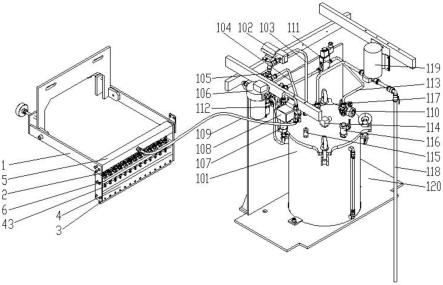
1.本实用新型涉及板栅连续铸造用润滑领域,具体涉及一种用于板栅连续铸造的出油组件及模具润滑系统。
背景技术:
2.板栅是铅酸蓄电池主要组成部件,是铅酸蓄电池极板内起支撑活性物质的栅状结构部件;而连铸板栅是目前新型工艺下所制造的新型板栅;融化的合金铅通过铅泵连续不断的将铅液抽取到转模和定模之间的型腔中,通过转模的转动和冷却,连续拉出网带式的板栅。
3.而由于连续板栅属于快速凝固后就及时拉出,凝固时间短,板栅较软,强度较低,再加上板栅的筋条与型腔粘接,在板栅拉出时,极易造成板栅变形,甚至将板栅筋条拉断,同时还会伴随着板栅毛刺的增多;而未拉出的筋条会残留在动模型腔中,从而造成动模的型腔出现堵塞,影响后续成型过程中铅液的流动和板栅的质量;同时,在生产过程中,由于转模和定模之间具有大约300mpa以上的接触压力,转模和定模之间的转动摩擦很大,模具之间存在较大的磨损,从而使模具使用寿命较低;而铸造过程中,由于铅液的高温以及转模和定模之间的摩擦生热,使得转模和定模的表面温度的较高且波动范围大,会直接导致模具拉伤,甚至导致转模的型腔发生形变,进一步影响定转模和定模的使用寿命以及产品的质量。
4.由于转模各个区域的型腔存在深浅、大小以及结构的差异,因此,转模的各个区域所需润滑油量也存在差异;因此,滴油位置、滴油速率和润滑油油量直接决定着模具的使用寿命和产品质量;然而由于目前均采用气压方式供油,因为气压的不稳定性,不但导致各个预设区域的供油量波动较大,而且也会导致同一区域供油油量波动也较大;再加上,无法精确观察和调整每个区域的滴油油量,进一步加大了对各预设区域供油油量的波动。
5.因此,针对当前的生产工艺和存在的缺陷,需要一种用于板栅连续铸造的出油组件及模具润滑系统,能够具备对预设区域供油油量平稳、各个区域供油流量便于观察和可调的特点,以使得降低板栅连续生产过程中模具由于润滑不佳造成的:板栅的筋条与模具型腔粘连、定模和转模之间转动摩擦导致的模具磨损、以及转模和定模之间摩擦生热导致的接触面温度高且波动范围大等一系列问题。
技术实现要素:
6.有鉴于此,本实用新型的目的是克服现有技术中的缺陷,提供用于板栅连续铸造的出油组件及模具润滑系统,能够具备对预设区域供油油量平稳、各个区域供油流量便于观察和可调的特点,以使得降低板栅连续生产过程中模具由于润滑不佳造成的:板栅的筋条与模具型腔粘连、定模和转模之间转动摩擦导致的模具磨损、以及转模和定模之间摩擦生热导致的接触面温度高且波动范围大等一系列问题。
7.本实用新型的用于板栅连续铸造的出油组件,
8.所述出油组件包括辅助安装架、出油调节阀、浸油件和浸油件安装座;
9.所述出油调节阀通过辅助安装架安装于预设位置ⅰ,所述浸油件通过浸油件安装座安装于辅助安装架,
10.所述浸油件安装座具有供油通道,所述供油通道具有供油通道进油端和供油通道出油端,
11.所述供油通道进油端与出油调节阀的出油口连通,所述供油通道出油端与浸油件的进油口连通,进入浸油件的油以渗出的方式扩散至预设位置ⅱ,
12.所述供油通道具有观察口,所述观察口位于供油通道进油端和供油通道出油端之间,通过所述观察口监测流经供油通道的油的流量,
13.所述出油调节阀通过油阀安装座安装于辅助安装架,所述油阀安装座具有送油油道,所述送油油道具有送油油道进油端和送油油道出油端,
14.所述送油油道进油端用于将油引入至送油油道,所述送油油道出油端与出油调节阀的进油口连通,
15.所述出油调节阀为若干个,若干个所述出油调节阀按照既定的排列方式安装于油阀安装座,所述供油通道与出油调节阀呈一一对应的关系。
16.进一步,所述出油组件还包括排气件,所述排气件设置于浸油件和浸油件安装座之间,所述排气件具有将浸油件中气体导出的排气孔。
17.进一步,所述浸油件安装座高度方向的顶面向上凸出形成上连接部,所述浸油件安装座高度方向的底面向上凹陷形成下连接部,所述供油通道为沿高度方向贯通于上连接部和下连接部的直油道,所述供油通道进油端位于上连接部,所述供油通道出油端位于下连接部;
18.所述观察口为经过供油通道穿设于上连接部开设的通孔,所述通孔的孔径尺寸大于供油通道的孔径尺寸;所述出油调节阀设置于供油通道高度方向的顶部,所述浸油件固定于下连接部;
19.所述出油调节阀具有将油引入至供油通道进油端的油嘴,所述油嘴伸入至供油通道进油端;所述油嘴的出油口暴露于观察口,通过所述出油调节阀的油通过油嘴以滴落的方式导入至浸油件。
20.进一步,所述排气件包括引气部和排气部;
21.所述引气部由排气件顶部沿高度方向向上延伸形成,所述引气部贴合于浸油件外表面被限位在浸油件安装座形成的下连接部内;
22.所述排气部由排气件底部沿高度方向向下延伸出下连接部并朝向背离浸油件设置方向折弯形成;
23.所述排气孔为在高度方向连续的条形孔,所述排气孔高度方向的顶部位于引气部,所述排气孔高度方向的底部位于排气部。
24.进一步,所述浸油件安装座呈沿横向延伸的条形,若干个所述出油调节阀沿横向均布于油阀安装座,浸油件安装座上具有与出油调节阀呈一一对应关系的若干条供油通道;
25.所述浸油件为毛毡,所述毛毡呈固定于下连接部的片状。
26.进一步,所述浸油件安装座通过下连接部的横向侧面与辅助安装架形成固定,所
述油阀安装座的横向侧面与辅助安装架形成固定,
27.所述出油组件还包括位于油阀安装座和浸油件安装座之间的油阀支撑座,所述油阀支撑座的横向侧面与辅助安装架形成固定,所述油阀支撑座形成对若干个所述出油调节阀的支撑。
28.进一步,所述浸油件具有呈齿状的安装端,所述浸油件通过安装端安装至下连接部,齿状所述安装端的齿槽与供油通道呈一一对应关系,在高度方向上所述供油通道出油端位于对应齿槽的正上方。
29.本方案还公开了一种模具润滑系统,包括所述的用于板栅连续铸造的出油组件;
30.还包括供油组件,所述供油组件包括主供油装置和油罐,所述油罐用于储油,所述主供油装置包括供油油泵,所述供油油泵将油罐内的油按照设定的供油量ⅰ通过送油油道进油端泵入至送油油道。
31.进一步,所述供油组件还包括副供油装置,所述副供油装置用于将油罐内的油按照设定的供油量ⅱ通过送油油道进油端导入至送油油道。
32.本实用新型的有益效果是:本实用新型公开的一种用于板栅连续铸造的出油组件及模具润滑系统,通过供油组件和出油组件的布置,具备对预设区域供油油量平稳、各个区域供油流量便于观察和可调的特点,以使得降低板栅连续生产过程中模具由于润滑不佳造成的:板栅的筋条与模具型腔粘连、定模和转模之间转动摩擦导致的模具磨损、以及转模和定模之间摩擦生热导致的接触面温度高且波动范围大等一系列问题;本方案主要用于板栅连铸模具的润滑及板栅的顺利成型和脱模;满足通过供油油泵或者气压两种方式将润滑油平稳的供给转模上方的出油组件;再通过出油组件中的微量调节阀,精确控制单个出油调节阀的滴油量,使毛毡上各个区域的油量适中且均匀,从而使涂刷在连铸转模表面和型腔中的油量均匀;易于板栅脱模,减少板栅变形和断筋等不良品的产生;同时也增加了铅液在转模型腔中的流动,易于板栅铸造成型;此外还增加了定模和转模之间的润滑,降低和平稳转模表面温度,使转模表面温度不会因摩擦生热而导致温度过高,防止模具被拉伤,延长模具使用寿命。
附图说明
33.下面结合附图和实施例对本实用新型作进一步描述:
34.图1为本实用新型的结构示意图;
35.图2为本实用新型出油组件的结构示意图;
36.图3为本实用新型浸油件、浸油件安装座和排气件的爆炸结构示意图;
37.图4为本实用新型图2的主视结构示意图。
具体实施方式
38.图1为本实用新型的结构示意图,如图所示,所述横向即为油阀安装座5长度方向,所述纵向即为油阀安装座5宽度方向,所述高度方向即为油阀安装座5高度方向,在此不再赘述;本实施例中的模具润滑系统包括用于板栅连续铸造的出油组件和供油组件,所述供油组件用于为出油组件供油,所述出油组件用于将油按照既定的方式输送至预设位置ⅱ,其目的在于为模具摩擦面提供润滑介质和对模具摩擦面降温,该摩擦面在本方案中为定模
和转模之间的摩擦面;
39.本实施例中的用于板栅连续铸造的出油组件包括辅助安装架1、出油调节阀2、浸油件3和浸油件安装座4;
40.所述出油调节阀2通过辅助安装架1安装于预设位置ⅰ,所述浸油件3通过浸油件安装座4安装于辅助安装架1;
41.所述辅助安装架1形成对出油调节阀2和浸油件安装座4的支撑安装,辅助安装架1安装于预设位置ⅰ,本方案该预设位置ⅰ位于转模高度方向的正上方,以使得浸油件3位于转模高度方向的正上方,实际使用时浸油件3的位置可根据情况选择布置,以能够对预设位置ⅱ按照既定的方式送油为宜,在此不再赘述,其中转模未在图中示出;
42.所述出油调节阀2通过油阀安装座5安装于辅助安装架1,所述油阀安装座5具有送油油道,所述送油油道具有送油油道进油端和送油油道出油端,所述送油油道进油端用于将油引入至送油油道,所述送油油道出油端与出油调节阀2的进油口连通,如图所示,本方案中油阀安装座5呈沿横向延伸的条状矩形,所述油阀安装座5的横向侧面与辅助安装架1形成固定,本方案中油阀安装座5的横向两侧面分别对应与辅助安装架1形成固定,提高安装强度和使用强度,送油油道即形成于油阀安装座5的内部,并且送油油道除送油油道进油端和送油油道出油端外为封闭式的腔室构造,防止油由送油油道由内向外造成的泄露,供油组件即通过供油管109连通至送油油道进油端,且送油油道进油端有且仅有一个,送油油道出油端数量与出油调节阀2数量呈一一对应关系,该送油油道进油端位于油阀安装座5横向中部,提高供油路径的对称性,满足供油稳定性的需求;
43.所述出油调节阀2选择现有技术中的任一种可控流量的调节阀,达到将油按照既定的方式输送至预设位置ⅱ的目的即可,本方案中出油调节阀2为手动调节阀(微调阀),手动调节阀的进油端与送油油道出油端连通,手动调节阀的出油端连通至供油通道进油端,使用时调节手动调节阀的旋钮控制流经出油调节阀2的出油速率,以达到控制流经出油调节阀2的油的出油量,所述出油调节阀2为若干个,若干个所述出油调节阀2按照既定的排列方式安装于油阀安装座5,该既定的排列方式根据实际生产需求以并排、并列、交错或折弯等方式布置,满足生产结构需求的功能为宜,在此不再赘述,本方案中,所述出油组件还包括位于油阀安装座5和浸油件安装座4之间的油阀支撑座6,所述油阀支撑座6的横向侧面与辅助安装架1形成固定,更进一步的,油阀支撑座6的横向两侧面分别对应与辅助安装架1形成固定,提高安装强度和使用强度,所述油阀支撑座6形成对若干个所述出油调节阀2的支撑,提高出油调节阀2在辅助安装架1上的安装强度,若干个所述出油调节阀2沿横向均布于油阀安装座5,也即每个所述出油调节阀2对应形成一条出油路径,根据生产结构对应位置的需油量不同可随时定点的调整出油调节阀2的出油量,满足节油需求,起到降本增效的目的,所述手动调节阀具备结构简单、操作便捷且安全可靠的特点,同时手动调节阀较为廉价且具备更换便捷的特点,使得其在调节阀选择中经济性更为突出;
44.所述浸油件安装座4具有供油通道,所述供油通道具有供油通道进油端和供油通道出油端,所述供油通道进油端与出油调节阀2的出油口连通,所述供油通道出油端与浸油件3的进油口连通,如图所示,所述浸油件安装座4高度方向的顶面向上凸出形成上连接部41,所述浸油件安装座4高度方向的底面向上凹陷形成下连接部42,所述供油通道为沿高度方向贯通于上连接部41和下连接部42的直油道,起到缩短供油路径提高供油效率的作用,
实际上供油通道还可以是折弯状走向或者弧形走向,以起到连通浸油件3和出油调节阀2的作用,达到将油按照既定的方式输送至预设位置ⅱ的目的即可,在此不再赘述,所述供油通道进油端位于上连接部41,所述供油通道出油端位于下连接部42,所述供油通道与出油调节阀2呈一一对应的关系,所述浸油件安装座4呈沿横向延伸的条形,浸油件安装座4上具有与出油调节阀2呈一一对应关系的若干条供油通道,所述浸油件安装座4通过下连接部42的横向侧面与辅助安装架1形成固定,更进一步的,下连接部42的横向两侧面分别对应与辅助安装架1形成固定,提高安装强度和使用强度;
45.所述供油通道具有观察口43,所述观察口43位于供油通道进油端和供油通道出油端之间,通过所述观察口43监测流经供油通道的油的流量,本方案中所述观察口43数量与供油通道条数呈一一对应的关系,满足观察需求,实际使用时可按照既定的对应关系调整观察口43数量与供油通道条数,在此不再赘述;所述观察口43为经过供油通道穿设于上连接部41开设的通孔,所述观察口43的开设方向平行于纵向,所述通孔的孔径尺寸大于供油通道的孔径尺寸,满足对油滴滴落的直观观察需求,所述观察口43处还可设有现有监测设备的任一种以起到监测油滴流量的目的,在此不再赘述,所述出油调节阀2设置于供油通道高度方向的顶部,所述浸油件3固定于下连接部42;
46.所述出油调节阀2具有将油引入至供油通道进油端的油嘴21,所述油嘴21伸入至供油通道进油端;所述油嘴21的出油口暴露于观察口43,通过所述出油调节阀2的油通过油嘴21以滴落的方式导入至浸油件3,开放式的所述观察口43还可以降低滴油阻力,使得通过油嘴21滴落的油可完全且快速的进入至供油通道,不会产生滴油粘连、挂壁或是带入空气等情况,提升滴油有效性,如图所示,本方案中出油组件的结构布置,使得被供入送油油道的油以由上至下的路径输送至浸油件3,使得重力起到辅助作用,出油调节阀2通过油嘴21的油以滴落的方式落入至供油通道,并通过供油通道渗透至浸油件3,油嘴21中的油在滴落时经过观察口43,以使得能够根据滴油速率判断滴油量,满足对预设位置ⅱ供油的有效输送;
47.进入浸油件3的油以渗出的方式扩散至预设位置ⅱ,所述浸油件3为毛毡,所述预设位置ⅱ为用于连续板栅制造的转模和定模的接触面,如图所示,所述毛毡呈固定于下连接部42的片状,所述浸油件3还可以为棉、麻、布等材质,具有吸油渗油特性即可,所述浸油件3还可以喷射或溅射的方式将油送至预设位置ⅱ,在此不再赘述;毛毡的选择主要因为其富有弹性,粘合性能好,不易松散,组织紧密,孔隙小,耐磨性较好,具有保湿性和防震性能,能够满足对预设位置ⅱ的供油;所述浸油件3具有呈齿状的安装端31,所述浸油件3通过安装端31安装至下连接部42,齿状所述安装端31的齿槽与供油通道呈一一对应关系,在高度方向上所述供油通道出油端位于对应齿槽的正上方;如图所示,齿槽的布置使得能够在此处形成渗油槽,其目的在于将油滴在齿槽内,便于油的吸收和短暂存储,更利于提高供油效果,当然,浸油件3的安装端31还可以为直线型或波浪形,不影响供油目的为宜,在此不再赘述。
48.所述出油组件还包括排气件7,所述排气件7设置于浸油件3和浸油件安装座4之间,所述排气件7具有将浸油件3中气体导出的排气孔71;本方案中,所述排气件7包括引气部和排气部;所述引气部由排气件7顶部沿高度方向向上延伸形成,所述引气部贴合于浸油件3外表面被限位在浸油件安装座4形成的下连接部42内;所述排气部由排气件7底部沿高
度方向向下延伸出下连接部42并朝向背离浸油件3设置方向折弯形成;所述排气孔71为在高度方向连续的条形孔,所述排气孔71高度方向的顶部位于引气部,所述排气孔71高度方向的底部位于排气部,所述排气件7呈在横向延伸的板状,所述排气件的截形呈“l”形,所述排气孔71为沿高度方向延伸的条形孔,所述排气孔71为沿横向布置于排气件7的若干个;如图所示,毛毡和排气件7通过在纵向穿设于下连接部42的螺栓被限位在下连接部42内,且毛毡伸出下连接部42外侧的部分用于对预设位置ⅱ供油浸润;排气件7的部分排气孔71延伸至螺栓穿设排气件7的通孔处,排气孔71的布置使得能够进一步提高毛毡渗油的均匀性,并能保证滴油的顺畅性。
49.所述供油组件包括主供油装置和油罐101,所述油罐101用于储油,所述主供油装置包括供油油泵102,所述供油油泵102将油罐101内的油按照设定的供油量ⅰ通过送油油道进油端泵入至送油油道;供油油泵102的使用能够持续的按照设定的供油量ⅰ对送油油道供给,不受压力变化影响,具备供油油量平稳的特点,能够保证预设位置ⅱ形成均匀的油层;
50.当然所述主供油装置还包括图示中与供油油泵102适配使用的出油管103、回油管104、三通阀105、过滤器106、流量计107、电动阀108和供油管109等配件,出油管103的始端伸入至储油罐101内,出油管103的末端与三通阀105的第一接口连通,供油油泵102设置在出油管103上,回油管104将三通阀105的第二接口和储油罐101连通,三通阀105的第三接口连通至过滤器106的始端,过滤器106的末端连通至流量计107的始端,流量计107的末端与供油管109连通,电动阀108设置在供油管109上,其目的在于提高供油准确性和供油纯度;使用供油油泵102泵送时油从油罐101内经出油管103被泵送至供油管109,通过过滤器106、流量计107和电动阀108等配件完成对送油油道的定量供油,多余的油通过三通阀105连接的回油管104回流至储油罐101;由于本方案对预设位置ⅱ的供油量需严格把控,保证对应功能的同时最大限度的降低油量的使用,现有技术的常规油泵很难达到对应少量的泵送供油,所以本方案设置回油管104收集多余的油来降低油耗,节约生产成本,所述出油管103、回油管104、三通阀105、过滤器106、流量计107、电动阀108和供油管109等配件的功能、使用目的和使用原理为本领域技术人员所知晓的,属于现有技术,在此不再赘述;
51.所述供油组件还包括副供油装置,所述副供油装置用于将油罐101内的油按照设定的供油量ⅱ通过送油油道进油端导入至送油油道;本方案中,所述副供油装置包括调压阀110、电磁阀111和气源三联件112(空气过滤器、减压阀和油雾器)等配件,气源三联件112通过连接管113与调压阀110连通,电磁阀111设置在连接管113上,调压阀110连通至储油罐101;使用调压阀110供油时油从油罐101内经回油管104被压送至供油管109,通过过滤器106、流量计107和电动阀108等配件完成对送油油道的定量供油;所述调压阀110、电磁阀111和气源三联件112等配件的功能、使用目的和使用原理为本领域技术人员所知晓的,属于现有技术,在此不再赘述;也即副供油装置保持原有技术中的压力供油方式,能够按照既定的供油量对预设位置ⅱ供油,使得满足设备的连续生产功能,作为备用供油装置使用,需要注意的是压力供油时需保证油罐101内腔处于封闭状态,满足压力供油的稳定性,提高资源利用率,无需对现有设备进行适应性调整,满足紧凑型的结构需求;实际使用时副供油装置也可以为泵送式供油装置或者其他方式的供油装置,以满足作为备用供油源的使用,满足设备连续生产的功能,在此不再赘述;所述设定的供油量ⅰ和设定的供油量ⅱ以实际使用需求为准,在此不再赘述;
52.当然所述储油罐101还包括图示中的电子液位计114、安全阀115、手动加油口116和自动加油口117等配件,所述自动加油口117与抽油油管118连接,抽油油管118上设有加油油泵119,以使得抽油油管118内的油通过泵送的方式被泵入至油罐101,满足自动化加油需求;所述电子液位计114、安全阀115、手动加油口116、自动加油口117、抽油油管118和加油油泵119等配件的功能、使用目的和使用原理为本领域技术人员所知晓的,属于现有技术,在此不再赘述;
53.本方案还包括对油罐101以及供油组件中各构件安装和支撑的固定支架120。
54.本方案具备供油油量平稳、各个区域流量便于观察和精确可调的特点;不但能使供油油量平稳,而且能清楚的观察和单独调节每个出油调节阀2的油量,能够使转模的表面形成均匀的油层;可以根据不同板栅的结构和生产速度单独调整各个区域的滴油油量,从而使板栅从转模的型腔中脱模均匀,使板栅脱模过程不会出现粘结情况,从而有效的避免了生产过程中发生板栅脱模变形、毛刺和断筋现象,提高了产品的质量和生产效率,而且能够有效降低转模和定模之间的磨损,降低和平稳模具温度,减少模具变形,延长设备的使用寿命;采用了油泵供油方式,有效避免因气压不稳定导致生产过程中供油油量的较大波动,还可以解决了气压方式中中途无法加油的缺陷,同时本方案还兼容了原气压方式,以满足不同工况下的使用,尤其是泵油设备故障时可作为备用供油源使用。
55.更为具体的,本方案主要用于板栅连铸模具的润滑及板栅的顺利成型和脱模;满足通过供油油泵102或者气压两种方式将润滑油平稳的供给转模上方的出油组件;再通过出油组件中的微量调节阀,精确控制单个出油调节阀2的滴油量,使毛毡上各个区域的油量适中且均匀,从而使涂刷在连铸转模表面和型腔中的油量均匀;易于板栅脱模,减少板栅变形和断筋等不良品的产生;同时也增加了铅液在转模型腔中的流动,易于板栅铸造成型;此外还增加了定模和转模之间的润滑,降低和平稳转模表面温度,使转模表面温度不会因摩擦生热而导致温度过高,防止模具被拉伤,延长模具使用寿命。
56.最后说明的是,以上实施例仅用以说明本实用新型的技术方案而非限制,尽管参照较佳实施例对本实用新型进行了详细说明,本领域的普通技术人员应当理解,可以对本实用新型的技术方案进行修改或者等同替换,而不脱离本实用新型技术方案的宗旨和范围,其均应涵盖在本实用新型的权利要求范围当中。
再多了解一些
本文用于创业者技术爱好者查询,仅供学习研究,如用于商业用途,请联系技术所有人。