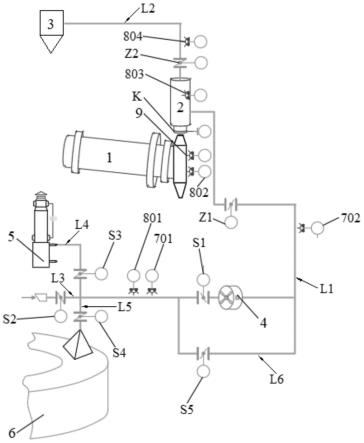
1.本发明涉及含湿烟气的防结露除尘系统和工艺,具体涉及一种智能控制抗结露型饱和湿烟气混流系统及方法,属于烟气除尘技术领域。
背景技术:
2.一次混合机中生石灰消化过程是其加水后与水发生剧烈放热反应的过程,其反应方程式为:
3.cao h2o=ca(oh)2 6489.15j
4.生石灰消化后生成的消石灰ca(oh)2颗粒,进一步吸水后在空气中与co2反应生成caco3沉淀,大量的caco3沉淀易形成硬垢而板结。因此烧结一次混合机烟气具有以下特点:(1)烟气中含湿量较高;(2)烟气中粉尘的粘附性较强,易粘附于排气筒内壁、管道及设备等处;(3)烟气中生石灰含量较高(占粉尘重量的30%以上);(4)烟气温度高于环境温度,容易结露,尤其在冬季;(5)烟气中粉尘浓度超标且波动范围较大,即使较低水平也远超国标要求的10mg/nm3限值。
5.生石灰消化后产生的饱和湿烟气温度高于环境温度,露点温度高,在管道中输送的过程中如温度降低太快极易引起结露,烟气凝结析出的水分又与未反应的生石灰发生化学放热反应,产生的caco3物质在管道内壁沉积后,将造成管道内壁结垢堵塞,影响除尘效果。
6.现有控制烟气露点的方式及其弊端如下所述:
7.(1)采用混合热风来防止管道结垢。该方式通过设置支管引入一股热风汇入除尘管道,理论上计算的混合温度能够保证控制露点温度,且热风直接加热饱和湿烟气,加热效果好,但是因其在实际运用的过程中无法保证热源的温度,且汇入热风的初期,烟气仍可能处于露点温度以下,久而久之,管道内壁堵塞的问题无法彻底解决。
8.(2)采用电伴热的方式来加热含湿烟气。在管道外侧设置电伴热带,通过电能加热除尘管道外壁,通过金属热传导的作用将热量传导至除尘管道内壁加热湿烟气。该方式能量消耗大,且热能经过几次热传导后存在一定的热量消耗,湿烟气的加热需要一个过程,因此,管道堵塞的问题只能缓解,仍不能彻底解决。
9.(3)采用蒸汽伴热的方式加热含湿烟气。该方式的防结露原理同(2),其优点是利用了工业厂区的多余的蒸汽资源,缺点除了同第二种方式一样需要多次导热外,因蒸汽管道为压力管道,其制作、施工要求高,蒸汽管道导热用的导热泥不便于采购等因素,这种防结露方式一直无法大规模推广使用。
10.因此,现有装置或工艺未能很好地解决饱和湿烟气在除尘系统中结露、管道堵塞的问题。
技术实现要素:
11.针对上述现有技术中的不足,本发明提出一种智能控制防结露型饱和湿烟气混流
系统。该系统引入了混流筒,将混流筒设置在混合机排气端的上方,并通过气动阀连接,混流筒的下游通过除尘管道连接至除尘器。向混流筒内通入热介质,待混流筒内的温度上升至混合机中含湿烟气露点温度以上,此时混合机内的含湿烟气进入混流筒,从而能够避免现有技术中在热风汇入初期含湿烟气仍然可能结露堵塞管道的问题,进而确保混合烟气进入除尘器的温度全程均在烟气露点温度以上。
12.基于上述混流系统,本发明还提出了一种智能控制抗结露型饱和湿烟气混流方法。该方法基于混合机中含湿烟气的状态参数确定含湿烟气的露点温度,待混流筒内含湿烟气与热介质的混合烟气的温度高于含湿烟气的露点温度,混合烟气进入除尘器进行除尘处理。采用本发明混流方法能够有效控制烟气进入除尘器的温度,避免现有技术中在热风汇入初期烟气仍处于露点温度以下的问题,即能够彻底解决含湿烟气结露堵塞管道内壁的问题,确保系统长期稳定运行。
13.根据本发明的第一种实施方案,提供一种智能控制防结露型饱和湿烟气混流系统。
14.一种智能控制防结露型饱和湿烟气混流系统,该系统包括混合机、混流筒、除尘器。所述混流筒设置在混合机排气端的上方,混合机的排气口通过气动阀与混流筒的烟气入口连接。热介质输送管道连接至混流筒的热介质入口。混流筒的烟气出口经由除尘管道连接至除尘器。
15.在本发明中,该系统还包括气体输送管道。所述气体输送管道连接至热介质输送管道的输入端。
16.作为优选,热介质输送管道上设有第一开关阀和增压风机。优选,气体输送管道上设有第二开关阀。
17.在本发明中,该系统还包括预热器。所述预热器经由第一供热管道连接至热介质输送管道的输入端。作为优选,第一供热管道上设有第三开关阀。优选,所述预热器为热风炉。
18.在本发明中,该系统还包括生产余热装置。所述生产余热装置经由第二供热管道连接至热介质输送管道的输入端。作为优选,第二供热管道上设有第四开关阀。
19.在本发明中,从热介质输送管道上分出旁路管道,旁路管道绕过第一开关阀和增压风机后合并至热介质输送管道。优选,旁路管道上设有第五开关阀。
20.作为优选,热介质输送管道上设有第一压力传感器和第二压力传感器。其中,第一压力传感器位于热介质输送管道上分出旁路管道位置的上游。第二压力传感器位于旁路管道合并至热介质输送管道位置的下游。
21.在本发明中,热介质输送管道上设有第一温度传感器。第一温度传感器位于热介质输送管道上分出旁路管道位置的上游。混合机上设有第二温度传感器和湿度传感器。混流筒上设有第三温度传感器。除尘管道上设有第四温度传感器。
22.作为优选,热介质输送管道上设有第一调节阀。第一调节阀位于旁路管道合并至热介质输送管道位置的下游。除尘管道上设有第二调节阀。
23.作为优选,该系统包括n个混合机。每个混合机的排气端上方均对应设置一个混流筒。各混合机与混流筒之间均通过气动阀连接。在旁路管道合并至热介质输送管道位置的下游,所述热介质输送管道分出n根热介质支管分别连接至n个混流筒的热介质入口。各混
流筒的烟气出口分别通过各自的除尘管道连接至除尘器。优选,n的取值为1-10,优选为2-6。
24.优选的是,每个混合机上均设有第二温度传感器和湿度传感器。每个混流筒上均设有第三温度传感器。每个混流筒各自连接的除尘管道上均设有第四温度传感器和第二调节阀。每根热介质支管上均设有第一调节阀。
25.作为优选,每个混流筒各自连接的除尘管道在合并后经由除尘总管连接至除尘器。优选,除尘总管上设有第五温度传感器。
26.在本发明中,该系统还包括控制装置。所述控制装置与气动阀、第一开关阀、第二开关阀、第三开关阀、第四开关阀、第五开关阀、第一压力传感器、第二压力传感器、第一温度传感器、第二温度传感器、第三温度传感器、第四温度传感器、第五温度传感器、湿度传感器、第一调节阀、第二调节阀连接,并控制各阀门和各传感器的操作。
27.根据本发明的第二种实施方案,提供一种智能控制防结露型饱和湿烟气混流方法。
28.一种智能控制防结露型饱和湿烟气混流方法或使用第一种实施方案中所述系统的混流方法,该方法包括以下步骤:
29.1)确定混合机中含湿烟气的露点温度。
30.2)通过热介质输送管道向混流筒内通入热介质,待混流筒内的温度高于步骤1)中所述含湿烟气的露点温度,此时打开气动阀,混合机中的含湿烟气进入混流筒。
31.3)含湿烟气与热介质在混流筒内混合,得到混合烟气,待混合烟气的温度高于步骤1)中所述含湿烟气的露点温度,此时混合烟气通过除尘管道进入除尘器进行除尘处理。
32.根据本发明的第三种实施方案,提供一种智能控制防结露型饱和湿烟气混流方法。
33.一种智能控制防结露型饱和湿烟气混流方法或使用第一种实施方案中所述系统的混流方法,该方法包括以下步骤:
34.1)确定n个混合机中含湿烟气的露点温度。
35.2)通过热介质输送管道分出的热介质支管分别向各混流筒内通入热介质,待各混流筒内的温度高于对应混合机中含湿烟气的露点温度,此时打开气动阀,各混合机中的含湿烟气进入对应的混流筒。
36.3)含湿烟气与热介质在各混流筒内混合,得到混合烟气,待各混流筒内混合烟气的温度高于对应混合机中含湿烟气的露点温度,此时各混流筒内的混合烟气通过各自的除尘管道合并至除尘总管后进入除尘器进行除尘处理。
37.在本发明中,步骤2)中还包括检测清灰的步骤,具体为:在向混流筒内通入热介质之前,先采用第一压力传感器和第二压力传感器对热介质输送管道上的压力进行检测。若压力检测异常,则启动系统清灰程序,此时外界空气通过增压风机引入气体输送管道和热介质输送管道,外界空气对热介质输送管道及混流筒进行反吹清扫。直至第一压力传感器和第二压力传感器检测压力恢复正常,结束系统清灰程序。
38.在本发明中,步骤2)中所述向混流筒内通入热介质,具体为:在系统运行之初,通过预热器为热介质输送管道提供热介质。当工艺生产状态稳定,生产余热装置可提供有效余热,此时通过生产余热装置为热介质输送管道提供热介质。
39.在本发明中,步骤1)中所述确定混合机中含湿烟气的露点温度,具体包括以下子步骤:
40.①
收集工程中大量含湿烟气的湿度、温度数据,通过焓湿图(即将湿空气各种参数之间的关系用图线表示,可查阅应用)获得相应工况条件下的烟气露点温度,建立烟气露点温度数据库。
41.②
采用湿度传感器和第二温度传感器分别测量混合机中含湿烟气的湿度和温度,从烟气露点温度数据库中获取对应混合机中含湿烟气的露点温度。
42.在本发明中,计算步骤2)中需要向混流筒内通入热介质的量,具体包括以下子步骤:
43.a)计算预热混合机中的含湿烟气所需热量:
44.混合机中含湿烟气的量为v
烟
,m3/h。检测含湿烟气的温度为t
烟
,℃。烟气露点温度为t0,℃。设定含湿烟气与热介质混合后得到的混合烟气的温度为t
设
,℃。t
设
=t0 (5~30)℃。由此,预热混合机中的含湿烟气所需要吸收的热量q
烟
为:
45.q
烟
=c
烟v烟
ρδt
烟
=c
烟v烟
ρ
烟
(t
设-t
烟
)。
46.式中:c
烟
为含湿烟气的比热容,kj/(kg
·
℃)。ρ
烟
为含湿烟气的密度,kg/m3。
47.b)计算进入混流筒的热介质所释放的热量:
48.设进入混流筒的热介质的量为v
热
,m3/h。检测热介质的温度为t
热
,℃。由此,进入混流筒的热介质所释放的热量q
热
为:
49.q
热
=c
热v热
ρδt
热
=c
热v热
ρ
热
(t
热-t
设
)。
50.式中:c
热
为热介质的比热容,kj/(kg
·
℃)。ρ
热
为热介质的密度,kg/m3。
51.c)由预热含湿烟气所需要吸收的热量q
烟
与进入混流筒的热介质所释放的热量q
热
相等,可得:
52.c
烟v烟
ρ
烟
(t
设-t
烟
)=c
热v热
ρ
热
(t
热-t
设
)。
53.即得:
[0054]v热
=c
烟v烟
ρ
烟
(t
设-t
烟
)/[c
热
ρ
热
(t
热-t
设
)]。
[0055]
调节热介质输送管道上或热介质输送管道分出的热介质支管上的第一调节阀的开度,使得步骤2)中混流筒内通入的热介质的量为v
热
。
[0056]
作为优选,在步骤3)中,调节除尘管道上第二调节阀的开度,使得各除尘点的风量满足要求,各除尘点无粉尘外逸的现象。同时,第四温度传感器在线检测除尘管道上混合烟气的温度t,并调节热介质输送管道上或热介质支管上的第一调节阀的开度,使得t等于t
设
。
[0057]
针对现有技术中烧结一次混合机烟气由于含湿量高、粉尘浓度高,因而混合机烟气在除尘降温过程中容易结露堵塞管道的问题,本发明提出了一种智能控制防结露型饱和湿烟气混流系统。该混流系统包括混合机、混流筒和除尘器。所述混流筒设置在混合机排气端的上方,混合机的排气口位置设有气动阀,即混合机的排气口通过气动阀与混流筒的烟气入口连接。热介质输送管道连接至混流筒的热介质入口,即热介质输送管道为混流筒的预热及混合机中含湿烟气的加热提供热介质。除尘器设置在混流筒的下游,混流筒的烟气出口通过除尘管道连接至除尘器。在实际运用过程中,向混流筒内通入热介质,待混流筒内的温度上升至混合机中含湿烟气露点温度以上,此时气动阀开启,混合机内的含湿烟气进入混流筒,从而能够避免现有技术中在热风汇入初期含湿烟气仍然可能结露堵塞管道的问
题,进而确保混合烟气进入除尘器的温度全程均在烟气露点温度以上。
[0058]
作为优选,本发明还包括气体输送管道,所述气体输送管道与热介质输送管道的输入端连接。热介质输送管道上还设有增压风机。通过压力传感器(包括第一压力传感器和第二压力传感器)对热介质输送管道上的压力进行检测,从而判断热介质输送管道与混流筒内是否处于积灰状态。若压力检测异常,则启动系统清灰程序,外界空气引入气体输送管道内并通过增压风机增压,外界空气依次对热介质输送管道和混流筒进行反吹清扫,从而避免管道积灰堵塞,使系统长期稳定运行。
[0059]
在本发明中,所述混流系统还包括预热器和生产余热装置。所述预热器和生产余热装置分别经由第一供热管道和第二供热管道连接至热介质输送管道的输入端。在系统运行之初,通过预热器为热介质输送管道提供热介质。其中,预热器可以选择热风炉。当工艺生产状态稳定,生产余热装置能够提供有效热源,此时预热器停止运行,采用生产余热装置为热介质输送管道提供热介质。其中,生产余热装置所提供的工艺余热不对具体工艺进行限制,例如可以是烧结工艺过程中产生的余热,也可以是玻璃煅烧、球团生产等工艺过程中产生的余热。本发明采用预热器作为备用热源,当判断生产工艺中有余热可利用(可通过设置在热源处的热电阻测量值进行判断,经过一段时间运行后,后期可按照时间来控制),即可优先利用工艺生产过程中产生的余热,实现能源梯级利用,节约能源。此外,热介质输送管道上设置的增压风机除了给清灰用的外界空气进行增压,还可作为备用动力源,避免因热介质输送管道阻力过大引起的压力不平衡现象,使热介质的引入更加稳定,也有利于后续对除尘烟气温度的稳定。
[0060]
作为优选,本发明从热介质输送管道上分出旁路管道,旁路管道绕过增压风机后合并至热介质输送管道。当热介质输送管道阻力较小、热介质的引入较为稳定时,此时热介质可通过旁路管道输送至混流筒,而无需经过增压风机所在的管道位置。
[0061]
在本发明中,热介质输送管道上设有第一压力传感器和第二压力传感器。其中,第一压力传感器位于热介质输送管道上分出旁路管道位置的上游。第二压力传感器位于旁路管道合并至热介质输送管道位置的下游。第一压力传感器和第二压力传感器用于对热介质输送管道上的压力进行检测,从而判断热介质输送管道与混流筒内是否处于积灰状态,是否需要启动系统清灰程序。一般来说,在管道无积灰的正常工况下,热介质输送管道内的压力范围为-100pa~0pa。管道内压力情况的具体检测判断与压力测点的位置有关,例如,本技术中当第一压力传感器与第二压力传感器所检测到的压差(压力差)大于100pa时即可判断热介质输送管道内压力异常,即管道或混流筒内存在积灰,需启动系统清灰程序,以避免进一步沉降。
[0062]
本发明在热介质输送管道上设有第一温度传感器。第一温度传感器位于热介质输送管道上分出旁路管道位置的上游。第一温度传感器用于检测热介质的温度。混合机上设有第二温度传感器和湿度传感器。第二温度传感器用于检测混合机中含湿烟气的温度,湿度传感器用于检测混合机中含湿烟气的湿度。混流筒上设有第三温度传感器。第三温度传感器用于实时监测混流筒内的温度,一方面通过实时监测能够准确判断混合机中含湿烟气进入混流筒的时间节点,另一方面能够确保含湿烟气与热介质混合后得到的混合气体温度达到烟气露点温度以上再进入除尘器进行处理。除尘管道上设有第四温度传感器。第四温度传感器在线检测除尘管道上混合烟气的温度,进一步确保进入除尘器的烟气温度在烟气
露点温度以上,从而彻底解决现有技术中烧结一次混合机含湿烟气在除尘过程中容易结露堵塞管道内壁的问题。
[0063]
作为优选,本发明在热介质输送管道上设有第一调节阀。第一调节阀位于旁路管道合并至热介质输送管道位置的下游。第一调节阀用于调节通过热介质输送管道进入混流筒的热介质的量。除尘管道上设有第二调节阀。第二调节阀用于调节除尘管道上的风量(或烟气量),使得除尘点的风量满足要求,即除尘点无粉尘外逸的现象。
[0064]
作为优选方案,本发明所述的混流系统包括n个混合机。每个混合机的排气端上方均对应设置一个混流筒。各混合机与混流筒之间均通过气动阀连接。在旁路管道合并至热介质输送管道位置的下游,所述热介质输送管道分出n根热介质支管分别连接至n个混流筒的热介质入口。各混流筒的烟气出口分别通过各自的除尘管道连接至除尘器。其中,n的取值为1-10,优选为2-6,例如n=3,n=4,或n=6。
[0065]
当混流系统中包括多个混合机时,相应的,每个混合机上均设有第二温度传感器和湿度传感器。每个混流筒上均设有第三温度传感器。每个混流筒各自连接的除尘管道上均设有第四温度传感器和第二调节阀。每根热介质支管上均设有第一调节阀。此时,各热介质支管上的第一调节阀用于调节进入对应混流筒的热介质的量。第二调节阀用于调节与对应混流筒相连接的除尘管道上的风量(或烟气量),进而来平衡各除尘点的阻力,使得各除尘点的风量满足要求,即各除尘点无粉尘外逸的现象。在本技术中,可通过现场观察或设置相应的粉尘浓度检测仪对各除尘点(例如各混合机)的粉尘浓度进行实时监测,从而确保相应除尘点无粉尘外逸现象。第二调节阀用于平衡系统阻力,当第二调节阀的开度设定完成后一般可不做调整,只在出现扬尘情况时进行按需调整即可。
[0066]
优选,每个混流筒各自连接的除尘管道在合并后经由除尘总管连接至除尘器。为进一步确保进入除尘器的混合烟气温度在露点温度以上,除尘总管上设有第五温度传感器,以保证系统稳定运行。基于此,本技术所述的混流系统能够同时对多个混合机的含湿烟气进行处理,并确保进入除尘器的烟气温度在烟气露点温度以上,即能够彻底解决含湿烟气结露堵塞除尘管道的问题,确保系统长期稳定运行。
[0067]
进一步优选,本发明所述混流系统还包括控制装置。所述控制装置与气动阀、第一开关阀、第二开关阀、第三开关阀、第四开关阀、第五开关阀、第一压力传感器、第二压力传感器、第一温度传感器、第二温度传感器、第三温度传感器、第四温度传感器、第五温度传感器、湿度传感器、第一调节阀、第二调节阀连接,并控制各阀门和各传感器的操作。即本技术将各检测点的检测信号接入控制装置进行分析/反馈,并在控制装置中显示饱和湿烟气混流系统的运行状态,从而实现混流系统的智能控制。
[0068]
基于前述智能控制抗结露型饱和湿烟气混流系统,本发明还提出了一种智能控制抗结露型饱和湿烟气混流方法。所述混流方法主要包括确定混合机中含湿烟气的露点温度、判断含湿烟气进入混流筒的时间节点、判断含湿烟气与热介质的混合烟气进入除尘器的时间节点并进行除尘处理等步骤。首先,通过大量的工程实测数据建立烟气露点数据库,获取混合机中含湿烟气的湿度和温度,分析比对得出该混合机中含湿烟气的露点温度。然后,通过热介质输送管道(或热介质输送管道分出的热介质支管)向混流筒内通入热介质,待混流筒内的温度高于对应混合机中含湿烟气的露点温度,此时打开气动阀,混合机中的含湿烟气进入混流筒。含湿烟气与热介质在混流筒内混合,得到混合烟气,待混合烟气的温
度高于对应混合机中含湿烟气的露点温度,此时混合烟气通过除尘管道进入除尘器进行除尘处理。其中,需要向混流筒内通入的热介质的量,可以通过热平衡进行计算。本技术可设定在系统运行中控制混流筒内混合烟气的温度高于含湿烟气露点温度10℃以上,保证混合烟气在除尘过程中不冷凝结露。同时,本技术还可根据含湿烟气露点温度及控制混合烟气温度在露点温度以上而计算最小热介质量,即热介质所提供的热量仅使得混合烟气的温度达到在除尘过程中不冷凝结露即可,而不需要多余的热量,从而降低能耗。
[0069]
在实际运用过程中,本发明所述智能控制混流方法的控制流程如图4所示。首先,通过第一压力传感器和第二压力传感器对热介质输送管道进行压力检测,若压力检测异常则启动管道清灰程序。开启第一开关阀、第二开关阀,此时室外空气引入气体输送管道和热介质输送管道内并通过增压风机增压,空气依次经过热介质输送管道和各混流筒,直至热介质输送管道压力信号恢复正常,即各混流筒清灰全部完成。接着热风炉(即预热器)运行,第三开关阀、第五开关阀开启,同时第一开关阀、第二开关阀关闭,系统引入热风炉提供的热风。通过设置在各混合机上的湿度传感器和温度传感器测量烟气状态参数,将所测得的含湿烟气的湿度和温度传入烟气露点温度数据库进行分析,确定对应混合机中含湿烟气的露点温度。待各混流筒上的第三温度传感器检测到混流筒内的温度达到对应混合机中含湿烟气的露点温度以上时,方可开启混合机排气口与混流筒烟气入口之间的气动阀,混合机中的含湿烟气进入混流筒。含湿烟气与热介质在混流筒内混合,形成混合烟气,待混流筒上的第三温度传感器检测到混合烟气的温度达到含湿烟气露点温度以上时,混合烟气通过除尘管道进入除尘器进行处理。当与各混流筒连接的各自的除尘管道的风量满足要求,现场无扬尘则保持第一调节阀和第二调节阀的开度状况。当现场有岗位出现扬尘时,则启动调节程序,此时通过调节各除尘管道上的第二调节阀来平衡各点的阻力,使进入各除尘管道的风量满足要求,即岗位无粉尘外逸。需要注意的是,第一调节阀在调节风量时,可能使得混流筒内或除尘管道内混合烟气的温度发生变化,而不再满足混合烟气温度在含湿烟气露点温度以上的要求,此时通过调节热介质输送管道(或热介质输送管道分出的热介质支管)上的第一调节阀,进而调节进入热介质输送管道或混流筒内的热介质的量,使得混合烟气的温度处于含湿烟气的露点温度以上。此循环运行至岗位无扬尘及除尘管道上的第四温度传感器检测温度达到含湿烟气的露点温度以上后记录此时系统中各阀门的开度状态。当工艺生产状态稳定,生产余热装置可提供有效余热给系统使用时,第四开关阀开启,第三开关阀关闭,热风炉停止运行,此时系统使用工艺生产余热,实现能量梯级利用,智能控制系统启动程序结束。
[0070]
与现有技术相比,本发明具有以下有益技术效果:
[0071]
1、本发明引入了混流筒,将混流筒设置在混合机排气端的上方,并通过气动阀连接,待混流筒内的温度上升至混合机中含湿烟气露点温度以上,此时混合机内的含湿烟气进入混流筒,从而能够避免现有技术中在热风汇入初期含湿烟气仍然可能结露堵塞除尘管道的问题,进而确保混合烟气进入除尘器的温度全程均在烟气露点温度以上。
[0072]
2、本发明通过压力检测判断热介质输送管道和混流筒内是否处于积灰状态,并通过增压风机引入外界空气进行反吹清扫,从而避免管道积灰堵塞,使系统长期稳定运行。
[0073]
3、本发明采用预热器作为备用热源,当判断生产工艺中有余热可利用,即可优先利用工艺生产过程中产生的余热,实现能源梯级利用,节约能源。热介质输送管道上设置的
增压风机除了给清灰程序中的外界空气进行增压,还可作为备用动力源,避免因热介质输送管道阻力过大引起的压力不平衡现象,使热介质的引入更加稳定,也有利于后续对除尘烟气温度的稳定。
[0074]
4、本发明通过湿度、温度等检测数据判断烟气的露点温度,用于计算控制进入除尘器的烟气温度在露点温度以上所需的最小热介质量,即在保证烟气在除尘过程中不冷凝结露的前提下,还能够最大程度的降低能耗。
[0075]
5、本发明混流系统能够同时对多个混合机的含湿烟气进行处理,并确保进入除尘器的烟气温度在烟气露点温度以上,即能够彻底解决含湿烟气结露堵塞除尘管道的问题,确保系统长期稳定运行。而且,本发明混流系统带有多测点,多处设置传感器和多个阀门,各处烟气量或温度均可调控,控制精确灵活,智能化程度高。
附图说明
[0076]
图1为本发明一种智能控制抗结露型饱和湿烟气混流系统的结构示意图;
[0077]
图2为本发明混流系统具有多个混合机和混流筒的结构示意图;
[0078]
图3为本发明中控制装置的示意图;
[0079]
图4为本发明一种智能控制抗结露型饱和湿烟气混流方法的控制流程图。
[0080]
附图标记:
[0081]
1:混合机;2:混流筒;3:除尘器;4:增压风机;5:预热器;6:生产余热装置;701:第一压力传感器;702:第二压力传感器;801:第一温度传感器;802:第二温度传感器;803:第三温度传感器;804:第四温度传感器;805:第五温度传感器;9:湿度传感器;10:控制装置;
[0082]
k:气动阀;s1:第一开关阀;s2:第二开关阀;s3:第三开关阀;s4:第四开关阀;s5:第五开关阀;z1:第一调节阀;z2:第二调节阀;
[0083]
l1:热介质输送管道;l2:除尘管道;l3:气体输送管道;l4:第一供热管道;l5:第二供热管道;l6:旁路管道;l7:热介质支管;l8:除尘总管。
具体实施方式
[0084]
下面对本发明的技术方案进行举例说明,本发明请求保护的范围包括但不限于以下实施例。
[0085]
根据本发明的第一种实施方案,提供一种智能控制防结露型饱和湿烟气混流系统。
[0086]
一种智能控制防结露型饱和湿烟气混流系统,该系统包括混合机1、混流筒2、除尘器3。所述混流筒2设置在混合机1排气端的上方,混合机1的排气口通过气动阀k与混流筒2的烟气入口连接。热介质输送管道l1连接至混流筒2的热介质入口。混流筒2的烟气出口经由除尘管道l2连接至除尘器3。
[0087]
在本发明中,该系统还包括气体输送管道l3。所述气体输送管道l3连接至热介质输送管道l1的输入端。
[0088]
作为优选,热介质输送管道l1上设有第一开关阀s1和增压风机4。优选,气体输送管道l3上设有第二开关阀s2。
[0089]
在本发明中,该系统还包括预热器5。所述预热器5经由第一供热管道l4连接至热
介质输送管道l1的输入端。作为优选,第一供热管道l4上设有第三开关阀s3。优选,所述预热器5为热风炉。
[0090]
在本发明中,该系统还包括生产余热装置6。所述生产余热装置6经由第二供热管道l5连接至热介质输送管道l1的输入端。作为优选,第二供热管道l5上设有第四开关阀s4。
[0091]
在本发明中,从热介质输送管道l1上分出旁路管道l6,旁路管道l6绕过第一开关阀s1和增压风机4后合并至热介质输送管道l1。优选,旁路管道l6上设有第五开关阀s5。
[0092]
作为优选,热介质输送管道l1上设有第一压力传感器701和第二压力传感器702。其中,第一压力传感器701位于热介质输送管道l1上分出旁路管道l6位置的上游。第二压力传感器702位于旁路管道l6合并至热介质输送管道l1位置的下游。
[0093]
在本发明中,热介质输送管道l1上设有第一温度传感器801。第一温度传感器801位于热介质输送管道l1上分出旁路管道l6位置的上游。混合机1上设有第二温度传感器802和湿度传感器9。混流筒2上设有第三温度传感器803。除尘管道l2上设有第四温度传感器804。
[0094]
作为优选,热介质输送管道l1上设有第一调节阀z1。第一调节阀z1位于旁路管道l6合并至热介质输送管道l1位置的下游。除尘管道l2上设有第二调节阀z2。
[0095]
作为优选,该系统包括n个混合机1。每个混合机1的排气端上方均对应设置一个混流筒2。各混合机1与混流筒2之间均通过气动阀k连接。在旁路管道l6合并至热介质输送管道l1位置的下游,所述热介质输送管道l1分出n根热介质支管l7分别连接至n个混流筒2的热介质入口。各混流筒2的烟气出口分别通过各自的除尘管道l2连接至除尘器3。优选,n的取值为1-10,优选为2-6。
[0096]
优选的是,每个混合机1上均设有第二温度传感器802和湿度传感器9。每个混流筒2上均设有第三温度传感器803。每个混流筒2各自连接的除尘管道l2上均设有第四温度传感器804和第二调节阀z2。每根热介质支管l7上均设有第一调节阀z1。
[0097]
作为优选,每个混流筒2各自连接的除尘管道l2在合并后经由除尘总管l8连接至除尘器3。优选,除尘总管l8上设有第五温度传感器805。
[0098]
在本发明中,该系统还包括控制装置10。所述控制装置10与气动阀k、第一开关阀s1、第二开关阀s2、第三开关阀s3、第四开关阀s4、第五开关阀s5、第一压力传感器701、第二压力传感器702、第一温度传感器801、第二温度传感器802、第三温度传感器803、第四温度传感器804、第五温度传感器805、湿度传感器9、第一调节阀z1、第二调节阀z2连接,并控制各阀门和各传感器的操作。
[0099]
实施例1
[0100]
如图1所示,一种智能控制防结露型饱和湿烟气混流系统,该系统包括混合机1、混流筒2、除尘器3。所述混流筒2设置在混合机1排气端的上方,混合机1的排气口通过气动阀k与混流筒2的烟气入口连接。热介质输送管道l1连接至混流筒2的热介质入口。混流筒2的烟气出口经由除尘管道l2连接至除尘器3。
[0101]
实施例2
[0102]
重复实施例1,只是该系统还包括气体输送管道l3。所述气体输送管道l3连接至热介质输送管道l1的输入端。
[0103]
实施例3
[0104]
重复实施例2,只是热介质输送管道l1上设有第一开关阀s1和增压风机4。
[0105]
实施例4
[0106]
重复实施例3,只是气体输送管道l3上设有第二开关阀s2。
[0107]
实施例5
[0108]
重复实施例4,只是该系统还包括预热器5。所述预热器5经由第一供热管道l4连接至热介质输送管道l1的输入端。所述预热器5为热风炉。
[0109]
实施例6
[0110]
重复实施例5,只是第一供热管道l4上设有第三开关阀s3。
[0111]
实施例7
[0112]
重复实施例6,只是该系统还包括生产余热装置6。所述生产余热装置6经由第二供热管道l5连接至热介质输送管道l1的输入端。
[0113]
实施例8
[0114]
重复实施例7,只是第二供热管道l5上设有第四开关阀s4。
[0115]
实施例9
[0116]
重复实施例8,只是从热介质输送管道l1上分出旁路管道l6,旁路管道l6绕过第一开关阀s1和增压风机4后合并至热介质输送管道l1。
[0117]
实施例10
[0118]
重复实施例9,只是旁路管道l6上设有第五开关阀s5。
[0119]
实施例11
[0120]
重复实施例10,只是热介质输送管道l1上设有第一压力传感器701和第二压力传感器702。其中,第一压力传感器701位于热介质输送管道l1上分出旁路管道l6位置的上游。第二压力传感器702位于旁路管道l6合并至热介质输送管道l1位置的下游。
[0121]
实施例12
[0122]
重复实施例11,只是热介质输送管道l1上设有第一温度传感器801。第一温度传感器801位于热介质输送管道l1上分出旁路管道l6位置的上游。混合机1上设有第二温度传感器802和湿度传感器9。混流筒2上设有第三温度传感器803。除尘管道l2上设有第四温度传感器804。
[0123]
实施例13
[0124]
重复实施例12,只是热介质输送管道l1上设有第一调节阀z1。第一调节阀z1位于旁路管道l6合并至热介质输送管道l1位置的下游。除尘管道l2上设有第二调节阀z2。
[0125]
实施例14
[0126]
如图2所示,重复实施例13,只是该系统包括3个混合机1。每个混合机1的排气端上方均对应设置一个混流筒2。各混合机1与混流筒2之间均通过气动阀k连接。在旁路管道l6合并至热介质输送管道l1位置的下游,所述热介质输送管道l1分出3根热介质支管l7分别连接至3个混流筒2的热介质入口。各混流筒2的烟气出口分别通过各自的除尘管道l2连接至除尘器3。
[0127]
实施例15
[0128]
重复实施例14,只是每个混合机1上均设有第二温度传感器802和湿度传感器9。每个混流筒2上均设有第三温度传感器803。每个混流筒2各自连接的除尘管道l2上均设有第
四温度传感器804和第二调节阀z2。每根热介质支管l7上均设有第一调节阀z1。
[0129]
实施例16
[0130]
重复实施例15,只是每个混流筒2各自连接的除尘管道l2在合并后经由除尘总管l8连接至除尘器3。除尘总管l8上设有第五温度传感器805。
[0131]
实施例17
[0132]
如图3所示,重复实施例16,只是该系统还包括控制装置10。所述控制装置10与气动阀k、第一开关阀s1、第二开关阀s2、第三开关阀s3、第四开关阀s4、第五开关阀s5、第一压力传感器701、第二压力传感器702、第一温度传感器801、第二温度传感器802、第三温度传感器803、第四温度传感器804、第五温度传感器805、湿度传感器9、第一调节阀z1、第二调节阀z2连接,并控制各阀门和各传感器的操作。
[0133]
实施例18
[0134]
一种智能控制防结露型饱和湿烟气混流方法,使用实施例13所述的系统,该方法包括以下步骤:
[0135]
1)确定混合机1中含湿烟气的露点温度。
[0136]
2)通过热介质输送管道l1向混流筒2内通入热介质,待混流筒2内的温度高于步骤1)中所述含湿烟气的露点温度,此时打开气动阀k,混合机1中的含湿烟气进入混流筒2。
[0137]
3)含湿烟气与热介质在混流筒2内混合,得到混合烟气,待混合烟气的温度高于步骤1)中所述含湿烟气的露点温度,此时混合烟气通过除尘管道l2进入除尘器3进行除尘处理。
[0138]
实施例19
[0139]
如图4所示,一种智能控制防结露型饱和湿烟气混流方法,使用实施例17所述的系统,,该方法包括以下步骤:
[0140]
1)确定3个混合机1中含湿烟气的露点温度。
[0141]
2)通过热介质输送管道l1分出的热介质支管l7分别向各混流筒2内通入热介质,待各混流筒2内的温度高于对应混合机1中含湿烟气的露点温度,此时打开气动阀k,各混合机1中的含湿烟气进入对应的混流筒2。
[0142]
3)含湿烟气与热介质在各混流筒2内混合,得到混合烟气,待各混流筒2内混合烟气的温度高于对应混合机1中含湿烟气的露点温度,此时各混流筒2内的混合烟气通过各自的除尘管道l2合并至除尘总管l8后进入除尘器3进行除尘处理。
[0143]
实施例20
[0144]
重复实施例19,只是步骤2)中还包括检测清灰的步骤,具体为:在向混流筒2内通入热介质之前,先采用第一压力传感器701和第二压力传感器702对热介质输送管道l1上的压力进行检测。若压力检测异常,则启动系统清灰程序,此时外界空气通过增压风机4引入气体输送管道l3和热介质输送管道l1,外界空气对热介质输送管道l1及混流筒2进行反吹清扫。直至第一压力传感器701和第二压力传感器702检测压力恢复正常,结束系统清灰程序。
[0145]
实施例21
[0146]
重复实施例20,只是步骤2)中所述向混流筒2内通入热介质,具体为:在系统运行之初,通过预热器5为热介质输送管道l1提供热介质。当工艺生产状态稳定,生产余热装置6
可提供有效余热,此时通过生产余热装置6为热介质输送管道l1提供热介质。
[0147]
实施例22
[0148]
重复实施例21,只是步骤1)中所述确定混合机1中含湿烟气的露点温度,具体包括以下子步骤:
[0149]
①
收集工程中大量含湿烟气的湿度、温度数据,通过焓湿图获得相应工况条件下的烟气露点温度,建立烟气露点温度数据库。
[0150]
②
采用湿度传感器9和第二温度传感器802分别测量混合机1中含湿烟气的湿度和温度,从烟气露点温度数据库中获取对应混合机1中含湿烟气的露点温度。
[0151]
实施例23
[0152]
重复实施例22,只是计算步骤2)中需要向混流筒2内通入热介质的量,具体包括以下子步骤:
[0153]
a)计算预热混合机1中的含湿烟气所需热量:
[0154]
混合机1中含湿烟气的量为v
烟
,m3/h。检测含湿烟气的温度为t
烟
,℃。烟气露点温度为t0,℃。设定含湿烟气与热介质混合后得到的混合烟气的温度为t
设
,℃。t
设
=t0 10℃。由此,预热混合机1中的含湿烟气所需要吸收的热量q
烟
为:
[0155]q烟
=c
烟v烟
ρδt
烟
=c
烟v烟
ρ
烟
(t
设-t
烟
)。
[0156]
式中:c
烟
为含湿烟气的比热容,kj/(kg
·
℃)。ρ
烟
为含湿烟气的密度,kg/m3。
[0157]
b)计算进入混流筒2的热介质所释放的热量:
[0158]
设进入混流筒2的热介质的量为v
热
,m3/h。检测热介质的温度为t
热
,℃。由此,进入混流筒2的热介质所释放的热量q
热
为:
[0159]q热
=c
热v热
ρδt
热
=c
热v热
ρ
热
(t
热-t
设
)。
[0160]
式中:c
热
为热介质的比热容,kj/(kg
·
℃)。ρ
热
为热介质的密度,kg/m3。
[0161]
c)由预热含湿烟气所需要吸收的热量q
烟
与进入混流筒的热介质所释放的热量q
热
相等,可得:
[0162]c烟v烟
ρ
烟
(t
设-t
烟
)=c
热v热
ρ
热
(t
热-t
设
)。
[0163]
即得:
[0164]v热
=c
烟v烟
ρ
烟
(t
设-t
烟
)/[c
热
ρ
热
(t
热-t
设
)]。
[0165]
调节热介质输送管道l1分出的热介质支管l7上的第一调节阀z1的开度,使得步骤2)中混流筒2内通入的热介质的量为v
热
。
[0166]
实施例24
[0167]
重复实施例23,只是在步骤3)中,调节除尘管道l2上第二调节阀z2的开度,使得各除尘点的风量满足要求,各除尘点无粉尘外逸的现象。同时,第四温度传感器804在线检测除尘管道l2上混合烟气的温度t,并调节热介质支管l7上的第一调节阀z1的开度,使得t等于t
设
。
[0168]
应用实施例1
[0169]
一种智能控制防结露型饱和湿烟气混流方法,该方法包括以下步骤:
[0170]
1)确定混合机1中含湿烟气的露点温度,具体包括以下子步骤:
[0171]
①
收集工程中大量含湿烟气的湿度、温度实测数据,通过焓湿图获得相应工况条件下的烟气露点温度,建立烟气露点温度数据库。
[0172]
②
采用湿度传感器9测量混合机1中含湿烟气的相对湿度d=85%,第二温度传感器802测量混合机1中含湿烟气的温度t
烟
=49℃,从烟气露点温度数据库中获取对应混合机1中含湿烟气的露点温度t0=45℃。
[0173]
2)采用第一压力传感器701和第二压力传感器702对热介质输送管道l1上的压力进行检测。其中,第一压力传感器701显示对应位置管道压力p1=-60pa,第二压力传感器702显示对应位置管道压力p2=-500pa,即两者所检测到的压差大于200pa,由此判断热介质输送管道l1内压力异常,启动系统清灰程序。此时外界空气通过增压风机4引入气体输送管道l3和热介质输送管道l1,外界空气对热介质输送管道l1及混流筒2进行反吹清扫。直至第一压力传感器701和第二压力传感器702检测压力恢复正常,结束系统清灰程序。
[0174]
在系统运行之初,通过预热器5为热介质输送管道l1提供热介质。热介质输送管道l1向混流筒2内通入热介质,待混流筒2内的温度高于对应混合机1中含湿烟气的露点温度,此时打开气动阀k,混合机1中的含湿烟气进入对应的混流筒2。
[0175]
计算需要向混流筒2内通入热介质的量,具体包括以下子步骤:
[0176]
a)计算预热混合机1中的含湿烟气所需热量:
[0177]
混合机1中含湿烟气的量为v
烟
=20000m3/h。第二温度传感器802检测含湿烟气的温度为t
烟
=49℃。烟气露点温度为t0=45℃。设定含湿烟气与热介质混合后得到的混合烟气的温度为t
设
,℃。t
设
=t0 15℃=60℃。由此,预热混合机1中的含湿烟气所需要吸收的热量q
烟
为:
[0178]q烟
=c
烟v烟
ρδt
烟
=c
烟v烟
ρ
烟
(t
设-t
烟
)=240999kj/h。
[0179]
式中:c
烟
为含湿烟气的比热容,c
烟
=1.005kj/(kg
·
℃)。ρ
烟
为含湿烟气的密度,ρ
烟
=1.09kg/m3。
[0180]
b)计算进入混流筒2的热介质所释放的热量:
[0181]
设进入混流筒2的热介质的量为v
热
,m3/h。第一温度传感器801检测热介质的温度为t
热
=150℃。由此,进入混流筒2的热介质所释放的热量q
热
为:
[0182]q热
=c
热v热
ρδt
热
=c
热v热
ρ
热
(t
热-t
设
)。
[0183]
式中:c
热
为热介质的比热容,c
热
=1.005kj/(kg
·
℃)。ρ
热
为热介质的密度,ρ
热
=0.78kg/m3。
[0184]
c)由预热含湿烟气所需要吸收的热量q
烟
与进入混流筒的热介质所释放的热量q
热
相等,可得:
[0185]c烟v烟
ρ
烟
(t
设-t
烟
)=c
热v热
ρ
热
(t
热-t
设
)。
[0186]
即得:
[0187]v热
=c
烟v烟
ρ
烟
(t
设-t
烟
)/[c
热
ρ
热
(t
热-t
设
)]=3416m3/h。
[0188]
调节热介质输送管道l1上的第一调节阀z1的开度,使得步骤2)中混流筒2内通入的热介质的量为v
热
。
[0189]
3)含湿烟气与热介质在混流筒2内混合,得到混合烟气,待混流筒2内混合烟气的温度高于对应混合机1中含湿烟气的露点温度,此时混流筒2内的混合烟气通过除尘管道l2进入除尘器3进行除尘处理。
[0190]
在步骤3)中,调节除尘管道l2上第二调节阀z2的开度,使得各除尘点的风量满足要求,各除尘点无粉尘外逸的现象。同时,第四温度传感器804在线检测除尘管道l2上混合
烟气的温度t,并调节热介质输送管道l1上的第一调节阀z1的开度,使得t等于t
设
。记录此时系统中各阀门的开度状态。
[0191]
当工艺生产状态稳定,生产余热装置6可提供有效余热,此时通过生产余热装置6为热介质输送管道l1提供热介质。
再多了解一些
本文用于创业者技术爱好者查询,仅供学习研究,如用于商业用途,请联系技术所有人。