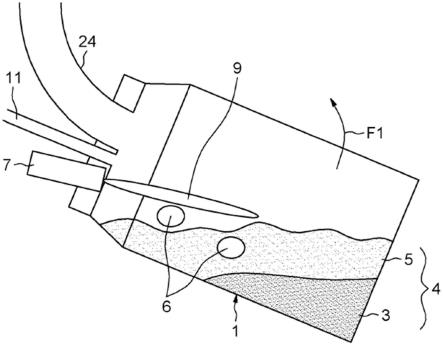
1.本发明涉及一种方法,该方法允许通过在铁合金中回收废催化剂中所含的金属,这些废催化剂来自于在石油精炼和石油化学领域中进行的烃处理方法。
背景技术:
2.在炼油厂和/或石化装置中进行的烃处理方法包括在含有金属化合物的催化剂存在下进行的一定数量的处理。非限制性示例包括加氢裂化、重整、氢化以及诸如加氢脱硫、加氢脱氮、加氢脱芳烃、加氢脱金属的“加氢处理”方法。
3.这些方法中使用的催化剂为包含多孔载体的固体颗粒形式,所述多孔载体包含一种或多种难熔无机氧化物,例如氧化铝,其上沉积有一种或多种催化活性金属,所述催化活性金属包含元素周期表第viii族的至少一种金属,例如镍和/或钴,通常与vib族的一种或多种金属共生,例如钼。
4.在使用过程中,这些催化剂会逐渐失活,特别是因为焦炭沉积在其表面,也就是说,重质烃类的混合物、碳残留物的混合物以及已处理原料中所含的金属杂质的混合物,例如,特别是钒的化合物。
5.在使用周期后,这些催化剂可通过“再生”处理进行再循环,在此过程中焦炭通过燃烧消除,目的是使催化剂的活性水平尽可能接近其初始水平。
6.然而,在一个或多个使用周期和再循环之后,废催化剂不再能够以技术和经济上令人满意的方式再生。
7.出于经济和环境保护的原因,现在越来越多地寻求在使用寿命结束时再利用这些废催化剂。
8.在废催化剂中,金属大体上以金属硫化物的形式存在,烃类、硫和碳的浓度分别可高达催化剂重量的20%。
9.废催化剂主要分为三种状态:
[0010]-原料状态下的废催化剂:这些催化剂未经过任何处理,并且含有硫化物形式的金属以及硫和碳化合物,这些化合物大体上以固定碳和烃类的形式存在,每种浓度可高达20重量%;
[0011]-脱油状态下的废催化剂:这些催化剂经过几乎完全提取烃类的处理,通常是在温度和气体流的作用下,所述气体可以是氮气、水蒸气以及在中等温度的一定条件下的空气。这些催化剂含有硫化物形式的金属以及硫和固定碳形式的碳,其浓度可分别高达20重量%,残余烃类的浓度可高达5重量%;
[0012]-煅烧或“焙烧(grilled)”状态下的废催化剂:这些催化剂经过煅烧处理,它们含有大体上以氧化物形式存在的金属,它们的硫和碳化合物的浓度均小于3%,烃类的浓度为零。
[0013]
在本技术中,“碳化合物”是指所有含碳的化合物,无论它们是有机性质还是无机性质。该术语包括烃类和固定碳。
[0014]“固定碳”是指不同于烃类的所有含碳的化合物。该术语对应于以本身已知方式命名的“焦炭”。
[0015]
表1在以下表示了,作为非限制性示例,在原料状态、脱油状态和焙烧状态下氧化铝载体上“nimo”或“como”或“nicomo”或“nimov”催化剂的典型化学组成。在该表中,所有浓度均以分别相对于总原料催化剂、脱油催化剂或焙烧催化剂的重量%表示,镍、钴、钼和钒的浓度除外,其以相对于总焙烧催化剂的重量%表示(在不含烃类的催化剂上的氧化物状态的金属浓度,其碳浓度少于3重量%,硫浓度少于3重量%)。
[0016]
表1
[0017][0018]
通常,原料废催化剂在任何后处理之前已进行脱油。
[0019]
也通常的是,现有的各种回收行业(sector)(水冶或火冶)都通过煅烧来进行焙烧操作,目的是将金属硫化物转化为氧化物,并消除困扰水冶行业操作的碳。
[0020]
这就导致了烃类中所含能量的浪费。
[0021]
钼、钒、有时还有镍和/或钴,通常在焙烧后通过一系列水冶步骤,通过浸出和选择性沉淀某些元素来分离和纯化。这种水冶行业的主要缺点是其连续进行大量复杂的步骤,直至最终产品,这涉及大量的能源消耗和反应物消耗,特别是化学产品的消耗,以及在生产废物和二氧化碳排放方面的强烈环境影响,需要相当大的关联成本。此外,诸如镍、钴、钼、钒(ni、co、mo、v)的金属的回收率相对较低。
[0022]
一个不太广泛的行业,尤其是在欧洲,涉及在潜弧电炉型或自由电弧炉(eaf)型的电炉(其中一种替代方案是直流电炉)中进行焙烧和熔化,然后在一个单独的步骤中对铁合金进行精炼,尤其通过在另一个反应器中消除硫和磷,然后可选地通过硅铝热处理将变成矿渣的钒转化成钒铁而获得所述铁合金。
[0023]
在此方法中,能源消耗尤其显著。连续的步骤以及一系列反应器导致了高电耗。
[0024]
而且,当催化剂包含显著比例的钒(例如高于5重量%)的情况下,大部分的钒被转移至炉渣并被固化。然后,这些炉渣在水冶或火冶步骤中被处理以从中提取钒。
[0025]
专利ep 1 983 066提出了一种在电炉中直接处理脱油催化剂(无需之前的焙烧)的方法,通过将这些催化剂喂送至铸铁熔体(含2-4%碳的碳化铁)上并在铸铁熔体上处理,通过注入中性气体来进行搅拌,并加入石灰以获得液态炉渣。熔融成铁合金之后,随后在同一熔炼炉中进行可选的补充脱硫处理(使用石灰),然后对铁合金进行脱磷处理(通过注入
氧气并添加石灰和铁氧化物来进行脱磷),使其硫浓度和磷浓度降低至少于0.1%。
[0026]
然而,此方法具有诸多缺点。
[0027]
一方面,在原料催化剂中存在的碳化合物(包括固定碳以及烃类形式的碳)实际上并没有得到利用。只有部分固定碳用于还原反应,例如:nio c
→
ni co。然而,原料催化剂中存在的co气体、硫和所有烃类的显著能量含量被浪费。
[0028]
另一方面,铁合金的补充脱硫和脱磷处理在电炉中进行,其性能受到技术几何结构的限制,特别是扁平和静态的熔体,这导致铸铁熔体和炉渣之间的交换受到限制,尽管采用了气体搅拌。由此可见,这些处理在时间、搅拌气体和补充添加能量以保持金属熔体和炉渣的温度方面是昂贵的。此外,出于技术几何结构的相同原因,要形成相当大比例的炉渣(每吨经处理的催化剂,炉渣超过1吨),需要经常清除炉渣(或“除渣”),这会导致时间和生产力的损失,因为该方法经常中断。
[0029]
最后,当催化剂含有钒时,钒被转移到炉渣中,在这种方法中,炉渣被少量除渣,必须单独处理炉渣才能从炉渣中提取钒。因此,对炉渣中存在的钒进行的这种处理是在炉渣冷却后进行的,这需要新的能量消耗(电 电极)以在通过硅铝热型的火冶法从炉渣中提取钒之前将炉渣重新熔化。
技术实现要素:
[0030]
本发明旨在提出一种允许高效回收存在于废催化剂中的金属的新方法,所述金属诸如钼、镍、钴,且可选为钒,同时,相对于现有的方法,本方法成本更低且尤其需要更低的能耗。
[0031]
本技术人已经开发了一种从废催化剂中回收这些金属的方法,该方法的特征在于,该方法在含有液态铸铁熔体的回转转炉型熔融反应器中实施,并且存在靶向注入的氧化气体。这种类型的反应器能够通过其旋转进行比具有扁平熔体的静态炉更有力的搅拌,并且比具有相同容量的电炉包含更多的炉渣。
[0032]
根据本发明的方法允许高效回收转移入铸铁中的有价值金属,例如钼、镍、钴、钨。当废催化剂包含钒时,本发明的方法允许处理富含钒的大量炉渣,因此这些炉渣能够被“热”处理,也就是说,无需特定的加热步骤,尤其是通过将炉渣直接转移至另一个回转反应器。
[0033]
根据本发明的方法具有重要的优点,即在或多或少的程度上使用存在于原料催化剂和脱油催化剂中的碳化合物(特别是烃类和固定碳)和硫中所包含的能量。
[0034]
本发明的目标因此是一种用于处理废催化剂的方法,所述废催化剂包含至少一种难熔矿物氧化物、一种或多种硫化物形式的金属以及碳化合物,所述硫化物形式的金属选自以下金属:钼、镍、钴、钨、钒。该方法包括以下连续步骤:
[0035]
a)在回转转炉型熔炼炉中制备熔化状态的铸铁熔体,所述铸铁熔体上方存在一层炉渣;然后
[0036]
b)将所述废催化剂引入熔炼炉,并将废催化剂与炉渣和熔化状态的铸铁熔体接触,同时维持熔炼炉旋转,并同时在催化剂、炉渣和铸铁的混合物上方,将含有氧气的氧化气体注入熔炼炉,以此方式使与炉渣和液态铸铁接触的催化剂释放的碳化合物和/或硫化合物燃烧;然后
[0037]
c)通过连续铸造,从熔炼炉中提取在步骤b)中形成的炉渣,以此方式,一方面在熔炼炉中回收富含一种或多种金属的铸铁熔体,另一方面回收含有除金属外的催化剂组分的炉渣,但钒除外,当废催化剂包含钒时,废催化剂最后落入炉渣中。
[0038]
因此,根据本发明的方法通过将金属转移,并通过以高效的方式在铸铁熔体中(当金属为钼、镍、钴、钨时)或在炉渣中(当金属为钒时)分离金属,以允许重复利用包含在催化剂中的金属,同时,使用包含在废催化剂中的能量,也就是碳化合物(以固定碳和烃类形式)和硫中的能量。
[0039]
尤其,在步骤b)中废催化剂熔化的高吸热阶段期间,碳化合物、烃类和金属硫化物在注入的氧化气体存在下大部分转化为so
x
型挥发性硫化物和co2,其通过加热熔炼炉的内容物并允许将熔炼炉的温度保持在所需水平来重复利用它们的能量。
[0040]
事实证明,与静态电炉相反,回转转炉的技术特别适合于进行这种热高效的燃烧。事实上,除了转炉的有利几何形状之外,转炉的旋转允许将通过燃烧传递的热量经由熔炼炉的难熔壁重新传递给铸铁熔体和炉渣熔体。
[0041]
通常,含有10重量%固定碳和10重量%烃类的一吨原料催化剂的能量含量约为2000kwh(热),这是由于总燃烧成co2和h2o(冷排出烟气)。在传统技术中,该能量会丢失。对于含有20重量%固定碳和20重量%烃类的一吨原料催化剂,该能量含量可高达约4000kwh。在电熔化催化剂的情况下,熔化所需的能量约为每吨催化剂1000至1500kwh(电)。因此,不仅以固定碳、烃类和硫的形式包含在催化剂中的能量会损耗,而且需要增加大量的电能消耗来进行熔化。
[0042]
因此,相对于现有技术,根据本发明的方法的能量平衡是特别有利的,因为碳、烃类和硫作为燃料被高效使用。事实上,在传统技术中,这些元素在处理(湿法冶金或火法冶金)之前或在单独的后燃烧室中的烟气补充处理中被消除,并且它们的能量被浪费。此外,在后燃烧室中对烟气的这种补充处理需要在后燃烧后实施用于冷却烟气的装置,从而增加天然气(用于后燃烧)和电力(用于冷却)的消耗,同时需要处理过量的气体、通过稀释烟气而大量消耗对烟气进行脱硫的反应物及其中和产率,这也导致了气体、电力、需要消除和运输的废物的消耗。
[0043]
此外,与现有技术中使用的电炉的金属炉渣浇铸孔的插拔技术相比,回转转炉技术允许容易地将反应器翻转过来,炉渣和金属的浇铸阶段更容易和更安全。
附图说明
[0044]
在阅读以下说明和示例以及附图时,本发明的其他目的、特征、方面和优点将更加清楚地显现。
[0045]
图1和图2示意性地说明了根据本发明的方法的步骤b)和c)的实施。
[0046]
图3显示了适用于实施本发明的回转转炉型熔炼炉的示例。
[0047]
以下,除非另有说明,数值范围的限制包括在此范围内,特别是表达式“介于”和
“……
至
……
的范围”中。
[0048]
此外,本说明书中使用的表达“至少一个”和“至少”分别等同于表达“一个或多个”和“大于或等于”。
具体实施方式
[0049]
根据本发明的方法包括第一步骤a),该步骤包括在回转转炉型熔炼炉中制备处于熔化状态的铸铁熔体,该铸铁熔体上方有一层炉渣。
[0050]
可以在熔炼炉中加热铸铁和/或铸铁锭、铁合金的颗粒给料、和/或铸铁和/或钢的金属废料的给料,以此方式使其熔化。
[0051]
一个优选的实施方案涉及从具有尽可能接近于步骤b)中引入的废催化剂原料处理所产生的组分的铸铁熔体开始。事实上,在具有长持续时间(通常为几天)的活动中处理给定类型的催化剂是有利的,这允许在该持续时间内制造具有稳定组分的铁合金。
[0052]
可通过将石灰和氧化铝(例如,催化剂的氧化铝)以相对的比例(例如分别是40重量%和60重量%)加入熔炼炉中来获得炉渣的层。这种氧化铝-石灰化合物因熔点低且特别是具有极强的脱硫作用而闻名,也就是说,它将使硫矿化,而不是将硫留在烟气中。
[0053]
回转转炉是冶金领域中本身已知的一种装置,它由一个加热的反应器组成,其内壁由难熔材料制成,以便支持非常高的温度,并通过电机围绕其对称轴旋转驱动。
[0054]
在步骤a)中加热铸铁熔体的温度通常在1400℃至1650℃的范围内,优选1450℃至1550℃。
[0055]
在第二步骤b)中,将废催化剂引入保持旋转的转炉中,以此方式使废催化剂与浮层的炉渣和处于熔化状态的铸铁熔体接触,从而导致废催化剂的熔化。
[0056]
根据优选的实施例,冶金中通常称为“助熔剂(flux)”的材料,尤其可以选自石灰、铁氧化物、碳酸钠和氟化钙,在这一步骤中也被引入熔炉。
[0057]
同时,在催化剂、炉渣和铸铁的混合物上方,将一种称为氧化气体的含有氧气的气体连续注入熔炼炉内,这会导致从催化剂中释放的碳化合物和/或硫化合物的燃烧或转化,同时归还其燃烧能量。
[0058]
氧化气体可以由氧气、富氧空气或氧气和惰性气体(如氮气)的混合物组成。优选地,氧化气体具有至少30重量%的氧浓度。
[0059]
为了有效地将烃类和气体、特别是从催化剂中释放的一氧化碳(co)和硫化气体转化为能量,氧化气体的注入有利地通过一个或多个气体注入器进行,该气体注入器的轴线基本上平行于铸铁熔体和炉渣熔体,与冶金中其他地方用于穿透金属炉渣熔体的“硬”喷射(“hard”jets)相反,以温和的注入压力产生不穿透金属熔体和炉渣熔体的低推力喷射(或“软”喷射)。
[0060]
实际上,目的不是将氧化气体注入铸铁熔体或炉渣熔体中,而是通过尤其是烃类、固定碳、硫和一氧化碳的燃烧,在熔体和炉渣上方产生热源。这种热量以直接的方式传递给铸铁、炉渣、助熔剂材料和催化剂的给料,并通过转炉的难熔壁通过转炉旋转以间接的方式传递给铸铁、炉渣、助熔剂材料和催化剂的给料。
[0061]
在步骤b)期间,熔炼炉的温度有利地保持在1400℃至1650℃的范围内。
[0062]
在步骤b)期间,存在于铸铁熔体上方的炉渣逐渐富集催化剂的组分,特别是包括难熔氧化物(氧化铝、二氧化硅
……
)、一部分硫和钒(当处理过的废催化剂含有钒时)。可选地,添加的“助熔剂”材料也会最终落入炉渣中,铁氧化物除外,铁氧化物在铁形式的铸铁熔体和炉渣之间被分开。
[0063]
以氧化物形式存在于废催化剂中的选自钼、镍、钴、钨的金属在废催化剂中存在的
碳的存在下被还原,并进入铸铁熔体。例如,就镍而言,还原反应如下:nio c
→
ni co。
[0064]
根据一个实施例,在步骤b)期间,烃类燃料气体也被注入熔炼炉中。该燃料气体优选包含轻质烃类,例如包含1至4个碳原子的烃类。特别优选的燃料气体的示例是天然气。
[0065]
该燃料气体可以与氧化气体一起注入,也就是说,通过相同的注入器,或者通过不同的注入器。
[0066]
当在步骤b)期间引入含很少碳的催化剂时,例如被完全或部分焙烧的催化剂,该实施方案是有利的。事实上,烃类燃料气体的注入允许添加碳化合物的组成,以促进金属氧化物的还原反应。在这种情况下,还优选实施含较高氧浓度的氧化气体。
[0067]
步骤b)在所有废催化剂都已处理时结束,或者当回转转炉已满且如果必要的话,在必要的添加物(例如助熔剂)存在的情况下不能再向其中加入额外的催化剂时结束。
[0068]
在步骤b)之后,该方法包括步骤c),包括通过铸造从熔炼炉中提取步骤b)中形成的炉渣。铸造是以本身已知的方式,以顺序方式进行的。
[0069]
这允许在熔炼炉中回收富含从催化剂中提取的一种或多种金属的铸铁熔体。
[0070]
在排出炉渣(步骤c)之后,步骤(b)然后步骤(c)的顺序可以重复一次或多次,以此方式使熔炼炉中所含的铸铁熔体再次富含金属,必要时重复多次,直到获得具有所需金属浓度的铸铁。在这种情况下,在步骤c)之后,引入废催化剂的步骤b)优选直接进行,优选不在中间冷却铸铁熔体。
[0071]
一旦在铸铁熔体中达到所需的金属浓度,根据本发明的方法可以进一步包括一个或多个处理或精炼铸铁熔体的步骤,优选在回转转炉中进行。
[0072]
特别地,该方法可以进一步包括一个或多个对铸铁熔体进行脱硫和脱磷的步骤,以便将铸铁熔体的硫和磷的浓度降低到通常低于0.1重量%的值。这些处理可以通过向回转转炉中添加石灰和/或包含铁氧化物的碳酸氢钠-碳酸钠溶液来进行。
[0073]
在这些处理操作期间,可以进行一次或多次“除渣”操作,即清空炉渣,直到达到硫和磷的目标浓度。
[0074]
在可选的处理步骤之后,将富含一种或多种金属的铸铁熔体从熔炼炉中浇铸出来,以使其凝固。然后就可以上市了。
[0075]
此外,在步骤c)中从回转转炉中除去的炉渣也被回收。
[0076]
根据第一种备选方案,炉渣以导致其凝固的方式冷却。然后炉渣可以例如以铝酸钙的形式被直接再利用,特别是在其来源的废催化剂不含有钒的情况下。
[0077]
根据第二种备选方案,适用于处理的废催化剂含有钒的情况,在步骤c)中回收的炉渣可以有利地转移到第二熔炼炉中,在第二熔炼炉中处理炉渣以从炉渣中提取钒。根据优选实施例,该第二熔炼炉也是回转转炉。可以通过将颗粒状的铝和/或硅加入炉渣中来提取钒,这一方面可以回收没有钒的炉渣,另一方面,可以回收铁-钒。因此,炉渣可以例如以硅铝酸钙的形式再利用。
[0078]
在根据本发明的方法的步骤b)期间从回转转炉逸出的气体在本身已知的合适的装置中处理。
[0079]
根据优选实施例,该方法实施了用于处理气体的装置,以允许获得低排放标准。
[0080]
在本发明的背景下,用于处理气体的装置可以具有更小的尺寸,特别是包含用于气体后燃烧的腔室,其尺寸相对于电炉中现有技术的装置减小了至少30%,因为所处理的
废催化剂中所含的可燃化合物在回转转炉中得到有效燃烧。
[0081]
此外,本发明允许显著减少用于气体脱硫的反应物的量(例如石灰乳、碳酸氢钠溶液),因为在步骤b)期间通过转炉旋转引起的机械搅拌更好地捕获炉渣中至少30%的硫。
[0082]
根据本发明的方法允许以高效的方式处理在石油精炼和石油化学领域中烃类的处理和/或转化中使用的任何废催化剂。
[0083]
这些催化剂通常是具有小尺寸的固体颗粒的形式,例如球、或多或少的圆柱形颗粒、挤出产品。
[0084]
这些催化剂包括通常由一种或多种难熔无机氧化物组成的多孔载体,在多孔载体上沉积有一种或几种催化活性金属,这些金属可以选自元素周期表的vb、vib、ib、viii和vib族金属。
[0085]
这些催化剂的载体由一种或多种难熔矿物氧化物形成,例如特别是氧化铝、二氧化硅、硅铝、沸石、氧化锆、钛氧化物和硼氧化物以及这些氧化物的混合物。
[0086]
特别地,根据本发明的方法特别适用于处理含有以下金属共生物中的至少一种的废催化剂:como、nimo、nicomo、nimov、niw、nimowco、fecemok。
[0087]
这些催化剂也可能含有废态钒,来自于在催化剂使用周期期间处理的烃类的给料的污染物。
[0088]
如上所述,特别是当它们在原料或脱油状态下处理时,这些催化剂进一步含有碳化合物以及特别是金属硫化物形式的硫,所述碳化合物可以特别是烃类和固定碳的形式。
[0089]
根据一个优选实施方案,在步骤b)中引入的废催化剂处于原料状态,也就是说,它没有经历任何先前的处理。
[0090]
这种催化剂含有硫化物形式的金属以及烃类、硫和固定碳。相对于废催化剂的总重量,烃类的浓度优选为5重量%至20重量%,优选为10重量%至20重量%。
[0091]
根据第二实施方案,在步骤b)中引入的废催化剂处于脱油状态,也就是说,它在温度和气流(可以是氮气、水蒸气和空气)的作用下经历了先前的清洗。
[0092]
这种催化剂含有硫化物形式的金属以及烃类、硫和固定碳。相对于废催化剂的总重量,烃类的浓度优选在0.1重量%至5重量%的范围内。
[0093]
不管实施方案如何,废催化剂含有的固定碳的浓度相对于废催化剂的重量优选为5重量%至20重量%,优选为10重量%至20重量%。
[0094]
图1示意性地说明了步骤b)的实施。
[0095]
该图显示了回转转炉型的熔炼炉1,如箭头f1所示保持旋转。
[0096]
该熔炼炉包含由熔融状态的铸铁熔体3形成的混合物4,在铸铁熔体3上方有一层来自经“助熔剂”处理的废催化剂的熔化的炉渣5。
[0097]
在混合物4的上方,注入器7将充氧的氧化气体注入熔炼炉中,以导致碳化合物和/或硫化合物的燃烧9,其中所述碳化合物和/或硫化合物释放自与炉渣和液态铸铁接触的催化剂(以圆圈6表示)。
[0098]
该注入器可以是例如名为“oxygaz”的燃烧器,根据催化剂提供的碳和烃类的量,供应充氧的氧化气体和可选的烃类燃料气体。应当注意,如有需要,氧化气体中氧的浓度也根据催化剂和燃料气体提供的碳和烃类的量进行调节。
[0099]
优选地,相对于从催化剂释放的碳化合物和/或硫化合物的燃烧以及可选地用燃
烧器注入的气体的燃烧,充氧的氧化气体被过量地注入。
[0100]
待处理的废催化剂通过供应管11被引入熔炼炉1中。管道24允许回收从熔炼炉中释放的烟气。
[0101]
图2显示了从熔炼炉1中取出炉渣5的步骤:熔炼炉停止旋转,通过铸造f2取出炉渣5。
[0102]
在这一铸造步骤中,提取炉渣5的大部分5’,同时在铸铁熔体3上方保留小部分5”的浮层炉渣。
[0103]
图3显示了回转转炉型的传统装置,也称为顶吹回转转炉(或tbrc,top blown rotary converter)。这种装置本身在冶金领域是已知的。
[0104]
熔炼炉1包含难熔材料制成的壁15,该难熔材料耐非常高的温度。可以通过驱动驱动齿轮21的电机组件17绕其对称轴旋转驱动熔炼炉1。
[0105]
电机组件17包括电机20,电机20旋转驱动轴,齿轮19旋转驱动与转炉壳体刚性连接的槽口。
[0106]
胎面14允许将转炉保持在其轴线上。元件22和元件26分别表示位于转炉顶部的静态锥体或盖件以及锁定轮。这些元件本身是已知的。
[0107]
切割线aa下方的图3下部显示了熔炼炉1的内部,其中含有铸铁和炉渣的混合物4。
[0108]“oxygaz”型燃烧器7供应有充氧的氧化气体,其氧气浓度根据废催化剂提供的碳和烃类的量进行调节,允许在混合物4的上方将过量的充氧氧化气体注入熔炼炉1中。如果需要,该装置还允许同时引入烃类燃料气体。待处理的废催化剂与助熔剂化合物一起经由供应管11引入熔炼炉1。管道24允许回收在熔炼炉运行期间从熔炼炉中释放的烟气,并将烟气输送到用于处理烟气的组件(未示出),该烟气大体上包含碳化合物和/或硫化合物燃烧的产物,碳化合物和/或硫化合物释放自与炉渣和液态铸铁接触的催化剂。如果需要,该组件可以包括用于烟气后燃烧的腔室以及用于回收硫的腔室,这本身是已知的。
[0109]
下面的例子是作为本发明的说明给出的,不应以限制本发明范围的方式解释。
[0110]
实施例
[0111]
实施例1:原料催化剂的处理
[0112]
经处理的催化剂为包含镍和钼的常规废催化剂。该催化剂在原料状态下被处理。该催化剂的组成(对于1吨催化剂)如以下表2详细所示:
[0113]
表2
[0114]
[0115][0116]
为了处理该催化剂,使用容量为10吨的回转转炉型熔炼炉。
[0117]
该熔炼炉含有3吨铸铁熔体,其组成与下表3中给出的组成相似,这是由使用相同废催化剂的先前生产顺序产生的。
[0118]
将熔炼炉旋转,将铸铁熔体加热至1500℃,使其熔化。
[0119]
将一批约30吨的上述催化剂逐步引入(通过连续进料,约3吨/小时)旋转熔炼炉中,同时在铸铁熔体上方经由燃烧器将每吨催化剂氧气流速为203nm3的氧气注入,以便允许在与炉渣和铸铁熔体接触的熔化过程中从催化剂释放的化合物(烃类、co、硫化合物)的燃烧。
[0120]
在这一步骤中,在铸铁熔体表面形成的炉渣通过以大约一小时的间隔定期进行的铸造而被清除。
[0121]
在熔炼炉中回收富含金属的铸铁熔体,其组成如以下表3详细描述:
[0122]
表3
[0123]
组成含量(kg)fe120ni21.6mo99c10p0.6s1.3总计252.5
[0124]
而且,所回收的炉渣具有以下表4详细描述的组成:
[0125]
表4
[0126]
[0127][0128]
通过在转炉中进行常规脱硫操作,金属熔体中的硫浓度(0.51重量%)可以降低到0.1重量%的目标值,该操作通过用200kg含cao石灰的脱硫混合物处理铸铁熔体来实现。该处理还允许将金属熔体的磷浓度降低到0.1重量%。这些操作以及脱硫剂和脱磷剂是在铁冶金领域中以常规方式实施的操作。
[0129]
在该实施例中,由从与炉渣和液态铸铁接触的催化剂释放的化合物(烃类、无机碳和硫化合物)的燃烧所提供的能量可以完全满足所述方法步骤b)期间熔炼炉的冶金需求和热损耗。
[0130]
步骤b)的能量平衡如下,以一吨催化剂表示:
[0131]
由化合物燃烧产生的能量输入:2029kwh
[0132]
熔炼炉的能量需求:
[0133]-金属的熔化:96kwh
[0134]-炉渣的熔化:670kwh
[0135]-吸热反应和放热反应的平衡(烃类、固定碳、硫的燃烧,金属氧化物的还原):-193kwh
[0136]-反应器的壁的热损耗:400kwh
[0137]-烟气的能量损耗:1056kwh
[0138]
总需求:2029kwh。
[0139]
实施例2:脱油催化剂的处理
[0140]
通过使用含有镍、钼和钒的常规废催化剂,重复实施例1。该催化剂在脱油状态下被处理,也就是说,在经历了经由水蒸气汽提的操作之后被处理。该催化剂的组成(对于1吨催化剂)如以下表5中详细描述:
[0141]
表5
[0142]
[0143][0144]
该催化剂在与实施例1中使用的相同回转转炉型熔炼炉中处理,容量为10吨。
[0145]
该熔炼炉含有3吨铸铁熔体,其组成接近下表6所示的组成,这是由使用相同废催化剂的先前生产顺序产生的。
[0146]
将熔炼炉旋转,将铸铁熔体加热至1500℃,使其熔化。
[0147]
将一批约20吨的上述催化剂逐步引入(通过连续进料,约3吨/小时)旋转熔炼炉中,同时在铸铁熔体上方经由燃烧器将每吨催化剂氧气流速为114nm3的氧气注入,以便允许在与炉渣和铸铁熔体接触的熔化过程中从催化剂释放的化合物(烃类、co、硫化合物)的燃烧。
[0148]
此外,由50nm3天然气组成的燃料气体与作为氧化剂的100nm3纯氧通过“oxygaz”燃烧器一起添加。
[0149]
以大约一小时的固定时间间隔,通过铸造消除在铸铁熔体表面形成的炉渣。
[0150]
在熔炼炉中回收富含金属的铸铁熔体,其组成如以下表6详细描述。
[0151]
表6
[0152]
组成含量(kg)fe204ni35.7mo33.6v3.4c12.4p2.8s3.3总计295
[0153]
还获得了组成如以下表7详细描述的炉渣。
[0154]
表7
[0155]
组成含量(kg)al2o3433cao284cas116
sio27mgo0moo36v2o5197feo15p2o52总计1060
[0156]
金属熔体的硫浓度(1.1重量%)可以通过在转炉中进行的常规脱硫操作(可选地分几个步骤)降低到0.1重量%的目标值,该脱硫操作通过使用含有石灰(cao)的脱硫混合物来处理铸铁熔体。
[0157]
金属熔体的磷浓度(0.9重量%)然后可以通过在转炉中进行的常规脱磷操作降低到0.1重量%的目标值,该脱磷操作通过用含有石灰、铁氧化物和氧气的混合物来处理铸铁熔体。
[0158]
在该实施例中,由从与液态铸铁接触的催化剂释放的化合物(无机碳和硫化合物)的燃烧提供的能量可以满足所述方法步骤b)期间熔炼炉的大部分(72%)冶金需求和热损耗。
[0159]
步骤b)的能量平衡如下:
[0160]
由化合物燃烧产生的能量输入:1298kwh
[0161]
熔炼炉的能量需求:
[0162]-金属的熔化:111kwh
[0163]-炉渣的熔化:611kwh
[0164]-吸热反应和放热反应的平衡(烃类、固定碳、硫的燃烧,金属氧化物的还原):-116kwh
[0165]-反应器的壁的热损耗:400kwh
[0166]-烟气的能量损耗:792kwh
[0167]
总需求:1798kwh。
[0168]
为了平衡能量平衡,如上所述,需要提供500kwh的燃料气体,燃料气体由50nm3的天然气组成,并通过“oxygaz”燃烧器与作为氧化剂的100nm3纯氧一起添加。
再多了解一些
本文用于创业者技术爱好者查询,仅供学习研究,如用于商业用途,请联系技术所有人。