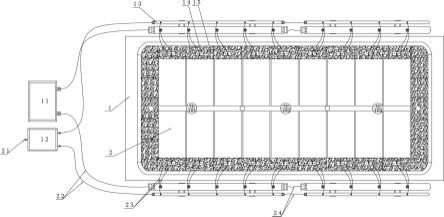
1.本发明涉及电解槽焙烧和启动技术领域,具体的说,涉及了一种铝电解槽高能焙烧装置、高温焙烧电解槽机构和启动方法。
背景技术:
2.铝电解槽燃气焙烧技术是近10几年来新兴起的一种焙烧方法,并且应用日益广泛。现有技术主要操作过程如下:通过燃气焙烧装置,按照预定的升温曲线,将电解槽阴极表面温度加热至700~950
°
c(cn 201883155u或cn 110042427 b),最终焙烧温度的高低因槽型大小而有所差异;停火、拆除焙烧装置;灌入电解质液;进行通电启槽操作。
3.以上过程要求时操作间短、衔接紧凑,整个操作时间一般控制在30min以内,一旦操作时间过长,就会引起启槽冲击电压过高、启动风险大,甚至启槽失败。
4.现有技术中的焙烧装置存在的主要问题有:最高焙烧温度只能达到950
°
c,达不到电解质熔化的温度,一旦超过设定时间,会导致电解质降温;燃烧负荷偏小,单位面积加热强度不足,仅有41.5kw,满足不了熔化电解质所需的加热强度;采用的保温盖板为不锈钢材质,当温度进一步升高时,当前保温盖板变形严重,无法满足使用需求;对于铝电解生产来说,培养液态电解质较为麻烦,往往启动1台电解槽,需要3~8台在产电解槽培养电解质,在产电解槽培养电解质时会破坏自身的正常生产工艺条件,炉邦熔化,后续再恢复正常生产工艺条件也需要一定的时间。
5.对于铝电解生产来说,电解质抽取较为繁琐,第一容易抽到铝水,第二真空抬包易堵包管,这两个问题都可能造成启槽失败,当抽到铝水较多时,倒入焙烧启动槽会造成通电启动过程电压摆动严重甚至滚铝现象,滚铝严重时将不得不停槽;当出现堵包管、处理不及时时,会造成焙烧槽温度下降明显,不具备送电条件从而引起启槽失败。
6.因此,就目前的铝电解槽焙烧技术来说,亟需一种可以解决灌装熔融电解质带来的一系列技术问题的设计,以避免上述各个问题。
7.为了解决以上存在的问题,人们一直在寻求一种理想的技术解决方案。
技术实现要素:
8.本发明的目的是针对现有技术的不足,从而提供一种升温高度可直接融化电解质、不再需要外置培养和抽取电解质、减少了焙烧步骤、电解槽启动更安全快捷和稳定的铝电解槽高能焙烧装置、高温焙烧电解槽机构和启动方法。
9.本技术的基本设计构思在于:在电解槽的焙烧过程中,对传统的焙烧结构进行改造,在电解槽的a/b面分别铺设作为密封材料的耐火纤维模块,然后将燃烧器成组的安装在电解槽的a/b面,对电解槽进行高温焙烧,最终的焙烧温度达到950
°
c-1100
°
c,能够将电解质熔融,在这种情况下,无论是传统的灌装电解质,亦或是直接在电解槽中将固态的电解质融化,都能够保证电解质的状态保持稳定,且直接融化的方式还能够省略灌装电解质的步骤,解决灌装电解质带来的一系列问题。
10.为了实现上述目的,本发明所采用的技术方案是:一种铝电解槽高能焙烧装置,包括主站、燃气站、供风机构、燃烧架和若干燃烧器;若干所述燃烧器分两列成对排列,分别用于安装在电解槽的两个长边内侧面处,两列燃烧器的喷头相对设置或交叉布置,以使高温气流聚集,形成950
°
c-1100
°
c的焙烧温度;所述燃烧架对应两列燃烧器设置,用于安装供应燃气和空气的管道,所述燃烧架上对应各个燃烧器设置有若干用于连接燃烧器的燃气支管和空气支管;所述燃气站通过管道与燃烧架上的燃气管道连通,所述燃烧架上的空气管道与供风机构连通;所述主站连接燃气站、燃烧架、供风机构和燃烧器以对所述燃气站、燃烧架和燃烧器的工作状态进行控制。
11.基上所述,所述燃烧器的外周包围有耐火纤维材料。
12.基上所述,所述供风机构集成于所述主站中。
13.基上所述,所述燃烧器为分体结构,包括燃烧室和上部结构,所述上部结构包括燃气进口、空气进口、堵帽、点/观火、定位板和固定螺栓,所述燃气进口、空气进口、点/观火孔均安装于所述定位板上,所述堵帽设置于点/观火孔的顶端,所述燃烧室通过固定螺栓与所述上部结构实现可拆卸连接;所述燃烧室的内侧设置喷口。
14.基上所述,所述燃烧架为沿成对排列的燃烧器设置的管道结构。
15.基上所述,还包括温度传感器,所述温度传感器分布于两列燃烧器之间的加热空间中,所述温度传感器连接主站。
16.基上所述,还包括氧含量传感器,所述氧含量传感器设置于所述燃烧器中,所述氧含量传感器连接主站。
17.一种高温焙烧电解槽机构,包括电解槽和铝电解槽高能焙烧装置,两列所述燃烧器分别安装于电解槽的两个长边的内侧面上,所述电解槽的内侧面设置有耐火纤维层,所述电解槽内预铺设有电解质块或电解质粉,所述耐火纤维层的耐火温度≥1250
°
c。
18.一种电解槽高能焙烧启动方法,通过以下方法进行启动:步骤1)在电解槽内预铺一定高度的电解质块或电解质粉的原料,挂阳极炭块;步骤2)将所述的铝电解槽高能焙烧装置安装于电解槽中,电解槽的内侧壁设置有耐火温度≥1250
°
c的耐火纤维层;步骤3)保温,对电解槽的上部覆盖电解质或冰晶石进行保温;步骤4)主站控制通入燃气和助燃空气并进行点燃,对电解槽内进行加热升温,直到焙烧温度达到950
°
c-1100
°
c;步骤5)随着电解槽内电解质的熔融,逐步填入新的电解质块或电解质粉的原料;
步骤6)当电解质量足够、阳极炭块和阴极炭块的温度也足够,控制电解槽启动。
19.基上所述,步骤1)中,预铺的电解质块或电解质粉的原料超过阴极炭块180mm-250mm。
20.本发明相对现有技术具有突出的实质性特点和显著的进步,具体的说,本发明具有以下几个优点:1.本方案相对传统的高温焙烧电解槽的方案而言,使电解槽内的焙烧温度可提升至融化电解质的程度,即便是仍采用传统灌注方案,电解质在灌注完成后依然可以保持融化,对启动时间更加宽容;2.由于电解槽内的温度满足融化电解质需求,电解质的熔融过程可以不依赖外部电解槽,直接在电解槽内铺固态电解质,通过加热融化,同时还能够对阴极炭块和阳极炭块进行同步加热,节省了灌注工序,操作时间得以缩短,电解槽通电启动的整个过程更加快速和平稳,安全性更高;3.由于阴极炭块在电解质熔融的过程中被覆盖,并通过熔融的电解质进行热传导,彻底避免了焙烧过程中对阴极炭块的损坏,有利于提高电解槽的使用寿命;4.燃烧器设计为分体结构,下部的燃烧室作为易损件,可以定期更换,降低应用成本;5.因焙烧后期业态电解质已经充分渗透阴极和伸腿可能产生的热膨胀裂纹,所以通电启动后可以明显减少灌铝的时间间隔,由传统的24h减少为4-8h,有利于提高生产效率,缩短非正常生产管理的时间;6.电解槽的单位热负荷可达到55-63kw,最终焙烧温度在950
°
c-1100
°
c,供风系统负责提供q=3000~6000nm3/h、p=8~30kpa的助燃风,以满足1100
°
c升温需求;燃气站负责提供q=300~600nm3/h、p=5~20kpa的出口燃气,以满足1100
°
c升温需求;充分满足焙烧温度和效率的需求,可用于230ka-600ka的各类电解槽槽型。
附图说明
21.图1是本发明中铝电解槽高能焙烧装置的布置结构示意图。
22.图2是本发明中铝电解槽高能焙烧装置的框架图。
23.图3是本发明中燃烧器的结构示意图。
24.图中:1.电解槽;2.阳极炭块;11.主站;12.燃气站;13.燃烧架;14.燃烧器;15.耐火纤维模块;141燃气进口;142.空气进口;143.堵帽;144.点/观火孔;145.定位板;146.固定螺栓;147.燃烧室;148.喷口;21.外部燃气进口;22.助燃风和燃气连接总管;23.燃烧器和燃烧架之间连接管;24.燃烧架之间连接软管。
具体实施方式
25.下面通过具体实施方式,对本发明的技术方案做进一步的详细描述。
26.如图1-图3所示,一种铝电解槽高能焙烧装置,包括主站11、燃气站12、供风机构、燃烧架13和若干燃烧器14,附属的装置有温度传感器和氧含量传感器,密封采用耐火纤维
模块15。
27.若干所述燃烧器14分两列成对排列,分别用于安装在电解槽1的两个长边内侧面处(a/b面),在电解槽1的a/b面分别安装耐火纤维模块15做铺装,燃烧器14四周的空间也用耐火纤维模块15包围密封,两列燃烧器14的喷头相对或交叉设置,相邻燃烧器14的间距控制在500-800mm,燃烧器14的安装高度通过定位板145与电解槽的配合来确定,燃烧器14的设计形式,可以使高温气流聚集,形成950
°
c-1100
°
c的焙烧温度。
28.具体的,所述燃烧器14为分体结构,包括燃烧室147和上部结构,所述上部结构包括燃气进口141、空气进口142、堵帽143、点/观火孔144、定位板145和固定螺栓146,所述燃气进口141、空气进口142、点/观火孔144均安装于所述定位板145上,所述堵帽143设置于点/观火孔144的顶端,所述燃烧室147通过固定螺栓146与所述上部结构实现可拆卸连接;所述燃烧室147的内侧设置喷口148。
29.所述燃烧架13对应两列燃烧器14设置,用于安装供应燃气和空气的管道,所述燃烧架13上对应各个燃烧器14设置有若干用于连接燃烧器14的燃气支管和空气支管,用于供应每个燃烧器14所需的空气和燃气。
30.供气系统集成在主站中,所述燃气站12和主站11通过助燃风和燃气连接总管22与燃烧架13上的燃气管道和助燃空气管道连通,温度传感器插在电解槽的中缝位置,氧含量传感器设置于各个燃烧器中。
31.所述主站内集成控制系统,用于连接控制燃气站12、燃烧架13、供风机构和燃烧器14以对所述燃气站12、燃烧架13和燃烧器14的工作状态进行控制,连接温度传感器,用于对电解槽内的焙烧温度进行控制。
32.其中,耐火纤维模块的耐火温度控制在≥1250
°
c,电解质原料为电解质块、电介质粉、再生冰晶石、冰晶石等原料的一种或几种,物料粒度范围在0-35mm,装炉量控制在高于阴极表面180-250mm的高度,且表面平整。
33.电解质原料的填装是在燃烧器装入之前,以便埋过阴极。
34.主站中的控制系统包括控制器、io模块、人机界面、隔离元件和变频器等常规控制元器件,供风系统主要包括风机、流量计、调节阀等,控制系统控制整个焙烧过程,供风系统负责提供q=3000~6000nm3/h、p=8~30kpa的助燃风,以满足1100
°
c升温需求。
35.所述燃气站:由分配器、减压阀、快速切断阀、调节阀、流量计、压力变送器、防回火装置、燃气泄漏检测装置等组成,其进口通过外部燃气进口21导入燃气,其工作受主站控制;燃气站负责提供q=300~600nm3/h、p=5~20kpa的出口燃气,以满足1100
°
c升温需求。
36.通过以上结构和参数设置,使整个装置的单位面积加热负荷为55~63kw,最终焙烧温度为950~1100
°
c;可应用于230ka~600ka的各类电解槽槽型。
37.电解槽高能焙烧启动方法如下:步骤1)安装前准备:在电解槽1内预铺一定高度的电解质块或电介质粉的原料,超过阴极180-250mm,然后挂阳极炭块2,要求阳极炭块2的底掌距离电解质表面150-300mm。
38.步骤2)将主站11、燃气站12分别布置在铝电解槽1的大面,燃烧架13布置在电解槽1的a/b面,燃烧器14安装在电解槽1的a/b面,放入电解槽炉膛内部,通过燃烧器14的定位板145固定燃烧器放入的高度,燃烧器间距为500~800mm,燃烧器14的四周采用耐火纤维模块15进行密封;主要设备安装完毕后,燃气站12的燃气进口21外接燃气总管,燃气站12和燃烧
架13、主站11和燃烧架13之间分别连接助燃风和燃气连接总管22,燃烧架13之间通过燃烧架之间连接软管24连接,燃烧架13和燃烧器14之间通过燃烧器和燃烧架之间连接软管23连接,其中:燃气管连接至燃烧器141接口,空气管连接至燃烧器142接口,燃气站12、燃烧架13、燃烧器14的控制线分别连接至主站11,温度传感器和氧含量传感器信号线分别连接至主站11;温度传感器插在电解槽中缝位置,根据槽型大小不同,温度传感器数量在3~10个;步骤3)保温,对电解槽的上部覆盖10~15cm厚度的电解质或冰晶石进行保温;步骤4)焙烧:保温结束后,可开始进行电解槽1的焙烧工作,升温策略设置和相关控制操作均在主站11进行,同时主站11根据主机控制策略提供一定压力和一定量的助燃风,燃气站12根据主机控制策略提供一定压力和一定量的燃气,燃气和助燃风通过燃烧架13输送至燃烧器14,在燃烧器的燃烧室147内进行混合燃烧,燃烧后的高温烟气经过燃烧器喷口148进入电解槽1,最终温度焙烧至950~1100
°
c,使电解槽炉膛内部的电解质熔化,同时达到焙烧的目的,焙烧期间的点火或观火均通过燃烧器14的点/观火孔144进行,图3所示燃烧器为人工点/观火燃烧器,点火完毕或观火结束后可盖住堵帽143。
39.步骤5)随着电解槽内电解质的熔融,逐步填入新的电解质块或电解质粉的原料,对熔融的电解质进行覆盖。
40.步骤6)当电解质量足够、阳极炭块和阴极炭块的温度也足够,控制电解槽启动。
41.实施例1新型铝电解槽高能焙烧装置,以230ka铝电解槽设备配置为例,单位面积加热负荷计算过程:(1)230ka铝电解槽,内炉膛尺寸为:3840*11700mm;炉膛面积为:3.84*11.7=44.928m2;(2)230ka铝电解槽,燃烧器数量32个、单个燃烧器功率为80kw时,总功率为:80*32=2560kw;(3)单位面积加热负荷:2560/44.928=56.98kw/m2;由计算结果可知:230ka槽型新型电解槽高能焙烧装置,单位面积加热负荷为56.98kw。
42.实施例2新型铝电解槽高能焙烧装置,以300ka铝电解槽设备配置为例,单位面积加热负荷计算过程:(1)300ka铝电解槽,内炉膛尺寸为:4000*14460mm;炉膛面积为:4*14.46=57.84m2;(2)300ka铝电解槽,燃烧器数量40个、单个燃烧器功率为80kw时,总功率为:80*40=2400kw;(3)单位面积加热负荷:3200/57.84=55.3kw/m2;由计算结果可知:300ka槽型新型电解槽高能焙烧装置,单位面积加热负荷为55.3kw。
43.实施例3新型铝电解槽高能焙烧装置,以600ka铝电解槽设备配置为例,单位面积加热负荷计算过程:
(1)600ka铝电解槽,内炉膛尺寸为:4270*22640mm;炉膛面积为:4.27*22.64=96.6728m2;(2)600ka铝电解槽,燃烧器数量60个、单个燃烧器功率为100kw时,总功率为:100*60=6000kw;(3)单位面积加热负荷:6000/96.6728=62.06kw/m2;由计算结果可知:600ka槽型新型电解槽高能焙烧装置,单位面积加热负荷为62.06kw。
44.通过以上实施例和装置的结构特性可知,与传统焙烧装置相比,采用高能焙烧装置的突出效果:启动时不需要在额外的灌液态电解质,操作步骤更少,操作时间更短,通电启动更加安全可靠;并且焙烧期间,熔融的电解质已经渗入焙烧期间可能产生的热膨胀裂纹,十分有利于提高电解槽使用寿命。
45.它解决了传统燃气焙烧装置使用过程中遇到的痛点问题,使用新型高能燃气焙烧装置,在焙烧电解槽的同时可加热熔化足量的液态电解质,启动前不再需要进行培养电解质、抽灌电解质等操作,因此操作时间更短,电解槽通电启动更加安全平稳;因不再需要在产电解槽培养电解质,节电环保;因焙烧期间阴极表面铺设的电解质物料,彻底避免了焙烧过程中阴极的氧化烧损,十分有利于提高电解槽使用寿命;因焙烧后期液态电解质已经充分渗透阴极和伸腿可能产生的热膨胀裂纹,所以通电启动后可以明显减少灌铝时间间隔,由24h改为4~8h,十分有利于提高生产效率,及缩短非正常生产管理期。
46.最后应当说明的是:以上实施例仅用以说明本发明的技术方案而非对其限制;尽管参照较佳实施例对本发明进行了详细的说明,所属领域的普通技术人员应当理解:依然可以对本发明的具体实施方式进行修改或者对部分技术特征进行等同替换;而不脱离本发明技术方案的精神,其均应涵盖在本发明请求保护的技术方案范围当中。
再多了解一些
本文用于创业者技术爱好者查询,仅供学习研究,如用于商业用途,请联系技术所有人。