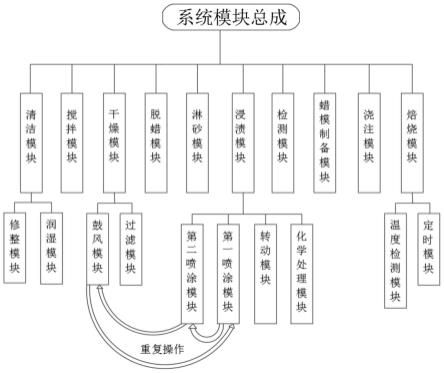
1.本发明涉及蜡模铸造技术领域,尤其涉及一种低温蜡精密铸造系统。
背景技术:
2.大型复杂薄壁精密铸件用整体蜡模的轮廓尺寸常常超越1m,常常分布着众多的凸台与空腔等复杂结构,因此在使用蜡模制壳过程时,面层浆料涂挂的均匀性难度很大使其精准度不够好,强度不高。
3.普遍使用的精密铸造方法,通常是从模具制作、制蜡模、制壳模、脱蜡、焙烧、浇注金属而得到铸件,对于一些结构较复杂的铸件,的大体积铸件,其壳模强度不能得到保证,铸件的质量也很难得到保障,所以行业中,该种铸件一般都采用砂铸来完成,但是砂铸不能达到精密铸造的尺寸精度,且铸件的表面强度差、精度低,不能满足人们的要求,因此,提出一种低温蜡精密铸造系统显得非常必要。
技术实现要素:
4.(一)解决的技术问题
5.针对现有技术的不足,本发明提供了一种低温蜡精密铸造系统,解决了一般低温蜡铸件的表面强度差、精度低,不能满足人们的要求的问题。
6.(二)技术方案
7.为了实现上述目的,本发明采用了如下技术方案:
8.一种低温蜡精密铸造系统,包括系统模块总成,所述系统模块总成包括用于清洁蜡模的清洁模块、干燥模块和搅拌模块、浸渍模块、淋砂模块、检测模块、脱蜡模块、蜡模制备模块、浇注模块,所述蜡模制备模块采用低温蜡和机械注蜡技术,制作与铸造件一致并包含有保温冒口的蜡模,所述清洁模块包括修整模块,修整模块连接有润湿模块,所述干燥模块包括鼓风模块和设置在出风口处的过滤模块,所述系统模块总成包括焙烧模块,且焙烧模块包括温度检测模块和定时模块,所述浸渍模块连接有第一喷涂模块、第二喷涂模块,且第一喷涂模块在浸渍后在蜡模的表面涂用锆粉与硅溶胶粘结剂配制浆液,然后用锆砂在蜡模表面进行人工浮砂,然后对其进行干燥处理,所述第二喷涂模块在第一喷涂模块处理后蜡模表面浸涂用马来粉与硅溶胶粘结剂配制的浆液,然后马来砂在蜡模表面进行人工浮砂,然后进行干燥处理,并在干燥后进行重复第一喷涂模块和第二喷涂模块的操作1-3次。
9.在前述方案的基础上,所述清洁模块包括清洁池和清洁剂,把蜡模放入清洁池中再加入清洁剂进行浸泡清洗,然后再用清水冲洗,清洁模块与干燥模块相连接。
10.进一步的,所述清洁剂为烷基糖苷类非离子表面活性剂和月桂醇聚氧乙烯醚磺基琥珀酸酯二钠,且浸泡时间为20-34秒。
11.作为本发明再进一步的方案,所述搅拌模块包括电机和搅拌杆,搅拌模块包括控制模块和定时模块。
12.在前述方案的基础上,所述浸渍模块中包括转动模块,转动模块与淋砂模块和检
测模块相连接,转动模块带动蜡模在模壳面层浆料中正向和反向各转动6-10周,使模壳面层浆料完全覆盖蜡模表面,将蜡模提出模壳面层浆料的液面,以45
°
倾角将蜡模托盘正向和反向各转动,7-9周,将浆料流到浆料桶中,然后进行淋砂。
13.进一步的,所述脱蜡模块进行脱蜡时整体的压力为0.6mpa,时间为20-40分钟。
14.作为本发明再进一步的方案,所述焙烧模块焙烧时首先在500-600摄氏度以前升温速度控制在100-140摄氏度/小时,然后在450-540摄氏度保温2-4小时,当全速升温到1000-1200摄氏度,且保持此摄氏度半个小时,最后出炉冷却。
15.在前述方案的基础上,所述浸渍模块连接有化学处理模块,在浸渍前,化学处理模块采用化学气相沉积法在蜡模表面沉积耐火涂层,耐火涂层包括氧化铝的基质相、碱性酚醛树脂基质相以及纳米颗粒相。
16.本发明的有益效果为:
17.1.本发明中,通过壳模多次浆液浸粘与人工浮砂,并采用分段升温焙烧方式,形成高强度的壳模,更稳定,能进一步提高铸件的表面精度。
18.2.本发明浸泡时通过搅拌杆搅动清洁池中的清洁液,使其流动,清洁液充分与蜡模相接处,液体产生波动,使得蜡模表面的杂质更容易脱落,节省清洁时间的同时提高了清洁效果。
19.3.本发明中,确定蜡模表面和内腔无浆料堆积后,进行淋砂,若有浆料堆积,则对蜡模进行旋转,进行控浆和甩浆,直至蜡模表面和内腔无浆料堆积后,进行淋砂,提高强度和精度。
20.4.本发明中,通过耐火涂层的设置,能够提高产品的耐火性能,而且大大提高了壳模的强度,达到了铸造大铸件的强度要求。
附图说明
21.图1为本发明提出的一种低温蜡精密铸造系统的系统框架结构示意图。
具体实施方式
22.下面将结合本发明实施例中的附图,对本发明实施例中的技术方案进行清楚、完整地描述,显然,所描述的实施例仅仅是本发明一部分实施例,而不是全部的实施例。需要说明的是,除非另有明确的规定和限定,术语“安装”、“连接”、“设置”应做广义理解,对于本领域的普通技术人员而言,可以根据具体情况理解上述术语在本专利中的具体含义。
23.实施例1
24.参照图1,一种低温蜡精密铸造系统,包括系统模块总成,系统模块总成包括用于清洁蜡模的清洁模块、干燥模块和搅拌模块、浸渍模块、淋砂模块、检测模块、脱蜡模块、蜡模制备模块、浇注模块,蜡模制备模块采用低温蜡和机械注蜡技术,制作与铸造件一致并包含有保温冒口的蜡模,清洁模块包括修整模块,修整模块连接有润湿模块,润湿模块使用的润湿剂为jfc润湿剂,干燥模块包括鼓风模块和设置在出风口处的过滤模块,系统模块总成包括焙烧模块,且焙烧模块包括温度检测模块和定时模块,浸渍模块连接有第一喷涂模块、第二喷涂模块,且第一喷涂模块在浸渍后在蜡模的表面涂用锆粉与硅溶胶粘结剂配制浆液,然后用锆砂在蜡模表面进行人工浮砂,然后对其进行干燥处理,第二喷涂模块在第一喷
涂模块处理后蜡模表面浸涂用马来粉与硅溶胶粘结剂配制的浆液,然后马来砂在蜡模表面进行人工浮砂,然后进行干燥处理,并在干燥后进行重复第一喷涂模块和第二喷涂模块的操作1次,壳模通过多次浆液浸粘与人工浮砂,并采用分段升温焙烧方式,形成高强度的壳模,更稳定,能进一步提高铸件的表面精度。
25.本发明中清洁模块包括清洁池和清洁剂,把蜡模放入清洁池中再加入清洁剂进行浸泡清洗,然后再用清水冲洗,清洁模块与干燥模块相连接,清洁剂为烷基糖苷类非离子表面活性剂和月桂醇聚氧乙烯醚磺基琥珀酸酯二钠,且浸泡时间为28秒,浸泡时通过搅拌杆搅动清洁池中的清洁液,使其流动,清洁液充分与蜡模相接处,液体产生波动,使得蜡模表面的杂质更容易脱落,节省清洁时间的同时提高了清洁效果。
26.尤其的,搅拌模块包括电机和搅拌杆,搅拌模块包括控制模块和定时模块,浸渍模块中包括转动模块,转动模块与淋砂模块和检测模块相连接,转动模块带动蜡模在模壳面层浆料中正向和反向各转动8周,使模壳面层浆料完全覆盖蜡模表面,将蜡模提出模壳面层浆料的液面,以45
°
倾角将蜡模托盘正向和反向各转动9周,将浆料流到浆料桶中,确定蜡模表面和内腔无浆料堆积后,进行淋砂,若有浆料堆积,则对蜡模进行旋转,进行控浆和甩浆,直至蜡模表面和内腔无浆料堆积后,进行淋砂,提高强度和精度。
27.实施例2
28.参照图1,一种低温蜡精密铸造系统,包括系统模块总成,系统模块总成包括用于清洁蜡模的清洁模块、干燥模块和搅拌模块、浸渍模块、淋砂模块、检测模块、脱蜡模块、蜡模制备模块、浇注模块,蜡模制备模块采用低温蜡和机械注蜡技术,制作与铸造件一致并包含有保温冒口的蜡模,清洁模块包括修整模块,修整模块连接有润湿模块,润湿模块使用的润湿剂为jfc润湿剂,干燥模块包括鼓风模块和设置在出风口处的过滤模块,系统模块总成包括焙烧模块,且焙烧模块包括温度检测模块和定时模块,浸渍模块连接有第一喷涂模块、第二喷涂模块,且第一喷涂模块在浸渍后在蜡模的表面涂用锆粉与硅溶胶粘结剂配制浆液,然后用锆砂在蜡模表面进行人工浮砂,然后对其进行干燥处理,第二喷涂模块在第一喷涂模块处理后蜡模表面浸涂用马来粉与硅溶胶粘结剂配制的浆液,然后马来砂在蜡模表面进行人工浮砂,然后进行干燥处理,并在干燥后进行重复第一喷涂模块和第二喷涂模块的操作2次,壳模通过多次浆液浸粘与人工浮砂,并采用分段升温焙烧方式,形成高强度的壳模,更稳定,能进一步提高铸件的表面精度。
29.本发明中清洁模块包括清洁池和清洁剂,把蜡模放入清洁池中再加入清洁剂进行浸泡清洗,然后再用清水冲洗,清洁模块与干燥模块相连接,清洁剂为烷基糖苷类非离子表面活性剂和月桂醇聚氧乙烯醚磺基琥珀酸酯二钠,且浸泡时间为30秒,浸泡时通过搅拌杆搅动清洁池中的清洁液,使其流动,清洁液充分与蜡模相接处,液体产生波动,使得蜡模表面的杂质更容易脱落,节省清洁时间的同时提高了清洁效果。
30.尤其的,搅拌模块包括电机和搅拌杆,搅拌模块包括控制模块和定时模块,浸渍模块中包括转动模块,转动模块与淋砂模块和检测模块相连接,转动模块带动蜡模在模壳面层浆料中正向和反向各转动7周,使模壳面层浆料完全覆盖蜡模表面,将蜡模提出模壳面层浆料的液面,以45
°
倾角将蜡模托盘正向和反向各转动8周,将浆料流到浆料桶中,确定蜡模表面和内腔无浆料堆积后,进行淋砂,若有浆料堆积,则对蜡模进行旋转,进行控浆和甩浆,直至蜡模表面和内腔无浆料堆积后,进行淋砂,提高强度和精度,脱蜡模块进行脱蜡时整体
的压力为0.6mpa,时间为30分钟。
31.需要特别说明的是,焙烧模块焙烧时首先在580摄氏度以前升温速度控制在120摄氏度/小时,然后在500摄氏度保温2小时,当全速升温到1100摄氏度,且保持此摄氏度半个小时,最后出炉冷却,浸渍模块连接有化学处理模块,在浸渍前,化学处理模块采用化学气相沉积法在蜡模表面沉积耐火涂层,耐火涂层包括氧化铝的基质相、碱性酚醛树脂基质相以及纳米颗粒相,通过耐火涂层的设置,能够提高产品的耐火性能,而且大大提高了壳模的强度,达到了铸造大铸件的强度要求。
32.以上所述,仅为本发明较佳的具体实施方式,但本发明的保护范围并不局限于此,任何熟悉本技术领域的技术人员在本发明揭露的技术范围内,根据本发明的技术方案及其发明构思加以等同替换或改变,都应涵盖在本发明的保护范围之内。
再多了解一些
本文用于创业者技术爱好者查询,仅供学习研究,如用于商业用途,请联系技术所有人。