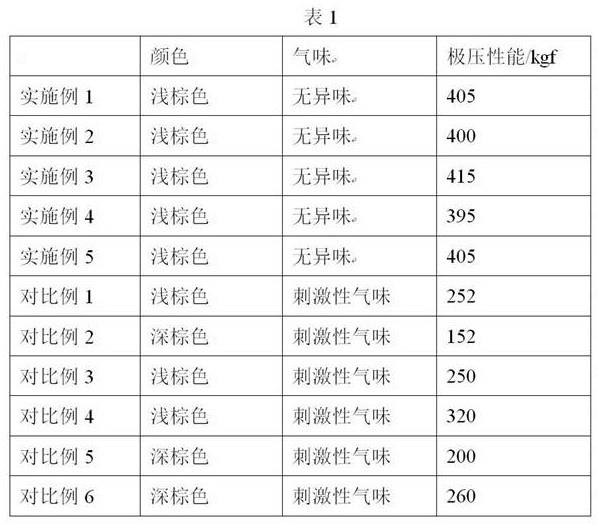
1.本发明属于硫化物技术领域,具体涉及一种硫化油酸甲酯及其制备方法和应用。
背景技术:
2.硫化油酸甲酯是一种重要的含硫极压剂,拥有优良的极压性能,可作为添加剂广泛应用于润滑油中。
3.硫化油酸甲酯的现有合成技术主要包括硫氯路线、硫磺路线和硫化氢路线,主要区别在于使用的硫化剂不同(可参见leslie r. rudnick, lubricant additives: chemistry and applications (third edition), crc press, 2017)。硫氯路线,以单氯化硫(s2cl2)为硫化剂,反应中放出大量的hcl等强腐蚀性气体,同时产生了废水和废渣(含nacl和硫化物),使三废处理困难,且生产工艺复杂。硫磺路线,以硫磺为硫化剂,直接与油酸甲酯反应,该反应路线遵循自由基机理,极易发生副反应,副产颜色深且伴有刺激性气味的硫酮、硫醇等,导致最终产品呈现深黑色且具有浓重刺激性气味,应用范围窄,硫磺路线遵循的自由基机理图如图1所示。硫化氢路线,以硫化氢和硫磺作为共硫化剂,但最终产品也具有浓重刺激性气味,硫化氢路线遵循的亲核机理图如图2所示。因此,设计一种新的硫化油酸甲酯的制备方法以生成颜色浅、无异味、极压性能好的硫化油酸甲酯具有重要的现实意义。
技术实现要素:
4.为解决现有技术中存在的技术问题,本发明的目的在于提供一种硫化油酸甲酯及其制备方法和应用。
5.为实现上述目的,达到上述技术效果,本发明采用的技术方案为:一种硫化油酸甲酯,所述硫化油酸甲酯通过先将硫磺、硫化氢和有机胺混合反应再加入油酸甲酯混合反应后制成。
6.在本发明提供的一种硫化油酸甲酯中,所述硫磺、硫化氢、有机胺和油酸甲酯的摩尔比为(1~3):1:(0.1~0.3):(4~10)。
7.在本发明提供的一种硫化油酸甲酯中,所述有机胺为二环己胺、正丁胺、环己胺、哌啶、六亚甲基亚胺中的一种或几种的组合。
8.本发明还公开了一种硫化油酸甲酯的制备方法,包括以下步骤:(1)将硫磺、硫化氢和有机胺混合,随后加入油酸甲酯,反应一定时间;(2)将步骤(1)所得产物进行蒸馏,得到所需硫化油酸甲酯。
9.步骤(1)中,将硫磺、硫化氢和有机胺混合,随后加入油酸甲酯,反应一定时间的步骤包括:将硫磺、硫化氢和有机胺加入高压釜内,升温至140~200℃,搅拌反应0.5~3h后往高压釜内匀速加入油酸甲酯,所述硫磺、硫化氢、有机胺和油酸甲酯的摩尔比为(1~3):1:(0.1~0.3):(4~10),所述油酸甲酯在1~3h内全部加完,加完后继续反应1~6h。
10.步骤(2)中,蒸馏温度为80~120℃,蒸馏时间为1~6h。
11.本发明还公开了一种硫化油酸甲酯在极压剂中的应用。
12.与现有技术相比,本发明的有益效果为:本发明公开了一种硫化油酸甲酯及其制备方法和应用,该硫化油酸甲酯通过先将硫磺、硫化氢和有机胺混合反应再加入油酸甲酯混合反应并蒸馏后制成。本发明中,先将硫磺、硫化氢和有机胺混合反应,再加入油酸甲酯进行反应,使硫磺及时与硫化氢反应生成具有强亲核性的hs
x-中间体,hs
x-中间体再与油酸甲酯上的碳碳双键发生亲核反应生成硫化油酸甲酯,保证了硫磺不与油酸甲酯直接反应,使获得的硫化油酸甲酯具有颜色浅、无异味、极压性能好等特点,特别适合作为极压剂添加到润滑油中。
附图说明
13.图1为硫磺路线遵循的自由基机理图;图2为硫化氢路线遵循的亲核机理图;图3为本发明实施例1得到的硫化油酸甲酯的色谱图;图4为本发明实施例3得到的硫化油酸甲酯的色谱图;图5为本发明实施例5得到的硫化油酸甲酯的色谱图;图6为对比例2得到的硫化油酸甲酯的色谱图;图7为对比例5得到的硫化油酸甲酯的色谱图。
具体实施方式
14.下面对本发明进行详细阐述,以使本发明的优点和特征能更易于被本领域技术人员理解,从而对本发明的保护范围做出更为清楚明确的界定。
15.以下给出一个或多个方面的简要概述以提供对这些方面的基本理解。此概述不是所有构想到的方面的详尽综览,并且既非旨在指认出所有方面的关键性或决定性要素亦非试图界定任何或所有方面的范围。其唯一的目的是要以简化形式给出一个或多个方面的一些概念以为稍后给出的更加详细的描述之序。
16.实施例1一种硫化油酸甲酯,通过先将硫磺、硫化氢和有机胺混合反应再加入油酸甲酯混合反应并蒸馏后制成。
17.本实施例的硫化油酸甲酯的制备方法,包括以下步骤:(1)将硫磺、硫化氢和二环己胺加入高压釜内,升温至150℃,搅拌反应2h后往高压釜内匀速加入油酸甲酯,油酸甲酯在2h内全部加完,加完后继续反应4h;本步骤中,硫磺、硫化氢、二环己胺和油酸甲酯的摩尔比为1:1:0.1:8。
18.(2)将步骤(1)所得产物于100℃条件下蒸馏6h,即可得到所需硫化油酸甲酯。
19.实施例2本实施例的硫化油酸甲酯的制备方法,包括以下步骤:(1)将硫磺、硫化氢和正丁胺加入高压釜内,升温至140℃,搅拌反应3h后往高压釜内匀速加入油酸甲酯,油酸甲酯在3h内全部加完,加完后继续反应1h;本步骤中,硫磺、硫化氢、正丁胺和油酸甲酯的摩尔比为2:1:0.3:4。
20.(2)将步骤(1)所得产物于80℃条件下蒸馏6h,即可得到所需硫化油酸甲酯。
21.余同实施例1。
22.实施例3本实施例的硫化油酸甲酯的制备方法,包括以下步骤:(1)将硫磺、硫化氢和正丁胺加入高压釜内,升温至170℃,搅拌反应1h后往高压釜内匀速加入油酸甲酯,油酸甲酯在1h内全部加完,加完后继续反应6h;本步骤中,硫磺、硫化氢、正丁胺和油酸甲酯的摩尔比为3:1:0.1:8。
23.(2)将步骤(1)所得产物于100℃条件下蒸馏4h,即可得到所需硫化油酸甲酯。
24.余同实施例1。
25.实施例4本实施例的硫化油酸甲酯的制备方法,包括以下步骤:(1)将硫磺、硫化氢和哌啶加入高压釜内,升温至200℃,搅拌反应0.5h后往高压釜内匀速加入油酸甲酯,油酸甲酯在2h内全部加完,加完后继续反应6h;本步骤中,硫磺、硫化氢、哌啶和油酸甲酯的摩尔比为1.5:1:0.2:10。
26.(2)将步骤(1)所得产物于120℃条件下蒸馏1h,即可得到所需硫化油酸甲酯。
27.余同实施例1。
28.实施例5本实施例的硫化油酸甲酯的制备方法,包括以下步骤:(1)将硫磺、硫化氢和六亚甲基亚胺加入高压釜内,升温至170℃,搅拌反应1h后往高压釜内匀速加入油酸甲酯,油酸甲酯在3h内全部加完,加完后继续反应6h;本步骤中,硫磺、硫化氢、哌啶和油酸甲酯的摩尔比为2:1:0.2:8。
29.(2)将步骤(1)所得产物于100℃条件下蒸馏6h,即可得到所需硫化油酸甲酯。
30.余同实施例1。
31.对比例1本对比例与实施例3的区别在于,本对比例的硫化油酸甲酯的制备方法,包括以下步骤:(1)将单氯化硫(s2cl2)、氯化铝和油酸甲酯按摩尔比为12:0.1:8加入高压釜内,升温至45℃,搅拌反应6h。
32.(2)将步骤(1)反应完毕后得到的产物经过量硫化钠水溶液脱氯,其中,所述脱氯条件为40℃下处理4h。
33.对比例2本对比例与实施例3的区别在于,本对比例的硫化油酸甲酯的制备方法,包括以下步骤:(1)将硫磺、正丁胺和油酸甲酯按摩尔比为3:0.1:8加入高压釜内,升温至170℃,搅拌反应6h。
34.(2)将步骤(1)反应完毕后得到的产物经蒸馏后得到产品硫化油酸甲酯,其中,所述蒸馏条件为100℃下蒸馏4h。
35.对比例3本对比例与实施例3的区别在于,本对比例的硫化油酸甲酯的制备方法,包括以下
步骤:(1)将硫磺、硫化氢、正丁胺和油酸甲酯按摩尔比为3:1:0.1:8加入高压釜内,升温至170℃,搅拌反应6h。
36.(2)将步骤(1)反应完毕后得到的产物经蒸馏后得到产品硫化油酸甲酯,其中,所述蒸馏条件为100℃下蒸馏4h。
37.对比例4本对比例与实施例3的区别在于,本对比例的硫化油酸甲酯的制备方法,包括以下步骤:(1)将油酸甲酯加入高压釜内,升温至170℃后,往高压釜内匀速加入硫磺、硫化氢和正丁胺,并在1h内全部加完,加完后继续反应6h;本步骤中,硫磺、硫化氢、正丁胺和油酸甲酯的摩尔比为3:1:0.1:8。
38.(2)将步骤(1)所得产物于100℃条件下蒸馏4h,即可得到所需硫化油酸甲酯。
39.对比例5本对比例与实施例1的区别在于,本对比例的硫化油酸甲酯的制备方法,包括以下步骤:(1)将硫磺、硫化氢和四丙基氢氧化铵按摩尔比为1:1:0.1加入高压釜内,升温至150℃,搅拌反应2h后,按油酸甲酯与硫化氢的摩尔比为8:1往高压釜内匀速加入油酸甲酯,油酸甲酯在2h内加完,加完后继续反应4h。
40.(2)将步骤(1)反应完毕后得到的产物经蒸馏后得到产品硫化油酸甲酯,其中,蒸馏条件为100℃下蒸馏6h。
41.对比例6本对比例与实施例4的区别在于,本对比例的硫化油酸甲酯的制备方法,包括以下步骤:(1)将硫磺、硫化氢和氨气按摩尔比为1.5:1:0.2加入高压釜内,升温至200℃,搅拌反应0.5h后,按油酸甲酯与硫化氢的摩尔比为10:1往釜内匀速加入油酸甲酯,油酸甲酯在2h内加完,加完后继续反应6h。
42.(2)将步骤(1)反应完毕后得到的产物经蒸馏后得到产品硫化油酸甲酯,其中,蒸馏条件为120℃下蒸馏1h。
43.对实施例1、实施例3、实施例5、对比例2、对比例5得到的产品分别进行气相色谱分析,气相色谱分析结果见图3-7。对实施例1-5和对比例1-6得到的硫化油酸甲酯分别进行性能测试,测试方法和测试标准如下:极压性能测试:根据国家标准《gb/t 12583-1998润滑剂极压性能测试法(四球法)》测试上述实施例和对比例得到的硫化油酸甲酯。
44.颜色和气味测试:将硫化油酸甲酯样品注入透明烧杯中,通过目测判断样品颜色,通过嗅闻判断样品气味。
45.性能测试结果见表1。
46.由表1可知,对比例1将单氯化硫(s2cl2)、氯化铝和油酸甲酯直接混合反应,然后利用硫化钠进行脱氯后得到带有刺激性气味的产物,且产物的极压性能差,并放出大量的hcl等强腐蚀性气体,同时产生了废水和废渣(含nacl和硫化物)。对比例2中将硫磺、正丁胺和油酸甲酯直接混合反应,产物颜色深并伴有刺激性气味的硫酮、硫醇的产生,且产物的极压性能差。对比例3中将硫磺、硫化氢、正丁胺和油酸甲酯直接混合反应会产生带有刺激性气味的产物,且产物的极压性能差,这是因为硫磺不能及时与硫化氢反应生成hs
x-中间体,伴随着硫磺与油酸甲酯直接反应,导致少量颜色深且伴有刺激性气味的硫酮、硫醇的产生。相比对比例2和3,实施例3先将硫磺、硫化氢和正丁胺混合反应,再加入油酸甲酯进行反应,使硫磺及时与硫化氢反应生成hs
x-中间体,保证了硫磺不与油酸甲酯直接反应,从而制成了颜色浅、无异味、极压性能好的硫化油酸甲酯,但是先加入油酸甲酯再加入硫磺、硫化氢和正丁胺(见对比例4),会产生带有刺激性气味的产物,且产物的极压性能差,硫磺、硫化氢、正丁胺、油酸甲酯的加入顺序很重要,直接影响是否能够得到所需颜色浅、无异味、极压性能好的硫化油酸甲酯。将实施例1与对比例5相比可知,四丙基氢氧化铵等铵类物质不能通过复配硫磺、硫化氢和油酸甲酯得到颜色浅、无异味、极压性能好的硫化油酸甲酯,采用本发明的有机胺(二环己胺)替代四丙基氢氧化铵有助于生成颜色浅、无异味、极压性能好的硫化油酸甲酯。将实施例4与对比例6相比可知,氨气不能通过复配硫磺、硫化氢和油酸甲酯得到颜色浅、无异味、极压性能好的硫化油酸甲酯,采用本发明的有机胺(哌啶)替代氨气有助于生成颜色浅、无异味、极压性能好的硫化油酸甲酯。
47.本发明未具体描述的部分或结构采用现有技术或现有产品即可,在此不做赘述。
48.以上所述仅为本发明的实施例,并非因此限制本发明的专利范围,凡是利用本发明说明书内容所作的等效结构或等效流程变换,或直接或间接运用在其他相关的技术领域,均同理包括在本发明的专利保护范围内。
再多了解一些
本文用于创业者技术爱好者查询,仅供学习研究,如用于商业用途,请联系技术所有人。