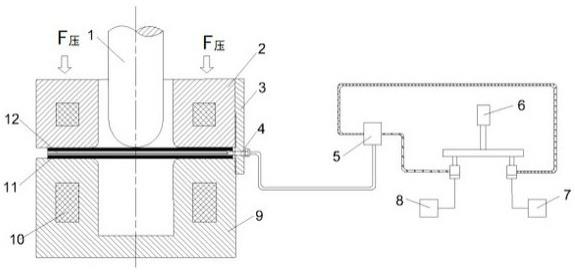
纤维金属层板热压rtm原位复合成形工艺方法及设备
技术领域
1.本发明属于复合材料成形制造技术领域,具体涉及一种纤维金属层板热压rtm原位复合成形工艺方法及设备。
背景技术:
2.纤维金属层板(fiber metal laminates,简称fmls)是由金属薄板(铝合金、钛合金等)和纤维(芳纶纤维、玻璃纤维、碳纤维)增强树脂预浸料交替铺设,在适当的温度和压力环境作用下固化而成的一种高性能混杂复合材料。fmls结合了单一金属和纤维增强复合材料的优点,具有高的比刚度和比强度、优异的抗疲劳性能和较高的损伤容限、高耐冲击性和耐腐蚀性,被认为是在航空航天、汽车、轨道交通等领域具有广泛应用前景的新型复合材料。纤维金属层板按树脂基体材料的不同,可分为热固性纤维金属层板和热塑性纤维金属层板,热固性树脂的特点是固化成形后,再受热也不会软化,形态不可逆转;而热塑性树脂是具有受热软化、冷却硬化的性能,且树脂的形态受温度的变化可逆,因此这两种纤维金属层板的制备和成形工艺完全不同。
3.目前,fmls成形方法主要可分为两种,一种是铺贴-热压罐成形技术,其借鉴了纤维增强树脂复合材料的成形方法,将成形后的金属薄板在曲面模具内与纤维树脂预浸料依次铺贴后放入热压罐内固化,在一次工艺中完成曲面构件的制造,可成形出曲率较小的单、双曲率构件,但是该方法成本高且周期较长。另一种是塑性成形技术,将制备好的fmls平板通过塑性成形的方法制造出曲面构件,可用于小型、多曲率构件成形。但纤维与金属的变形行为差异较大,纤维的破坏应变较小,金属与复合材料层间结合较为薄弱,导致分层、起皱、开裂和回弹常常伴随成形过程,使得纤维金属层板成形极限远低于相应的金属材料,成形难度大,限制了其进一步的推广应用。另外,降低零件生产成本且增加零件可成形的复杂程度,是fmls大规模应用的前提。而现有的成形方法中,无论是热固性还是热塑性纤维金属层板,其制备工艺过程复杂耗时、难以成形复杂形状零件且成形价格昂贵,导致fmls在工业上的应用没有吸引力,是制约其进一步的推广应用的瓶颈问题。
技术实现要素:
4.为了解决上述问题,本发明提供一种纤维金属层板热压rtm原位复合成形工艺方法及设备,该方法能够在一套设备上完成纤维金属层板构件的制备与成形两个工艺步骤,提高生产效率,极大地降低生产成本。其次,基于此工艺方法可以成形热塑性和热固性两种类型的纤维金属层板,提高工艺柔性。
5.为了达到上述目的,本发明提供一种纤维金属层板热压rtm原位复合成形工艺方法,按顺序包括如下步骤:1)对金属板的表面进行预处理,增强金属板对纤维复合材料树脂基体的粘附力;2)确定达到目标产品性能要求所需的纤维干布和金属板的数量和铺放顺序,将纤维干布与金属板按所需要求铺放,完成预制层板的铺贴;
3)将预制层板放置于成形模具中,并安装树脂注射通道,完成压边操作、预热工序:将铺贴的预制层板放置于凹模之上,并安装树脂注射通道,压边圈下行,使压边圈与预制层板接触,施加预设压边力f,并对预制层板和模具进行预热,调整树脂注射通道的出胶口使其对准纤维干布所在区域,完成预热工序;4)预设使凸模接触预制层板的拉深高度,凸模下行贴紧预制层板;5)对于热塑性纤维金属层板,直接加热使热塑性树脂基体处于粘流态存放于树脂存放罐,并通过树脂泵将热塑性树脂基体注入混合罐中;对于热固性纤维金属层板,将树脂基体和固化剂分别放入两个罐,在树脂泵的作用下,将树脂基体和固化剂通过管道输送,并按比例在混合罐内充分混合,使树脂基体达到成形性能最佳的流动状态;6)进入成形阶段,凸模继续下行,并使层板逐步变形至一定程度,维持层板的成形状态不变,使层板处于动态成形中或静止,将混合罐内达到最佳流动性能的树脂基体通过树脂注射通道注入层板的层间,同时设定凸模的拉深速度,并调控压边力和成形温度,使层板各层与各界面在压边力和成形温度的耦合作用下能处于最佳的成形状态,所述树脂基体为不间断的连续注入,完成树脂基体注入并继续成形固化;7)热压成形完成之后,成形模具保持闭合,根据目标纤维金属层板为热固性还是热塑性,分别选择对应的固化温度加载曲线进行加热或冷却工艺,在成形模具上完成固化过程。树脂注射通道撤出,继续保持包括凸模、凹模、压边圈在内的成形模具始终处于闭合压紧的状态,直至树脂基体在成形模具上完成固化;8)固化阶段结束后,按照树脂固化规律,等待成形模具梯度降温至室温,卸载开模,获得最终的纤维金属层板,也就获得了纤维金属层板构件。
6.本技术中成形之前称为预制层板,成形过程中为层板,最终产品为纤维金属层板构件。
7.与现有技术相比,本发明的有益效果是:本发明纤维金属层板热压rtm原位复合成形工艺方法创造性地将热压成形和树脂传递模塑成型(rtm)工艺结合在一起,能达到纤维金属层板制备成形一体化,解决制备工艺过程复杂耗时,难以成形复杂零件、成形价格昂贵的问题。因此,本技术是将热压成形技术与树脂传递模塑成型技术(rtm)进行交叉融合而衍生出的一种新型纤维金属层板制备成形一体化技术,对动态成形过程中的纤维金属层板进行注胶,其中动态成形过程中会有纤维和金属的协同变形,且纤维、树脂、金属在成形过程中也会相互有影响,本技术通过注入时间和相应状态点的控制使其能够在外力变形作用下实现很好的结合。
8.本发明方法是针对目前航空航天、汽车、轨道交通等领域对复合材料的应用需求逐渐增大,复合材料的制备、成形步骤繁杂且耗时,价格昂贵无法大批量生产,难以满足实际的应用需求,而研发出的一种新型热压成形与树脂传递模塑成型(rtm)的复合工艺,该工艺兼具两者的优点,利用热压成形可以进一步提高纤维金属层板的成形极限,利用树脂传递模塑成型(rtm)能够使树脂基体定量匹配,柔性更大,且在纤维干布层中的分布更加均匀,抑制层板分层现象,获得壁厚分布均匀、复杂结构的纤维金属层板构件。首先,通过热压方法成形层间不含树脂(成形后注胶)或含有粘流态树脂(成形中注胶)的纤维金属层板,具有层间约束应力降低、协同变形能力增强、成形裕度提高的优势,可以获得复杂形状的纤维金属层板构件。其次,利用特定温度下树脂兼具优良的可塑性和流动性的特点,可以提高纤
维金属层板的成形性能,并且成形后直接在模具上完成固化,可使纤维金属层板构件获得优良的层间性能,并进一步抑制层板回弹。同时,rtm工艺可根据成形构件的特征形貌和尺寸大小,选择成形阶段树脂基体的合适注入时机(成形过程中、成形后),可以实现金属和纤维干布在没有树脂或使用不同粘度状态树脂基体的情况下成形,极大地提高了纤维金属层板的成形裕度。选择合适的成形阶段(成形过程中、成形后),维持层板受压的状态始终不变,使其处于动态成形或静止状态,通过树脂注射通道注入树脂基体,成形结束后直接在模具上完成固化,大大缩短了制备层板的时间,提高了生产效率,减少了人员和设备的投入,进一步地降低了纤维金属层板构件的制造成本。同时,该工艺方法适用于热固性和热塑性纤维金属层板。
9.本发明提供的一种纤维金属层板热压rtm原位复合成形工艺方法及设备,可以充分实现纤维金属层板的制备成形一体化过程。
10.本技术的热压rtm原位复合成形包括了热压成形和rtm工艺,成形过程既有纤维的变形,又有金属的变形,为动态拉深过程,纤维干布和金属板先预压再将树脂基体在成形阶段注入,利用热压成形获得复杂形状,通过压边力与成形温度的耦合作用获得最佳成形状态,相较于一般的纤维金属层板先将纤维、树脂、金属板铺层固化好后再成形,层间的约束应力更小,成形裕度得到提升;该工艺方法适用于热固性和热塑性纤维金属层板,成形工艺柔性更好;成形结束后直接在模具上完成固化,避免了零件回弹、分层等缺陷,提高了纤维金属层板构件的成形质量;最后,通过对成形过程树脂注入时机的把握和成形工艺参数的调控,能得到壁厚分布均匀、复杂特征的纤维金属层板构件,为成形合格的纤维金属层板零件扩大了工艺窗口。
附图说明
11.图1为采用本发明提供的一种纤维金属层板热压rtm原位复合成形工艺方法及设备一种实施例的设备结构示意图。
12.图2为采用本发明提供的一种纤维金属层板热压rtm原位复合成形工艺方法及设备一种实施例的成形阶段示意图。
13.图3为采用本发明提供的一种纤维金属层板热压rtm原位复合成形工艺方法及设备一种实施例的固化阶段示意图。
14.图中:1-凸模,2-压边圈,3-定位夹持机构,4-树脂注射通道,5-混合罐,6-树脂泵,7-树脂存放罐,8-固化剂存放罐,9-凹模,10-加热单元,11-金属板,12-纤维干布,13-树脂基体。
具体实施方式
15.下面结合附图和具体实例对本发明提供的一种纤维金属层板热压rtm原位复合成形工艺方法进行详细说明。
16.本发明一种纤维金属层板热压rtm原位复合成形工艺方法,所用设备包括液压机和注胶装置,在液压机的凸模和凹模之间放置预制层板,所述液压机的凹模和压边圈均设置有加热单元,能够对其进行加热升温;所述注胶装置的出胶口数量不少于所要制备纤维金属层板中金属板的数量-1,所述注胶装置的出胶口正对纤维金属层板中纤维干布所在区
域,出胶口可伸入相邻两层金属板之间一段小距离,此时在设计纤维金属层板尺寸时需要设置一定的裕量,出胶口也可以不伸入相邻两层金属板内部,仅对准纤维干布所在区域即可;所述出胶口由定位夹持机构3固定,定位夹持机构3为了方便安装固定树脂注射通道4,防止成形过程或注胶过程导致树脂注射通道4偏离或掉落,定位夹持机构可以沿高度方向上设置不同排、用于固定相应出胶口的夹持口,定位夹持机构的主体部分可与压边圈的侧面固定,也可与凹模9的侧面固定,均要保证注胶时夹持口和出胶口相对应,所述夹持口可以为可开合结构,需要夹持时将注射通道伸入到位后,进行夹紧,具体结构形式可依据现有技术实现;所述注胶装置具有两个进料口,一个进料口用于树脂基体材料引入,一个进料口用于固化剂引入,树脂基体材料和固化剂根据比例需求混合后经注胶装置的树脂注射通道的出胶口注入纤维干布中。
17.示例性地,本发明工艺所用设备(参见图1)包括凸模1、压边圈2、凹模9、定位夹持机构3、树脂注射通道4、混合罐5、树脂泵6、树脂存放罐7、固化剂存放罐8、加热单元10,所述凸模1又称上模,凹模9又称下模,凸模1和凹模9在结构、位置上相互配合,凸模、凹模、压边圈构成成形模具,也就是液压机的主要组成部分,在压边圈2和凹模9内部或外部设置有用于加热升温的加热单元10,所述加热单元可以采用加热炉形式包裹在压边圈和凹模的外围,也可以在压边圈2和凹模9的内部安装加热单元,加热单元对模具和层板进行均匀加热;所述定位夹持机构3固定安装在压边圈2的侧面上,此时定位夹持机构3超出压边圈下边缘的部分沿高度方向上设置有多排夹持口,定位夹持机构会随着压边圈2的下移过程而向下移动,压边圈与预制层板接触后,夹持口能够对准相应的预制层板中纤维干布所在区域;所述树脂注射通道4安装在定位夹持机构3上并且头端位于层板层间,所述头端即为出胶口位置,树脂注射通道4、混合罐5、树脂泵6、树脂存放罐7、固化剂存放罐8为注胶装置的主要组成部件,树脂存放罐7用于存放树脂基体材料,固化剂存放罐8用于存放固化剂,树脂存放罐7和固化剂存放罐8的输出分别通过相应的管道和阀门连接树脂泵6,所述混合罐5的两个输入口分别连接树脂存放罐7和固化剂存放罐8的输出,混合罐5的输出口连接树脂注射通道4的尾端,树脂注射通道4的头部经定位夹持机构固定对准纤维干布所在区域,所述混合罐内设置有搅拌机构;树脂泵、混合罐和固化剂存放罐8之间,树脂泵、混合罐和树脂存放罐7之间均可通过电动三通阀连接;在树脂泵6的作用下,能将相应的物料输送至混合罐5中,热塑性树脂基体无须添加固化剂,不添加固化剂时,固化剂存放罐和树脂泵之间的阀门不打开,直接加热使其处于粘流态而存放于树脂存放罐7中,此时通过树脂泵6仅将热塑性树脂基体注入混合罐5中进行注胶;对于热固性树脂基体需要添加固化剂,在树脂泵6的作用下,将树脂基体13和固化剂通过管道输送,在混合罐5内充分混合,使树脂基体达到成形性能最佳的流动状态。
18.作为优选地,本发明中混合罐5、树脂泵6、树脂存放罐7、固化剂存放罐8之间的均通过透明塑料管连接,树脂注射通道4 和混合罐5之间通过透明的软管连接,能够更加方便观察胶体的流动性、判断出胶时间等。
19.如图1-3所示,本发明提供的一种纤维金属层板热压rtm原位复合成形工艺方法包括按照顺序进行下列步骤:
1)对金属板11表面进行预处理,以增强金属板11对树脂基体13的粘附力,所述预处理的过程为将金属板表面进行打磨,并用化学粘合剂进行预处理,打磨可手动打磨也可机械打磨,化学粘结剂可以为硅烷粘附促进剂。
20.2)确定达到目标产品性能要求所需的纤维干布和金属板的数量和铺放顺序,将纤维干布12与金属板11按所需要求铺放粘附,纤维干布之间及纤维干布与之前处理后的金属板之间通过粘接剂粘附,完成预制层板的铺贴;所述纤维金属层板中金属层和纤维层采用n 1/n的铺层结构,n指纤维层的数量,纤维金属层板的外表面均为金属板,纤维层中可以铺设多块或多层纤维干布,铺放顺序是两层金属板中间铺放纤维干布,不同的需求的纤维金属层板的纤维干布数量不同。此外可以通过对层板中金属和纤维的材料、厚度、层状结构和纤维方向的改变来最大限度地实现层板的优化设计,得到满足产品的性能要求的纤维金属层板。本实施例中以制备两层金属板加一层纤维层的纤维金属层板为例进行说明,纤维金属层板的结构是上下层都是相同的金属板,中间是纤维层和树脂。
21.3)将铺贴完成的预制层板放置于凹模9之上,并将树脂注射通道4安装在定位夹持机构3上,压边圈2下行,使压边圈与预制层板接触,施加预设压边力f,并通过加热单元10对预制层板和模具进行预热,调整树脂注射通道4的出胶口使其对准纤维干布所在区域,完成预热工序。
22.4)预设凸模的拉深高度,使凸模1下行接触预制层板的顶部金属板11,凸模继续下行贴紧预制层板,并使其逐步变形至一定程度。对预制层板采用预成形工序,让凸模贴紧预制层板,使得在树脂一开始注入进来或顶胀层板时,能避免上下层板向两个方向鼓胀。
23.5)对于热塑性纤维金属层板,直接加热使热塑性树脂基体处于粘流态存放于树脂存放罐7,并通过树脂泵6将热塑性树脂基体注入混合罐5中(不添加固化剂时,固化剂存放罐和树脂泵之间的阀门不打开);对于热固性纤维金属层板,将树脂基体和固化剂分别放入两个罐(即分别放置于树脂存放罐7和固化剂存放罐8中),通过不同的注入量控制加入量,在树脂泵6的作用下,将树脂基体13和固化剂通过管道输送,并在混合罐5内充分混合,使树脂基体达到成形性能最佳的流动状态。
24.6)进入成形阶段,维持层板的成形状态不变,使层板处于动态成形中或静止,将混合罐内达到最佳流动性能的树脂基体按一定的流速、压力通过树脂注射通道4注入层板层间,同时设定凸模1的拉深速度,并对压边圈2的压边力和加热单元10的成形温度进行调控,在压边力和温度的耦合作用下层板各层与各界面处于最佳的成形状态,促进树脂基体在层板间的流动贴合(参见图2),所述树脂注入过程为不间断的连续注入,完成基体注入并继续成形固化。
25.对于结构简单的零件,注树脂的时机可以是成形过程中或者成形后,但是对于复杂零件一般采用边成形边注射的方式,因为对于复杂零件的小特征处,成形完成后树脂在该区域的流动较困难。通过对成形阶段注树脂时机的把握并配合相应的工艺能得到壁厚分布均匀、复杂结构的纤维金属层板构件,为成形合格的纤维金属层板零件扩大了工艺窗口。纤维金属层板构件成形阶段中可以根据实际工况调整相应的工艺参数,包括温度,压边力、树脂粘度、树脂和固化剂的比例、树脂注射速度等,能够获得最佳性能的构件。在成形过程中凸模持续向下运动,层板变形,成形后保持静止状态,此时凸模不动,层板不继续变形。
26.所述复杂零件为具有复杂曲面、局部小特征和/或超小圆角的板材零件,零件为厚度方向的几何尺寸远小于其他方向(除了厚度方向以外的方向)的几何尺寸,复杂曲面指的是形状曲率变化多或者形状不简单或者不对称的异形类形状,局部小特征指局部形状复杂尺寸小的形状特征,超小圆角指半径只有 0.7-1.5 倍料厚的小圆角特征。
27.通过树脂泵和混合罐的共同作用,使粘流态树脂以最佳的状态、最合适的流速注入层板中间,避免出现纤维“冲刷”和树脂堆积等现象,提高了纤维金属层板构件的成形质量和成形性能。
28.7)热压成形完成之后,树脂注射通道4撤出,继续保持包括凸模1、凹模9、压边圈2在内的成形模具始终处于闭合压紧的状态,直至树脂基体在成形模具上完成固化,即凸模、凹模、压边圈保持成形后的位置不变,树脂注射通道关闭,让层板保持成形后的形状直接固化。对于热固性纤维金属层板,根据热固性树脂的固化温度曲线对加热单元10进行温度调控,完成固化。对于热塑性纤维金属层板,可将加热单元10关闭后自然冷却,或提供低温环境或冷却介质将其冷却固化。纤维金属层板直接在成形模具上固化成形,可以抑制回弹、分层等缺陷的发生。
29.8)固化阶段结束后,按照树脂固化规律,等待成形模具梯度降温至室温,卸载凸模1的凸模力和压边圈2的压边力,并且凸模1上行,压边圈2退回,取出零件,完成纤维金属层板的成形,获得相应的纤维金属层板构件。
30.本文中应用了具体个例对本发明的原理及实施方式进行了阐述,以上实施例的说明只是用于帮助理解本发明的构建方法及其核心思想。应当指出,对于本技术领域的普通技术人员来说,在不脱离本发明原理的前提下,还可以对本发明进行若干改进和修饰,这些改进和修饰也落入本发明的保护范围内。
31.本发明未述及之处适用于现有技术。
再多了解一些
本文用于创业者技术爱好者查询,仅供学习研究,如用于商业用途,请联系技术所有人。