块体形成的绝缘体40,保持足够开放的孔隙,以允许气相通过,同时具有希望的有效热导率。
[0058]
当然,本领域技术人员将小心地选择绝热体40,使得它在气相的通过过程中保持固定,这样使得待涂覆的微粒不会停留在其孔隙中,并且使得它不会引起流化气体中的显著压降。本领域技术人员从他的常识知道用于形成绝缘体40的材料的密度的选择,以及其孔隙的选择,以便响应这些条件。例如,有可能使用由块状颗粒形成的颗粒床,该块状颗粒具有小于或等于10mm,例如在0.5μm与10mm之间的平均直径d50,以及大于或等于3g/cm3,例如在3.2g/cm3与9g/cm3之间的密度。在上述具有5厘米直径和1米高度的反应器3的实施例的情况下,例如,有可能使用氧化锆珠粒的块状堆叠,以便形成绝缘体40,该氧化锆珠粒具有等于1mm的平均直径d50。
[0059]
如在流化床化学气相沉积方法中常见的,将注意在沉积过程中获得一种流化现象。为了允许监测流化,设备10包括差压传感器4,使得能够评估穿过床的气体的压降。本领域技术人员可以有利地将这个压降保持在接近床的重量与反应器3的截面之间的比率( /-20%)的值,以便保证流化状态。本领域技术人员也要注意床内部温度的相对均匀性。通过气泡的存在获得这种热性质,最优操作的流化床的特征,这些气泡确保待涂覆的微粒的优异搅拌。热电偶17能够控制床的等温特性。因此,从通过热电偶显示的最大温差,可以评估流化的质量。例如,本领域技术人员可以采用小于或等于20℃的最大温差进行沉积,以进行
高温沉积(大于800℃)。
[0060]
通过化学气相沉积从气相可以获得涂层。气相在20℃下可以具有小于或等于0.04w.m-1
.k-1
,例如小于或等于0.035w.m-1
.k-1
的热导率。气相的热导率可以在0.01w.m-1
.k-1
与0.04w.m-1
.k-1
之间,例如在0.01w.m-1
.k-1
与0.035w.m-1
.k-1
之间。
[0061]
沉积后,获得包含核和包裹核的表面涂层的微粒,通过流化床气相沉积获得该涂层。微粒被称为核-壳微粒。待涂覆的微粒可以是任何种类,例如由陶瓷材料、碳或金属材料制成。根据所希望的应用,所沉积的涂层可以是任何种类,例如陶瓷或碳或金属。微粒的尺寸和形状可以根据所希望的应用而变化。待涂覆的微粒可以属于geldart分组a或b。所沉积的涂层可以是单层或多层,通过在不同层的沉积之间改变前体的性质,以便沉积具有不同化学性质的层。使用根据本发明的方法涂覆的微粒可以用于各种应用中,例如,形成催化剂或烧结助剂。
[0062]
进行试验以涂覆以上详述的多孔氧化铝粉末,此时使用如图5所示的根据本发明的设备10的实施例,其他操作条件保持相同。
[0063]
图6中给出了在沉积过程中对流化床的平均温度的监测。在这个图中,丙烷注入由虚线“a”表示,并且丙烷注入的结束由虚线“b”表示。观察到使用绝缘体40导致在沉积操作过程中流化床的高热稳定性,并且导致提高的沉积产率。在涂层沉积之后,从反应器3提取涂覆的微粒。
[0064]
当绝缘体40为颗粒床的形式时,可能需要进行将涂覆的微粒与形成绝缘体40的颗粒分离的步骤。为此目的,各种方法是可能的。特别地,可以进行筛分,以便由于它们不同的尺寸和形状而将涂覆的微粒与颗粒分离。在通过筛分将涂覆的微粒与颗粒分离的情况下,可以有利地选择具有大于或等于0.5μm的平均直径d50的颗粒。可替代地,涂覆的微粒或颗粒可以被磁性地吸引,以便将它们分离。
[0065]
表述“在
……
与
……
之间”应理解为包括端值。
再多了解一些
本文用于创业者技术爱好者查询,仅供学习研究,如用于商业用途,请联系技术所有人。