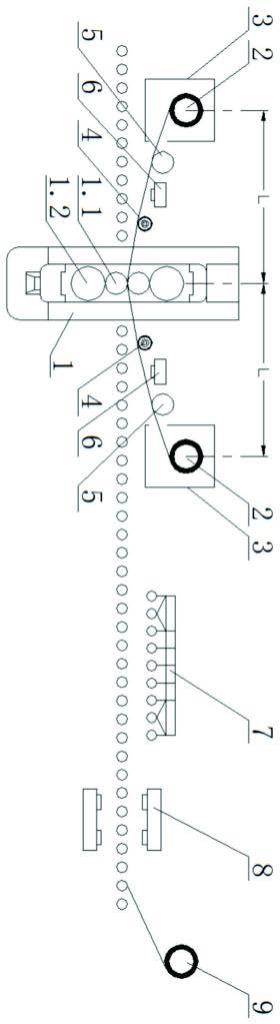
1.本发明涉及有色金属精密带箔材生产技术领域,具体涉及精密铜板带轧制生产线、生产工艺及张力控制方法。
背景技术:
2.铜带箔是铜及其合金加工应用的主要产品类型,占到变形加工铜产量的20%以上,广泛应用于航空航天、国防军工、军事装备、现代通讯、电子信息等领域;随着技术的不断发展,航空航天、国防军工、军事装备、现代通讯、电子信息等领域对铜带箔的质量要求越来越高,其中包括对铜带箔的尺寸精度、残余应力、表面光洁度、各向异性、伸长率、强度、介电常数、抗腐蚀性、抗高温、抗蠕变性能越来越严格,此类高等级的铜带材也被国内外业界称为“精密带箔材”。
[0003]“精密带箔材”最终质量的保证,并非在其最终精轧、表面处理及热处理生产中决定,而是由贯穿在“精密带箔材”生产的铜胚热轧、铜带粗轧、中轧、铜箔精轧及表面处理、热处理生产的全过程决定,即铜胚热轧、铜带粗轧对最终“精密带箔材”的质量也有重大影响,特别是粗轧生产后铜带的尺寸精度、残余应力、显微结构组织对后续“精密带箔材”轧制生产的质量影响最大;而目前国内由于受到生产设备、工艺设计的限制(铜带粗轧多采用冷粗轧工艺),以及粗轧生产后铜带的尺寸精度、残余应力、显微结构组织对后续“精密带箔材”生产最终质量影响的认识存在不足,导致国内能够生产高尺寸精度、低残余应力、具有良好显微结构组织的“精密铜板带”的企业少之又少,结果前端铜板带质量与最终“精密带箔材”生产的匹配性产生问题,成为国内有“精密带箔材”制造的技术盲点。
[0004]
目前,“精密带箔材”的进口量占到国内“精密带箔材”消费量的90%以上,因此如何保证前端“精密铜板带”质量与后端“精密带箔材”生产的匹配性,解决“精密带箔材”生产的技术盲点,促进国产替代进口,成为国内“精密带箔材”生产亟待解决的关键问题之一。
技术实现要素:
[0005]
为了克服背景技术中的不足,本发明公开了一种精密铜板带轧制生产线、生产工艺及张力控制方法;该精密铜板带轧制生产线的轧机采用四辊系结构,在轧机两侧对称设置了中间品卷取机,在中间品卷取机的卷轴外部设置了卷材加热炉,在卷取机与轧机之间设置了张力检测辊、冷却装置,在成品卷取机与其相邻的中间品卷取机之间设置了高温固溶系统,从而可在该生产线上一次完成从铜胚热轧到铜带热粗轧的生产;四辊系轧机配合张力检测辊,对铜带粗轧过程张力参数进行精确控制,极大提高了铜带粗轧后的尺寸精度;卷材加热炉对铜带加热保温,将原有的铜带粗轧工艺从冷粗轧改为热粗轧,同时配合高温固溶系统,极大改善了铜带粗轧后的残余应力和显微组织结构,从而获得了高尺寸精度、低残余应力、具有良好显微结构组织的“精密铜板带”,克服了前端“精密铜板带”质量与后端“精密带箔材”生产的匹配性问题,解决了国内目前“精密带箔材”生产的技术盲点,为国内实现“精密带箔材”生产打下了良好的基础。
[0006]
为了实现所述发明目的,本发明采用如下技术方案:一种精密铜板带轧制生产线,包括辊道和设置在辊道中段的轧机;轧机采用四辊辊系结构,及在原轧机工作辊外侧各增加了一个支撑辊,同时减小了原工作辊直径,使轧机不仅可以满足铜胚热轧的工艺要求,同时也满足了铜带粗轧的工艺要求;轧机两侧对称设置有中间品卷取机,中间品卷取机2的卷取铜带厚度为3~28mm,最大卷取外径为2500mm;中间品卷取机与轧机之间的距离设置在5-12m之间,中间品卷取机的卷轴外部设置有卷材加热炉,卷材加热炉的加热温度范围为600~1000℃,同时配置有氮气、氩气等保护性气体;铜胚轧制完成后,在中间品卷取机中成卷,同时在卷材加热炉中保温加热,继续进行铜带的热粗轧,该工艺的改进带来两大有益效果:1、利用铜胚热轧后的余温继续进行铜带的热轧,省去了铜胚热轧后原有的冷却工艺,可充分利用铜胚热轧后的余热,因此降低了能源消耗;2、铜带有冷粗轧改为热粗轧,降低了冷粗轧后铜带的残余应力;卷取机与轧机设置有张力检测辊、冷却装置、卷取机导辊;其中张力检测辊用于检测铜带热粗轧中的轧制张力,提高了热粗轧的张力控制精度,从而进一步提高了热粗轧的尺寸控制精度;其中冷却装置在热粗轧完成后进行快速冷却,改善了热粗轧后铜带的显微组织结构;其中卷取机导辊用于保证铜带在张力检测辊上的包角,改善张力检测辊的检测精度;辊道一端设置有成品卷取机,成品卷取机与其相邻的中间品卷取机之间设置有高温固溶系统,可对粗轧后的铜带进行在线高温固溶处理,进一步改善了铜带热粗轧后的显微组织结构;高温固溶系统与成品卷取机设置有对接拼焊装置,对接拼焊装置对热粗轧后铜带的在线连接,形成更大规格的热轧铜带卷;该精密铜板带轧制生产线即可以生产厚度12-20mm的热轧铜板,同时也可生产厚度为1-4mm的精密热轧铜带,在保证生产质量的同时,还减少了后续冷轧的加工量,缩短了生产流程;将铜板带的后续冷轧轧程更多分配在热轧工序阶段,不仅降低了铜板带生产的总能耗,同时还降低了后续铜带冷轧和中间退火的设备投资、缩短了精密铜带箔的总的加工工序流程。
[0007]
进一步的,轧机包括两对上、下对称设置的工作辊系,工作辊系包括一个工作辊和一个支撑辊,工作辊直径设置在200-400mm之间,支撑辊直径设置在400-900mm之间,支撑辊对称设置在两个工作辊轧制辊缝的外侧,用于支撑补强工作辊刚度;在金属轧制生产中,轧辊直径与最终所能生产的板带厚度有直接关系,即轧辊直径越大,最终所能轧制生产的铜板带的最小厚度也约大,因此传统铜胚轧制生产线受限于较大的轧辊直径,其只能用于铜胚的热轧,而无法完成厚度更薄的精密铜带的轧制加工,在本发明中,通过减小工作辊直径,实现了在传统铜板轧制生产线上对成品厚度更小的精密铜带的热轧;工作辊直径减小后,其刚性通过支撑辊予以补强。
[0008]
进一步的,张力检测辊为实心辊,绕轴线均布设置有两组压力传感器,两组压力传感器在轴线方向对称设置;实际工作中,取两组压力传感器输出值的平均值作为张力检测传感器的采集值,以提高数据采集的稳定性;张力检测辊的辊体为整体结构,压力传感器沿轴向置入张力检测辊的辊体中。
[0009]
进一步的,中间品卷取机卷轴的驱动传动链中设置有若干个磁流变液离合器,通过若干个磁流变液离合器合成驱动扭矩驱动卷轴旋转,通过控制合成驱动扭矩的大小控制卷轴输出的轧制张力;在本发明中,改变了传统的通过控制卷轴与工作辊的转速差,或卷轴驱动电机的驱动扭矩来控制轧制张力的控制结构,而是采用磁流变液离合器直接控制卷轴的扭矩来控制轧制张力,因此克服了传统张力控制结构的驱动系统传动链长、转动惯量大、
响应速度慢、精度低的问题;另外,在本发明中之所以采用多个磁流变液离合器合成驱动卷轴的扭矩,是因为现有磁流变液离合器所能提供的最大扭矩较小,而铜带热粗轧所需轧制张力较大,目前尚无法实现用一个磁流变液离合器为卷轴提供足够的扭矩。
[0010]
一种所述精密铜板带轧制生产线的精密铜带轧制生产工艺,包括精密铜板热轧、精密铜带热粗轧、高温固溶热处理;上述精密铜板的热轧、精密铜带的热粗轧、高温固溶热处理均在精密铜板带轧制生产线上完成;上述精密铜带轧制生产工艺实际实施时,可以组合在一起实施,最终在精密铜板带轧制生产线上生产出1.4mm的精密铜带材;也可单独实施,例如仅在精密铜板带轧制生产线实施精密铜板热轧,最终生产出12-20mm的铜板材,经冷却装置在线冷却后,直接在成品卷取机成卷。
[0011]
进一步的,精密铜板热轧将铜及铜合金铸锭往复可逆轧制至12-20mm,在中间品卷取机成卷;精密铜带热粗轧将12-20mm的铜板卷往复可逆轧制至1-4mm,轧制过程中通过卷材加热炉在线加热,保持轧制温度;高温固溶热处理前,铜带卷通过卷材加热炉在线加热,经高温固溶系统在线高温固溶热处理后,最终在成品卷取机成卷。
[0012]
一种基于精密铜板带轧制生产线的轧制张力控制方法,通过张力检测辊采集的张力信号反馈控制若干个磁流变液离合器中单独一个的工作扭矩,实现对卷轴所提供轧制张力的精确控制;在本发明中,若干个磁流变液离合器是通过扭矩合成减速机最终合成卷轴工作所需扭矩,同时磁流变液离合器的输出轴与扭矩合成减速机的扭矩输出轴(卷轴)之间设有3:1减速比,以提高卷轴最终的输出扭矩,因此对磁流变液离合器工作扭矩的调节控制量通过减速比实际会被放大,如果对多个磁流变液离合器同时进行调节控制,虽然其调节控制方法较为简单,但会导致控制精度的降低;通过对多个磁流变液离合器中的一个单独进行工作扭矩的调节控制,虽然其调节控制方法较为复杂,但可以显著提高卷轴最终输出轧制张力的控制精度。
[0013]
进一步的,通过控制若干个磁流变液离合器实际提供的工作扭矩,控制合成驱动扭矩;由合成驱动扭矩控制卷轴输出的轧制张力;其控制过程包括以下步骤:s1、磁流变液离合器工作速度设置:磁流变液离合器工作速度为其扭矩输入轴与扭矩输出轴的转速差,扭矩输入轴与扭矩输出轴的转速差设置维持在20-80rpm之间;s2、磁流变液离合器工作扭矩分配:其初始工作扭矩以卷轴实际工作所需扭矩平均分配给若干个磁流变液离合器,计算公式为:mci=mj/i*n
ꢀꢀꢀꢀ
......(1)mj=t*rj
ꢀꢀꢀꢀꢀꢀꢀ
......(2)其中:mci为单个磁流变液离合器分配的扭矩;mj为卷轴实际工作所需扭矩;i为磁流变液离合器输出轴与卷轴之间的传动比;n为磁流变液离合器数量;t为轧制张力;rj为卷轴上铜带卷的外径;s3、磁流变液离合器工作扭矩控制:若干个磁流变液离合器工作扭矩由张力检测辊采集的张力信号反馈形成pid控制;反馈控制过程中,仅对若干个磁流变液离合器中的一个进行工作扭矩调整控制,一个磁流变液离合器的扭矩累计调整值设定有一个阈值;当被反馈控制的磁流变液离合器的扭矩累计调整值达到或超出设定阈值时,反馈控制按设定的磁流变液离合器排序对另一个磁流变液离合器进行反馈控制;依次类推,在整个反馈控制过程中,实现对每个磁流变液离合器工作扭矩的反馈控制;
卷轴输出轧制张力控制流程具体参见说明书附图6。
[0014]
由于采用如上所述的技术方案,本发明具有如下有益效果:本发明公开的一种精密铜板带轧制生产线、生产工艺及张力控制方法;该精密铜板带轧制生产线的轧机采用四辊系结构,在轧机两侧对称设置了中间品卷取机,在中间品卷取机的卷轴外部设置了卷材加热炉,在卷取机与轧机之间设置了张力检测辊、冷却装置,在成品卷取机与其相邻的中间品卷取机之间设置了高温固溶系统,从而可在该生产线上一次完成从铜胚热轧到铜带热粗轧的生产;四辊系轧机配合张力检测辊,对铜带粗轧过程的轧制张力参数进行精确控制,极大提高了铜带粗轧后的尺寸精度;卷材加热炉对铜带加热保温,将原有的铜带粗轧工艺从冷粗轧改为热粗轧,同时配合高温固溶系统,极大改善了铜带粗轧后的残余应力和显微组织结构,从而获得了高尺寸精度、低残余应力、具有良好显微结构组织的“精密铜板带”,克服了前端“精密铜板带”质量与后端“精密带箔材”生产的匹配性问题,解决了国内目前“精密带箔材”生产的技术盲点,为国内实现“精密带箔材”生产打下了良好的基础。
附图说明
[0015]
图1为精密铜板带轧制生产线结构示意图;图2为中间品卷取机传动结构示意图;图3为张力检测辊压力传感器周向布置结构示意图;图4为张力检测辊压力传感器轴向布置结构示意图;图5为中间品卷取机卷轴驱动系统结构示意图;图6为卷轴张力控制流程示意图。
[0016]
图中:1、轧机;2、中间品卷取机;2.1、机架;2.2、中间品卷取机卷轴;2.3、扭矩合成减速机;2.3.1、扭矩输出轴;2.3.1.1、输出轴齿轮;2.3.1.2、输出轴联轴器;2.3.1.3、散热盘;2.3.2、扭矩输入轴;2.3.2.1、输入轴齿轮;2.3.2.2、输入轴联轴器;2.4、磁流变液离合器;2.5、变速箱;2.6、电机;3、卷材加热炉;4、张力检测辊;4.1、压力传感器轴向布置孔;4.2、压力传感器轴向布置区;5、卷取机导辊;6、冷却装置;7、高温固溶系统;8、对接拼焊装置;9、成品卷取机;10、初始扭矩分配流程;11、磁流变液离合器工作扭矩排序流程;12、反馈控制循环流程。
具体实施方式
[0017]
通过下面的实施例可以详细的解释本发明,公开本发明的目的旨在保护本发明范围内的一切技术改进。
[0018]
一种精密铜板带轧制生产线,包括辊道、轧机1、中间品卷取机2、卷材加热炉3、张力检测辊4、卷取机导辊5、冷却装置6、高温固溶系统7、对接拼焊装置8、成品卷取机9;轧机1包括两对上、下对称设置的工作辊系,工作辊系包括一个直径300mm的工作辊和一个直径800mm的支撑辊,支撑辊对称设置在两个工作辊轧制辊缝的外侧,工作辊与支撑辊外圆周面接触设置;轧机1设置在辊道中段;中间品卷取机2设置有两个,对称设置在轧机1两侧,距离轧机12m;卷材加热炉3设置在中间品卷取机2的卷轴2.2外部;张力检测辊4、冷却装置6、卷取机导辊5依次设置在卷取机2与轧机1之间;成品卷取机9设置在辊道一端,高温固溶系统7设置在成品卷取机9与其相邻的中间品卷取机2之间,靠近成品卷取机9;对接拼焊装置8设
置在高温固溶系统7与成品卷取机9之间;张力检测辊4为直径300mm的实心辊,其周向均布设置有两组压力传感器,两组压力传感器之间轴线距离80mm,每组压力传感器设置有20个,两组压力传感器以张力检测辊4长度方向对称设置,沿张力检测辊4轴向置入张力检测辊4的辊体中;中间品卷取机2包括机架2.1、卷轴2.2、扭矩合成减速机2.3、磁流变液离合器2.4、变速箱2.5、电机2.7;卷轴2.2转动设置在机架2.1上;其右侧端部通过联轴器与扭矩合成减速机2.3的扭矩输出轴2.3.1固定连接;扭矩合成减速机2.3设有三个扭矩输入轴2.3.2,变速箱2.5设有三个输出轴,扭矩合成减速机2.3的三个扭矩输入轴2.3.2分别通过三个磁流变液离合器2.4与变速箱2.5的三个输出轴传动连接,其中扭矩合成减速机2.3的扭矩输入轴2.3.2与扭矩输出轴2.3.1之间通过齿轮啮合连接,设有3:1的减速比,磁流变液离合器2.4最大工作扭矩为2.0kn*m;变速箱2.5的输入轴与电机2.7传动连接;本发明精密铜板带轧制生产线是采用磁流变液离合器2.4直接控制卷轴2.2的扭矩来控制轧制张力,其工作原理为:卷轴2.2的驱动传动链中设置的三个磁流变液离合器2.4所提供的工作扭矩,通过扭矩合成减速机2.3的合成、放大后,为卷轴2.2提供驱动扭矩;通过张力检测辊4反馈信号轮流控制三个磁流变液离合器2.4中一个磁流变液离合器2.4工作扭矩的大小,达到控制卷轴2.2的驱动扭矩,从而保证在铜带热粗轧过程中卷轴2.2所提供的轧制张力保持恒定;该轧制张力控制系统的工作原理,解决了传统轧制张力系统转动惯量大、响应速度慢、控制精度低的问题,因此可极大提高铜带热轧过程中轧制张力的控制精度,确保了铜带热粗轧后的尺寸精度的稳定性;卷轴2.2右侧端与与扭矩合成减速机2.3的扭矩输出轴2.3.1连接时,在联轴器中间固定设置有一个隔热块,用于阻止卷轴2.2的高温传递至扭矩合成减速机2.3的扭矩输出轴2.3.1上;在联轴器右侧端面还设置有一个散热盘2.3.1.3,散热盘2.3.1.3右侧端面设置有散热鳍片,当扭矩合成减速机2.3的扭矩输出轴2.3.1旋转时,散热盘2.3.1.3的散热鳍片带动空气形成散热气流,对联轴器和扭矩输出轴2.3.1进行散热。
[0019]
一种精密铜板带轧制生产线的精密铜带轧制生产工艺,包括精密铜板热轧、精密铜带热粗轧、高温固溶热处理;上述精密铜板的热轧、精密铜带的热粗轧、高温固溶热处理均在精密铜板带轧制生产线上完成;其中精密铜板热轧将铜及铜合金铸锭往复可逆轧制至12-20mm,在中间品卷取机2成卷;其中精密铜带热粗轧将12-20mm的铜板卷往复可逆轧制至1-4mm,轧制过程中通过卷材加热炉3在线加热,保持轧制温度;高温固溶热处理前,铜带卷通过卷材加热炉3在线加热,经高温固溶系统7在线高温固溶热处理后,最终在成品卷取机9成卷;以纯铜c11000生产终轧厚度1.5mm的精密铜带为例,其生产具体工艺参数如下:纯铜c11000坯料规格为厚度300mm,长度9000mm,在步进式加热炉内加热到950℃,坯料温度均匀性为950
±
6℃;坯料在炉内步进精度为1.8mm/次,在还原性气氛下的加热内压力为80kpa,压力控制精度值为
±
4pa;坯料出炉后进行5~9道次可逆轧制到厚度15mm,在每个道次轧制时的恒定辊缝值的液压压制精度偏差为
±
0.6μm,例如成品道次时的15mm
±
0.6μm;轧制速度在90~200m/min范围内逐渐提高,速度控制精度为
±
0.1%v(v为轧机运行速度,在90~200m/min之间);在轧制过程中长度方向的弯曲值为0.5 mm/m,总长范围内不超过25mm,带材的横向厚度偏差为
15mm
±
0.012mm,纵向厚度偏差为15mm
±
0.018mm,轧后的板形凸度值为85i;最后终轧温度为530℃;热轧后的带坯在加热炉3加热保温,进行精密铜带热粗轧;热粗轧成品厚度为1.5mm,轧制道次为7~9个,每个道次的轧制张力在高速时为7~70kn,在低速时为14~140kn或18~180kn,张力精度均为实际张力最大值的
±
1%范围内;轧后带卷内径为φ610 mm,带卷外径为φ1850 mm,内外径之间料卷的层错值均为
±
0.5mm,带卷总的塔型度为
±
5mm;带材的厚度偏差为1.5mm
±
0.001mm,轧后的板形凸度值为45i,带材的表面残油量为115mg/m2;终轧后料卷在高温固溶系统7中加热至600~1050℃,1~2.5分钟内降低到200~400℃以下,最终经成品卷取机9成卷。
[0020]
以高铜合金c19040生产终轧厚度15.5mm的铜板为例,其生产具体工艺参数如下:高铜合金c19040高铜合金c19040合金坯料规格为厚度200mm,长度6000mm,在步进式加热炉内加热到1020℃,坯料温度均匀性为1020
±
7℃。坯料在炉内步进精度为1.5mm/次,在还原性气氛下的加热内压力为75kpa,压力控制精度值为
±
3pa;c19040合金坯料出炉后进行5~9道次可逆轧制到厚度15.5mm,在每个道次轧制时的恒定辊缝值的液压压制精度偏差为
±
0.55μm,例如成品道次时的15.5mm
±
0.55μm;轧制速度在90~180m/min范围内逐渐提高,速度控制精度为
±
0.08%v(v为轧机运行速度,在90~180m/min之间);在轧制过程中长度方向的弯曲值为0.48 mm/m,总长范围内不超过20mm,带材的横向厚度偏差为15.5mm
±
0.01mm,纵向厚度偏差为15.5mm
±
0.012mm,轧后的板形凸度值为80i;最后在保证终轧温度为750℃时进行在线冷却至室温,最终经成品卷取机9成卷。
[0021]
一种基于精密铜板带轧制生产线的轧制张力控制方法,通过若干个磁流变液离合器2.4实际提供的工作扭矩合成驱动扭矩;通过张力检测辊4采集的张力信号反馈控制调整若干个磁流变液离合器2.4中单独一个的工作扭矩,实现对合成驱动扭矩的控制调整,最终由控制调整的合成扭矩控制卷轴2.2输出的轧制张力,其控制过程包括以下步骤:s1、磁流变液离合器2.4工作速度设置:磁流变液离合器2.4工作速度为其扭矩输入轴与扭矩输出轴的转速差,扭矩输入轴与扭矩输出轴的转速差设置维持在30rpm;s2、磁流变液离合器2.4工作扭矩分配:其初始工作扭矩以卷轴2.2实际工作所需扭矩平均分配给若干个磁流变液离合器2.4,计算公式为:mci=mj/i*n......(1)mj=t*rj
ꢀꢀꢀꢀꢀꢀꢀ
......(2)其中:mci为单个磁流变液离合器2.4分配的扭矩;mj为卷轴2.2实际工作所需扭矩;i为磁流变液离合器2.4输出轴与卷轴2.2之间的传动比;n为磁流变液离合器2.4数量;t为轧制张力;rj为卷轴2.2上铜带卷的外径;s3、磁流变液离合器2.4工作扭矩控制:若干个磁流变液离合器2.4工作扭矩由张力检测辊4采集的张力信号形成pid控制;反馈控制过程中,仅对若干个磁流变液离合器2.4中的一个进行工作扭矩调整控制,一个磁流变液离合器2.4的扭矩累计调整值设定有一个阈值;当被反馈控制的磁流变液离合器2.4的扭矩累计调整值达到或超出设定阈值时,反馈控制过程开始按设定排序对另一个磁流变液离合器2.4进行反馈控制;依次类推,在整个反馈控制过程中,实现对每个磁流变液离合器2.4的反馈控制;补充说明的是:在精密铜板带轧制生产线轧制张力控制过程中,实际还包括卷轴
2.2转速的控制,其控制结构和方法与现有技术基本相同,在此不再详细赘述;其不同之处在于:相对于现有卷轴2.2转速的控制,计算出的电机转速要适当提高,确保磁流变液离合器2.4的扭矩输入轴与扭矩输出轴的转速差维持在20-80rpm之间,通常为降低磁流变液离合器2.4在工作中的发热,扭矩输入轴与扭矩输出轴的转速差设定在下限附近,通常设置在30rpm;例如铜带热粗轧速度为150米/分,卷轴2.2的卷取外径为2m,计算出卷轴2.2的旋转速度为23.885rpm,根据扭矩合成减速机2.3的扭矩输入轴2.3.2与扭矩输出轴2.3.1之间3:1的减速比,计算出扭矩合成减速机2.3的扭矩输入轴2.3.2转速为71.656rpm,根据磁流变液离合器2.4扭矩输入轴与扭矩输出轴的转速差30rpm,则磁流变液离合器2.4的扭矩输入轴转速为101.656rpm;假设变速箱2.5的减速比为10,则最终计算得到的电机2.6的转速为1016.56rpm;精密铜板带轧制生产线的轧制张力控制流程具体参见说明书附图6,在轧制张力控制流程中实际包括初始扭矩分配流程10、磁流变液离合器2.4工作扭矩排序流程11、反馈控制循环流程12;下面以铜带热粗轧最终道次轧制为例,说明精密铜带在热粗轧过程中其轧制张力的控制过程,其轧制参数如下:热粗轧铜带成品厚度1.5mm,厚度偏差
±
0.001mm;带卷内径610mm,带卷外径φ1850 mm;起卷速度5m/min,轧制速度180m/min,加速时间30s;起卷张力1.0kn,轧制张力10kn,轧制张力允许波动范围
±
0.5%;磁流变液离合器2.4参数如下:最大工作扭矩2.0kn*m,起始扭矩(非控制状态下)0.01kn*m;为方便说明,假设控制电流与工作扭矩为线性关系(实际为非线性关系),其线性系数为0.25kn*m/a,工作电流控制精度为10.0ma;初始扭矩分配流程10:起卷时三个磁流变液离合器2.4工作扭矩分配如下:起卷时卷轴2.2实际工作扭矩为:mj=t*rj=1.0*0.305=0.305kn*m,每个磁流变液离合器2.4平均分配工作扭矩为mci=mj/i*n=0.305/(3*3)=0.0339kn*m,因此每个磁流变液离合器2.4的工作电流为95.6ma;设定每个磁流变液离合器2.4的累计扭矩调整阈值为0.01kn*m;磁流变液离合器2.4工作扭矩排序流程11:假设三个磁流变液离合器2.4分别为a、b、c,因其初始工作扭矩平均分配,其随机排序后前后顺序为a、b、c;反馈控制循环流程12:随着工作辊转速逐渐提高,卷轴2.2的转速和轧制张力也逐渐升高,轧制张力升高后的目标值由控制系统给出;当张力检测辊4按设定周期检测出的实际张力值与轧制张力升高后的目标值出现偏差,控制系统通过pid控制运算输出反馈控制信号,反馈控制信号导入卷轴张力控制流程,首先判断反馈信号控制方向(正向为增大工作扭矩,反向为减小工作扭矩),然后按照已经排定磁流变液离合器2.4的a、b、c顺序,对磁流变液离合器2.4c进行增大工作扭矩的控制;在每一个反馈控制循环流程12周期中,均需判断磁流变液离合器2.4c的扭矩累计调整值是否超过设定阈值0.01kn*m,如果没有超过,则进入下一周期的反馈控制循环;当在后续控制循环中,磁流变液离合器2.4c的扭矩累计调整值超过设定阈值0.01kn*m时,则重新进入工作扭矩排序流程11,从新对三个磁流变液离合器2.4a、b、c按照扭矩大小进行排序,排序结果为c、a、b(因c的工作扭矩最大,故排在第一位,a、b的排序为随机生成);磁流变液离合器2.4工作扭矩排序流程11结束后,重新进入反馈控制循环流程12,在新的反馈控制循环流程12中,会持续对磁流变液离合器2.4b的工作扭矩进行进行正向反
馈控制;在经过若干个反馈控制循环流程12后,磁流变液离合器2.4b的扭矩累计调整值会超过设定阈值0.01kn*m,此时重新进入工作扭矩排序流程11,对三个磁流变液离合器2.4a、b、c按照扭矩大小从新进行排序,排序结果为b、c、a(或因c 、b工作扭矩相等,排序结果为c、b、a,c、b的排序为随机生成);以上述工作扭矩排序流程11、与反馈控制循环流程12的反复执行,热粗轧铜带最终道次轧制逐渐从起卷阶段进入稳定轧制阶段,在此过程中,三个磁流变液离合器2.4a、b、c的工作扭矩从最初的0.0339kn*m,增加至1.1kn*m以上(带卷直径增加,进入稳定轧制阶段时三个磁流变液离合器2.4a、b、c的实际工作扭矩会超过1.1kn*m);进入稳定轧制阶段后,随着带卷直径持续增加,三个磁流变液离合器2.4a、b、c的实际工作扭矩会持续增加,在精密铜板带轧制生产线的轧制张力控制流程控制之下,轧制张力始终稳定控制在10kn保持不变;轧制张力控制精度分析:以稳定轧制阶段轧制张力控制为例,磁流变液离合器2.4的工作电流控制精度为10.0ma,即在一个反馈控制循环流程12中,磁流变液离合器2.4的工作扭矩变化量为0.0025kn*m,其所导致卷轴2.2的工作扭矩变化量为0.0075kn*m,以最大带卷直径1450mm计算,最终引起轧制张力的最大变化量为0.00544kn,其控制精度为0.0544%,远远高于精密铜带热粗轧最终道次轧制时轧制张力所允许波动的
±
0.5%的范围,因此其极高的轧制张力控制精度充分保证了精密铜带粗轧后的尺寸精度。
[0022]
本发明未详述部分为现有技术。
再多了解一些
本文用于创业者技术爱好者查询,仅供学习研究,如用于商业用途,请联系技术所有人。