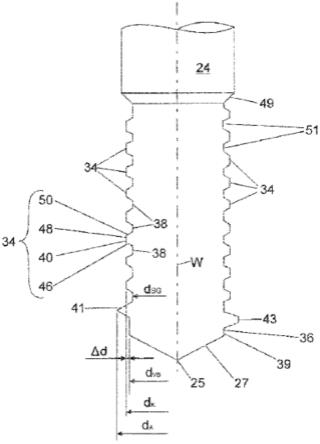
1.本发明涉及一种根据权利要求1的前序部分所述的攻丝刀具和根据权利要求15所述的用于产生工件螺纹孔的方法。
背景技术:
2.在所谓的一次性攻丝过程中,利用攻丝刀具以共同的刀具行程(即攻丝行程)既执行了底孔钻削(也就是说钻底孔)又执行了内螺纹产生。为此,攻丝刀具有至少一个底孔切削刃和带有至少一个加工齿的螺纹产生部段。在该方法中,首先进行攻丝行程,在该攻丝行程中,攻丝刀具能进入到未预先钻底孔的工件中,直至达到额定螺纹深度。当达到额定螺纹深度后,接下来是退刀行程,在该退刀行程中,攻丝刀具的转速被制动,并进行转动方向反向。在转动方向反向后执行逆向行程,在该逆向行程中,能以相反的转动方向将攻丝刀具从工件螺纹孔引导出来。在此时,螺纹产生部段的加工齿在内螺纹的螺纹槽中无负荷地运动。
3.这种类型的攻丝刀具在其钻尖处具有用于产生底孔的端侧的底孔切削刃。相对钻尖轴向错开地设置有螺纹产生部段,在攻丝行程中,利用螺纹产生部段在底孔壁上产生内螺纹粗型廓,其中,径向内部的螺纹牙顶所位于的直径比要产生的螺纹内直径小直径余量。此外,攻丝刀具具有沉孔切削刃,借助沉孔切削刃能在工件螺纹孔的开口边缘处产生螺纹沉孔。
4.在现有技术中,在攻丝行程中产生的底孔已经具有了螺纹内直径。在这种情况下,端侧的底孔切削刃延伸直至的径向外部的底孔切削角部位于底孔直径上。底孔切削刃的相应大的切削刃长度在攻丝行程中受到了相应大的切削刃负荷。
5.这种攻丝刀具示例性地由ep 3 458 219 b1和ep 3 484 647 b1已知。
技术实现要素:
6.本发明的目的在于,提供一种攻丝刀具以及一种用于产生工件螺纹孔的方法,其中,在攻丝过程中减少刀具负荷。
7.该目的通过权利要求1或15的特征来解决。在从属权利要求中公开了本发明的优选的改进方案。
8.根据权利要求1的特征部分,攻丝刀具沿刀具轴向方向在螺纹产生部段与沉孔切削刃之间具有多个内直径切削刃,这些内直径切削刃在攻丝行程中可以与端侧的底孔切削刃的底孔直径无关地产生螺纹内直径。内直径切削刃在攻丝行程中在内螺纹粗型廓的螺纹槽之内引导。在攻丝行程之后紧接着沿相同的行程方向进行退刀行程,在该退刀行程中,内直径切削刃通过切削加工将径向内部的螺纹牙顶处的直径余量去除,直至螺纹内直径。
9.在一技术实现方案中,每个内直径切削刃可以构造在攻丝刀具的孔钻型肋的脊面上。在此,内直径切削刃从切削刃底部径向向外伸出切削刃高度。
10.内直径切削刃的切削刃几何形状对于在工件的螺纹孔中过程可靠地产生内螺纹方面是有利的:因此,每个内直径切削刃都可以具有沿刀具轴线延伸的径向外部的纵向切
削边棱。这些纵向切削边棱可以位于螺纹内直径上。纵向切削边棱可以在朝向钻尖的切削角处与一切削刃侧边汇合。以相同方式,纵向切削边棱可以在朝向刀柄的切削角处与一切削刃侧边汇合。内直径切削刃的两个切削刃侧边可以以倾斜延伸的方式过渡到切削刃底部,该切削刃底部位于切削刃底部直径上。
11.在退刀行程中,相应的内直径切削刃的朝向钻尖的切削刃侧边、朝向钻尖的切削角和纵向切削边棱处于作用状态,以便去除直径余量。
12.为了产生底孔,攻丝刀具的端侧的底孔切削刃可以在径向外部的底孔切削角处与沿刀具轴线延伸的副切削刃汇合。径向外部的底孔切削角位于底孔直径上。根据本发明,该底孔直径小于螺纹内直径。底孔直径还可以小于或大于切削刃底部直径,或者备选地可以与切削刃底部直径相同。
13.内直径切削刃可以沿刀具轴线通过切削刃间隙相互隔开。切削刃间隙以如下方式定尺寸:使得在攻丝行程中,每个内直径切削刃都伸入到内螺纹粗型廓的螺纹槽中。内直径切削刃的数量至少可以与螺纹槽的数量相应。
14.上述刀具几何形状在攻丝行程中具有以下优点:在攻丝行程中产生的切屑因此以与攻丝行程相反的排屑方向被输送出螺纹孔。借助在攻丝行程中伸入到螺纹槽中的内直径切削刃过程可靠地防止切屑进入先前产生的螺纹粗型廓中并对先前产生的螺纹粗型廓造成损害。
15.由于底孔直径小于内直径,使得在攻丝行程中进给力以及转矩可以设计地比现有技术低。
16.在第一实施变型方案中,内直径切削刃沿刀具轴线可以位于相同的内直径上。对此备选地,内直径切削刃的内直径可以沿刀具轴线变化。
17.在第一实施变型方案中,在攻丝行程中,内直径切削刃可以被引导到内螺纹粗型廓的螺纹槽中而没有切削接合。在这种情况下优选的是,在攻丝行程中,内直径切削刃的切削刃侧边能支撑在先前产生的内螺纹粗型廓的螺纹牙侧面上。以该方式,在攻丝行程中提供对攻丝刀具的侧向引导。
18.在一个实施变型方案中,内直径切削刃的切削刃底部直径可以小于或等于底孔切削角的底孔直径。
19.在第二实施变型方案中,内直径切削刃在攻丝行程中可以不再没有切削作用地而是相反具有切削作用地引导到内螺纹粗型廓的螺纹槽中。在这种情况下,可以在攻丝行程中进行第一次材料去除,其中,内直径切削刃(尤其是其切削刃底部)去除直径余量的一部分。在随后的退刀行程中可以进行第二次材料去除,其中,内直径切削刃(尤其是其纵向切削边棱)去除了直径余量的剩余部分。
20.在另外的实施变型方案中,螺纹产生部段可以构造有至少一个逆向齿。在攻丝行程期间,逆向齿与工件不切削接合。只有在逆向行程中,逆向齿才可以从例如面对切屑的螺纹牙侧面去除或通过成型去掉可能额外留存的侧边余量,由此能完成工件内螺纹的加工。
21.下文是对用于产生螺纹孔的优选过程顺序的描述:钻削和攻丝在一个工序中(即在攻丝行程中)。在攻丝行程期间,内直径切削刃在螺纹型廓中保护性地运动,并防止切屑进入并损坏先前产生的螺纹型廓。与现有技术不同的是,底孔切削刃并不产生内直径,而是产生较小的底孔直径。由于底孔直径小于内直径,使得进给力和转矩可以比现有技术中更
低。在达到额定螺纹深度时进行退刀行程,其中,进给和转速的同步化被切断。在刀具进给被制动时,与现有技术类似地产生退刀槽;附加地,内直径切削刃切割出内直径。内直径切削刃可以如下这样地布置,使得内直径可以沿着螺纹是变化的。在退刀行程中,刀具转动方向发生逆向。此外,接通相反的刀具进给,进行同步化,并且使刀具通过先前产生的螺纹型廓从孔不受力地引导出来。刀具可以如下这样地设计,即,使得在攻丝行程中产生的螺纹型廓不是精加工的。如有必要,在刀具在退刀槽中沿刀具轴线已经错开了加工余量后,可以在刀具从孔引导出来时进行精加工。
附图说明
22.下面参照附图对本发明的实施例进行描述。其中:
23.图1示出构造在工件中的螺纹盲孔的侧剖图;
24.图2和图3示出攻丝刀具的不同视图;
25.图4以极为简化的等效图示出攻丝刀具,该攻丝刀具在图平面中只示出了与本发明有关的几何形状特征;
26.图5至图8示出产生图1中所示的螺纹盲孔的视图;以及
27.图9至12示出本发明的另外的实施例。
具体实施方式
28.图1示出了完成的工件螺纹孔1。借助所谓的一次性钻削加工,将具有直至目标孔深tb的孔底3的孔1加工到工件5中,该一次性钻削加工稍后将结合图4至图8进行解释。螺纹孔1在其孔口处具有环绕的螺纹沉孔7,在进一步的延伸中,螺纹孔向下过渡到内螺纹9。内螺纹9沿孔轴线b延伸直至可用的额定螺纹深度tg。从图1可以进一步得知,具有螺纹收尾部11的内螺纹9的螺纹槽15通到环绕的退刀槽13中,该退刀槽没有螺距,并且沿轴向方向观察构造在内螺纹9与孔底3之间。螺纹槽15具有径向外部的螺纹牙底17以及在径向上向内过渡到螺纹芯部/螺纹型芯(gewindekern)20的侧向的上和下螺纹牙侧面18、19。螺纹牙底17位于外直径da上,而螺纹芯部21位于螺纹内直径dk上。图1中的上螺纹牙侧面19是在攻丝加工时面对切屑的螺纹牙侧面,而图1中的下螺纹牙侧面18是背离切屑的螺纹牙侧面。
29.借助于下文结合图2、图3和图4描述的攻丝刀具23加工图1中所示的工件螺纹孔1。因此,图2中的刀具23在其钻尖25处具有三个周向均匀分布的端侧的以及横向延伸的底孔切削刃27和沿攻丝方向落后的螺纹产生部段29(图3)。
30.在图3中,刀具23包括刀柄24以及与之邻接的攻丝刀具基体26,沿刀具轴线w总共三个周侧分布的排屑槽28延伸至钻尖25处的相应端侧的底孔切削刃27。在每个底孔切削刃27处,钻尖25的限定排屑槽28的前刀面31和端侧的后刀面33(图2)汇合。沿刀具的圆周方向,相应的排屑槽28通过孔钻型肋35限界。图2和图3中所示的攻丝刀具23总共具有三个孔钻型肋35。排屑槽28的前刀面31在形成副切削刃36的情况下过渡到相应的孔钻型肋35的外周侧的脊面37。在图3中,副切削刃36和端侧的底孔切削刃27在径向外部的底孔切削角39处汇合。
31.在三个孔钻型肋35的每个外周侧的脊面37上,螺纹产生部段29分别具有加工齿41、42、43。加工齿41、42、43以不同的几何形状实施以及与钻尖25的轴向距离不同地间隔
开,以便产生图1中所示的内螺纹9的螺纹槽15。
32.攻丝刀具23在攻丝刀具基体26与刀柄24之间的过渡处具有沉孔切削刃49,以用于形成图1中所示的螺纹沉孔7。
33.从图3中进一步得知,在孔钻型肋35的外周侧的脊面37上分别构造有内直径切削刃34,这些内直径切削刃分别从切削刃底部38径向向外伸出切削刃高度。
34.在图4中,每个内直径切削刃34都具有沿刀具轴线w延伸的径向外部的纵向切削边棱40,纵向切削边棱位于螺纹内直径dk上。纵向切削边棱40在朝向钻尖25的切削角44处过渡到第一切削刃侧边46。以同样方式,切削刃40在朝向刀柄24的切削角48处过渡到第二切削刃侧边50。两个切削刃侧边46、50与切削刃底部38汇合,切削刃底部位于切削刃底部直径d
sg
上。
35.端侧的底孔切削刃27在径向外部的底孔切削角39处过渡到副切削刃36。径向外部的底孔切削角39位于底孔直径d
vb
上。
36.从图3或图4中可以进一步看出,内直径切削刃34沿刀具轴线w被切削刃间隙51彼此隔开。切削刃间隙51以如下方式定尺寸,即,在下文描述的攻丝行程g中(图5或图6),使得每个内直径切削刃34都伸入到内螺纹粗型廓8的螺纹槽15中。内直径切削刃34的数量在此至少相应于要产生的螺纹槽15的数量。
37.在下文中,将结合图5至图8描述用于产生图1中所示的工件螺纹孔1的方法。因此,攻丝刀具23沿攻丝方向被引导到尚未进行底孔钻削的工件5上,并以攻丝行程g(图5或图6)进入到工件5中。在攻丝行程g中,底孔切削刃27产生底孔直径为d
vb
的底孔30(图5或图6)。后续的螺纹产生部段29在底孔30的内壁部上产生内螺纹粗型廓8(图6或图7)。攻丝行程g在攻丝进给情况下并在与之同步的攻丝转速情况下沿攻丝转动方向执行,更确切地说执行直至达到额定螺纹深度tg。在上述螺纹成形行程g期间,内直径切削刃34被引导到内螺纹粗型廓8的螺纹槽15中而不发生切削接合。如图5和图6中所示,内直径切削刃34的切削刃侧边46、50支撑在内螺纹粗型廓8的螺纹槽的螺纹牙侧面18、19上。
38.在图4至图8的实施例中,内直径切削刃34的切削刃底部直径d
sg
小于底孔切削角39的底孔直径d
vb
。
39.在图6中示出在攻丝行程g结束时的攻丝刀具23。紧接着,执行退刀行程(图6和图7)。与攻丝行程g区别是,在退刀行程中,进给和转速的同步性被切断。在退刀行程f中,攻丝刀具23的转速被制动,并且进行转动方向反向。同时,沉孔切削刃49产生环绕的螺纹沉孔7。此外,在退刀行程f中,内直径切削刃34通过切削加工去除掉径向内部的螺纹牙顶21(图5和图6)处的直径余量δd,直至螺纹内直径dk。在退刀行程f中进行的直径余量δd的材料去除通过相应的内直径切削刃34的朝向钻尖25的切削刃侧边46、通过朝向钻尖25的切削角44以及通过纵向切削边棱40来进行。
40.在内螺纹粗型廓8中,径向内部的螺纹牙顶21(图5和图6)位于直径ds上,该直径相应于底孔直径d
vb
,该直径比螺纹内直径dk小直径余量δd。
41.在退刀行程f(图5和图6)中,为了准备逆向行程r(图8)执行转动方向反向。在逆向行程r中,攻丝刀具23沿逆向方向从螺纹孔1被引导出来,更确切地说以相反的逆向进给以及与之同步的逆向转速执行。这些参数被如下这样地定尺寸,即,使得攻丝刀具23的螺纹产生部段29基本上无负荷地在内螺纹9的螺纹槽15中从螺纹孔引出。
42.在逆向行程r(图8)中,加工齿41、42、43、底孔切削刃27、副切削刃36和内直径切削刃34无负荷地从螺纹孔1引导出来。
43.在下文中,将结合图9描述根据另外的实施例的攻丝刀具23的结构和作用方式。图9中所示的攻丝刀具23与前图中的攻丝刀具相应。因此,参考前面的描述。图9和图10中所示的攻丝刀具23具有附加的逆向齿69。利用逆向齿69在逆向行程r中从面对切屑的螺纹牙侧面19去除侧边余量δz。为了准备逆向行程r,攻丝刀具23(在完成退刀行程f后)以加工余量的方式进行驱控,使得逆向齿69面对切屑的螺纹牙侧面19去除或造型掉侧边余量δz直至成品尺寸。逆向齿69构造在孔钻型肋脊面37上。
44.在图11、图12和图13中示出了备选的实施方式,其中,攻丝刀具23与前图中所示的基本相应。因此,参考前面的描述。与图4至图8的实施例区别如下:图11、图12和图13中的切削刃底部直径d
sg
不小于底孔切削刃39的底孔直径d
vb
而是大于底孔直径。由此,内直径切削刃34的切削刃底部38在攻丝行程g(图11)中与内螺纹粗型廓8切削接合。在图11说明示的攻丝行程g中实现了第一次的材料去除m1,其中,内直径切削刃34的切削刃底部38去除了部分直径余量δd。在接下来的退刀行程f中实现了第二次材料去除m2,其中,内直径切削刃34的纵向切削边棱40去除了直径余量δd的剩余部分。
45.附图标记列表
46.1螺纹孔
47.3孔底
48.5工件
49.7螺纹沉孔
50.8内螺纹粗型廓
51.9内螺纹
52.11螺纹收尾部
53.13退刀槽
54.15螺纹槽
55.17径向外部的螺纹牙底
56.18、19螺纹牙侧面
57.20螺纹芯部
58.21螺纹牙顶
59.23攻丝刀具
60.24刀柄
61.25钻尖
62.27底孔切削刃
63.29螺纹产生部段
64.26攻丝刀具基体
65.28排屑槽
66.30底孔
67.31前刀面
68.33端侧的后刀面
69.34内直径切削刃
70.35孔钻型肋
71.36副切削刃
72.37外周侧的脊面
73.38切削刃底部
74.39径向外部的底孔切削角
75.40纵向切削边棱
76.41、42、43加工齿
77.44切削角
78.46第一切削刃侧边
79.48切削角
80.49沉孔切削刃
81.50第二切削刃侧边
82.51切削刃间隙
83.69逆向齿
84.d
sg
切削刃底部直径
85.d
vb
底孔直径
86.da螺纹外直径
87.di螺纹内直径
88.dk螺纹内直径
89.ds螺纹牙顶直径
90.δd直径余量
91.δz侧边余量
92.g攻丝行程
93.f退刀行程
94.r逆向行程
95.b孔轴线
96.w刀具轴线
97.m1第一次材料去除
98.m2第二次材料去除
再多了解一些
本文用于创业者技术爱好者查询,仅供学习研究,如用于商业用途,请联系技术所有人。