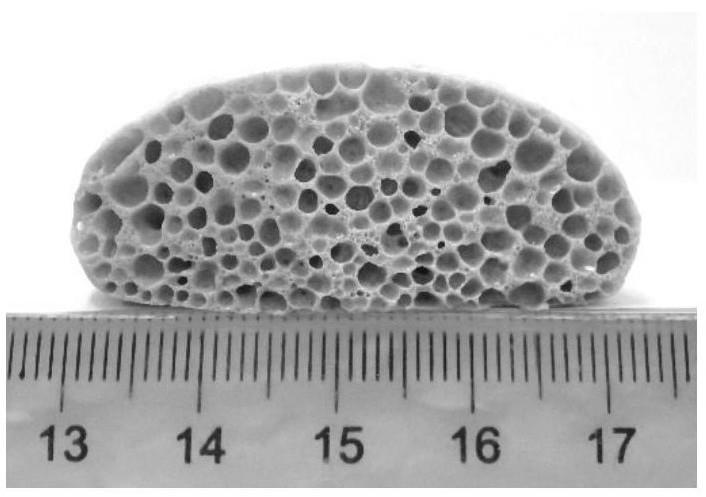
1.本发明属于固废材料资源化处理及陶瓷材料及其制备技术领域,具体涉及一种采用花岗岩废石粉为主要原料制备发泡陶瓷的方法。
背景技术:
2.公开该背景技术部分的信息仅仅旨在增加对本发明的总体背景的理解,而不必然被视为承认或以任何形式暗示该信息构成已经成为本领域一般技术人员所公知的现有技术。
3.花岗岩因其强度高、质地坚硬而被广泛应用于建筑装饰、雕刻材料和地面装饰中,但在花岗岩石材的加工过程中,切割和抛光会产生大量的石粉,造成大气和水土污染,影响人体健康,其堆积也占用了大量的耕地。据统计,花岗岩石材在加工后大约50%成为了固体废弃物,对社会、经济和环境造成了巨大的压力。目前,研究人员已对花岗岩废料的再利用展开了研究,比如cn110328047a公开了一种利用花岗岩石粉制备陶瓷原料的方法,制备过程中要用到隔渣、分级和三段磁选、脱泥处理等多道工序,处理工艺的复杂性提高了处理成本,制约了花岗岩废料的大规模消耗处理;专利cn112573884a公开了利用花岗岩石粉制备高韧性碱矿渣加气混凝土的方法,花岗岩石粉掺量为50%左右,其利用率有待进一步提高。
4.发泡陶瓷是一种具有三维空间网架结构的高气孔率陶瓷材料,具有隔热隔音、防火防潮、良好的机械强度和化学稳定性等优良性能,在隔热隔音、吸波、催化剂载体等方面具有广阔的应用前景。花岗岩废石粉属于硅铝质原料,其矿物组成为长石和石英,该组成特征为利用花岗岩废石粉制备发泡陶瓷提供了可行性。专利cn112759417a公开了一种利用花岗岩石粉为原料制备发泡陶瓷的方法,其中花岗岩石粉掺加量为40%~60%;专利cn109502981a中利用黄金尾矿和花岗岩尾矿制备了发泡陶瓷,花岗岩尾矿用量为12%~39%。上述报道中花岗岩的利用率较低、所制得的发泡陶瓷孔结构均匀性有待提升。而不均匀的孔结构会导致发泡陶瓷材料受压时受力不均匀,导致机械强度下降;不利于导热系数,导致保温隔热能力下降等,限制了发泡陶瓷的应用。因此,大宗利用花岗岩废料制备孔结构均匀、高性能的发泡陶瓷是目前该领域亟需解决的难题。
技术实现要素:
5.为了解决上述问题,本发明提供一种利用花岗岩废石粉制备的发泡陶瓷及其制备方法,通过添加优化剂,实现在较低的烧结温度下花岗岩废石粉的利用率高达90%以上,降低能耗,并有效改善了发泡陶瓷孔结构的均匀性,同时制备方法简单,有利于推广应用。
6.为了实现上述目的,本发明采用如下技术方案:
7.本发明的第一个方面,提供了一种利用花岗岩废石粉制备的发泡陶瓷,由花岗岩废石粉、优化剂和发泡剂组成;
8.其中,优化剂的质量占花岗岩废石粉质量的4%~14%;
9.发泡剂的质量占花岗岩废石粉和优化剂质量总和的0.5%~2%。
10.所述优化剂为碱土金属氧化物/碳酸盐中的一种或几种复配而成,所述发泡剂为碳化硅、碳酸盐、氧化锰、氧化铁中的一种或几种复配而成。
11.本发明所述优化剂通过降低熔体的黏度,使得液相表面张力与气孔膨胀生长力相平衡,制得的发泡陶瓷孔结构饱满、均匀,闭气孔率高,从而具有导热系数低、吸水率低、抗冻性好的特点,均匀的孔结构使得发泡陶瓷承压时受力均匀,并且优化剂的加入使发泡陶瓷孔壁析出晶体,有利于获得高抗压强度,使发泡陶瓷在获得高气孔率的同时具有较好的机械强度。
12.本发明的第二个方面,提供了一种利用花岗岩废石粉制备的发泡陶瓷的制备方法,包括:
13.将花岗岩废石粉球磨、过筛,备用;
14.将花岗岩废石粉、发泡剂、优化剂,球磨混合均匀,得到混合料;
15.将混合料放入模具中,压制坯体;
16.将坯体进行煅烧,即得。
17.本发明的第三个方面,提供了上述的发泡陶瓷在隔热隔音、吸波、催化剂载体领域中的应用。
18.本技术的第四个方面,提供了碱土金属氧化物/碳酸盐在提高花岗岩废石粉基发泡陶瓷孔结构均匀性中的应用。
19.本发明的有益效果
20.(1)本发明添加优化剂,有效降低熔体黏度,使气孔膨胀生长力和液相表面张力达到平衡,发泡顺利进行,实现花岗岩废石粉掺加量达到90%以上。
21.(2)本发明利用优化剂在发泡陶瓷烧结过程中的助熔、稳泡效果来调控孔结构,改善发泡陶瓷孔结构的均匀性,制得的发泡陶瓷孔结构饱满、均匀,闭气孔率高,使其导热系数低,吸水率低,抗冻性好;并且均匀的孔结构使其承压时受力均匀,提高其机械性能,在达到高孔隙率的同时可以获得较好的机械强度。实验结果表明:本发明制得的发泡陶瓷总孔隙率≥76%,闭气孔率≥74.23%,吸水率≤0.54%,抗压强度≥3.21mpa,导热系数≤0.14w/m
·
k。
22.(3)本发明制备方法简单、实用性强,易于推广。
附图说明
23.构成本发明的一部分的说明书附图用来提供对本发明的进一步理解,本发明的示例性实施例及其说明用于解释本发明,并不构成对本发明的不当限定。
24.图1为本发明实施例1所制备的发泡陶瓷的断面照片。
25.图2为本发明实施例2所制备的发泡陶瓷的断面照片。
26.图3为本发明实施例3所制备的发泡陶瓷的断面照片。
27.图4为本发明实施例4所制备的发泡陶瓷的断面照片。
28.图5为本发明实施例5所制备的发泡陶瓷的断面照片。
29.图6为本发明对比例1所制备的发泡陶瓷的断面照片。
具体实施方式
30.应该指出,以下详细说明都是示例性的,旨在对本发明提供进一步的说明。除非另有指明,本发明使用的所有技术和科学术语具有与本发明所属技术领域的普通技术人员通常理解的相同含义。
31.一种利用花岗岩废石粉制备的发泡陶瓷,其原料由基料和辅料组成,以质量百分数计,所述基料为花岗岩废石粉,按100%计;所述辅料为优化剂和发泡剂,辅料中优化剂的质量占基料质量的4%~14%,辅料中发泡剂的质量占基料和优化剂总质量的0.5%~2%。
32.本发明的原理为:
33.本发明利用所添加的优化剂的助熔及稳泡效果,实现对发泡陶瓷孔结构的调控,改善了发泡陶瓷孔结构的均匀性,而发泡陶瓷的性能与孔结构密切相关,从而其性能得到改善。原料花岗岩废石粉的主要构成成分为硅酸盐,优化剂中的碱土金属氧化物/碳酸盐是硅酸盐网络中典型的网络改性剂,碱土金属离子进入到硅酸盐熔体网络间隙中,提供更多的非桥氧离子使桥氧键断裂,离子团被分化,网络断裂程度增加,导致原来的硅氧负离子团被解聚成较简单的结构单位,低聚物浓度升高,流动活化能减小,从而使熔体黏度降低,起到助熔效果,使气体生长过程中的膨胀阻力降低,并且可加速硅酸盐液相中的氧迁移,从而促进发泡剂氧化产生更多气体,气泡内气体压力升高,使气泡的生长驱动力增大,气泡更容易长大。碱土金属氧化物可使熔体的表面张力升高。气泡的生长驱动力增大使气体容易冲破液相包裹,而升高的表面张力则抑制了这一趋势,两者相互作用达到平衡,使得生成的气孔多为封闭气孔,形状饱满,近似于球形。另外,碱土金属氧化物破坏了硅酸盐网络结构的连续性,使得原子重排时质点迁移阻力减小,析晶活化能降低,促进析晶,部分晶体在发泡陶瓷孔壁上析出,提高液膜弹性,起到类似于稳定剂的作用,使气泡稳定,从而获得均匀稳定的孔结构。
34.在一些实施例中,所述优化剂为氧化钙、氧化镁、碳酸钙、碳酸镁中的一种或几种复配而成,所述发泡剂为碳化硅、碳酸盐、氧化锰、氧化铁中的一种或几种复配而成。掺加优化剂后,本发明的发泡陶瓷的孔结构均匀性得到明显改善,获得了形状饱满且独立分布的闭气孔,闭气孔率高,有利于获得良好的隔热性能,极低的显气孔率使产品的吸水率低,有助于获得良好的抗冻性。
35.更进一步地,对上述的多组优化剂和发泡剂的组合进行实验发现:采用氧化钙和碳化硅进行组合时,发泡陶瓷孔结构的均匀性的改善效果更优,闭气孔率更高、隔热性能和抗冻性更好、吸水性更低。
36.在一些实施例中,所述花岗岩废石粉中各化学成分及其所占质量百分比包括:sio
2 66~75%,al2o
3 12~16%,cao 2~4%,na2o 3%~5%,k2o 4%~6%,fe2o
3 1~4%。
37.在一些实施例中,所述花岗岩废石粉的平均粒径为75μm;所述发泡剂的平均粒径为15μm。
38.碱土金属氧化物有助于促进析晶进行,例如:氧化钙与花岗岩石粉中的sio2成分反应生成硅灰石,硅灰石晶体在孔壁上析出,发泡陶瓷发泡过程中,由液相包裹的气体形成的孔隙在气液界面具有气膜、界面电阻膜和液膜,沉淀晶体起到稳定剂的作用,可以增加孔隙液膜的弹性,降低液膜的流动性,从而改善界面性质,有助于保持孔隙稳定,并且晶相量
的增加有助于提高陶瓷基体的强度,孔结构的改善使发泡陶瓷承压时受力均匀,也有利于强度提高,因此在获得高孔隙率的同时,发泡陶瓷的整体抗压强度也较高。
39.本发明还提供一种利用花岗岩石粉制备的发泡陶瓷的制备方法,包括如下制备步骤:
40.(1)将花岗岩废石粉球磨、过200目筛,备用;
41.(2)将各原料按配比称取,各原料所占质量百分数包括:花岗岩废石粉按100%计,优化剂占花岗岩废石粉质量的4%~14%,发泡剂占花岗岩废石粉和优化剂质量总和的0.5%~2%,球磨混合均匀,得到混合料;
42.(3)将混合料放入模具中,压制坯体;
43.(4)将坯体放入高温炉中按照预设烧成制度煅烧,得到发泡陶瓷成品。
44.在一些实施例中,所述烧成制度为:以5℃/min~10℃/min的升温速率升温到1110℃~1150℃的烧成温度,在烧成温度保温30~60min。
45.下面结合具体的实施例,对本发明做进一步的详细说明,应该指出,所述具体实施例是对本发明的解释而不是限定。
46.以下实施例中,采用的花岗岩废石粉的组分及其各组分所占质量百分数如下:
[0047][0048]
实施例1
[0049]
本实施例利用花岗岩石粉制备发泡陶瓷,其制备方法包括以下步骤:
[0050]
(1)将花岗岩废石粉球磨,过200目筛,备用;
[0051]
(2)将各原料按配比称取,各原料所占质量百分数包括:花岗岩废石粉按100%计,氧化钙作为优化剂,总质量占花岗岩废石粉质量的8%,碳化硅作为发泡剂,占花岗岩废石粉与氧化钙质量总和的1%,球磨混合均匀,得到混合料。
[0052]
(3)将混合料放入模具中,压制成直径为3cm,高度约4cm的坯体;
[0053]
(4)将坯体放入高温炉中煅烧,得到发泡陶瓷成品;具体的烧成制度为:以5℃/min的升温速率升温至1130℃保温30min,然后随炉冷却至室温。
[0054]
本实施例制备的花岗岩废石粉发泡陶瓷,气孔饱满,孔结构均匀,其体积密度为581kg/m3,总孔隙率为81.55%,闭气孔率为79.55%,抗压强度为4.2mpa,吸水率为0.48%,导热系数为0.14w/m
·
k。
[0055]
实施例2
[0056]
本实施例利用花岗岩石粉制备发泡陶瓷,其制备方法包括以下步骤:
[0057]
(1)将花岗岩废石粉球磨,过200目筛,备用;
[0058]
(2)将各原料按配比称取,各原料所占质量百分数包括:花岗岩废石粉按100%计,氧化钙占花岗岩废石粉质量的4%,碳化硅占花岗岩废石粉和氧化钙质量总和的1%,球磨混合均匀,得到混合料;
[0059]
(3)将混合料放入模具中,压制成直径为3cm,高度约4cm的坯体;
[0060]
(4)将坯体放入高温炉中煅烧,得到发泡陶瓷成品;具体的烧成制度为:以7℃/min
的升温速率升温至1130℃保温60min,然后随炉冷却至室温。
[0061]
本实施例制备的花岗岩废石粉发泡陶瓷,气孔饱满,孔结构均匀,其体积密度为557kg/m3,总孔隙率为83.12%,闭气孔率为81.21%,抗压强度为3.97mpa,吸水率为0.36%。
[0062]
实施例3
[0063]
本实施例利用花岗岩石粉制备发泡陶瓷,其制备方法包括以下步骤:
[0064]
(1)将花岗岩废石粉球磨,过200目筛,备用;
[0065]
(2)将各原料按配比称取,各原料所占质量百分数包括:花岗岩废石粉按100%计,氧化钙占花岗岩废石粉质量的4%,碳化硅占花岗岩废石粉和氧化钙质量总和的2%,球磨混合均匀,得到混合料;
[0066]
(3)将混合料放入模具中,压制成直径为3cm,高度约4cm的坯体;
[0067]
(4)将坯体放入高温炉中煅烧,得到发泡陶瓷成品;具体的烧成制度为:以5℃/min的升温速率升温至1150℃保温30min,然后随炉冷却至室温。
[0068]
本实施例制备的花岗岩废石粉发泡陶瓷,其体积密度为534kg/m3,总孔隙率为83.69%,闭气孔率为81.23%,抗压强度为3.21mpa,吸水率为0.54%。
[0069]
实施例4
[0070]
本实施例利用花岗岩石粉制备发泡陶瓷,其制备方法包括以下步骤:
[0071]
(1)将花岗岩废石粉球磨,过200目筛,备用;
[0072]
(2)将各原料按配比称取,各原料所占质量百分数包括:花岗岩废石粉按100%计,氧化钙占花岗岩废石粉质量的14%,碳化硅占花岗岩废石粉和氧化钙质量总和的1%,球磨混合均匀,得到混合料;
[0073]
(3)将混合料放入模具中,压制成直径为3cm,高度约4cm的坯体;
[0074]
(4)将坯体放入高温炉中煅烧,得到发泡陶瓷成品;具体的烧成制度为:以10℃/min的升温速率升温至1110℃保温30min,然后随炉冷却至室温。
[0075]
本实施例制备的花岗岩废石粉发泡陶瓷,其体积密度为610kg/m3,总孔隙率为76.22%,闭气孔率为74.62%,抗压强度为5.01mpa,吸水率为0.28%。
[0076]
实施例5
[0077]
本实施例利用花岗岩石粉制备发泡陶瓷,其制备方法包括以下步骤:
[0078]
(1)将花岗岩废石粉球磨,过200目筛,备用;
[0079]
(2)将各原料按配比称取,各原料所占质量百分数包括:花岗岩废石粉按100%计,氧化钙占花岗岩废石粉质量的10%,碳化硅占花岗岩废石粉和氧化钙质量总和的0.5%,球磨混合均匀,得到混合料;
[0080]
(3)将混合料放入模具中,压制成直径为3cm,高度约4cm的坯体;
[0081]
(4)将坯体放入高温炉中煅烧,得到发泡陶瓷成品;具体的烧成制度为:以5℃/min的升温速率升温至1130℃保温30min,然后随炉冷却至室温。
[0082]
本实施例制备的花岗岩废石粉发泡陶瓷,其体积密度为631kg/m3,总孔隙率为75.33%,闭气孔率为74.23%,抗压强度为5.63mpa,吸水率为0.18%。
[0083]
对比例1
[0084]
本实施例利用花岗岩石粉制备发泡陶瓷,其制备方法包括以下步骤:
[0085]
(1)将花岗岩废石粉球磨,过200目筛,备用;
[0086]
(2)将各原料按配比称取,各原料所占质量百分数包括:花岗岩废石粉按100%计,碳化硅占花岗岩废石粉质量的1%,球磨混合均匀,得到混合料;
[0087]
(3)将混合料放入模具中,压制成直径为3cm,高度约4cm的坯体;
[0088]
(4)将坯体放入高温炉中煅烧,得到发泡陶瓷成品;具体的烧成制度为:以5℃/min的升温速率升温至1130℃保温30min,然后随炉冷却至室温。
[0089]
本对比例未额外添加优化剂,所得发泡陶瓷发泡不充分,许多区域未发泡,结构趋于致密化,不能作为发泡陶瓷加以应用。
[0090]
以上所述仅为本发明的优选实施例而已,并不用于限制本发明,对于本领域的技术人员来说,本发明可以有各种更改和变化。凡在本发明的精神和原则之内,所作的任何修改、等同替换、改进等,均应包含在本发明的保护范围之内。
再多了解一些
本文用于创业者技术爱好者查询,仅供学习研究,如用于商业用途,请联系技术所有人。