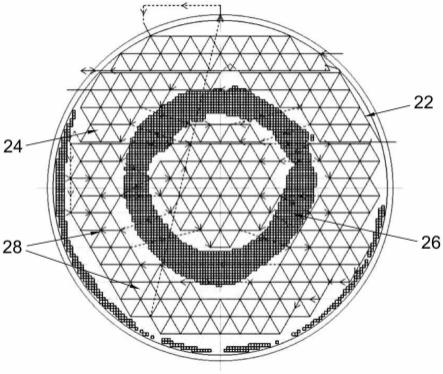
1.本发明涉及一种由超硬盘加工制品的方法,特别是涉及一种能以最小损耗高效加工的机器设备的套料方法。
背景技术:
2.用于机加工的刀具刀片和其他刀具通常包括粘结到硬质合金基底的多晶金刚石(pcd)层。pcd是“超硬”材料的一个例子,也称为超级磨料,其硬度值远大于烧结碳化钨硬质合金。超硬材料的维氏硬度大于40gpa。
3.包括pcd的部件被用于切削、加工、钻孔或降解硬质或耐磨材料(如岩石、金属、陶瓷、复合材料和含木材的材料)的各种刀具中。pcd通常包括大量基本互生的立方金刚石颗粒,它们形成骨架块,限定了立方金刚石颗粒之间的间隙。pcd材料包含至少约80体积百分比的金刚石,可通过在烧结助剂(也称为金刚石催化剂材料)的存在下,使聚集的金刚石颗粒经受大于约5gpa(通常约5.5gpa)的超高压和至少约1200℃(通常约1440℃)的温度来制备。该烧结过程在放置在高温高压(hpht)的压机内的高温高压容器内进行。
4.金刚石催化剂材料被理解为能够在一定的压力和温度条件下促进金刚石颗粒的直接相互生长的材料,在该压力和温度条件下,金刚石在热力学上比石墨更稳定。金刚石催化剂材料的例子是钴、铁、镍和某些合金,包括任何这些元素的合金。
5.pcd可以是独立的或有支撑的。pcd可形成在钴烧结碳化钨基底上,其可为pcd提供钴催化剂材料源。在pcd材料主体的烧结过程中,硬质合金基底的成分,例如来自钴硬质合金碳化钨基底的钴,液化并从邻近金刚石颗粒体的区域延伸进入金刚石颗粒之间的间隙区域。在这个例子中,钴充当催化剂以促进粘结金刚石颗粒的形成。可选地,在使金刚石颗粒和基底经受高温高压烧结条件之前,金属溶剂催化剂可与金刚石颗粒混合。pcd材料内的空隙可至少部分地填充有该催化剂材料。因此,互生金刚石结构包括原始金刚石颗粒以及新沉淀或重新生长的金刚石相,其桥接原始颗粒。在最终的烧结结构中,催化剂/溶剂材料通常保留在存在于烧结金刚石颗粒之间的至少一些间隙内。
6.在烧结时,根据期望的最终pcd烧结体的性质设置最佳烧结温度。此时,如果烧结温度太低或太高,pcd烧结体的性能(例如抗冲击性和耐磨损性)将超出期望性能的范围,导致产品缺陷。
7.通常,pcd烧结体是圆柱形的,随后从烧结体上切削下具有圆形横截面(标准直径)的盘。pcd通常以背面抛光盘的形式提供给刀具制造商。刀具制造商根据设计,使用以pcd内的金属辅助进行的放电加工(edm)去除制品(例如刀具坯料)。可替换地,可将制品本身提供给刀具制造商,然后由他们应用最终的几何形状和抛光。
8.当多个制品(可能具有不同的尺寸和形状)要从一个盘上下料时,这些制品被套料(组合排样,nest)以实现最大分配。基于计算机执行的预定套料程序,在盘上分配制品通常是自动的。
9.将制品分配到盘上有缺陷的部分会导致质量差的刀具毛坯。
10.本发明的一个目的是最大化用于套料分配的盘的可用面积,同时考虑盘表面上或主体内可能存在的任何缺陷。
技术实现要素:
11.根据本发明的第一方面,提供了一种从包括超硬材料的盘加工制品的方法,该方法包括:
[0012]-提供一个待加工的盘,该盘的直径不超过100mm,厚度不超过10mm;
[0013]-提供套料模式,该套料模式包括一个或多个待由盘加工的制品;
[0014]-扫描盘以识别无缺陷和/或缺陷部分,所述缺陷部分包含以下任何一种或多种:微观结构瑕疵、划痕和成分污染物;
[0015]-将套料模式叠加到在扫描期间识别出的盘的缺陷和/或无缺陷部分上,以创建加工程序;
[0016]-根据加工程序从盘加工出一个或多个制品。
[0017]
本发明的第一方面的优选和/或可选特征在从属权利要求2至17中阐述。
[0018]
根据本发明的第二方面,提供了一种包括计算机可读代码的计算机程序,当在计算机设备上运行时,该计算机程序使计算机设备执行根据本发明第一方面的方法。
[0019]
根据本发明的第三方面,提供了一种包括计算机可读介质和根据本发明第二方面的计算机程序的计算机程序产品,其中所述计算机程序存储在所述计算机可读介质上。
附图说明
[0020]
现在将参照附图(仅作为示例)更具体地描述本发明,其中
[0021]
图1是现有技术刀具模块的透视图;
[0022]
图2是现有技术切削刀具的透视图;
[0023]
图3是表示根据本发明的由超硬盘加工制品的方法的流程图;
[0024]
图4是超硬盘的透视图;和
[0025]
图5是根据本发明的图像,显示了切削刀具去除之前,并置在盘上的所提出的套料切削刀具的组合,特别是指示了盘的缺陷部分。
具体实施方式
[0026]
参考图1,现有技术的刀具模块通常以10表示。刀具模块10可连接到例如铣床或车床上的刀具组件(未示出)。刀具模块10包括一个细长的刀夹12和一个可拆卸地安装在刀夹12一端的可去除切削刀具14。该特定的切削刀具14在平面图中是方形的。切削刀具14由可释放夹具16保持在适当位置。
[0027]
图2显示了另一种现有技术的切削刀具,其以18表示。切削刀具16在平面图中是三角形的,具有中心通孔20。
[0028]
通常从在平面图中为圆形的盘状烧结体上移除切削刀具10、18。为了最大限度地分配可由盘获得的刀具,通常使用套料软件。
[0029]
图3显示了根据本发明从超硬盘22加工制品的示例性方法。以下编号与图3的编号相对应:
[0030]
s1.选择所需的盘22。只有直径不超过100mm且厚度不超过10mm的盘才适合使用。该盘包括烧结pcd。pcd通常被认为是一种超硬材料,因为其维氏硬度超过80gpa。可替换地,该盘可以包括烧结的多晶立方氮化硼(pcbn)材料。pcbn通常被认为是超硬材料,因为其维氏硬度超过80gpa。
[0031]
在该实施例中,如图4所示,盘22包括烧结到碳化钨基底23上的pcd层21。盘22的直径为76.5mm,总高度为1.6mm。pcd层22的厚度为0.5mm。
[0032]
每个盘22被分配一个唯一的编号来识别它,并且该标识符在整个过程中伴随着盘22。每个盘22还具有用于盘定向的参考点。
[0033]
s2&s3.扫描盘22以表征盘22并确定其质量。有时,超硬盘22包括无缺陷部分24和缺陷部分26,如图5所示。缺陷部分26包括瑕疵或不可接受的瑕疵等级或数量,而无缺陷部分22不包括瑕疵,或在最坏情况下,包括可接受的瑕疵等级和数量。瑕疵可能是层中相对于等级公差规范的偏差、表面划痕或抛光缺陷。并非所有盘22都包括缺陷部分26,但在由盘移除刀具段或坯料28之前识别任何缺陷显然是有益的。由有缺陷的刀具段制成的加工刀具在使用中容易过早失效,损坏正在加工的工件,并增加损失。
[0034]
扫描可以包括视觉扫描和/或超声波扫描。
[0035]
视觉扫描包括对每个盘上大约12000个点的自动扫描。起初,通过放大目视检查确定表面缺陷。然后在盘表面上标记视觉缺陷部分,视觉缺陷相机拍摄表面的反差图像,并输出所有12000个点,其中以高值或低值表示盘的上色(painted)区域。
[0036]
超声波扫描测量盘的厚度,扫描大约96000个点,测量每个点的深度。超声波扫描也是自动的。
[0037]
记录每个盘的扫描数据,以便于跟踪。每个点包含x和y位置,以及超声波扫描的z层深度。
[0038]
步骤2和3可以按任一顺序进行。扫描可以可选地仅由s2或仅由s3组成。优选地,扫描步骤包括视觉扫描和超声波扫描两者。
[0039]
s4.然后将来自视觉扫描、超声扫描或两者的扫描数据汇编成单个扫描结果文件。这是表示扫描数据的数字文件,例如,该文件可以是autocad dxf文件。扫描结果文件对于每个盘都是唯一的,不可被转移到任何其他盘或指示任何其他盘。扫描结果文件包含识别缺陷和定位这些缺陷的手段。可选地或附加地,扫描结果文件包含用于识别和可选地定位盘的无缺陷部分的手段。
[0040]
优选地,通过宏自动分析扫描数据文件,并且以dxf格式仅绘制出指示超出容许量的层的位置和以高对比度上色的区域。
[0041]
s5.选择套料文件。根据各个刀具段的大小和形状,每组刀具段的每个预配置套料文件都不同。套料文件指示了一个或多个推荐的刀具段的轮廓,这些刀具段布置在盘上,以最大程度地利用盘,而与盘材料的质量无关。在图5中,推荐的刀具段28为三角形。
[0042]
s6.结合扫描结果和套料模式以帮助创建加工文件。如图5所示,套料刀具段28的推荐布局并置在扫描结果上。如果在任何进一步的干预下使用盘,将产生源自盘20的缺陷部分26的刀具段28。
[0043]
s7.因此,此时可调整加工文件。该步骤优选地通过软件自动进行,其中需要一些手动操作。从加工程序中去除由缺陷部分加工的刀具段28。只有落在盘的无缺陷部分24内
的刀具段28被保留。可替换地,可以调整加工文件以过滤掉盘22的无缺陷24部分。
[0044]
s8.根据修改的加工程序,使用线切削或激光切削从盘中加工出刀具段18。
[0045]
根据工艺,随后需要清洁刀具段18。
[0046]
随后,在装运给客户之前,目视检查每个刀具段18以确定是否符合批准的图纸。
[0047]
在大多数情况下,客户会将刀具段18钎焊到特定的加工刀具上。可替换地,刀具段18可以如先前关于图1所述被夹紧在适当位置。
[0048]
加工程序的盘定向和加工前实际盘的盘定向必须相同。
[0049]
总之,发明人发现,新工艺在切削和加工方面更有效,重要的是,它节省了人工。用户可以更好地控制材料。值得注意的是,该工艺支持iso认证,对于最终用户来说是一个卖点。
[0050]
虽然已经参考实施例具体示出和描述了本发明,但是本领域技术人员将理解,在不脱离所附权利要求书所限定的本发明的范围的情况下,可以进行形式和细节上的各种改变。
再多了解一些
本文用于创业者技术爱好者查询,仅供学习研究,如用于商业用途,请联系技术所有人。