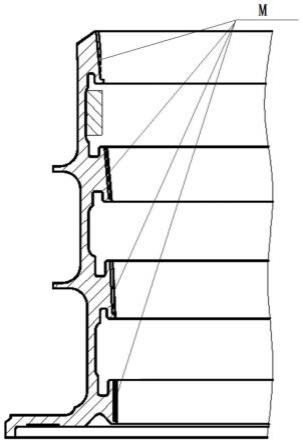
1.本发明涉及航空发动机零部件的表面涂层的结构设计和应用技术领域,特别提供了一种用于航空发动机后机匣高温可磨耗封严涂层。
背景技术:
2.航空发动机后机匣内壁表面要求喷涂封严涂层,服役过程中转子叶片与涂层刮削磨擦,起到提高发动机气密性及保护叶片基体的作用。目前采用氧乙炔火焰棒材喷涂的方法制备该涂层,主要存在以下问题:一是氧乙炔火焰棒材喷涂工艺起源于俄罗斯,为上世纪70年代开发,其主要原理为通过氧乙炔焰流将高致密度的棒材融化,并经焰流及压缩空气加速、雾化,最终沉积在基材上制备出相应的涂层,但存在熔滴雾化不均匀造成的涂层质量不稳定等问题,且设备对于氧气、乙炔流量等工艺参数控制精度较低;二是棒材是采用硅基粘结剂将ni、bn等成分混合压制而成,存在棒材同轴度不稳定、断丝等问题,从而影响涂层质量;三是棒材火焰喷涂设备在喷涂到棒材尾端时,因送棒装置不能完全将棒材送出喷涂,需要操作者用新的棒材顶住前推才能保证喷涂过程的连续,存在送丝速度不稳定的现象。
3.人们迫切希望获得一种技术效果优良的用于航空发动机后机匣高温可磨耗封严涂层。
技术实现要素:
4.本发明的目的是提供一种技术效果优良的用于航空发动机后机匣高温可磨耗封严涂层。在航空发动机后机匣m处喷涂高温可磨耗封严涂层,参见附图1,解决航空发动机后机匣封严涂层服役过程中剥落等问题,从而提高发动机性能稳定性。
5.所述用于航空发动机后机匣高温可磨耗封严涂层具体为镍-氮化硼涂层,镍-氮化硼涂层由镍-氮化硼粉末经过氧乙炔火焰喷涂制成,所述镍-氮化硼粉末的成分及重量百分比如下:bn:12.5-14.5%,cuo:7.0-10.0%,cdo:1.0-1.5%,sio2:≤6.0%,c:1.0-3.0%,余量为ni。
6.优选的,所述镍-氮化硼涂层与零件基体之间设置镍铝过渡层。
7.优选的,所述用于航空发动机后机匣高温可磨耗封严涂层硬度范围为hb8~10,在700
±
10℃下加热保温,然后采用水冷热震,反复15次,涂层应无剥落,无分层。
8.所述用于航空发动机后机匣高温可磨耗封严涂层制备步骤如下:
9.步骤一,除油及保护。清理待喷涂零件表面,去除待喷涂零件表面油污、附着物等污染物;采用耐高温压敏胶带遮蔽非喷涂区域。
10.步骤二,吹砂处理。对待喷涂零件表面吹砂粗化;表面吹砂粗化是为了清洁、粗化和活化零件基体合金表面,提高涂层与零件基体之间的结合强度。
11.步骤三,大气等离子喷涂镍铝过渡层,其中,电流500-550a,氩气流量:50-55nlpm,氢气流量:10-12nlpm,送镍铝粉速率:40-45g/min,零件表面线速度:800-850mm/s。所述镍铝粉末的成分及重量百分比如下:al:4-4.5%,ni:≥95%;有机物≤0.5;fe s=≤0.5。
12.步骤四,氧乙炔火焰粉末喷涂镍-氮化硼涂层,其中,将镍-氮化硼粉末放置在送粉器内,通过惰性气体ar,将镍-氮化硼粉末送入氧乙炔火焰中,送镍-氮化硼粉末速率:30-35g/min,氧气流量:22-26nlpm,乙炔流量:16-18nlpm,零件表面线速度:400-430mm/s,喷枪与零件表面距离:180-200mm。
13.步骤五,清理及涂层性能检测。对完成喷涂的零件拆除用于保护非喷涂区域的高温压敏胶带,并清理表面粉尘等污染物;检查涂层外观及性能。
14.为保证镍-氮化硼涂层起到提高发动机气密性及保护叶片基体的作用,且能够长期稳定使用,其关键是将涂层硬度及热震性能控制在一个合适的范围。涂层硬度过高时,会对叶片造成磨损,达不到保护叶片的作用,硬度过低则涂层自身强度不足,与叶片刮磨时易因受力而产生掉块;同时发动机服役过程是一个冷热交替的过程,其会产生一定的冷热交变应力,因此需要涂层具备一定的抗热震性能,才能实现长期稳定的工作。
15.所述用于航空发动机后机匣高温可磨耗封严涂层,采用氧乙炔火焰对喷涂材料进行加热、加速,并最终沉积在基材上制备出相应涂层。但由于喷涂材料状态不同,其在焰流中的烧蚀、氧化、分解等存在一定的差异,对得到的涂层性能有较大的影响。如镍等金属在涂层组织中起骨架支撑作用,其会增加涂层硬度,提高涂层结合力,但过量则会导致涂层刮削性能下降;氮化硼等非金属起润滑作用,其过量则导致涂层内部强度不足而产生掉块等问题。因此针对火焰粉末喷涂的工艺特点,确定了采用团聚制粒技术生产镍-氮化硼粉末的化学成分(wt%):bn:12.5-14.5%,cuo:7.0-10.0%,cdo:1.0-1.5%,sio2:≤6.0%,c:1.0-3.0%,余量为ni。
16.所述用于航空发动机后机匣高温可磨耗封严涂层是采用镍-氮化硼粉末替代棒材,并采用氧乙炔火焰粉末喷涂工艺进行镍-氮化硼涂层的生产制备,与火焰棒材喷涂工艺相比,具有以下优点:一是镍-氮化硼粉末是采用团聚制粒技术制备而成,并采用筛分的方式控制粉末的粒度分布,均匀性要明显优于棒材;二是粉末火焰喷涂是将喷涂用粉末放置在送粉器内,然后通入可控流量的惰性气体ar,将粉末通过专用的送粉管送入氧/乙炔火焰中,且在送粉器内有电机带动搅拌器对粉末进行不断的搅拌,以保证粉末的均匀性,送料过程更加稳定、可控;三是粉末火焰喷涂设备工艺参数控制精度高,且在信息化、自动化方面有着较为明显的优势。
17.所述用于航空发动机后机匣高温可磨耗封严涂层,可以满足航空发动机后机匣的封严需求,提高了发动机工作效率,研究出的镍-氮化硼粉末成分能够保证制备的涂层具有优异的可刮削性能,完全满足发动机服役要求;设计的基体 过渡层 封严涂层的应用结构大大降低了涂层掉块的风险,延长了涂层使用寿命;同时采用的氧乙炔火焰粉末喷涂制备工艺具备操作简单、加工效率高、成本低,可实现局部喷涂等特点,有利于航空发动机、燃机及相关行业其它零组件的批量生产。
附图说明
18.下面结合附图及实施方式对本发明作进一步详细的说明:
19.图1为后机匣零件及其喷涂镍-氮化硼涂层部位;
20.图2为显微镜下过渡层和封严涂层显微组织图。
具体实施方式
21.实施例1
22.所述用于航空发动机后机匣高温可磨耗封严涂层具体为镍-氮化硼涂层2,镍-氮化硼涂层2由镍-氮化硼粉末经过氧乙炔火焰喷涂制成,所述镍-氮化硼粉末的成分及重量百分比如下:bn:12.5-14.5%,cuo:7.0-10.0%,cdo:1.0-1.5%,sio2:≤6.0%,c:1.0-3.0%,余量为ni。
23.优选的,所述镍-氮化硼涂层2与零件基体之间设置镍铝过渡层1。
24.优选的,所述用于航空发动机后机匣高温可磨耗封严涂层硬度范围为hb8~10,在700
±
10℃下加热保温,然后采用水冷热震,反复15次,涂层应无剥落,无分层。
25.采用氧乙炔火焰粉末喷涂镍-氮化硼涂层工艺参数参见表1。
26.涂层氧气流量乙炔流量送粉速率表面线速度喷涂距离镍-氮化硼24nlpm17nlpm32g/min413mm/s190mm
27.表1
28.氧乙炔火焰粉末喷涂镍-氮化硼涂层外观呈均匀的灰黑色,无过烧变色;涂层表面没有裂纹,涂层没有翘起、剥落等现象,涂层表面硬度测试值为hb9.2;涂层显微组织检测结果显示涂层与基体界面结合良好,无翘起、分层现象,涂层内部无裂纹等缺陷;在700
±
10℃下加热保温,然后采用水冷热震,反复15次,涂层无剥落,无分层。
29.实施例2
30.所述用于航空发动机后机匣高温可磨耗封严涂层具体为镍-氮化硼涂层2,镍-氮化硼涂层2由镍-氮化硼粉末经过氧乙炔火焰喷涂制成,所述镍-氮化硼粉末的成分及重量百分比如下:bn:12.5%,cuo:7.0%,cdo:1.0%,sio2:1.0%,c:1.0%,余量为ni。
31.优选的,所述镍-氮化硼涂层2与零件基体之间设置镍铝过渡层1。
32.优选的,所述用于航空发动机后机匣高温可磨耗封严涂层硬度范围为hb8,在700
±
10℃下加热保温,然后采用水冷热震,反复15次,涂层应无剥落,无分层。
33.实施例3
34.所述用于航空发动机后机匣高温可磨耗封严涂层具体为镍-氮化硼涂层2,镍-氮化硼涂层2由镍-氮化硼粉末经过氧乙炔火焰喷涂制成,所述镍-氮化硼粉末的成分及重量百分比如下:bn:14.5%,cuo:10.0%,cdo:1.5%,sio2:6.0%,c:3.0%,余量为ni。
35.优选的,所述镍-氮化硼涂层2与零件基体之间设置镍铝过渡层1。
36.优选的,所述用于航空发动机后机匣高温可磨耗封严涂层硬度范围为hb8~10,在700
±
10℃下加热保温,然后采用水冷热震,反复15次,涂层应无剥落,无分层。
37.实施例4
38.所述用于航空发动机后机匣高温可磨耗封严涂层具体为镍-氮化硼涂层2,镍-氮化硼涂层2由镍-氮化硼粉末经过氧乙炔火焰喷涂制成,所述镍-氮化硼粉末的成分及重量百分比如下:bn:12.5-13.5%,cuo:8.0-9.0%,cdo:1.2-1.3%,sio2:3-4%,c:1.5-2.5%,余量为ni。
39.优选的,所述镍-氮化硼涂层2与零件基体之间设置镍铝过渡层1。
40.优选的,所述用于航空发动机后机匣高温可磨耗封严涂层硬度范围为hb8~10,在700
±
10℃下加热保温,然后采用水冷热震,反复15次,涂层应无剥落,无分层。
再多了解一些
本文用于创业者技术爱好者查询,仅供学习研究,如用于商业用途,请联系技术所有人。