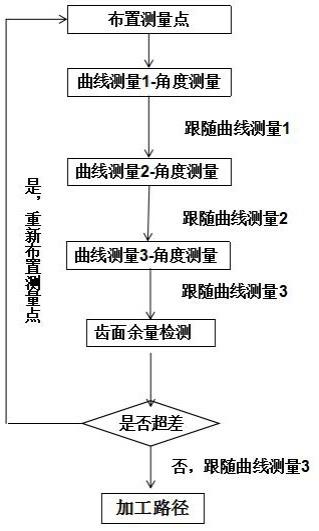
1.本发明属于齿轮模具生产领域,具体涉及一种基于在机测量的齿轮模具精加工基准找正方法。
背景技术:
2.齿轮模具加工市场是公司产品在模具行业应用的有力支撑。而齿轮精加工过程中存在的一系列问题必须借助在机测量技术解决。在机测量技术可实现产品加工过程中的自动化实时检测。基于测量工件基准角度的偏转量,可实现加工路径的智能修正,保证加工定位的准确性,从而提高产品的加工精度。
3.现有的齿轮模具摆正方法需要通过定位基准,人工手动拉表来实现,精度低、效率低下,且找正精度依赖于加工人员的经验。且人工拉表无法实现角度的迭代摆正、无法通过量化的检测数据来判断摆正效果。
技术实现要素:
4.本发明的目的在于针对上述现有技术中的问题,提供基于在机测量的齿轮模具精加工基准找正方法,能够减少用户操作,降低出错率,操作方便,进而提高工作效率。
5.为了实现上述目的,本发明采用的技术方案包括以下步骤:1)布置用于角度摆正的测量点;2)生成角度摆正测量路径;2.1)创建“角度测量1”路径,开启“角度测量”;2.2)创建“角度测量2”路径,开启“跟随测量角度找正”、“使用数据组号1”与“角度测量”;2.3)创建“角度测量3”路径,开启“跟随测量角度找正”、“使用数据组号2”与“角度测量”;3)在第2)步角度摆正基础上,开启“跟随测量角度找正”、“使用数据组号3”进行模具产品面余量检测,进而进行摆正精度判断;4)如果第3)步的摆正精度合格,则加工路径开启“跟随测量角度找正
””
、“使用数据组号3”进行加工;如果第3)步的摆正精度不合格,则需要重新布置用于角度摆正的测量点,然后进行2)-3)步,直到摆正精度合格。
6.进一步的,所述步骤1)在齿轮模具的cad模型上布置两个高度一致的测量点,用于进行角度摆正。
7.进一步的,所述步骤2.1)中创建“角度测量1”后,使用上一步布置的测量点。
8.进一步的,所述步骤2.2)中创建“角度测量2”,测量点理论位置与“角度测量1”相同。
9.进一步的,所述步骤2.3)创建“角度测量3”,测量点理论位置与“角度测量2”相同。
10.与现有技术相比,本发明具有以下技术效果:
本发明通过在机测量技术实现了齿轮模具精加工基准找正方法,通过三次角度迭代找正,实现了找正精度的大幅提高。且与人工手动拉表找正相比,找正时间大幅缩短。
11.本发明通过在机测量检测齿面余量来判断摆正精度,检测效率更高,且减少了人工参与,对现场工艺人员的技术和经验要求进一步降低。
12.本发明通过在机测量代替人工找正,使得半精加工与精加工直接无需人工干预,大大缩短生产准备时间,适合大批量产品的连续、自动化加工。
附图说明
13.图1 本发明基于在机测量的齿轮模具精加工基准找正方法的原理图;图1a)本发明找正方法原理图的初始坐标系下理论直线与实际直线的夹角计算;图1b)本发明找正方法原理图的 下理论直线与实际直线的夹角计算;图1c)本发明找正方法原理图的 下理论直线与实际直线的夹角计算;图2 本发明基于在机测量的齿轮模具精加工基准找正方法的流程图;图3 本发明摆正测量点生成示意图;图4 本发明角度测量1的操作界面示意图;图4a) 本发明角度测量1的选择角度测量补偿操作界面示意图;图4b) 本发明角度测量1的设置角度测量补偿具体参数操作界面示意图;图5 本发明角度测量2的操作界面示意图;图5a) 本发明角度测量2的选择角度测量补偿操作界面示意图;图5b) 本发明角度测量2的设置角度测量补偿具体参数操作界面示意图;图6 本发明角度测量3的操作界面示意图;图6a) 本发明角度测量3的选择角度测量补偿操作界面示意图;图6b) 本发明角度测量3的设置角度测量补偿具体参数操作界面示意图;图7 本发明齿轮模具余量检测测量点分布示意图;图8 本发明余量检测跟随角度找正示意图。
具体实施方式
14.下面结合附图对本发明做进一步的详细说明。
15.参见图1及图2,本发明一种基于在机测量的齿轮模具精加工基准找正方法原理及流程如下:1)通过计算理论直线方向与初始工件坐标系下的实际直线方向的夹角,得到初始的角度偏转量。
16.其中:,2)使用数控指令g68(平面内旋转),将初始工件坐标系在xoy平面内,绕原点旋转角度,得到,在工件坐标系下测量得到实际直线的方向,计算理论
直线与实际直线的夹角。
17.其中: 3)继续使用数控指令g68(平面内旋转),将初始工件坐标系在xoy平面内,绕原点旋转角度,得到,在工件坐标系下测量得到实际直线的方向,计算理论直线与实际直线的夹角。
18.其中:继续使用数控指令g68(平面内旋转),将初始工件坐标系在xoy平面内,绕原点旋转角度,得到,在下进行余量检测。如果余量不超差,证明工件已经摆正。直接使用进行精加工。如果的余量检测(摆正精度)不合格,则需要重新布置用于角度摆正的测量点,然后重新进行摆正。
19.本发明一种基于在机测量的齿轮模具精加工基准找正方法包括以下步骤:1)参见图3,在齿轮模具的cad模型上布置角度摆正的测量点,测量点需要在同一高度(z坐标相同)。
20.2)参见图4a)和图4b),创建“角度测量1”,测量点为第1步中布置的测量点,并开启角度测量。测量完成后,计算理论直线(两个测量点理论位置连线)与实际直线(两个测量点实际位置连线)的夹角,记为夹角1。将该夹角记录在“数据组号1”中。
21.3)参见图5a)和图5b),创建“角度测量2”,测量点理论位置与“角度测量1”相同,开启“跟随测量角度找正”、“使用数据组号1”,并开启角度测量。在实际测量中,“角度测量2”的测量路径会首先在xy平面内旋转“夹角1”(通过数控指令完成),再进行实际检测。测量完成后,计算理论直线(两个测量点理论位置连线)与实际直线(两个测量点实际位置连线)的夹角,记为夹角2。将该夹角记录在“数据组号2”中。
22.4)参见图6a)和图6b),创建“角度测量3”,测量点理论位置与“角度测量2”相同,开启“跟随测量角度找正”、“使用数据组号2”,并开启角度测量。在实际测量中,“角度测量3”的测量路径会在xy平面内旋转“夹角1 夹角2”,再进行实际检测。测量完成后,计算理论直线(两个测量点理论位置连线)与实际直线(两个测量点实际位置连线)的夹角,记为夹角3。将该夹角记录在“数据组号3”中。
23.5)参见图7和图8,在角度偏转跟随“角度测量3”的基础上,进行余量检测,进而进行摆正精度判断。在实际余量检测中,余量检测的路径会在xy平面内旋转“夹角1 夹角2 夹角3”,再进行实际检测。测量完成后,通过在nc程序中自动判断测量点的余量分布是否超差,来确认是否摆正精度是否合格。如果摆正精度不合格,则需要重新布置用于角度摆正的测量点,然后进行2)
‑ꢀ
5)步直到摆正精度合格。
24.6)在摆正精度合格的前提下,加工路径开启“跟随测量角度找正”使用“数据组号3”,来完成齿轮模具的精加工。
再多了解一些
本文用于创业者技术爱好者查询,仅供学习研究,如用于商业用途,请联系技术所有人。